Режущий инструмент, применяемый на токарных станках
Хвостовики
у сверла до 10 мм цилиндрический (обычно) и крепится в патроне. У хвостовика имеется поводок для дополнительной передачи крутящего момента.
Сверла большего диаметра имеют конический хвостовик. На конце – лапка, не позволяющая сверлу провертываться в шпинделе и служащая упором при выбивании сверла из гнезда. Размеры 0,1,2,3,4,5,6 с разными размерами конуса
Изготавливаются – У10, У12А, хромистой 9Х, хромокремнистой 9ХС, быстрорежущей Р9, Р18, металлокерамические сплавы марок ВК6, ВК8 и Т15К6, с корпусами из стали марок Р9,9ХС и 40Х.
Сверла с пластинками из твердых сплавов применятся для чугуна, закаленной стали, пластмасс, стекла, мрамора.
Бывают сверла с отверстиями для подвода охлаждающей жидкости к режущим кромкам сверла.
При сверлении затупившееся сверло очень быстро нагревается, настолько, что произойдет отпуск стали, и сверло станет негодным. Поэтому сверла охлаждают.
Сталь………………………………….мыльная эмульсия или смесь минерального и жирного мала.
Изм. |
Лист |
№ докум. |
Подпись |
Дата |
Лист |
10 |
УП 21.02.01 ЭС5-19 000000 |
Медь…………………………………..мыльная эмульсия или сурепное масло
Алюминий…………………………….мыльная эмульсия или в сухую
Дюралюминий………………………..мыльная эмульсия, керосин с касторовым или сурепным маслом
Силумин………………………………мыльная эмульсия или смесь спирта со скипидаром.
|
|
Износ сверла обнаруживается по резко скрипящему звуку.
Заточку ведут с охлаждением водно-содовым раствором. Затачивают сверло следующим образом: слегка прижимая режущую кромку к поверхности абразивного круга так, чтобы режущая часть приняла горизонтальное положение, прилегая задней поверхностью к кругу. Плавным движением правой руки, не отнимая сверла от круга, поворачивают сверло вокруг своей оси, соблюдая правильный наклон, затачивают заднюю поверхность, при этом следят за тем, чтобы режущие кромки были прямолинейны, имели одинаковую длину и были заточены под одинаковыми углами.
Сверла с режущими кромками разной длины или с разными углами их наклона будут сверлить отверстия больше своего диаметра.
Сверлят ручными, электрическими, пневматическими дрелями и Эл. станками.
1.7 Нарезание резьбы
Нарезание резьбы - операция, выполняемая со снятием стружки или методом накатывания, в результате которой образуются винтовые канавки на поверхностях.
Резьба бывает двух видов: наружная и внутреняя. Резьба может быть правой и левой.
По профилю резьбы бывают:
· Трубная, как бывшая дюймовая, но меньше по шагу измеряется в дюймах и обозначается Труб 3/8”. Бывает до 6 дюймов. Дюймовая резьба применяется только в старых машинах. Имеет в профиле равнобедренный треугольник с углом при вершине 55 градусов, вершины выступов винта и гайки плоско срезаны, по наружному и
Изм. |
Лист |
№ докум. |
Подпись |
Дата |
Лист |
11 |
УП 21.02.01 ЭС5-19 000000 |
|
|
· Метрическая, угол профиля 60 о,которые бывают с крупным шагом М20 и мелким М20 1,5. применяются как крепежные в технике и кип.
· Прямоугольная – квадратный профиль, для червяков, непрочная.
· Трапецеидальная резьба ленточная. В форме трапеции с углом в 30о. Витки имеют наибольшее сечение у основания, у неё малое трение поэтому применяется для передачи вращения и больших усилий. Преобразуют вращательное движение в поступательное;
· Упорная профиль в виде неравнобокой трапеции, основания витков закруглены для прочности, на домкратах и винтах прессов;
· круглая обладает выносливостью в загрязненной среде, патроны электролампочек.
