ОБЩАЯ ПОСЛЕДОВАТЕЛЬНОСТЬ НАЗНАЧЕНИЯ РЕЖИМОВ РЕЗАНИЯ ПРИ МЕХАНИЧЕСКОЙ ОБРАБОТКЕ
Nbsp;
НАЗНАЧЕНИЕ И РАСЧЕТ
РЕЖИМОВ РЕЗАНИЯ
ПРИ МЕХАНИЧЕСКОЙ ОБРАБОТКЕ
Уфа 2012
![]() |
НАЗНАЧЕНИЕ И РАСЧЕТ
РЕЖИМОВ РЕЗАНИЯ
ПРИ МЕХАНИЧЕСКОЙ ОБРАБОТКЕ
«Допущено Учебно-методическим объединением вузов по образованию
в области автоматизированного машиностроения (УМО АМ) в качестве
учебного пособия для студентов высших учебных заведений, обучающихся
по направлению подготовки дипломированных специалистов и бакалавров «Конструкторско-технологическое обеспечение машиностроительных
производств»
Уфа 2012
Авторы: В. М. Кишуров, М. В. Кишуров, М. Ф. Мугафаров,
П. П. Черников, Ч. А. Яруллин
УДК 621.91 (07)
ББК 34.63 (я7)
Н
Рецензенты:
зав. кафедрой машин и аппаратов БашГУ, д-р техн. наук, профессор
Кузнецов В.А.; главный технолог ОАО «ИМЗ» Войнов А.М.
Н Назначение и расчет режимов резания при механической обработке: Учеб. пособие / В. М. Кишуров, М. В. Кишуров, М. Ф. Мугафаров, П. П. Черников, Ч. А. Яруллин. – Уфа, 2012. – 176 с.
Представлен материал к практическим занятиям по расчету режимов резания при механообработке, а также комплекс заданий и рекомендации к выполнению расчетно-графической работы по резанию материалов для направлений 151000 – Конструкторско-технологическое обеспечение автоматизированных машиностроительных производств; 151900 – Конструкторско-техноло-гическое обеспечение машиностроительных производств. Приведены классические методики и программное обеспечение для расчета режимов резания на различные технологические операции.
|
|
Может быть использовано студентами при выполнении курсовых и выпускных квалификационных работ, а также может быть полезно инженерно-техническим работникам машиностроительных предприятий.
Табл. 134. Ил. 36. Библиогр.: 18 назв.
УДК 621.91 (07)
ББК 34.63 (я7)
ISBN
© Уфимский государственный авиационный технический университет,2012
ОГЛАВЛЕНИЕ
Введение…………………………………………………………………..5
1. Общая последовательность назначения режимов резания
при механической обработке……………………………………………6
2. Табличный метод расчета режима резания при точении………….13
2.1. Выбор марки инструментального материала, сечения державки
резца и геометрических параметров режущей части инструмента..13
2.2. Выбор глубины резания и числа проходов ...…………………….13
2.3. Выбор подачи .……………………………………………………..11
2.4. Расчет скорости резания ..…………………………………………12
2.5. Проверка выбранного режима резания по прочности механизма
подачи станка и мощности станка………………………………….….13
2.6. Расчет машинного времени ….......………………………………..14
|
|
3. Аналитический метод расчета режима резания при точении….….18
3.1. Выбор марки инструментального материала, сечения державки
резца и геометрических параметров режущей части инструмента.…18
3.2. Выбор глубина резания и числа проходов ……………………….18
3.3. Расчет подачи ..……………………………………………..............18
3.4. Расчет стойкости инструмента…………………..……...…………23
3.5. Расчет скорости резания ..…………………………………………24
3.6. Расчет подачи, при которой полностью используются режущие свойства инструмента и мощность станка…….....................................26
3.7. Расчет машинного времени………………………………..............29
4. Расчет режима резания при сверлении……………………………...30
4.1. Выбор марки инструментального материала,
конструкции и геометрии сверла………………………………………30
4.2. Выбор глубины резания .…………………………………..............30
4.3. Выбор подачи .……………………………………………..............30
4.4. Расчет скорости резания .………………………………………….30
4.5. Расчет крутящего момента и осевой силы …….………………….31
4.6. Расчет мощности резания …..……………………………..............32
4.7. Расчет мощности электродвигателя станка………………………32
4.8. Расчет машинного времени ….……………………………………32
|
|
5. Расчет режима резания при фрезеровании………………………...33
5.1. Выбор марки инструментального материала, конструкции
и геометрии фрезы……………………………………………………..33
5.2. Назначение глубины резания и ширины фрезерования………...33
5.3. Определение подачи на зуб...……………………………………...33
5.4. Определение минутной подачи ..………………………………….33
5.5. Расчет скорости резания ..…………………………………………33
5.6. Расчет силы резания и крутящего момента ….…………...............34
5.7. Расчет эффективной мощности резания ………………………….35
5.8. Расчет мощности электродвигателя станка………………………35
5.9. Расчет машинного времени ….……………………………………35
6. Расчет режима резания при протягивании………………………….37
