ОПРЕДЕЛЕНИЕ ПРОГРАМЫ УЧАСТКА, ВЫБОР МЕТОДА РЕМОНТА, РАСЧЕТ ПАРАМЕТРОВ ПРОИЗВОДСТВЕННОГО ПРОЦЕССА
ВВЕДЕНИЕ
Важную роль в развитии экономики играет железнодорожный транспорт. От четкой, слаженной работы его во многом зависит эффективность общественного производства. Повышение эффективности работы железнодорожного транспорта требует улучшения использования транспортных средств, увеличения мощности предприятий по ремонту подвижного состава и производству запасных частей. Перед железнодорожным транспортом стоит задача - предотвратить потерю грузов. Одно из видных мест в обеспечении перевозочного процесса принадлежит вагонному хозяйству. Назначение вагонного хозяйства заключается в обеспечении железной дороги исправным вагонным парком, удовлетворяющим требованиям безопасности движения, сохранности перевозимых грузов, а также в создании удобств при перемещении пассажиров. Отсюда вытекают и его главные задачи, которые сводятся к поддержанию высокого уровня работоспособности грузовых и пассажирских вагонов в условиях непрерывного роста интенсивности их использования, выполнению установленного плана ремонта вагонов, экономическому использованию имеющихся технологических средств достижению наибольшей эффективности работы ремонтно-эксплуатационных предприятий и их подразделений. В вагонном хозяйстве постоянно увеличивается доля специализированного подвижного состава. Применение вагонов - хопперов для перевозки зерна, минералов, цемента, окатышей и других грузов позволяет в 3-4 раза повысить производительность труда на грузовых операциях, в 1,5-2 раза сократить эксплуатационные расходы. Вагонный парк пополняется также специализированными вагонами для перевозки гранулированных полимерных материалов с резервуарами из алюминиевого сплава, цистернами для перевозки цемента, разгружаемыми с использованием сжатого воздуха, платформами для перевозки большегрузных контейнеров, спецвагонами для перевозки тонковолокнистой стали в рулонах и другие. Для увеличения провозной способности железных дорог при ограниченных нагрузках от оси колесной пары на рельс значительно возрос выпуск восьмиосных вагонов. Переводят все грузовые вагоны на роликовые подшипники, что позволяет повысить их надежность и удлинить участки следования поездов без ТО до 500-600 км.
|
|
Целью данного курсового проекта является организация работы вагоносборочного участка по ремонту четырехосных цистерн.
ХАРАКТЕРИСТИКА ПРОЕКТИРОМОГО УЧАСТКА (ПРЕДПРИЯТИЯ)
Вцелях обеспечения безопасности движения, сохранности перевозимых грузов и поддержания цистерн в исправном состоянии, они ежегодно подвергаются деповскому ремонту. Для выполнения ремонтных работ депо имеет следующие участки и отделения:
|
|
• цех подготовки цистерн к ремонту;
• вагоносборочный участок;
• колесный цех; механический; автоконтрольный;
• контрольный пункт автосцепки;
• инструментальный;
• деревообделочный;
• отделение по сливным и предохранительным клапанам;
• отделение по комплектовке буксового узла.
Вагоносборочный участок является основным участком депо и служит для выполнения ремонтных работ. Участок имеет следующие отделения:
1 Отделение разработки и подготовки вагонов к ремонту
Служит для выполнения разборочных и ремонтно-правильных работ по раме, элемента кузова.
2 Ремонтное отделение
Для производства работ на путях организуются ремонтные отделения, позиции, которые оснащаются подъемными площадками для слесарных и столярных работ; приспособления для снятия и постановки поглощающих аппаратов автосцепки; различные стеллажи, стенды, а также оснащаются электрогаикотвертами, электрическими и пневматическими инструментами, рабочее место оборудуется различными колонками сжатого воздуха, электролинией для питания электросварочных аппаратов и электрического инструмента, водопроводом и горячим водоснабжением. Передвижение с позиции на позицию осуществляется при помощи конвейера с
|
|
автоматическим управлением, для подъема вагона и перемещения тяжелых деталей на участке имеются 2 мостовых крана грузоподъемностью 10 тонн.
