Требования, предъявляемые к качеству шихтовых материалов
На основании полученных документов и внешнего осмотра материалов вагоны должны быть размечены и сгруппированы в соответствии с фронтом выгрузки и схемой расположения материалов на рудном дворе. Фронты разгрузки каждого материала должны быть четко разграничены указателями.
Выбор фронтов разгрузки материалов должен обеспечить исключение перемешивания различных видов материалов на рудном дворе. Качество шихтовых материалов должно соответствовать требованиям ГОСТа и ТУ.
Технологические свойства кокса
Контроль качества кокса осуществляется по следующим его характеристикам.
1. Технический анализ.
2. Гранулометрический состав.
3. Прочность.
4. Пористость.
5. Насыпная масса.
6. Температура воспламенения.
7. Реакционная способность.
Технический анализ кока. Здесь дается информация о содержании серы (S), золы (А), летучих веществ (ЛВ) и влаги (W). Важнейшая характеристика кокса – содержание углерода (нелетучего) – здесь не определяется. Его находят по разности СНЕЛЕТ = 100 – (А + ЛВ + S ), а содержание влаги в коксе дается сверх 100 %.
Сера является вредной примесью чугуна и в подавляющем большинстве случаев кокс является главным ее поставщиком. Содержание серы в коксе определяется её содержанием в углях, поступающих на коксование. Практикой работы доменных печей установленно, что увеличение содержания серы в коксе на 0,1 % сопровождается увеличением удельного расхода кокса в среднем на 0,3 % с одновременным таким же снижением производительности печи.
|
|
Зольностькокса. Зола в коксе является крайне нежелательной примесью и ее содержание должно быть минимальным. Зола в коксе влияет на выход шлака и прочность кокса. Известно, что разрушение кусков кокса происходит по его зольным включениям. Поскольку содержание кремнезема (SiO 2) в золе кокса чаще всего составляет 50 % и более, то для получения требуемой основности шлака необходим ввод в шихту основных оксидов, что снижает показатели доменной плавки. Считается, что каждый процент увеличения золы в коксе снижает производительность печи от 1,0 до 1,8 % (при содержании золы в коксе, соответственно, от 10 до 13 %) и увеличивает расход кокса от 1,2 до 2,0 %.
Летучие кокса. Содержание летучих в коксе косвенно характеризует его качество. Их содержание зависит от продолжительности периода коксования и конечной температуры коксования. Чем выше указанные параметры коксования, тем меньше в коксе летучих веществ. Нормальным содержанием летучих в коксе считается 0,8 - 1,2 %. Повышенное содержание летучих в коксе свидетельствует о незавершенности процесса коксования и отрицательно сказывается на его качестве. Такой кокс получил название – “недопал”. Он характеризуется более темным цветом в сравнении с коксом хорошего качества и пониженной механической прочностью. Уменьшение выхода летучих веществ в коксе ниже 0,5 % свидетельствует об увеличенном периоде коксования, что приводит также к снижению прочности кокса вследствие его “пережога” и увеличения трещиноватости.
|
|
Влажность кокса. Влага в коксе не приносит вреда доменному процессу. При загрузке в печь влажного кокса происходит испарение этой влаги за счет тепла отходящих из печи газов - температура колошникового газа снижается. Для нормального технологического режима плавки очень важно использовать кокс с минимальными колебаниями его влажности. Поскольку загрузка кокса в печь осуществляется по массе, то при минимальных колебаниях влажности кокса гарантирует стабильность теплового режима плавки.
Технические составы коксов, производимых на различных коксохимических предприятиях России, приводятся в специальной справочной литературе.
