Химический состав алюминиевых сплавов
Билет
1Вопрос
Алюминий и его сплавы: характеристика, свойства,
Алюминий — серебристо-белый легкий парамагнитный металл. Впервые получен физиком из Дании Гансом Эрстедом в 1825 году. В периодической системе Д. И. Менделеева имеет номер 13 и символ Al, атомная масса равна 26,98.
Производство алюминия
Для производства алюминия используют бокситы — это горная порода, которая содержит гидраты оксида алюминия. Мировые запасы бокситов почти не ограничены и несоизмеримы с динамикой спроса. Боксит дробят, измельчают и сушат. Получившуюся массу сначала нагревают паром, а затем обрабатывают щелочью — в щелочной раствор переходит большая часть оксида алюминия. После этого раствор длительно перемешивают. На этапе электролиза глинозем подвергают воздействию электрического тока силой до 400 кА. Это позволяет разрушить связь между атомами кислорода и алюминия, в результате чего остается только жидкий металл. После этого алюминий отливают в слитки или добавляют к нему различные элементы для создания алюминиевых сплавов.
Алюминиевые сплавы
Наиболее распространенные элементы в составе алюминиевых сплавов — медь, марганец, магний, цинк и кремний. Реже встречаются сплавы с титаном, бериллием, цирконием и литием. Алюминиевые сплавы условно разделяют на две группы: литейные и деформируемые. Для изготовления литейных сплавов расплавленный алюминий заливают в литейную форму, которая соответствует конфигурации получаемого изделия. Эти сплавы часто содержат значительные примеси кремния для улучшения литейных свойств. Деформируемые сплавы сначала разливают в слитки, а затем придают им нужную форму.
|
|
Происходит это несколькими способами в зависимости от вида продукта:
-Прокаткой, если необходимо получить листы и фольгу.
-Прессованием, если нужно получить профили, трубы и прутки.
-Формовкой, чтобы получить сложные формы полуфабрикатов.
-Ковкой, если требуется получить сложные формы с повышенными механическими свойствами.
Марки алюминиевых сплавов
Для маркировки алюминиевых сплавов согласно ГОСТ 4784-97 пользуются буквенно-цифровой системой, в которой:
· А — технический алюминий;
· Д — дюралюминий;
· АК — алюминиевый сплав, ковкий;
· АВ — авиаль;
· В — высокопрочный алюминиевый сплав;
|
|
· АЛ — литейный алюминиевый сплав;
· АМг — алюминиево-магниевый сплав;
· АМц — алюминиево-марганцевый сплав;
· САП — спеченные алюминиевые порошки;
· САС — спеченные алюминиевые сплавы.
После первого набора символов указывается номер марки сплава, а следом за номером — буква, которая обозначает его состояние:
· М — сплав после отжига (мягкий);
· Т — после закалки и естественного старения;
· А — плакированный (нанесен чистый слой алюминия);
· Н — нагартованный;
· П — полунагартованный.
Виды и свойства алюминиевых сплавов
Алюминиево-магниевые сплавы
Эти пластичные сплавы обладают хорошей свариваемостью, коррозийной стойкостью и высоким уровнем усталостной прочности. В алюминиево-магниевых сплавах содержится до 6% магния. Чем выше его содержание, тем прочнее сплав. Повышение концентрации магния на каждый процент увеличивает предел прочности примерно на 30 МПа, а предел текучести — примерно на 20 МПа. При подобных условиях уменьшается относительное удлинение, но незначительно, оставаясь в пределах 30–35%. Однако при содержании магния свыше 6% механическая структура сплава в нагартованном состоянии приобретает нестабильных характер, ухудшается коррозийная стойкость. Для улучшения прочности в сплавы добавляют хром, марганец, титан, кремний или ванадий. Примеси меди и железа, напротив, негативно влияют на сплавы этого вида — снижают свариваемость и коррозионную стойкость.
|
|
Алюминиево-марганцевые сплавы
Это прочные и пластичные сплавы, которые обладают высоким уровнем коррозионной стойкости и хорошей свариваемостью. Для получения мелкозернистой структуры сплавы этого вида легируют титаном, а для сохранения стабильности в нагартованном состоянии добавляют марганец. Основные примеси в сплавах вида Al-Mn — железо и кремний.
