Технологии изготовления литых отливок
Машиностроительный комплекс составляют машиностроение и металлообработка. Предназначение отрасли машиностроения заключается в создании машин и оборудования, аппаратов и приборов, различного рода механизмов для различных отраслей экономики.
Металлообработка занимается производством металлических изделий, ремонтом машин и оборудования.
Выбор оборудования производится при разработке маршрута обработки детали, при этом исходными данными для выбора служат: чертеж и технические требования к детали, тип производства и годовая программа выпуска, принятые способы обработки поверхностей, желаемая степень механизации и автоматизации и пр.
При составлении маршрута изготовления детали производят сокращенное описание всех технологических операций в маршрутной карте в последовательности их выполнения без указания переходов и технологических режимов, но с указанием типа оборудования (станка). Исходные данные для разработки маршрутной технологии˸ рабочий чертеж детали с техническими требованиями, чертеж заготовки с техническими условиями, ранее установленный тип производства, ранее проведенная отработка технологичности конструкции детали, предварительно определенные маршруты обработки отдельных поверхностей, ранее выбранные технологические базы с предварительно намеченным планом обработки заготовки.
Поскольку машиностроительный комплекс очень ёмкий и сложный, остановимся на технологии изготовления литых отливок, которые могут применяться, например, в качестве запасных деталей в экскаваторах, грунтовых и песковых насосах, конусных дробилках и других видах машин и оборудования при добыче и переработке полезных ископаемых.
|
|
Для изготовления отливок применяют литейную оснастку. Литейная оснастка – это комплект приспособлений для изготовления отливок, в который входят модель отливки, модели элементов литниковой системы, модельные плиты, стержневые ящики, опоки, трамбовки ручные, встряхивающая машина, пескометная и прессовая машины и др.
Основными этапами технологического процесса изготовления литых отливок являются подготовка производства, основное производство и заключительный этап обработки. Подробная схема производства отливок дана на рис. 3.5.
Рис.3.5. Технологическая схема производства отливок
Для изготовления формы применяют песочно-глинистую смесь. Песок кварцевый может характеризоваться следующими свойствами:
- содержанием кремнезёма (SiO2) – 98,0%;
- массовой долей влаги не более 4%;
- рН от 6,2 до 7,0;
- массовая доля примесей (оксидов щелочных и щелочноземельных металлов) не более 0,4%;
|
|
- содержание оксидов Fe2O3 не более 0,2%;
- коэффициент угловатости не более 1,4;
- массовая доля потерь при прокаливании не более 0,2%.
Глина огнеупорная молотая должна иметь такие физико-химические свойства, как:
- огнеупорность – 1670-1720ºС;
- влажность – 6-10%;
- содержание Al2O3 – 31-34%.
В смесь дополнительно могут входить опилки древесные и технический лигносульфонат с улучшенными связующими свойствами.
Фактический развес отливок от 2 до 2000 кг. Производства фасонного литья может быть единичным и мелкосерийным. Изготавливаются отливки из легированных и углеродистых марок сталей и серых чугунов различного назначения, получаемых литьем в песочно-глинистые формы, массой до 1500 кг, бронзовые (О5Ц5С5, А9ЖЗЛ и др.) и алюминиевые сплавы (АК9М2, АК5М7 и др.) – в виде фасонного литья, литья под давлением и методом центробежного литья заготовок и др.
Рассмотрим основные этапы изготовления отливок.
Приготовление смеси. Для приготовления наполнительных, облицовочных и стержневых смесей могут использоваться одни бегуны модели 3М3, 2 бегунов модели 114. Смесь проходит предварительно очистку от крупных включений скрапа, проходя через полигональное сито.
Порядок засыпки исходных материалов в бегуны.
|
|
В первую очередь засыпаются сухие материалы. Затем, после перемешивания в течение 5 минут, в бегуны вводят жидкие материалы, глину и воду (при необходимости, после получения анализа на влажность).Общее время перемешивания смеси в бегунах не превышает 10-15 мин.
