Устройства для контакта газа с глиноземом
Т а б л и ц а 6 1
Фирма | Реактор | Скорость газа,
![]() | Концентрация
![]() ![]() | Гидравлическое
![]() |
![]() |
Вертикальная труба ![]() | 19 |
![]() | <400 |
![]() | То же | 19 | 10-150 | <400 |
![]() | Расширенный кипящий слой |
![]() |
![]() ![]() | 3000 |
![]() | Ввод ![]() | Соответствует скорости газа | 10-150 | Незначительно |
"ALCOA" | ![]() |
![]() | Нет данных |
![]() |
Фирма гарантирует содержание на выходе из установки HF и твердых фторидов — не более 1, пыли — не более 5 В России установки этой фирмы эксплуатируют на Саянском алюминиевом заводе и обеспечивают проектные показатели — согласно статистическим данным, выбросы фтора
на этом заводе самые низкие из российских заводов и не превышают 0,35 кг фтора на 1 т произведенного алюминия, т на уровне лучших зарубежных показателей
Система фирмы "Procedair". Эта компания, так же как и "Rakt", широко применяет сухую очистку электролизных газов; по ее данным на декабрь 1994 г., 11 226 электролизеров в разных странах мира, производящих около 4,4 млн т алюминия в год, оборудовано такими системами.
Как и фирма "Rakt", эта компания применяет модульный
принцип построения своих систем (рис. 6.9), который позволяет из однотипных установок собирать мощные газоочистные бло- ки, способные очищать газ от половины ванн корпуса, упрощать и резко сокращать сроки монтажа и наладки.
Кроме того, применение однотипных блоков дает возможность минимизировать затраты на запасные части к газоочистным установкам.
|
|
Реактором в этой системе является вертикально установлен- ная низконапорная труба Вентури, в которой контакт глинозема с газом осуществляется в восходящем турбулентном потоке с последующим отделением глинозема на фильтре. В схеме предусмотрена возможность рециркуляции глинозема с кратно- стью от 10 до 40
6.2
Характеристика пылеуловителей
Фирма | Тип | Материал | Метод регенера- ции | Давление воздуха для регене- | Гидравличес- кое сопро- Па | Остаточная запылен- ность,
![]() |
![]() | Рукава | Нетканый полиэфир | Импуль- сный | 1,5-2,0 | До1500 | <5 |
![]() |
![]() | То же |
![]() |
![]() | До 1500 | <5 |
![]() | Электро- фильтр, рукава |
![]() |
![]() | 7,0 | 300(Эф) 1500 (Рф) | <30 (Эф) 5-1 (Рф) |
"ALCOA" | Мешки |
![]() |
![]() | 7,0 | 300 (Эф) | (Эф) |
1500 (Рф) | 5-1 (Рф) | |||||
![]() | Рукава |
![]() |
![]() | 7,0 | 300 (Эф) | (Эф) |
1500 (Рф) | 5-1 (Рф) | |||||
"Кайзер |
![]() |
![]() |
![]() | 6,5 | 1500 | Нет |
![]() | данных |
Эф — — рукавный фильтр.
Установка для очистки электролизных газов объемом 1,7 млн
состоит из 14 модулей реактор — фильтр, общая площадь фильтрации в каждом модуле 1532
Рукава изготавливаются из нетканого полиэфирного материала диаметром 0,127 и длиной 6 м. Практически весь потребный
|
|
для электролиза глинозем проходит через модули.
Характеристика систем сухой очистки газов. Проведенная в ВАМИ [30] экспертная оценка технических решений основных широко используемых в мировой практике систем сухой очистки газов, разработанных ведущими фирмами Европы и США, показала, что по своей эффективности они практически одина- ковы и обеспечивают улавливание
%
газов и почти всей пыли, содержащейся в отсасываемом
газе. Различаются же эти системы в основном принципом действия и конструкцией реакторов. В табл. 6.1 и 6.2 приведены характеристики систем сухой очистки газов.
Таким образом, гидравлическое сопротивление и расход энергии наиболее низки у систем фирм "Flakt", "Procedair" и "ALCAN". Такая же тенденция наблюдается и при сравнении капиталовложений.
Г л а в а 7
ОТХОДЫ ПРОИЗВОДСТВА И ИХ УТИЛИЗАЦИЯ
В процессе деятельности алюминиевого завода в его цехах и подразделениях накапливаются отходы производства, которые подлежат утилизации, длительному хранению или уничтожению. В настоящем разделе рассматриваются вопросы, связанные с утилизацией отходов, образующихся при рабо- те газоочистных сооружений и
хозяйства, пере- работке угольной пены, проведении капитального ремонта электролизеров.
|
|
7.1. Производство регенерированного криолита
Как показано в гл. 6, при использовании мокрого способа улавливания отходящих газов раствор газоочистки, содержащий воду, бикарбонат натрия, фтористый натрий, а также уловлен- ную в скрубберах пыль (шлам, состоящий из глинозема, криолита, фтористых солей, частиц угля, пека и
применяют для получения криолита. В ре- зультате утилизации фторсодержащих соединений выполняются две функции: улучшаются экологические показатели производ- ства и одновременно снижаются расходы на производство алюминия за счет выработки дорогостоящего криолита.
Газоочистка может вестись при высокой (В) или низкой концентрации солей в растворе, и поэтому в зависимости от
выбранной технологии в растворах могут содержаться следу- ющие концентрации солей
— фтористого натрия — (Н) или (В);
|
|
- соды - 3-7 (Н) или 10-15 (В);
—
бикарбоната натрия — (Н) или (В);
— сульфата натрия — до 70.
4 Заказ № 22
Принципиальная схема производства растворов и варки криолита приведена на рис.
Содовый раствор, поступающий на орошение газа в скруб- берах, должен содержать % соды
г/л) и готовится растворением кальцинированной соды в воде.
раствор из скрубберов после газо- очистки со взвешенными в нем частицами шлама поступает в
![]() |
Рис. 7.1. Схема приготовления растворов и варки криолита
отстойники отделения регенерации для осветления. Отстаива- ние растворов зависит от скорости оседания взвешенных частиц, которая составляет всего 0,1
но при предваритель- ном подогреве раствора до 60 — 70 °С ее удается повысить в раз и увеличить производительность отстойников по осветленному раствору. Осветление осуществляется в сгусти- теле, стенки которого теплоизолированы. Оно считается закон-
ченным, если раствор содержит твердых взвесей до г/л.