Гранулометрический состав кокса. Кокс в доменной печи определяет газодинамическое сопротивление слоя шихты движущемуся потоку газа и должен быть крупным, а также сохранять размер кусков по мере его движения от колошника к фурменным очагам. Гранулометрический состав кокса - это распределение его кусков по классам крупности, выраженное в процентах к массе исходной пробы. ГОСТ предусматривает следующую градацию кусков кокса по крупности: > 80 мм, 80-60 мм, 60-40 мм, 40-25 мм и < 25 мм. Гранулометрический состав коксов различных коксохимических предприятий России также приводится в справочной литературе. Следует отметить, что фракция + 80 нежелательна. Увеличение фракции +80 на 1 % приводит к увеличению удельного расхода кокса на 1,2 %. Фракция -25 отсеивается и не используется в доменных печах.
|
|
Прочность кокса. Это - важнейшая характеристика кокса, определяющая в первую очередь газодинамические характеристики столба шихтовых материалов в доменной печи. Появление мелочи при разрушении непрочного кокса не только ухудшает газопроницаемость шихты в печи, но и уменьшает размеры фурменного очага, а значит и газораспределение в поперечном сечении доменной печи.
Под прочностью кокса понимают его способность противостоять разрушающим воздействиям всех видов. Прочность определяется в барабане диаметром 1 м и длиной 1 м. Внутри барабана приварены 4 уголка с полочкой 100 мм. В барабан загружается 50 кг кокса фракции > 25 мм. Затем барабан вращается в течение 4 минут со скоростью 25 об./мин., после чего кокс извлекается из барабана и рассеивается на ситах с ячейками 60х60 мм, 40х40 мм, 25х25 и 10х10 мм. Выход кусков менее 10 мм (показатель М10) характеризует истираемость кокса, а выход кусков кокса более 40 и 25 мм (показатели М40 и М25) – определяет его механическую прочность. Истираемость производимого кокса меняется в пределах от 6 до 11 % (от массы загруженного в барабан кокса), а выход класса более 25 мм составляет 84-98 %.
|
|
К числу важных показателей качества кокса как топлива относятся также пористость, насыпная масса, температура воспламенения.
Пористость - это отношение объема пор куска к объему всего куска, выраженное в процентах. Пористость кокса влияет на условия его горения: чем выше пористость, тем интенсивнее происходит горение кокса, что приводит к сокращению объема фурменных очагов. Пористость кокса зависит от свойств исходных углей, состава угольных шихт, идущих на коксование, она определяется также режимом коксования и колеблется в пределах 35 - 50 %.
Насыпная масса кокса. Это - масса кокса в единице объема. Установлено, что доменные печи лучше работают на коксе с меньшим значением насыпной массы. Насыпная масса определяется не только геометрией куска, но и соотношением в слое крупных и мелких фракций. Чем однороднее кокс по гранулометрическому составу, тем меньше его насыпная масса и выше газопроницаемость. Считается, что насыпная масса доменного кокса имеет значение в пределах 0,45 - 0,47 м3/м3.
Температура воспламенения кокса. Определенную роль играет при задувке доменной печи. Для производимых коксов температура воспламенения находится в пределах 650 - 750 °С.
Реакционная способность кокса характеризует его способность взаимодействовать с диоксидомуглерода по реакции С+СО2=2СО-Q и определяет ее скорость. Повышение реакционной способности кокса приводит к развитию реакции прямого восстановления железа и перерасход кокса.
Качество железорудного сырья
Железорудные материалы контролируются по следующим параметрам.
1. Химический состав железорудных материалов.
2. Гранулометрический состав железорудных материалов.
3. Восстановимость железорудного материала.
4. Горячая и холодная прочность.
5. Температурный интервал вязкопластичного состояния.
Химический состав железорудных материалови его стабильность определяют все технико-экономические показатели доменной плавки: производительность печи, удельный расход кокса, выход шлака, качество получаемого чугуна и др. Для постоянного контроля за работой доменной печи в обязательном порядке определяется содержание в нем следующих элементов и оксидов: Fe общ , FeO , Mn , SiO 2 , CaO. Лишь в отдельных случаях оговаривается определение содержания других соединений. Для осуществления нормального технологического режима плавки, оптимизации шлакового режима необходимо иметь информацию как минимум еще по содержанию двух оксидов: Al 2 O 3 и MgO.
