Приемка строительной части объекта
Подготовительные и вспомогательные работы при монтаже
12.01.2019 https://extxe.com/11066/podgotovitelnye-i-vspomogatelnye-raboty-pri-montazhe/#3
Содержание страницы
1. Приемка и подготовка оборудования к монтажу
2. Приемка строительной части объекта
3. Предмонтажное укрупнение оборудования в блоки
Приемка и подготовка оборудования к монтажу
Приемка оборудования. Во время приемки проверяют: комплектность оборудования по упаковочным листам и комплектовочно-отгрузочным ведомостям; его соответствие заводским чертежам и техническим условиям; исправность; наличие пломб; отсутствие повреждений или поломок, трещин и раковин; наличие избыточного давления в сосудах (если это предусмотрено в документации), а также полноту технической документации на оборудование, если она не была получена ранее.
Транспортирование оборудования со склада завода-заказчика (базисного) до приобъектного склада, а при монтаже «с колес» в монтажную зону осуществляют силами и средствами заказчика по заявкам монтажной организации, передаваемым за три дня до планируемого срока подачи.
Документом, фиксирующим приемку (сдачу) оборудования в монтаж, является приемосдаточный акт. В акте делается оговорка, что полная характеристика технического состояния: дефекты конструкции и заводского изготовления, некомплектность, выявленные при расконсервации, монтаже и испытании оборудования, — будет зафиксирована дополнительным актом. Акты подписывают представители заказчика, монтажной организации и генерального подрядчика, а также, при необходимости, завода-изготовителя.
|
|
Принятое от заказчика оборудование находится на ответственном хранении монтажной организации. Для предохранения от повреждений и деформации отдельные машины, их элементы, узлы и детали укладывают на деревянные подкладки или настилы. Приборы, аппаратура, арматура, фитинги и другое мелкое оборудование хранят в закрытом складе на стеллажах, на которых вывешивается опись изделий, находящихся на данном стеллаже.
По способу хранения в зависимости от массы, габаритных размеров, характера упаковки и требований защиты от атмосферных осадков оборудование делится на четыре группы.
Оборудование, не требующее защиты от атмосферных осадков, а также имеющее большую массу (негабаритное) и мало подверженное коррозии, хранится на открытых площадках или прирельсовых эстакадах.
Оборудование, нуждающееся в защите от атмосферных осадков, хранится на полуоткрытых площадках под индивидуальным или общим навесом.
Оборудование с обработанными посадочными или рабочими поверхностями, которое надо защищать от влаги и сырости, и мелкие детали содержат в сухих закрытых неутепленных и неотапливаемых помещениях, а оборудование, требующее дополнительной защиты от температурных влияний, хранят в закрытых утепленных, отапливаемых и вентилируемых складах.
|
|
Резиновые манжеты и другие изделия из резины должны храниться в закрытых помещениях при температуре 0…20 °С.
Расконсервация и очистка оборудования. Консервация — временное предохранение защитными покрытиями (смазочными материалами, красками, лаками, упаковкой) поверхностей от коррозии.
Пластичные и консервационные смазки и лакокрасочные покрытия обеспечивают сохранность оборудования в течение одного года, а ингибированные смазки и рабочие масла с присадками — в течение 3…5 лет. Корпуса редукторов и внутренние поверхности емкостей консервируют маслостойкими красителями, растворами нитрата натрия или воздухом, насыщенным парами ингибитора.
Расконсервацию — удаление консервационных смазок, лакокрасочных и других покрытий выполняют на приобъектных складах или в монтажной зоне на специально отведенных площадках или непосредственно на фундаментах. Затраты на выполнение этих работ учтены в стоимости монтажа оборудования.
|
|
Пластичные и консервационные смазки удаляют нагревом в ваннах с минеральным маслом при 100…120 °С с последующей протиркой салфетками из бязи, а также промыванием горячей водой или водно-моющими растворами с пассиваторами и последующей сушкой.
Используют также специальные химические растворяющие вещества: растворители; обезжиривающие составы и моющие жидкости.
Основные растворители представляют собой бесцветные прозрачные подвижные и летучие жидкие органические соединения с характерным запахом, которые подразделяются на углеводороды, спирты, кетоны, сложные и простые эфиры.
Ацетон (диметилкетон) смешивается во всех пропорциях с водой, спиртом, эфирами, минеральными и растительными маслами, бензином, керосином и др. Он растворяет жиры, многие смолы и лаки, ацетилен, ацетат целлюлозы; не растворяет резину.
Бензин-растворитель (уайт-спирит) растворяет все масла, кроме касторового, и является активным растворителем для масляных лаков, красок и эмалей.
Бензин-растворитель марок БР-1 — «галоша», БР-2 — растворитель резины.
Бензин для технических целей применяют в качестве растворителя.
