Производство горячебрикетированного железа
Производство железорудных брикетов
Производство окатышей
Производство окатышей осуществляется на фабриках окомкования, сырьём для изготовления которых служит железистый концентрат.. Фабрика окомкования состоит из цеха шихтоподготовки, участков окомкования, обжиговых машин конвейерного типа, например, ОК-306, участка грохочения (сортировки), системы складирования и транспортировки готовой продукции, вспомогательных систем и систем газоочистки.
Фабрика окомкования производит два вида окатышей: окисленные из рядового концентрата для доменной плавки и не окисленные, из дообогащенного концентрата для завода горячебрикетированного железа.
Технология производства окатышей включает в себя такие процессы (рис. 3.3.1):
- шихтоподготовка;
- окомкование;
- контрольное грохочение сырых окатышей;
- обжиг в обжиговых машинах ОК – 306;
- сортировка обожженных окатышей.
Исходным сырьем для получения железорудных неофлюсованных окатышей является концентрат железорудный обогатительной фабрики с массовой долей железа менее 69,5 % для окомкования и связующая добавка.
Концентрат по среднесменным качественным характеристикам должен соответствовать требованиям:
- массовая доля железа общего 68,37–0,15 %;
- массовая доля влаги 9,8+0,2 %;
- массовая доля контрольного класса крупности – 0,045 мм 91,0-2,0 %.
Рис. 3.3. Технологическая схема производства окатышей
|
|
В качестве связующей добавки применяется двухкомпонентная смесь, состоящая из бентонитового порошка, полученного из комового бентонита» и полимерного связующего «Floform».
По среднесменным качественным характеристикам бентонитовый порошок должен соответствовать требованиям:
- массовая доля влаги 7,5±1,5 %;
- доля контрольного класса крупности -0,071 мм 96,0–2,5 %.
В качестве связующей добавки могут применяться и другие материалы.
Исходным сырьем для получения железорудных офлюсованных окатышей является концентрат железорудный с массовой долей железа более 69,5 % , связующей добавки и флюсоупрочняющей смеси.
Концентрат по среднесменным качественным характеристикам должен соответствовать требованиям:
- массовая доля железа общего 70,0–0,5 %;
- массовая доля влаги 9,8±0,15 %;
- массовая доля диоксида кремния не более 3,0 %;
- массовая доля контрольного класса крупности –0,045 мм не более 97,0 %;
- удельная поверхность не более 2100 см2/г.
Флюсоупрочняющая смесь готовится, как правило, на фабрике и состоит из боксита и мела. По среднесменным качественным характеристикам флюсоупрочняющая смесь должна отвечать требованиям:
- массовая доля влаги 3,0±1,5 %;
- массовая доля контрольного класса крупности 0,071 мм должна составлять 96,0±2,5 %;
|
|
- массовая доля СаО 25,5±1,5 %;
- массовая доля Al2O3 21,0±1,5 %
- массовая доля SiO2 не более 14,0 %.
В качестве флюсоупрочняющей смеси могут применяться и другие композиции.
Предварительно усредненный концентрат железорудный с массовой долей железа менее 69,5%, системой конвейеров подается в корпус приготовления бентопорошка и загружается в расходные бункера концентрата обжиговых машин, что позволяет иметь запас концентрата в бункерах до 500 тонн. Бункера, с целью предотвращения зависания и налипания концентрата на стенки покрываются гидрофобным материалом - эпоксидной смолой в 5 слоев. Поступающий на фабрику концентрат подвергается взвешиванию на автоматических тензовесах, установленных на конвейерах.
В качестве связующей добавки в шихту вводится бентопорошок, который готовится из комовых привозных щелочно-земельных активированных бентонитов (болгарский, хакасский, индийский и др.). Возможно применение принципиально других материалов, поиски и изучение которых продолжаются.
Комовой бентонит или комовые флюсоупрочняющие компоненты (бокситы, известняк, доломит) могут поступать на фабрику в железнодорожных вагонах, а мел - в думпкарах из рудоуправления. Разгрузка комовых материалов производится грейферным краном грузоподъемностью 20 т (высота подъема - 23 м, длина пролета - 34 м) с последующей их ручной доочисткой через открытые люки. Общая емкость склада корпуса приема бентонита 7400 т, разгрузочная емкость 2500-3000 т.
|
|
Со склада комовые материалы тем же грейферным краном загружаются в бункер конвейера - питателя КП-1, подающий их на дробление в молотковую дробилку типа ДМ-1.7 х 1,45.
После дробления в молотковой дробилке дробленые материалы системой конвейеров транспортируется в корпус приготовления бентопорошка и реверсивным передвижным конвейером разгружаются в два силоса общей емкостью 11000 т. Для учета подробленного материала на конвейере КБ-13 установливаются автоматические тензовесы. Для усреднения и последующей отгрузки дробленого сырья над силосами установлен грейферный кран. Этим краном дробленый материал загружается в приемный бункер конвейера КБ-14 и через конвейер КБ-9 попадает в сушильную установку.
