Аустенитные нержавеющие хромоникелевые стали.
К конструкционным материалам реакторного контура ядерных энергетических установок (ЯЭУ) предъявляют весьма жесткие требования в отношении их коррозионной стойкости. Это особенно важно для контуров, в которых в качестве теплоносителя используют легкую воду или жидкие металлы. Вода даже высокой чистоты является коррозионно-агрессивной средой. В жидких металлах при температуре выше 773 К наблюдается перенос массы.
В первые годы строительства ЯЭУ с водным и жидкометаллическим теплоносителями было мало данных о коррозионной стойкости различных материалов в воде высокой чистоты и в жидких металлах, так как обычная теплоэнергетика не ставила своей задачей изучение этих проблем. Поэтому исследовались в основном материалы, обладающие самой высокой коррозионной стойкостью, освоенные в смежных отраслях промышленности. Основным конструкционным материалом была выбрана аустенитная хромоникелевая нержавеющая сталь (советские марки Х18Н9 и Х18Н10Т и американские стали типа 304 и 347). Стали этого класса коррозионно-стойки в воде до температуры 633 К, в газовом теплоносителе (например, в углекислоте до 873 К) и в водяном перегретом паре — до температуры 923 К. Наряду с высокой коррозионной стойкостью эти стали имеют необходимые технологические характеристики.
Аустенитные нержавеющие стали успешно применяют в качестве оболочек твэлов и других элементов активной зоны в реакторах на тепловых и быстрых нейтронах. Несмотря на более высокие значения сечения поглощения тепловых нейтронов [(2,7—2,9)·10-28 м2 по сравнению с 0,19·10-28 м2 у циркония], что приводит к необходимости использования более обогащенного топлива, хромоникелевые нержавеющие стали имеют ряд важных преимуществ перед другими материалами. Они в несколько раз дешевле, чем цирконий, обладают высокой жаропрочностью и жаростойкостью, вплоть до 823—873 К, имеют хорошую свариваемость, технологичны. Оболочки из стали Х18Н10Т предпочтительны для реакторов на быстрых нейтронах, так как в таких реакторах в основном в качестве теплоносителя используют жидкие металлы.
|
|
Состав некоторых хромоникелевых сталей и их сплавов приведен в табл. 8.12. Нержавеющие аустенитные стали обладают достаточно высокими механическими характеристиками вплоть до температуры 873—923 К (табл. 8.13), поэтому их можно применять в реакторах с высоким давлением теплоносителя. Для повышения жаропрочности аустенитных нержавеющих сталей необходимо дополнительное легирование молибденом или вольфрамом.
При использовании аустенитных нержавеющих сталей для оболочек твэлов необходимо обращать внимание на совместимость стали с ядерным топливом. Сталь X18Н ЮТ хорошо совместима с двуокисью урана до температуры 1023 К. Это особенно важно при использовании жидкометаллических теплоносителей, так как даже при нарушении герметичности оболочки твэла двуокись урана не взаимодействует
|
|
Механические свойства стали Х18Й10Т при различных температурах | |||||||||||||
Л С | га С | (В С | щ й | сз С | « с | ■й | |||||||
Г, к | % V* ь | g м t> | 6. % | ■ф. % | £ в) о | о — я . С Й | Т. К | о | S Ь | а. % | '!>. % | 2 я а | 2 га . С Ш S |
293 | 270 | 655 | 55,0 | 75,5 | 2,50 | 2,02 | 773 | 170 | 430 | 30,0 | 64,5 | 3,65 | 1,69 |
373 | 245 | 510 | 44,0 | 76,5 | .— | 1,98 | 823 | 180 | 455 | 40,5 | 61,0 | 3,65 | 1,64 |
473 | 205 | 465 | 38,0 | 70,5 | 3,70 | 1,93 | 873 | 160 | 360 | 28,5 | 64,5 | 3,60 | 1,60 |
573 | 160 | 450 | 29,0 | 66,0 | — | 1,85 | 923 | 160 | 355 | 30,0 | 68,3 | _ | 1,55 |
673 | 180 | 445 | 20,5 | 64,0 | 3,17 | 1,77 | 973 | 180 | 275 | 29,5 | 57,5 | 3,40 | 1,50 |
|
|
с жидким металлом (натрием). С металлическим ураном такие стали вступают во взаимодействие в пределах температур 773—973 К, образуя урансодержащие интерметаллические соединения в слое от 0,03 до 0,5 нм.
