ФАКТИЧЕСКАЯ ПРОИЗВОДИТЕЛЬНОСТЬ
СТРУКТУРА МАШИН-АВТОМАТОВ
Технологические машины-автоматы представляют собой рабочие машины , в которых механизированы не только все рабочие и вспомогательные операции, но и процесс управления.
Машина-автомат состоит из тех же структурных элементов, которые входят в состав машинного агрегата, т.е. двигателя (или двигателей, передаточных механизмов и исполнительных механизмов. Последние подразделяются на исполнительные механизмы основных и вспомогательных операций.
Отличаясь от обычной машины тем, что рабочие и вспомогательные операции выполняются без участия человека, машина- автомат имеет еще один структурный элемент – систему управления. Система управления определяет последовательность работы и взаимодействие исполнительных механизмов машины, осуществляет блокировку (защиту) машины при нарушении технологических режимов, может регулировать параметры, при которых выполняются отдельные операции.
В машинах-автоматах химических производств обычно используются электродвигатели, преобразующие электрическую энергию в механическую. Механическая энергия либо непосредственно (через передаточные механизмы) подводится к исполнительным механизмам, либо дополнительно преобразуется, когда в энергетическую цепь привода включены пневматические или гидравлические агрегаты. Например, в случае дополнительного преобразования, электродвигатель приводит гидронасос, от которого через систему коммуникаций приводится электродвигатель.
|
|
Передаточные механизмы передают движение от двигателя кисполнительным механизмам, при этом в большинстве случаев изменяются кинематические параметры движения. Передаточные механизмы машин-автоматов особой специфики не имеют – они представляют собой традиционные передачи, применяемые в машиностроении: ременные, зубчатые, цепные, варианты скоростей и т.п.
Специфичными для машин-автоматов являются дополнительные механизмы и система управления, особенности которых определяются выполняемыми машиной видами операций, характером движения рабочих органов и их взаимосвязью.
Стадия создания машины-автомата
Основными этапами проектирования схемы машины-автомата являются:
1. Разработка машинного технологического процесса.
2. Синтез структурной схемы машины, принципиальной компоновочной схемы машины и определение ее основных параметров – числа позиций, потоков и т.п.
3. Составление принципиальной кинематической (гидрокинематической, гидропневматической и т.п.) схемы и проектной циклограммы машины.
4. Разработка и расчет принципиальной системы управления.
|
|
5. Расчет теоретической и прогнозирование фактической производительности машины.
В процессе работы машины-автомата можно различить три взаимосвязанных потока: поток обрабатываемых объектов, энергетический и информационный потоки.. Поток обрабатываемых объектов состоит из деталей, материалов, изделий, которые перемещаются внутри машины.
В процессе их перемещения, который сам по себе представляет вспомогательную транспортную операцию, вывполняются рабочие операции по изменению физических свойств, состояния или формы объекта обработки, а также и такие вспомогательные операции, как загрузка, захват, фиксация, разгрузка и т.п. Выполнение всех (в особенности рабочих) операций связано с энергетическими затратами. Таким образом, от двигателя поток энергии идет через передаточные механизмы к исполнительным механизмам, в которых происходит то или иное преобразование энергии с получением новых качеств объекта обработки. Этот процесс сопровождается частичной диссипацией (рассеиванием) энергии из-за трения в передаточных и исполнительных механизмах. Поток информации управляет работой исполнительных механизмов машины-автомата и направлен от системы управления к исполнительным и перердаточным механизмам и к двигателям; в машинах-автоматах с обратной связью меняется поток информации и к двигателям, в машинах-автоматах с обратной связью имеется поток информации противоположного направления – от структурных элементов машинного агрегата к системе управления. Поток информации, идущей от системы управления, состоит из команд на переключение или останов тех или иных исполнительных механизмов и их двигателей, включение или выключение контрольно-измерительных операций, операций регулировки, поднастройки и т.п.
|
|
Поток информации, направленной от исполнительных механизмов машины-автомата или их рабочих органов к системе управления, передает сведения о состоянии объекта обработки рабочих органов и тех или иных параметров технологического процесса. Эта информация может характеризовать положение объекта обработки, его размеры и их изменение в процессе рабочих операций, износ рабочих органов, температуру, давление и т.п. Через этот канал осуществляется обратная связь технологического процесса с системой управления, что позволяет регулировать его в зависимости от контролируемых параметров.
|
|
ЦИКЛЫ МАШИН-АВТОМАТОВ
Прерывно-операционные технологические процессы обычно осуществляются при помощи машин-автоматов циклического действия, объект обработки в таких машинах штучный.
