Размеры и масса радиальных подшипников ВЗД
Типоразмер двигателей
Шифр радиальной опоры
Типоразмер двигателей | Шифр радиальной опоры | Диаметр, мм | Длина, мм | Масса, кг | Примечания | |
наружный | внутренний | |||||
Д1-240 | ОН-240/155 | 205 | 155 | 200 | 18,0 | Резинометалли- |
ческие опоры | ||||||
Д2-195 | ОН-195/135 | 165 | 135 | 400 | 25,0 | То же |
ДЗ-172, Д5-172 ДГ-155 | ОН-172/120 ДГ-155.025 | 148 128 | 120 102 | 200 НО | 8,0 6.4 | Металлические опоры |
Д1-127 | Д1-127.060 | 105 | 85 | 200 | 4,0 | Резинометалли- |
ческие опоры | ||||||
Д-108 | Д-108.027 | 88 | 70 | 100 | 1,8 | Металлические |
опоры | ||||||
ДГ-108 | Д-108.027 | 88 | 76/70 | 160/100 | 1,9 | То же |
Д1-105 | Д-105.037 | 88 | 70 | too | 1,7 | |
ДГ-95 | ДГ-95.025 | 76 | 65/60 | 120/80 | 1,8 | |
ДГУ-95 | ДГУ-95.026 | 76 | 62,5 | 100 | 1,2 | |
Д-85,Д1-88 | ОН-85 | 70 | 54 | 190 | 2,1 | Резинометалли- |
ческие опоры | ||||||
Д1-54 | ОН-54 | 45 | 33 | 120 | 0,7 | То же |
Д-48 | Д-48.025 | 38 | 32/28 | 80/50 | 0,2 | Металлические |
1 | опоры |
Рис.3.13.Торцевой сальник:
1-втулка в корпусе шпинделя;
2-неподвижный элемент сальника; 3-пружина; 4-подвижной элемент сальника;5-уплотнение; 6-втулка на валу.
ванные твердым сплавом или элементами синтетических алмазов [174].
|
|
Уплотнение выходного вала.Для использования гидромониторных долот в отечественных ВЗД практическое применение получили четыре варианта уплотнений:
торцовый сальник, устанавливаемый в верхней части шпинделя ниже радиальной опоры [94]. Используется в двигателях диаметром 172 и 195 мм (рис. 3.13);
многорядный упорный подшипник скольжения, эффективно выполняющий роль уплотнения [94, 124]. Используется в двигателях диаметром 172-240 мм;
лабиринтное уплотнение, выполняющее роль дросселирующего устройства [94];
упорно-радиальные подшипники с резиновыми тороидными кольцами, устанавливаемые вместо одного ряда шаров [102].
Два последних варианта используются в опытных конструкциях ВЗД.
В зарубежных двигателях с маслонаполненными шпинделями уплотнение вала входит в конструкцию гидрозащиты.
При эксплуатации ВЗД большое внимание уделяется выбору рациональных режимов работы двигателей, обеспечивающих разгрузку и эффективное охлаждение осевых опор. Методика расчета шпиндельной секции ВЗД и определение условий ее разгрузки представлены в § 5.5.
СОЕДИНЕНИЕ РОТОРА И ВАЛА ШПИНДЕЛЯ
Соединение ротора ВЗД и вала шпинделя является одним из основных узлов двигателя, определяющим долговечность и надежность гидромашины в целом.
|
|
Механизм, соединяющий планетарно движущийся ротор с концентрично вращающимся валом, работает в тяжелых условиях. Помимо передачи крутящего момента и осевой силы, этот узел должен воспринимать сложную систему сил в РО, характеризующуюся непостоянной ориентацией ротора (см. § 5.5; 8.3).
В отличие от известных в технике соединений, передающих вращение между двумя несоосными концентрическими вращающимися валами, рассматриваемое соединение в ВЗД является связующим звеном с ротором, совершающим планетарное движение. Причем за один оборот выходного вала ротор Z1поворачивается вокруг своей оси, соответственно совершая Z1циклов переменных напряжений. Эти обстоятельства предопределяют повышенные требования к циклической прочности соединения, особенно при использовании многозаходных ВЗД.