Хорошо совместим с аустенитными нержавеющими сталями до температуры 873 К монокарбид урана, при более высокой температуре он обычно взаимодействует со сталью и несовместим с водой и паром при высоких параметрах последнего. Эти стали в воде высокой чистоты и в паре достаточно коррозионно-стойки. Высокая коррозионная стойкость этих сталей обусловлена их способностью пассивироваться.
В зависимости от состава сталей, их структуры, значения pH и наличия примесей среды нержавеющие аустенитные стали могут подвергаться нескольким видам коррозии: общей (охватывающей всю поверхность равномерно), местной (точечные, язвенные поражения), межкристаллитной (поражения по границам зерен) и коррозии под напряжением.
Общая коррозия этих сталей в дистиллированной воде при комнатной температуре протекает с кислородной деполяризацией. С ростом температуры возрастает скорость разряда попов водорода, и при температуре 573—633 К в деаэрированной воде коррозия протекает с водородной деполяризацией. При наличии в воде кислорода эта сталь может корродировать с кислородной деполяризацией и при высокой температуре. Скорость коррозии аустенитных нержавеющих сталей в насыщенном паре практически равна скорости коррозии ее в воде при той же температуре.
|
|
Скорость общей коррозии в воде в статических условиях при 553— 623 К составляет 0,8—4 мкм/год, а в пароводяной смеси при наличии кислорода при температуре до 873 К и давлении до 3,5 МПа она равна 5—10 мкм/год. В промышленных установках под действием радиации и при циркуляции воды и пара скорость коррозии несколько повышается, но до температуры 873К эти стали достаточно коррозионноустойчивы.
Наличие в стали шлаковых включений, трещин, раковин, различных загрязнений и других неоднородностей может привести к развитию местной коррозии (язвенной, точечной или отдельными пятнами). Этот вид коррозионных повреждений особенно опасен для тонкостенных оболочек твэлов, так как образование отверстия в оболочке открывает доступ теплоносителя к ядерному горючему, что приводит к аварийному состоянию реактора. Различные неоднородности металла приводят к образованию микрогальванических коррозионных пар, следствием которого являются местная депассивация участков металла и растравливание их.
Развитию местной коррозии способствует также присутствие в воде нона хлора, вызывающее усиление процессов депассивации поверхности металла, о чем свидетельствуют анодные кривые на рис. 8.6. С увеличением концентрации ионов хлора в растворе область пассивности сокращается и при концентрации 1000 мг/кг хлоридов металл переходит полностью в активное состояние. Поэтому допустимое количество хлоридов в воде реактора не должно превышать 0,1 мг/кг. Местная коррозия таких сталей более интенсивно протекает в застойных зонах, в щелях, в местах возможного упаривания воды, когда состав воды меняется в сторону увеличения в ней примесей. Эти стали используют в активной зоне реактора для изготовления кассет, подвесок, дистаициопирующнх и других элементов, тепловых экранов. При изготовлении деталей из разнородных металлов, например нержавеющая сталь—алюминий, возможно увеличение общей скорости коррозии алюминия за счет образования макрогальванических пар вследствие разности их потенциалов.
