Особенности изготовления тонкостенных сосудов.
Изготовление сосудов, работающих под давлением.
Общим для такого типа конструкций является требование возможно более равномер ного распределения напряжений. Это достигают применением соединений встык, плавным сопряжением стыкуемых элементов и обеспечением проплавления на всю их толщину. При рассмотрении вопросов технологии изготовления сварные сосуды давления целесообразно разделить на три группы: тонкостенные, со стенками из листов средней толщины и толстостенные.
Тонкостенные сосуды обычно являются конструктивными элементами различных транспо.ртных установок, в том числе современных летательных аппаратов. С целью снижения веса таких сосудов для их изготовления часто используют листовые материалы, обладающие высокой удельной прочностью — алюминиевые и магниевые сплавы, стали высокой прочности и сплавы титана. Для соединения тонколистовых элементов встык используют преимущественно сварку в среде защитных газов. Существенное улучшение качества стыковых соединений тонкого металла может быть достигнуто за счет пластического деформирования зоны шва путем прокатки между роликами и последующей термической обработки. Такой прием позволяет осуществить заглаживание усиления шва, устранить депланацию кромок и улучшить механические свойства и структуру сварного соединения. В сосудах типовыми являются прямолинейные, кольцевые и круговые стыковые швы. Приемы выполнения каждого из них имеют свои особенности, разнообразна и применяемая оснастка.
Сборку и сварку прямолинейных швов тонкостенных сосудов рекомендуется производить с помощью зажимных приспособлений клавишного типа без прихватки, обеспечивающих равномерное и плотное прижатие кромок к подкладке. При сварке тонколистовых элементов из жаропрочных и нержавеющих сталей используют медные подкладки, а при сварке высокопрочных сталей и алюминиевых сплавов — стальные. Усилие зажатия обычно составляет 30—70 кг на 1 пог. см шва и создается гидравлическим или пневматическим устройством.
Деформации тонкостенных обечаек от продольных швов можно устранить прокаткой соединений роликами.
Кольцевые стыки тонкостенных обечаек собирают и сваривают обычно на подкладках разжимных колец. Такой прием имеет определенные недостатки, так как не препятствует перемещению кромок наружу, подогрев кромок впереди сварочной дуги заставляет их расширяться и отходить от подкладного кольца в радиальном направлении, что нередко приводит к возникновению депланации кромок. В тонкостенных сосудах, работающих под давлением, такое смещение кромок может оказаться опасным для прочности концентратором. Эффективным средством предотвращения смещений является прижатие кромок к подкладке роликом. Помимо сварки на подкладном кольце, можно использовать схему, при которой зона кольцевого шва охватывается снаружи жестким бандажом, а сварка стыка выполняется изнутри обечайки. В этом случае напряжения сжатия, возникающие в зоне нагрева, стремясь увеличить длину свободной кромки стыка, прижимают ее к наружному бандажу, исключая возможность образования смещений и вспучивания.
Элементы арматуры (фланцы, штуцеры) вваривают в стенки сосудов с помощью круговых швов, которые выполняют встык на подкладке с канавкой. Требования к сборочно-сварочной оснастке и конструктивному оформлению стыка определяются необходимостью плотного прижатия кромок к подкладке, предотвращения их перемещения в процессе выполнения кругового шва и устранения сварочных деформаций, вызывающих искажение формы оболочки. При небольших размерах сосуда или элемента, в которые вваривают деталь арматуры, сварку кругового шва целесообразно осуществлять неподвижной сварочной головкой, вращая приспособление. В узлах значительных размеров круговой шов более удобно выполнять перемещающейся сварочной головкой при неподвижном изделии.
Сосуды со стенками из листов средней толщины (до 40 мм) из малоуглеродистых и низколегированных сталей изготовляют преимущественно с помощью автоматической сварки под флюсом. Сосуды, работающие в агрессивных средах, изготовляют из хромоникелевых и хромистых сталей, цветных металлов и их сплавов автоматической сваркой под флюсом и по слою флюса полуоткрытой дугой (алюминиевые сплавы), а также аргоно-дуговой сваркой. Необходимость экономии дорогостоящих и дефицитных материалов заставляет расширять применение двухслойных листов. При выполнении сварных соединений двухслойных сталей обеспечение коррозионной стойкости и пластичности шва достигается за счет раздельного плавления углеродистой стали и металла защитного слоя и использования для каждого из слоев различных присадочных материалов и приемов сварки. Сварка всего стыка автоматом требует точной сборки и высокой культуры выполнения сварного соединения. Поэтому более часто при сварке двухслойной стали автомат используют только для основного слоя, а плакированный сваривают вручную.
