Балансировка по методу трёх пусков
Для балансировки турбин турбокомпрессора используется специальный балансировочный станок, вариант конструкции которого показан на рис.6.
Турбина устанавливается на двух виброопорах с призмами (рис.7а), между которыми на неё надевается ремень, передающий вращение с электродвигателя. Вибродатчик находится на одной из опор (в зависимости от того, какой торец турбины балансируется). Слева и справа от турбины стоят прижимные стойки, предохраняющие турбину от горизонтальных смещений и вибрации. Вся платформа отделена от основания с электродвигателем пружинными виброгасящими опорами.
Особое внимание следует уделить конструктивному исполнению технологических опор (рис.7).
Установочной призмой (рис. 7 а) называют элемент, имеющий две рабочие плоскости (грани), расположенные под некоторым углом. Номинальный угол призмы равен 90°, но используют призмы и с другими углами. Расстояние от центра призмы до основания должно быть таким, чтобы ось призм совпадала с осью станка.
Рис. 6. Балансировочный станок
а б в г д
Рис.7. Технологические опоры
Основным недостатком призмы является малая площадь контакта с цапфой. По этой причине для роторов большой массы вместо призм применяют полуцилиндрические гнезда (рис. 7 б).
Установочную функцию выполняет только гнездо – нижнее полуотверстие. Съемную или откидную крышку строго не фиксируют. Она должна равномерно передавать давление зажатия на подшипник и не смещать его при закреплении.
|
|
При установке на технологические опоры подшипников качения возникает перекос внешних колец, что создает погрешность балансировки. Установочным элементом повышенной точности является технологическая опора с косыми роликами (рис. 7 в).
Косые ролики - разновидность призм, у которых вместо рабочих поверхностей установлены ролики под углом 90°. Ролик имеет одну точку контакта с подшипником, что определяет высокую стабильность положения подшипника при многократных его установках на косых роликах.
Динамическую балансировку роторов часто проводят на технологических подшипниках качения, в качестве которых используют подшипники тех же типоразмеров, что и рабочие, но повышенной точности, с малыми радиальными зазорами.
При балансировке роторов используют также подшипники скольжения (рис. 7 г) с полужидкостным и жидкостным трением. При этом трущиеся поверхности разделяются слоем жидкости, что значительно снижает трение скольжения твердых тел. Применение газа для разделения поверхностей еще больше уменьшает сопротивление трению скольжения.
|
|
Роликовые опоры (рис. 7 д) имеют ряд преимуществ по сравнению с другими типами технологических опор:
большая универсальность, так как на одной и той же паре роликов возможна установка роторов с большим диапазоном диаметров цапф;
малый коэффициент трения, высокие удельные давления и угловые скорости вращения.
К недостаткам роликовых опор относятся помехи, возникающие из-за погрешностей формы и взаимного положения поверхностей самих роликов и подшипников, на которых они смонтированы.
Для балансировки используется виброизмеритель ВШВ-003-М2, укомплектованный датчиком ДН-3 с полосой измеряемых частот колебаний от 1 Гц до 4 кГц. Датчик крепится к элементам конструкции станка с помощью магнитного основания.
Виброизмерителем регистрируются уровни виброскорости в информативном диапазоне частот ВА колебаний 4...63 Гц, выделяемых прибором посредством октавных фильтров. Основная частота при этом – 31 Гц (соответствует частоте вращения ротора 1860 об/мин). Известно, что виброскорость (V) пропорциональна дисбалансу и более помехоустойчива, чем виброускорение (меньше скорость вращения, шумы подшипников и т.д): ,
|
|
где - масса ротора,
- значение дисбаланса).
Весьма ответственным является выбор пробной корректирующей массы. Теоретически эта масса и угол ее установки могут быть произвольными. Практически, однако, неудачный выбор их может привести к потере пуска; например, слишком большая пробная корректирующая масса, если она совпадет с исходным дисбалансом, может вызвать такое увеличение вибраций, которое не позволит довести частоту вращения ротора до балансировочной. Если пробная корректирующая масса слишком мала, то вызванное ею приращение вибраций будет соизмеримо с погрешностями измерений, что также не позволит правильно рассчитать необходимую корректирующую массу. В обоих случаях пробный пуск придется повторить.
Расчет требуемой системы корректирующих масс можно провести по формуле:
,
где A1 - пуск с пробной корректирующей массой ;
A2 - пуск с той же массой, но сдвинутой на 180° относительно первого положения.