Аустенитная нержавеющая сталь подвергается еще одному виду местной коррозии—межкристаллнтной. Сущность ее состоит в том, что выдержка этих сталей при температуре 823—923 К приводит к выпадению карбидов хрома по границам зерен. Граничные области зерен обедняются хромом, что уменьшает электрохимическую стойкость этих областей. Отмечается, что сталь с повышенным содержанием углерода более чувствительна к межкристаллитпой коррозии, так как при этой температуре углерод интенсивно диффундирует к границам зерен. Увеличение содержания никеля в аустеиитной нержавеющей стали не влияет на склонность ее к этому виду разрушения; повышение содержания хрома или дополнительное легирование ее молибденом в некоторых случаях способствует пассивации обедненных границ и тем самым увеличивает стойкость сталей к межкристаллнтной коррозии. Однако такой способ борьбы с этим видом разрушения не является радикальным. Наилучшие результаты получают при легировании или, как принято говорить, при стабилизации аустенитных нержавеющих сталей титаном или ниобием. Титан и ниобий дают с углеродом весьма стойкие карбиды, не диссоциирующие даже в случае аустенизации сталей при температуре 1323—1373 К. В стабилизированных сталях содержание свободного углерода, т. е. не связанного в карбиды титана и ниобия, мало и не превышает растворимости углерода в аустените при комнатной температуре. В связи с этим образования карбидов хрома и обеднения хромом границ зерен не. происходит.
Количество титана и ниобия, вводимого в сталь, зависит от содержания углерода в ней и определяется но следующим зависимостям: %Ti = 5 (%С — 0,03); %Nb = 10 (%С — 0,03).
Если сталь легирована азотом, то стабилизировать ее следует ниобием, так как титан расходуется на образование нитридов. Для изготовления особо тонких труб с толщиной стенки 0,5 мм и менее также следует применять стали, легированные ниобием. Титан может давать карбиды, размеры которых могут быть почти соизмеримы с толщиной стенки трубы.
Стойкость аустенитных нержавеющих сталей к межкристаллитной коррозии существенным образом зависит от термической обработки. Стойкость деталей, изготовленных из стали, склонной к межкристаллитной коррозии, может быть повышена аустенизацией, если их рабочая температура не превышает 873 К. При аустенизации карбиды хрома диссоциируют, и сталь становится стойкой к межкристаллитной коррозии. В ряде случаев аустенитную нержавеющую сталь целесообразно подвергать стабилизирующему отжигу при температуре 1073—1143 К в течение 1—3 ч. При этом максимальное количество углерода связывается в карбиды. Пограничные области зерен при этом обедняются хромом. Однако при температуре 1073—1143 К скорость диффузии хрома достаточно велика, и вследствие диффузии его из
середины зерен к границам концентрация хрома у границ увеличивается и сталь становится стойкой к межкристаллитной коррозии.
Аустенитные нержавеющие стали, стабилизированные титаном и ниобием, после длительной эксплуатации при температуре 773— 873 К становятся склонными к межкристаллитной коррозии. Для устранения этого явления следует увеличивать отношение титана к углероду в стали и подвергать сталь аустенизации с последующей стабилизацией. Для обеспечения стойкости аустенитной нержавеющей стали к межкристаллитной коррозии при длительной эксплуатации при температуре 773—923 К отношение титана к углероду должно быть 10—17.
Выпадение карбидов и обеднение границ зерен хромом происходят при нагреве стали в процессе сварки. Нагрев стали до 823—923 К происходит в пришовной зоне, которая чаще всего и становится склонной к межкристаллитной коррозии.
Следует отметить, что на стали, склонной к межкристаллитной коррозии, последняя развивается не во всех средах. Наиболее интенсивно межкристаллитная коррозия развивается в кислых средах при повышенной температуре. При температуре выше 373 К и высоком давлении межкристаллитная коррозия развивается при наличии в водей паре кислорода более 0,1—0,3 мг/кг. В деаэрированной воде и паре межкристаллитная коррозия не развивается па сталях, склонных к ней, при испытаниях по стандартному методу, так же как и в аэрированной воде при температуре ниже 373 К.
Испытания сталей на склонность их к межкристаллитной коррозии производятся в соответствии с ГОСТ 6032—75. Склонность к межкристаллитной коррозии проверяют также на сварных образцах. Для контроля межкристаллитной коррозии на готовых изделиях в ряде случаев испытания также проводят в соответствии с ГОСТ 6032—75.
При изготовлении наиболее ответственных узлов проверке на межкристаллитную коррозию подвергают каждую поковку, трубу и т. п., для менее ответственных узлов достаточно произвести проверку металла данной партии плавки.