Движение объектов обработки, энергетический и информационный потоки в этих машинах-автоматах характеризуются технологическим, кинематическим, рабочим, энергетическим и информационным циклами.
Технологический цикл ТТ (см. стр.8) – время, необходимое для выполнения всех операций технологического процесса, или время, в течение которого объект обработки находится внутри машины.
Кинематический цикл ТК машины-автомата при установившемся режиме работы – минимальное время, по истечении которого повторяются положения, скорости и ускорения всех рабочих органов машины.
Рабочий цикл ТР период времени между двумя последовательными выдачами единицы продукции. Следует отметить, что рабочий цикл может отличаться от других циклов по продолжительности, в частности, от технологического, что обусловлено структурой машины (см.стр. 23).
Энергетический цикл ТЭ – минимальный период установившегося движения, по истечении которого повторяется закономерность изменения мгновенной мощности машины.
Информационный цикл Ти минимальный период времени, по истечении которого вновь возобновляется передача потока информации в заданной последовательности.
Кинематический, энергетический и информационный циклы обычно совпадают. Связь технологического и рабочего цикла с кинематическим определяется типом машины-автомата.
Кинематический цикл отдельных исполнительных механизмов, входящих в машину-автомат, может быть равен кинематическому циклу машины или кратен ему.
Часть цикла исполнительного механизма, во время которой выполняется заданная операция, называется фазой рабочего хода, соответственно различают фазу холостого хода (механизм движется, а операция не выполняется) и фазу выстоя или останова (исполнительный механизм неподвижен). Для машин нештучной продукции сохраняют смысл технологический и информационный циклы.
КЛАССИФИКАЦИЯ ТЕХНОЛОГИЧЕСКИХ МАШИН
С.И.Артоболевским разработана классификация технологических машин по их функционально-производственной схеме, т.е.е в зависимости от связи между перемещениями объектов обработки внутри машины и перемещениями рабочих органов. Технологические машины разделяются на три рода. В машинах I рода для осуществления заданного технологического процесса необходимо обеспечить заданные значения скоростей vp рабочих органов по величине и направлению.
Машины I рода могут дать нештучную и штучную продукцию. Машинами I рода нештучной продукции в химической промышленности являются мешалки, смесители, дробилки, вальцы, червячные машины, центрифуги непрерывного действия и пр. Машины I рода штучной продукции – каландры некоторых типов, агрегаты для изготовления т руб из стеклопластиков и т.д.
В машинах II рода необходимо помимо заданных скоростей рабочих органов обеспечить дополнительную заданную последовательность в их перемещениях. Эти машины также могут давать нештучную и штучную продукцию.
К машинам II рода производства нештучной продукции в химической промышленности относятся автоматические фильтр-прессы, центрифуги периодического действия, оплеточные машины и др. К машинам штучной продукции относятся различного типа гидравлические и механические прессы, вулканизаторы, станки для сборки автопокрышек, станки для механической обработки изделий из полимерных материалов, сортировочно-контрольные машины для резино-технических изделий, литьевые машины и т.д. В машинах III рода обеспечиваются заданная скорость и последователльность движения рабочих органов, а также определенные их относительные перемещения. Машины III рода используются только для производства штучной продукции (копировальные станки, трикотажные автоматы и т.п.
Рис. 5 Схема классификации технологических машин II рода
В связи с большим разнообразием машин II рода рассмотрим схему их классификации (рис. 5).
Машины II рода для штучной продукции характеризуются тремя циклами: рабочим Тр , кинематическим Тк и технологическим ТТ . Эти машины могут начать обработку изделия только при определенном относительном положении рабочих органов; повторяемость таких положений определеляет длительность рабочего цикла машин II рода.