· Упорная резьба имеет профиль в виде неравнобокой трапеции с рабочим углом при вершине 30 градусов. Основания витков закруглены, что обеспечивает в опасном сечении прочный профиль (винтовые пресса, домкраты);
|
|
· Круглая резьба имеет профиль образованный двумя дугами, сопряженными с небольшими прямолинейными участками, и углом в 30 градусов.
По числу ниток резьбы разделяются на однозаходные и многозаходные. Ходом резьбы называют осевое перемещение винта, на один его борот. У многоходовых на торце видно несколько витков.
Клепка, пайка металла
Клепкой металла называется соединение двух или нескольких деталей при помощи заклепок, представляющих собой цилиндрические стержни с головками.
Клепка металла применяется для создания неразъемного соединения деталей, а также соединения листового полосового и фасонного металла. Заклепочные соединения применяют при ремонтах воздуховодов и вентиляторов, а также при изготовлении отдельных деталей вентиляционных систем.
Клепка металла подразделяется на холодную, горячую и смешанную. Заклепки изготовляются из мягкой стали и состоят из цилиндрического стержня и головки, называемой закладной.
Головка, которая расклепывается на другом конце стержня и служит для скрепления деталей, называется замыкающей. Клепка называется обыкновенной, если обе головки заклепки находятся над поверхностями
Изм. |
Лист |
№ докум. |
Подпись |
Дата |
Лист |
12 |
УП 21.02.01 ЭС5-19 000000 |
|
|
Толщина заклепок выбирается расчетом. Длина стержня заклепки между головками не должна превышать пяти диаметров стержня; в случае отсутствия этого соотношения следует заклепочное соединение заменить болтовым. Клепку производят на специальных стальных поддержках, имеющих углубление по форме головки заклепки, чтобы не смять ее при расклепывании.
Чтобы поддержка не отскакивала от головки при нанесения ударов молотком, вес ее должен быть в 4—5 раз больше веса молотка. Молоток по весу выбирают в зависимости от диаметра стержня заклепки.
Для склепывания деталей, кроме слесарного молотка (лучше с квадратным бойком) и стальной поддержки, применяют стальную натяжку для уплотнения и прижимания склепываемых деталей друг к другу и к головке заклепки и стальную обжимку для окончательного формирования замыкающей головки.
Натяжки и обжимки изготовляются из инструментальной стали У8. Их рабочий конец на длине около 15 мм закаливается.
Клепка металла может производиться также и механизированным методом при помощи пневматических молотков и клепальных машин.
Пайкой называется процесс соединения металлов посредством введенного между ними расплавленного связующего материала - припоя. Последний заполняет зазор между соединяемыми деталями и, застывая, прочно соединяется с ними, образуя неразъемное соединение.
При пайке припой нагревают до температуры, превышающей температуру его плавления, но не достигающей точки плавления металла соединяемых деталей. Становясь жидким, припой смачивает поверхности и заполняет все зазоры за счет действия капиллярных сил. Происходит растворение основного материала в припое и их взаимная диффузия. Застывая, припой прочно сцепляется с паяемыми деталями.
При пайке должно выполняться следующее температурное условие: Т1<Т2<Т3<Т4, где:
- Т1 - температура, при которой паяное соединение работает;
- Т2 - температура плавления припоя;
- Т3 - температура нагрева при пайке;
- Т4 - температура плавления соединимых деталей.
Изм. |
Лист |
№ докум. |
Подпись |
Дата |
Лист |
13 |
УП 21.02.01 ЭС5-19 000000 УП 21.02.01 ЭСК-18 000 000 |
2.1 Техника безопасности при работе на токарных станках
Техника безопасности - это система организационных и технических мероприятий и средств, предотвращающих воздействие на работающих опасных и вредных производственных факторов. Основное содержание мероприятий по технике безопасности и производственной санитарии заключается в профилактике травматизма, т. е. предупреждении несчастных случаев на производстве, и в частности в период прохождения учебной практики.