Своеобразные условия работы соединения и невозможность переноса напрямую из других отраслей техники готового технического решения предопределили многообразие компоновок этого узла. Принципиально могут быть использованы четыре типа соединений на базе:
деформации одного или нескольких элементов конструкции;
|
|
обеспечения свободы перемещения ротора за счет введения элементов с относительно большим люфтом;
шарнирных соединений;
гибкого вала (торсиона).
Первый и второй типы соединения [22] ввиду существенных удельных нагрузок в ВЗД не нашли применения.
Шарнирные соединения.ВЗД прошли эволюцию от применения пальцевых шарниров (аналогичных автомобильным) до специальных конструкций, наиболее приспособленных для передачи динамических осевой нагрузки и крутящего момента.
В первом поколении отечественных ВЗД применялись двух-шарнирные соединения зубчатого типа с центральным шаром [90]. Они использовались для передачи крутящих моментов до 7 кНм при частоте вращения до 200 об/мин. Эксцентриситет соединения доходил до 5 мм. Известны разновидности такого соединения для ВЗД с разделенным потоком, позволяющие через его внутреннюю полость пропускать жидкость высокого давления [95].
14. Двухшарнирное соединение:
1 - полумуфта; 2 - гайка; 3 - манжета; 4 - втулка; 5 - шар; 6 - корпус; 7 - соединительная труба.
Шарнирные соединения ВЗД работают, как правило, в среде абразивных жидкостей. Поэтому надежная герметизация шарниров является одним 6 из основных направлений повышения их работоспособности. Проблема герметизации осложняется тем, что полости, которые требуется изолировать, вращаются вокруг смещенных осей в условиях вибрации и значительного гидростатического давления. Поэтому герметизирующие элементы должны быть гибкими и прочными при циклической нагрузке, а устройство для герметизации в целом простым и надежным.
|
|
Сначала в шарнирах использовались простейшие резиновые уплотнения, в дальнейшем стали применять уплотнения сильфонного и манжетного типов (рис. 3.14) [25].
Заслуживает внимания оригинальная система смазки шарниров под давлением, которая включает подпружиненный поршневой лубрикатор, устанавливаемый во внутренней полости трубы, соединяющей головки шарниров. Тем самым внутренняя полость шарниров постоянно находится под избыточным по отношению к перекачиваемой среде давлением.
Зарубежные компании также используют двухшарнирные соединения. Разновидность конструкции, используемой в двигателе "Anadrill", приведена на рис. 3.15 [48].
Гибкие валы.Существенный шаг, оказавший влияние на подходы к конструированию ВЗД в целом, был сделан в середине 70-х годов, когда ВНИИБТ выполнил комплекс научно-исследовательских работ [46] и впервые в практике проектирования ВЗД предложил конструкцию гибкого вала, защищенную патентами 6. СССР и других стран [32, 151].
В отличие от шарниров в гибких валах внешнее трение деталей заменяется на внутреннее трение материала вала.
Методика расчета гибких валов и обоснование выбора их рациональных размеров изложены в § 8.2.
К началу 90-х годов в большинстве типоразмеров ВЗД, выпускавшихся в России, для соединения ротора и выходного вала применялись гибкие валы. В двигателях с наружным диамет-
Рис.3.15.Двухшарнирное соединение “Anadrill”:
1-корпус; 2-центральный шар; 3-перифирийный шар; 4-уплотнение; 5-гайка; 6-соединительная трубка.
Рис.3.16. Конструкции гибких валов
ром 88 мм и более гибкий вал размещается в расточке ротора, а в малогабаритных двигателях - ниже ротора.
В большинстве случаев гибкий вал ВЗД представляет собой металлический стержень круглого сечения с утолщенными концами (рис. 3.16). На концах выполняются присоединительные элементы: гладкий конус или коническая резьба. Иногда гибкий вал выполняется полым со сквозным цилиндрическим каналом для подвода рабочей жидкости высокого давления непосредственно к долоту. Для повышения циклической прочности в месте перехода от заделки к рабочей части вала имеется конус с углом 5-15° или галтель с отношением радиуса галтели г к диаметру вала d в пределах 0,1-0,2. Кроме того, применяются технологические методы поверхностного упрочнения. Наиболее распространен поверхностный наклеп (обкатка роликами или обдувка дробью), способствующий образованию сжимающих остаточных напряжений, благоприятно сказывающихся на сопротивлении усталости [ИЗ].
