Работы и ресурсы в Project 2003
Работы определяются такими показателями как продолжительность, трудоемкость и количество ресурсов. В зависимости от правил формирования взаимосвязи этих показателей в Project используются следующие виды работ:
- составные работы;
- вехи;
- работы с фиксированной продолжительностью;
- работы с фиксированной численностью ресурсов;
- работы с фиксированной трудоемкостью.
Составные работы позволяют формировать иерархическую структуру работ графика. Каждая из составных работ может включать произвольное количество любых перечисленных выше типов, в том числе и составных.
Вехи представляют собой работу с нулевой продолжительностью- событие. Введение таких работ в график часто бывает удобно для того , чтобы контролировать качественно важные моменты, например, завершение некоторой фазы проекта.
Тип работы для работ других типов определяется при помощи специального поля Type , которое может иметь значение Fixed Duration Fixed Units и Fixed Work соответственно.
Влияние основных показателей друг на друга для работ различных типов имеют существенные особенности, характеристики которых приведены в таблице 1.
Правила преобразования показателей работ разных типов в Project
Таблица 2.7
Не переносится
|
| ||||
| |||||
| |||||
| |||||
| |||||
N=Q/Ti | |||||
N=Qi/T | |||||
Суммарное число единиц ресурсов Nн | Т=Q/Ni | Q=const | Ni |
В Project единицами времени могут быть минуты, часы, дни и недели.
Виды ресурсов. При реализации проектов используют ресурсы: рабочее время машин, рабочих, материалы, энергия или финансовые средства.
Задание значения потребности в ресурсах для любой работы или для ресурса в целом производится в процентах. Таблицы загрузки ресурсов являются основой двух форм представления данных о проекте:
- сводных данных о загрузке ресурсов (Resource Usage);
- таблицы данных о загрузке ресурсов с разбивкой по работам (Task Usage).
Для формирования диаграммы загрузки ресурсов следует выполнить команду View,Resource Graph.
Создание графиков является важным элементом определения работ и непременным этапом работы над проектом.
Рекомендуемая последовательность создания графика проекта следующая:
- определение опорных дат проекта;
- создание перечня работ с оценкой их продолжительности;
- организация иерархической структуры работ графика;
|
|
- формирование ресурсного обеспечения;
- сохранения файла.
Предлагаемая последовательность формирования модели проекта является типовой, но может варьироваться пользователем по своему усмотрению с учетом условий и объема работы.
Важнейшим процессом управления проектом является управление циклом реализации проекта с применением метода критического пути. При этом для каждой работы графика Project автоматически вычисляет значения:
- ранней даты начала
- ранней даты окончания,
- поздней даты начала,
- поздней даты окончания,
- полного резерва времени,
- свободного резерва времени.
Project 2003 обеспечивает поддержку процессов управления финансами, которые включают анализ выполнения проекта и определения потребности в финансовых ресурсах для отдельных работ графика. Project 2003 позволяет учитывать потребность в финансовых ресурсах уже на самых ранних стадиях проекта и обеспечивает автоматическое суммирование затрат как по элементам работ, так и по всему графику в целом.
Методика проведения лабораторной работы
Получить у преподавателя задание на разработку проекта.
2. После включения компьютера найти программу MS Project 2003 и открыть ее. На левой панели открывшегося окна выбрать диаграмму Gant Chart и открыть ее. Выполнить команду Project, Project Information,а в открывшемся окне выбрать опорную дату проекта Project Start Date(дата начала работ). Ввести опорную дату проекта в поле Start date и нажать клавишу OK.
|
|
3. В открытом окне линейной диаграммы Gant Chart выделить в первой строке ячейку колонки Task name (наименование работ) и ввести с клавиатуры первую работу проекта, а затем ввести последовательно наименование всех последующих работ в соответствии с заданием на разработку проекта.