3 Сборочное отделение
Организуются ремонтные позиции, которые оснащены необходимым оборудованием и инструментом.
4 Малярное отделение
Служит для окраски вагонов и последующей их сушки. Для облегчения и ускорения процесса и облегчения труда маляров, в депо широко используется механизированный способ окраски и сушки с применением установок «Радуга-0-63», «УЗРЦ-4» и других.
ОПРЕДЕЛЕНИЕ ПРОГРАМЫ УЧАСТКА, ВЫБОР МЕТОДА РЕМОНТА, РАСЧЕТ ПАРАМЕТРОВ ПРОИЗВОДСТВЕННОГО ПРОЦЕССА
Расчет производственной программы
Производственная программа вагоносоорочного участка равна годовой программе ремонтного депо, согласно задания составляется 6500 четырехосных цистерн.
Метод ремонта
При организации ремонта цистерн предусматривается обезличенный способ ремонта, т. е. путем замены неисправных узлов и деталей заранее отремонтированными деталями и узлами. Простой цистерн должен быть не более установленных норм при ритмичной работе производственной процесса. При этом исходим из следующих норм и мер:
|
|
1. Создание запаса вагонных деталей.
2. Организация ремонта цистерн на основе графиков планирования и управления технологического процесса.
3. Автоматизация и механизация всех трудоемких работ путем применения
автоматических линий и механизированных комплексов обеспечивающих
повышение производительности труда при высоком качестве выпускаемой
продукции.
4. Рациональная организация рабочих мест, обеспечивающих высокую
производительность труда при строгом соблюдении техники безопасности.
5. Применение поточно-конвейерного метода ремонта цистерн. На каждом рабочем месте позиции, расположенными на поточной линии, выполняются определенные операции.
позициям сборочного участка производится с помощью конвейера через определенные промежутки времени.
Режим работы и фонд времени
Режим работы вагоносборочного участка двухсменный при пятидневной рабочей недели с часовым перерывом, продолжительностью одной смены восемь часов. Работа участков по ремонту цистерн организуется в две смены:
Первая смена с 7-00 до 16-00
перерыв с 11-00 до 12-00
Вторая смена с 16-00 до 00-30
перерыв с 19-00 до 19-30
Фонд рабочего времени одного работающего определяем по формуле:
F = [(Дк - Дп) tc - Дп(tс - In)] (1)
Где: Дк- количество календарных дней в году ;
Дп- количество праздничных и выходных дней в году;
tc - продолжительность рабочей смены;
In - количество предпраздничных дней в году с сокращенной продолжительностью рабочей смены;
tn - продолжительность смены в предпраздничные дни.
F = [(365 - 116) • 8 - 5 • (8 - 7) = 1987 ч.
Фонд времени работы оборудования - это количество часов его работы в течение определенного периода (год, квартал, месяц).
Различают номинальный и действительный годовой фонд времени работы оборудования.
Номинальный фонд времени работы оборудования определяется по формуле:
FH = [(Дк – Дn)tc – Пn(tc – tn)]Мсм (2)
Где: Дк - количество календарных дней в году;
Дп - количество праздничных и выходных дней в году;
Пп - количество предпраздничных дней в году с сокращенной продолжительностью рабочей смены;
tc - продолжительность рабочей смены, ч;
tn- продолжительность смены в предпраздничные дни, ч;
Мсм - количество смен,
FH = [(365 - 116)8-5(8-7)]2= 3974 ч.
Действительный фонд времени работы оборудования определяется по формуле:
FД = Fn .Ур (3)
Где: Ур - коэффициент, учитывающий простой оборудования по техническим неисправностям и в ремонте, принимаетсяравным 0,95 -0,98.
Fд = 3974 · 0,95 = 3775 ч
Расчет параметров производственного процесса
Основными параметрами производственного процесса ремонта вагонов является ритм, такт выпуска, длительность производственного процесса и фронт ремонта.