Сплавы алюминий-медь-кремний
Сплавы этого вида также называют алькусинами. Из-за высоких технических свойств их используют во втулочных подшипниках, а также при изготовлении блоков цилиндров. Обладают высокой твердостью поверхности, поэтому плохо прирабатываются.
Алюминиево-медные сплавы
Механические свойства сплавов этого вида в термоупрочненном состоянии порой превышают даже механические свойства некоторых низкоуглеродистых сталей. Их главный недостаток — невысокая коррозионная стойкость, потому эти сплавы обрабатывают поверхностными защитными покрытиями. Алюминиево-медные сплавы легируют марганцем, кремнием, железом и магнием. Последний оказывает наибольшее влияние на свойства сплава: легирование магнием значительно повышает предел текучести и прочности. Добавление железа и никеля в сплав повышает его жаропрочность, кремния — способность к искусственному старению. Алюминий-кремниевые сплавы
|
|
Сплавы этого вида иначе называют силуминами. Некоторые из них модифицируют добавками натрия или лития: наличие буквально 0,05% лития или 0,1% натрия увеличивает содержание кремния в эвтектическом сплаве с 12% до 14%. Сплавы применяются для декоративного литья, изготовления корпусов механизмов и элементов бытовых приборов, поскольку обладают хорошими литейными свойствами. Сплавы алюминий-цинк-магний
Прочные и хорошо обрабатываемые. Типичный пример высокопрочного сплава этого вида — В95. Подобная прочность объясняется высокой растворимостью цинка и магния при температуре плавления до 70% и до 17,4% соответственно. При охлаждении растворимость элементов заметно снижается.
Основной недостаток этих сплавов — низкую коррозионную стойкость во время механического напряжения — исправляет легирование медью.
Авиаль
Авиаль — группа сплавов системы алюминий-магний-кремний с незначительными добавлениями иных элементов (Mn, Cr, Cu). Название образовано от сокращения словосочетания «авиационный алюминий». Применять авиаль стали после открытия Д. Хансоном и М. Гейлером эффекта искусственного состаривания и термического упрочнения этой группы сплавов за счет выделения Mg2Si. Эти сплавы отличаются высокой пластичностью и удовлетворительной коррозионной стойкостью. Из авиаля изготавливают кованые и штампованные детали сложной формы. Например, лонжероны лопастей винтов вертолетов. Для повышения коррозионной стойкости содержание меди иногда снижают до 0,1%. Также сплав активно используют для замены нержавеющей стали в корпусах мобильных телефонов.
Физические свойства
· Плотность — 2712 кг/м3.
· Температура плавления — от 658°C до 660°C.
· Удельная теплота плавления — 390 кДж/кг.
· Температура кипения — 2500 °C.
· Удельная теплота испарения — 10,53 МДж/кг.
· Удельная теплоемкость — 897 Дж/кг·K.
· Электропроводность — 37·106 См/м.
· Теплопроводность — 203,5 Вт/(м·К).
Химический состав алюминиевых сплавов
Вопрос
МЕТОДЫ ЦЕНТРОВКИ
Существует широкий спектр методов проведения центровки. Наиболее общие – следующие:
Рис.3.1 Методы центровки
Несоосность в муфтовом соединении, где мощность передается от привода к приводной машине, порождает вибрацию и разрушающие усилия. Следовательно, это именно то место, где необходимо проверять состояние центровки. Все вышеприведенные методы имеют общее то, что измерения проводятся на валах или полумуфтах. Значения корректировок же даются применительно к лапам машины. Положения лап должны быть рассчитаны, чтобы сделать правильные перемещения. Если это не осуществимо, успех будет зависеть от навыков того, кто производит центровку и удачи, потребуется множество перемещений, а точность будет сомнительной.
Механические методы
Край линейки,
Щупы
Конусные калибры (иголки)
Эти грубые инструменты центровки, в общем, до сих пор используются в России и нашли свое место в процессе точной центровки в качестве метода достижения грубой центровки.
В основе они зависят от чистоты плоскостей полумуфт и их биения относительно осей валов. Методы просты и, если, к примеру, полумуфты отличаются по диаметру, то измерения невозможно будет выполнить во всех 4-х точках.