4. В этой же диаграмме Gant Chart для обеспечения ввода Duration (продолжительности работ) выполнить команду Format,Timescale и в диалоговом окне в группе Major scale и Minor scale в списковом окне Units выбрать единицу времени, используемую при разработке проекта. Система позволяет оценивать продолжительность работ в любой единице времени.
5. В последующем требуется ввести ресурсы (специальности), для чего необходимо в диаграмме Gant Chart выполнить команду View, Resours sheet, и на экране сформированного окна в колонку Resours Name ввести полный список всех определенных проектом ресурсов. Здесь же требуется ввести максимальное количество ресурса в колонку Max Units (100%),часовую тарифную ставку для каждого ресурса (Std Rate).
|
|
6. Объем работ, выполненных ресурсом каждого вида при введенных ранее продолжительности работ и количества единиц ресурсов, будет вычислен автоматически: Work=Duration*Unit,
где Work-трудоемкость назначения,
Duration –продолжительность работ
Units- количество единиц ресурсов.
Открыть на левой панели экрана диаграмму Task Usage и просмотреть данные этой диаграммы.
7. Следующим этапом лабораторной работы является установление связей между работами. В соответствии с возможностями Project для любой пары взаимосвязанных работ можно задать любой из типов связи. Комплекс зависимостей между работами часто называют логической структурой проекта, а связи образуют структуру сети. В соответствии с установленными связями, работы делятся на предшествующие и последующие. Предшествующая работа является обеспечивающей, т. е. для начала выполнения последующей работы требуется выполнение всех предшествующих. Для установления связи между работами в графическом режиме необходимо выполнить следующие действия. Выбрать тип пиктограммы (связь-цепь) на панели управления, затем указать курсором на задачу предшественницу (Predecessors) и, не отпуская мышь, перевести курсор на последующую работу (Successors). Эта операция позволяет установить жесткую связь типа (конец-начало). В дальнейшем устанавливаются связи между оставшимися работами.
Кроме связи типа конец-начало (Finish-to-Start) формами связи между работами могут быть: конец-конец (Finish-to-Finish), начало-начало (Start -to– Start), начало-конец (Start-to-Finish).
Связь конец-начало – наиболее часто встречающаяся зависимость, при которой последующая работа не может быть начата, пока не завершена предшествующая.
Связь конец-конец – используется, если окончание последующей работы зависит от окончания некоторой работы (предшественницы), но начинаться работы могут независимо
Связь начало-начало – применяется для моделирования работ, которые должны выполняться одновременно.
Связь начало-конец – используется редко, но может быть полезна, когда при планировании требуется задержать окончание работы на как можно более длительный срок, связав ее окончание с началом другой работы.
8. Существует альтернативный вариант установления связей между работами. При формировании последовательности работ наиболее часто приходится выполнять следующие действия:
-определение списка работ, предшествующих текущей работе,
-разрыв связи между работами.
Для решения первой задачи необходимо выделить в Gant Chart любую ячейку в строке, соответствующей работе, для которой будет формироваться список предшествующих работ. Затем необходимо выполнить команду Project ,Task Information .В сформированном в результате окне в ячейке колонки ID ввести при помощи клавиатуры номер предшествующей работы и завершить ввод нажатием клавиши (Enter). В соответствующей строке столбца Task Name автоматически появится наименование предшествующей работы, а в столбце Tupe появится значение Finish-Start (FS). Повторить эти действия необходимое количество раз для каждой из предшествующих работ, а для завершения ввода работ, предшествующих отмеченной работе, нажать кнопку ОК.
При необходимости изменения установленного по умолчанию характера связи между работами следует установить курсор на нужную ячейку столбца Type и отметив ее, щелкнув левой кнопкой мыши. Затем выбрать нужную форму связи и нажать кнопку ОК.
9. В практике имеют место случаи необходимости удаления связей между работами. Для удаления связей на диаграмме Gant Chart курсор необходимо установить на строку, связанную с подлежащей удалению и выполнить команду Task Information,затем установить курсор в строке в колонке Tape и нажать клавишу (Delete).Для удаления связей следует нажать кнопку ОК.