Тетрахлорэтан используют для растворения жиров, серы, фосфора и др.
Толуол — растворитель масел, смол, асфальтов; смешивается с ацетоном, углеводородами, эфиром.
|
|
Трихлорэтилен служит для обезжиривания деталей перед сборкой. Он негорюч, малотоксичен.
Четыреххлористый технический углерод растворяет жиры, масла, каучук, канифоль, смолы, фосфор и др. Продукт негорюч, но ядовит: предельная концентрация в рабочей зоне не выше 20 мг/м3 (вблизи открытого огня токсичен).
Технический хифробензол растворим в спирте, нерастворим в воде. Служит в качестве растворителя смол, лаков, этилцеллюлозы. Трудно воспламеняется, но токсичен.
Этиловый спирт смешивается в любых пропорциях с водой, спиртами, эфиром, глицерином, бензином. Его применяют в качестве растворителя, моющей жидкости, в антиобледенительных составах и др.
Для удаления смазок используют струйную промывку узлов и поверхностей оборудования подогретой смесью керосина и минерального масла или одного масла. Мелкие детали промывают в механизированных установках на решетках в ванне с подогревом и подачей промывочной смеси на очищаемые поверхности.
Громоздкие детали и узлы очищают от смазки струей насыщенного или сухого пара, который подается на деталь по резиновому шлангу с наконечником.
Если не истек гарантийный срок хранения, ингибированные смазки удаляют из механизмов заливкой рабочего масла и прокручиванием механизмов вхолостую в течение 20…30 мин. Затем смесь сливают и заливают чистое масло. Масляные краски удаляют щелочной пастой, в которую входят (мас. доли, %): каустическая сода 25, негашеная известь 15, порошковый мел 25, вода 35. Пасту наносят на очищаемую поверхность слоем толщиной 1…1,5 мм и выдерживают 1…3 ч в зависимости от типа и числа слоев краски. Размягченную краску вместе с пастой снимают шпателем, а ее остатки смывают водой.
Лаковые покрытия снимают пастойсмывкой, которую наносят на поверхность и выдерживают в течение 3…5 мин, а затем удаляют кистью, а поверхность протирают салфеткой. Лакокрасочные покрытия снимают также с помощью скребков, щеток и шлифовальных машинок, оснащенных специальными щетками и кругами. Для временного предохранения от коррозии расконсервированные поверхности не позже 1…2 ч после их очистки покрывают техническим вазелином, синтетическим солидолом или смазкой, указанной в технических условиях завода-изготовителя.
На поверхность, покрытую ржавчиной (коррозией), наносят пасту слоем толщиной 1…1,5 мм и выдерживают в течение 0,25…6 ч в зависимости от плотности и толщины ржавчины. С очищенной поверхности пасту удаляют салфетками или водой. Для предохранения поверхности от дальнейшего окисления ее нейтрализуют 10 %-ным водным раствором «Можеф» или 5…10 %-ным раствором ортофосфорной кислоты. Технико-экономические показатели применения паст приведены в табл. 1.
Расконсервацию узлов с подшипниками качения осуществляют на участке, специально оборудованном для этих целей. Подшипниковые узлы или крупногабаритные подшипники промывают в механизированной (душирующей) установке или направленной струей минерального масла, нагретого до 105…120 °С. При необходимости проводят предварительную сушку сухим паром. Промытые подшипники (узлы) протирают салфетками и обертывают плотной бумагой.
Загущенный раствор нитрата натрия удаляют из емкостей промывкой (2…2,5) %-ным раствором нитрата натрия, содержащим 0,5 %-ную кальцинированную соду, с последующей сушкой. Воздух с парами ингибитора удаляют продуванием полостей (емкостей) нагретым воздухом иди промывкой мыльно-содовым раствором с добавлением 1…2 % нитрата натрия.
Таблица 1. Технико-экономические показатели применения паст
Паста | Расход, кг/м2 | Время выдержки на поверхности металла, мин |
Щелочная | 2 | 60…180 |
Смывка | 0,8 | 3…5 |
«Целлогель» | 1,5 | 15…360 |
Обезжиривание кислородного оборудования осуществляют в соответствии с инструкциями на монтаж и стандартами. Пожаровзрывоопасные растворители применяют для обезжиривания изделий, работающих в среде кислорода, без ограничения рабочих давлений и температур. К ним относятся: четыреххлористый углерод, трихлорэтилен, тетрахлорэтилен и фреон-113. Расход растворителей этой группы для однократного обезжиривания труб приведен в табл. 2.
Для промывки и обезжиривания других деталей и узлов машин кроме растворителей и их композиций наибольшее распространение получили моющие составы:
1. водные щелочные растворы с некоторыми улучшающими добавками; в их состав входят кальцинированная или каустическая сода, тринатрий фосфат, калиевый или натриевый хромпик, моющие присадки, эмульгаторы и др. (табл. 3);
2. специальные концентрированные смеси, например креолин, предназначенный для отмывки гидроприводов и других гидросистем, деталей двигателей внутреннего сгорания от пригара и углеродистых сложений.
