Описать способы химико-термической обработки стали: цементацию, азотирование, нитроцементацию, диффузионную металлизацию
Механические свойства строительных материалов: твердость материалов, методы определения твердости, шкала Мооса
Твердость - свойство материала сопротивляться местной пластической деформации, возникающей при внедрении в него более твердого тела.
Твердость минералов оценивают шкалой Мооса, представленной десятью минералами, из которых каждый последующий своим острым концом царапает все предыдущие. Эта шкала включает минералы в порядке возрастающей твердости от 1 до 10:
. Тальк 3MgO 4SiO2
H2 O - легко царапается ногтем.
. Гипс CaSO4 2H2 O - царапается ногтем.
. Кальцит CаCO3 - легко царапается стальным ножом.
. Флюорит (плавиковый шпат) CaF2 - царапается стальным ножом под небольшим нажимом.
. Апатит Ca(PO4 )3 F - царапается ножом под сильным нажимом.
. Ортоклаз K2 O Al2 O3
6SiO2 - царапает стекло.
. Кварц SiO2 -
. Топаз Al2 (SiO4)(F,OH)2
9. Корунд Al2 O3
. Алмаз C
Твердость древесины, металлов, бетона и некоторых других строительных материалов определяют, вдавливая в них стальной шарик или твердый наконечник (в виде конуса или пирамиды). В результате испытания вычисляют число твердости
НВ = Р / F
F - площадь поверхности отпечатка.
От твердости материалов зависит их истираемость: чем выше твердость, тем меньше истираемость.
Истираемость оценивают потерей первоначальной массы образца материала, отнесенной к площади поверхности истирания F
И = (m1 - m2) / F,
|
|
m1 и m2 - масса образца до и после истирания.
Сопротивление материала истиранию определяют пользуясь стандартными методами: кругом истирания и абразивами (кварцевым песком или наждаком). Это свойство важно для эксплуатации дорог, полов, ступеней лестниц и т. п.
Износом называют свойство материала сопротивляться одновременному воздействию истирания и ударов. Износ определяют на образцах материалов, которые испытывают во вращающемся барабане со стальными шарами или без них. Показателем износа является потеря массы пробы материала в результате проведенного испытания (% к первоначальной массе):
Из = (m1 - m2)/m1) ×100%.
Деформативные свойства
Основными деформативными свойствами строительного материала являются: упругость, пластичность, хрупкость, модуль Юнга (модуль упругости), коэффициент Пуассона, модуль сдвига, объемный модуль упругости (модуль всестороннего сжатия), предельные деформации (растяжения, сжатия), ползучесть. Другие характеристики могут определяться для специальных условий нагрузки.
Упругостью твердого тела называют его свойство деформироваться под влиянием нагрузки и самопроизвольно восстанавливать первоначальную форму и размеры после прекращения действия внешней силы. Упругая деформация полностью исчезает после прекращения действия внешней силы, поэтому ее принято называть обратимой.
|
|
Пластичностью твердого тела, называют его свойство изменять форму и размеры под действием внешних сил, не разрушаясь, причем после прекращения действий силы тело не может самопроизвольно восстановить свои размеры и форму, и в теле остается некоторая остаточная деформация, называемая пластической деформацией. Пластическую, или остаточную деформацию называют необратимой.
Хрупкость - свойство твердых тел разрушаться при механических воздействиях без значительной пластической деформации (свойство, противоположное пластичности.
Модуль упругости Е (модуль Юнга) связывает упругую деформацию ε и одноосное напряжение σ соотношением, выражающем закон Гука:
ε = σ / Е,
Модуль упругости представляет собой меру жесткости материала. Механические свойства материала характеризуются диаграммой деформации, построенной в координатах σ(ε).
Модуль упругости определяется тангенсом угла наклона производной к оси деформации. Диаграммы деформации позволяют определить модуль упругости и установить его изменение в зависимости от уровня напряженного состояния.
|
|
Модуль Юнга Е связан с другими упругими его характеристиками посредством коэффициента Пуассона. Одноосное растяжение σz вызовет удлинение по этой оси +εz и сжатие по боковым осям -εx и -εy, которые у изотропных материалов равны между собой.
Коэффициент Пуассона, или коэффициент поперечного сжатия, μ равен отношению:
μ = -εx / εy/
Если бы объем материала при одноосном упругом нагружении оставался постоянным, то наибольшее теоретическое значение μ = 0,5. Значения коэффициента Пуассона реальных материалов сильно отличаются от теоретических значений. Так для бетона 0,17 - 0,2; полиэтилена 0,4.
Объемный модуль упругости, или модуль всестороннего сжатия (растяжения), К связан с Е следующим соотношением:
К = Е / 3(1 - 2μ).