Каждый студент должен получить инструктаж о технике безопасности, производственной санитарии и противопожарной охране.
Инструктаж на рабочем месте проводится перед допуском к работе всех вновь прибывших на практику учащихся, а также переведенных.
До начала работы
1) Надеть спецодежду; застегнуть рукава; спрятать волосы под головной убор.
2) Проверить наличие и надёжность крепление защитных ограждений и соединение защитного заземления с корпусом станка.
3) Расположить инструменты и заготовки в определённом порядке на приставной тумбе.
4) Прочно закрепить резец и обрабатываемую деталь. Вынуть ключ из патрона и установить на установленное место.
5) Проверить работу станка на холостом ходу и исправность пусковой коробки путём выключения кнопок и рычагов управления.
Во время работы
1) Строго выполнять технологию операций.
2) Во избежание травм запрещается:
· наклонять голову близко к патрону или режущему инструменту.
· предавать или принимать предметы через вращающие части станков.
Изм. |
Лист |
№ докум. |
Подпись |
Дата |
Лист |
14 |
УП 21.02.01 ЭС5-19 000000 |
· измерять обрабатываемую деталь, чистить и убирать стружку со станка до полной его остановки.
· охлаждать режущий инструмент или обрабатываемою деталь с помощью тряпки.
· останавливать станок путём торможения рукой патрона.
· отходить от станка не выключив его.
· поддерживать и ловить рукой отрезанною деталь.
3) Зачистку детали на станке производить напильником или шкуркой прикрепленной оправе. Рукоятка оправы должна быть с предохранительным кольцом. При работе держать левой рукой.
4) При выключение станка необходимо отвести резец от обрабатываемой детали.
5) При работе в центрах проверить надёжно ли закреплена задняя бабка и следить, чтобы засверловка была достаточна, и угол ее соответствовал углу центров.
6) Пользоваться ключами, соответствующими гайками и головками болтов.
7) Обрабатываемый пруток не должен выступать за пределы станка
8) При выключении тока в сети, во время работы, немедленно выключить машину.
По окончанию работы
1) Отключить суппорт, выключить электродвигатель.
2) Удалить стружку со станка при помощи щётки, из пазов станины крючками. Сдувать стружку ртом или сметать рукой запрещается.
3) Протереть станок, смазать, привести в порядок инструменты и индивидуальные средства защиты. Сдать станок преподавателю.
Режущий инструмент, применяемый на токарных станках
Главный вид режущего инструмента для обработки заготовок на токарных
Изм. |
Лист |
№ докум. |
Подпись |
Дата |
Лист |
15 |
УП 21.02.01 ЭС5-19 000000 УП 21.02.01 ЭСК-18 000 000 |
Токарные резцы: отрезной; проходной прямой; проходной отогнутый; чистовой широкий (лопаточный); чистовой радиусный; прорезной (канавочный); проходной упорный; подрезной; фасонный призматический; галтельный; резьбовой наружный; фасочный; расточный проходной
На токарных станках выполняются различные стадии обработки поверхности; используемые при этом резцы называются черновыми, чистовыми, получистовыми. Геометрия режущей части этих резцов приспособлена к работе с большой или с малой глубиной резания.
Резцы, предназначенные для обработки внутренних поверхностей называются расточными. По виду выполняемой работы различают резцы проходные - для обработки гладкой цилиндрической поверхности (внутренней или наружной) на «проход» и упорные проходные - для обработки одновременно цилиндрической поверхности и торцовой плоскости .
Торцовые поверхности цилиндрических .тел на токарных станках «подрезают» так называемыми подрезными резцами, которые работают с поперечной подачей к оси вращения или от оси вращения заготовки. Отрезку заготовки ведут отрезным резцом, а образование канавок - канавочным или прорезным резцом. Резьбовые поверхности образуют резьбовыми резцами, фасонные - фасонными, фаски - фасочными, галтели - галтельными и т. д.