Таблица 2. Расход растворителей для обезжиривания труб
Внутренний диаметр трубы, мм | Расход растворителя на 1 м трубы, дм3 (л) | Внутренний диаметр трубы, мм | Расход растворителя на 1 м трубы, дм3 (л) | Внутренний диаметр трубы, мм | Расход растворителя на 1 м трубы, дм3 (л) |
3 | 0,02 | 40 | 0,25 | 200 | 1,6 |
6 | 0,04 | 50 | 0,3 | 250 | 2 |
10 | 0,06 | 70 | 0,4 | 300 | 2,4 |
15 | 0,09 | 80 | 0,5 | 500 | 4 |
20 | 0,12 | 100 | 0,8 | 750 | 6 |
25 | 0,15 | 125 | 1 | 1000 | 8 |
32 | 0,2 |
Состав креолина (%): масло для креолина 49; каменноугольные фенолы 11; канифоль 17; хозяйственное мыло 14; остальное — раствор каустической соды.
Креолин применяют обычно в виде эмульсии (1 : 1), нагретой до 60…70 °С; он токсичен и пожароопасен.
Масло для креолина выпускают марок А и Б.
Моечный состав 1120 предназначен для удаления ржавчины и масляных следов с металлических поверхностей перед окрашиванием с последующей обработкой нейтрализующим составом 107. Нейтрализующий состав 107 — водная смесь этилового спирта (40 %) с аммиаком (не менее 0,5 %) для нейтрализации металлической поверхности после очистки ее моечным составом 1120. Для очистки поверхностей оборудования от коррозии применяют пасты (табл. 4), водные травильные растворы (табл. 5), а также водные растворы кислот для одновременного обезжиривания и травления (табл. 6).
Расконсервацию оборудования осуществляют в зависимости от примененного метода консервации и вида защитных составов, используя способы, приведенные в табл. 7.
Ревизия оборудования. Предмонтажная ревизия — комплексная проверка состояния оборудования и устранение повреждений, вызванных хранением машин и агрегатов на складах заказчика сверх нормативных гарантийных сроков, указанных техническими условиями на их изготовление и поставку. При отсутствии гарантийного срока ревизия проводится через год.
Затраты на выполнение предмонтажной ревизии в сметах не приводятся, поэтому ревизию выполняет заказчик или работники монтажной организации по прямому договору, заключенному с заказчиком.
Предмонтажная ревизия предусматривает:
· расконсервацию оборудования;
· разборку для расконсервации и осмотра вращающихся и движущихся деталей;
· удаление коррозии, грязи и посторонних частиц с последующими промывкой, протиркой и консервацией обработанных поверхностей;
Таблица 3. Область применения и составы водных моющих растворов
Область применения | № раствора | Компоненты | Количество компонента на 1 дм3 (л) воды, г | Продолжительность обезжиривания, мин |
Трубопроводы из коррозионно-стойких сталей всех марок, чугуна, меди, латуни | 1 | Натрий фосфорнокислотный (тринатрийфосфат) | 15 | 20 |
То же, из алюминия и его сплавов | 2 | Стекло натриевое жидкое. Моющее вещество1 | 20 | 30 |
Трубопроводы из коррозионно-стойких сталей всех марок, меди, латуни | 3 | Натрий гидрат оксида (едкий натр) | 10 | 15 |
Для сильно загрязненных деталей | Натрий фосфорнокислотный (тринатрийфосфат) | 15 | ||
4 | Стекло натриевое жидкое. Моющее вещество1 | 2…3 | ||
Трубопроводы из стали всех марок, чугуна, меди, латуни, алюминия и его сплавов | 5 | Моющее вещество МЛ-2 | 50 | 30 |
6 | Моющее вещество бытовой химии2 |
1 ОП-7 или ОП-10 в количестве 2…3 г/дм3 (2…3 г/л); моющий препарат синтанол ДС-10 в количестве 5 г/дм3.
2 Средство бытовой химии в количестве 5 г/дм3 в растворах 1, 2 и 4.
Примечание. При употреблении растворов 5 и 6 следует обязательно осматривать обезжиренные изделия после промывки и просушки. Обнаруженные сухие остатки моющих растворов должны быть удалены.
