Описать основные свойства, состав, способы получения, область применения строительной извести
О сновные свойства и состав.
Известь - неорганическое вяжущее вещество.
Воздушная известь - продукт умеренного обжига кальциево-магниевых карбонатных горных пород: мела, известняка, доломита с содержанием глины не более 6%. Известняк в основном состоит из карбоната кальция СаСО3. Обжигают известняк при 900 - 12000С до возможно более полного удаления СО2 по реакции:
СаСО3 = СаС + СО2.
Продукт обжига содержит, кроме СаО (главной составной части), также некоторое количество оксида магния, образовавшегося в результате термической диссоциации содержащегося в известняке
MgCO3 = MgO + CO2
Химико-минеральный состав и свойства извести, как и любого вяжущего, зависят от гидравлического модуля и температуры обжига сырья.
Гидравлический модуль m выражает содержание основного оксида СаО по отношению к суммарному количеству кислотных оксидов, %:
m = .
У воздушной извести самый большой гидравлический модуль, m = 9%.
Воздушная известь не обладает гидравлическими свойствами, её прочность на сжатие после 28 суток твердения невелика - около 0,4 МПа; m гидравлической извести составляет 1,7 - 9%;
Таблица 32. 1. Важнейшие показатели качества воздушной извести (негашеной комовой или молотой).
Показатели. | Сорт. | ||
I | II | III | |
Содержание активных (СаО + МgО) в пересчёте на сухие вещества, не менее, % Содержание непогасившвшихся зёрен в негашеной извести, не более, % | 90 7 | 80 11 | 70 14 |
|
|
Способы получения
Известняк обжигают чаще всего в шахтных печах (рис 32.1.).
Рис. 32.1. Шахтная печь для обжига извести. 1 - шахта; 2 - загрузочный механизм; 3 - дымосос; 4- подача воздуха; 5 - разгрузочный механизм.
В таких печах известняк поступает в виде кусков размером 8 - 20 см; обжиг мелких кусков известняка может производиться во вращающихся печах. Применяют тепловые установки для обжига известняка «в кипящем слое». Термическая диссоциация СаСО3 начинается при 9000С, в заводском производстве температура обжига составляет 1100 - 12000С в зависимости от плотности известняка и типа печи.
Шахтные печи состоят и з шахты, загрузочного и разгрузочного устройств, воздухопроводящей и газоотводящей аппаратуры. Известняк загружают в шахтную печь сверху, материал по мере выгрузки извести опускается вниз, а навстречу обжигаемому материалу просачиваются горячие дымовые газы. В печи одновременно происходит подогрев, подсушивание известняка, его обжиг (декарбонизация) и охлаждение. В пересыпных печах топливо (антрацит, кокс и т. п.) загружают слоями вперемежку с кусками известняка, поэтому к получающейся извести примешивается зола. В печах, работающих на газовом топливе, получают «чистую» и более дешевую известь. Процесс декарбонизации эндотермический (сопровождается поглощением теплоты): для разложения 1 г-моля СаСо3 затрачивается примерно 190 кДж. Расход топлива в шахтных печах сравнительно невысок: 13 - 16% массы обожженной извести, или 3800 - 4700 кДж на 1 кг СаО.
|
|
При обжиге известняка удаляется углекислый газ, составляющий 44% массы СаСО3, поэтому комовая негашеная известь получается в виде пористых кусков, активно взаимодействующих с водой.
Гашение воздушной извести заключается в гидратации оксида кальция при действии воды
СаО + Н2О = Са(ОН)2 + 65,5 кДж.
1 г-моль СаО выделяет 65,5 кДж теплоты, а 1 кг извести-кипелки - 1160 кДж. Гашение сопровождается разогревом массы вследствие значительного выделения количества теплоты.
Стехиометрически для полного гашения СаО требуется 32,1% воды (по массе), практически в зависимости от способа гашения берут воды в 2 - 3 раза больше, так как часть воды теряется в виде пара.
Известь гасят на специализированных растворных заводах в известегасильных машинах, в которых получается так называемое «известковое тесто». На небольших стройках известь сначала гасят в творилах и известковое тесто через сетку сливают в известегасильную яму. Известковое тесто выдерживают в такой яме в течение не менее двух недель.
|
|
В зависимости от количества воды, добавляемой к комовой извести, можно получить известковое тесто или гидратную известь - пушонку - в виде порошка.