Модуль сдвига связан с модулем Юнга:
G = Е / 2(1 + μ).
Поскольку μ = 0,2 - 0,3 , G составляет 35 - 42№Е. Можно получить:
G = 3К(1 - 2μ) / 2(1 + μ).
Экспериментально определив модуль Юнга и коэффициент Пуассона, можно вычислить модуль сдвига и объемный модуль упругости, приведенными формулами.
Дать характеристику чугуна как конструкционного материала. Описать состав, применение и марки чугунов: серого, высокопрочного, белого, ковкого - и влияние химического состава на свойства чугунов
|
|
Сплав железа с углеродом, содержащий более 2,14% углерода, называется чугуном.
Чугуны являются как конструкционным материалом, так и промежуточным продуктом при производстве стали.
Свойства чугунов, как и всех других металлов, применяемых в строительстве, определяются в основном механическими и технологическими характеристиками. К механическим свойствам относятся - предел прочности при растяжении, предел текучести, относительное удлинение, твёрдость, ударная вязкость. К технологическим - жидкотекучесть, свариваемость, ковкость, электропроводность, магнитность и др.
В зависимости от состояния углерода и его формы чугун подразделяется на серый, белый, высокопрочный, ковкий и легированный. Чугун отличается от стали наличием в структуре свободного углерода - графита. Форма графита в различных чугунах различная: в сером - пластинчатая, в ковком - хлопьевидная, в высокопрочном - шаровидная (глобулярная). В белом чугуне весь углерод находится в связанном состоянии в виде цементита Fe3 C.
Кроме углерода в чугунах присутствуют кремний, марганец, сера, фосфор и ряд других - хром, никель, медь, алюминий (в легированных чугунах).
Графитообразующие элементы - кремний, никель, алюминий, медь - способствуют выделению более крупных чешуек графита.
Карбидообразующие элементы - хром, марганец, молибден, ванадий - способствуют выделению мелких чешуек графита.
Некоторые элементы обеих групп - титан, ванадий, алюминий - способствуют получению мелкого первичного зерна чугуна, т. е. улучшает его свойства.
Углерод и кремний совместно способствуют образованию графита и обеспечивают хорошие литейные свойства чугуна - жидкотекучесть. Практически в чугунах содержится до 4,5 - 5% свободного углерода, содержание кремния колеблется от 0,5 до 4,5%, содержание марганца - 0,4 - 0,6%. Марганец соединяется с серой и парализует вредное влияние серы, которое сказывается на отбеливании, т. е. сохранении цементита. При увеличении содержания марганца уменьшается графитизация чугуна и для её восстановления необходимо повышать содержание кремния. При достаточном содержании в чугуне Mn и Si содержание S не должно превышать 0,15%. Фосфор способствует жидкотекучести, поэтому присутствие его до 0,5% полезно.
Серый чугун.
При замедленном охлаждении расплавленного чугуна цементит подвергается разложению Fe3C Fe +C с образованием феррита и графита. Благодаря графиту такой чугун имеет серый излом. В зависимости от степени разложения цементита серый чугун может иметь следующие структуры: перлит - графит; перлит - графит - феррит; феррит - графит. С увеличением содержания феррита и перлита в чугуне уменьшается его твёрдость и увеличивается пластичность.
Состав применяемого чугуна обычно следующий: 2,8 - 3,6% С; 1,5 - 3,0% Si; 0.5 - 1,0% Mn; 0,3 - 1,2% P и до 0.12% S.
В таблице 18.1. дана характеристика свойств серого чугуна, применяемого в отечественной промышленности.
Таблица 18.1.
Марка чугуна | Предел прочности, МПа | Стрела прогиба, мм | Предел прочности на сжатие, МПа | Твёрдость, НRC | Примерно назначение | ||||||
На растяжение | На изгиб | При расстоянии между опорами, мм | |||||||||
|
| 600 | 300 | ||||||||
Не менее | |||||||||||
Чугун небольшой прочности. | |||||||||||
СЧ - 00 СЧ-12-28 СЧ-15-32 СЧ-18-36 | Не испытыв. | 6 7 8 | 2 2 2 | 500 600 670 | 143 - 229 163 - 229 170 - 229 | Детали и изделия, испытывающие небольшие рабочие нагрузки, к которым не предъявляются высокие требования по свойствам. | |||||
120 150 180 | 280 320 360 |
| |||||||||
Чугун повышенной прочности. | |||||||||||
СЧ-21-40 СЧ-24-44 СЧ-28-48 СЧ-32-52 | 210 240 280 320 | 400 440 480 520 | 8 9 9 9 | 2 3 3 3 | 750 830 900 1000 | 170 - 241 170 - 241 170 - 241 170 - 241 | Отливки более ответственного назначения. Станины мощного оборудования и механизмов. Поршни, цилиндры. | ||||
Модифицированные чугуны* | |||||||||||
СЧМ-36-56 СЧМ-40-60 | 360 400 | 560 600 | 9 9 | 3 2 | 1100 1230 | 197 - 248 197 - 262 | Конструкции и детали, работающие на износ, а также детали, подвергающиеся износу в атмосфере пара, газа, активных сред и т. п. | ||||
модифицированные чугуны получают путём введения графитизирующих присадок, например ферросилиция или вторичного алюминия.
