Основные операции термообработки
Общие положения
Термообработка (ТО)– это процесс теплового воздействия на металл и охлаждения с различными скоростями с целью изменения структуры и свойств в заданном направлении.
Назначение термообработки (ТО)
По назначению все операции термообработки делятся на две группы: предварительную (ПТО) и окончательную (ОТО).
Назначение ПТО:
1) устранение дефектов микроструктуры после горячих видов обработки (литья, ГПД);
2) придание требуемых технологических свойств (обрабатываемости резанием, деформируемости при ХПД);
3) повышение точности изготовления изделий;
4) подготовка структуры к ОТО.
Основными операциями ПТО являются: отжиг, нормализация, улучшение.
Назначение ОТО – придание требуемых эксплуатационных свойств готовому по конфигурации изделию. Основными операциями ОТО являются закалка + отпуск (в качестве ОТО малоуглеродистых сталей в ряде случаев возможно использование нормализации).
Основными видами термической обработки, различно изменяющими структуру и свойства стали и назначаемыми в зависимости от требований, предъявляемых к полуфабрикатам и готовым изделиям, являются отжиг, нормализация, закалка с отпуском.
Принципиальная возможность проведения операций термообработки в сталях (кроме отжига I рода) основана на фазовых превращениях в твердом состоянии.
К отжигам I рода относятся операции ТО, результат которых не зависит от фазовых превращений. Главным процессом является переведение стали из неравновесного состояния, полученного в результате предшествующей обработки, в более стабильное, равновесное состояние. В зависимости от того, какие отклонения от равновесного состояния устраняются, различают следующие разновидности отжига I рода: гомогенизационный (диффузионный), рекристаллизационный и отжиг для снятия напряжений.
|
|
Гомогенизационный отжиг применяют для слитков или отливок из легированной стали с целью уменьшения дендритной ликвации. Нагрев при диффузионном отжиге должен быть высоким (1100-1200°С), так как только в этом случае протекают диффузионные процессы, необходимые для выравнивания химсостава в отдельных объемах стали. Таким образом, фазовые превращения при этом отжиге присутствуют, но они являются попутными, так как основной процесс – диффузия.
Рекристаллизационный отжиг – это операция термообработки, где главным процессом является рекристаллизация. Рекристаллизация – процесс замены вытянутых зерен с искаженной решеткой равноосными зернами той же фазы с более совершенной решеткой, разделенными высокоугловыми границами. Цель отжига – устранение наклепа и повышение пластичности. Этот вид отжига применяют как промежуточную операцию термообработки, а в некоторых случаях и как окончательную. Температура рекристаллизационного отжига зависит от состава стали и чаще всего находится в пределах 650-760°С.
|
|
Отжиг для снятия напряжений используют для отливок, сварных изделий, деталей после обработки резанием и др., в которых в процессе предшествующих технологических операций из-за неравномерного охлаждения, неоднородной пластической деформации и т.п. возникли остаточные напряжения. Остаточные напряжения могут вызвать изменение размеров, коробление изделия в процессе его обработки, эксплуатации и хранения. Отжиг проводят при 160-700°С с последующим медленным охлаждением (например, температура отжига для снятия шлифовочных напряжений составляет 160-170°С, сварочных – 650-700°С).
Таким образом, фазовые превращения при отжигах I рода не являются главным процессом, они могут протекать лишь как попутные.
В данной работе рассматриваются операции термообработки, результат которых зависит от фазовых превращений.
Температурный режим этих операций определяется критическими точками – температурами начала и конца фазовых превращений Ас1, Ас3, Асm.
|
|
Ещё один основной параметр термообработки – время нагрева. Общее время нагрева складывается из времени нагрева до заданной температуры (tн) и времени выдержки при этой температуре (tв), необходимого для выравнивания температуры и химического состава по сечению изделия. Следовательно:
tобщ=tн+tв.
Величина tн зависит от нагревающей способности среды, от размеров и формы деталей, от их укладки в печи; tв зависит от скорости фазовых превращений, которая определяется степенью перегрева выше критической точки и дисперсностью структуры.
Ориентировочно для углеродистой стали tн принимается равным 1 мин на 1 мм сечения; для легированной – 1,5-2 минуты на 1 мм сечения, а время выдержки tв рассчитывается как 0,25×tн.
Кроме температуры и времени, немаловажную роль при термообработке играет скорость охлаждения, так как она определяет окончательную структуру стали.