Сгущенный в отстойниках шлам с соотношением жидкого к твердому ж т
фильтруется на барабанном фильтре. Шламовая паста после в мешалках откачива- ется на шламовое поле, полученный фильтрат направляется в баки осветленного раствора. Химический состав шлама в значительной степени зависит от типа электролизера. Так, по данным
содержание веществ составляет (числи- тель — ВТ, знаменатель — F - 32,7/15,5; - 13,0/27,3;
- 21,9/10,5; - 0,5/0,4; - 0,3/0,2;
- 3,7/1,2;
- 0,9/0,3; - 5,2/3,7; — 16,2/18,9; смолистые —
8,2.
Собственно процесс выделения криолита из
раствора, называемый варкой, может идти как в перио-
дическом, так и в непрерывном режиме, и последнему следует отдать предпочтение как обеспечивающему более высокую производительность и лучшее качество криолита.
Для получения криолита необходимо приготовить
![]() |




где
— алюминат натрия с каустическим модулем 1,5, под которым понимают молекулярное отношение оксида натрия к оксиду алюминия в растворе.
Варка криолита ведется в теплоизолированных реакторах с
мешалками, обогреваемых паром при температуре 85 - 95 °С. Из
осветленный раствор подается в напорный бак и далее из него самотеком поступает в дозатор, а затем — в реакторы, которые обычно собираются в нитки по штук.
![]() |



При расчете дозировки алюминатного раствора определя- ющим является отношение содержания в осветленном растворе бикарбоната натрия к фтористому натрию
![]() |
где 84 и 42 — молекулярные массы бикарбоната натрия и фтористого натрия соответственно. Если в осветленном раст- воре это соотношение больше или равно 1,5, то дозировку алюминатного раствора

где 202 — соотношение молей вещества к
6 — остаточная концентрация NaF в маточном растворе, г/л;
— концентрация соответствующих компонентов в раст-
воре, г/л.
![]() |


где 135 — соотношение молей глинозема к бикарбонату натрия;
3 — остаточная концентрация бикарбоната натрия в растворе, г/л; — концентрация бикарбоната натрия в растворе,
г/л.
Из реакторов пульпа с соотношением ж т (40 - 100) 1 поступает на сгущение в сгуститель, из которого слив осветленной части пульпы (маточный раствор) направляется как оборотный содовый раствор на газоочистку,
при этом содержание соды в маточном растворе должно быть г/л, а взвешенных частиц криолита не более 0,5 г/л.
В маточных растворах накапливается значительное количе- ство сульфатов, и чтобы избежать ухудшения качества криолита, предусмотрено периодическое удаление их из цикла газо- очистки. Обычно это производится во время ремонта баковой аппаратуры и трубопроводов отделения регенерации — сульфа- ты в виде двойной соли
оседают на стенках и удаляются механическим путем или в растворе каустической
соды.
Сгущенная пульпа с соотношением
—
1 из сгустителя выводится в
и оттуда подается на вакуум-фильтр. Фильтрат поступает в бак маточного раствора, а отфильтрованный криолит еще дважды для снижения отношения и содержания в нем сульфата натрия, причем во второй раз пульпа криолита смешивается со сгущенной пульпой флотационного криолита, производство которого из угольной пены рассмотрено в разд. 7.2. Поскольку
отношение регенерационного криолита составляет иногда называют щелочным.
Паста смешанного криолита с влажностью % посту- пает на сушилку, где сушится до влажности 1,5
а оттуда направляется в бункер готовой продукции и периодически отгружается в электролизный цех.
7.2. Переработка угольной пены и производство криолита
![]() |
Как показано в разд. 4.2, в процессе электролиза в электролизе- рах образуется угольная пена, которую периодически удаляют с поверхности электролита и направляют на переработку. Вместе с пеной снимается и электролит, содержание которого достигает
Химический состав пены приблизительно следующий
F - -
0,5; - 0,2-0,5; - С -
- 0,2-
![]() |
Производство криолита из угольной пены осуществляется по схеме, представленной на рис. 7.2.
Рис. 7.2. Схема получения флотационного криолита.
Доставленная из цеха угольная пена про- ходит магнитную сепарацию (во избежание попадания в дро- билку металлических
а затем дробится на дробилке и поступает на мокрое измельчение в шаровую
мельницу. Измельченная пена далее делится на спиральном классификаторе на два продукта: слив с классификатора с высоким измельчением пены и песков, состоящих из более крупных частиц пены. Тонина помола пены в сливе составляет
% частиц класса тоньше 0,075 мм, что обеспечивает хорошее разделение частиц угля и электролита. Пески возвра- щаются на в шаровую мельницу.
Слив из классификатора, разбавленный до ж т
(4 - 3) поступает в контактный чан для перемешивания с и далее — на флотацию. Последняя основана на свойстве несмачивающихся водой (гидрофобных) материалов прилипать к находящимся в водном растворе пузырькам воздуха. материалов может быть усилена введением в
раствор которые попадая на поверхность мел- кодисперсных гидрофобных частиц, еще более ухудшают их смачиваемость водой, поэтому они более интенсивно прилипа- ют к пузырькам воздуха и вместе с ними выносятся на поверхность пульпы. Для увеличения эффективности процесса флотации важно иметь тонкоизмельченные материалы, так как крупные частицы не могут удерживаться пузырьками воздуха.
При флотации угольной пены имеются два вида частиц — хорошо смачиваемые водой (гидрофильные) частицы электролита и плохо смачиваемые (гидрофобные) частицы угля. Для усиления гидрофобных свойств угля в качестве
применяют смесь соснового масла с керосином в соотношении 1 9 или скипидара и керосина в соотношении 2 1. На производство 1 т расходуется 1700 кг угольной пены, 0,4 кг сосно-
вого масла и кг керосина. Возможно применение и других видов флотореагентов.
Частицы угля сорбируют на своей поверхности
становятся практически несмачиваемыми водой и, увле-
каясь вверх пузырьками воздуха, образуют пену. Последняя непрерывно механическими гребками снимается с поверхности пульпы, благодаря чему пульпа обогащается частицами элект- ролита, которые оседают на дно флотационной машины, а затем удаляются из нее как конечный продукт флотации — концен- трат. Угольные частицы, снимаемые с пеной, — это второй конечный продукт флотации, они носят название хвостов, которые являются отвальным продуктом. По данным химический состав хвостов флотации следующий
F — 8,8;
- 5,7; Na - 6,7; - 0,7;
- 0,5;
-
-
0,25;
- 0,5; - 72,1.