Сушильная установка служит для сушки дробленого материала до влажности 8-10% и состоит из топочного агрегата, сушильного барабана СБ -3,5 х 18, вентиляторов ВД-12 и ВМ-100/1200 . Топочный агрегат служит для приготовления сушильного агента, вентилятор ВД-12 - для подачи воздуха в топку, ВМ - 100/1200 -для забора использованного теплоносителя из сушильного барабана. Сушка сырья происходит непосредственно в сушильном барабане. При неисправности любого из механизмов, участвующих в сушке материалов, последние могут подаваться на измельчение, минуя сушку через конвейер - питатель КБ-15 и конвейер КБ-10 непосредственно на конвейер КБ-8 и на измельчение.
|
|
Шаровая мельница служит одновременно для измельчения и сушки материалов. Горячие газы, подаваемые в мельницу, служат не только сушильным, но и транспортирующим агентом.
Измельченный в мельнице порошок транспортируется газовым потоком, создаваемым вентиляторами ВМ - 17 и ВМ - 180/1100 в пылевой сепаратор СПЦ-5500/2000. В пылевом сепараторе происходит разделение порошка на крупную (более 0.071 мм) и мелкую (менее 0.071 мм) фракции. Разделение на фракции достигается за счет сил гравитационных и инерционных при изменении газового потока.
Выделенная в сепараторе крупная фракция поступает через клапан-мигалку Ду-600 по аэротрубе в загрузочный патрубок мельницы на доизмельчение, кондиционная же по крупности фракция порошка из сепаратора направляется на газоочистку, которая осуществляется в три ступени.
1-я ступень газоочистки происходит в двух циклонах типа НИИОГаз диаметром 3250 мм (правый и левый).
2-я ступень газоочистки происходит в 4-х циклонах ЦН-11 диаметром 2000 мм.
3-я ступень газоочистки - очистка воздуха перед выбросом в атмосферу - мокрая газоочистка в трубах «Вентури».
Для поддержания в расходных бункерах разряжения во время закачки порошков и выброса очищенного воздуха в атмосферу применяются рукавные фильтры ФВК-60 и вентиляторы ВВД-8.
Шихта для производства железорудных неофлюсованных окатышей с массовой долей железа менее 66,5% и железорудных офлюсованных окатышей с массовой долей железа более 66,5% состоит из железорудной составляющей - концентрата и связующей добавки - бентопорошка. Основная задача технологической операции приготовления шихты состоит в правильном и точном дозировании ее компонентов.
Производительность технологической линии по концентрату регулируется количеством работающих питателей и их производительностью, которая зависит от скорости вращения диска.
Смешивание компонентов шихты осуществляется в две стадии. Для участка окомкования и обжига при приготовлении шихты могут использоваться роторные смесители СР-400/1200 (1-я стадия смешивания) и барабанные смесители СБ-3.2 х 8 (2-я стадия смешивания). Для приготовлении шихты могут используются только роторные смесители установленные на конвейерах.
Окомкование шихты происходит в чашевых окомкователях диаметром 7,0 и 7,5 м. Процесс получения окатышей из шихты протекает по двум путям: образование зародышей и рост комков. Первичный зародыш образуется при попадании капли воды в объем сухого материала. Переувлажненные первичные комки обладают высокой пластичностью, что играет важную роль для успешного протекания окомкования. Увеличение размера окатыша происходит в результате многократных ударов зародыша о слой материала и борт чашевого окомкователя во время движения в окомкователе. Под действием динамических нагрузок комок уплотняется. При этом избыточная влага выдавливается на поверхность, что обеспечивает присоединение к комку дополнительных частиц материала.
Прочность сырых окатышей повышается с увеличением диаметра окатышей и скорости вращения чашевого окомкователя. Влияние влажности шихты, количества и типа связующего материала не является однозначным. При увеличении влажности до определенного значения наблюдается упрочнение сырых окатышей, после превышения этого значения прочность снижается.
Диаметр сырых окатышей уменьшается с уменьшением скорости вращения чашевого окомкователя (менее 5,5 об/мин снижать скорость чашевого окомкователя не рекомендуется), увеличением угла наклона чашевого окомкователя, увеличиваем количества бентонита в шихте, увеличением количества шихты в чашевый окомкователь, уменьшением количества воды, добавляемой в чашевый окомкователь.
Одним из наиболее сложных технологических моментов производства окатышей является их обжиг. Основной целью его является получение обожженных железорудных окатышей, максимально отвечающих требованиям металлургического передела, сохраняющими свои свойства при транспортировках, перегрузках и хранении их на открытых складах. Обжиг окатышей осуществляется на обжиговой машине конвейерного типа. Высокотемпературный теплоноситель, используемый в процессе термообработки, получают при сжигании природного газа, поступающего по газопроводу из Острогожска.