10. Важнейшим процессом управления проектом является управление циклом реализации проекта. Project 2000 позволяет определить критические пути. Для контроля критического пути графика наиболее важными являются следующие возможности:
- определение продолжительности критического пути, дат начала и окончания работ;
- визуальное выделение критического пути при помощи форматирования;
- применение фильтров с тем, чтобы иметь возможность сосредоточить внимание только на работе критического пути
Для определения продолжительности критического пути, дат начала и окончания работ необходимо выполнить команду Project, Project Information.
Определить дату начала работ в поле Start Date и дату окончания в поле Finish Date. Для визуального выделения работ критического пути необходимо в Gant Chart выполнить команду Project, Filtered for, Critical и нажать левую кнопку мыши. Выполнить командуTools, Option, Options и затем выбрать вкладку View и установить флажок Show summury task в группе Outline options. На экране будет выделен критический путь.
11. На следующем этапе лабораторной работы необходимо просмотреть на левой панели следующие формы:
Calendar - календарное расписание
Gant Chart - диаграмма Гантта
Network diagram - сетевая диаграмма
Task Usage - таблица загрузки ресурсов
Tracking Gant - линейная диаграмма хода работ
Resource Graph - диаграмма загрузки ресурсов
Resource sheet - сводные данные о ресурсах
Resource Usage - таблица загрузки ресурсов
More Views - другие таблицы
По данным этих диаграмм выполнить индивидуальное задание преподавателя.
ЛАБОРАТОРНОЕ ЗАНЯТИЕ 3
«Организация группового производства деталей»
Одним из направлений повышения производительности труда и успешного выполнения плановых заданий по изготовлению продукции машиностроения на судостроительно-судоремонтных предприятиях может быть организация группового производства.
Групповое производство – это прогрессивная в технико-экономическом отношении форма организации прерывных производственных процессов, экономико-организационной основой которой является целевая - подетальная или предметная - специализация участков и цехов, а технологической составляющей – унифицированная групповая форма организации технологических процессов.
Одной из форм организации в условиях единичного и мелкосерийного производства, обеспечивающей возможность в наиболее полной мере реализовывать принципы рациональной организации производственного процесса, характерного для массового производства, является подетально-групповая специализация. При подетально-групповой специализации цехи (участки) организуются по принципу конструктивно-технологического подобия деталей независимо от того, для какого изделия или узла предназначена деталь.
В основе группового метода лежит принцип классификации и группирования деталей по определенным признакам и создание для этих групп унифицированных процессов изготовления деталей.
Для судоремонтных предприятий, работающих в условиях единичного и малосерийного производства, наиболее целесообразным будет использование метода группирования деталей по типу оборудования, единству технологического оснащения, общности наладки станка с использованием комплексной детали.
Под комплексной деталью понимается реальная или условная (искусственно созданная) деталь, содержащая в своей конструкции все основные элементы (поверхности), характерные для деталей данной группы, и являющаяся ее конструктивно-технологическим представителем.
Именно на комплексную деталь разрабатывается групповой технологический процесс, проектируется групповая оснастка, приспособления. Повышенная себестоимость группового приспособления по сравнению с индивидуальным экономически оправдывается, так как затраты раскладываются на все детали, входящие в группу.
Затраты вспомогательного, подготовительно-заключительного времени, а также простои оборудования по организационно-техническим причинам при внедрении групповой обработки уменьшаются.
Одной из причин низкого уровня развития группового производства в настоящее время является отсутствие четкой системы в организации внедрения, которое осуществляется без должной целенаправленности и учета достигаемого эффекта.
При проведении мероприятий по развитию группового производства на предприятиях прежде всего необходимо оценивать существующий и планируемый на перспективу уровень. Такая задача может быть решена с помощью соответствующих показателей.