Формирование структуры при охлаждении характеризуется диаграммами изотермического превращения аустенита (ДИПА или, как их еще называют, С-кривыми). На них накладываются лучи скоростей охлаждения при различных операциях термообработки и анализируются превращения, определяются структуры. Схематическое изображение С- кривой для эвтектоидной стали представлено на рис. 1.
|
|
![]() |
Рис. 1. Диаграмма изотермического пре- вращения аустенита эвтектоидной стали
Из рис.1. видно, что превращение при непрерывном охлаждении происходит в интервале температур. Для каждой скорости охлаждения имеется температура начала (𝑡н ) и конца превращения (𝑡к ). Чем больше скорость охлаждения, тем в область более низких температур сдвигается превращение, то есть достигаются все большие степени переохлаждения, а от степени переохлаждения зависит дисперсность структуры.
Следовательно, при небольшой скорости охлаждения v1 (например, охлаждение с печью) образуется перлит (П), при бóльшей v2 (на воздухе) – сорбит (С) и еще большей v3 (в струе воздуха) – троостит (Т). Бейнит при непрерывном охлаждении углеродистой стали обычно не образуется.
При очень большой скорости охлаждения v5 (например, в воде) перлитный распад аустенита становится вообще невозможным и тогда аустенит переохлаждается до точки Мн и превращается в мартенсит. Превращение аустенита в мартенсит не идет до конца, поэтому в закаленной стали, наряду с мартенситом, всегда присутствует в некотором количестве остаточный аустенит. Минимальная скорость охлаждения vк, при кото- рой подавляется распад аустенита и
обеспечивается структура мартенсита, называется критической скоростью закалки.
Если охлаждать со скоростью, немного меньшей критической v4, то аустенит частично превратится в верхнем районе температур, и структура будет смешанной (рис.2):
кроме мартенсита и аустенита (светлой составляющей на микрошлифе) будут присутствовать ещё и троостит с бейнитом (темная составляющая).
Рис. 2. Структура стали после ча- стичной закалки (мартенсит + сет- ка троостита)
Основные операции термообработки
Отжиг II рода
Отжиг II рода заключается в нагреве стали до температур выше критических точек Ас3 или Ас1, выдержке и последующем медленном охлаждении (с печью). В результате при отжиге протекают фазовые превращения, приводящие сталь практически к равновесному структурному состоянию. Структуры после отжига: феррит и перлит в доэвтектоидной стали; перлит в эвтектоидной стали, перлит и цементит вторичный в заэвтектоидной.
Назначение отжига:
1) исправление дефектов микроструктуры (крупного зерна, строчечности, видманштеттовой структуры);
2) максимальное снижение твердости, повышение пластичности, вязкости для улучшения обрабатываемости резанием, деформируемости сталей.
Место отжига в технологическом цикле – после горячих видов обработки, перед холодной механической обработкой.
Разновидности отжига.
В зависимости от полноты превращения исходной структуры в аустенит различают следующие виды отжига: полный, где вся структура участвует в превращении (температура нагрева Ас3+30…50°С), и неполный, нагрев в этом случае производится в двухфазную область (температура отжига составляет Ас1+30…50°С).
Полный отжиг применяется только для доэвтектоидных сталей, в заэвтектоидных сталях не используется, так как при медленном охлаждении после нагрева выше Аcm образуется грубая сетка цементита.
Неполный отжиг используется для до- и заэвтектоидных сталей, если в них нет дефектов строения избыточной фазы, устранение которых требует полной фазовой перекристаллизации. В основном неполный отжиг применяется для смягчения сталей за счет уменьшения степени дисперсности перлита и попутного снятия напряжений. По сравнению с полным он более экономичен – за счет более низкой температуры нагрева, следовательно, меньшей потери времени при охлаждении, меньшего окисления и обезуглероживания, сокращения затрат на электроэнергию.
По условиям охлаждения различают: отжиг с непрерывным охлаждением и изотермический отжиг.
Скорость охлаждения при отжиге зависит от устойчивости переохлажденного аустенита, и, следовательно, от состава стали. Чем больше устойчивость аустенита в области температур перлитного превращения, тем медленнее должно быть охлаждение. Поэтому легированные стали, обладающие высокой устойчивостью переохлажденного аустенита, охлаждают значительно медленнее (10-100°С/час), чем углеродистые (150- 200°С/час). Для уменьшения длительности охлаждения, особенно в легированных сталях, и получения более однородной
структуры используют изотермический отжиг (рис.3). Он заключается в нагреве стали до температур Ас3+50…70° (для повышения устойчивости
Рис. 3. Диаграмма изотер- мического отжига легированной доэвтектоидной стали
аустенита) и быстром охлаждении (обычно переносом в другую печь) до температуры, лежащей ниже Ас1 на 100-150°С, выдержке при этой температуре до полного завершения превращения и последующего охлаждения на воздухе. Изотермическому отжигу подвергают штамповки, заготовки инструмента и других изделий. Недостатком данного отжига является невозможность обеспечения изотермичности процесса при крупных изделиях или больших садках.
