Понятие прогрессивной нормы времени и аналитическо-расчётного метода расчёта.
Урок № 25
1.7 Техническое нормирование.
Тема урока: «Классификация затрат рабочего времени. Методика расчёта основного времени»
Цели урока:
Дидактическая:
создание условий для формирования понятий о важности расчётов технически обоснованной нормы времени, структуре основного времени методах его расчёта.
Воспитательная:
воспитание познавательного интереса, осознанного отношения к процессу обучения.
Развивающая:
развитие умения рационально выполнять и оформлять свою работу, развитие гибкости мышления.
Оснащение урока:
1. Интерактивный комплект.
Вид урока: урок смешанный
Методы и приёмы: сообщение нового материала с элементами демонстрации и привлечением студентов.
План урока.
1. Классификация затрат рабочего времени.
2. Основное технологическое время.
Понятие прогрессивной нормы времени и аналитическо-расчётного метода расчёта.
Нормирование методом сопоставления.
Задание на дом: 1. с. 148-150.
Урок № 25.
Классификация затрат рабочего времени.
Себестоимость выпускаемой машины является одним из важнейших факторов, характеризующих в денежном выражении основные затраты человеческого труда и материалов на её изготовление. Одной из составляющей себестоимости является расход на заработную плату. Заработная плана рабочих-станочников зависит от времени, затрачиваемого на технологическую операцию.
|
|
Время t, затрачиваемое на операцию, слагается из двух частей:
- подготовительно-заключительного времени, затраченного на единицу продукции, проходящей данную операцию;
- штучного времени, т.е. времени, затрачиваемого на выполнение данной операции.
Следовательно, можно записать
где tn.з - подготовительно-заключительное время; n - количество изделий в партии; tшт - штучное время.
Штучное время включает в себя следующие составляющие:
где tо.т. - основное технологическое время; tB — вспомогательное время; toб - время обслуживания рабочего места; tд - время, необходимое на личные потребности и отдых при утомительных работах.
Основное технологическое время.
Основное технологическое время затрачивается на изменение размеров, формы, состояния поверхностного слоя, структуры материала (или других физико-механических свойств) заготовки или детали либо на изменение ее положения в процессе сборки и т.д.
Если перечисленные изменения производятся при помощи оборудования (станка, пресса, печи) без участия человека, основное технологическое время называется машинным. Если такие изменения производятся человеком без помощи оборудования, основное технологическое время называется ручным. При изменения производимых одновременно при помощи машины и с участием рабочего, основное технологическое время называется машинно-ручным.
|
|
Для установления нормы времени необходимо уметь определять все ее слагаемые.
|
Наиболее просто определяется машинное время. Действительно, для определения машинного времени служит основная исходная формула
где Li - требуемое перемещение инструмента с рабочей подаче относительно обрабатываемого объекта или, наоборот, обрабатываемого объекта относительно инструмента, мм; i — число необходимых для обработки проходов; S м - минутная рабочая подача инструмента или обрабатываемой детали, мм/мин; п – частота вращения шпинделя или двойных ходов обрабатываемой детали или инструмента; S о - рабочая подача инструмента или обрабатываемой детали один оборот шпинделя или двойной ход станка, мм.
Обычно перемещение Li представляет собой сумму следующих составляющих:
Li = l 1 + l д + l 2 или Li = l вр + l д + l пер
где l 1 ( l вр ) - добавочное относительное перемещение инструмента или детали, необходимое для исключения удара одного о другую;
l д - размер длины поверхности, указанный на чертеже обрабатываемого объекта;
|
|
l 2 ( l пер ) - добавочное относительное перемещение инструмента и детали, необходимое в ряде случаев для выхода режущего инструмента, как это, например, показано на рис. 1.
![]() |
Рисунок 1 - Схема определения длины хода инструмента с рабочей подачей.
Удары инструмента о деталь оказываются возможными вследствие колебаний размеров поверхностей обрабатываемых деталей, зазоров в кинематических цепях и упругих деформаций звеньев технологической системы, возникающих в результате действия сил, особенно при быстром подводе инструмента к детали или детали к инструменту.
При токарной обработке частота вращения шпинделя
где v — скорость резания; d — диаметр обрабатываемой детали.
При обработке деталей на продольно-строгальном станке
Li =В+ l 1 + l 2
где vp x и vx x - соответственно скорость рабочего и холостого ходов стола станка, м/мин; В - ширина поверхности, подлежащей обработке, мм.