Сосуды из листов средней толщины наиболее часто имеют цилиндрическую форму. По длине сосуд составляется из нескольких обечаек и двух полусферических или эллиптических днищ. В зависимости от диаметра сосуда каждую обечайку либо вальцуют из целого листа, либо составляют из нескольких листов. В последнем случае нередко встык сваривают плоские листы и вальцовке подвергают сварную карту при расположении швов вдоль образующей. Днища либо сваривают из отдельных штампованных лепестков, либо штампуют из целого листа или из сварной заготовки. Сборку и сварку цилиндрической части сосуда производят на роликовом стенде. Продольный стык обечайки собирают па прихватках с помощью стяжных приспособлений. Сборка кольцевого стыка между обечайками является более трудоемкой операцией. Сварку продольных и кольцевых швов сосудов со средней толщиной стенки выполняют, как правило, с двух сторон. Укладка первого слоя на весу требует тщательной сборки и ограничения зазора по всей длине шва. Поэтому роликовые стенды обычно оборудуют флюсовыми подушками, позволяющими производить сварку первого слоя шва без ограничения зазора в стыке. Такие флюсовые подушки удобно монтировать на тележках, предусматривая между роликами стенда рельсовый путь для их передвижения к свариваемому стыку. После выполнения первого слоя изнутри обечайки на флюсовой подушке второй слой сваривают снаружи по ранее уложенному первому с полным проплавлением всей толщины стенки. При толщине стенки сосуда более 25 мм автоматическую сварку под флюсом обычно производят в несколько слоев. При сборке цилиндрических обечаек с днищами целесообразно использовать центрирующие устройства. Сварку этих кольцевых стыков выполняют так же, как и стыков между обечайками.
В серийном производстве сосудов используют поточные методы производства. Примером может служить изготовление котлов железнодорожных цистерн из стали Ст.З па Ждановском заводе тяжелого машиностроения. Цилиндрическую часть котла составляют из четырех листов 9280X1680X9 мм и одного листа 9280X2100X11 мм. На сборочном стенде листы собирают встык на прихватках с постановкой заходных и выходных планок. Собранное полотнище поднимается системой роликов, а затем транспортирующим устройством подается на стенд для сварки, где оно собранными стыками ложится на флюсовые подушки. Кромки прижимаются пневмоцилиндрами, расположенными па двух поперечных балках-порталах. Эти же балки служат направляющими для четырех сварочных головок, предназначенных для одновременной сварки всех швов полотнища. По окончании сварки полотнище передается на кантователь, переворачивается и поступает на вторую сварочную установку для одновременной сварки четырех стыков с другой стороны. Далее полотнище перемещается рольгангом в 10-метровые гибочные вальцы, где вальцуется вдоль швов в обечайку диаметром 2800 мм без предварительной подгибки кромок. Свальцованная обечайка мостовым краном переносится в сборочный стапель, где стягивают и прихватывают кромки продольного стыка, а затем подается в установку для сварки и поворачивается так, чтобы продольный стык оказался в нижнем положении. Первый слой выполняется изнутри обечайки на флюсовой подушке, а второй снаружи после разворота обечайки. Сваренная обечайка поступает в гибочные вальцы для калибровки, а затем устанавливается на роликовый конвейер и попадает на место сборки с днищами (рис. 29), оборудованное двумя центраторами 2 с откидными рабочими площадками 1. К зажатой боковыми домкратами 3 обечайке подводятся подвешенные на специальных захватах днища и прижимаются четырьмя откидными винтовыми прижимами 5. Выравнивание кромок перед прихваткой осуществляется с помощью 26 радиальных пневматических цилиндров 4, расположенных на каждом центраторе. После прихватки обечайка освобождается от закрепления и передается конвейером на стенд для сварки изнутри, оборудованный двумя флюсоременными подушками. Изготовление цилиндрической части котла завершается на стенде сварки наружных швов с двумя сварочными головками, расположенными на поворотных консолях. На каждом из этих двух рабочих мест вращение обечайки со сварочной скоростью обеспечивается с помощью подъемных поперечных роликоопор, приподнимающих обечайку над роликами конвейера.