Загрузка в бегуны связующего производится после полного перемешивания сухих составляющих смеси. Температура связующего при загрузке в бегуны не должна превышать 50°С, во избежание повышенной прилипаемости смеси и осыпаемости стержней и форм после сушки.
Для улучшения физико-механических свойств смесей рекомендуется их приготовление за 1,5-2 часа до начала формовки.
Формовочный песок сушится в проходном барабанном сушиле и конвейером доставляется в бункер – накопитель песка. Затем все компоненты формовочной смеси дозируются строго в объемных частях. Смесь после загрузки сухих и жидких компонентов подвергается перемешиванию.
Формовка — наиболее сложная и трудоемкая операция производства отливок в разовых песчано-глинистых формах. Трудоемкость изготовления литейных форм составляет 40-60 % от общей трудоемкости получения отливок.
Формование осуществляют на формовочных машинах (например, модели 22111М) или формовочной стационарной встряхивающей машине модели 703М.
|
|
Уплотнение формовочной смеси в опоке происходит в режиме встряхивания соударением встряхивающего стола с ударником. В режиме встряхивания с одновременным прессованием вместе со встряхиванием происходит движение вверх прессового поршня. После прижатия опоки к прессовой плите траверсы уплотнение происходит также за счет ударов, наносимых ударником по встряхивающему столу. Этот режим уплотнения является наиболее эффективным.
После окончания процесса встряхивания с одновременным прессованием происходит опускание прессового поршня. В нижнем положении прессового поршня поступает команда на отвод в исходное положение прессовой траверсы и подъема вытяжного механизма. Вытяжной механизм отделяет уплотненную полуформу от модели посредством подъема вытяжных штырей.
Максимальный размер опок в свету на машине 22111М-500х400х200. Грузоподъемность 200 кг. Сборка форм производится вручную.
Максимальный размер опок в свету на формовочной машине 703М - 900х600х250, грузоподъемность 700 кг. Сборка форм производится с помощью кран – балки. Максимальная металлоемкость формы с машинной формовки 50 кг.
Изготовление остальных отливок производится в металлические формы – кокили, в песчано-глинистые разовые формы (Рис. 3.6) и в холоднотвердеющие смеси (ХТС).
Рассмотрим последовательность ручной формовки для отливок детали типа втулки.
На подмодельный щит 3 (рис. 3.6, а) укладывается половина модели 2 и устанавливается нижняя опока 1, затем сквозь сито 4 на поверхность модели наносится противопригарный припыл - древесно-угольная пыль, графитовый порошок (рис. 3.6, б). Лопатой 5 наносят на модель облицовочную формовочную смесь, а затем засыпают всю опоку наполнительной формовочной смесью (рис. 3.6, в). Ручной или
Рис.3.6. Технологический процесс формовки втулки
пневматической трамбовкой 6 уплотняют смесь (рис. 3.6, г), сгребают ее остатки и накалывают душником (шилом) 7 отверстия для лучшего выхода газов (рис. 3.6, д). Затем нижнюю опоку с заформованной моделью переворачивают на 180° устанавливают вторую половину модели 8 и верхнюю опоку 9 (рис. 3.6, е). После установки моделей литниковой системы 10 в той же последовательности заформовывают верхнюю опоку (рис. 3.6, ж). По окончании формовки опоки разнимают, осторожно удаляют модели, поправляют обрушившиеся места формы припыливают ее изнутри и, уложив в нижнюю полуформу на место знаков 11 стержень 12 (рис. 3.6, з), вновь устанавливают верхнюю полуформу на нижнюю и скрепляют их при помощи болтов, струбцин или просто придавливают грузом, чтобы предотвратить прорыв металла по плоскости разъема формы. В таком виде литейная форма готова для заливки металла.
Плавка. Выплавка стали, производится в дуговой сталеплавильной печи емкостью 0,5т. (Рис. 3.7).