В зависимости от характера перемещения объекта обработки различают три класса машин II рода для штучной продукци. К 1-му классу относятся машины, в которых изделие может быть неподвижным или вращаться вокруг одной из своих осей. Таким образом , машины 1-го класса являются однопозиционными, число позиций q = 1. Рабочие органы машины осуществляют операции технологического процесса последовательно (машины группы II, 1А) или параллельно (машины группы II, 1Б). В этих машинах возможно одновременное выполнение всех технологических операций на нескольких объектах обработки, такие машины называются многопоточными (число потоков w> 1). Например, в промышленности переработки пластмасс в изделия и при изготовлении резино-технических изделий широко используются прессы-автоматы с многогнездным пресс-инструментом Число гнезд пресс-инструмента соответствует числу потоков изготавливаемого изделия. Многопоточными машинами являются этажные прессы, сдвоенные индивидуальные вулканизаторы (w=2) и т.п.
В том случае, если однопозиционная машина является w-поточной, она должна иметь w рабочих мест, оснащенных всеми аагоегатами, необходимыми для выполнения операций технологического процесса. Если рабочие места неподвижны, то либо число загрузочно-разгрузочных устройств увеличивается в w раз, либо эти устройства должны перемещаться вдоль рабочих мест, и их конструкция усложняется.
Циклы выполнения операций в отдельных потоках могут выполняться параллельно или со сдвигом фаз. При совмещении циклов во времени необходимо загрузочно-разгрузочные операции производить одновременно, а при сдвиге фаз загрузочные операции можно распределить равномерно по времени.
Время рабочего цикла Тр в w-поточной машине со сдвигом фаз связано со временем рабочего цикла соответствующей однопоточной машины:
Тр' =
В группе машин типа II, IА с последовательным выполнением операций технологического процесса или при их частичном совмещении рабочий и технологический циклы одинаковы:
Тр = ТТ = tу + + tс -
(2)
где tу и t с – время, затрачиваемое на операции установки и съема объекта обработки;
- суммарное время, затрачиваемое на выполнение отдельных операций технологического процесса:
- суммарное время перекрытия (совмещения) отдельных операций технологического цикла машины.
К машинам-автоматам и полуавтоматам II рода группы IА относятся кривошипные таблеточные машины, термопластавтоматы, индивидуальные камерные вулканизаторы, форматоры-вулканизаторы, шиносборочные машины и т.п. В этих машинах иногда технологический процесс выполняется в несколько потоков.
При параллельном выполнении операций обработки (многоинструментальная обработка) для машины группы II, IБ
Тр =ТТ = tу + tmax + tс , (3)
где tmax - время, затрачиваемое на выполнение наиболее длительной операции (лимитирующая операция) из числа n операций данного технологического процесса. Примером машины группы II, IБ являются токарный полуавтомат для механической обработки пластмассовых деталей – снятия гоаьа. В машине одновременно выполняются три операции: две выполняются резцами (снятие заусенцев), а одна – зенкером (снятие пленки в отверстии).
Как видено из сопоставления формул (2) и (3), использование много многоинструиментальной обработки изделий позволяет сократить время рабочего цикла и, следовательно, увеличить производительность машины
Машины II рода 2-го класса являются многопозиционными и разделяются на две группы. К группе II, 2А относятся машины, в которых объект обработки периодически перемещается с одной позиции на другую при помощи специального транспортирующего устройства периодического действия , например револьверного или конвейерного типа.
Рабочий цикл технологических машин группы II, 2А равен кинематическому циклу транспортирующего устройства Тmр:
Тр = Ттр = to + t n
где to - время останова транспортирующего устройства (время останова объекта.
ТЕХНОЛОГИЧЕСКАЯ И ЦИКЛОВАЯ ПРОИЗВОДИТЕЛЬНОСТЬ
Цикловая производительность машины-автомата определяется количеством изделий, выдаваемой машиной в единицу времени в предположении, что машина работает непрерывно и вся производимая ею продукция удовлетворяет техническим требованиям.