Аустенитные нержавеющие стали при совместном воздействии на них механических напряжений и коррозионно-агрессивной среды подвергаются особому виду разрушений — коррозионному растрескиванию. Напряжение может быть приложенным или остаточным, по, как правило, всегда растягивающим. Коррозионное растрескивание проявляется в виде трещин, скорость распространения которых зависит от состава и параметров коррозионной среды. Трещины могут развиваться от поверхности в глубь металла, проходя по телу зерен (транс- кристаллитное разрушение) и по границам зерен (межкристаллитное разрушение). Коррозионное растрескивание — опасный вид коррозионного разрушения и может привести к выходу из строя оборудования. Оно зависит от многих факторов — напряжения, состава среды, температуры, длительности воздействия среды, структуры и состава металла, степени пластической деформации (наклепа), характера защитных пленок на металле и др.
Для снижения склонности аустенитной стали к коррозионному растрескиванию необходимо обеспечить полное снятие наклепа. Растягивающие напряжения от наклепа, складываясь с растягивающими действующими (рабочими) напряжениями, могут резко усилить растрескивание.
Увеличение содержания в стали хрома при постоянном содержании никеля, а также уменьшение содержания элементов, способствующих образованию аустенита (углерода, азота), до 0,01—0,002% делают эту сталь более стойкой к коррозионному растрескиванию. Увеличение
содержания аустенитообразующего элемента — никеля — более 10— 12% делает аустенит более стабильным, а сталь более стойкой к коррозионному растрескиванию. Сплавы типа инконель, иикалой и др. с повышенным содержанием никеля более стойки к коррозионному растрескиванию, чем сталь Х18Н10Т.
Большую роль в коррозионном растрескивании аустенитных нержавеющих сталей играет состав коррозионной среды. Коррозионное растрескивание аустенитной нержавеющей стали наблюдается в растворах, содержащих хлориды и кислород. С увеличением содержания в растворе хлоридов уменьшается область пассивности таких сталей (см. рис. 8.6). Из рис. 8.6 видно, что при содержании в растворе 1000 мг/кг хлоридов стали полностью переходят в активное состояние. С ростом количества хлоридов увеличивается коррозионное растрескивание аустенитной нержавеющей стали. На рис. 8.7 представлены данные по коррозионному растрескиванию одной из таких сталей с наклепом 30% в нейтральных растворах при различном содержании хлорид-ионов при температуре 583 К без начальной деаэрации раствора. С ростом содержания хлоридов в растворе коррозионное растрескивание стали редко возрастает, и при концентрации хлоридов 1000 мг/кг образцы полностью разрушаются.
Коррозионное растрескивание аустенитных нержавеющих сталей происходит также в паровой фазе. Но наиболее опасными с точки зрения коррозионного растрескивания являются участки металла, подверженные попеременному увлажнению и высушиванию, т. е. местному упариванию. Ядерные энергетические реакторы используют
в качестве теплоносителя воду высокой чистоты. Реакторная и подпиточная вода строго нормируется по содержанию хлорид-иона. Но, несмотря на малые нормируемые значения содержания хлоридов в реакторной воде (от 0,1 до 0,5 мг/кг) и в воде парогенератора (0,5 — 1 мг/кг), в некоторых местах (места заделки труб парогенератора в трубные доски, участки с вялой циркуляцией и т. п.) может возникнуть упаривание и повышение содержания хлоридов до опасных с точки зрения коррозионного растрескивания концентраций. На рис. 8.8 представлена микрофотография трубки парогенератора, подверженной коррозии в результате упаривания воды с содержанием хлоридов 0,5 мг/кг.
В прямоточных парогенераторах с давлением 3—5 МПа растворимость солей в паре мала. В связи с этим происходит накопление хлоридов в воде в зоне испарения. Это исключает создание прямоточного парогенератора со средними параметрами пара из аустенитных нержавеющих сталей.