Состояние и развитие группового производства должны оцениваться в двух взаимосвязанных направлениях:
а) по уровню внедрения группового производства (Кг.п.);
б) по уровню групповой технологии (Кг.т.).
Первый показатель дает совокупную количественную оценку развития на предприятии форм группового производства по механообрабатывающей (или заготовительной) стадии. Может быть определен по отдельным участкам, цехам и в целом по предприятию.
Второй показатель характеризует глубину захвата унифицированной групповой технологией процессов обработки деталей в указанных подразделениях.
Однако, прежде чем установить показатели Кг.п. и Кг.т , требуется определить удельные значения группового производства Уг.п. и групповой технологии Уг.т..
В качестве расчетной единицы, обеспечивающей соизмеримость всех указанных показателей и объективность полученных результатов, принимается трудоемкость.
Показатель удельного значения группового производства в j-й системе (участок, цех, предприятие или стадия технологического процесса) определяется соотношением
(3.1)
где Qпсj – трудоемкость годового объема работ, выполняемых в j-й системе на подетальных или подетально-групповых участках (в цехах, на предприятии), нормо-час;
Qoj – общая трудоемкость годового объема работ j-й системы, нормо-ч.
Тогда показатель достигнутого (или планируемого) уровня развития группового производства в j-й системе составит
(3.2)
где kг.п.j – коэффициент перспективного (или планируемого) уровня охвата деталей (заготовок) групповым производством.
Аналогично определяются показатели удельного значения групповой технологии и достигнутого (или планируемого) уровня ее внедрения (развития) в подетально-специализированных подразделениях (цехах, участках, групповых линиях):
(3.3)
где Qг.т.j – трудоемкость годового объема работ, выполняемых подетально-специализированными подразделениями j-й системы по групповой технологии, нормо-ч;
(3.4)
где kг.т.j - коэффициент перспективного (или планируемого) уровня охвата процессов обработки деталей (заготовок) групповой технологией.
Для определения ожидаемой (прогнозируемой) эффективности от внедрения группового производства необходимо рассчитать показатель специализации рабочих мест j-й системы:
С достаточной степенью точности коэффициент специализации может быть определен по формуле:
(3.5)
где s – число станков;
Уг.т. – уровень групповой технологии;
До – количество деталеопераций, выполняемых системой в течение месяца.
Показатель КСПj определяет среднее число приведенных детале-операций, приходящихся на одно рабочее место системы в течение месяца. Он характеризует частоту прерывности процессов на рабочих местах j-й системы (КСПj³1). Нетрудно убедиться, что при отсутствии в системе групповой обработки Уг.т.j= 0, и тогда коэффициент специализации КСПj равен коэффициенту закрепления операций КЗОj, а при выполнении системой всего объема работ только по групповой технологии Уг.т.j =1, и тогда КСПj <<КЗОj .
В показателе КСПj синтезируется влияние большого числа факторов, воздействующих на конечные экономические результаты производственного процесса и для расчета ожидаемых значений показателей в процентах при переходе от технологической специализации к подетально-специализированным участкам можно использовать следующие зависимости:
(3.6)
(3.7)
(3.8)
где - показатель, отражающий рост производительности труда;
- показатель, отражающий снижение себестоимости продукции;
- показатель, отражающий сокращение производственного цикла.
Приведенные зависимости позволяют прогнозировать улучшение технико-экономических показателей в действующих групповых системах в результате внедрения мероприятий по совершенствованию конструкции, технологии, организации труда. В этом случае по формуле (3.5) вначале определяют значения в существующих и
в планируемых условиях, а затем находят по два значения соответствующих им показателей
и
(производительность труда), DС1 и DС2 (себестоимость продукции), DТц1 и DТц2 (длительность цикла) и по их разности определяют прирост показателей.