Технологическая схема обжига включает следующие операции:
- загрузка постели и укладка сырых окатышей на обжиговые тележки;
- термообработка сырых окатышей на обжиговой машине;
- разгрузка обожженного продукта в бункер-выравниватель температуры;
- уборка просыпи окатышей;
- очистка технологических газов от пыли.
Сортировка обожженного продукта участков обжига осуществляется в отдельных корпусах на самобалансных грохотах ГСО-3600х6400. Обожженные окатыши из бункеров - выравнивателей температуры системой конвейеров подаются в корпуса сортировки на грохоты, где происходит распределение окатышей на три продукта: отсев, «постель» и готовые товарные окатыши. Грохота имеют сита с размерами ячеек 5 и 20 мм, 10 и 16 мм.
На грохотах происходит сортировка офлюсованных окатышей. Готовые офлюсованные окатыши класса крупностью +5÷16 мм подаются на конвейер, над крытой галереей которого располагается установка по "приготовлению цементной суспензии, предназначенная" для покрытия окатышей перед подачей на ГБЖ.
Офлюсованные окатыши, покрытые цементной суспензией, конвейерами подаются на трубчатый конвейер цеха ГБЖ. При сбоях в работе установки по покрытию окатышей цементной суспензией, по согласованию с ГБЖ возможна подача непокрытых суспензией офлюсованных окатышей напрямую на ГБЖ с увеличением расхода цемента непосредственно при покрытии в цехе ГБЖ.
Отсев - это продукт крупностью менее 5мм. Он системой конвейеров транспортируется в погрузбункер отсева емкостью 1220,4 м3 для отгрузки в железнодорожные вагоны или в думпкары.
Готовые товарные окатыши отгружаются в железнодорожный транспорт двумя погрузочными бункерами. Окатышевозы или полувагоны подаются по железнодорожные пути в тоннель погрузбункера.
Погрузка окатышей в полувагоны ведется тремя течками в три конуса. Дозирование окатышей - объемное с помощью радиоактивного контроля (высота конуса) через секторные затворы. Для предотвращения просыпи окатышей на железнодорожный путь, на каждой течке кроме рабочих секторных затворов дополнительно установлены аварийные секторные затворы.
Фабрика окомкования относится к горячим цехам.
Основными источникам опасных и вредных производственных факторов на фабрике окомкования являются сложные машины и оборудование, к которым относятся: смесительные барабаны СБ – 3,5х18; молотковые дробилки ДМ-1,7х1,45; шаровые мельницы Ш-50А; сепараторы пылевые CGW-5500/2000; барабанные смесители СБ-3200х8000; роторные смесители СР-400х1200; окомкователи чашевые Ф-7000 мм; обжиговые машины ОК-306; маятниковые и роликовые укладчики; роликовые грохоты; самобалансные грохоты ГСО3000х6400; роторные заборщики ЗР-550-1; штабелеукладчики ШТК-50-11; ленточные конвейеры различных модификаций; вентиляторы; дымососы.
Офлюсованные окатыши с содержанием железа более 66,5% являются сырьем для производства горячебрикетированного железа.
Производство горячебрикетированного железа
В основе производства горячебрикетированного железа (ГБЖ) лежит процесс прямого восстановления железа, заключающийся во взаимодействии потоков реформированного природного газа и железорудных окатышей, происходящий при температуре около 900°С. По своим качественным характеристикам ГБЖ превосходит металлолом и используется на многих сталеплавильных предприятиях мира. Однако, в отличие от металлического лома, использующегося в настоящее время как основное сырье для получения стали в электросталеплавильных печах, брикеты являются первородным сырьем, не содержащим примеси цветных металлов и пластмасс, существенно ухудшающих качество стали.
Цех горячебрикетированного железа состоит из шахтной восстановительной печи, установки по получению реформированного газа, контуров движения технологического газа, системы загрузки сырья в печь, системы брикетирования, системы транспортировки и отгрузки готовой продукции, вспомогательных и газоочистных систем.
На рис. 3.4. представлена схема производства горячебрикетированного железа.
![]() | Рис. 3.4. Технологическая схема производства горячебрикетированного железа |
Брикеты отправляются внешним потребителям железнодорожным и морским транспортом.
Дата добавления: 2020-12-22; просмотров: 963; Мы поможем в написании вашей работы! |
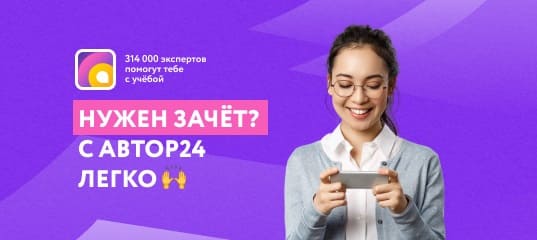
Мы поможем в написании ваших работ!