· проверку состояния (сохранности) изделий;
· замену антикоррозионных смазок рабочими, прокладок, сальниковых набивок и мелких деталей (подшипников, питательных трубок, масленок, пробок и т.п.), пришедших в негодность в результате хранения;
· исправление мелких (неконструктивных) дефектов, шабрение посадочных мест подшипников, трущихся поверхностей, шлифование шеек и цапф валов;
· перемещение и кантовку оборудования, связанные с ревизией;
· последующую сборку оборудования;
· устройство стеллажей, настилов и ванн, необходимых для ревизии, и организацию участка;
· выполнение работ, определяемых особыми требованиями завода-изготовителя по сохранности оборудования.
Ревизию и совмещенную с ней укрупнительную сборку оборудования в монтажные блоки осуществляют на специально отведенных площадках.
Таблица 4. Составы паст (%) для очистки от коррозии
Состав | Паста | Состав | Паста | ||
«Целлогель» | травильная | «Целлогель» | травильная | ||
Вода | 39,7 | 17 | Жидкое мыло Ингибиторы: ЧМ уротропин Нефтяной контакт Древесные опилки Трепел | 6,6 | – |
Кислота (плотность, | |||||
кг/м3): | – | 0,5 | |||
серная (1840) | – | 7,7 | 1 | – | |
соляная (1190) | 49,2 | 21,3 | – | 0,5 | |
фосфорная (1707) | – | 2,4 | 3,5 | – | |
Сульфитоцеллюлозный щелок | — | 14,6 | — | 36 |
Таблица 5. Составы водных травильных растворов (кг на 1 м 3 раствора) и режимы обработки поверхностей изделий
Материал изделия | Состав | Режим травления | |||||||
Кислота (плотность, кг/м3) | Каустик (сода) | Ингибиторы | Температура, °С | Продолжительность обработки, мин | |||||
соляная (1190) | серная (1840) | азотная (1420) | Катапин | Н-1-А | в ваннах | струйным методом | |||
Чугун и сталь | 150±30 | 35±5 | – | – | 1…3 | – | 50…70 | 10…30 | – |
– | – | 2…3 | 60…80 | ||||||
– | 50…60 | – | 3…5 | ||||||
Медь и ее сплавы | – | 70±20 | 30…40 | 10…20 | – | ||||
Алюминий и его сплавы | – | 100±5 | 50…60 | – | 0,5…1 | ||||
Магнитные сплавы | 5±1 | 90±1 | – | 30 | 20…30 | – |
Примечания.
1. Медь и ее сплавы после травления осветляют в растворе азотной кислоты.
2. Магнитные сплавы после травления осветляют в 4…5 %-ном водном растворе плавиковой кислоты.
3. При струйном методе обработки давление 0,15…0,25 МПа.
Таблица 6. Составы водных растворов (кг на 1 м3 раствора) и режим обработки для одновременного обезжиривания и травления металлических поверхностей
Изделие | Серная кислота (плотность 1840 кг/м3) | Хлористый натрий | Сульфанол | ||||
Стальной прокат; конфигурация простой и средней сложности | 175±25 | — | — | ||||
Стальные отливки с большим слоем окалины | 165±25 | 120±10 | 4±1 | ||||
Сложной конфигурации (с карманами и зазорами) | 250±50 | — | — | ||||
Чугунные отливки, обрабатываемые в шнековых установках | 175±25 | ||||||
Изделие | Жидкость ПМС-200 или уайтспирит | Эмульгатор ОП-7 или ОП-10 | Температура, °С | Продолжительность обработки, мин | |||
в ваннах | струйным методом | ||||||
Стальной прокат; конфигурация простой и средней сложности | 0,3±0,2* или 25±5** | 2,5±0,5 | 50…60 | — | 3…5 | ||
Стальные отливки с большим слоем окалины | – | – | 5…15 | ||||
Сложной конфигурации (с карманами и зазорами) | 0,3±0,2* или 25±5** | 2,5±0,5 | 60…70 | ||||
Чугунные отливки, обрабатываемые в шнековых установках | — | 4±1 | 50…60 | 5…10 | — | ||
* Жидкость ПМС-200.
** Уайт-спирит.
Подготовка материалов и комплектующих изделий. В качестве материалов и комплектующих изделий применяют прокладки, сальниковые набивки, манжеты и специальные герметизирующие составы. Они служат для уплотнения плоских стыков машин и мест выхода подвижных деталей механизмов.
Прокладочные материалы. Конструкции и размеры прокладок при монтаже соединений выбирают, руководствуясь указаниями чертежей или технических условий (табл. 8).