Высокопрочный чугун.
Процесс получения высокопрочного чугуна заключается в модифицировании его магнием (0,05 - 0,1%) или церием и продувании через жидкий чугун (1400 - 1450 ) азота. Магний вводят в виде лигатуры сплава магния с медью, никелем, ферросилицием и др.
Состав применяемого чугуна обычно следующий: 3,2 - 3,4% С; 1,9 - 2,5% Si; 0.3 - 0,7% Mn; до 0,03% P и до 0.03% S.
Механические свойства чугуна непосредственно после литья:
предел прочности при растяжении - 500 - 650 МПа;
удлинение δ = 1 - 3%;
НRC = 210 - 260.
Механические свойства чугуна повышают закалкой и отпуском литья.
Высокопрочный чугун имеет следующую маркировку: ВЧ - 50- 2 ; ВЧ - 60 - 2 и т. д. Здесь первая цифра - предел прочности при растяжении (500, 600…. МПа), вторая - удлинение в %.
Высокопрочный чугун с шаровидным графитом находит широкое применение в строительстве и машиностроении благодаря своим высоким прочностным свойствам и технологическим преимуществам по сравнению с серыми чугунами и сталью. Долговечность и надёжность работы деталей из него привлекают к нему внимание конструкторов, вследствие снижения веса деталей.
Ковкий чугун.
При длительном отжиге белого чугуна (до 80 ч.) цементит распадается на железо и графит, причём графит выделяется в виде округлых зёрен так называемого углерода отжига. Округлые зёрна образуются при том условии, что в белом чугуне не было даже минимального количества чешуек графита, характерных для кристаллизации графита в серых чугунах. При выделении графита в округлой форме чугун приобретает некоторую пластичность, так как ослабляющее действие графита при такой его форме будет минимальным.
Отожженный белый чугун с зернистым графитом получил название ковкого чугуна (термин этот неточен, т. к. этот чугун ковке не поддаётся).
Состав применяемого чугуна обычно следующий: 2,2 - 2,6% С; 1 - 1,3% Si; 0.3 - 0.4% Mn; до 0.18% P и до 0.12% S.
В таблице 18.2. дана характеристика свойств ковкого чугуна, применяемого в отечественной промышленности.
Таблица 18.2.
Марка чугуна | Группа чугуна | Предел прочности при растяжении, МПа | Относительное удлинение, δ, % | Твёрдость HRC | Применение. | |
Образец d = 16 мм | Образец d = 12 мм | |||||
Не менее | Не более | |||||
КЧ-37-12 КЧ-35-10 КЧ-33-8 КЧ-30-6 КЧ-40-3 КЧ-35-4 КЧ-30-3 | I - чёрносердечные (ферритные) II - белосердечные (перлитные) | 370 350 330 400 350 300 | 12 10 8 6 3 4 3 | --- --- --- --- 4 5 4 | 149 149 149 163 201 201 201 | Замена более дорогих стальных фасонных деталей. Изготовление ответственных строительных конструкций: опорные части железобетонных балок, ферм, башмаки под колонны, тюбинги для тоннелей метрополитенов и др. |
Белый чугун.
Состав белого чугуна обычно следующий: около 0% С; 1 - 1,3% Si; 1 - 3,5% Mn; .
В белом чугуне весь углерод находится в связанном состоянии в виде цементита. Белые чугуны очень твёрдые и хрупкие, с трудом отливаются и обрабатываются инструментом.
В основном эти чугуны - передельные чугуны идут на переплавку в сталь или используются для получения ковкого чугуна.
Легированные чугуны.
Легирование чугунов проводится с различными целями:
· для общего повышения механических свойств;
· для придания чугуну специальных свойств - механических, физических и физико-химических: высокой износостойкости, немагнитности, высокой химической стойкости (от окисления и коррозии).
Для получения высокопрочного чугуна с основой из тонкопластинчатого или даже сорбитообразного перлита чаще всего применяют легирование чугуна хромом (0,2 - 0,5%) и никелем (0,5 - 1,5%). Хорошие результаты даёт легирование с этой целью чугуна медью (1,5 - 2%).