Для смягчения стали широко применяют сфероидизирующий отжиг (отжиг на зернистый перлит), заключающийся в нагреве и длительной выдержке в районе температур А1 (чуть выше или чуть ниже), что
позволяет получить зернистую форму перлита вместо пластинчатой. Частицы цементита, не растворившегося при нагреве, и микрообъемы с повышенной концентрацией углерода в аустените из-за недостаточно полной его гомогенизации служат центрами кристаллизации для цементита, выделяющегося при последующем охлаждении ниже точки А1 и принимающего в этом случае зернистую форму. При нагреве значительно выше Ас1 и растворения бóльшей части цементита и более полной гомогенизации аустенита последующее выделение его при охлаждении происходит в пластинчатой форме. Стали, близкие к эвтектоидному составу, имеют узкий интервал температур нагрева (750-760°С) для отжига на зернистый перлит, для заэвтектоидных сталей интервал расширяется до 770-790°С. Легированные заэвтектоидные стали можно нагревать до более высоких температур и в более широком интервале (770-820°С). Охлаждение при сфероидизации медленное. Оно должно обеспечить распад аустенита на феррито-карбидную структуру, сфероидизацию и коагуляцию карбидов.
Сфероидизирующий отжиг проводят в условиях непрерывного охлаждения или по режиму изотермического отжига.
Сталь с зернистым перлитом имеет более низкие значения твердости и временного сопротивления и соответственно более высокие относительного удлинения и сужения. После отжига на зернистый перлит эвтектоидные и заэвтектоидные стали обладают хорошей обрабатываемостью резанием – возможно применение больших скоростей резания и достигается высокая чистота поверхности. Кроме того, такая структура при последующей закалке стали обеспечивает мелкое зерно, расширяет интервал закалочных температур и уменьшает склонность к образованию трещин. Отжигу на зернистый перлит подвергают также тонкие листы и прутки из низко- и среднеуглеродистой стали перед холодной штамповкой или волочением для повышения пластичности.
Нормализация
Нормализация заключается в нагреве стали до температуры выше Ас1(Acm) на 30…50°С, выдержке при этой температуре и охлаждении на воздухе.
Структуры после нормализации: перлит и феррит (цементит вторичный). Ускоренное по сравнению с отжигом охлаждение обусловливает несколько большее переохлаждение аустенита, поэтому при нормализации получается более тонкое строение эвтектоида (тонкопластинчатый перлит или сорбит). Кроме того, частично подавляется выделение избыточной фазы (феррита или вторичного цементита). Таким образом, твердость стали после нормализации выше, чем после отжига.
Назначение нормализации:
3) исправление дефектов микроструктуры (крупного зерна, строчечности, видманштеттовой структуры, сетки цементита в заэвтектоидной стали);
4) некоторое повышение твердости слишком мягких малоуглеродистых сталей для улучшения их обрабатываемости режущим инструментом;
5) подготовка структуры перед ОТО инструментальных сталей.
Место нормализации в технологическом цикле – может использоваться и как предварительная, и как окончательная (если комплекс получаемых свойств удовлетворяет условиям эксплуатации) термическая обработка.
Нормализация – более производительный способ термообработки по сравнению с отжигом, применяется, если необходимо исправить дефекты микроструктуры, а получение минимальной твердости не требуется.
Закалка
Назначение закалки
Закалка стали является частью ОТО и, в совокупности с отпуском, обеспечивает упрочнение стали, получение требуемого комплекса механических и эксплуатационных свойств.
Показателем качественно проведенной закалки является достижение максимально возможной для данной стали твердости.
Сущность закалки
Закалка — это операция ТО, заключающаяся в нагреве до температур выше критических, выдержке и охлаждении со скоростью подавляющей распад аустенита (больше критической) с целью получения неравновесных структур.
В стали продуктом закалки является мартенсит - пересыщенный твердый раствор углерода в α-железе. Это твердый раствор внедрения, поэтому его образование ведет к большим искажениям решетки, напряжениям, чем объясняется высокая твердость и хрупкость стали со структурой мартенсита. Таким образом, закалка для стали – всегда упрочняющая обработка, в отличие от цветных сплавов, в которых при закалке образуется твердый раствор замещения, и, следовательно, она может быть как упрочняющей, так и разупрочняющей. После закалки стали всегда требуется отпуск.
Разновидности закалки
Схема используемых разновидностей закалки представлена на рис.4.
Рис. 4. Разновидности закалки:
1 – непрерывная, 2 – прерывистая (в двух средах); 3 – с подстужива- нием; 4 – ступенчатая;5 – изотер- мическая
Непрерывная закалка
Непрерывная закалка заключается в нагреве выше критических температур, выдержке и охлаждении в одном охладителе со скоростью больше критической.
Выбор температуры закалки
В зависимости от температуры нагрева закалка может быть полной и неполной.
