Анодно-механическая обработка
Основана на комбинированном электрохимическом, (электролиз), электротермическом (электроэрозия) и механическом разрушении металлов и других токопроводящих материалов. На рисунке 6.84 показаны схемы анодно-механической обработки и конструкция анодно-механического станка .
![]() |
Рисунок 6.84 - Схемы анодно-механической обработки |
Зазор между инструментом-катодом и заготовкой-анодом заполняют электролитом. Иногда заготовку помещают в ванну с электролитом. При прохождении постоянного тока на обрабатываемой поверхности заготовки появляется пленка, не проводящая электрический ток. При этом процесс анодного растворения заготовки прекращается. Для его продолжения пленку удаляют механически при перемещении режущего инструмента.
Электротермическое (электроэрозионное) разрушение происходит при возбуждении искровых разрядов между участками заготовки и инструментом, где пленка удалена. Электрические разряды создают высокую температуру, происходит процесс электроэрозии металла и на поверхности заготовки образуется впадина. Разряд: на этом участке прекращается и возбуждается на соседних участках.
При черновой обработке, когда требуется лишь высокая производительность процесса по съему металла, должен преобладать электротермический процесс. При чистовой обработке должен преобладать электрохимический процесс анодного растворения и механического удаления анодной пленки инструментом. Чистота обработанной поверхности достигает Rz 0,32…0,63 мкм, однако производительность процесса мала.
|
|
Электроконтактная обработка
При этом способе обработки разрушение металла происходит под действием электродуговых разрядов 1 при быстроперемещающемся инструменте без применения электролита.
Типовые схемы электроконтактной обработки приведены на рисунке 6.85.
![]() |
Прохождение электрического тока высокой плотности сопровождается выделением тепла в местах соприкосновения инструмента с заготовкой за счет высокого контактного сопротивления, что приводит к резкому местному повышению температуры на заготовке. Металл заготовки расплавляется и удаляется быстро вращающимся инструментом. Инструмент имеет относительно низкую температуру благодаря большой скорости вращения (30…80 м/с) и применению охлаждения. Для лучшего удаления частиц расплавленного металла используют cтрую сжатого воздуха.
Электроконтактную обработку применяют для прошивания отверстий металлической трубкой, прорезания пазов вращающимся диском, для сглаживания шероховатостей поверхности металлических изделий и другой черновой обработки.
|
|
Ультразвуковая обработка
Ультразвуковая обработка основана на явлении магнитострикции, т. е. изменении размеров ферромагнитного сердечника, помещенного в магнитное поле, изменяющееся с ультразвуковой частотой 15…20 кГц.
Схема ультразвуковой обработки отверстия показана на рисунке 6.86.
![]() |
При появлении магнитного поля сердечник 1 уменьшается в размерах поперечного сечения и удлиняется. Для увеличения амплитуды колебаний его торца сердечник соединяют с концентратором колебаний 2, что позволяет получить амплитуду колебаний пуансона-инструмента 3 в пределах 0,02…0,06 мм. Заготовку 4 помещают в ванну, куда подается абразивная суспензия (абразивный материал и вода). Энергия колебательного движения пуансона-инструмента передается абразивным частицам, которые имеют скорость 40…50 м/с. При ударе частиц абразива по обрабатываемой поверхности заготовки происходит местное разрушение материала.
Прокачивание суспензии способствует удалению продуктов разрушения и поступлению в зону обработки свежего абразива.
Производительность процесса ультразвуковой обработки зависит от амплитуды и частоты колебаний, размера абразивных зерен, концентрации суспензии и других параметров.
|
|
Ультразвуковую обработку применяют, например, для прошивания отверстий в заготовках из твердых и хрупких материалов, требующих высокой чистоты поверхности, точности формы и размеров.
Наиболее эффективно обрабатываются хрупкие материалы: стекло, керамика, алмаз, германий, фарфор и др.
Несколько хуже обрабатываются металлокерамические твердые сплавы, стали высокой твердости, при обработке которых происходят микропластические деформации.
Ультразвуковой метод обработки позволяет получить изделия с с высокой точностью и чистотой обработанной поверхности.
Ультразвуковую обработку применяют также для интенсификации процессов травления, удаления окалины, жировых и масляных пленок и т. д.
Электрохимическая обработка
Метод обработки основан на анодном растворении металла при пропускании через раствор электролита постоянного электрического тока.
Электрохимическое травление (рисунок 6.87,а) используют для очистки поверхности металлов от окислов, ржавчины, жировых пленок и других загрязнений.
|
|
![]() |
Рисунок 6.87. Схемы электрохимической обработки |
В ванну 1, заполненную электролитом, помещают обрабатываемую заготовку – анод 2 и катоды 3. В качестве электролита используют растворы кислот или щелочей, нагретые до 60…80° С.
Электрохимическое полирование. Струя электролита 1 прокачивается с большой скоростью по зазору между катодом 2 и обрабатываемой деталью – анодом 3. при пропускании тока большой плотности интенсивно растворяются выступы (гребешки) на обрабатываемой поверхности
(рисунок 6.87,б).
Преимущественное разрушение гребешков происходит благодаря более высокой плотности тока на их вершинах. Кроме того, во впадинах образуется пленка из продуктов растворения, которая защищает их от действия тока. Интенсивность съема металла составляет 3…10 мкм/мин. Продолжительность обработки 4…10 мин.