В качестве износостойких очень часто применяют высоколегированные белые чугуны, в структуре которых не содержится графита. Отметим износостойкие белые никелевые чугуны (5% Ni) и высокохромистых двух типов: (12 - 20% Сr) (22 - 35% Cr). Последний отличается высокой окалистной плёнкой и коррозионной стойкостью.
Коррозионная стойкость чугунных изделий может быть обеспечена только путём введения в чугун никеля, хрома и меди. Например, хромоникельмедистый чугун - нирезист, содержащий 2.7 - 3.2% C; 12 - 16% Ni; 2 - 4% Cr; 6 - 8% Cu, кремний и марганец в обычной норме. Такой чугун устойчив в минеральных и органических кислотах, в щелочах и морской воде.
Другая группа - немагнитные чугуны - это аустенитные чугуны. Такие чугуны легируют марганцем, никелем, медью и алюминием.
В практике получили распространение 1.) маргенцовоникелевые и 2.) маргенцовомедеалюминиевые чугуны с довольно высоким содеожанием кремния (2 - 3%).
Состав:
1.) около 3,5% С; 2 - 2.3% Si; 8 - 9%Mn; 4 - 4.5% Ni.
2.) 3.5 - 3.9% C; 2.4 - 2.8% Si; 8 - 10% Mn; 1.5 - 2% Cu; 0.1 - 0.7% Al.
Немагнитные чугуны широко применяются в качестве заменителей конструкций из цветных металлов.
Описать способы химико-термической обработки стали: цементацию, азотирование, нитроцементацию, диффузионную металлизацию
Насыщение поверхности стальных деталей углеродом (цементация) или азотом (азотирование) или тем и другим одновременно (нитроцементация), а также хромом, кремнием, бором и другими элементами (диффузионная металлизация) с последующей закалкой в воде, масле или на воздухе называется химико-термической обработкой стали (ХТО).
Сущность химико-термической обработки стали заключается в том, что в результате её получается как бы многослойная сталь, обладающая высокой прочностью, зависящей от химического состава стали и термической обработки после диффузионного процесса насыщения стали тем или иным элементом (или элементами), что придаёт специфические свойства поверхностным слоям стали. Эти свойства в основном характеризуются контактной прочностью и износостойкостью поверхностного слоя.
Основные требования к ХТО:
В настоящее время обращается внимание на прокаливаемость исходной стали и закаливаемость поверхностного слоя, поэтому выбор марки стали, подлежащей ХТО, основывается на прокаливаемости стали в рабочем сечении детали или конструкции, а закаливаемость обеспечивается отработкой технологии закалки. В связи с разработкой новых тех. регламентов изменились условия на качество сердцевины. Необходимо, чтобы сердцевина закаливалась на твёрдость, соответствующей сорбитной структуре данной марки стали, поэтому содержание углерода в стали, предназначенной для ХТО, должно быть достаточно высоким. Рекомендуются стали с содержанием не менее 0,25% углерода. Допускается верхний предел углерода до 0,45%. Чем выше содержание углерода, тем прочнее сердцевина.
Цементация.
В настоящее время цементация производится в газовой атмосфере, содержащей богатые углеводом углеводороды (метан, этан, бутан и др.). газовая цементация является управляемым процессом, управление им осуществляется автоматически, а загрузка и выгрузка деталей из печи механизирована. Науглероживающая атмосфера должна быть универсальной по отношению к различным маркам стали. Она состоит из двух газов, смешиваемых перед вводом в печь: из газа-носителя и газа, богатого углеводородами - карбюризатора.
Газом-носителем является атмосфера, состоящая из 29% окиси углерода, 40% азота и 40% водорода. Эта атмосфера получается в эндогазовых генераторах. Она является нейтральной (не окисляет и не обезуглероживает поверхность стали). Газом-карбюризатором служат в основном метан, этан, пропан, бутан. Эти газы получаются из природного газа путём крекинг-пиролиз-процесса. В некоторых случаях газы вводят в печь без газа-носителя.
На рис. 30.1 представлена схема установки для цементации, непосредственной закалки, низкого отпуска и охлаждения.
Рис. 30. 1. Схема установки для цементации.
Процесс цементации совершается в три стадии:
. Образование атомарного углерода;
. Абсорбция углерода на поверхности стали;
. Диффузия углерода в глубь металла и растворение в аустените (растворимость углерода в аустените - 2,14%).
Процесс протекает нормально, если в объёме рабочей камеры почти сохраняется однородный состав газа и постоянство температуры.