В зависимости от типоразмера двигателя диаметр гибких валов изменяется в диапазоне 18-70 мм, а длина - 500-3000 мм.
Преимущества использования гибких валов заключаются в простоте конструкции и высокой технологичности, большом сроке службы, соизмеримым с ресурсом корпусных деталей двигателя, а также возможности реализации различных компоновок двигателей.
В 90-е годы западные компании вслед за фирмой "Drilex", выпускающей двигатели по отечественной лицензии, также стали использовать гибкие валы. Для их изготовления помимо сталей используют титановые сплавы и стеклопластики.
Опыт эксплуатации двигателей в наклонно направленном и горизонтальном бурении выявил недостаточную стойкость гибких валов при углах перекоса секций более ГЗО'. В связи с этим двигатели типа ДГ стали оснащать шарнирно-торсионными соединениями [10].
КЛАПАНЫ
Объемный принцип действия винтовых двигателей предопределил необходимость оснащения их специальными клапанами. В большинстве двигателей они представляют собой автономный узел, а иногда встроены в ротор.
Переливной клапанпредназначен для сообщения внутренней полости бурильной колонны с затрубным пространством при спуско-подъемных операциях. Применение клапана уменьшает
Рис.3.17. Переливной клапандвигателяд1-105;
1-переводник; 2-кольцо; 3-упор; 4 армированная манжета;
5-втулки;6-уплотнение; 7-корпус.
гидродинамическое воздействие на забой при спуске и подъеме колонны, а также устраняет холостое вращение двигателя при этих операциях.
Разработаны и используются несколько конструкций переливных клапанов. В одной из них, не имеющей линейно перемещающихся деталей, в качестве запорного элемента применена резиновая манжета, деформирующаяся за счет падения давления при движении жидкости в щели клапана. Клапан устанавливается в верхней части полого ротора. Серьезный недостаток этой схемы -невозможность определения утечки при опробовании клапана на устье скважины.
В дальнейшем Пермским филиалом ВНИИБТ была разработана модернизированная конструкция клапана (рис. 3.17), применяемая в нескольких типоразмерах ВЗД [127].
В конструкции переливного клапана в первых моделях двигателей диаметром 240 и 172 мм и уплотнительный элемент клапана заимствован от бурового насоса. Выполнение основных функций клапана обеспечивает специальная гидравлическая коробка (рис. 3.18) [20].
В зарубежных двигателях повсеместно используются золотниковые клапаны (рис. 3.19).
Попытки использовать подобные клапаны в среде применяемых в России буровых растворов оказались неудачными: наблюдался быстрый износ и нестабильное закрытие клапана.
Редукционные клапаныприменяются в исключительных случаях, когда по технологическим соображениям требуется увеличить расход жидкости для очистки забоя и затрубного пространства. Они являются альтернативой насадке в роторе. Редукционный клапан ВНИИБТ для двигателя диаметром 95 мм устанавливается в автономном переводнике выше РО [50]
Рис.3.18.Переливной клапан двигателя Д-240:
1-гидравлическая пробка; 2-седло; 3-клапан; 4-корпус; 5- пружина; 6-шток; 7-переводник.
Рис.3.19.Переливной клапан двигателя ‘’Dyna-Drill”:
1-корпус; 2-поршень;3-седло; 4-пружина.
Рис.3.20.Редукционный клапан двигателя ДГУ-95:
1-корпус; 2-упорная шайба; 3-поршень; 4-пружина; 5,6-уплотнение.
(рис. 3.20). При увеличении расхода жидкости создается дополнительный перепад давления и поршень, преодолевая усилие пружины, перемещается вниз, позволяя части потока жидкости проходить в затрубное пространство, минуя РО.