В соответствии с (ГОСТ 3.11.09 - 83) Ритмом выпуска называется количество вагонов, выпускаемых из ремонта.
Находим ритм выпуска вагонов и ремонта:
г = N / F (4)
г= 6500 /3851= 2 вагона в час
N - годовая программа
FД - действительный годовой фонд времени работы оборудования. Фронт работы - это количество одновременно ремонтируемых вагонов. Рассчитываем по формуле:
ФР= r • tв (5)
Где: tв - время простоя вагона в ремонте.
Фр = 2 • 6 = 12 вагонов
Количество поточных линий, необходимых для освоения заданной программы, определяем исходя из того, что ремонт цистерн осуществляется на 6-позициях, из которых:
1) разборочно-правильная - одна
2) четыре ремонтно-сборочные
3) одна для малярных работ.
На каждую позицию устанавливается по одному вагону, тогда количество поточных линий будет равно:
Пр = Фр/с·пв (6)
Где: Фр- фронт работ
с – количество ремонтных позиций
пв – количество вагонов на одной позиции
Фронт каждой поточной линии:
П=12/6●1=2 линии
Фрл = с • пв (7)
Фрл =6•1 = 6 вагонов.
Такт выпуска - это интервал времени, через который производится выпуск вагонов из ремонта:
τ=F2/N (8)
τ =3851/6500=0,6•60=36мин.
Корректируем такт ремонта:
τ = 36 мин • 2 = 72мин.
ТЕХНОЛОГИЧЕСКИЙ ПРОЦЕСС
Ремонт цистерн осуществляется поточно-конвейерным методом на двух поточно-конвейерных линиях на 6-ти ремонтных позициях по одному вагону на одной ремонтной позиций. Простой цистерн в ремонт составлен. Перед тем как цистерны попадают в сборочный участок, они проходят промывочно-пропарочный пункт. После чего цистерны осматриваются старшим мастером с целью определения объема ремонта и составления дефектной ведомости - наряд на ремонт цистерн. После того как цистерна была промыта и пропарена, ее закатывают на I позицию вагоносборочного участка, на этой позиции выявляют неисправности и определяют объем ремонта. Слесаря-автоматчики разъединяют рычажную передачу. Для слесаря по ремонту вагонов производят подъем цистерны с помощью 4-х стационарных электро-домкратов. После поднятия цистерны, слесаря-ремонтники выкатывают тележки при помощи конвейера для выкатки тележек. Далее слесаря-ремонтники снимают автосцепку и поглощающие аппараты, предохранительные впускные клапаны, разбирают сливной прибор. Параллельно с ними слесаря-тормозники снимают тормозное оборудование. После этого подают технологические тележки под цистерну и ставят ее на них. Все неисправные детали направляются в соответствующие отделения, а на их-место ставят новые или заранее отремонтированные. Оператор перемещает цистерну на П позицию с помощью конвейера.
На П позиции слесаря-ремонтники подготавливают поверхность рамы и котла к сварочным работам. При ремонте котлов сваркой большое внимание уделяется подготовке дефектного места и выполнению самой сварки. Подготовка заключается в тщательной очистке места сварки от ржавчины, краски и в разделке шва для обеспечения провара всей толщины листов. Ремонтируют крышки люков, лестницы, хомуты, болты. По окончании этих работ цистерну оператор подает на III позицию.
На IIIпозиции сварщики проводят сварочно-наплавочные работы. Им разрешается на котлах заварка трещин 1 и 3 в сварных швах и в основном
металле с постановкой усиливающих накладок в местах пробоин
двусторонними швами. Размер накладок должен быть не свыше 0,1 м , а сами накладки должны перекрывать кромки пробоин не менее, чем на 40-50 мм.
Трещины в основном металле и стыковых швах заваривают двусторонним швом, а в нахлесточных швах вырубают с обеих сторон и заваривают.