Химизм процесса насыщения углеродом заключается в том, что при определенной температуре происходит диссоциация - распад молекул газов, содержащих углерод, и образование активных атомов этих газов, диффундирующих с поверхности в глубь металла. Реакции протекают следующим образом:
2СО СО2 + С;
СН4 ⇆ С + 2Н2;
CnH2n ⇆ nC + nH2.
Наибольшая прочность цементованного слоя получается при содержании в поверхностных слоях его углерода от 0,8 до 0,85%. Слой после закалки не содержит крупных включений карбидов и цементитной сетки и содержание в нём остаточного аустенита минимально. Карбидная сетка и грубые включения карбидов образуются при замедленной диффузии углерода, практически установлено, что чем выше содержание углерода в стали в исходном состоянии, тем меньше должна быть глубина слоя. При возрастании прочности сердцевины деталей в рабочих местах, подвергающихся цементации, возрастает сопротивление продавливания слоя. Окончательно глубина слоя устанавливается при массовом производстве эмпирически. разрушение слоя при продавливании вызывает выщербление металла и образование осповидного износа - питтинга.
Процесс газовой цементации производится в каменных или методических муфельных и безмуфельных печах, а также в шахтных печах. Наиболее целесообразно вести процесс в безмуфельных проходных печах любого размера рабочей камеры по длине, но однорядных, т. к. при двух и тем более трёх рядах поддонов нельзя обеспечить однородность качества по насыщению углеродом и азотом.
Температура в рабочей камере печи должна быть в пределах 900 - 930 в течение времени, необходимого для получения заданного по глубине слоя. Обычно для получения слоя глубиной около 1 мм требуется 8 - 10 часов при массе детали около 1 - 2 кг. науглероживание происходит с момента образования аустенита, т. е. при температуре несколько выше 727
. Скорость науглероживания в первую очередь зависит от температуры. разница, например, в 100
уже вызывает увеличение скорости науглероживания примерно на 40%.
После цементации детали перед закалкой рекомендуется подстуживать до 800 - 820 , т. е. выше на 50 градусов температуры Ас3 (см. диаграмму в приложении), с целью снижения заключенных напряжений, которые могут вызвать излишнюю деформацию.
Существует процесс высокотемпературной цементации при 1000 и выше. Применение его вызвано стремлением интенсифицировать процесс и повысить его экономический эффект. Для этого процесса необходимы специальные печи, выложенные максимально стойким огнеупорным кирпичом, а также изготовление деталей и конструкций из специальных сталей, не склонных к росту зёрен при высокой температуре процесса. Рекомендуется использовать для этих целей стали, легированные церием и цирконием (например, сталь 30ХГТЦ или 30ХГЦЦ) зерно аустенита таких сталей не должно быть меньше 7 - 8-го балла стандартной шкалы.
Цементованные детали подвергают закалке в воде, масле или расплавленных солях. В зависимости от этого получается та или иная твёрдость поверхностных слоёв и сердцевины в рабочем участке конструкции оптимальной структурой цементованного и закалённого слоя является мелкодисперсный мартенсит, но неизбежно в структуре имеется остаточный аустенит и карбиды. Температура и состав закалочной смеси в сильной мере влияют на образование структуры при одной и той же степени насыщения углеродом. Выбор охлаждающей среды должен зависеть не только от желания иметь ту или иную твёрдость, но и получить не менее важное качество цементованного слоя - минимальную деформацию детали или конструкции. При ступенчатой закалке в масле (особенно в горячем масле) степень деформации получается минимальной, но твёрдость может быть недостаточной. Для получения комплексного эффекта в этом случае необходимо энергичное и постоянное перемешивание масла в закалочном баке.
В зависимости от структуры стали после закалки поверхностная твёрдость в пределах НRC 56 - 63. Чем больше в структуре остаточного аустенита, тем ниже твёрдость, но это не характеризует ещё недостаточной износостойкости поверхностного слоя. Практически в поверхностных слоях на глубине до 0,2 мм допускается не более 25% остаточного аустенита, если деталь не испытывает в эксплуатации сосредоточенных нагрузок, в противном случае количество остаточного аустенита должно быть максимально снижено. Структура сердцевины должна состоять из сорбита или троостосорбита. Твёрдость должна быть в пределах НRC 35 - 45. Поэтому в различных местах одной и той же конструкции твёрдость сердцевины будет различной. Необходимо обеспечить отсутствие феррита в сердцевине рабочих сечений детали после закалки во избежание поломок от усталости.
После закалки цементованные детали подвергают отпуску при температуре 180 - 200 с выдержкой не менее 1 часа. Твёрдость после отпуска снижается на 1 - 2 единицы НRC.