|
|
|
|
|
|
|
|
При изготовлении толстостенных сосудов (толщина свыше 40—60 мм) наиболее эффективным оказывается способ электрошлаковой сварки, позволяющий получить надежное проплавление всего сечения за один проход. Продольные швы толстостенных обечаек, как правило, выполняют электрошлаковой сваркой. В зависимости от размеров сосуда и имеющегося в наличии гибочного оборудования листовую заготовку гнут в нагретом состоянии вдоль длинной или вдоль короткой кромки листа. В нервом случае уменьшается
количество более трудоемких кольцевых швов в сосуде, а во втором — менее трудоемких — продольных. На рис. 30, а, б показаны сечения обечаек с одним и двумя продольными стыками, величина зазора фиксируется приваркой скоб.. Если обечайку после сварки продольных швов необходимо править, ее нагревают до 1000—1050° С, а охлаждение на воздухе при калибровке используют одновременно для осуществления процесса нормализации.
Кольцевые швы выполняют многослойными сваркой под флюсом или электрошлаковой сваркой в один проход. Полное нроплавление при многослойной сварке обеспечивают укладкой в разделку нескольких подварочных слоев с внешней стороны (рис. 31), зачисткой корня шва с помощью пневматического зубила или резака и наложением внутреннего подварочного шва. После этого производят многослойное заполнение внешней разделки.
Сборка кольцевого шва под электрошлаковую сварку должна быть достаточно точной,.так как местная депланация криволинейных кромок стыка свыше 3 мм может привести к нарушению уплотнения и вытеканию шлаковой ванны. Поэтому сборке обычно предшествует проточка внешней и внутренней поверхности обечаек у кромок на ширине 70—100 мм от торца. Собирают стык при помощи планок, которые устанавливают «на ребро» поперек кольцевого шва и приваривают к поверхности обечаек. Если в качестве внутреннего формирующего устройства используют медные охлаждаемые подкладки, изогнутые по радиусу свариваемого изделия, то внутри обечайки дополнительно устанавливают скобы временного крепления. Внутренний ползун применяют тогда, когда допускает форма изделия, в этом случае внутренних скоб не ставят.
При изготовлении барабанов котлов, сосудов высокого давления и реакторов большое значение придают термообработке. Окончательная термообработка
полностью сваренного сосуда часто ограничивается высоким отпуском. При приварке днищ электрошлако-пой сваркой иногда требуется нормализация для улучшения структуры зоны шва. В этом случае возникает опасность, что при нагреве до столь высоких температур (900—1000° С) могут возникнуть деформации от собственного веса, искажающие форму сосуда. Предотвратить эти деформации можно путем предварительной герметизации готового сосуда и создания в нем избыточного внутреннего давления углекислого газа 2—3 кГ/см2. Такое мероприятие не только сохраняет форму сосуда, но и предотвращает образование окалины на его внутренней поверхности. Для термообработки обычно используют печи большого размера. Если сосуд не может быть подвергнут термообработке целиком из-за отсутствия печи требуемого размера или из-за необходимости выполнения монтажных стыков, то применяют местную или общую термообработку с йбпользованием индукционных или иных нагревателей.