Все резцы, работающие с продольной подачей, могут в рабочем движении перемещаться справа налево - это правые резцы, и слева направо - левые резцы.
У правых резцов главная режущая кромка находится со стороны большого пальца правой руки, положенной на резец сверху, у левых резцов главная режущая кромка при аналогичном положении левой руки находится также со стороны большого пальца.
Головка резца по отношению к его телу может быть отогнутой, изогнутой и оттянутой, а может совпадать по направлению с сечением тела. Тогда резцы называют прямыми, с отогнутой головкой, с оттянутой головкой и с изогнутой головкой.
Резцы одинакового назначения могут выполняться с державкой - телом разного сечения: квадратного, прямоугольного, круглого, специального.
Изм. |
Лист |
№ докум. |
Подпись |
Дата |
Лист |
16 |
УП 21.02.01 ЭС5-19 000000 |
Инструментальными являются материалы, основное назначение которых - оснащение рабочей части инструментов. К ним относятся инструментальные углеродистые, легированные и быстрорежущие стали, твердые сплавы, минералокерамика, сверхтвердые материалы.
По химическому составу, степени легированности инструментальные стали разделяются на инструментальные углеродистые, инструментальные легированные и быстрорежущие стали. Физико-механические свойства этих сталей при нормальной температуре достаточно близки, различаются они теплостойкостью и прокаливаемостью при закалке.
В инструментальных легированных сталях массовое содержание легирующих элементов недостаточно, чтобы связать весь углерод в карбиды, поэтому теплостойкость сталей этой группы лишь на 50-1000С превышает теплостойкость инструментальных углеродистых сталей. В быстрорежущих сталях стремятся связать весь углерод в карбиды легирующих элементов, исключив при этом возможность образования карбидов железа. За счет этого разупрочнение быстрорежущих сталей происходит при более высоких температурах.
Инструментальные углеродистые (ГОСТ 1435-74) и легированные (ГОСТ 5950-73) стали. Основные физико-механические свойства инструментальных углеродистых и легированных сталей приведены в таблицах. Инструментальные углеродистые стали обозначаются буквой У, за которой следует цифра, характеризующая массовое содержание углерода в стали в десятых долях процента. Так, в стали марки У10 массовое содержание углерода составляет один процент. Буква А в обозначении соответствует высококачественным сталям с пониженным массовым содержанием примесей.
В инструментальных легированных сталях первая цифра, характеризует массовое содержание углерода в десятых долях процента (если цифра отсутствует, то содержание углерода в ней до одного процента). Буквы в обозначении указывают на содержание соответствующих легирующих элементов: Г - марганец, Х - хром, С - кремний, В - вольфрам, Ф - ванадий, а цифры обозначают содержание элемента в процентах. Инструментальные легированные стали глубокой прокаливаемости марок 9ХС, ХВСГ, Х, 11Х, ХВГ отличаются малыми деформациями при термической обработке.
Эти материалы имеют ограниченные области применения: углеродистые идут, в основном, для изготовления слесарных инструментов, а легированные - для резьбообразующих, деревообрабатывающих и длинномерных инструментов (ХВГ)- протяжек, разверток и т.д.
Изм. |
Лист |
№ докум. |
Подпись |
Дата |
Лист |
17 |
УП 21.02.01 ЭС5-19 000000 |
2.4 Основные узлы токарных станков
Станина является опорой для передней и задней бабок, а также служит для перемещения по ней суппорта и задней бабки.
Передняя бабка служит для поддержания обрабатываемой детали и передачи ей вращения.
Задняя бабка служит для поддержания другого конца обрабатываемой детали; используется также для установки сверла, развертки, метчика и других инструментов.
Суппорт предназначен для перемещения резца, закрепленного в резцедержателе, в продольном, поперечном и наклонном к оси станка направлениях.