Процесс полирования состоит из следующих этапов:
- предварительного шлифования;
- химического травления;
- собственно полирования;
- промывания в холодной воде;
- промывания в щелочи для окончательного удаления кислоты;
- промывания в проточной воде;
- протирки и сушки.
Состав электролита: фосфорная или серная кислота, хромовый ангидрид и др.
Электрополирование применяют для заготовок из черных и цветных металлов, а также для окончательной отделки поверхностей режущих и измерительных инструментов.
Этот способ обработки улучшает чистоту поверхности, повышает коррозионную стойкость, усталостную прочность. Полированная поверхность имеет большую отражательную способность, поэтому этот процесс часто называют глянцеванием.
На рисунке 6.45,в показана схема процесса непрерывного электрополирования проволоки и ленты.
Электрохимическая размерная обработка заключается в направленном анодном растворении металла при высоких плотностях тока. В качестве примера на рисунке 6.45,г приведена схема электрохимического прошивания отверстия в заготовке 1. Проточный электролит поступает через трубчатый катод 2, заполняет полость 3 под прижимом 4 и откачивается для повторного использования. Высокая плотность тока и большая скорость потока электролита интенсифицируют процесс растворения: скорость съема металла достигает 500…200 мкм/мин.
Электрохимическую размерную обработку применяют для высокопрочных, труднообрабатываемых материалов, нежестких тонкостенных изделий, обеспечивая высокое качество и точность обработанной поверхности.
Лучевые методы обработки
Лучевые методы обработки основаны на снятии обрабатываемого материалапод воздействием лучей, имеющих чрезвычайно высокую плотность энергии. Удаление материала осуществляется преобразованием лучевой энергии в теплоту непосредственно в зоне резания.
К лучевым методам обработки относится резание электронным, ионным, световым и плазменным лучами.
Электроннолучевая обработка выполняется фокусированным пучком электронов, испаряющих металл.
Отличительными особенностями размерного электроннолучевого резания по сравнению со сваркой электронным лучом является острая фокусировка луча с повышенной плотностью энергии и импульсная его подача.
Режимы резания электронным лучом определяются плотностью тока в луче, величиной ускоряющего напряжения, плотностью тока в фокальном пятне на заготовке, скоростью перемещения луча по заготовке, частотой , повторения и длительностью импульса.
Достоинства электроннолучевой обработки:
- возможность обработки сверхпрочных материалов;
- получение глухих и сквозных отверстий очень малых размеров.
Этот способ обработки применяют, например, для сверления отверстий диаметром 5…10 мкм,
Недостаток – сложность и высокая стоимость оборудования, ограничение габаритов обрабатываемых деталей.
Ионнолучевая обработка основана на использовании явления катодного распыления, возникающего при тлеющем газовом разряде.
Электроны, эмиттируемые катодом, ионизируют молекулы газа. Ионы ускоряются сильным электрическим полем и фокусируются в узком конусе, вершина которого совпадает с поверхностью обрабатываемой детали. Этот способ применяют для прошивки отверстий от 5 мкм и больше в тонком листовом материале, а также для сверления отверстий в алмазах. Время на ионную обработку относительно больше, чем при других лучевых методах обработки, но энергии затрачивается меньше.
Светолучевая (лазерная) обработка. Для резания применяют узкий направленный пучок видимого света с высокой плотностью тепловой энергии, получаемый в лазерах – оптических квантовых генераторах. Поэтому этот способ иногда называют лазерной обработкой.
Обрабатываемость материалов световым лучом определяется теплофизическими свойствами материалов (температурой плавления и кипения, теплоемкостью, теплопроводностью), а также их отражательной способностью. Для уменьшения отражения луча от поверхности ее делают матовой.
Этот способ обработки применяется для получения отверстий малого диаметра, резки материалов высокой прочности по заданному контуру, прорезки пазов и щелей шириной в несколько микрометров.
В сравнении с другими лучевыми методами светолучевая обработка обладает высокой производительностью – до 100 мм3/мкм и особенно эффективна при изготовлении алмазных фильер, тончайших сеток, сит и т. п. На специальных станках с программным управлением можно сверлить десятки отверстий в минуту.
В настоящее время широко используется лазерная резка листового и другого проката.
Достоинства этого метода в сравнении с электронно-лучевой: удобство обслуживания, отсутствие вакуумных систем, большая удельная мощность.
Плазменно-лучевая обработка используется чаще всего для разрезания относительно толстых листов из алюминиевых сплавов (до 125 мм), нержавеющих сталей (до 100 мм). Скорость резки составляет 16…75 м/ч. Плазменная струя используется при предварительном черновом точении прочных материалов, в особенности литых заготовок с труднообрабатываемой коркой значительной толщины. Плазменная горелка устанавливается под углом 40…60° к поверхности вращающейся детали, струя плазмы расплавляет и выдувает расплавленный металл.
Вопросы для самоконтроля
Дата добавления: 2018-02-15; просмотров: 1779; Мы поможем в написании вашей работы! |
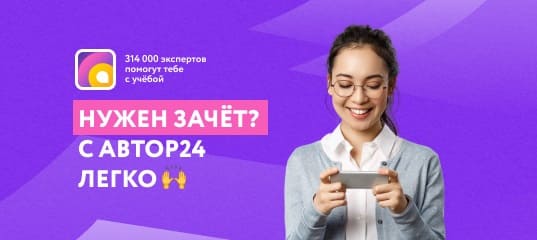
Мы поможем в написании ваших работ!