Эффективность доменной плавки в значительной степени зависит от постоянства химического состава и физических свойств загружаемых в печь шихтовых материалов. Колебания химического состава шихты значительно ухудшают работу доменной печи, так как его неконтролируемые изменения приводят к нарушению нормального хода процесса. Особенно важным является постоянство содержания железа: снижение его приводит к разогреву печи, а повышение – к похолоданию. Опасность похолодания заставляет вести процесс с резервом тепла, т.е. с перерасходом кокса. Изменения содержания кремнезема и основных оксидов приводят к изменению состава шлака и его физических свойств и расстройству процесса. Изменение гранулометрического состава шихты вызывает нарушение установившегося распределения материала на колошнике и изменяет распределение газового потока. На передовых предприятиях количество проб агломерата и руд с колебаниями содержания железа в пределах 0,5 % изменяется от 50 до 93 %, а в пределах
1,0 % - до 99 %. Пределы колебаний основности окускованных материалов составляют
0,05 абс.
Немаловажное значение для эффективности плавки имеет и стабильность содержания в шихтовых материалах MgO и Al 2 O 3. Считают, что при содержании MgO 2 % колебания не должны превышать 0,1 % абс. Пределы колебаний М gO должны быть внесены в технические условия качества окускованного сырья. Когда окускованное сырье содержит значительное количество глинозема, оценка основности производится по отношению ( CaO + MgO ):( SiO 2 + Al 2 O 3 ), а также по кремниевому модулю SiO 2 : Al 2 O 3.
Механическая прочность железорудных материалов является одной из важных его характеристик. Под механической прочностью железорудного материала понимают сопротивление его дроблению и истиранию. Для испытания железорудного материала на механическую прочность применяют барабан (ГОСТ 15137-77) диаметром 1 м и длиной 0,5 м. Внутри барабана диаметрально привариваются два уголка 50х50х5 мм. Внутрь барабана загружается 15 кг агломерата крупностью 5-40 мм или окатышей размерами 5-25 мм. Барабан вращается в течение 8 минут с частотой 25 об/мин. После этого пробу рассеивают на ситах с размером ячеек 5 и 0,5 мм. Масса материала фракции более 5 мм в процентах от массы пробы является показателем прочности на дробление, а масса фракции менее 0,5 мм характеризует прочность на истирание. Первый показатель чаще применяется к агломерату и его численное значение меняется в пределах от 55 до 82 %, а второй – к окатышам, его значение для производимых окатышей составляет 5-11 %. Следует отметить, что определяемая таким образом механическая прочность железорудного материала далеко не отражает прочностные характеристики железорудных материалов в доменной печи, где эти материалы подвергаются не только механическим нагрузкам, но и восстановительно-тепловой обработке. Установлено, к примеру, что механическая прочность окатышей в печи может быть значительно ниже определяемой описанным методом в связи с явлением разупрочнения, связанного с обработкой окатышей газом-восстановителем. Имеющаяся методика определения “горячей прочности” железорудных материалов (ГОСТ 19575-84) не нашла в настоящее время широкого практического применения.
Восстановимость. Под восстановимостью железорудного материала понимается его способность с большей или меньшей скоростью отдавать кислород от оксидов железа газу-восстановителю. Этот показатель относится к одному из важнейших, определяющих развитие процессов косвенного восстановления и расход кокса. Для определения восстановимости железорудных материалов используется методика согласно ГОСТ 17212-84. Восстановление производится в вертикальной реакционной трубе, помещенной в электропечь. Навеска рудного материала крупностью 12,5 - 10 мм массой 500 г загружается в реакционную трубу, которая подвешивается к весоизмерительному устройству. Навеска продувается газом с расходом 30 ± 1 кубических дециметров в минуту. Газ имеет следующий состав: СО = 33 %, N 2 = 65 %, остальное Н2, СО2, Н2О. В процессе продувки навески газом печь нагревается в начале до 600 °С в течение 40 минут, а затем до 1100 °С в последующие 175 минут. В процессе нагрева навески и продувки ее газом-восстановителем производится регистрация потерь массы кислорода. Восстановимость определяется как отношение массы отнятого кислорода к массе первоначально связанного кислорода, выраженное в процентах. Железорудные материалы хорошей восстановимости имеют этот показатель в пределах 60-70 %.