Процесс флотации ведется во флотационной машине [4], представляющей собой емкость прямоугольного сечения, раз- деленную поперечными перегородками на ряд камер, снабженных импеллерами, вращающимися со скоростью 275— 600 об/мин. Благодаря наличию отверстий в придонной части перегородок уровень пульпы во всех камерах одинаков. Пульпа подается в первую камеру машины и последовательно переходит из одной камеры в другую. Из последней камеры первой
непрерывно самотеком выпускается пульпа, обо- гащенная криолитом, а угольные частицы в виде пены снима- ются гребками с поверхности пульпы в каждой камере в общий желоб. В первой группе камер первой флото- машины проводится основная флотация. Хвосты же основной флотации отправляются на контрольную, которая осуществля- ется в нескольких камерах второй флотомашины. В остальных камерах первой и второй
соединенных последо- вательно, производится перечистка криолита с получением концентрата. После контрольной флотации и дополнительного отделения криолита — промышленного про-
дукта II (ППП) — хвосты увозятся в отвал.
Первичный
концентрат направляется на флотацию, продуктами которой являются промышлен-
ный продукт I
возвращаемый на классификацию, и криолитовый концентрат, который после сгущения, фильтрации и сушки направляется в электролизный цех. Но обычно
пульпа, полученная флотацией угольной пены, сме- шивается с пульпой криолита, и в электро- лизный цех направляется смешанный
Сухой готовый должен содержать F — более 44; — более 12; Na — не более 30; С — 1,5; —
0,9; - 0,5;
- 1,5.
На производство 1 т
расходуется около 1700 кг пены, поэтому на шламовое поле направляется 700 кг хвостов (т.е. примерно 40 % от исходной массы пены), в основном состоящих из углерода, но в которых большую долю занимают компоненты электролита, и в том числе фтористые соединения и смолистые погоны. Если считать, что при
1 т алюминия снимается 50 кг пены, то около 20 кг из нее поступает на шламовое поле. Надо добавить к этому уловленную пыль в мокрых скрубберах, количество которой, по данным, приведенным в разд. 3.4, составляет около 20 кг на 1 т алюминия (для электролизеров
и тогда общее количество и хвостов флотации возрастает до 40 кг на 1 т алюми-
ния. Следовательно, завод производительностью, например, 250 тыс. т алюминия в год направляет на шламовое поле более 10 тыс. т веществ, содержащих углерод, фтористые, смолистые и иные соединения. Понятно, что сооружение и эксплуатация шламового поля относятся к экологическим проблемам про- изводства алюминия.
7.3. Утилизация изношенной футеровки электролизера
Утилизация изношенной футеровки электролизера — большая экологическая проблема вследствие того, что пропитыва- ется
солями и другими компонентами, ко- торые входят в состав электролита. По данным [26], материал ИФЭ содержит около 30 % углерода, 30 % — огнеупоров и
40 % — солей фторидов. Эти сведения лишь приблизительно отражают состав ИФЭ, а фактическое содержание компонентов зависит, конечно, от конкретных заводских условий: параметров работы ванн, конструкции и срока службы футеровки, качества материалов и т.д.
Значительная часть солей, содержащихся в ИФЭ, водораст- воримы и при складировании отходов капитального ремонта ванны на площадках или в отвалах могут выщелачиваться атмосферными осадками и загрязнять водоисточники. С другой стороны, наличие ценных компонентов в ИФЭ ставит задачу их извлечения и утилизации.
Изношенную футеровку можно разделить на две большие части — угольную и огнеупорную. Угольная
по данным [26], в среднем содержит 30 % углерода, 26 — глино- зема, 13 — криолита, 8 — фтористого натрия, 3 — фтористого кальция, 6 — соды, 3 — кварца и 11 % остальных примесей. В состав огнеупорной части футеровки входит % оксида кремния, а остальное приходится приблизительно поровну на глинозем и
соли.
За последнее десятилетие, по данным [26], в наиболее развитых странах (Франция, Норвегия, США, Германия и др.) в связи с переходом на мощные электролизеры с обожженными анодами срок службы ванн возрос более чем в 2 раза и достиг что привело к резкому сокращению количества
Применение же сухой газоочистки отходящих от элект- ролизера газов сократило потребность в криолите, сделало невыгодным его извлечение из отходов футеровки и поэтому снизило внимание исследователей к данной важной проблеме. Только в США запас непереработанных отходов ИФЭ превы- шает 2 млн т и увеличивается на 20 тыс. т ежегодно [26].
В отечественной алюминиевой промышленности, оснащен- ной электролизерами с самообжигающимися анодами с невы- соким выходом по току, низкой анодной плотностью тока и большими расстояниями от анода до борта, срок службы футеровки в среднем составляет
сут) и поэтому удельное количество ИФЭ, приходящееся на 1 т алюминия, значительно (в
раза) превышает зарубежные аналоги. Например, на Новокузнецком алюминиевом заводе она достигает 75 кг на 1 т алюминия и за год общая масса ИФЭ составляет почти 19 тыс. т, и в том числе более половины угольной футеровки. В пересчете на чистый фтор в ИФЭ его содержится около 3 тыс. т, значительная часть которого на- ходится в водорастворимом виде.
В мировой практике извлечение ценного криолита из ИФЭ практиковалось в течение многих лет на различных пред- приятиях [26], общая утилизация ИФЭ зависит от экономич- ности и технологического уровня этого процесса. Существует несколько потенциально экономичных и экологичных способов переработки и повторного применения материалов
электролизеров, но ни один из них не нашел широкого распространения. По мнению ведущих специалистов, в ближай- шие годы следует решающего поворота в области утилизации ИФЭ.
![]() |
Как известно, при капитальном ремонте ИФЭ заливается водой, в результате начинается экзотермическая реакция, иду- щая с выделением большого количества газов. При условии, что ИФЭ содержит алюминий и натрий, между водой и ИФЭ протекают следующие реакции:
Таким образом, при заливке водой выделяются метан
и аммиак
которые не только горючи, но и взрывоопасны, и поэтому ИФЭ следует хранить в хорошо вентилируемых помещениях. Большинство выделяющихся газов
нетоксичны, а аммиак имеет относительно высокую Данное обстоятельство необходимо учитывать при отправке ИФЭ для переработки на других предприятиях.
Существуют различные способы переработки ИФЭ, осно- ванные на ее утилизации в смежных отраслях промышленности или нейтрализации цианидов и водорастворимых фторидов. Имеются также способы извлечения полезных веществ, напри- мер фторидов, и их использования в производстве алюминия.
Основные способы утилизации ИФЭ. По данным 26,
и из накопленного опыта известно несколько способов перера- ботки ИФЭ, основные сведения о которых приводятся ниже.
Процесс Австралийская компания
Ltd" [31] разработала процесс КОМПТОР, предназначенный для разложения цианидов и извлечения фторидов методом кальци- нации отходов. Суть метода разложения цианидов заключается в том, что при подогреве отходов подины до температуры
550 °С в присутствии кислорода и воды соединения разлагаются на
и
Однако при этой температуре еще не происходит агломерации частиц, препятствующей дальнейшему извлечению фторидов. Основным недостатком данного процес- са является необходимость измельчения ИФЭ до размера зерен менее 1 мм, что достаточно трудно. Оставшаяся после кальци- нации зола направляется на извлечение фтора методом выще- лачивания.