Для давлений 18 МПа и выше вследствие быстрого увеличения растворимости хлоридов в паре их концентрия в воде не превышает допустимых значений. Следовательно, прямоточные парогенераторы, в которых трубы теплообменника выполнены из аустенитных сталей, целесообразно создавать только на высокие давления. При давлении 3-5 МПа эти стали следует применять для изготовления парогенератора с многократной циркуляцией.
Коррозионное растрескивание может возникнуть как при высокой, так и при относительно низкой температуре (353—363 К). При попадании воды (например, вследствие протечек) на наружную поверхность трубопровода, нагретую до 353—373 К, происходит упаривание ее и увеличение концентрации хлоридов на поверхности трубопровода. В этом случае коррозионное растрескивание может происходить под влиянием внутренних напряжений в металле, которые могут возникнуть в процессе холодной прокатки труб, а также в результате наклепа от случайных ударов и царапин. При температуре 293—313 К, как правило, коррозионного растрескивания аустенитных нержавеющих сталей не происходит, что позволяет использовать их даже в конденсаторах, охлаждаемых морской водой. Хлориды могут проникать в сталь из изоляционных материалов, вызывая коррозию под напряжением. Коррозионное растрескивание сталей протекает и в паровой фазе при загрязнении пара хлоридами и кислородом. Отмечалось разрушение оболочек твэлов при ядерном перегреве пара вследствие развития коррозионного растрескивания.
Аустенитные нержавеющие стали имеют высокую коррозионную стойкость в широком интервале значений pH воды как в отношении общей скорости коррозии, так и в отношении коррозионного растрескивания. Кислород существенным образом влияет на коррозионное растрескивание стали, усиливая его. Так, при концентрации кислорода 1 мг/кг в присутствии в воде хлоридов наблюдается коррозионное растрескивание. Увеличение концентрации кислорода до 1200 мг/кг не приводит к резкому усилению процессов коррозионного растрескивания, т. е. в данном случае важна не концентрация кислорода, а сам факт его присутствия. Процессы коррозионного растрескивания сталей могут происходить и в отсутствие кислорода, если в воде имеются другие легко восстанавливающиеся элементы (например, трех-валентное железо).
В ядерных энергетических установках в результате радиолиза в воде реактора всегда присутствует радиолитический кислород. Процессы радиолиза воды в большей степени реализуются в кипящих реакторах, и количество радиолитического кислорода в паре может достигать 40 мг/кг. Поэтому принято строгое нормирование хлорид-иона в реакторной воде. Следовательно, для избежания коррозионного растрескивания стали состав воды, насыщенного и перегретого пара должен поддерживаться на высоком уровне чистоты. Склонность хромоникелевых аустенитных сталей к коррозионному растрескиванию уменьшается с увеличением содержания в них никеля.
Несовершенство решетки металлов и сплавой играет существенную роль в процессах их коррозионного растрескивания. Образование и особое распределение дефектов могут вызвать хрупкое состояние в обычно пластичном материале.
Никель оказывает заметное влияние на распределение дислокаций в аустенитных нержавеющих сталях. Эти дислокации связаны с плоскостями скольжения. При увеличении содержания никеля повышается энергия дефектов упаковки и облегчается поперечное скольжение.
Основываясь на зависимости распределения дислокаций деформированных аустенитных нержавеющих сталей от содержания никеля, следует ожидать значительного повышения стойкости нержавеющих сталей с 18% Сr против коррозионного растрескивания при содержании никеля более 18—20% (рис. 8.9).
При высокой концентрации щелочи и наличии напряжений в металле аустенитная нержавеющая сталь подвержена особому виду разрушений — щелочной хрупкости. Она может развиваться и в отсутствие кислорода. Природа этого разрушения еще не выявлена. Щелочная хрупкость может наблюдаться, например, в местах упаривания, где происходит увеличение содержания щелочи в 10 и более раз. Предупреждение коррозионного растрескивания аустенитной нержавеющей стали в ЯЭУ должно проводиться как применением современных средств водоочистки и водообработки, так и улучшением условий службы металла, его качества, сварки, термообработки. Существенное значение также приобретает правильный выбор тепловой схемы АЭУ и правильных конструктивных решений ее элементов.