При изготовлении толстостенных сосудов из двухслойных сталей основной слой сваривают электрошлаковой сваркой. Наплавку коррозионно-стойкого сплава производят только после термообработки сваренного узла и контроля. Сосуды, предназначенные для работы при очень высоком давлении, целесообразно выполнять многослойными. За рубежом такие сосуды изготовляют для давления до 2000 кГ/см2 и выше. При этом путем предварительного натяжения каждого слоя стремятся создать такое распределение напряжений, которое при рабочем нагружении сосуда внутренним давлением обеспечит равномерную работу всех слоев. Конструктивное оформление таких сосудов и способы создания начальных напряжений при изготовлении многослойных обечаек могут быть различны. Один из способов предусматривает изготовление центральной обечайки толщиной 25—30 мм, приварку к ней края стальной ленты, навивку ленты на обечайку в несколько слоев с натяжением и закреплением свободного конца ленты к корпусу продольным швом. Многослойные обечайки сваривают между собой встык кольцевыми швами, к обоим концам цилиндрической части сосуда приваривают днища или кованые фланцы для крепления крышек (рис. 32).
Для сохранения полезных предварительных напряжений, созданных за счет натяга или механической обтяжки слоев и усадки от продольных и кольцевых швов, многослойные сосуды после сварки термообработке не подвергают.
Особенности изготовления тонкостенных сосудов.
Шов тонкостенных сосудов зачастую выполняется в среде защитных газов. Сборка производится с помощью специальных зажимных приспособлений. Во время сборки и дальнейшей сварке прямолинейных швов, расположенных между листами, а также продольных швов обечаек, осуществляется равномерное прижатие кромок к подкладке при помощи зажимных приспособлений клавишного типа. Стоит отметить, что прижатие в таком случае достаточно плотное. Усилие прижатия колеблется в пределах 300-700 Н на сантиметр длины шва. Данное усилие создается посредством пневматического или гидравлического устройства.
На верхнем основании каркаса (жесткого) в закрепленном положении находится ложемент с подкладкой. Разжим кромок, которые необходимо сваривать между собой, осуществляется отдельно для каждого из листов при помощи набора клавиш, расположенных на балках. На клавиши пневмо штангами передается давление. Регулировка давления осуществляется редуктором.
Установка и дальнейшее прижатие листов имеет четкую последовательность:
1. Поворот эксцентрикового валика.
2. Далее из подкладки выдвигаются фиксаторы.
3. Заводится листовая заготовка в фиксаторы до упора.
4. Заготовка зажимается посредством подаваемого в шланг воздуха.
5. Фиксаторы убираются, после чего следует установка другой заготовки в кромку до упора.
6. Зажим подачей воздуха в шланг.
Сборка и сварка продольных стыков обечаек предусматривает выполнение основания приспособления в виде консоли. Таким образом, прижимные балки с клавишами закрепляются жестко одним концом, в то время как другим концом закрепление производится при помощи откидных болтов. Продольные швы служат побудителями нарушений прямолинейности образующих тонкостенных обечаек, после чего происходит уменьшение кривизны в поперечном сечении зоны шва. Для того чтобы исправить подобные сварочные деформации, используется прокатка роликами.
Во время выполнения кольцевых стыков сосудов, работающих под давлением, с тонкими стенками из материалов осуществляется концентрация напряжений. В связи с этим используется остающиеся подкладные кольца, облегчающие центровку кромок, а также их дальнейшую одностороннюю сварку. Отметим, что для целого ряда высокопрочных материалов подобный прием остается нежелательным. В данном случае рекомендуется собирать кольцевые стыки, после чего сваривать их на подкладках разжимных (съемных) колен. Нужно обратить внимание на то, что вследствие подогрева кромок перед сварочной дугой они будут расширяться, отходить в радиальном направлении от подкладного кольца. Это в свою очередь с большой вероятностью приведет к смещению кромок или же последующему образованию домика.
В тонкостенных сосудах, которые работают под давлением, всякое смещение кромок на стыке шва – опасный концентратор. Таким образом, при изготовлении нужно в обязательном порядке принимать меры их предотвращения или устранения. В целях прижатия кромок часто применяются наружные стяжные ленты, но их приходится размещать на определенном расстоянии от стыковой оси, к тому же перемещения лишь частично удастся предотвратить.
Более эффективным является прижатие кромок к роликовым подкладкам, которые перекатываются по поверхности стыка перед дугой сварки. Данный прижим не позволяет кромкам отрываться от поверхности подкладного кольца на месте сварного соединения. Прижимное приспособление для кромок обечаек закрепляется на консоли сварочной головки. При этом ролики для прижима опираются на обе кромки, которые свариваются между собой, во время чего происходит их прижатие к подкладному кольцу посредством пружины.