Если за рабочий цикл Тр сек в одном потоке выдается одно изделие, а общее число потоков в машине w , то цикловая производительность машины в штуках за 1 сек будет
Время Tр зависит от структуры машины. Для машин II рода штучной продукции в табл. 12 приведены формулы для расчета времени рабочего цикла Tр (см.гл. II) и цикловой производительности Qц .
Формулы расчета рабочего цикла и цикловой производительности машин II рода штучной продукции
Класс | Группа | Время рабочего цикла Тр в сек | Цикловая производительность Qц в штуках за 1 сек |
1 | II IА | tу + ![]() ![]() | w
tу + ![]() ![]() |
II IБ | tу + tmax + tс | w tу + tmax + tс | |
2 | II 2А | tmax + tn
![]() ![]() | w
tmax + tn
![]() |
II 2Б | tосн | ![]() | |
3 | II 3А | tmax | ![]() |
II 3Б | ![]() | ![]() |
Как следует из таблицы, в общем случае рабочий цикл
Тр = tтр + t х , (80)
где tр - время рабочих ходов; tх – время холостых ходов.
При совмещении холостых ходов с рабочими или их отсутствии
tх = 0) получим выражение, определяющее технологическую производительность машины Л в штуках за 1 сек.
В машине циклического действия штучной продукции
где η коэффициент производительности , который характеризует степень непрерывности технологического процесса, выполняемого в данной машине. Этот коэффициент отражает конструктивное совершенство машины-автомата, степень ее приближения к машине непрерывного действия, т.е. к такой машине, где основные операции технологического процесса выполняются непрерывно. Чем выше коэффициент производительности, тем конструктивно совершеннее машина.
Следует иметь ввиду, что технологическая производительность не является неизменной величиной: использование прогрессивной технологии, новых физических и химических методов обработки позволяет сокращать величину К.
В машинах-автоматах с жесткими связями время рабочего цикла практически постоянно и от длительности работы машины не зависит. Следовательно, постоянными являются технологическая и цикловая производительность машины. В машинах с гидравлическими и пневматическими исполнительными механизмами колебания времени рабочего цикла более значительны, так как свойства рабочего тела (масла, воздуха) зависят от температуры и других факторов.
Производительность машин-автоматов I рода штучной продукции в штуках в м/сек:
где v - cкороть перемещения объекта обработки в машине в м/сек;
w - число потоков;
l - длина обрабатываемой части изделия в м;
а - расстояние между двумя соседними обрабатываемыми частями одного или разных изделий в м.
Производительность машин-автоматов нештучной продукции в зависимости от вида изделий измеряется в единицах длины, площади, объема или массы, отнесенных соответственно к единице времени.
Теоретическая производительность машин I нештучной продукции подсчитывается по формулам (соответственно в м/сек ; м2сек, м3/сек и кг/сек
Q = vw;
Q = vbw;
Q = vbhw ;
Q = vbhpw ;
Где b – ширина в м;
h– высота или толщина слоя продукта в м;
p – плотность материала продукта в кг/м3 ;
Производительность машин II рода нештучной продукции (соответственно в м/сек; м2/сек; м3/сек и кг/сек)
;
ЦИКЛОГРАММЫ
Рассмотрим пример:
Изготовление изделий выдуванием из литьевых заготовок на оправках.
(Бортников, 321) /Диск «Foboha» см.в папке ФПК-2/
Стадии:
1) плавление, гомогенизирование и дозирование расплава;
2) установка оправки в форму для литья;
3) смыкание литьевой формы и подвод узла впрыска;
4) впрыск расплава и выдержка;
5) размыкание литьевой формы и перенос оправки с отлитой заготовкой в форму для выдувания;
6) смыкание формы для выдувания и формование изделия;
7) охлаждение;
8) размыкание форм и извлечение изделия.
Последовательность операций, выполняемых отдельными исполнительными механизмами машины-автомата, отображается в циклограмме. Циклограмма машины-автомата – графическое отображение программы его работы. Циклограмма машины представляет собой совокупность циклограмм исполнительных механизмов, каждая из которых показывает интервалы движения и выстоя соответствующего рабочего органа исполнительного механизма за кинематический цикл.