При проведении балансировки по методу трёх пусков необходимо производить достаточно большой объём вычислений. И применение ЭВМ вместо обычного калькулятора для вычислений не только существенно ускоряет процесс получения результатов, но и позволяет автоматизировать анализ и отсеивание заведомо неверных.
|
|
На рис.8 представлены схемы действия неуравновешенных сил в плоскости 1-1 ротора. Здесь А0 - измеренная амплитуда виброускорений, вызванных центробежными силами инерции неуравновешенной части Mn от массы ротора (рис.8 а).
Рис.8. Схема действия неуравновешенных сил на торец ротора в плоскости 1-1
Для уменьшения величины А0 в плоскости 1-1 необходимо установить противовес – добавочный груз Md. Масса добавочного груза Md - и положение (угловая координата ) рассчитываются следующим образом.
Если поместить в плоскости 1-1 на расстоянии Rg от оси вращения пробный груз массой Mp, то амплитуда виброускорений изменится и станет равной (рис.8 б):
A1 = A0 + Ap1,
где Аp1 - амплитуда виброускорений, вызываемая пробной массой Mp (угол 0 º).
Поместив пробный груз Mp на том же расстоянии Rg в плоскости 1-1, но с противоположной стороны ротора, получим другую результирующую векторной суммы виброускорений (рис.8 в):
А2 = A0 + Ap2 ,
где Аp2 - амплитуда виброускорений, вызываемая пробной массой Mp (угол 180 º).
Как следует из рис.8 б, в, полученные параллелограммы амплитуд равны как имеющие равные стороны и углы. Амплитуды А1 и А2 являются диагоналями этих параллелограммов.
Зная формулу связи между диагоналями и сторонами в параллелограмме, а также наложив друг на друга имеющиеся параллелограммы (когда Ap0 заменяет собой Ap1 и Ap2), получим (рис.8 г):
Для определения углового положения противовеса используется соотношение (теорема косинусов):
;
откуда
;
.
Одному значению косинуса соответствуют два угла + и -
, поэтому проверка сбалансированности должна вестись при четырех углах:
+ , -
, 180° +
, 180° -
.
Масса противовеса (добавочного груза) рассчитывается по формуле:
.
Критерием окончания балансировки в обеих плоскостях в результате выполнения указанных выше операций является снижение уровня виброускорений на частоте 31 Гц до уровня собственных колебаний станка. В процессе обработки результатов достаточно часто могут возникать ситуации, когда значение косинуса превышает единицу (по модулю). В этом случае приходится повторно производить пуски станка с изменённым углом расположения на роторе пробного груза. Причиной такого явления являются погрешности измерений, невозможность выделить нужные колебания из общего шумового фона станка, особенно когда пробный груз Mp попал в искомое место с точностью 2-3º и скомпенсировал дисбаланс ротора. В расчётах ситуация с "переполнением" косинуса решается следующим образом.
В параллелограмме (рис.9) при значении треугольник со сторонами Ap0-A0-A1 просто распадается, т.к. сумма длин двух его сторон меньше длины третьей. Это говорит лишь о том, что угол пробного груза совпал с углом дисбаланса ротора Mn. Значит, искомый угол должен быть равен 0º или 180º. Сравнение значений A1 и A2 точно указывает на место, где нужно установить противовес (добавочный груз Md). В других (нормальных) ситуациях, при получении четырёх значений возможного угла, методом сравнения тех же A1 и A2 исключаются из рассмотрения два угла. И, наконец, четвёртым пуском из двух оставшихся выбирается необходимый угол.
Рис.9. Угол , косинус которого не может быть больше единицы
После уравновешивания в плоскости 1-1 ротор переставляется на станке и производится уравновешивание в плоскости II-II (на втором торце ротора) аналогичным образом.
Эта методика математических расчётов применима и для балансировочных станков другой конструкции. Ниже представлен реальный пример результатов балансировки ротора электродвигателя ЭД-118, который балансировался на станке МС9Г717. В этом балансировочном станке измеряется такой параметр вибраций, как виброускорение. Технологические опоры используются роликовые, т.к. только они позволяют на одном станке балансировать самые различные по конструкции и массе роторы.
Результаты расчётов и итоговые значения частично не совпадают по причине отсутствия пробных масс Mp (грузиков) необходимой массы, что, однако, не сильно отражается на качестве балансировки.