Как уже отмечалось, аустенитные нержавеющие стали широко используют в системах с жидкометаллическим теплоносителем (эвтектика Pb—Bi, Na, К, эвтектика Na—К, Li). Коррозионное воздействие жидкого металла па сталь отличается своеобразными особенностями; эти воздействия имеют иную природу, чем химическая или электрохимическая коррозия. Это воздействие наиболее ощутимо при температуре большинства теплоносителей выше 773 К.
Для аустенитной нержавеющей стали при сложном составе жидко-металлического теплоносителя (например, эвтектика Na—К) и при наличии различных примесей (С, О, N, Н и др.) процессы взаимодействия значительно усложняются. В этом случае возможно избирательное взаимодействие отдельных компонентов жидкого металла с твердым н его компонентами, В системах из аустенитных нержавеющих сталей с щелочными жидкометаллическими теплоносителями термический перенос массы становится заметным при температуре 773—873 К с разностью температуры в системе порядка нескольких десятков градусов. Коррозионные поражения в этом случае локализуются в местах с максимальной температурой.
С увеличением скорости движения жидкометаллического теплоносителя скорость растворения стали увеличивается. Скорость растворения пропорциональна скорости движения жидкого металла в степени ~ 0,8. При больших скоростях к коррозионному воздействию добавляется еще эрозионное и механическое повреждение, особенно для тяжелых жидких металлов. Главной причиной переноса массы является значительное различие растворимости данного вещества при разной температуре (табл. 8.14). Так, в эвтектике Pb—Bi в активной зоне, где более высокая температура, возможно растворение из стали никеля или железа, а в менее нагретой части контура — осаждение их в виде интерметаллических соединений или чистого металла.
Примерная растворимость твердых металлов в жидких щелочных металлах Таблица 8.14
Жидкий металл |
Температура, К | Массовое содержание твердого металла,% | ||||
Ni | Cr | Fe | Nb | Mo | ||
LiLi Li | 873 1073 1273 1473 | 0,1 1,8 4 - | 0,01 0,02 - 4 | 0,002 0,005 0,025 0,065 | - - <0,0001 - | - - <0,0001 0,03-0,1 |
Na Na | 873 1073 1273 1473 | - - 0,004 - | 0,00001 - - - | 0,001 0,002 0,008 0,06 | - - 0,0007 0,003 | - - - - |
металле того или иного компонента, в результате которой может происходить, например, науглероживание аустенитной стали вследствие обезуглероживания перлитной, если такая присутствует в контуре. Это приводят к изменению механических свойств стали. Так, в эвтектике Pb—Bi происходит выщелачивание никеля и хрома из стали, в результате чего сильно снижаются прочность и пластичность сталей, а в зоне взаимодействия аустенит частично переходит в феррит.
В жидком натрии также возможны растворение компонентов стали В горячей части и осаждение их в холодной части контура. Аустенитные
нержавеющие стали весьма устойчивы в жидком натрии и в эвтектике Na— К. Так, при 873 К в контуре с движущимся потоком натрия при содержании в нем 0,002% кислорода глубина коррозионного поражения стали Х18Н8Б составляет 2—3 мкм/год. Следовательно, необходимо в первую очередь очищать жидкий металл от кислорода. Кроме того, очень легко происходят выщелачивание и перенос углерода. Поэтому при конструировании реакторных контуров из таких сталей необходимо брать стали с минимальным содержанием углерода, а также систематически очищать жидкий металл от углерода.
По сравнению с другими жидкометаллическими теплоносителями щелочные металлы наименее агрессивны и аустеиитные нержавеющие стали наиболее пригодны для длительной работы в них до температуры 873 К. При более высокой температуре наблюдается заметное науглероживание поверхности нержавеющих сталей, особенно сталей, легированных сильными карбидообразующими элементами, например титаном. Науглероживание усиливается при наличии углеродсодержащих материалов в системе и может сопровождаться переносом углерода в ней. Перенос массы усиливается также в случае значительного перепада температуры в системе (423—473 К).