Гашение извести в пушонку осуществляют в гидраторах непрерывного действия, где выделяющаяся теплота и водяные пары используются для превращения комовой извести в тончайший рыхлый порошок насыщенной плотности 400 - 450 кг/м3. При гашении в пушонку известь увеличивается в объёме в 2 - 3.5 раза. В большей степени «распушивается» высокоактивная известь с высоким содержанием СаО.
В процессе гашения куски негашеной извести самопроизвольно диспергируются, распадаясь на тонкие частицы Са(ОН)2 размером в несколько микрон. Воздушная известь отличается от других вяжущих веществ тем, что она превращается в тонкий порошок при помоле, а также путём гашения водой. Громадная удельная поверхность частиц Са(ОН)2 обуславливает большую водоудерживающую способность и пластичность известкового теста. После отстаивания известковое тесто содержит около 50% твёрдых частиц Са(ОН)2 и 50% Н2О. каждая частица окружена тонким слоем адсорбированной воды, играющей роль своеобразной гидродинамической смазки. Высокая пластичность известкового теста в смеси с песком - это свойство, которое так ценится при изготовлении строительных растворов.
|
|
Чем больше содержание основных оксидов (СаО + МgО) в извести, тем пластичнее известковое тесто и тем выше его сорт. Содержание непогасившихся частиц, к которым относятся частицы недожога и пережога, снижает качество извести. Недожогом называют оставшиеся зёрна сырья-известняка, которые отощают известковое тесто, ухудшают его пластичность и пескоёмкость. Пережог представляет собой остеклованный трудно гасящийся СаО, уплотненный при высокой температуре. Частицы пережога гидратируются очень медленно с увеличением своего объёма, что в дальнейшем вызывает растрескивание штукатурки или известковых изделий.
Твердение гашеной извести.
Известь применяется в идее строительных растворов, т. е. в смеси с песком и другими заполнителями. На воздухе известковый раствор постепенно отвердевает под влиянием двух противоположных факторов-процессов:
А) высыхания раствора, сближения кристаллов Са(ОН)2 и их срастания.
Б) карбонизации извести под действием углекислого газа, который в небольшом количестве содержится в воздухе:
Са(ОН)2 + СО2 = СаСО3 + Н2О.
Образовавшийся карбонат кальция срастается с кристаллами Са(ОН)2 и упрочняет известковый раствор. При карбонизации выделяется вода, поэтому штукатурку и стены, к которым применены известковые растворы, подвергают сушке. Известковые растворы твердеют медленно, сушка ускоряет процесс твердения. Для ускорения твердения часто в известковые растворы добавляют гипс и цемент. Применение цемента и активных минеральных добавок повышают водостойкость известковых растворов.
Молотая негашеная известь.
Молотую негашеную известь получают путём тонкого размола комовой извести без предварительного гашения. Строительные растворы и бетоны, приготовленные на негашеной извести, быстро схватываются и отвердевают вследствие гидратационного твердения негашеной извести. При правильно подобранном водоизвестковым отношением (0,9 - 1,5) кристаллы Са(ОН)2, получившиеся при гидратации СаО непосредственно в растворе СаО Н2О, срастаются между собой и быстро образуют прочный кристаллический сросток. Саморазогревание материалов (раствора, бетона), со своей стороны, способствует ускорению твердения и росту прочности раствора, что особенно важно при работах в зимних условиях.
В молотую негашеную известь и гидратную известь (пушонку) разрешается вводить тонкомолотые минеральные добавки: доменные и топливные шлаки, золы, известняк. Продукт совместного помола негашеной извести и карбонатной породы называют карбонатной известью.
Молотую негашеную известь обычно используют сразу после помола, так как вследствие поглощения влаги из воздуха она теряет свои вяжущие свойства
Дата добавления: 2021-04-24; просмотров: 64; Мы поможем в написании вашей работы! |
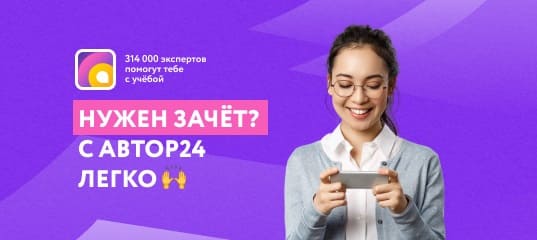
Мы поможем в написании ваших работ!