Коробка подач предназначена для передачи вращения ходовому винту или ходовому валу, а также для изменения числа их оборотов. Ходовой винт используется для передачи движения от коробки подач к каретке суппорта только при нарезании резьбы, а ходовой вал — при выполнении всех основных токарных работ.
Фартук служит для преобразования вращательного движения ходового вала в продольное или поперечное движение суппорта.
2.5 Измерительные инструменты
По способу применения измерительные средства делят на три группы: меры, измерительные приборы и инструменты, калибры. Мерами называют средства измерения, воспроизводящие физическую величину заданного размера. К ним относят масштабные стальные линейки, рулетки, транспортиры, плоскопараллельные концевые меры длины, угломеры, угломеры-угольники, угольники простые и тавровые.
Измерительными приборами и инструментами называют устройства, с помощью которых измеряют фактические размеры детали. Штангенциркуль предназначен для измерения диаметров и длины деталей с точностью 0,1 мм. Он состоит из штанги, измерительных губок, рамки, зажима рамки, нониуса 5 и глубиномера 6. Штангенциркули выпускают с пределами измерения 0—200 мм, 0—320 мм и 0—500 мм, 240—700 мм, 320—1000 мм, 500—1400 мм и 800— 2000 мм.
К микрометрическому инструменту относят гладкие микрометры, предназначенные для измерения диаметра детали. Микрометр состоит из скобы, пятки, винта, стопора, стебля, барабана, на конической части которого
Изм. |
Лист |
№ докум. |
Подпись |
Дата |
Лист |
18 |
УП 21.02.01 ЭС5-19 000000 |
Микрометрический глубиномер применяют для измерения глубины отверстий, высоты уступов и др. Он состоит из основания, микрометрической головки, стопорного устройства, цилиндрического гнезда и сменных измерительных стержней.
Индикатор часового типа применяют для измерения толщины и отклонения детали от симметричности. Он состоит из корпуса, стопорного винта, циферблата, обода, стрелки, малой стрелки нониуса, гильзы, стержня, шейки, шарика и головки. Точность измерения 0,01 и 0,001 мм.
Калибры — это бесшкальные контрольные инструменты. К ним относят предельные калибры-пробки, состоящие из корпуса 2 и двух пробок: проходной и непроходной. С помощью этих пробок измеряют внутренний диаметр отверстия. Предел измерения от 1 до 50 мм. Для проверки отверстий больших размеров применяют пробки односторонние, насадные и неполные . Калибры-скобы служат для измерения диаметра валов. Жесткими скобами измеряют диаметры. Предел измерений от 1 до 200 мм. Для контроля валов диаметром до 300 мм применяют регулируемые скобы. К корпусу привернута неподвижная губка. Вставки регулируют на величину от 3 до 8 мм как по проходному, так и непроходному размеру винтами. После установки необходимого размера вставки стопорят втулками с лыской и винтами. Вал обточен правильно, так как непроходная часть скобы через него не проходит. . Меньший проходной конец двусторонней предельной пробки входит в отверстие, а больший непроходной не входит в это отверстие. Следовательно, отверстие расточено правильно. Контроль длины обработанной части поверхности производят односторонними и двусторонними шаблонами.
2.6 Обрабатываемые материалы
Уникальные характеристики, которые зависят от состава легирующих элементов, термообработки, твёрдости и пр. Все обрабатываемые материалы группируются определенным образом, и в соответствии с принадлежностью к той или иной группе осуществляется выбор геометрии режущего инструмента, марки сплава и режимов резания.
Изм. |
Лист |
№ докум. |
Подпись |
Дата |
Лист |
19 |
УП 21.02.01 ЭС5-19 000000 УП 21.02.01 ЭСК-18 000 000 |
ISO P – Сталь. Самая большая по составу группа материалов, включающая различные сорта стали - от нелегированных до высоколегированных, включая стальные отливки, ферритную и мартенситную нержавеющую сталь. Как правило, материалы данной группы имеют хорошую обрабатываемость, но это зависит от твёрдости стали и процентного содержания в ней углерода.