Использование ИФЭ при производстве чугуна и стали. Изве- стно, что образование шлака в металлургических агрегатах (мартеновские печи, конвертеры и вагранки) способствует
выводу неметаллических оксидов из металла, а используемый в качестве флюса плавиковый шпат
снижает вязкость и температуру ликвидуса шлака, обеспечивая лучшие условия для плавки чугуна или стали. Однако плавиковый шпат — дефи- цитный и дорогостоящий продукт, а отходы
содержащие значительное количество
и
могут заменить его.
По данным [26], ИФЭ с добавками известняка оказалась хорошим заменителем плавикового шпата при производстве серого чугуна в вагранках. Такие же результаты получены в промышленных дуговых печах. При этом установлено, что уровень выброса цианидов с дымовыми газами не изменился.
Мариупольский металлургический комбинат (Украина) в течение ряда лет использовал угольную футеровку Новокузнец- кого алюминиевого завода при выплавке стали в мартеновском производстве. В настоящее время Западно-Сибирский метал- лургический комбинат перерабатывает десятки тысяч тонн ИФЭ с Братского и Красноярского алюминиевых заводов. Можно считать, что проблема переработки угольной части футеровки практически решена, но на алюминиевых заводах необходимо организовать дробление ИФЭ до размеров менее 60 мм, так как в противном случае возникают непреодолимые трудности при ее дозировке на заводах черной металлургии.
Значительно хуже обстоит дело с переработкой огнеупорной части ИФЭ — в литературе нет примеров ее практической утилизации, имеются лишь ссылки на отдельные попытки ее использования для приготовления шамотной крупки, применя- емой при монтаже электролизеров.
Использование ИФЭ при производстве цемента. Большин- ство печей для производства цемента работает при температуре около 1500 °С и поэтому в них можно сжигать почти любой вид топлива. Поскольку обычно печи работают на угле, часть топлива можно заменить измельченной угольной футеровкой. Лабораторные испытания [26] показали, что можно применять
всю футеровку электролизеров, но при промышленных испы- таниях использовали лишь ее угольную часть. Установлено, что содержание фторида в ИФЭ благоприятствует протеканию реакции образования клинкер-цемента при меньшей темпера- туре; при сжигании ИФЭ практически полностью сгорают фториды и их содержание в трубе незначительно. Однако большое количество натрия в ИФЭ делает невозможным полу-
слабощелочных цементов, а примеси алюминия могут ухудшить качество цемента. Именно эти и некоторые другие соображения заставили многих производителей цемента отка- заться от использования
Сжигание отходов в кипящем слое. Для разрушения циани- дов в ИФЭ и превращения фторидов в невыщелачиваемые вещества [26] наиболее перспективным оказалось сжигание ИФЭ в кипящем слое толщиной 900 мм при температуре 760 °С. Как показали результаты исследований, при такой
температуре сгорает 99,99 % цианидов, 99 % фторидов остается в кипящем слое в невыщелачиваемом виде, а газообразный фтор улавливается рукавным фильтром влажного скруббера. Для реализации этого способа задействовали [26] установку произ- водительностью 10 тыс. т в год, в которой использованы отдель- ные передвижные модули (дробилки, установки для сжигания, лаборатория и
![]() |


При 300 °С разрушается около 99,5 % цианида, содержаще- гося в ИФЭ, а при 400 °С — 99,8 % цианидов в течение часа. В качестве способа утилизации фторида применили обра- ботку ИФЭ серной кислотой с последующей нейтрализацией гидрооксидом кальция и карбонатом кальция. В результате этого большинство соединений превращается в нераст-
воримый фторид кальция. На основании результатов исследо- ваний был сделан вывод о том, что такой процесс утилизации ИФЭ превращает отходы футеровки в материал, стойкий к выветриванию без нарушения требований экологических стан- дартов.
Способ выщелачивания. Выщелоченные отходы прореагиро- вавшей с водой ИФЭ имеют очень разный химический состав
[26] (г/л): фторидов — карбонатов —
цианидов —
натрия — Как правило, перед многими процессами выщелачивания стоит проблема утилизации цианидов, большая часть которых образует
комплексные соединения с железом и с трудом поддается окислению. Извлечение фторидов из отходов по технологии фирмы "ALCOA" считалось слишком невыгодным, поэтому все внимание было сосредоточено на разрушении сложных циани- дов. Наиболее перспективным был признан способ химического окисления под каталитическим действием ультрафиолетовых лучей. Процесс выщелачивания был организован так, чтобы в обработанных отходах содержался несвязанный в комплексных соединениях цианид, который легко окисляется химически. Для этого ИФЭ обрабатывают известью с осаж- дением фторида в виде
и для окисления
цианида. Количество извести превышает
дозу, необходимую для образования а избыток извести идет на снижение уровня фтора и других анионов до требо- ваний
с целью утилизации.
Полагают, что в процессе обработки ИФЭ образуется
твердый остаток, годный для отправки в обычные промышлен- ные отвалы, так как содержание в нем растворимого фторида и цианида отвечает нормам ПДК.
Значительное количество угольной части ИФЭ и практи- чески вся ее огнеупорная часть на заводах как в России, так и в СНГ не утилизируется и вывозится в промышленные отвалы. За каждую тонну твердых отходов взимается плата и, кроме того, надо платить за те площади, которые занимают отвалы и полигоны.
Добавки ИФЭ в аноды или анодную массу. Наличие примесей в ИФЭ препятствует ее использованию в качестве заменителей кокса при производстве обожженных анодов или анодной массы. Эксплуатация опытных анодов с добавкой до 25 % ИФЭ показали, что с увеличением доли ИФЭ расход анодов резко возрастал. Попытки ввести добавки ИФЭ в анод в виде только крупных фракций также оказались безуспешными, поскольку при повышении доли ИФЭ в составе анодов резко повышалась их в токе
и возрастал расход анодов.
Сравнительно успешными были испытания анодов с добав- ками 1,5 % ИФЭ. Это естественно, так как при небольшой доле добавок трудно ожидать явно выраженных изменений, но совершенно очевидно, что организационные трудности превы- сят возможный эффект от утилизации небольшого количества отходов.
Извлечение фтористых соединений из Существуют или прошли промышленные испытания несколько способов извле- чения фтористых соединений — криолита, фтористого алюми- ния и фтористого натрия из ИФЭ.