Если при эксплуатации деталь или конструкция не подвергается ударным нагрузкам, целесообразно не подвергать её отпуску с целью сохранения сжимающих напряжений, возникающих при закалке и способствующих повышению усталостной прочности. Для повышения усталостной прочности цементованных деталей их после закалки и отпуска подвергают наклёпу дробью, что создаёт дополнительные сжимающие напряжения. Усталостная прочность и долговечность таких конструкций значительно повышается.
Процесс газовой цементации интенсифицируется путём повышения температуры до 100 - 1050 и нагрева с помощью индукционного тока частотой 2 500 - 8 000 Гц (индукционный нагрев). Процесс насыщения углеродом при индукционном нагреве ускоряется в несколько раз. Так при нагреве с помощью машинного генератора (2000 Гц) при температуре 1050
науглероженный слой глубиной 0,8 мм получается за 25 мин.
Исследования показали, что качество химико-термически упрочненного слоя зависит не только от степени насыщения углеродом и азотом закалки и отпуска, но и от окисления элементов, входящих в состав стали в процессе науглероживания. Явление внутреннего окисления связано с диффузией кислорода в сталь и наличием в атмосфере СО2 и паров Н2О, вызывающих образование окислов легирующих элементов. Процесс происходит в три фазы:
. Образование атомарного кислорода;
. Диффузия его в кристаллическую решётку;
. Окисление легирующих элементов.
В зарубежной практике (ноу - хау Германии) существуют процессы, применяемые в комплексе с другими, которые заканчиваются газовой цементацией деталей и конструкций. Они называются гомогенной и реставрационной цементацией. Суть процессов заключается в том, что гомогенная цементация применяется для деталей, изготовляемых штамповкой из листовой стали с содержанием углерода около 0,1% (автомобилестроение), а реставрационная цементация применяется при производстве деталей высадкой в холодном состоянии. Детали, изготовленные холодной штамповкой, подвергаются газовой цементации с автоматическим регулированием содержания углерода по всему сечению конструкции до любого заданного с последующей закалкой в различных средах. Если детали изготовляются высадкой, то металл в штангах предварительно обезуглероживают, а затем после высадки уже готовые детали подвергают газовой цементации. Качество деталей и конструкций после закалки и отпуска получается очень высоким.
Азотирование.
Азотирование производится в атмосфере азота при температуре 480 - 650 . Железо при этой температуре находится в α-состоянии (см. Диаграмму). Растворимость азота при температуре азотирования достигает 0,42%. Обычно атмосферный газ - аммиак NH3.
Азотирование придаёт поверхности стальных изделий исключительно высокую твёрдость, сохраняющуюся при нагреве до 600 - 650 , износоустойчивость, повышает предел усталости и сопротивление коррозии в атмосфере воды и её паров.
Механизм образования азотированного слоя:
При взаимодействии азота с металлом образуется группа соединений - нитридов. Реакция заключается в образовании азотистого феррита и азотистого аустенита.
В системе железо - азот (рис.30.2) образуются следующие фазы:
. твёрдый раствор азота в α-железе; концентрация азота в α-фазе составляет при эвтектоидной температуре (5910) 0,42%, снижаясь до 0,015% при нормальной комнатной температуре;
2. γ'-фаза - твёрдый раствор на базе нитрида железа Fe2N (5.5 - 5.95% N2);
3. ε-фаза - твёрдый раствор на базе нитрида Fe4N (8 - 11.2 N2); предельное содержание азота в ε-фазе (11,2%) отвечает нитриду железа Fe2N.
При температуре 5910 существует γ-фаза, которая представляет собой твёрдый раствор азота в γ-железе. При 5910 γ -фаза претерпевает эвтектоидный распад. Азотистый эвтектоид, напоминающий во многом перлит, содержит 2,35% азота и состоит из смеси α- и γ'-фаз.
строительный материал твердость чугун
Рис. 30.2 Диаграмма состояния Fe - N2.
Азот растворяется и в α- и γ-железе (аустените). Однако значительное количество азота может быть поглощено стальной поверхностью лишь в тех случаях, когда он находится в атомарном состоянии и является продуктом распада аммиака. Аммиак при температуре азотирования диссоциирует по реакции:
2NH3 ⇆ 2N + 6H.
Образовавшийся атомарный азот и диффундирует в сталь. При диффузии азота в железо имеет место последовательное образование фаз, идущее по диаграмме состояния (рис. 30. 2.) от меньших концентраций в сторону больших концентраций азота.
Схема установки для азотирования представлена на рис 30.3.
Рис 30.3 Схема установки для азотирования стали.