Рис.3.7. Схема дуговой плавильной печи
Дуговая печь питается трёхфазным переменным током. Имеет три цилиндрических электрода 9 из графитизированной массы, закреплённых в электрододержателях 8, к которым подводится электрический ток по кабелям 7. Между электродом и металлической шихтой 3 возникает электрическая дуга. Корпус печи имеет форму цилиндра. Снаружи он заключён в прочный стальной кожух 4, внутри футерован основным или кислым кирпичом 1. Плавильное пространство ограничено стенками 5, подиной 12 и сводом 6. Съёмный свод 6 имеет отверстия для электродов. В стенке корпуса рабочее окно 10 (для слива шлака, загрузки ферросплавов, взятия проб), закрытое при плавке заслонкой. Готовую сталь выпускают через сливное отверстие со сливным желобом 2. Печь опирается на секторы и имеет привод 11 для наклона в сторону рабочего окна или желоба. Печь загружают при снятом своде. Вместимость печей составляет 0,5 тонн. В литейных цехах используют электропечи с кислой футеровкой.
Выплавка износостойких, серых чугунов и медных сплавов в двух индукционных печах ИЧТ-2,5. Электропечь индукционная тигельная ИЧТ-2,5 состоит из собственно электропечи и комплекта оборудования, необходимого для ее работы. Электропечь конструктивно выполнена в виде рамы, внутри которой размещается быстросъемный плавильный узел, состоящий из индуктора, магнитопроводов, сварного корпуса, футеровки, подины, набивного тигля и верхнего футерованного пояса - воротника.
Чугун ИЧ300Х18Г3 выплавляется в индукционных электропечах с кислой футеровкой. Шихта состоит из стального лома, феррохрома, ферромарганца, чушкового чугуна с низким содержанием кремния. При выплавке чугуна в основной электропечи ферромарганец вводится в печь за 20-25 мин. до выпуска. Угар марганца составляет около 5%. Температура жидкого металла при выпуске из электропечи 1460-15000С. При выплавке чугуна в печи с кислой футеровкой весь ФМn вносится (в ковш) предварительно нагретым до температуры 8000С.
Заливка в формы. Заливка сплава производится вначале в ковш, который цепляется с помощью крана. Затем заливщик разливает сплав по формам, они стоят до полного остывания. Затем формы разбираются и выбиваются отливки.
Очистка и обрубка отливок происходит ручным пневмоинструментом и на обдирочно-шлифовальных станках с кругами Æ600. Мелкие отливки весом до 15 кг окончательно обрабатываются в галтовочном барабане. В термообрубных отделениях производят очистку, обрубку, зачистку, грунтовку, исправление дефектов и термическую обработку отливок. Термическая обработка (отжиг и закалка) стального и износостойкого литья производится в шахтных печах Æ2000 мм.
Заключительным этапом изготовления литых отливок является грунтовка и маркировка готового изделия. После этого изделие поступает к заказчику. Перед отправкой потребителю отливки грунтуют с целью защитить их поверхности от коррозии. Продолжительность защитного действия грунтовки зависит от условий хранения отливок: при хранении отливок в помещениях склада срок действия грунтовки - 25-30 дней, при хранении отливок на открытых площадках склада точечная коррозия появляется уже на 5-15-й день в зависимости от влажности атмосферы. Если срок защитного действия грунтовки истек, то перед окончательным нанесением лакокрасочных покрытий отливку вновь очищают и грунтуют.
Таким образом, производство литых отливок состоит из следующих основных этапов:
- Формовка, сборка формы.
- Плавка металла (выполняется одновременно с формовкой).
- Заливка.
- Выдержка.
- Выбивка.
- Обрубка.
- Очистка (от окислов, пригаров и т.д.).
- Грунтовка и маркировка.
Дата добавления: 2020-12-22; просмотров: 103; Мы поможем в написании вашей работы! |
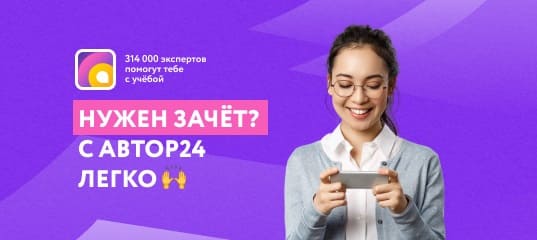
Мы поможем в написании ваших работ!