ТАБЛИЧНЫЙ МЕТОД РАСЧЕТА РЕЖИМА РЕЗАНИЯ
ПРИ ТОЧЕНИИ
Выбор марки инструментального материала, сечения державки резца и геометрических параметров режущей части инструмента
1. Выбирают и обосновывают в зависимости от марки обрабатываемого материала марку инструментального материала. Для токарных резцов рекомендуется применять твердые сплавы или минералокерамику, так как они обеспечивают значительно большую производительность обработки по сравнению с быстрорежущими сталями. Статистика показывает, что в металлообрабатывающей промышленности на долю твердосплавного инструмента приходится 70 %объема снятой стружки (табл. П. 1.3, П. 1.4 или [1–18]).
2. Выбирают форму заточки передней поверхности резца в зависимости от марки обрабатываемого материала и его прочностных свойств, жесткости технологической системы, характера выполняемой операции и необходимости завивания и дробления стружки.
3. Выбирают размеры поперечного сечения державки резца, исходя из паспортных данных станка. Выбранные размеры округляют до ближайших меньших стандартных размеров, приведенных в справочной литературе [13, 17] или в табл. П. 2.1–П. 2.11.
4. Выбирают геометрические параметры режущей части инструмента (табл. П. 2.1–П. 2.11 или [1–18]).
При токарной обработке используются как резцы общего назначения (табл. П. 2.1–П. 2.8), так и резцы с МНП (табл. П. 2.9–П. 2.12).
2.2. Выбор глубины резания и числа проходов
При выборе глубины резания необходимо стремиться снять весь припуск за один проход и лишь при чистовой и отделочной обработке припуск снимается за два и более проходов.
|
|
Например, при черновой обработке с шероховатостью поверхности до мкм весь припуск следует снимать за один проход, т.е.
. При получистовой обработке
от 10 до 40 мкм припуск
мм следует снимать за один проход, т.е.
. Если же припуск более 2 мм, то обработку производят за два прохода.
При проектировании технологических процессов рекомендуется выбирать значения параметров шероховатости из числа предпочтительных значений, принятых ГОСТ 2789-73 и приведенных в табл. 2.1 [6] или прил. 10.
Таблица 2.1
Предпочтительные значения шероховатости
Область применения | Значение Rz, мкм | Значение Rа, мкм |
Отделочная и доводоч- ная обработка | 0,025 | - |
0,05 | 0,012 | |
0,1 | 0,025 | |
0,2 | 0,05 | |
0,4 | 0,1 | |
0,8 | 0,2 | |
Чистовая и получистовая обработка | 1,6 | 0,4 |
3,2 6,3 12,5 | 0,8 1,6 3,2 | |
25,0 | 6,3 | |
Предварительная (черновая) обработка | 50 | 12,5 |
100 | 25 | |
200 | 50 | |
400 | 100 |
2.3. Выбор подачи
Подача назначается с учетом требований к шероховатости обработанной поверхности, радиуса при вершине резца r, марки обрабатываемого материала, жесткости технологической системы (табл. П. 3.1–П. 3.11 или [3–17]).
|
|
Величина подачи уточняется по станку; берется ближайшая меньшая подача.
Выбранная величина подачи проверяется по прочности пластинки твердого сплава или минералокерамики, для чего находится тангенциальная составляющая силы резания Рz при выбранном режиме резания и сопоставляется с силой резания, допустимой прочностью пластинки для заданных условий обработки. Если фактическая сила Рz не превышает допустимой, то подача выбрана правильно, в противном случае выбранную подачу необходимо уменьшить.
2.4. Расчет скорости резания
Скорость резания (м/мин): при наружном продольном и поперечном точении и растачивании рассчитывают по эмпирической формуле
, (2.1)
а при отрезании, прорезании и фасонном точении – по формуле
. (2.2)
Среднее значение стойкости Т при одноинструментальной обработке 30–60 мин. Значения коэффициента СV показателей степени х, у и m приведены в справочной литературе [1, 7, 10–16], табл. П. 3.12.
Коэффициент КV является произведением коэффициентов, учитывающих влияние материала заготовки КМV, состояния поверхности КПV, материала инструмента КИV, СОТС КVСОТС (табл. П. 3.12–П. 3.20, П. 9.1–9.7).
|
|
При многоинструментальной обработке и многостаночном обслуживании период стойкости увеличивают, вводя соответственно коэффициенты КТИ и КТС, угол в плане резцов Кφ и радиуса при вершине резца Кr [7, 12, 13], табл. П. 3.19.
Оптимальную скорость резания V0 при точении выбирают из [5, 10] или подсчитывают по формулам (1.1–1.7).
После окончательного выбора или расчета скорости резания, с учетом всех поправок, произвести сравнительный анализ их величин и в дальнейших расчетах использовать наибольшую из них.
Определяют число оборотов шпинделя
, об./мин, (2.3)
где D – диаметр обрабатываемой поверхности, мм.
Число оборотов шпинделя уточняется по станку (для универсального оборудования) и рассчитывается уточненная скорость резания.
Дата добавления: 2018-02-15; просмотров: 1480; Мы поможем в написании вашей работы! |
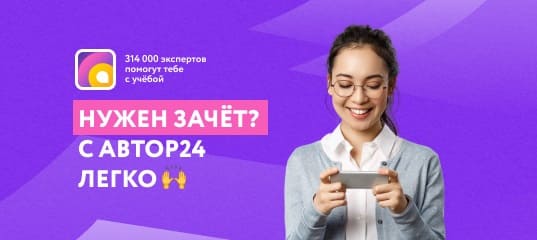
Мы поможем в написании ваших работ!