Определим наиболее важный показатель – показатель роста производительности труда DПТ. Для его определения необходимо:
· разработать комплексную деталь (по заданному варианту). Вариант выбирается по табл. 3.1 и рис. 3.1;
· определить трудоемкость изготовления заданных по варианту деталей групповым методом;
· определить трудоемкость изготовления остальных деталей по существующей технологии;
· определить по формуле (3.3) показатель удельного значения объема работ, выполняемых подетально-специализированным участком по групповой технологии;
· рассчитать количество станков, необходимых для выполнения заданной программы при работе по существующей организации SC и при работе по проектируемой организации (с частичным изготовлением деталей групповым методом) SП.
Расчет количества станков производится по формуле
(3.9)
где Q – трудоемкость, нормо-ч;
Фд – действительный фонд рабочего времени, ч;
Кп – коэффициент переработки норм;
Кз – коэффициент загрузки оборудования.
Сокращение числа станков может быть определено как разность
DS = SС – SП (3.10)
Далее по формуле (3.5) определяется коэффициент специализации при существующей организации и
при частичном применении группового метода. По формуле (3.6) находится планируемый рост производительности труда DПТ.
Пример выполнения работы
1. В соответствии с заданным вариантом (например, перевод на групповую технологию деталей № 1 и № 2 по рис. 4.1) разрабатываем комплексную деталь.
При построении комплексной детали используется ПЭВМ и применяется прикладная программа «ACAD».
Последовательность построения комплексной детали:
Включить персональный компьютер. Осуществить запуск программы «ACAD». После появления на экране дисплея стандартной пусковой заставки (Главное меню) просмотреть команды ввода.
Дать название будущему рисунку комплексной детали. Дать команду нажатием клавиш «1» «RETURN». После появления на экране дисплея поля построения рисунка и координатного визира, нажать «RETURN» для вывода на экран списка имеющихся команд. Ознакомится со списком команд. Затем вернуться на поле построения рисунка.
Поле построения представляет собой графический редактор, который состоит из графической зоны, подающего меню, экранного меню, окна ввода команд. Команды можно ввести двумя способами: а – с клавиатуры, б – мышью. Повтор команды: RETURN или пробел. Отказ от команды Ctrl + C.
Диалог с ПЭВМ при построении комплексной детали необходимо осуществлять с помощью меню. Экранное меню работает без мышки. Подающее меню – подсвечивается мышью.
Выбрать на экранном меню метку «рисуй», нажать «RETURN». В зависимости от сложности строящейся комплексной детали дать одну из следующих команд: отрезок, круг, полоса, эллипс, кольцо, дуга, линия, фигура. Задать координаты узловых точек комплексной детали. Либо с клавиатуры, либо мышью.
Построение деталей необходимо вести в относительной декартовой системе координат (система задана ранее).
Для редактирования рисунка следует обратиться в подающее меню к разделу «Редактор», где выбираются требуемые процедуры.
Построенную комплексную деталь предъявить преподавателю и если потребуется откорректировать ее, по завершению построения комплексной детали дать команду «конец» с клавиатуры или обратиться к подающему меню – (окно файлы) и мышью установить курсор на команду «конец» и нажать клавишу.
После выхода в «Главное меню» нажать последовательно клавиши «0» и RETURN.
На этом работа с программой «ACAD» завершается.
2. Определяем по исходным данным табл. 4.1 трудоемкость изготовления
деталей №№ 1 и 2.
Групповым методом:
Qг.т.=åtini= 2´500+3´400=1000+1200=2200 нормо-ч.
По существующей организации:
Q1,2=3´500+4,5´400=1500+1800=3300 нормо-ч.
3. Определяем по исходным данным табл. 4.1 и 4.2. трудоемкость изготовления остальных деталей (с №3 по № 10) по существующей организации:
нормо-ч.
4. Определяем уровень групповой технологии
.
5. Определим число станков:
при существующей организации ед.
при частичном переходе на групповой метод ед.
Сокращение числа станков составит:
DS=SC – SП=8 – 7 =1 ед.