В патентной литературе известны редукционные клапаны, размещаемые в роторе двигателя [44]. Они обеспечивают циркуляцию промывочной жидкости через двигатель при заторможенном роторе. Такая ситуация может возникать при шламовании двигателя и в случае его прихвата в скважине при расхаживании инструмента снижается износ РО.
Циркуляция достигается тем, что клапан снабжен диафрагмой, расположенной в верхнем торце полого ротора, и бойком, жестко связанным с подпружиненным полым поршнем.
ОПОРНО-ЦЕНТРИРУЮЩИЕ ЭЛЕМЕНТЫ
К опорно-центрирующим элементам относятся калибраторы, центраторы и децентраторы. Они используются в компоновках низа бурильной колонны при проводке вертикальных, наклонных и горизонтальных скважин в целях повышения качества ствола скважины и управления параметрами его искривления, а также предупреждения осложнений в процессе бурения [109].
Калибраторпредназначен для калибрования ствола скважин, центрирования и снижения поперечных колебаний долота и вала двигателя и устанавливается на выходном валу непосредственно над долотом.
Центраторпредназначен для центрирования нижней части бурильной колонны и забойного двигателя с целью стабилизации параметров искривления ствола или изменения зенитного угла скважины.
Децентраторпредназначен для смещения оси забойного двигателя или бурильной колонны за ось скважины в месте его установки.
Геометрические параметры опорно-центрирующих элементов и расположение их относительно долота определяют из назначения КНБК.
Центраторы и децентраторы устанавливают между секциями или непосредственно на корпусе забойного двигателя.
Конструктивное исполнение (с прямыми или спиральными планками, с шарошками), тип и вид вооружения, а также размеры калибраторов и центраторов забойных двигателей регламенрующие элементы компоновки, предназначенные для долот диаметром от 114,3 до 490,0 мм.
В практике бурения долотами диаметром 215,9 мм и более используются серийно выпускаемые стационарные центраторы типа 1ЦД-214МС и передвижные типов ЗЦДП-295,3 МСТ и ЗЦДП-215,9 МСТ, предназначенные для забойных двигателей диаметром 240 и 172 мм соответственно.
В ВЗД для горизонтального бурения центраторы (табл. 3.5) и децентраторы входят в комплект сменных частей и поставляются с двигателями по желанию заказчика.
Таблица 3-5
ДГ-95 | ДГ-108 | ДГ-155 | |||
Параметр | Диаметр долота, мм | ||||
120,6 | 139,7 | 139,7 | 190,5 | 215,9 | |
Диаметр опорной поверхности, мм Число лопастей Длина, мм Ширина лопасти, мм Диаметр корпуса, мм | 114, 116, 118 8 170 25 | 132, 134, 136 8 170 25 | 132, 134, 136 8 150 30 | 182, 184, 186, 188 8 146 40 | 202, 206, 208, 210 8 146 40 |
105 | 105 | 118 | 165 | 180 |
Корпусные центраторы в двигателях диаметром 95 и 108 мм устанавливаются между двигательной и шпиндельной секциями, а для двигателей 155 мм - на корпусе шпинделя.
Децентраторы двигателей ДГ-108 имеют одну лопасть длиной 150 мм и шириной 70 мм. Радиус опорной поверхности децентра-торов равен 74, 76 и 78 мм.
В двигателях ДГ-155 децентраторы выполнены также с одной лопастью длиной 146 мм и шириной 100 мм. Радиусы опорной поверхности децентраторов составляют 118 и 122 мм.
Дата добавления: 2018-02-18; просмотров: 1161; Мы поможем в написании вашей работы! |
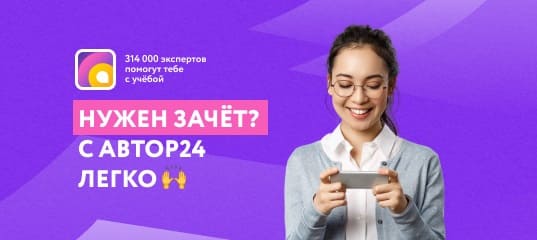
Мы поможем в написании ваших работ!