Полная закалка – такая, при которой вся структура участвует в превращении. Она производится из области однофазного аустенита (то есть tзакалки = Ас3 (Асm)+30…50°C) и обеспечивает структуру мартенсита и некоторое количества аустенита остаточного. Для доэвтектоидной стали полная закалка обеспечивает структуру мартенсита с небольшим количеством остаточного аустенита (3 - 4%), при которой достигается максимальная для данной стали твердость. Для заэвтектоидной стали после полной закалки в структуре присутствует повышенное количество (10 - 20%) остаточного аустенита, что способствует снижению твердости.
Неполная закалка – такая, при которой в превращениях участвует лишь часть структуры, нагрев производится в межкритическую область (выше Ac1, но ниже Ас3(Асm)). При неполной закалке доэвтектоидной стали образуется структура мартенсит + феррит + остаточный аустенит, отличающаяся пониженной твердостью за счет присутствия мягкой составляющей – феррита. Следовательно, неполная закалка для доэвтектоидной стали всегда является браком.
Неполная закалка в заэвтектоидной стали обеспечивает следующую структуру: мартенсит + цементит вторичный + остаточный аустенит. При этом количество аустенита остаточного, зависящее от содержания углерода, растворенного в аустените, значительно меньше, чем в случае полной закалки. Например, для стали У12 при полной закалке в аустените содержится 1,2% С, а при неполной около 0,8% С. Поэтому неполная закалка для заэвтектоидной стали, в случае правильно подготовленной структуры к окончательной термообработке (отсутствия цементитной сетки, равномерном распределении частиц цементита вторичного в виде отдельных включений – глобулей), обеспечивает лучшие результаты, чем полная.
Преимущества неполной закалки для заэвтектоидной стали:
1) повышение твердости за счет присутствия частиц вторичного цементита, который имеет более высокую твердость, чем мартенсит;
2) повышение твердости за счет уменьшения количества мягкой составляющей – остаточного аустенита;
3) наличие равномерно распределенных очень твердых частиц цементита повышает износостойкость стали;
4) уменьшение уровня закалочных напряжений, снижение коробления и опасности возникновения трещин (неисправимого брака), что имеет особое значение для инструмента сложной формы, в котором уже имеются концентраторы напряжений;
5) уменьшение обезуглероживания при нагреве под закалку до более низких температур – наличие обезуглероженного слоя снижает твердость на рабочих поверхностях инструмента после закалки;
6) большая экономичность (уменьшение расхода электроэнергии и металла (потерь в окалине)), производительность.
Поэтому для заэвтектоидной стали всегда применяется только неполная закалка с нагревом до Ac1+30…50°С.
Выбор закалочной среды
Скорость охлаждения при непрерывной закалке должна обеспечивать возможность переохлаждения аустенита без распада до температуры начала мартенситного превращения Мн, то есть она должна быть больше критической. Даже небольшое уменьшение скорости охлаждения по сравнению с критической ведет к частичному распаду аустенита в троостит- ной области. В результате такой закалки образуется смешанная структура: троостит (признак частичной закалки) + бейнит + мартенсит + остаточный аустенит.
Поскольку при небольшом снижении скорости охлаждения по сравнению с критической скоростью закалки троостита немного и так как все фазовые превращения (в том числе и распад аустенита) начинаются на границах зерен, то образующаяся в этом случае структура весьма характерна: светлые участки мартенсита, окаймленные темной трооститной сеткой (рис. 2). Чем меньше скорость охлаждения, тем больше троостита в структуре - образуется троосто-мартенсит – твердость понижается. Таким образом, частичная закалка на поверхности – всегда брак.
Итак, скорость охлаждения при закалке должна быть больше критической. Однако и чрезмерное увеличение скорости охлаждения тоже нежелательно, так как ведет к увеличению закалочных напряжений и возникновению коробления и трещин – неисправимого брака закалки.
Разные скорости охлаждения обеспечиваются различными закалочными средами. Идеальной средой является такая, которая обеспечивает достаточно высокую скорость охлаждения в районе минимальной устойчивости аустенита («носа» С-кривой) во избежание частичной закалки и небольшую скорость в интервале мартенситного превращения, сопровождающегося большими фазовыми напряжениями. В табл. 1 производится сравнение скоростей охлаждения в «опасных» интервалах температур при использовании различных закалочных сред.
Таблица 1
Дата добавления: 2021-12-10; просмотров: 92; Мы поможем в написании вашей работы! |
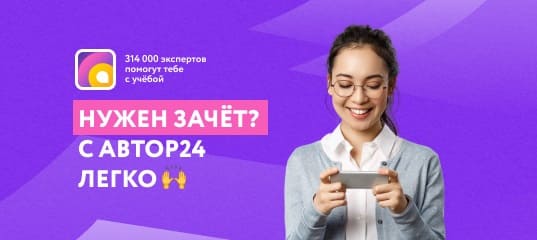
Мы поможем в написании ваших работ!