Перенос массы характерен и для компонентов стали (№, Fe, Сr) при одновременной межкристаллитной коррозии стали. Скорость межкристаллитной коррозии аустенитных хромоникелевых сталей в движущемся натрии составляет 0,05—0,25 мм/год при температуре 873—973 К и зависит в основном от содержания кислорода в натрии, резко повышаясь при содержании кислорода более 0,005%. В этом случае на поверхности стали образуются продукты коррозии в виде сложных окислов железа и натрия, которые могут также растворяться в потоке и осаждаться затем на холодных участках контура. При температуре более 973 К можно применять жаропрочные и жаростойкие металлы и их сплавы, например на основе никеля (60—75% Ni, 16— 20% Сr5, до 5 % Мо, 1—2,5% Ti, до 10% W). Улучшения коррозионной стойкости жаропрочных сталей можно достигнуть добавкой до 30% А1.
При высокой температуре натрия (более 1073 К) целесообразно применять тугоплавкие металлы (Та, Mo, Nb, W) и их сплавы. Присутствие в жидком металле кислорода и азота снижает коррозионную стойкость тугоплавких металлов.
Коррозионная стойкость аустенитных сталей в эвтектике Na—К ниже, чем в натрии, и понижается с увеличением содержания калия в смеси. В литии скорость коррозии значительна, кроме того, не рекомендуется сочетать с ним стали с высоким содержанием никеля, так как никель хорошо выщелачивается. На увеличение скорости коррозии в литии существенным образом влияют примеси, в первую очередь азот и кислород. Хромоникелевые стали с литиевым теплоносителем можно применять до 773—873 К, при более высокой температуре (973—1073 К) предпочтение следует отдать ферритным нержавеющим сталям (например, 0X13, 1X13, IX12М2БФ н др.), не содержащим никеля. Изменение температуры вызывают те или иные термические напряжения в конструкционном материале, зависящие от скорости
изменения температуры. Термические напряжения зависят от физических и механических свойств материала. В аустенитных нержавеющих сталях с относительно низкой теплопроводностью термические напряжения могут быть значительны и привести к разрушению стали.
Конструкционные материалы активной зоны подвергаются облучению нейтронами, γ-квантами и электронами.
Облучение приводит к изменению механических свойств материалов: возрастают предел текучести и предел прочности (в меньшей степени), а относительное удлинение и относительное сужение умень
шаются. Таким ооразом, облучение вызывает радиационное охрупчивание металлов и сплавов. Это охрупчивание в сочетании с термическими и другими напряжениями, вибрациями, термическими циклами и коррозионным воздействием теплоносителя может привести к разрушению оболочек твэлов. Низкотемпературное облучение сталей 1X18H10T флюенсом нейтронов до 4·1022 см-2 вызывает повышение прочности и снижение пластичности (рис. 8.10).
С увеличением температуры облучения выше 773 К механические свойства значительно ухудшаются. Высоко температурное охрупчивание свойственно не только нержавеющим аустеннтным сплавам-сталям, но и сплавам на никелевой основе. На рис. 8.11 приведено изменение механических свойств жаропрочного сплава XH77TЮP, облученного при 423—473 К и испытанного при температуре до 1073 К. При температуре выше 873 К происходит быстрое снижение относительного удлинения и предела прочности. Образование интерметаллических фаз, а также накопление гелия в результате некоторых ядерных реакций способствуют охрупчиванию стали и резкому снижению ее пластичности.
Дата добавления: 2021-01-21; просмотров: 540; Мы поможем в написании вашей работы! |
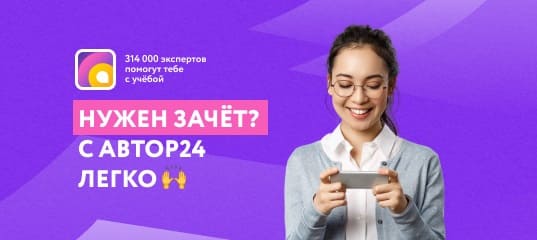
Мы поможем в написании ваших работ!