Способ регенерации криолита. На одном из
заводов в Норвегии [32] отходы ИФЭ подвергают экстракции раствором каустической соды, что приводит к получению углеродного и минерального остатка ИФЭ с очень низким содержанием фторида. Поэтому в экстракт добавляют с целью достижения определенного соотношения F
при этом выделяются силикатные примеси. Криолит осаждают на следу- ющей стадии путем нейтрализации щелочного раствора газом
с получением раствора
возвращаемого на стадию
выщелачивания. Из-за избытка NaF (по отношению к составу криолита) в составе ИФЭ избыток NaOH выделяется на этапе образования каустика. Цианид частично разлагается при про- ведении этого процесса, а остаток удаляется в результате окисления его водорода
![]() |


Термодинамика пирогидролиза даже при высоких темпера- турах неблагоприятна, и реакции могут быть сдвинуты вправо только путем подачи избытка пара в больших количествах. На рис. 7.3 приведена упрощенная схема разработанная фирмами "Кайзер и который идет
при температуре 1200 °С, причем цианиды полностью разруша- ются в реакторе, а образующаяся зола утилизируется эко- логически чистыми способами, так как количество в ней не превышает 0,3
Газообразный фтористый водород охлаждается, и его содер- жание доводится до 25 % в растворе на этапе адсорбции. При
Рис. 7.3. Упрощенная схема процесса
предложенная фирмами "Кайзер и
![]() |


Повышение температуры реактора способствует росту доли в газе реактора, но одновременно увеличивает испарения натрия из При охлаждении отходящего газа происходит
![]() |


которая уменьшает выход HF.
В отличие от предыдущего процесса с невыгодной термодинамикой, фирмой "Мартин
разработан процесс утилизации с помощью
путем впрыскивания в реактор серы или ее со- единений
и т.д.) при сжигании ИФЭ
![]() |
При этом цианиды разрушаются полностью, а термодинамика выгодна даже при более низких температурах.
Существуют и другие способы утилизации и извле- чения фтористых соединений из ИФЭ, краткие сведения о которых приведены в [14,
Таким образом, несмотря на широко распространенные способы извлечения фтористых соединений из растворов газо- очистки и из угольной пены, образуется большое количество и хвостов, которые гидротранспортом отправляются на шламовое поле. Значительная часть ИФЭ (в основном огне- упорная) а иногда и вся футеровка вывозится в промышленный отвал или на полигон для хранения твердых отходов, так как стоимость переработки ИФЭ достигает 400 долларов за 1 т. И шламовое поле, и отвал могут негативно влиять на экологию
производства.
7.4. Устройство и эксплуатация полигонов
Для промышленных отходов
Для централизованного сбора, обезвреживания и захоронения токсичных отходов промышленных предприятий сооружаются полигоны. В соответствии со в составе полигонов должны предусматриваться: завод по обезврежи- ванию отходов, участок захоронения отходов и гараж для специализированного транспорта, перевозящего отходы. Уча- сток захоронения токсичных промышленных отходов представ- ляет собой территорию для размещения специально оборудо- ванных карт или котлованов, в которые складируются ток- сичные твердые отходы I, II и III классов и при необходимости IV класса токсичности (I — чрезвычайно опасные; II — высокоопасные; III — умеренно опасные и IV — малоопасные). Отходы электролизных цехов относятся к II — IV классам. Таким образом, эти требования распространяются и на шламо- вые поля, куда транспортируются газоочистки и хвосты флотации, и на промышленные отвалы, куда вывозятся для последующего захоронения отходы ИФЭ, пыль из электро- фильтров, отходы капитального ремонта баковой аппаратуры и трубопроводов в виде сульфатов.
Полигоны следует размещать на площадках, где можно осуществлять мероприятия и инженерные решения, исключа- ющие загрязнение окружающей среды, ниже мест водозабора, и на участках со слабофильтрующими грунтами и залеганием
грунтовых вод (при их максимальном
не менее 2 от нижнего уровня отходов. Размер участка захоро- нения промышленных отходов устанавливается исходя из срока накопления отходов в течение лет.
Участок захоронения по периметру должен быть огражден колючей проволокой высотой 2,4 м с автоматической охранной сигнализацией. По периметру он должен иметь кольцевой канал, кольцевое обвалование высотой 1,5 и шириной поверху
3 м, кольцевую автодорогу с усовершенствованным капиталь- ным покрытием и въездами на карты, а также
лотки или кюветы с облицовкой бетонными плитами. Дождевые и талые воды следует отводить в специальные пруды, состоящие из двух секций. Чистые воды направляются на производствен- ные нужды, а загрязненные — в пруд-испаритель или на завод для обезвреживания.
Захоронению подлежат твердые токсичные отходы, а способ захоронения зависит от их токсичности и
Отходы разных классов подлежат раздельному захоронению. Размер карты не регламентируется, но он должен обеспечить прием отходов на захоронение в течение не более 2 лет. Отсыпку не растворимых в воде отходов надо производить по принципу "от себя" (от края карты и в глубь участка) и сразу на полную высоту, при этом засыпанный до проектной отметки участок котлована должен сразу покрываться защитным слоем грунта толщиной не менее 0,5 м, по которому осуществляется дальнейший подвоз отходов. После заполнения карты она должна покрываться местным грунтом на высоту не менее 2 м, включая первоначальный защитный слой. Засыпка должна иметь выпуклую поверхность — середина карты должна быть выше краев не менее чем на 1,5 м.
Жидкие негорючие отходы перед захоронением следует обезвоживать и при технической возможности — обезвреживать. При захоронении растворимых в воде отходов II и III классов необходимо предусматривать экран из мятой глины по дну и откосам котлована толщиной не менее 1 м.
Вокруг полигонов для захоронения токсичных промышлен- ных отходов предусматривается зона ши- риной не менее 3000 м.
Приведенные выше требования к полигону для приема, переработки и захоронения отходов свидетельствуют о значи- тельных капиталовложениях на их сооружение, и поэтому
следует принимать все возможные меры по снижению количе- ства отходов и их утилизации. Рассмотрим основные моменты, связанные с эксплуатацией таких сооружений.
Эксплуатация шламового поля. Как было показано в разд.
7.2, газоочистки и хвосты флотации до соотношения ж т
1 и гидротранспортом направ- ляются на шламовое поле. Средний химический состав усред- ненного шлама (по данным следующий F — 21,03;
- 11,74; - 13,85; - 0,80;
- 0,14; - 4,50;
— 0,60;
— 6,68; ram (в основном углерод) — 40,08 и смолистые вещества — 2,46. Остальное — незначительные содержания ванадия, и лития.
По всему периметру шламового поля уложен трубопровод, по которому транспортируется пульпа, и ее выход на поле предусмотрен во многих точках. Задача эксплуатационного персонала заключается в том, чтобы постоянно, изменяя точки слива пульпы, создавать пляжи, примыкающие к телу дамбы, и тем самым предотвращать возможный прорыв жидкости через дамбу. Поступившая пульпа отстаивается, а жидкость стекает через колодец и насосами возвращается в производ- ство для приготовления содового раствора. Количество такой
воды достигает
на 1 т алюминия.