В машинах-автоматах, ведущие звенья исполнительных механизмов которых приводятся от одного вала (называемого главным или распределительным), можно использовать круговую циклограмму , в которой циклограммы отдельных механизмов представлены концентрическими кольцами, разделенными радиальными лучами на центральные углы, соответствующие интервалам движения соответствующих механизмов (см.рис.9).
В прямоугольной циклограмме циклы отдельных механизмов представлены вытянутыми по горизонтали прямоугольниками. Эти прямоугольники поделены на части, соответствующие интервалам движения рабочего органа, выраженные в единицах времени или в углах поворота распределительного вала.
Линейные циклограммы отличаются от прямоугольных циклограмм тем, что в них отображен процесс перемещения рабочих органов, интервалу выстоя соответствует прямая, параллельная оси абсцисс , интервалам движения – наклонные прямые; узел впрыска.
Синхронные диаграммы представляют собой дальнейшее развитие линейных циклограмм: для отдельных исполнительных механизмов вместо условного изображения перемещений строятся графики перемещений их рабочих органов по углу поворота распределительного вала с соблюдением масштаба. Такая диаграмма дает полное представление об относительном движении рабочих органов (или других звеньев исполнительных механизмов) и используется при проектировании циклограмм тех исполнительных механизмов, которые взаимодействуют между собой. В частности, построение синхронных диаграмм позволяет «уплотнять» циклограммы машины, что приводит к сокращению длительности рабочего цикла и повышению производительности машины.
Анализ циклограмм машин-автоматов в сопоставлении с кинематической схемой машины позволяет уяснить взаимодействие исполнительных механизмов, правильность в соотношении интервалов движения рабочих органов, их соответствие технологическому процессу, вскрыть резервы сокращения рабочего цикла машины.
При проектировании схем управления машин-автоматов циклограмма является основным документом, определяющим последовательность действий исполнительных механизмов.
Циклограмма автомата состоит из совмещенных циклограмм всех исполнительнных механизмов машины (гл.III). Из рассмотренной ранее классификации машин, иллюстрированной различными примерами машин-автоматов химических производств, следует , что в зависимости от способа проведения операций технологического процесса возможны три типа циклограмм с последовательным, параллельно-последовательным (смешанным) и параллельным выполнением операций.
Приведенные циклограммы иллюстрируют эфективность использования многоинструментальной обработки. Однако последняя далеко не всегда может быть использована как резерв повышения производительности по самому характеру технологического процесса, вследствие чего и нашли применение многопозиционные машины (II рода, 2-го класса), которые позволяют распределить операции по отдельным позициям и выполнять их параллельно. Рабочий цикл в этом случае (рис. 138,г) будет еще короче [формула (4)].
![]() | ТIp | ||||
Подачи | |||||
I операции | |||||
II операции | |||||
III операции | |||||
Съема |
а)
![]() | ТIIp | ||||
Подачи | |||||
I операции | |||||
II операции | |||||
III операции | |||||
Съема | |||||
б)
![]() | ТIIp | ||||
Подачи | |||||
I операции | |||||
II операции | |||||
III операции | |||||
Съема | |||||
в)
![]() | ТIIp | |||||
Подачи | ||||||
I операции | ||||||
II операции | ||||||
III операции | ||||||
Съема | ||||||
Поворота стола | ||||||
г)
Рис. 138. Циклограммы машин-автоматов:
а – с последовательным выполнением операций;
б – с последовательно-параллельным выполнением операций;
в – с параллельным выполнением основных операций;
г – для многопозиционной машины.