Таблица 7. Способы расконсервации в зависимости от вида консервирующих покрытий или защитной среды
Консервирующее покрытие или защитная среда | Способ консервации |
Спиртовой раствор ингибитора НДА, порошки ингибиторов НДА, УЛИ, КЦА и Г-2 | Промывка 3…5 %-ным раствором нитрата натрия с последующей сушкой сжатым воздухом |
Ингибированный воздух | Продувка горячим воздухом с температурой 80…90 °С. Промывка мыльно-содовым раствором с добавлением 1…2 % нитрата натрия |
Ингибированная бумага | Удаление бумаги |
Жидкие ингибированные смазки НГ-203 (марок А, Б и В), К-17, НГ-204У | Промывка бензином или уайт-спиритом, протирка ветошью; промывка водными моющими растворами |
Пластичные смазки ПВК, 3ЭС, ГОИ-54П, АМС-3, торсиол | Погружение в нагретое до 110 °С минеральное масло с последующей промывкой бензином или уайт-спиритом; промывка бензином или уайт-спиритом (алюминиевые детали); промывка в ваннах специальными растворами с последующей пассивацией (трубы) |
Загущенный раствор нитрата натрия | Промывка раствором, содержащим 3…5 % нитрата натрия и 0,5 % кальцинированной соды с последующей сушкой |
Рабочие масла, ингибированные присадки АКОР-1, МРИ-3, МСДА-11, КП, КП-2 и др. | Расконсервации не требуется |
Сальниковые набивки. Для герметизации машин и механизмов применяют волокнистые и комбинированные, сухие и пропитанные сальниковые набивки — плетеные, скатанные и кольцевые. Материал и вид набивок выбирают в зависимости от рабочей среды, ее температуры и давления (табл. 9).
Резиновые уплотняющие детали. Наиболее общее применение нашли манжеты (для цилиндров и штоков валов, для
пневматических и гидравлических устройств) и кольца.
Герметизирующие составы. Для герметизации неподвижных разборных соединений, а также периодически подвижных соединений, частичного их смазывания, предохранения деталей от коррозии, обеспечения подвижности и разбираемости служат различные герметизирующие смазки, мастики и мази. Области применения герметизирующих смазок, резиновых и тиоколовых герметиков приведены в табл. 10 и 11.
Прокладки из пеньки пропитывают вареным маслом или суриком.
Таблица 8. Материалы для изготовления прокладок
Область применения | Материал | Характеристика | ||
Рабочая среда | Температура, °С, не более | Рабочее давление, МПа, не более | ||
Вода, пар | 55 | 5,0 | Паронит ПОН или ПА | Листы толщиной 0,4…6 мм |
Бензин, керосин, масло | 20 | 7,5 | ||
100 | 6,5 | Паронит ПМБ | Листы толщиной 0,4…3 мм | |
Вода, пар | 450 | 5,0 | Паронит ПА | Листы толщиной 0,8…1,2 мм |
Отработавший пар, горячие газы | 0,15 | Картон асбестовый | Листы толщиной 2…10 мм | |
250…425 | — | Асбест | Скрученный или плетеный шнур диаметром 0,75…55 мм | |
Горячие газы | 150 | Асбометаллический армированный материал | Полотно толщиной 0,6; 0,7 и 1,1 мм | |
Пар, газообразные продукты сгорания | 450 | 0,1 | Асбест | Ткань толщиной 1,8…3,5 мм |
Горячие газы | 0,2 | Листы толщиной 1,4…1,75 мм | ||
Вода, нефть, масло в соединениях | 40 | 1,0 | Картон технический | Листы или рулоны толщиной 0,3…2,5 мм |
Масло, вода, воздух в соединениях оборудования и трубопроводов | 30 | 0,15 | Прессшпан | Марка А толщиной 0,35…0,4 мм, марки В толщиной 0,5 мм |
Вода, воздух, вакуум | 0,3 | Резина листовая | Толщина 1…8 мм | |
Вода, воздух | 60 | 0,6 | Резина с парусиновой прослойкой | |
90 | 1,0 | Резина с металлической сеткой | ||
Масло, керосин, нефть | 20 | 0,1 | Чертежная бумага промасленная | Листы |
Вода | 40 | 0,3 | Пеньковые волокна | — |
Бензин, керосин | 80 | 1,0 | Фибра | Листы толщиной 0,4…12,5 мм |
Пар | 250 | 3,5 | Медь | Листы и проволока из меди марок М1 и М3 отожженные |
Вода | – | 10,0 | ||
Кислота | 0,2 | Свинец | Листы | |
Вода | 10,0 | Мягкая сталь | ||
Пар | 470 | – | ||
Кислота, бензин | 60 | 4,0 | Полихлорвинил | |
Пар | 300 | 20 | Алюминий | Листы толщиной 2…4 мм |
Примечание. Прокладки из бумаги или картона пропитывают смесью касторового масла с глицерином или машинным маслом. При установке на нефте- и мазутопроводах прокладки предварительно пропитывают керосином или нефтью.