Стоит отметить, что для сварки стыка обечаек сосуда может также быть использована определенная схема, при которой стык выполняют изнутри обечайки. В данном случае участок кольцевого шва охватывается при помощи жесткого бандажа, который вращается во время сваривания вместе с изделием. Касательно сварки первого прохода, то она выполняется изнутри обечайки. Возникающие в области нагрева напряжения сжатия, стремятся увеличить длину стыковой свободной кромки, прижима ее к наружному бандажу.
Для большинства материалов деформации от кольцевого шва производят такое воздействие, благодаря которому можно наблюдать уменьшение диаметра обечайки. Подобное сокращение участка при помощи прокатки роликами отлично поддается исправлению. При сварке алюминиевых сплавов диаметр обечайки в области шва кольца может стать не только диаметром меньше, он даже получить не только равный размер, но и размер, больше первоначального.
Огромное внимание нужно уделить конструктивным особенностям, а также технологии изготовления замыкающего кольцевого шва тонкостенного сосуда. Если имеют место лозовые отверстия патрубков большого размера, в сосуд можно ввести разжимное кольцо разборного типа. При таких обстоятельствах одностороннее сваривание замыкающего шва выполняется на подкладке (съемной), руководствуясь обычной технологией. Однако подобная задача становится более сложной при малых размерах отверстий патрубков. Односторонняя сварка применяется в том случае, если подкладное кольцо – слишком резкий концентратор, использование которого крайне нежелательно.
Соединение элементов арматуры со стенкой сосуда выполняется зачастую стыковым типом, допуская соединение при помощи угловых швов. Стыковые круговые швы выполняются односторонней сваркой с канавкой на подкладке. Конструктивное оформление, а также вид сборочно-сварочной оснастки стыка определяются необходимостью качественного прижатия кромок к подкладке. Форма поверхности стены может быть сферической или цилиндрической. В зависимости от формы, толщины и материала свариваемых материалов, могут различаться конструктивно-технологические решения.
Сваривая фланец, в сосуд сферической формы из сплава алюминия АМг6 целесообразным будет использование соединения с буртиком. Технологическое предназначение буртика заключается в передаче усилия прижатия фланца на оболочку, а также обеспечении соосности, повышении кромочной жесткости фланца. Буртик позволяет упростить приспособление для прижима. Вдобавок ко всему, буртик помогает свести на нет смещение кромки во время сваривания элементов, уменьшить искажения формы оболочки. Если размер сосуда небольшой, сварку кругового шва выгоднее будет осуществлять неподвижной сварочной головкой при вращении приспособления со свариваемым зафиксированным стыком. Вваривая арматуру в узел существенных размеров, круговой шов удобнее выполнять головкой сварки, которая перемещается по элементу оболочки (его поверхности), закрепленного в неподвижном положении.
Крупносерийное производство тонкостенных сосудов, работающих под высоким давлением, применяют для сборочно-сварочных операций специализированные полуавтоматические установки. Для сборки и сваривания продольного стыка обечайки в них нужно выполнят определеннее операции: ориентирование стыка, приемку обечайки, прижатие стыка к подкладке в симметрическом положении по отношению к формирующей проплав канавке, выполнение шва, а также освобождение обечайки. Пожалуй, самой сложной процедурой для автоматизации сегодня является ориентирование. В том случае, когда ориентирование выполняется рабочим, установка в значительной мере упрощается, что служит причиной от применения автоматизированных устройств.
Дата добавления: 2019-09-02; просмотров: 973; Мы поможем в написании вашей работы! |
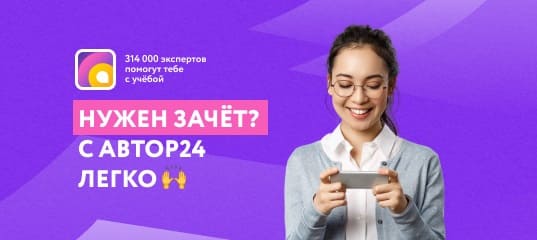
Мы поможем в написании ваших работ!