Факторы, влияющие на прокаливаемость
Глубина закаленного слоя обусловлена соотношением критической и фактической скоростей охлаждения. Критическая скорость определяется положением С-кривых (в зависимости от количества углерода и легирующих элементов в стали) и, следовательно, зависит от факторов, влияющих на устойчивость переохлажденного аустенита.
Существенное влияние на прокаливаемость также оказывают:
1) исходная структура (чем она дисперснее, тем легче и быстрее протекают процессы превращений и гомогенизации, тем прокаливаемость выше);
2) температура нагрева. Чем выше температура нагрева, тем выше гомогенность аустенита, больше величина зерна; а в заэвтектоидных сталях чем выше температура неполной закалки, тем больше содержание углерода и легирующих элементов в аустените, и в итоге прокаливаемость выше.
Фактическая скорость охлаждения зависит от:
1) закалочной среды (с повышением скорости охлаждения прокаливаемость увеличивается);
2) размера и формы изделия.
Для определения глубины прокаливаемости разработаны специальные методы. Один из них – метод торцевой закалки (ГОСТ 5657 Сталь. Метод испытания на прокаливаемость).
Образец стандартных размеров нагревают в печи до строго определенной температуры (углеродистую, марганцовистую, хромистую стали – 900°С) с применением мер, предотвращающих обезуглероживание, в течение определенного времени (30 мин). Нагретый до заданной температуры образец охлаждают водой с торца на специальной установке. После охлаждения измеряют твердость по длине (высоте) образца.
|
|
При торцевой закалке образец охлаждается со скоростью постепенно уменьшающейся по мере удаления от торца. Расстояние, на которое распространяется закалка по длине образца (до твердости полумартенситной зоны), является при торцевом методе мерой прокаливаемости. Затем с помощью специальных номограмм определяют соответствующий диаметр образца, прокаливающийся насквозь. Прокаливаемость даже одной и той же марки стали может колебаться в значительных пределах в зависимости от изменений химического состава и других факторов. Кривые прокаливаемости разных плавок одной и той же марки стали (с учетом колебания химического состава в пределах марки), построенные опытным путем на большом количестве проб, объединяются в полосы прокаливаемости.
Выбор оптимальной глубины прокаливаемости
Полосы прокаливаемости используются конструкторами при выборе марки стали для изделия определенного размера. Однако конструктор не должен требовать излишней глубины прокаливаемости сверх действительно необходимой.
Для тех изделий, которые в основном подвергаются действию изгиба и кручения, напряжения достигают максимума на поверхности изделия и постепенно снижаются к сердцевине до нуля. В этом случае, как показывает опыт, достаточно иметь слой с 90% мартенсита глубиной не менее ¼ радиуса изделия, для наиболее ответственных изделий – до ½ радиуса. Только для деталей, работающих, в основном, на растяжение (например, шатуны, болты) или подвергающихся упругим деформациям (рессоры, пружины), требуется получить сквозную прокаливаемость.
|
|
Отпуск стали
Отпуск заключается в нагреве закаленной стали до температуры ни- же Ac1, выдержке при заданной температуре и последующем охлаждении с любой скоростью.
Сущность процесса отпуска – распад пересыщенного твердого рас- твора на феррито-цементитную смесь.
Отпуск является окончательной операцией термической обработки, в результате которого сталь получает требуемые механические свойства. Кроме того, отпуск полностью или частично устраняет внутренние напряжения, возникающие при закалке. Эти напряжения снимаются тем полнее, чем выше температура отпуска. Так, осевые напряжения в цилин- дрическом образце из стали, содержащей 0,3%С, в результате отпуска при 550°С уменьшаются с 600 до 80 МПа.
|
|
Наиболее интенсивно напряжения снижаются в результате выдержки при 600°С в течение 15-30мин. После выдержки в течение 1,5ч напряже- ния снижаются до минимальной величины, которая может быть достигну- та отпуском при данной температуре.
Таким образом, назначение отпуска заключается в следующем:
1) снятие закалочных напряжений;
2) получение требуемого комплекса свойств в зависимости от условий работы изделия;
3) стабилизация размеров и свойств.