По мере накопления шлама он подлежит захоронению, так как неоднократные исследования, показавшие принципиальную возможность его применения для нужд черной металлургии и строительной индустрии, не завершились такой технологии в производство на заводах России. Необходимо постоянно вести отсыпку заполненных шламовых полей, по- скольку пыль, которую может разносить ветер, весьма токсична. Эксплуатация полигона для твердых отходов. Практически место расположения полигона для захоронения твердых отходов может находиться далеко от шламового поля, и зависит это от
местных условий.
Основная задача при эксплуатации полигона заключается в надзоре за состоянием ограждающих полигон дамб и своевре- менном их ремонте. Одной из основных задач является посто- янное захоронение уже отсыпанного слоя в соответствии с требованиями Полигон, как правило, ограждают, и выполняют необходимое освещение, а въезд на него осущест- вляется по пропускам круглые сутки во избежание заполнения бытовыми отходами других предприятий.
8
![]() |
И ОТВЕДЕНИЕ СТОЧНЫХ ВОД
Известно, что в результате влияния человеческого фактора и его техногенной деятельности на биосферу (атмосферу, воду, сушу) возможно нарушение взаимосвязи живого мира и окру- жающей среды. Это в полной мере относится к технологии водоснабжения и Строительство, реконструк- ция и эксплуатация систем водоснабжения и сопутствующих им сооружений должны осуществляться с учетом перспективного развития водопользователя и его влияния на окружающую среду, и в том числе на водную. Проектирование очистных сооружений должно основываться на взаимосвязи между соо- ружением, водопользователем и водной средой.
Для каждого гидротехнического сооружения (водоприемные устройства, водопроводные сооружения и водоводы) должны предусматриваться зоны санитарной охраны. При сбросе в реки производственных сточных вод, содержащих вредные вещества, необходимо учитывать возможность их разбавления речной водой до концентрации, при которой можно использовать воду для хозяйственно-питьевого водоснабжения и не наносить ущерб рыбному хозяйству.
Несмотря на огромные запасы всей воды на земле — 1500 млн — доля воды, которую человечество может применять для удовлетворения своих физиологических, бытовых и производственных нужд, составляет всего 2,53
причем доля
озерной и речной воды, на использование которой сейчас главным образом и сориентировано человечество, составляет соответственно 0,007 и 0,0002 Поэтому в ряде регионов страны наличие воды является определяющим фактором раз- вития общества и не случайно правительство принимает жесткие меры законодательного характера по охране и рациональному использованию водных ресурсов.
Цветная металлургия потребляет ежегодно до 10 млрд воды, и ее доля в балансе
страны составляет
10 Алюминиевая промышленность (включая добычу руд, производство глинозема и фтористых солей, электролиз крио- лит-глиноземных расплавов и т. д.) ежегодно расходует 1652 млн
воды, т.е. более 16 % от потребности цветной металлургии, и при этом сброс сточных вод достигает 289 млн
[33].
Однако собственно производство алюминия электролити- ческим способом не требует расхода воды, а все вспомогатель- ные производства потребляют ее сравнительно немного.
Вопросы водоснабжения и особенности очистки стоков от производства алюминия весьма сложны и специфичны, и поэтому в данном пособии приводятся лишь основные све- дения, а более детальные данные можно найти в [33, 34].
Водоснабжение
Системой водоснабжения называется комплекс инженерных сооружений и устройств, предназначенных для забора воды из природных источников (рек, озер, водохранилищ, морей и/или подземных вод), улучшения ее качества до заданных норм, транспортировки, хранения, подачи и распределения по пот- ребителям. Как правило, большинство алюминиевых заводов имеет собственные насосные станции, которые обеспечивают хозяйственные, производственные и противопожарные нужды. Питьевое снабжение завода может быть выполнено от город- ского водоисточника и/или от собственных артезианских сква- жин. По характеру использования воды на заводах существуют прямоточные системы, в которых воду после однократного использования очищают и сбрасывают в водоемы, и/или обо- ротные, в которых воду после использования для технических целей очищают, охлаждают и затем многократно потребляют на те же нужды.
Расход воды на среднем по производительности алюми-
ниевом заводе в зависимости от времени года может достигать тыс.
или до млн
Стоимость техничес-
кой воды в ценах 1996 г. достигает или затраты на водоснабжение могут составить до млрд
Именно поэтому на заводах разрабатываются и реализуются технические и организационные меры, связанные с сокра- щением
За последние десятилетия удельное потребление воды на алюминиевых заводах постоянно изменялось. С одной стороны, внедрялись мероприятия, снижающие
(пере- вод преобразовательных подстанций с ртутных выпрямителей на кремниевые
увеличение доли прокаленного кокса при производстве анодной массы и обожженных анодов, приме- нение сухой газоочистки отходящих газов от электролизеров и т.
а с другой — проводились мероприятия, которые требовали дополнительного расхода воды (строительство на ряде заводов систем мокрой очистки отходящих газов, увеличение доли выпуска слитков и
Кроме того, с целью снижения потребления технической воды и уменьшения сброса вредных веществ в водоемы на заводах сооружались локальные
системы и даже внедрялись бессточные схемы водоснаб-
жения, которые почти полностью исключали потребление све- жей технической воды.
Технология электролиза алюминия не допускает перерывов в подаче тока, а электроснабжение может быть надежным в том случае, если будет обеспечена непрерывная подача воды для охлаждения выпрямителей. Поэтому водоснабжение алюмини- евого завода всегда осуществляется не менее чем из двух водоисточников.
Основными потребителями производственной воды на алю- миниевом заводе (если на нем отсутствует производство глино- зема) являются:
— литейное производство электролизного цеха, где вода используется для охлаждения слитков, отливаемых полунепре- рывным способом, катанки и изредка чушек, отливаемых на конвейерах. Количество используемой воды зависит от количе- ства и ассортимента выпускаемой продукции, но расход воды относительно велик и составляет
на 1 т отливаемых слитков, так как перепад температуры воды на входе и выходе из литейной машины крайне невелик и не превышает не- скольких градусов;
—
системы мокрой очистки газов, отходящих от элект- ролизеров. Вода употребляется для приготовления содовых растворов, компенсации из и выведения
шлама из растворов газоочистки. В системах сухой очистки газов вода не используется;
— производство вторичного криолита методом регенерации растворов газоочистки и флотации угольной пены. Вода приме- няется в ходе приготовления раствора, промывки
криолита, отходов его про- изводства и хвостов флотации и перекачки их на шламовое поле;
—
процесс охлаждения сжатого воздуха в компрессорном отделении и диодов на КПП. правило, охлаждение хо- лодильников компрессоров и диодов в блоках выпрямителей на КПП осуществляется дистиллированной водой, которая охлаж- дается в теплообменниках проточной технической водой и которая при этом не загрязняется, а только нагревается;
— система охлаждения холодильников и полученных брике- тов анодной массы (при наличии на заводе цеха анодной
—
![]() |
другие потребители (мытье железнодорожных вагонов и автомашин, поливка территории завода, строительные работы, заливка катодов ванн, отключенных для капитального ремонта,
Помимо производственного водоснабжения на заводе име- ются системы хозяйственного (стирка спецодежды, душевые для обслуживающего персонала, противопожарные системы и др.) и питьевого.