Результаты приведены для двух плоскостей балансировки (1-1 и II-II):
_______________________________________________________________
ИСХОДНЫЕ И ПРОМЕЖУТОЧНЫЕ ДАННЫЕ:
Амплитуда виброускорений неуравновешенного ротора, A0 = 50
Амплитуда виброускорений с пробным грузом (угол 0°), A1 = 180
Амплитуда виброускорений с пробным грузом (угол 180°), A2 = 115
Амплитуда виброускорений пробного груза (общая), Ap0 = 142.5219
Амплитуда виброускорений пробного груза (угол 0°), Ap1 = 130
Амплитуда виброускорений пробного груза (угол 180°), Ap2 = 65
Косинус угла добавочного груза, AC = 0.6727035
Масса пробного груза, Mp = 71
РЕЗУЛЬТАТЫ РАСЧЁТОВ:
ALFA1 = 133 °
ALFA2 = 227 °
Масса добавочного груза, Md = 24.90845
Угол установленного добавочного груза (итоговый), ALFAi = 132
Масса добавочного груза (итоговая), Mdi = 70
_______________________________________________________________
ИСХОДНЫЕ И ПРОМЕЖУТОЧНЫЕ ДАННЫЕ:
Амплитуда виброускорений неуравновешенного ротора, A0 = 70
Амплитуда виброускорений с пробным грузом (угол 0°), A1 = 70
Амплитуда виброускорений с пробным грузом (угол 180°), A2 = 180
Амплитуда виброускорений пробного груза (общая), Ap0 = 117.2604
Амплитуда виброускорений пробного груза (угол 0°), Ap1 = 0
Амплитуда виброускорений пробного груза (угол 180°), Ap2 = 110
Косинус угла добавочного груза, AC = -0.8375743
Масса пробного груза, Mp = 71
РЕЗУЛЬТАТЫ РАСЧЁТОВ:
ALFA1 = 33 °
ALFA2 = 327 °
Масса добавочного груза, Md = 42.3843
Угол установленного добавочного груза (итоговый), ALFAi = 325
Масса добавочного груза (итоговая), Mdi = 85
_______________________________________________________________
Значения Ap1 и Ap2 нужны только для графического построения сил инерции (рис.8), их можно не рассчитывать, т.к. они не требуются для вычисления угла и массы добавочного груза (в отличие от Ap0).
Представленный пример динамической балансировки ротора электродвигателя, выполняемой на балансировочном станке, с соответствующей аппаратурной реализацией был заимствован из отчёта по технологическому процессу заключительной операции ремонтно-восстановительных работ (балансировки роторов) на предприятии АО "Тантал" г. Саратова. Величина остаточного дисбаланса ротора после балансировки, определяемая расчетным путем по уровню виброускорения на основной частоте ВА колебаний, ниже допустимой по технической документации (180 г×см) на 30...40%, снижение дисбаланса - в 3...15 раз, что свидетельствует об эффективности и достаточно высокой точности балансировочной операции.
ПРАКТИЧЕСКАЯ ЧАСТЬ
Для закрепления полученных знаний предлагается произвести операцию динамической балансировки ротора электродвигателя (или турбинки из автомобильной системы турбонаддува, в зависимости от имеющейся технической базы) по методу трёх пусков. При отсутствии балансировочного станка исходные данные для выполнения работы можно взять из приложения.
1. Раскрутить ротор и замерить его собственные колебания, т.е. амплитуду виброускорений неуравновешенного ротора (A0).
2. Установить на роторе пробный груз (Mp) – на угле 0°, раскрутить ротор и замерить амплитуду виброускорений (A1).
3. Переместить пробный груз (Mp) на угол 180°, раскрутить ротор и замерить амплитуду виброускорений (A2).
4. Рассчитать амплитуду виброускорений пробного груза по формуле:
.
5. Рассчитать угол противовеса (угол размещения добавочного груза) по формуле:
.
6. Рассчитать массу противовеса - добавочного груза (Md) по формуле:
.
7. Занести исходные и полученные данные в таблицу; полученные результаты (либо их отсутствие) объяснить:
A0 | A1 | A2 | Mp | Ap0 | ![]() | - ![]() | 180°+ ![]() | 180°- ![]() | Md |
Рекомендуется начертить схему действия неуравновешенных сил в роторе по примеру рис. 8. (Для этого может потребоваться вычисление значения Ap1 = A1 - A0 и Ap2 = A2 - A0)
ВОПРОСЫ ДЛЯ САМОПРОВЕРКИ
1. Для чего необходима балансировка?
2. Чем может быть вызван дисбаланс?
3. Типы балансировки. Отличие динамической балансировки от статической.
4. Балансировка методом обхода.
5. Балансировка с применением стробоскопа.
6. Резонансная балансировочная машина с оптическим отсчётным устройством.
7. В каких случаях используют балансировку по методу трёх пусков?
8. Состав балансировочного станка.
9. Какая аппаратура применяется на балансировочном станке по методу трёх пусков?