Исходные данные для расчета tмаш берутся из рабочих чертежей деталей, технологических процессов их изготовления, нормативов по режимам обработки, технологических характеристик и паспортных данных оборудования и инструмента.
|
|
Сложнее обстоит дело с нормированием ручных приемов и их элементов, так как время, необходимое рабочему для их выполнения, пока не поддается расчету. Поэтому для нормирования ручных приемов и их элементов используются различного рода нормативные данные в виде таблиц, графиков и номограмм, в которых приведены нормы времени на выполнение типовых ручных приемов и их элементов, связанных с подготовкой рабочего места к работе, управлением станком, сменой, установкой и закреплением обрабатываемых деталей.
Разработка нормативных данных базируется на сборе, систематизации и математической обработке статистических данных фактических затратах времени на ручные приемы и их элементы при выполнении существующих технологических процессов нормальных производственных условиях и при нормальной интенсивности труда.
Путем систематизации полученных таким способом однородных данных из различных технологических процессов обработка деталей на однородных станках разрабатывают нормативные таблицы.
Для изучения элементов отдельных ручных приемов, на которые затрачиваются иногда секунды и даже их доли, используется ускоренная киносъемка с отметкой малых промежутков времени.
Опыт нормирования ручных приемов показывает, что для получения наиболее надежных норм времени наилучшие результата дает использование исходных нормативных данных, имеющих однозначные цифровые значения по каждому ручному приему его элементу.
Понятие прогрессивной нормы времени и аналитическо-расчётного метода расчёта.
Имея исходные данные, рассчитывают и устанавливают прогрессивную норму времени, необходимую для выполнения oпepaции. Под прогрессивной нормой времени понимается такая норма, в которую заложены нормальные условия труда надлежащие интенсивности на исправном оборудовании при использования всех возможностей технологической системы. Благодаря этому прогрессивная норма времени способствует устранению различного рода неполадок и наилучшему использованию всех возможностей оборудования, технологической оснастки и организации.
Из изложенного следует, что для установления технической прогрессивной нормы времени необходимо иметь:
- тщательно разработанный с использованием передового опыта технологический процесс данной операции с перечнем всех ручных приемов (а в ряде случаев и их элементов), содержащий все исходные данные, необходимые для расчета машинного времени;
- нормативы по выбору режимов обработки, технологические характеристики и паспортные данные по оборудованию, технологической оснастке и инструменту;
- исходные нормативные данные по ручным приемам и их элементам.
Наличие перечисленных данных позволяет отдельно нормировать время, потребное на ручные приемы, и подсчитать машинное время. После этого простым суммированием продолжительности не совмещенных во времени ручных приемов и машинного времени подсчитывают оперативное и подготовительно-заключительное время. Имея эти данные, определяют техническую прогрессивную норму времени.
Изложенный метод нормирования, получивший название аналитического расчетного, отличается от других детальной разработкой технологического процесса с учетом передового опыта и использованием новейшей техники. Этот метод рекомендуется в качестве основного для расчета прогрессивных технически обоснованных норм времени.
Установление таких норм времени диктуется, во-первых, требованием непрерывного повышения производительности труда и наиболее экономичного использования всех средств производства и, во-вторых, необходимостью обеспечить надежные исходные данные для планирования производства, так как нормы времени, устанавливаемые на отдельные технологические операции, являются основой планирования.
Неправильные нормы времени приводят к значительным погрешностям в планировании и способствуют нарушению ритмичного хода производства.
В зависимости от изменения факторов, действующих при выполнении технологического процесса, время, фактически затрачиваемое на выполнение операции технологического процесса, может отличаться от расчетной нормы.
Нормирование должно производиться высококвалифицированными работниками, хорошо знающими оборудование, инструмент и другую оснастку современного производства, так как в противном случае нормы могут оказаться недостаточно обоснованными и ошибочными.
Дата добавления: 2022-06-11; просмотров: 84; Мы поможем в написании вашей работы! |
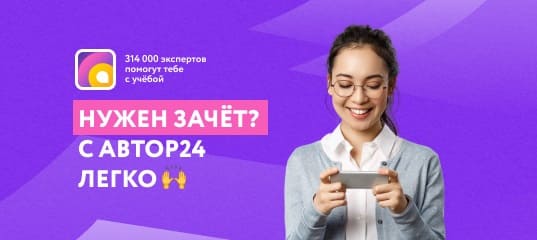
Мы поможем в написании ваших работ!