Рассмотрим подробнее особенности водопользователей на алюминиевом заводе. Одним из основных потребителей воды являются литейные отделения, в которых вода расходуется на охлаждение слитков, получаемых на машинах полунепрерывно- го литья, и катанки, производимой на станах непрерывной прокатки. В летнее время иногда приходится применять воду для охлаждения конвейеров при литье чушек. Использованная для охлаждения вода не только нагревается, но и загрязняется механическими примесями (асбестовый шнур, огнеупорная гли- на, производственный мусор и а также остатками жировой смазки, применяемой при литье слитков и катанки. Поэтому отработанная вода сливается в систему промышленных стоков или поступает в
систему, где очищается, охлаж- дается и вновь подается в литейное отделение; схемы оборот- ного водоснабжения рассмотрены ниже.
Значительное количество воды расходуется в системах мок- рой очистки отходящих газов, технология работы которых представлена в разд. 6.3. Использование отработанного содово- го раствора для варки криолита, и вывод шлама из скрубберов приводят к необходимости пополнить систему тех- нической водой.
Потребители значительного количества технической воды
— компрессорные отделения, цех анодной массы для охлаж- дения кокса в холодильниках и КПП. Как было указано выше, техническая вода на перечисленных производствах не загрязня- ется, а лишь нагревается, и поэтому весьма рационально применять для снабжения указанных потребителей системы оборотного водоснабжения.
Общие принципы организации систем оборотного водо- снабжения заключаются в разработке требований к качеству используемой воды, норм
и и в составлении материального баланса, причем надо исходить из принципа, что качество воды не должно ухудшать технологию и качество выпускаемой продукции.
Вода, используемая для охлаждения анодной массы, загряз- няется маслом и кусочками анодной массы и направляется в промышленные стоки или систему оборотного водоснабжения завода.
Таким образом, техническая вода на заводе употребляется для различных целей и качество использованной воды резко различается у различных потребителей. С точки зрения расхода воды и улучшения экологии водных источников необходимо сооружать оборотные системы водоснабжения. Затраты на осуществление этого мероприятия достаточно велики. В тех случаях, когда необходимо снижение температуры оборотной воды, следует применять локальные системы: для литейного отделения, для КПП и компрессорной станции, для цеха анодной массы и т. д.
Рассмотрим основные типы охладителей оборотной воды, которые используются в производстве [34].
бассейны оборудуют системой специальных сопел, через которые разбрызгивается подлежащая охлаждению вода. Бассейны сооружаются из бетона или камня с устройством гидроизоляционного экрана и состоят не менее, чем из двух секций, глубиной не менее 1,7 и шириной не более 50 а
разбрызгивающие сопла устанавливаются на расстоянии на высоте
Факелы разбрызгивания смежных сопел должны перекрывать всю площадь бассейна. Днища бассейна имеют уклон в сторону приямка с грязевой трубой.
Размеры
бассейна рассчитывают с помощью специальных номограмм, но ориентировочно его площадь мож- но определить по удельной тепловой нагрузке
Норму допустимой нагрузки выбирают в зависимости от климатических условий.
бассейны сооружают для охлаждения чистой технической воды, которая в процессе ее использования только нагревается и не загрязняется какими-либо примесями, так как в противном случае могут возникнуть проблемы с забивкой этих устройств. Кроме того,
бассейны требуют больших площадей и в настоящее время сооружаются весьма редко.
Башенные градирни представляют собой оболочку в виде прямого усеченного (малые градирни) или гиперболической формы (большие) конуса, вверху открытого, внутри оборудо- ванного оросительными устройствами и установленного над сборным резервуаром. Такие градирни применяют в системах оборотного водоснабжения, требующих устойчивого охлаж- дения воды до температуры °С. Они экономичны, по- скольку не требуют затрат дополнительной энергии на охлаждение воды и сооружаются в стесненных условиях уже за-
строенной территории. Удельная тепловая нагрузка для этих градирен составляет
ч). Башенные градирни нашли широкое применение на тепловых электростанциях.
Вентиляторные градирни рационально размещать на пло- щадках производственных предприятий, поскольку они меньше размерами в плане и по высоте, чем башенные. Их применяют для получения устойчивого и глубокого охлаждения воды и оперативного регулирования ее температуры. Много- секционные вентиляторные градирни устраивают с пленоч- ными, капельными и оросителями с площадью
орошения одной секции от 2 до 400 При необходимости перед градирней могут устраиваться специальные отстойники для очистки воды от масла и примесей, которыми загрязняется вода, например, в литейных отделениях. Удельная тепловая нагрузка для градирен такого типа принимается равной
Дж/ (ч и более.
Сравнение этих типов охладителей воды показывает, что предпочтение следует отдать вентиляторным градирням благо- даря их небольшим размерам и глубокому охлаждению воды. Опыт работы алюминиевых заводов также показал высокую надежность и эффективность вентиляторных градирен.
Однако на ряде алюминиевых заводов локальные системы не нашли широкого применения и там эксплуатируются систе- мы с использованием прудов-охладителей.
или водохранилища сооружают в случае невысоких требований к эффекту охлаждения воды, при нали- чии свободных земельных площадей, благоприятного релье- фа местности для создания водоема вблизи завода или возмож- ности использования водохранилища, построенного для других целей. На рис. 8.1 приведена одна из возможных схем оборот- ного водоснабжения с помощью водохранилища, сооруженного на реке.
размещают независимо от наличия реки, но предусматривают возможность сброса излишка воды в какой-либо водоем. Удельная тепловая нагрузка для прудов-
охладителей принимается равной
т.е. в раз меньше, чем у вентиляторных градирен, поэтому сооружают не только для охлаждения воды,
но и для ее очистки различными методами.