7. Расчет режима резания на ЭВМ………..............................................39
7.1. К расчету режимов резания при фрезеровании…………..............41
7.2. К расчету режимов резания при сверлении………………………47
7.3. К расчету режимов резания при точении…………………………50
8. Задания и порядок выполнения расчетно-графической работы
по расчету режимов резания при механической обработке………….60
8.1. Варианты и исходные данные на операции
механической обработки…..……..……………………………………60
|
|
Список литературы……………………………………………..............68
Приложение 1…………………………………………………………...70
Приложение 2…………………………………………………………...80
Приложение 3…………………………………………………………...89
Приложение 4………………………………………………………….104
Приложение 5………………………………………………………….112
Приложение 6………………………………………………………….130
Приложение 7………………………………………………………….131
Приложение 8………………………………………………………….134
Приложение 9………………………………………………………….139
Приложение 10………………..……………………………………….174
Приложение 11………………..……………………………………….175
ВВЕДЕНИЕ
Повышение эффективности металлообработки является одним из основных направлений развития современного машиностроения. По мере прогресса техники, с одной стороны, непрерывно улучшаются эксплуатационные характеристики материалов и, с другой – повышается производительность и экономичность их обработки. Последнее, как правило, обеспечивается назначением наивыгоднейших режимов резания. Под наивыгоднейшими режимами резания понимают такое сочетание глубины резания t, подачи s и скорости резания V, при которых в данных условиях производства обеспечивается максимальная производительность обработки.
В настоящее время широкое промышленное применение в механообработке нашли инструменты с многогранными неперетачиваемыми пластинами МНП (резцы, торцевые фрезы, сверла и др.), с нанесенными на них различными износостойкими покрытиями, которые позволяют значительно повысить стойкость и надежность режущих инструментов, увеличить производительность обработки деталей резанием и улучшить качество поверхностного слоя обработанных деталей. Кроме того, при механической обработке инструментами, особенно из быстрорежущих сталей, а их изготавливают около 70 %, рекомендуется применять смазочно-охлаждающие технологические средства (СОТС), так как рациональное применение СОТС позволяет примерно от 1,5 до 4 раз повысить стойкость инструмента и примерно на 20–60 % форсировать режимы резания и уменьшить энергозатраты при механообработке [3]. Применение современных эффективных СОТС позволяет резко увеличить качество обработки, а также в полной мере использовать широкие возможности современного высокопроизводительного оборудования при обработке труднообрабатываемых материалов. Классификация СОТС и область их применения представлены в табл. П. 9.1–9.7.
Учебное пособие предназначено для закрепления теоретических знаний студентов по курсам «Резание материалов», «Режущие инструменты» и приобретения дополнительных практических навыков по расчету наивыгоднейших режимов резания при различных видах обработки резанием, необходимых при конструировании режущего инструмента и разработке технологических процессов изготовления деталей машин.
ОБЩАЯ ПОСЛЕДОВАТЕЛЬНОСТЬ НАЗНАЧЕНИЯ РЕЖИМОВ РЕЗАНИЯ ПРИ МЕХАНИЧЕСКОЙ ОБРАБОТКЕ
Существует два способа назначения наивыгоднейших режимов резания: табличный и аналитический. На машиностроительных предприятиях отрасли чаще используют табличный способ. Суть этого способа заключается в следующем:
1. Изучение задания (исходные данные: материал детали, припуски на обработку, конфигурация, размеры и шероховатость обрабатываемых поверхностей).
2. Выбор и обоснование рациональной марки инструментального материала в зависимости от марки обрабатываемого материала.
3. Выбор конструкции и геометрии режущего инструмента.
4. В зависимости от величины припуска на обработку и шероховатости обработанной поверхности назначается глубина резания t, число проходов с учетом вида обработки.
5. Назначается подача s с учетом требований к шероховатости обработанной поверхности, геометрии инструмента, марки обрабатываемого материала, жесткости технологической системы. Из всех подач выбирается наименьшая, которая называется технологически допустимой подачей s0. Выбранная величина подачи уточняется по станку (для универсального оборудования).
6. Выбирается по соответствующим таблицам или рассчитывается скорость резания Vт и оптимальная скорость резания V0.