Скорость охлаждения после отпуска оказывает большое влияние на величину остаточных напряжений. Чем медленнее охлаждение, тем мень- ше остаточные напряжения. Быстрое охлаждение в воде от 600°С создает новые тепловые напряжения. Охлаждение после отпуска на воздухе дает напряжения на поверхности изделия в 7 раз меньшие, а в масле в 2,5 раза
меньшие по сравнению с напряжениями при охлаждении в воде. По этой причине изделия сложной формы во избежание их коробления после от- пуска при высоких температурах следует охлаждать медленно, а изделия из легированных сталей, склонных к обратимой отпускной хрупкости, по- сле отпуска при 500-650°С во всех случаях следует охлаждать быстро.
Основное влияние на свойства стали оказывает температура отпуска. Различают следующие три вида отпуска.
|
|
Низкотемпературный (низкий) отпуск проводят при температу- рах 100-300 °С. При этом снижаются закалочные макронапряжения, мар- тенсит закалки переводится в отпущенный мартенсит (неоднородный пересыщенный твердый раствор углерода в α-Fe) , повышается прочность и немного улучшается вязкость без заметного снижения твердости. Зака- ленная сталь (0,6-1,3%С) после низкого отпуска сохраняет твердость в пределах 58-63HRC, а, следовательно, высокую износостойкость. Однако такое изделие (если оно не имеет вязкой сердцевины) не выдерживает значительных динамических нагрузок.
Низкотемпературному отпуску подвергают режущий и мерительный инструмент из углеродистых и низколегированных сталей, а также детали, претерпевшие поверхностную закалку, цементацию, цианирование или нитроцементацию. Продолжительность отпуска составляет обычно 1-2,5ч, а для изделий больших сечений и измерительных инструментов назнача- ют более длительный отпуск.
Среднетемпературный (средний) отпуск выполняют при 350- 500°С и применяют главным образом для пружин и рессор, а также для штампов. Такой отпуск обеспечивает высокие пределы упругости и выносливости и релаксационную стойкость. Структура стали после среднего отпуска – троостит отпуска; твердость стали 40-50HRC. Температуру отпуска надо выбирать таким образом, чтобы не вызвать необратимой отпускной хрупкости.
Охлаждение после отпуска при 400-450 °С следует проводить в воде, что способствует образованию на поверхности сжимающих остаточных напряжений, которые увеличивают предел выносливости пружин.
Высокотемпературный (высокий) отпуск проводят при 500-680°С. Структура стали после высокого отпуска – сорбит отпуска. И сорбит и троостит отпуска – феррито-цементитные смеси зернистой формы, отли- чающиеся степенью дисперсности. Высокий отпуск создает наилучшее соотношение прочности и вязкости стали.
Закалка с высоким отпуском (по сравнению с нормализацией или от- жигом) весьма сильно одновременно повышает временное сопротивление, предел текучести, относительное сужение и особенно ударную вязкость.
Термическую обработку, состоящую из закалки и высокого отпуска, называют улучшением.
Улучшению подвергают среднеуглеродистые (0,3-0,5%С) кон- струкционные стали, к которым предъявляются высокие требования по пределу выносливости и ударной вязкости. Улучшение значительно по- вышает конструктивную прочность стали, уменьшая чувствительность к концентраторам напряжений, увеличивая работу развития трещин и сни- жая температуру порога хладноломкости. Однако износостойкость улуч- шенной стали вследствие ее пониженной твердости невысокая. Отпуск при 550-600 °С в течение 1-2 ч почти полностью снимает остаточные напря- жения, возникшие при закалке. Длительность высокого отпуска составляет 1,0-6 ч в зависимости от габаритов изделия. Иногда ее увеличивают до не- скольких десятков часов, чтобы снизить опасность возникновения флокенов.
Дата добавления: 2021-12-10; просмотров: 22; Мы поможем в написании вашей работы! |
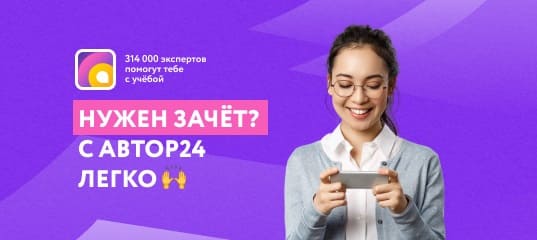
Мы поможем в написании ваших работ!