Таблица 9. Области и условия применения набивок
Набивки | Область применения | Давление, МПа, не более | Температура, °С, не выше |
Плетеные | |||
Хлобчатобумажные сухие ХБС | Воздух, питьевая вода, нейтральные растворы, спирт, смазочные масла | 20 | 100 |
Хлобчатобумажные пропитанные ХБП | Воздух, промышленная вода, пары и газы, нефтепродукты | ||
Пеньковые сухие ПС | Воздух, промышленная вода, водяной пар, смазочные масла | 16 | |
Тальковые пропитанные ТП | Промышленная вода, нейтральные растворы, слабокислые среды | 1 | 130 |
Асбестовые, пропитанные антифрикционным составом графитированные АП | Воздух, пары и газы агрессивные, слабокислые растворы, топливо нефтяное, нефтепродукты | 4,5 | 300 |
Скатанные | |||
Асбестовые маслобензостойкие АМБ | Кислые масла, топливо нефтяное, органические растворы | 3 | 300 |
Хлобчатобумажные МХБ | Вода промышленная | 20 | 100 |
Льняные ПЛ | |||
Асбестовые с фторопластом ПАФ | Промышленная вода, перегретый и насыщенный водяной пар | 10 | 400 |
Асбестометаллические пропитанные с латунной проволокой АПР |
Таблица 10. Область применения уплотнительных смазок
Смазка | Область применения | ||
Уплотняемые детали | Среда | Температура, °С | |
Бензиноупорная | Неподвижные резьбовые и другие соединения | Нефтепродукты | –10…+40 |
Вакуумная замазка | Соединения вакуумных установок | Воздух | –10…+50 |
Вакуумная (Рамзая) | Стеклянные и металлические подвижные соединения | –10…+40 | |
ВНИИ НП-263 | Резьбовые соединения | Воздух, вода | –50…+100 |
ЗЗК-2у | Люки, крышки и др. | Воздух, пары, вода | –15…+100 |
Смазка | Область применения | ||
Уплотняемые детали | Среда | Температура, °С | |
ЛЗ-162 | Задвижки, краны | Нефтепродукты, газ | –25…+150 |
Насосная | Сальниковые уплотнения высокого давления | Нефтепродукты, загрязненные жидкости, спирт, вода, глицерин | 120 |
ЦИАТИМ-205 | Неподвижные резьбовые соединения | Воздух, вода | –60…+50 |
Резьбовая: Р-2 | Резьбовые соединения деталей и труб | –40…+100 | |
Р-113 | –30…+200 | ||
Р-402 | –50…+200 | ||
Р-416 | –30…+100 |
Таблица 11. Область применения тиоколовых герметиков
Марка | Вид соединения | Среда | Температура эксплуатации, °С | Особенности применения |
У-30М | Металлические (кроме латунных, медных, серебряных) | Воздух, жидкое топливо, разбавленные кислоты и щелочи | –60…+130 | С клеевым подслоем |
У-30МЭС-5 | Металлические | Воздух, жидкое топливо | Без подслоя | |
УТ-31 | Металлические (кроме латунных, медных, серебряных) | С клеевым подслоем | ||
УТ-32 | Металлические | Воздух или топливо | Без подслоя | |
51-УТ-36А | Металлические, пластмассовые | Воздух, пары | С адгезивом | |
ВИТЭФ-1 | Металлические из органического стекла | Воздух, пары воды и топлива | –60…+150 | Без подслоя |
ВИТЭФ-2 | –60…+130 | С ускорителем |
Приемка строительной части объекта
Порядок приемки. В соответствии с графиком к моменту начала монтажных работ должны быть подготовлены монтажные и складские площадки, дороги и подъезды, фундаменты и опорные конструкции (подкрановые пути, монорельсы, постаменты, этажерки и т.п.) под оборудование, подземные коммуникации; выполнены обратная засыпка и уплотнение грунта, черновые полы, каналы и туннели; закончены стены, остекление окон и фонарей; уложена кровля; навешены ворота и двери; подготовлено временное или постоянное освещение.
При выполнении работ в зимнее время должны быть: утеплены производственные помещения, смонтирована и подключена система отопления, обеспечивающая поддержание температуры в помещениях не ниже 5 °С.
В насосных, насосно-аккумуляторных станциях, маслоподвалах, компрессорных, машинных залах, помещениях для турбовоздуходувок, турбин и другого аналогичного оборудования должны быть закончены штукатурные работы, а к началу комплексного опробования машин и агрегатов — отделочные работы.
Фундаменты и помещения необходимо освободить от строительных лесов, опалубки, очистить от мусора и сдать под монтаж оборудование по акту с предъявлением исполнительной схемы. При этом проемы в перекрытиях должны быть ограждены, а каналы, туннели, лотки и люки закрыты. Фундаменты под монтаж оборудования принимаются как по всему зданию, так и по участкам или пролетам. При этом мостовые краны, используемые для монтажа машин, должны находиться в рабочем состоянии, а дороги быть готовыми для подачи оборудования.