Расстояние между соседними параллельными сварными швами должно быть не менее 150 мм; вварка части днища или ленты в обечайку должна производиться двусторонним стыковым швом.
Не допускается полностью или частично накрывать одну накладку другой, а также приваривать накладки односторонними швами. Углы накладок должны быть закруглены. Расстояние между расположенными параллельно сварными швами соседних накладок или между швами накладок и котла должно быть не менее 150 мм. При меньшем расстоянии должны быть срублены старые накладки и поставлена общая новая. Далее оператор перемещает цистерну на IV позицию.
На IV позиции слесаря ставят сливной прибор, предохранительно-впускной клапан, автосцепку и поглощающие аппараты. Слесаря производят подъемку цистерны, выкатывают технологические тележки и подкатывают отремонтированные. Технологические тележки мостовым краном переносят на спецтележки. Далее слесаря испытывают котел на герметичность.
Котлы испытывают на герметичность: после деповского ремонта -воздухом под давлением 0,05 MПa с обмыливанием при этом всех сварных швов и мест, где может образоваться течь; после заводского -гидравлическим давлением цистерн для перевозки нефтепродуктов 0,2 МПа, для перевозки кислот 0,25 МПа. Испытание длится не менее 15 мин.
Для проверки исправности всех частей универсального сливного прибора
цистерна в течение 10 мин. находится под давлением с открытой нижней частью (заглушкой) сливного прибора и 5 мин. с частично открытым клапаном при закрытой заглушке. У выпускаемых из заводского ремонта цистерн проверяют соответствия нанесенного на котле калиброванного знака фактическому объему котла. Далее оператор перемещает цистерну на V позицию.
На V позиции слесаря по ремонту тормозов ставят на место тормозное оборудование, регулируют рычажную передачу, испытывают тормоза сжатым воздухом. Оператор перемещает цистерну на VI позицию.
На VI позиции маляры подготавливают поверхность рамы и котла под окраску, производят покраску котла и рамы с помощью краскораспылительной установки. Наносят знаки и трафареты. После ремонта приемщик проверяет качество ремонта цистерны.
РАСЧЕТ И ВЫБОР ОБОРУДОВАНИЯ
Оборудование и подъемно-транспортное средство выбирают на основании разработанного технологического процесса ремонта заданного объема с учетом рекомендаций типового технологического процесса.
Количество и тип оборудования устанавливаются исходя из затрат станкочасов на заданную программу ремонта и действительного фонда рабочего времени оборудования.
Специальное оборудование, стенды, приспособления, применяются в количестве необходимом для выполнения заданной программы. Рассчитываем потребность в электросварочных аппаратах:
Qbc = СВ•(Tcb•Nb/Fg•Кcb) (9)
Где: СВ - коэффициент, учитывающий работы, выполняемые для ТО, равный 1,4.
Тсв - суммарное время производства сварочных работ на 1 вагон.
Fg - годовой фонд, времени работы сварочного аппарата.
NB - суммарная мощность годовая программа ремонта вагонов.
Ксв - коэффициент использования сварочных аппаратов (0,95)
Qcb = 1,4 • (1 •6500 / 3813 • 0,95) = 2,4 св.