Эксплуатация систем оборотного водоснабжения, связанная даже с частичным сбросом подогретой воды, оказывает влияние не только на тепловой режим водоемов, но и на обитающих в нем представителей флоры и фауны. В результате происходит интенсивное цветение водоемов, развиваются различного рода
![]() |
Рис. 8.1. Схема оборотного водоснабжения с применением
1 — река; 2 — сброс горячей воды; 3 — откос нижнего бьефа плотины; 4 — плотина; 5 — пруд-охладитель; 6 — дамба; 7 — насосная станция; 8 — 9 —
Водозабор
водоросли, которыми обрастают трубопроводы и детали охла- дительных устройств. Эффективная борьба с этим явлением ведется успешно с помощью медного купороса, который вводят в отработанную воду, поступающую в пруд, из расчета 0,4— 2,0 на весь объем воды. Обработку же воды в водо- хранилище производят распылением измельченного медного купороса по поверхности воды. Применяют также различ- ные меры борьбы с последствиями сброса теплой воды в
— развитием мидий и других представителей гидрофауны, а также с отложениями карбонатов и другими осложнениями в работе прудов [34].
Качество используемой воды постоянно контролируется лабораторией завода, и при отклонении от нормы принимаются соответствующие меры. Следует отметить, что потребители технической воды на алюминиевых заводах не предъявляют жестких требований к химическому составу воды и в основном лимитируют содержание взвешенных частиц.
Характерной особенностью алюминиевого завода является наличие на заводской площадке, а иногда и за ее пределами блуждающих токов, источники которых — несовершенство элек- троизоляции катодных кожухов электролизеров и ошиновки, особенно в одноэтажных корпусах. При попадании трубопровода в зону действия блуждающих токов в последних наблюдается процесс электрохимической коррозии с образованием свищей, что приводит не только к потере воды, но и обводнению территории завода. С одной стороны, это еще больше способствует увеличению токов утечки, а с другой — увеличивает количество дренажных вод, которые поступают в промышленные стоки. В связи с изложенным вопросам изоляции трубопроводов (вне зависимости от вида транспортируемого вещества — газ, вода, пар, воздух и в пределах завода должно уделяться повышенное внимание и при необходимости трубопроводы должны снабжаться протекторной или катодной защитой. Однако радикальным сред- ством борьбы с негативными последствиями токов утечки является прокладка трубопроводов по надземным эстакадам.
82. Отведение сточных вод
Учитывая дефицит пресной воды, причины которого изложены основные направления по охране и рациональному
использованию воды можно сформулировать следующим обра- зом. С одной стороны, это мероприятия, направленные на снижение потребления свежей воды, а с другой — на сокра- щение сброса отработанной воды в водоемы, что ведет к их загрязнению.
К первой группе относятся мероприятия, которые способ- ствуют снижению
за счет повторного исполь- зования сточных вод, сооружения локальных систем оборотного водоснабжения, замены воды другими средами и разработки безводных технологий. Для производства алюминия элект- ролизом расплавов к этой группе ме- роприятий в первую очередь относится внедрение сухой очистки газов, которая является безводной, а также создание оборотных систем водоснабжения КПП, литейного отделения электролиз- ного цеха, компрессорной станции, систем охлаждения хо- лодильников печей в цехах анодной массы и обожженных анодов.
Вторая группа включает такие мероприятия, как сокра-
щение расхода реагентов, замену их менее токсичными, а также совершенствование техники и технологии очистки сточных вод
Ввод в действие систем оборотного водоснабжения позволил обеспечить в среднем по отрасли оборот воды в размере более 85 % от потребности, что дало возможность резко снизить сброс загрязненных стоков в поверхностные водоисточники. Резуль- таты расчетов показывают, что фондоемкость сооружений очис- тки и последующего сброса воды почти в 4 раза выше, чем у систем оборотного водоснабжения [33].
При разработке схем оборотного водоснабжения цеха или завода составляют баланс воды и потоков минеральных и органических загрязнителей для отдельных переделов, а затем с учетом количественных и качественных показателей образу- ющихся стоков определяют возможность их использования и необходимые для этого коммуникативные решения, а также технологию очистки. В настоящее время при разработке систем необходимо предусматривать сбор талых и ливне- вых вод и последующую их очистку с целью использования в производстве.
Применение талых и ливневых вод для водоснабжения алюминиевого завода возможно, если после их очистки на поверхности аппаратов не будут образовываться
солевые, биологические и механические отложения и не будет происходить коррозия металла. В противном случае необходимо применять специальные меры по доведению оборотной воды до требуемых норм, сведения о которых можно найти в [35].
Объем талых и ливневых вод на алюминиевых заводах достаточно велик, так как территория, занимаемая заводом, в зависимости от количества корпусов составляет га. Кроме того, из-за особенностей электролитического производства алюминия
выделение пыли по всему перимет- ру корпуса, огромная площадь кровли корпусов, на которой скапливается пыль и
территория завода засоряется большим количеством токсичной пыли (фтористые соли), которая смыва- ется атмосферными осадками и попадает в
соо- ружения или промышленные стоки. Небольшая часть этих примесей растворяется в воде, а остальные оседают в виде осадка в или уходят с промышленными стоками.
Положение еще больше усугубляется на тех заводах, кото- рые сооружены на площадках с высоким уровнем грунтовых вод. В теплое время года, и особенно в паводковые периоды, резко увеличивается поступление грунтовых вод в дренажи, которые приходится откачивать в систему Грун- товые воды содержат большое количество растворенных солей (магниевых, кальциевых, сульфатов и взвешенных
за которые приходится платить.
Наличие вредных соединений приводит к необходимости сооружения систем во избежание оплаты огром- ных средств за загрязнение водоемов. Например, Новокузнец- кому алюминиевому заводу, который имеет систему водооборота на одной из двух своих производственных площадок, прихо- дится платить за сбросы вредных веществ в водоемы более 600 млн руб. в год (в ценах 1996
или около 2,5 тыс. руб. на
1 т произведенного алюминия.
Из большого арсенала средств, применяемых для кондицио- нирования оборотной воды (нейтрализация, флотация, филь- трация), на алюминиевых заводах нашел применение практически только метод отстаивания в
из которых вода, очищенная от механических примесей (листва деревьев, кусочки древесины и др.), нефтепродуктов и взве- шенных частиц, попадает в где окончательно отстаивается и охлаждается.
9
Дата добавления: 2022-01-22; просмотров: 23; Мы поможем в написании вашей работы! |
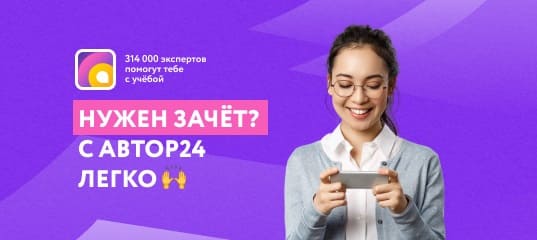
Мы поможем в написании ваших работ!