Аммиак из баллона 1 через редуцирующее устройство 2 поступает в осушитель 3 и далее через счётчик газа 4 - в печь 6. Из печи диссоциированный аммиак поступает в сосуд с водой. Для контроля процесса установлен водяной манометр 9 и диссоциометр 10. При помощи диссоциометра контролируется степень диссоциации аммиака в печи. При температуре азотирования 500 - 5200 степень диссоциации устанавливают 15 - 25%, а при 600 - 6500 - 40 - 50%. Для контроля температуры установлена термопара 7.
Процесс весьма длителен - до 70 часов.
Процесс завершается охлаждением изделий на воздухе.
Азотированию обычно подвергают легированные стали, содержащие алюминий, хром, молибден и другие элементы. С легирующими элементами азот образует нитриды типа AlN, CrN, Cr2N, MoN, Mo2N и др.
Так, хром повышает прочность сердцевины, никель повышает вязкость, молибден измельчает зёрна аустенита, алюминий образует алюминаты и повышает твёрдость. Содержание алюминие не должно превышать 0,5% во избежание хрупкости азотированного слоя.
Азотирование можно производить не только в атмосфере аммиака, но и в соляных ваннах, содержащих цианистые соединения. Обычно применяют цианистые соли натрия и калия - это процесс цианирования. Процесс в ваннах происходит весьма активно: при применении ванны из цианистого натрия и цианистого калия слой глубиной 0,4 - 0,5 мм получается за 2 часа.
В Германии для изделий, требующих большой выносливости и сопротивлением изнашиваемости, применяется мастрейсинг-процесс. Процесс заключается в сочетании азотирования с дополнительным нагревом до температуры Ас3, выдержкой в течение 30 мин при этой температуре и закалкой. При нагреве нитриды распадаются и твёрдый раствор легируется азотом. Вследствие легирования азотом мартенсита повышается закаливаемость стали. Цель процесса заключается в создании больших сжимающих напряжений, что повышает усталостную прочность изделий и их надёжность и долговечность.
Нитроцементация.
Процесс нитроцементации производят в той же газовой атмосфере и при той же температуре, что и при газовой цементации, но с добавлением 10 - 40% аммиака. Происходит одновременное насыщение стали углеродом и азотом. Азот способствует насыщению стали углеродом, так как понижает температуру образования аустенита, вследствие чего насыщение стали углеродом начинается при более низкой температуре (около 6000С). При температуре выше 8500С происходит преимущественное насыщение углеродом. Наличие в атмосфере углеводородов приводит к следующим реакциям:
NH3 + CH4 ⇆ HCN + 3H2;
NH3 + C2H6 ⇆ 2HCN + 5H5.
Содержание HCN является носителем, оно распадается с выделением азота и углерода. Перенасыщение стали азотом приводит к образованию ε-фазы.
Практика показала, что в процессе цементации происходит окисление кремния, хрома, марганца, титана, но если в эндогазовую атмосферу в зоне окончательного регулирования диффузии углерода ввести 10% аммиака, то можно исключить внутреннее окисление. Непрерывное введение NН3 в рабочее пространство печи в процессе карбонитрования исключает внутреннее окисление. Однако надо иметь в виду состав стали. Присутствие в стали молибдена, никеля, вольфрама, меди в больше степени снижает внутреннее окисление, но из этих элементов практически только Мо и Ni могут быть использованы для изготовления деталей, подвергающихся цементации (преимущество отдается Мо - стали марок 25ХГТ и 25ХГМТ).
Диффузионная металлизация.
Поверхностное насыщение стали алюминием, бериллием, хромом, кремнием и другими элементами называется диффузионной металлизацией.
При насыщении поверхности стали этими элементами изделие приобретает ряд ценных свойств, к числу которых относятся высокая жаростойкость, коррозионная стойкость, повышенная износоустойчивость и твёрдость.
Поверхностное насыщение стали металлами и кремнием осуществляется тремя способами:
. путем помещения изделия в соответствующие порошкообразные смеси (обычно ферросплавы);
. погружением в расплавленный металл, если диффундирующий элемент имеет невысокую температуру плавления (например, алюминий, цинк);
. путем насыщения из газовой среды.
Процесс насыщения стали металлами при непосредственном контакте насыщенной порошкообразной среды с поверхностью обрабатываемого изделия связан с большими числом трудностей вследствие проведения его при высоких температурах и длительных выдержках.
Насыщение стали осуществляется в большинстве случаев через газовую фазу, представляющую собой хлористые соединения данного металла (AlCl3; CrCl2; SiCl4 и т. д.), получаемые путём воздействия хлора (хлористого водорода - НСl - соляной кислоты) при высоких температурах на данный металл или его ферросплав. При высокой температуре диффузии хлориды диссоциируют и на поверхности обрабатываемого изделия в атомарном состоянии выделяется металл хлорида, который и диффундирует в сталь.
