Типовые аппараты для гранулирования порошков.
Тарельчатый (дисковый) грануляторпредставляет собой вращающийся вокруг центра наклонный диск диаметром 1–6 м и с высотой борта 0,1–0,6 м. Наклон оси вращения к горизонту 45–65°. Частоту вращения выбирают такой, чтобы окружная скорость у борта диска была в пределах 1,4–2,5 м/с. Гранулируемый материал подаётся на поверхность диска и при его вращении окатывается в гранулы. Под действием центробежной силы, сил тяжести, трения материал прижимается к плоскости диска и к его борту, а укрупнившиеся частицы скатываются по слою материала и пересыпаются через борт. Производительность тарельчатых грануляторов достигает 1 т продукта в час с 1 м2 площади тарелки.
Шнековыйгранулятор – горизонтальное или наклонное корыто (барабан) с одним или двумя валами, расположенными параллельно и вращающимися в противоположных направлениях. На валах насажены перемешивающие и транспортирующие лопасти, которые перемещают массу вдоль шнека от места загрузки к месту выгрузки гранул. В шнеки подаются твёрдые и жидкие исходные компоненты и ретур. Длина аппаратов обычно в пределах 3–5 м, частота вращения шнеков 0,5–1,7 с-1 (30–100 об/мин).
Барабанные грануляторычаще всего используют для структурного гранулирования. Это горизонтальные (с углом наклона 1–2°), опирающиеся бандажами на ролики, вращающиеся цилиндры, в которые подается гранулируемый материал, ретур и смачивающая жидкая фаза. Гранулы формируются в результате скатывания при вращении барабана, а затем подсушиваются в сушилке. Размеры барабанов: диаметр 1,5–3 м, длина 5–12 м. Частота вращения 0,1–0,2 с–1 (6–12 об/мин), окружная скорость 0,5–0,6 м/с. Степень заполнения объёма барабана гранулируемым материалом 20–30 %. Производительность аппаратов – десятки тонн гранулята в час.
|
|
Гранулирование и сушка сложных удобрений совмещаются в получившем широкое распространение аппарате БГС – барабанномгрануляторе-сушилке. В этом аппарате возможно изготовление гранул из суспензий при небольшой кратности ретура (0,5–2). Суспензия с помощью форсунок распыляется на взвешенную в объёме аппарата массу гранул, покрывает их и быстро высушивается в потоке топочных газов. Затем, при дальнейшем окатывании, гранулы уплотняются и окончательно высыхают. Обычные размеры барабана аппаратов БГС: диаметр 3–4 м, длина 10–20 м. Они устанавливаются с углом наклона 3°. Частота вращения 0,05–0,08 с–1 (3–5 об/мин). Степень заполнения барабана ~15 %. Содержание воды в гранулируемой суспензии может колебаться в широких пределах: 10–50 %. Температуру газа-теплоносителя выбирают в зависимости от свойств гранулируемого материала: 200–500 °С – на входе, 80–100 °С – на выходе. Аппарат работает под небольшим разряжением. Съём продукта зависит от свойств материала и режима гранулирования; обычно он составляет 80–120 кг/ч с 1 м3 объёма барабана.
|
|
БГС в основном работают с внутренним ретуром, внешний же составляет небольшую долю. Внутренний ретур обеспечивается находящимся в барабане обратным шнеком. Аппараты, называемые сферодайзерами,отличаются от БГС тем, что работают
с внешним ретуром.
Получают распространение наиболее совершенные аппараты – БГСХ (барабанные грануляторы-сушилки с холодильниками), в которых, помимо гранулирования и сушки, осуществляется охлаждение продукта воздухом. В аппаратах БГСХ происходит также предварительная классификация материала – после высушивания мелкая его фракция возвращается с помощью шнека в зону гранулирования, а крупная поступает в находящуюся в конце барабана зону охлаждения.
Гранулирование экструзиейиногда применяют при относительно небольшой производительности установок. Этот метод заключается в предварительной пластификации исходного материала его нагреванием или смешением с жидкой добавкой. Затем пластичная масса поступает в экструдер,в котором продавливается через отверстия в матрицах. Из отверстий материал выходит в виде шнуров и разрезается затем ножом на равные кусочки. Можно использовать два соприкасающихся перфорированных цилиндра, вращающихся в противоположных направлениях. Гранулируемая масса поступает между цилиндрами и продавливается сквозь отверстия внутрь, где расположены срезающие ножи. При круглых отверстиях гранулы имеют цилиндрическую форму. Путём обкатки с добавкой исходного порошкообразного материала и пластификатора их можно превращать в сферические гранулы. Экструзия позволяет получать однородные по размеру гранулы высокой прочности.
|
|
Аппараты с кипящим слоем(КС) можно использовать для получения гранулятов из растворов и суспензий с одновременной их сушкой в потоке газа-теплоносителя. В них же можно гранулировать плавы в потоке холодного воздуха. Газ или воздух подают под решётку, над которой поддерживается кипящий слой гранул (в безрешёточных аппаратах с фонтанирующим слоем – непосредственно в слой), а гранулируемую жидкую фазу диспергируют над кипящим слоем или впрыскивают внутрь его, в результате чего она отверждается на поверхности гранул, высушиваясь или застывая на них. При этом гранулы укрупняются, сепарируются и по достижению необходимого размера выводятся в качестве продукта. Кипящий слой гранул выполняет те же функции, что и ретур при ретурном гранулировании, но затраты теплоты здесь меньше, так как при отсутствии внешнего ретура не требуется расходовать теплоту на его нагревание. Уходящий газ уносит значительное количество пыли, которую необходимо улавливать и возвращать в процесс. Существенное значение имеет вязкость жидкой фазы, влияющая на её диспергирование.