Фундаменты под монтаж оборудования должны приниматься в соответствии с техническими условиями. В процессе выполнения подготовительных работ монтажная организация, осуществляющая монтаж оборудования, составляет и передает строительной организации для исполнения схему геодезической основы монтажа. Пример такой схемы приведен на рис. 1.
При приемке по схеме контролируют точность нанесения всех осей и высотных отметок.
На фундаментах, предназначенных для установки машин и агрегатов, связанных в одну технологическую линию и требующих высокой точности установки, оси и высотные отметки должны быть вынесены на закладные плашки и реперы. Их установку, «закрепление» осей и фиксацию высотных отметок осуществляет строительная организация.
В производственных зданиях и цехах, в которых размещается легкое промышленное оборудование, не связанное между собой кинематически, цеховыми коммуникациями и конвейерами, контрольные и основные оси и высотные отметки могут выноситься на несущие строительные конструкции (колонны или стены) и фиксироваться на специальных закладных деталях или при низких требованиях к точности геодезической разбивки масляной краской, а рабочие оси — на полу цеха.
Места установки плашек и реперов проверяют по монтажным (установочным) чертежам с уточнением мест расположения плашек и реперов по заводским чертежам на оборудование и сверкой с фактической конфигурацией оборудования и его габаритными размерами.
Число разбивочных осей, монтажных рисок, реперов, плашек, места их расположения, способ закрепления указывают в ППР или в проекте геодезических работ.
Сдачу (приемку) строительной части объекта и проверку его готовности к монтажу осуществляют в соответствии с правилами СНиП «Технологическое оборудование и технологические трубопроводы» и инструкциями по монтажу отдельных видов оборудования. Проведение и приемку геодезических работ выполняют исходя из требований СНиП «Геодезические работы в строительстве».
Рис. 1. Схема геодезической основы монтажа агломерационной машины: 1 – ось звездочек привода головной части; 2 – продольная ось машины; 3 – ось звездочек разгрузочного устройства;
— оси здания;
— контрольные оси;
— главные разбивочные оси;
— основные разбивочные оси;
— рабочий репер;
— рабочая плашка;
— выносные плашки с репером;
— привязка главной разбивочной оси к контрольной;
— контрольная привязка основной разбивочной оси
Технические условия на приемку фундаментов под монтаж. Приемку фундаментов под монтаж начинают после получения от строительной организации исполнительной схемы и разрешения на производство монтажных работ. Готовность фундаментов к проведению монтажных работ оформляется актом. К акту прилагаются составленные строительной организацией исполнительные схемы основных и привязочных размеров; отметок фундамента; расположения фундаментных болтов, шанцев и анкерных колодцев; размещения металлических плашек и реперов, заделанных в тело фундамента и фиксирующих его оси и высотные отметки.
К акту готовности фундаментов для монтажа машин с динамическими и ударными нагрузками прилагается акт выполнения виброизоляции в соответствии с проектом.
Фундаменты под машины и открытые технологические установки монтажная организация может принять до полной строительной готовности объекта, если их монтаж по графику должен быть выполнен до окончания основных строительных работ.
Фундаменты под машины и другое технологическое оборудование, устанавливаемые без подливки раствором, должны сооружаться на полную проектную отметку и сдаваться под монтаж с выровненной поверхностью.
Фундаменты под машины, устанавливаемые с последующей подливкой, сдают под монтаж забетонированными на 50…80 мм ниже проектной отметки опорной поверхности станины машины, а при наличии в основании корпусной детали выступающих частей или ребер жесткости — на 50…80 мм ниже их проектной отметки.
Перед сдачей машин под монтаж фундамент, включая колодцы для фундаментных болтов, должен быть освобожден от опалубки и очищен от строительного мусора. Раковины, пористость, наслоения и другие дефекты недопустимы; выступающие из бетона арматура и проволока, а также металлические кондукторы необходимо обрезать. На фундаментные болты следует установить гайки и шайбы, а их нарезанные части должны быть защищены от коррозии и предохранены от повреждений. Оси и реперы, закрепленные на фундаменте, надо размещать вне контура опорных поверхностей корпусных деталей машин и механизмов.
Расположение фундаментов контролируют относительно главных осей, а их элементов — относительно рабочих монтажных осей.
Фактическую точность вынесения основных и контрольных, а также отдельных рабочих осей и высотных отметок выборочно проверяют на соответствие требованиям, указанным в схеме геодезического обоснования, а для остальных осей и высотных отметок — по исполнительной схеме. В тех случаях, когда в проекте геодезического обоснования нет специальных требований к точности вынесения осей и высотных отметок, их принимают исходя из требований для заданных классов точности разбивочных работ. В этом случае во время приемки реперов, расположенных на одном монтажном горизонте, контролируют соответствие точности разбивки высотных отметок допускам, указанным в табл. 12, а точности разбивки осей — допускам, приведенным в табл. 13. Точность передачи высотных отметок с одного монтажного горизонта на другой должна отвечать допускам, представленным в табл. 14.