При построении циклограммы машиины один из исполнительных механизмов принимается за «основной» ; обычно это механизм, выполняющий основную операцию технологического процесса. В машинах-автоматах с приводом исполнительных механизмов от распределительного вала часто в качестве такого механизма принимают рычажный механизм или один из кулачковых механизмов. Цикловую диаграмму машины удобно устроить, начиная с положения «основного» механизма, принимая за него начало рабочего хода. Положение циклограмм других исполнительных механизмов по отношению к циклограмме «основного» механизма задается фазовым временем ti 1, ,которое определяет тот промежуток времени, по истечении которого начинается рабочий ход i-го механизма (рис. 139). В том случае, если ведущие звенья «основного» и i-го исполнительного механизмов приводятся от одного вала, положение циклограммы i-го механизма по отношению к «основному» определяется фазовым углом xi 1 , этого исполнительного механизма, который при постоянной угловой скорости вала машины будет пропорционален времени ti1.
Теория циклограммирования (теория синтеза цикловых диаграмм машин-автоматов) рассматривает два этапа составления циклограмм – предварительный и окончательный. При предварительном составлении циклограммы машины производится ориентировочная оценка деятельности технологического, кинематического и рабочего циклов машины. Для этого анализируются все операции технологического процесса и из них выделяются те, в которых движение рабочих органов обусловлено определенными закономерностями выполняемого процесса, вследствие чего время выполнения этих операций не может быть сокращено.
Далее оценивается возможность параллельного и параллельно-последовательного выполнения операций технологического процесса, т.е. выявляются условия полного или частичного операций. Наконец, определяется длительность межооперационных выстоев. Последние могут быть двоякого рода: обусловленные технологическим процессом (выдержка при прессовании, вулканизации, отверждении и т.д.) или конструктивными особенностями машины (время срабатывания переключателей и т.п.) Внецикловые простои см.след.стр.
№ № Исполнительных механизмов | Время, сек; Угол поворота распределительного вала | |||||
I | ||||||
2 | ||||||
![]() ![]() | t2.1 |
х •2.1 • • • | ||||
i | ||||||
![]() ![]() | ti1 х•i1 | |||||
Рис. 139. Циклограммы «основного» и i-го исполнительных механизмов машины.
В зависимости от структуры машины, ее рода и класса, по формулам гл. II рассчитывается время технологического и рабочего цикла машины. Таким образом, при предварительном составлении циклограммы автомата не учитывается особенность кинематических схем исполнительных механизмов; построение циклограммы и расчет времени цикла производится лишь на основании рассмотрения операций технологического процесса и структуры машины. Это позволяет производить предварительное составление циклограммы непосредственно после выбора и расчета структурной схемы машины. При составлении циклограмм может осуществляться выравнивание нагрузки за энергетический цикл машины путем равномерного распределения и последовательного чередования интервалов выполнения рабочих операций. Рассредоточивание нагрузок по времени цикла позволяет уменьшить пики моментов на валу двигателя, создает более благоприятные условия его эксплуатации или даже допускает возможность снижения установочной мощности. Построение циклограммы по условию выравнивания приведенных моментов сил производится обычно в тех случаях, когда технологический процесс состоит из ряда рабочих операций, приведенные моменты сил, от которых являются величинами одного порядка.
На окончательном этапе составления циклограммы производится ее «уплотнение»; сокращение длительности рабочего цикла путем частичного совмещения фаз движения исполнительных механизмов с учетом их взаимной связи; уточнение значений фазового времени или фазовых углов; проверка правильности взаимодействия исполнительных механизмов; определение возможных погрешностей в реализации циклограммы (возникающих из-за упругости звеньев, наличия зазоров, колебаний температуры и по другим причинам) и коррекция циклограмм и законов движения рабочих органов и исполнительных механизмов машины. При составлении циклограммы необходимо принимать во внимание особенности той системы управления, которая используется в проектируемой машине.
ФАКТИЧЕСКАЯ ПРОИЗВОДИТЕЛЬНОСТЬ
В реальных условиях машины не работают непрерывно. Простои машин связаны с необходимостью смены инструмента, заправки материала, устранения неполадок и т.д. Внецикловые простои по функциональным признакам разделяются на пять видов.
1. Простои по инструменту. Сюда относятся все потери времени, связанные с заменой инструмента из-за его неработоспособности, регулировки, подналадки и т.п.
2. Простои по оборудованию. К этому виду простоев относятся те, которые связаны с неработоспособностью машины из-за отказов в работе ее механизмов и устройств, нарушения регулировки и т.д. Сюда относится также время ремонта и профилактического обслуживания машины.