ISO M – Нержавеющая сталь. Сплавы с содержанием хрома не менее 12%; некоторые сплавы могут содержать никель и молибден. Различают различные виды нержавеющей стали. Например, ферритная, мартенситная, аустенитная и аустенитно-ферритная (дуплексная) сталь. Характерной особенностью для обработки всех этих сталей является интенсивный термический износ режущих кромок, износ в виде образования проточин и наростообразования.
ISO K – Чугун. В отличие от стали, дает короткую, сыпучую стружку. Серые чугуны (GCI) и ковкие чугуны (MCI) обрабатываются довольно легко, а чугун с шаровидным (NCI) и вермикулярным (CGI) графитом и отпущенный ковкий чугун (ADI) поддаются обработке сложнее. В состав любого чугуна входит карбид кремния (SiC), что определяет абразивный характер износа режущей кромки.
ISO N – Цветные металлы. Алюминий, медь, латунь и другие цветные металлы гораздо мягче черных. Алюминий с 13% содержанием кремния является очень абразивным материалом. В общем цветные металлы обрабатывают инструментом с острыми режущими кромками с высокой скоростью резания и продолжительным периодом стойкости.
ISO S – Жаропрочные сплавы. К данной группе относится большое число высоколегированных материалов на основе железа, никеля, кобальта и титана. Все они достаточно вязкие, поэтому их обработка сопровождается наростообразованием на инструменте и выделением большого количества тепла, к тому же для них характерно упрочнение в процессе резания. По свойствам данные сплавы схожи со сталями группы ISO M, но они гораздо труднее поддаются резанию, что объясняет небольшой срок службы режущих пластин.
ISO H – Материалы высокой твердости. В эту группу входят стали твёрдостью 45-65 HRС, а также отбелённый чугун твёрдостью 400-600 HB. Высокое значение твёрдости делает их трудно поддающимися обработке.
Изм. |
Лист |
№ докум. |
Подпись |
Дата |
Лист |
20 |
УП 21.02.01 ЭС5-19 000000 УП 21.02.01 ЭСК-18 000 000 |
2.7 Обработка наружных цилиндрических поверхностей на токарных станках
Если вращать прямоугольник АБСД вокруг оси АД, получим цилиндрическую поверхность. Любая точка на поверхности цилиндра одинаково удалена от оси АД, которую называют осью цилиндра. В зависимости от требований, предъявляемых к точности обработки и параметрам шероховатости обработанной поверхности, различают черновое» получистовое, чистовое и тонкое (алмазное) обтачивание.
В зависимости от длины заготовки обтачивание производят в патроне без поджатия центром, если 1,5, в патроне с поджатием задним центром, если L/d 1,5, в патроне с неподвижным люнетом, если L/d> >12. Если L/d< 12, обтачивание в центрах производят без люнета.
Частоту вращения заготовки и подачу инструмента назначают в зависимости от глубины резания, материала заготовки и инструмента. Частоту вращения и подачу устанавливают посредством рукояток, расположенных на передней стороне коробки скоростей и подач. При продольном точении в патроне соблюдают следующую последовательность. Устанавливают трехкулачко-вый самоцентрирующий патрон на шпиндель. Закрепляют резцы для черновой и чистовой обработки в резцедержателе так, чтобы их вершины совпадали с линией центра станка. Зажимают заготовку в патроне. Устанавливают на станке 1К62 требуемую частоту вращения и подаче рукоятками. Закрепляют в патроне заготовку и проверяют ее биение. Включают станок и подводят резец к заготовке до соприкосновения с ее поверхностью для определения толщины срезаемой стружки. Отводят резец вправо от торца заготовки и по лимбу устанавливают глубину резания. Включают продольную подачу, протачивают заготовку на длине 5—10 мм и отводят резец. Выключают станок и измеряют штангенциркулем обточенный диаметр. Если диаметр обработанной части заготовки не соответствует заданному, то корректируют глубину резания по лимбу. Включив станок и установив рукоятку продольной подачи, обтачивают заготовку на требуемую длину I. Выключают подачу, отводят резец и выключают станок. Проверяют полученный диаметр заготовки. Если он соответствует заданному, то разжимают кулачки и вынимают деталь из патрона.