Таблица 12. Допуски (мм) разбивки высотных отметок (для реперов)
Номинальный размер H* | Класс точности | |||||
1 | 2 | 3 | 4 | 5 | 6 | |
До 2500 | – | 0,6 | 1,0 | 1,6 | 2,4 | 4 |
Св. 2500 до 4000 | 0,6 | 1,0 | 1,6 | 2,4 | 4,0 | 6 |
» 4000 » 8000 | 1,0 | 1,6 | 2,4 | 4,0 | 6,0 | 10 |
» 8000 » 16 000 | 1,6 | 2,4 | 4,0 | 6,0 | 10,0 | 16 |
» 16 000 » 25 000 | 2,4 | 4,0 | 6,0 | 10,0 | 16,0 | 24 |
» 25 000 » 40 000 | 4,0 | 6,0 | 10,0 | 16,0 | 24,0 | 40 |
» 40 000 » 60 000 | 6,0 | 10,0 | 16,0 | 24,0 | 40,0 | 60 |
» 60 000 » 100 000 | 10,0 | 16,0 | 24,0 | 40,0 | 60,0 | 100 |
» 100 000 » 160 000 | 16,0 | 24,0 | 20,0 | 60,0 | 100,0 | 160 |
* Н — расстояние между точками в вертикальной плоскости.
Таблица 13. Допуски (мм) разбивки точек и осей в плане (для плашек)
Номинальный размер L* | Класс точности | |||||
1 | 2 | 3 | 4 | 5 | 6 | |
До 2500 | 0,6 | 1,0 | 1,6 | 2,4 | 4 | 6 |
Св. 2500 до 4000 | 1,0 | 1,6 | 2,4 | 4,0 | 6 | 10 |
» 4000 » 8000 | 1,6 | 2,4 | 4,0 | 6,0 | 10 | 16 |
» 8000 » 16 000 | 2,4 | 4,0 | 6,0 | 10,0 | 16 | 24 |
» 16 000 » 25 000 | 4,0 | 6,0 | 10,0 | 16,0 | 24 | 40 |
» 25 000 » 40 000 | 6,0 | 10,0 | 16,0 | 24,0 | 40 | 60 |
» 40 000 » 60 000 | 10,0 | 16,0 | 24,0 | 40,0 | 60 | 100 |
» 60 000 » 100 000 | 16,0 | 24,0 | 40,0 | 60,0 | 100 | 160 |
» 100 000 » 160 000 | 24,0 | 40,0 | 60,0 | 100,0 | 160 | – |
*L — расстояние между точками и осями в горизонтальной плоскости.
Таблица 14. Допуски (мм) передачи высотных отметок (для реперов)
Номинальный размер L* | Класс точности | |||||
1 | 2 | 3 | 4 | 5 | 6 | |
До 8000 | – | 0,6 | 1,0 | 1,6 | 2,4 | 4 |
Св. 8000 до 16 000 | 0,6 | 1,0 | 1,6 | 2,4 | 4,0 | 6 |
» 16 000 » 25 000 | 1,0 | 1,6 | 2,4 | 4,0 | 6,0 | 10 |
» 25 000 » 40 000 | 1,6 | 2,4 | 4,0 | 6,0 | 10,0 | 16 |
» 40 000 » 60 000 | 2,4 | 4,0 | 6,0 | 10,0 | 16,0 | 24 |
» 60 000 » 100 000 | 4,0 | 6,0 | 10,0 | 16,0 | 24,0 | 40 |
» 100 000 » 160 000 | 6,0 | 10,0 | 16,0 | 24,0 | 40,0 | 60 |
*L — расстояние между точками (реперами) в горизонтальной плоскости.
Готовые фундаменты принимают при условии соответствия их фактических размеров и расположения поверхностей закладных деталей, анкерной арматуры, фундаментных болтов и колодцев под них проектным параметрам.
Отклонения фактических размеров фундаментов и их элементов не должны превышать приведенных ниже допустимых значений.
Схемы проверки фундаментов и их элементов приведены в табл. 15.
Дата добавления: 2022-11-11; просмотров: 18; Мы поможем в написании вашей работы! |
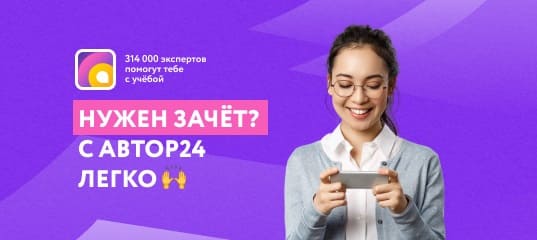
Мы поможем в написании ваших работ!