Щупы серии «Щ» незаменимы при сборке некоторых муфт для сохранения параллельности и являются частью каждого набора инструментов для устранения «мягкой лапы».
Преимущества:
o Простой метод
o Непосредственное измерение
o При ограниченном доступе может быть использован для тонких полумуфт
o Зависит полностью от биения фланцев полумуфт
3.2.1 Метод с использованием края линейки и щупов
С помощью прямого края линейки и набора щупов измеряется смещение так, как показано на рисунке ниже.
Рис. 3.2 Измерение смещения
Угловая несоосность измеряется щупами, конусными калибрами, штангенциркулями и т.д. Разница в зазорах, измеренных в двух противоположных точках, используется для определения направления и величины относительного наклона валов.
Рис. 3.3 Измерение угловой несоосности
3.2.2. Обзор методов, использующих индикаторы часового типа
Два фундаментальных метода центровки, использующих индикаторы часового типа и комплект приспособлений центровочный КПЦ (разработанный компанией «Балтех»), - это радиально-осевой метод и метод обратных индикаторов. Детальная информация по этим двум методам находится в разделах 3.2.2.1 и 3.2.2.2.
Радиально-осевой метод
В течение многих лет он был стандартным методом центровки. Преимуществ по сравнению с более современными технологиями у него относительно мало, но на полумуфтах большого диаметра он дает хорошую точность. С его помощью можно замерять биения фланцев больших полумуфт как часть процедуры предварительной проверки.
Когда используется радиально-осевой метод, одно измерение делается по ободу полумуфты для определения смещения вала. Другое измерение производится в осевом направлении на фланце для определения углового положения вала.
Рис.3.4 Радиально-осевой метод
Основные ограничения метода:
o Прогиб выносных элементов ограничивает расстояние применимости этой технологии.
o Конструкция муфтового соединения иногда препятствует доступу к плоскости фланца и в этом случае необходимо сочетать его с другими методами, например, щупами.
o Процесс корректировки становится многоэтапным, сначала исключающим параллелизм, а затем концентричность. Поскольку существуют горизонтальные и вертикальные составляющие для каждого компонента, в действительности будет четыре этапа, каждый из которых, если потребуется, может быть повторен.
o Чтобы оценить результат перемещения, необходимо повторное измерение.
o Осевые перемещения вала напрямую влияют на результат измерений.
Хотя, как и в большинстве технологий, имеются определенные преимущества. В ограниченном пространстве только этим методом можно сделать данную работу. Подобный инструмент и методика в большинстве случаев должны использоваться для оценки биения фланцев полумуфт и радиального биения валов в подшипниках.
Многие производители турбин назначают зазор в муфтовом соединении или биение боковой поверхности в качестве допусков при проведении центровки и в этом случае только данные значения необходимо измерять.
Одно важное замечание, относящееся к сопоставлению показаний, полученных методом с использованием индикаторов часового типа (MVR-1701) и лазерных систем, - то, что практически каждая лазерная система покажет положение валов ниже того уровня, где они по предположению должны находиться.
Необходимость разделения этапов центровки и корректировки угловой несоосности и смещения по вертикали и горизонтали с использованием радиальных измерений может замедлить проведение всей процедуры в целом. Во время перемещения механизма вы можете довольно сильно изменить смещение или угол, что потребует проведения повторных измерений и перемещений. Можно было бы закрепить два индикатора на одном стержне, но это не общепринятая практика. Практические ограничения возможности измерений на фланце – одна из причин, почему пренебрегают измерением угловой несоосности, полагаясь на точность изготовления полумуфт. Если имеется смещение или перекос, вы можете ошибочно полагать, что установили механизмы идеально соосно.
Метод обратных индикаторов
Обратных индикаторов, обратный снаружи, обратно-радиальный, обратный часовой, двойной обратный – все это термины для одного и того же метода центровки, использующего два индикатора часового типа и комплект приспособлений центровочный КПЦ (разработанный компанией «Балтех»). При его использовании делаются два измерения по окружности муфтового соединения в двух точках для определения смещения валов. Оба вала вращают одновременно или, в некоторых случая, измерения проводятся в два этапа одним индикатором, но с переменой его положения. Угловое положение вала является наклоном между измеренными смещениями в двух точках.