|
|
В зависимости от способов и места ввода в аппарат КС жидкой фазы (диспергирование над слоем гранул либо внутрь слоя с подачей снизу или сбоку) и газа (с подачей под решетку или в факел диспергирования, или с комбинированной подачей) устанавливаются различные режимы работы. Выбор их, а также температуры газа-теплоносителя зависит от свойств гранулируемой массы. Так, при подаче горячего газа в факел диспергируемой жидкости над кипящим слоем или внутри его создаются условия для наиболее интенсивного испарения воды с последующим досушиванием в слое.
Гранулирование порошков прессованием. Гранулирование прессованием,применявшееся раньше только для сухих мелкокристаллических веществ, не поддающихся формированию в прочные гранулы другими способами, теперь всё чаще используют и для гранулирования однокомпонентных и комплексных удобрений, сложных и смешанных. Этот метод более прост и экономичен. Он позволяет путём изменения давления прессования регулировать прочность получаемых гранул и изменять скорость их растворения в почве.
Прессование производят сжатием материала между двумя валками, на которые он подается с помощью червячного питателя. Воздух, удаляющийся из сжимаемого материала, отсасывают снизу, во избежание разрыхления им поступающего сверху порошка. Расстояние между валками – несколько миллиметров. Частота вращения 0,2–1 с– 1.
Гранулирование плавов. Распространённым методом гранулирования горячих плавов является диспергирование их в капли, затвердевающие при охлаждении в газообразной или жидкой тепловоспринимающей среде, например в потоке воздуха или в слое масла, воды. Так, жидкий шлак из фосфорных печей с температурой 1500 °С гранулируют, подавая его струю вместе со струёй воды в грануляционный бассейн (или в жёлоб, барабан) с водой. Образующийся из воды пар разрывает струю шлака на капли, охлаждающиеся и затвердевающие в зёрна.
Для получения из плавов гранулированных минеральных удобрений (нитрата аммония, карбамида, нитроаммофоса и других) широко используют приллирование – разбрызгивание плавов в башнях с восходящим потоком воздуха. Гранулы из не очень вязких плавов имеют шарообразную форму и высокую прочность.
Механизм образования гранул.
Для формирования гранул из исходных частиц порошкообразного материала необходимо обеспечить их сближение на такое расстояние, при котором проявляется какой-либо силы, вызывающей сцепление этих частиц. На рисунке 4.1 дана схема возможных сил, приводящих к сцеплению мелкодисперсных частиц в гранулу.
Рисунок 4.2 - Классификация связей между частицами при росте и формировании гранул
Существует определённая закономерность между природой силы сцепления и размером частиц (рисунок 4.3). Горизонтальной штриховой линией диаграмма разделена на две половины: для области I характерны силы связи, образованные связующим при поверхностном соприкосновении. Активная поверхность взаимодействия частиц при этом определяется в основном внешней энергией или давлением и в меньшей мере зависит от размера частиц исходного сыпучего материала. Область II иллюстрирует более слабые связи, обусловленные капиллярным сцеплением и кристаллическими мостиками. Для этой области наблюдается увеличение прочности связи с уменьшением размера частиц.
Рисунок 4.3 - Сопоставление связей между частицами при различных механизмах сцепления и размерах частиц
Область значений прочности электростатических связей, малозависящей от размера частиц, находится ниже области II. Наклонные прямые разделяют диаграмму на области различных механизмов связей, прочность которых не зависит от размера частиц. Для мелких частиц размером менее 10 мкм силы Ван-дер-Ваальса оказываются более эффективными, так как расстояния между частицами достаточно малы.
Граничная прямая области А рассчитана для среднего расстояния между частицами 3 мкм.
Область В соответствует силам сцепления, обеспечиваемым адсорбционными пленками. В этой области преобладают силы Ван-дер-Ваальса.
Область С иллюстрирует прочность связей, вызванных действием обоих механизмов: пленочного натяжения в жидкостных мостиках и отрицательного гидростатического давления в капиллярах. Выше области С возможно образование еще более прочных связей, обеспечиваемых спеканием, а также добавлением клейких или связующих веществ (область D). Рассмотрение видов связей и сопоставление их прочностных характеристик имеют особое значение при анализе механизма и кинетики процесса гранулирования, осуществляемого различными методами.
Дата добавления: 2020-04-08; просмотров: 190; Мы поможем в написании вашей работы! |
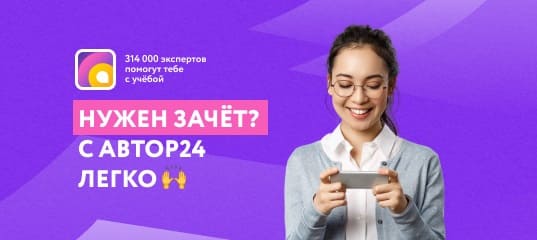
Мы поможем в написании ваших работ!