3. Простои по организационным причинам. Эти потери времени имеют место в тех случаях, когда машина работоспособна, однако вынуждена простаивать вследствие отсутствия материала (заготовок), электроэнергии, несвоевременного прихода обслуживающего персонала и т.п.
5. Простои по переналадке машины на выпуск новой продукции.
Фактическая производительность машины всегда меньше цикловой за счет внецикловых простоев. Перечисленные выше причины простоев можно разделить на две группы : простои по техническим причинам, т.е. связанные с конструктивным совершенством инструмента и машины и их надежностью, и простои по организационным причинам. Простои первой группы функционально связаны с режимом работы машины-автомата, так как износ инструмента, кинематических пар, регулировка, ремонтные и другие работы зависят от длительности работы машины и условий, в которых при этом находились ее исполнительные механизмы и устройства. Простои второй группы функционально не связаны с режимом работы машины и обусловлены организацией труда и производства на том предприятии, на котором установлена машина (трудовая дисциплина, своевременная подача материала и заготовок, отбраковка заготовок предыдущих операций, частота переналадок и т.п.).
Если принять, что за время θ за машиной последняя работала без простоев θр и выдала единиц продукции, а суммарное время простоев составляло ∑θn , то получим
θ = θр + ∑θn
где θ - время наблюдений ;
θр - время работы;
∑θn - суммарные простои.
Фактическая производительность машины
(81)
где суммарное количество выпущенной штучной продукции
где - время работы машины;
Zф - длительность работы цикла.
Подставляя значение и Zф в формулу (81) , найдем
Величина ηис называется коэффициентом использования , он представляет собой отношение времени бесперебойной работы машины за период наблюдения ко всему времени наблюдения:
Отношение суммарного времени простоев ко времени бесперебойной работы машины за время наблюдения представляет собой внецикловые потери . Чем меньше внецикловые потери, тем выше коэффициент использования машины и, следовательно, тем ближе фактическая производительность машины к цикловой.
Количество изготовленных деталей Zф пропорционально времени θр,, поэтому:
где цикловые потери, приходящиеся на единицу продукции. Принимая во внимание уравнение (80) получим
Из последней формулы следует , что внецикловые потери на единицу продукции ∑θорг:
∑θn = ∑θmex + ∑θорг
Коэффициент использования можно представить в виде:
или
Выражение
(82)
Называется коэффициентом технического использования. Коэффициент технического использования характеризует надежность машины.
Величина
Называется коэффициентом загрузки. Его значение зависит как от технического совершенства машины, так и от организации труда.
В процессе эксплуатации машины фактическая производительность не остается постоянной: она растет в период пуска и освоения машины, сохраняется приблизительно постоянной с некоторой тенденцией к увеличению в период стабильной эксплуатации и несколько снижается из-за увеличения износа и частоты отказов к моменту приближения периода планово-предупредительного ремонта.
Величины, характеризующие коэффициент технического использования и коэффициент загрузки, являются случайными, следовательно, для их нахождения, а также для анализа резервов производительности или сравнения различных вариантов машин необходимы длительные наблюдения.
Практически ограничиваются сравнительно кратковременными исследованиями значений Qф, ηис , ηmex , ηз ,∑tnв период стабильной эксплуатации машины.
Изложенные положения о расчете производительности машин распространяются и на автоматические линии. Методика анализа производительности машин и автоматических линий и расчета их надежности подробно рассматривается в ряде специальных работ.
Дата добавления: 2020-12-12; просмотров: 148; Мы поможем в написании вашей работы! |
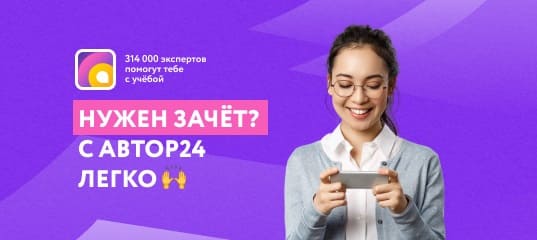
Мы поможем в написании ваших работ!