10. Наиболее часто возникающие ошибки при расчётах.
11. Какие величины используются в расчётах?
ПРИЛОЖЕНИЕ
№ | A 0 | A 1 | A 2 | Mp |
1 | 55 | 130 | 145 | 93 |
2 | 250 | 200 | 320 | 120 |
3 | 10 | 52 | 34 | 25 |
4 | 25 | 80 | 40 | 200 |
5 | 60 | 61 | 59 | 5 |
6 | 35 | 85 | 43 | 80 |
7 | 425 | 350 | 362 | 50 |
8 | 49 | 72 | 33 | 15 |
9 | 48 | 66 | 120 | 90 |
10 | 15 | 46 | 72 | 25 |
11 | 69 | 47 | 88 | 90 |
12 | 172 | 200 | 235 | 120 |
13 | 40 | 45 | 38 | 25 |
14 | 81 | 93 | 77 | 45 |
15 | 30 | 144 | 92 | 50 |
16 | 98 | 144 | 66 | 40 |
17 | 20 | 104 | 68 | 55 |
18 | 50 | 160 | 80 | 150 |
19 | 120 | 125 | 115 | 30 |
20 | 33 | 158 | 103 | 87 |
21 | 75 | 245 | 123 | 35 |
22 | 184 | 189 | 180 | 40 |
23 | 147 | 216 | 100 | 40 |
24 | 62 | 50 | 81 | 100 |
25 | 10 | 21 | 11 | 80 |
26 | 245 | 365 | 166 | 80 |
27 | 70 | 364 | 238 | 100 |
28 | 175 | 560 | 285 | 200 |
29 | 30 | 80 | 39 | 150 |
30 | 240 | 249 | 237 | 40 |
СПИСОК ЛИТЕРАТУРЫ
1. Автоматизация производственных процессов в машиностроении: учебник / под ред. Н. М. Капустина. – М.: Высш. шк., 2007. – 415 с.
2. Усакин К.С. Устройство автоматизированной балансировки шпинделя прецизионного токарного модуля в условиях эксплуатации / К.С. Усакин, М.В. Виноградов // Вестник СГТУ, 2010. № 2 (45). С. 132-137.
3. Добряков В.А. Оперативный контроль метрологических характеристик автоматизированного виброизмерительного комплекса / В.А. Добряков, М.В. Виноградов, М.Ю. Пальм // Автоматизация и управление в машино- и приборостроении: межвуз. научн. сб. Саратов: СГТУ, 2006. С.72-75.
4. Современные методы и средства балансировки машин и приборов / М.В. Баркан, Т.Т. Гаппоев, А.А. Геркус и др.; под общ. ред. В.А. Щепетильникова. М.: Машиностроение, 1985. 232 с.
5. Гемке Р.Г. Неисправности электрических машин / Р.Г. Гемке под. ред. Р.Б. Уманцева. 9-е изд. Л.: Энергоатомиздат, 1989. С.129-140.
6. Добряков В.А. Высокоточная балансировка крупногабаритных деталей типа "ротор" по параметрам вибрации / В.А. Добряков, М.В. Виноградов, С.С. Пчелинцев // Автоматизация и управление в машино- и приборостроении: межвуз. научн. сб. Саратов: СГТУ, 2000. С.43-46.
7. Паспорт к балансировочному станку для динамической балансировки модели МС9Г717.
8. Автоматизированная система балансировки роторов / Д. Егоров, Л. Глазырина, П. Жиганов и др. // Современные технологии автоматизации. 2001. №4. С. 48-53.
Динамическая балансировка
роторных систем
машино- и приборостроения
Методические указания
к лабораторной работе по курсам
"Автоматизированный контроль и диагностика",
"Технические средства автоматизации",
"Автоматизированные испытания технологических систем",
"Автоматизированные испытания".
Составили: ДОБРЯКОВ Владимир Анатольевич
ИГНАТЬЕВ Александр Анатольевич
УСАКИН Кирилл Сергеевич
Рецензент М.В.Виноградов
Редактор О.А.Панина
Дата добавления: 2021-02-10; просмотров: 777; Мы поможем в написании вашей работы! |
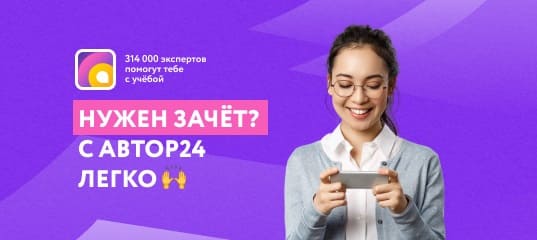
Мы поможем в написании ваших работ!