На скорость диффузии оказывает влияние состав стали. Увеличение в стали углерода затрудняет процесс диффузии. При этом необходимо отметить, что при диффузии того или иного элемента в сталь происходит перераспределение в поверхностных слоях концентрации углерода. В ряде случаев наблюдается вытеснение углерода из диффузионного слоя (при насыщении алюминием, кремнием); в других случаях, наоборот, имеет место интенсивная диффузия углерода к поверхности ( хром).
Диффузионная металлизация того или иного металла носит своё собственное название. Так, например насыщение стали алюминием называется алитированием; хромом - хромированием; кремнием - силицированием ; бериллием - бериллизацией; бромом - борированием и т. д.
Для примера рассмотрим процесс хромирования:
Поверхностное насыщение стальных изделий хромом сообщает стали хорошую устойчивость протии газовой коррозии при температуре до 8000С, высокую коррозионную стойкость в таких средах, как вода, морская вода и азотная кислота, а при хромировании высокоуглеродистых сталей - большую твёрдость и износоустойчивость. Различают три основных вида хромирования:
Хромирование в порошке.
Изделие упаковывают в смесь, состоящую из измельчённого феррохрома и порошков глинозёма, каолина, шамота и др. В состав для хромирования добавляется хлористый аммоний или соляная кислота (1 - 5%) - для образования активной газовой фазы, состоящей из хлоридов хрома. хромирование ведут при 1000 - 12000С. Продолжительность процесса 12 - 15 часов. При хромировании в смеси порошка феррохрома с хлористым аммонием протекают следующие реакции:
NH4Cl = NH3 + HCl;
HCl + Cr = H2 + CrCl2.
При контакте с о стальным изделием протекает обменная реакция, в результате которой выделяется атомарный хром, диффундирующий в изделие:
Fe + CrCl2 = FeCl2 + Cr.
Образующееся при взаимодействии хлористого хрома с железом летучее хлористое железо (Cr2OCl2) окисляется в хлорноe (FeCl2) железо и удаляется из камеры реакции/
Газовое хромирование.
При проведении газового хромирования стальные изделия нагревают при 950 - 10500С в атмосфере паров хлоридов хрома (CrCl2, CrCl3).
При температуре хромирования хлориды хрома контактируют с поверхностью изделия, в результате чего имеет место обменная реакция с выделением атомарного хрома, диффундирующего в сталь:
CrCl3 + Fe ⇆ FeCl3 + Cr;2 + Fe ⇆ FeCl2 + Cr.
Жидкое хромирование.
Стальные изделия выдерживаются при 900 - 10000С в расплавленных солях BaCl2, MgCl2, CaCl2 и других, к которым добавляются хлористые соли хрома CrCl2 (15 - 30%) по весу или феррохром (20 - 25%).
В основе жидкого хромирования лежит следующая реакция:
CrCl2 (расплав соли) + Fe(изделие) ⇆ FeCl2 + Cr.
В результате хромирования стали диффузионный слой состоит из твёрдого раствора хрома в α-железе, а при хромировании высокоуглеродистой стали - из сплошного слоя карбида хрома (Cr, Fe)7C3. Образование слоя сплошного карбида связано с диффузией углерода из внутренних слоёв к поверхности навстречу хрому. Углерод обладает большей скоростью диффузии, чем хром, поэтому не весь углерод используется для образования карбидного слоя и образует переходный слой с высоким содержанием углерода. образование на поверхности слоя карбида (Cr, Fe)7C3 сопровождается сильным повышением твёрдости. Твёрдость хромированного слоя, полученного на железе, составляет 250 - 300 НRC, а на высокоуглеродистых сталях - 1200 - 1300 НRC. Глубина хромированного слоя обычно не превышает 0,2 - 0,25 мм. наличие в стали углерода тормозит процесс диффузии хрома в сталь. Введение в сталь вольфрама, молибдена, кремния ускоряет процесс диффузии хрома, а никель, марганец - замедляют.
Дата добавления: 2021-04-24; просмотров: 59; Мы поможем в написании вашей работы! |
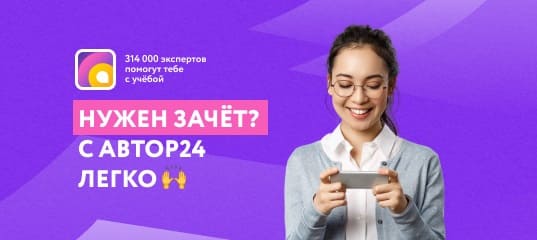
Мы поможем в написании ваших работ!