Следует отметить, что скорость резания Vт, соответствующая точке максимума , ниже оптимальной V0 и тем более экономической Vэ, т.е. всегда соблюдается неравенство Vт < V0< Vэ. Однако при обработке жаропрочных сплавов, закаленных сталей, некоторых марок жаропрочных сталей и титановых сплавов, а также при обработке любых материалов в условиях автоматизированного производства оптимальная скорость резания V0 практически совпадает с экономической Vэ [3].
При точении, фрезеровании, сверлении и протягивании деталей, особенно из труднообрабатываемых материалов, обработку рекомендуется проводить на оптимальных режимах резания, которые обеспечивают высокую точность и качество обработанной поверхности.
Под оптимальным режимом резания понимают такой, который обеспечивает минимум интенсивности износа инструмента при оптимальной температуре резания Θ0, инвариантной к изменению элементов сечения срезаемого слоя, геометрии инструментов, СОТС и ряду других технологических факторов. Работа на оптимальной скорости резания обеспечивает также максимум длины пути резания, максимум удельной размерной стойкости инструмента, более высокое качество обработанной поверхности.
При назначении оптимальных режимов резания (на токарную, сверлильную, фрезерную и протяжную операции) рекомендуется использовать учебное пособие [10] или расчет производить по нижеприведенным зависимостям.
При чистовой обработке конструкционных сталей (при точении) расчет оптимальных скоростей резания, обеспечивающих максимальную размерную стойкость инструмента, рекомендуется вести с использованием следующих зависимостей [3].
При точении конструкционных сталей резцами Т15К6
(1.1)
где σв – предел прочности (от 37 до 92 кгс/мм2);
s – подача, мм/об;
t – глубина резания, мм.
При продольном точении жаропрочных никелевых сплавов резцами ВК6М
(1.2)
где Sв – действительный предел прочности
Sв=σв(1+δ), (1.3)
где δ – относительное удлинение, %,
или
(1.4)
где r – радиус резца при вершине, мм;
φ – главный угол в плане, град.
При торцевом точении жаропрочных никелевых сплавов резцами ВК6М
(1.5)
При точении титановых сплавов резцами ВК6М
lgV0=1,0795+0,074lgβ–0,5158lgs+0,2192lgr–0,1151lgt+
+0,0087 lgslgβ–0,0636lgβlgr+0,0594lgβlgt+0,0213lgslgr+
+0,3026lgslgt–0,0771lgrlgt, м/мин (1.6)
или
(1.7)
где β – количество фазы, %.
При торцевом фрезеровании жаропрочных никелевых сплавов фрезой с пластинками ВК6М в широком диапазоне изменения действительного предела прочности Sв подачи sz, глубины резания t, радиуса при вершине r и главного угла в плане φ [9]
(1.8)
При торцевом фрезеровании литейных жаропрочных никелевых сплавов фрезой с использованием твердого сплава ВК8 [18]
м/мин, (1.9)
где Sк – истинное сопротивление разрыву, Н/мм2,
Sк =С(γ')х,
γ' – % упрочняющей γ'-фазы в жаропрочном сплаве типа Ni3(Al, Ti).
При использовании инструментов с износостойкими покрытиями рабочих поверхностей «…наиболее выгодно эксплуатировать инструмент с покрытием на оптимальных скоростях резания, минимизирующих износ инструмента, которые на 30–50 % превышают оптимальные скорости резания для инструмента без покрытия» [2].
При выборе или расчете скорости резания, в случае использования при обработке СОТС, необходимо учитывать их влияние на качество обработанной поверхности и производительность обработки. При этом смазывающий эффект СОТС приводит, как правило, к снижению интенсивности износа инструмента и улучшению качества обработанной поверхности, а охлаждающий эффект позволяет увеличить значение оптимальной скорости резания на 20–30 %, что ведет к повышению производительности обработки.
7. Выбранная скорость резания корректируется с учетом реальной геометрии инструмента, использования СОТС, износостойких покрытий на рабочих поверхностях инструментов др. технологических факторов.
8. Определяется число оборотов шпинделя станка п (при точении, фрезеровании и сверлении), которое корректируется по станку (для универсального оборудования), и подсчитывается действительная скорость резания.
9. Производится проверка выбранного режима резания по прочности механизма подачи и мощности станка.
Дата добавления: 2018-02-15; просмотров: 1504; Мы поможем в написании вашей работы! |
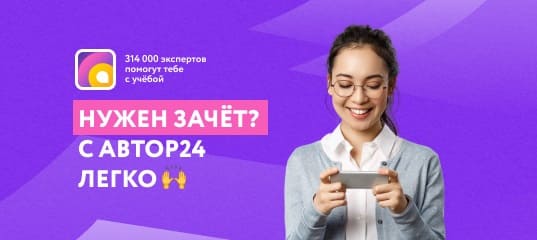
Мы поможем в написании ваших работ!