Этот метод был одобрен и рекомендован к применению в России компанией «Балтех». Заметна тенденция роста стандартизации этой техники в широкой области производств.
Рис.3.5 Метод обратных индикаторов
Главным преимуществом метода является то, что он дает сразу информацию о смещении и об угловом положении валов и обеспечивает простой расчет и графическое построение положения валов при центровке и корректировке. Увеличение расстояния между измерительными точками (А) увеличивает точность определения углового положения валов. Хотя, для индикаторов часового типа практического значения это не имеет, так как требуется ввод компенсационных значений прогиба.
На коротком расстоянии этот метод уступает в точности определения угла радиально-осевому методу, если расстояние А меньше диаметра полумуфты. Как и для всех измерений часовыми индикаторами, расчет центровки и корректировки требует графического построения. Будьте внимательны при считывании обратных показаний положительных и отрицательных значений. Легко перепутать знаки или пропустить полный оборот стрелки индикатора.
Также как и для радиально-осевого метода перемещения машины в значительной степени - результат пробных смещений с повторными измерениями. Преимущество метода обратных индикаторов в том, что корректирующие значения по смещению и углу даются одновременно, что сокращает время проведения центровки.
Лазерные системы
Несколько типов лазерных систем центровки доступно для решения задач центровки валов. Вместо стальных стержней с часовыми индикаторами, эти системы используют лазерные лучи и электронные детекторы. Одно из главных преимуществ лазерного луча - то, что нет потери точности измерений, вызванной прогибом выносных штанг. Все лазерные системы, включают в себя лазерные излучатели, приемники и электронный блок, который производит расчеты центровки.
В настоящее время существует два типа лазерных систем, основанных на различных методиках.
o Один лазер с одним приемником
o Двойной лазер, использующий метод обратных индикаторов.
3.3.1. Один лазер с одной или двумя мишенями.
Этот тип системы использует авто коллимацию для измерения смещения и угла с помощью отражающей призмы или пяти осевой мишени. Мишень измеряет и вертикальные и горизонтальные компоненты одновременно с углом. Хотя этот метод точен в угловых измерениях на коротких дистанциях, его труднее использовать и для грубой центровки.
Он может быть также чувствителен к люфтам при вращении валов с разъединенными полумуфтами, и без математических компенсаций тут не обойтись. Требуется повторное измерение после каждой подвижки, так как теряется опорная точка.
При этом нельзя определить боковые перемещения самим устройством или независимые повороты каждого вала. Для преодоления такого ограничения необходимо каким-либо образом соединить валы, чтобы заставить их поворачиваться синхронно. Данный тип используется в импортных лазерных системах.
Рис. 3.6 Один лазер с одной или двойной мишенью
3.3.2. Двойной лазер, использующий метод обратных индикаторов.
Этот тип системы использует главные преимущества метода обратных индикаторов. Две измерительные системы объединяют лазер и приемник в одном блоке. Техника позволяет отображать текущие значения компонент несоосности и непрерывно обновляет показания при перемещении машины.
Последнее поколение систем имеет разрешение 0,001 мм с фильтрацией для компенсации колебаний воздуха или механической вибрации.
Удобство системы в ее гибкости, которое особенно заметно в грубой центровке и технике конуса, применяемой при центровке карданных валов на больших расстояниях или приводов градирен. Данный тип используется в приборах и системах лазерной центровки валов, разработанных компанией «Балтех».
Рис. 3.7 Двойной лазер, использующий метод обратных индикаторов
Дата добавления: 2019-11-16; просмотров: 969; Мы поможем в написании вашей работы! |
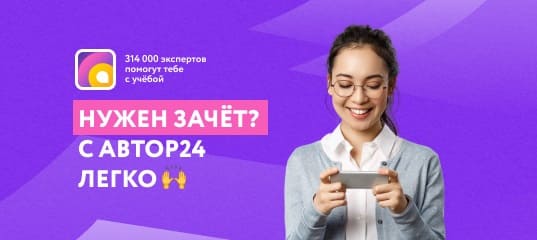
Мы поможем в написании ваших работ!