6. Определим коэффициент специализации при внедрении группового метода
Для определения количества деталеопераций До воспользуемся табл. 3.1. Для изготовления 500 шт. деталей № 1 необходимо выполнить 500´6=3000 деталеопераций, а для изготовления 400 шт. деталей № 2 необходимо выполнить 400´7=2800 деталеопераций, следовательно, До=3000+2800=5800 деталеопераций.
Тогда,
КСП= .
7. Определяем повышение производительности труда.
Расчет ведется в натуральных показателях и при условии, что на каждом станке работает один станочник.
aс= дет/чел;
aп= дет/чел;
Daп=aп - aс = дет/чел;
DПТ = .
Работа 4 «Организация и эффективность внедрения
гибких производственных систем»
Цель лабораторной работы.
Целью работы является:
- приобретение знаний о структуре гибких производственных модулей (ГПМ), роботизированных технологических комплексов (РТК), гибких производственных систем (ГПС) и составе капитальных и текущих затрат, связанных с их созданием и эксплуатацией;
- освоение практических навыков в решении задач повышения эффективности производства.
Организация ГПС
Общие положения
В работе рассматривается процедура обоснования уровня автоматизации производства путем сопоставления экономических показателей четырех систем разного организационного уровня: базового варианта на основе станков с числовым программным управлением (ЧПУ) или универсального оборудования; автономно функционирующих гибких производственных модулей (ГПМ), роботизированных технологических комплексов (РТК); гибких производственных систем (ГПС) (рис. 4.1).
В ГПМ входит единица технологического оборудования, оснащенная автоматизированным устройством программного управления и средствами автоматизации технологического процесса. ГПМ – это автономно функционирующая система, осуществляющая многократные циклы и имеющая возможность встраивания в систему более высокого уровня.
РТК – это совокупность единицы технологического оборудования, промышленного робота (ПР) и средств оснащения, автономно функционирующая и осуществляющая многократные циклы. При этом РТК, предназначенные для работы в ГПС, обладают автоматической переналадкой и возможностью встраиваться в систему.
ГПС – это совокупность в разных сочетаниях оборудования с ЧПУ, ГПМ, РТК, отдельных единиц технологического оборудования и систем их обеспечения функционирования в автоматическом режиме в течение заданного интервала времени, обладающая свойством автоматизированной переналадки при производстве изделий произвольной номенклатуры.
Выбор того или иного варианта автоматизации производства основывается на сопоставлении показателей экономической эффективности инвестиций: срока окупаемости, рентабельности инвестиций, внутренней нормы доходности, чистой текущей стоимости.
Основными источниками повышения эффективности производства в условиях гибкой автоматизации по сравнению с базовым вариантом являются:
- повышение производительности труда за счет более полного использования технических возможностей оборудования, увеличения коэффициента машинного времени;
- увеличение сменности работы оборудования;
- повышение производительности труда за счет замены ручного и машинно-ручного труда автоматизированным (на основных и вспомогательных операциях);
- сокращения потерь рабочего времени основных и вспомогательных рабочих;
- уменьшение количества применяемой оснастки;
- сокращение количества требуемого технологического оборудования, а значит, и производственных площадей;
![]() |
Составные части ГПС Система обеспечения функционирования ГПС
![]() |



ГПМ Основное технологическое оборудование РТК Автоматизированное транспортно-складская система
Дата добавления: 2018-02-15; просмотров: 427; Мы поможем в написании вашей работы! |
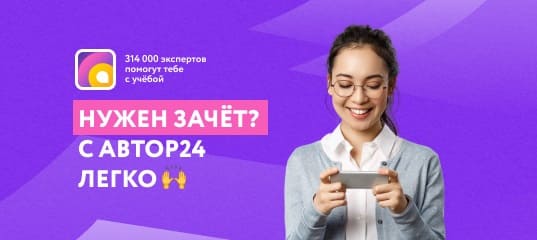
Мы поможем в написании ваших работ!