При обтачивании заготовки в центрах необходимо проделать следующее:
1. Установить центры в шпинделе передней и задней бабки.
2. Совместить центры и в зависимости от условий обработки установить
Изм. |
Лист |
№ докум. |
Подпись |
Дата |
Лист |
21 |
УП 21.02.01 ЭС5-19 000000 |
3. Исходя из припуска на обработку, глубины резания, параметров заготовки, материала резца и заготовки, установить на станке 16К20 требуемую частоту вращения и подачу. На станке 16К20 расположены рукоятки частоты вращения шпинделя, шага и направления резьбы, 5 включения и выключения станка, 6—8 подачи.
4. Закрепить резец в резцедержателе по линии центров.
5. Установить заготовку с хомутиком в центрах и резец под углом 90° к оси центров станка.
6. Для определения правильности установки заготовки и резца обработать поверхность на длине 3—5 мм и отвести резец. Затем установить требуемый размер заготовки. Включить станок, проточить заготовку на длине 10—15 мм. Выключить рукоятку подачи и отвести резец за торец заготовки.
Измерить штангенциркулем диаметр обточенной части заготовки и при необходимости внести коррекцию. Включить станок и рукоятку подачи, обточить заготовку на заданную длину. Выключить рукоятку подачи, отвести резец и выключить станок. Измерить обработанный диаметр заготовки микрометром и при необходимости обточить снова.
Взять левой рукой заготовку, правой рукой отвести задний центр и снять заготовку со станка. Открепить хомутики и закрепить его на обработанной поверхности заготовки через разрезную втулку. Установить заготовку в центрах станка. Подвести резец на заданный размер по лимбу, включив подачу, проточить необработанную поверхность заготовки. Выключить станок и измерить диаметр обработанной поверхности. Снять деталь со станка, затем с детали хомутик и разрезную втулку.
Для установки резца на требуемую глубину на винте поперечной и продольной подачи установлены лимбы, на которых нанесены деления. При касании резца поверхности заготовки лимб устанавливают на нулевую отметку. На большинстве станков лимб имеет 100 делений. При шаге Р — 5 мм винта поперечной подачи и полном обороте лимба резец перемещается на длину 5 мм. Следовательно, при перемещении лимба на одно деление резец переместится на 5/100 = 0,05 мм, а диаметр обработанной поверхности уменьшится на 0,1 мм. Необходимо помнить, что при установке резца на требуемую глубину резания рукоятку лимба следует повернуть назад на один оборот для устранения зазора.
Продольный и поперечный зазор в суппорте устраняют, перемещая подвижные гайки 2 в осевом направлении гайкой и винтами.
Изм. |
Лист |
№ докум. |
Подпись |
Дата |
Лист |
22 |
УП 21.02.01 ЭС5-19 000000 |
Для безопасной работы на токарном станке необходимо учесть следующее:
1. Нельзя обрабатывать заготовку, если кулачки выступают из корпуса патрона более чем на 1/4 своей длины.
2. Часть резца, выступающая из резцедержателя, -должна быть как можно короче.
3. Нельзя обрабатывать заготовки, ось которых не совпадает с осью станка (отклонение Я), в том числе изогнутые заготовки.
4. Нельзя работать с большими значениями подачи и глубины резания, так как резец «затягивается» под заготовку, что приводит к его поломке и вылету заготовки из патрона.
5. При большом продольном и поперечном зазоре между заготовкой и центрами заготовка может выскочить из центров.
6. Искривленные заготовки перед установкой на станке необходимо выправить с помощью винтового пресса.