Таблица 1 Потребное оборудование
Наименование оборудования | Кол-во | Габаритные размеры | Тех. Хар-ка | Мощность двигателя, Квт | Стоимость, руб. | Общая стоимость, руб. |
Конвейер для перемещения вагонов | 2 | 20 | 101000 | 2020000 | ||
Кран мостовой | 2 | =1700 | 10т | 48,4 | 143700 | 487400 |
Малый конвеер помещения тележек | 4 | 28 | 65100 | 260400 | ||
Кран балка | 1 | =100000 | 2т | 42,4 | 20280 | 162240 |
Лебедка | 2 | 31200 | 62400 | |||
Электродомкрат | 16 | 30т | 120 | 5900 | 82600 | |
Приспособление для снятия и замены С А | 4 | 12 | 4800 | 19200 | ||
Приспособление для снятия тормозных приборов | 4 | 25,6 | 4950 | 19800 | ||
Трансформатор для сварки | 2 | 646x314 х660 | ТМ-320 320/65-10 | 78 | 12300 | 24600 |
Стенд для испытания ТОРМОЗОВ | 2 | 1 | 12,8 | 14700 | 29400 | |
Тележка для окраски УРП-5 | 2 | 12,4 | 48590 | 97180 |
Продолжение таблицы 1
Наименование оборудования | Кол-во | Габаритные размеры | Тех. Хар-ка | Мощность двигателя, Квт | Стоимость, руб. | Общая стоимость, руб. |
Механизированная тележка для СУШКИ | 2 | 300 | 207500 | 415000 | ||
Пневмогайковерт | 4 | 1400 | 5600 | |||
Электрокар | 2 | 2250x860 х1170 | экп-750 | 96225 | 192450 | |
ИТОГО | 699,6 | 3878270 |
ПЛАНИРОВКА УЧАСТКА, ОПРЕДЕЛЕНИЕ РАЗМЕРОВ
(площадь и объем цеха, участка)
Вагоносборочный участок по ремонту цистерн проектируется сквозного типа, т. е. вагоны перемещаются в одном направлении. Основные размеры участка - это длина, ширина, высота, объем, ширина между путей. Основные размеры рассчитываются из числа поточных линий, ремонтных позиций на этих линиях, размещение оборудования, рациональной планировки рабочих мест и соблюдения проходов и проездов необходимой ширины.
При определении ширины учитывается расстояние от продольных стен или колонн здания до оси крайнего пути должно быть для проектированных депо 5 м; расстояние между осями смежных путей принимается для проектирования депо 7 м.
Размеры здания вагоносборочного участка устанавливается из условия оснащения его мостовым краном грузоподъемностью 10 тонн. Она слагается из расстояния от пола до головки подкранового рельса, высота формы крана и расстояние от верхней части крана до низа конструкции перекрытия и должна составлять 10,8 м для строящихся депо и не менее 8,5 м для ремонтируемых.
Длина участка определяется по формуле:
Lву= (Фс + Фм) Lв + Ln + Lmp +Lт+ (Фс -1)L1+ 2L2 + (Фм -1) L3 +2L4 (10)
Где: Фм - количество вагонов на одном пути малярного отделения.
Фс - количество вагонов на одном пути вагоносборочного участка.
L,j - расчетная длина вагона (для 4-х осных цистерн 12,2).
Ln - длина участка пути для выкатки тележек, 10 м.
Lmp - ширина проезда для транспортировки вагонных тележек, принимается 6 м.
Li - длина интервала между двумя вагонами в сборочном отделении (2м).
L3 - длина интервала между двумя соседними вагонами в малярном отделении (принимается 4 м).
L4 - расстояние от торцовой стены малярного отделения и от перегородки тамбура до автосцепки крайних вагонов (4 м).
Lву = (5 + 1) 12,2 +10 + 6 +6 +(5 - 1) 2 + 2-4 (1 - 1) 4 + 2-4 = 120
Ширина определяется по формуле:
Ш= 2вh (11)
Ш=2•5 + 8=18 м.
Площадь определяется по формуле:
S = LШ (12)
S = 120 •18 = 2160м2
Объем определяется по формуле:
V =hlш (13)
V =10,8 • 120 • 1 8 = 23328 м2
Дата добавления: 2019-09-02; просмотров: 280; Мы поможем в написании вашей работы! |
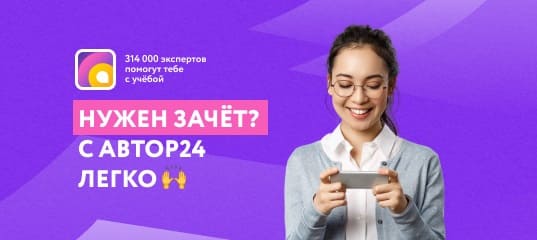
Мы поможем в написании ваших работ!