Гранулометрический состав. Размер кусков железорудной шихты определяет газопроницаемость столба материалов, а также развитие восстановительных процессов в печи. Размер кусков железорудного материала, как было показано выше, должен быть оптимальным, поскольку чрезмерно большой размер, обеспечивая достаточно хорошую газопроницаемость слоя шихты, значительно ухудшает протекание восстановительных процессов и, наоборот, мелкий рудный материал, имея развитую реакционную поверхность и хороший контакт с газом-восстановителем, ускоряет процессы восстановления, но слой, составленный из мелких кусков, оказывает большое сопротивление движущемуся газовому потоку и ограничивает производительность печи. Несмотря на важность информации о полном ситовом составе железорудных материалов, чаще всего в нем определяют только содержание мелочи - фракции менее 5 мм. Полный гранулометрический анализ агломерата предполагает определение в нем следующих фракций: > 50 мм, 25-40 мм, 10-25 мм, 5-10 мм, < 5 мм.
Что касается гранулометрического состава окатышей, то в нем указывается только их средний размер (обычно от 9 до 25 мм) и содержание фракции менее 5 мм (для производимых в России окатышей - от 2,3 до 3,7 %).
Температурный интервал вязкопластичного состояния. Температурный интервал зоны вязкопластичного состояния определяет газодинамическую напряженность в нижней зоне доменной печи. Температурный интервал определяется температурами начала плавления железорудного материала (tнп ) и температурой расплавления (tр).
Многочисленные экспериментальные исследования усадки материалов при их нагреве показали, что tнп определяется минералогическим составом агломерата, а именно, наличием в агломерате оливинов и силикатного стекла. В процессе нагрева, образуются расплавы эвтектического состава. Существенное влияние на tнп оказывает основность агломерата и содержание в нем MgO. Анализ диаграмм плавления системы CaO - SiO2- Al2O23 – MgO показал, что с ростом основности и содержания MgO в агломерате tнп увеличивается. Для расчета температуры начала плавления железорудных материалов используется уравнение В.З. Кацмана, которое имеет следующий вид.
tн.пл.=1085,3+63,8*(CaO/SiO2)+25,3*MgO-13,8*Al2O3-0,2*FeO-11,6*MnO,
где CaO,SiO2,MgO, Al2O3, FeO, MnO.- содержание соответствующих оксидов в железорудном материале, %.
Под температурой расплавления понимается такая температура, при которой расплав железорудных материалов вытекает из лабораторной установки.
Целесообразнее принимать за температуру расплавления материала такую температуру, при которой становится возможным вытекание расплава из коксовой насадки, состоящей из кусков диаметром 25 мм. По имеющимся в литературе данным, расплав из коксовой насадки вытекает тогда, когда его вязкость достигает 2,5 Па*с.
Рассчитать данную температуру можно исходя из температурной зависимости вязкости расплава. В общем виде эта зависимость может быть представлена уравнением Ле-Шателье ,
lg(lgh)=а0+а1*t.
Здесь а0 и а1- эмпирические коэффициенты;
t – температура шлака, оС.
Для определения коэффициентов а0 и а1 достаточно для каждого конкретного состава расплава знать его вязкость при двух температурах.
Дата добавления: 2019-09-13; просмотров: 438; Мы поможем в написании вашей работы! |
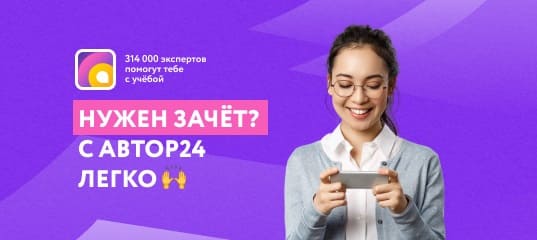
Мы поможем в написании ваших работ!