При наружном обтачивании выполняют отрезку заготовок и протачивание наружных канавок. Большое влияние на отрезку заготовок оказывает правильность заточки и установки отрезного резца. На рис. 186 показаны примеры неправильной заточки и установки резцов относительно линии центров: у резца отсутствуют вспомогательный угол и задние вспомогательные углы ой и а2, что приводит к поломке резца; большие задние и передние углы , что тоже приводит к поломке резца; затачивание резца с завалом боковых поверхностей относительно оси резца приводит к затуплению резца; установка резца ниже или выше центра приводит к поломке резца; установка резцов под углом к оси центров приводит к выпуклости или вогнутости торцов детали.
Широкие канавки обрабатывают за несколько рабочих ходов, если ширина с резца меньше ширины h канавки. Сначала прорезают правую часть канавки с припуском Д на глубину канавки. Затем прорезают левую часть канавки на втором рабочем ходе. За третий рабочий ход канавку проходят за всю глубину. Затем резцом снимают припуск Л на всей шарине h канавки.
2.8 Обработка конических поверхностей на токарных станках
Обточку конических поверхностей можно осуществлять различными способами в зависимости от величины конусности, от конфигурации и размеров обрабатываемой детали:
Поворотом верхних салазок суппорта . Салазки / верхнего суппорта поворачивают вокруг вертикальной оси суппорта на угол конусности а.
Изм. |
Лист |
№ докум. |
Подпись |
Дата |
Лист |
23 |
УП 21.02.01 ЭС5-19 000000 |
Смещение корпуса задней бабки . Корпус задней бабки смещают в поперечном направлении относительно салазок на величину ft, в результате чего ось заготовки, установленной в центрах, образует с линией центров, а следовательно, с направлением продольной подачи суппорта угол конусности обрабатываемой поверхности а. Образующая конической поверхности при такой установке располагается параллельно продольной подаче резца.
При длине конической поверхности / и длине заготовки L величину необходимого смещения корпуса задней бабки определяют по формуле
h = L sin a.
При малых значениях a: sina≈tga, следовательно,
h = L tga = L ( D — d ) /2l
При l=L
Этот способ применяют для обточки пологих конических поверхностей (угол а не более 8°).
Недостаток этого способа состоит в том, что вследствие неправильного положения центровых отверстий обрабатываемой детали на центрах станка центровые отверстия детали и сами центра быстро изнашиваются.
Для изготовления точных конических поверхностей этот способ непригоден.
Изм. |
Лист |
№ докум. |
Подпись |
Дата |
Лист |
24 |
УП 21.02.01 ЭС5-19 000000 |
При продольном перемещении суппорта резец получает результирующее движение: наряду с продольным поперечное перемещение, обусловленное движением ползушки 3 по линейке /. Результирующее движение направлено вдоль образующей конической поверхности.
Этот метод применяют для обточки конических поверхностей под углом до 12°.
С помощью широких фасонных резцов. Режущие лезвия резца устанавливают под углом конусности а обрабатываемой поверхности к линии центров станка параллельно образующей конической поверхности.
Обточку можно осуществлять как продольной, так и поперечной подачей.
Этот способ пригоден для обработки коротких наружных и внутренних конических поверхностей с длиной образующей не более 25 мм, так как при больших длинах образующей возникают вибрации, приводящие к получению обработанной поверхности низкого качества.
Дата добавления: 2020-12-22; просмотров: 56; Мы поможем в написании вашей работы! |
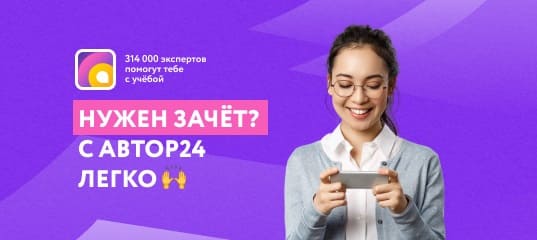
Мы поможем в написании ваших работ!