Поняття про суху перегонку деревини. Смоло - скипидарне виробництво.
Суха перегонка деревини – це розкладання деревини без доступу повітря під дією високої температури. При сухій перегонці проходять складні хімічні реакції, в процесі яких із складних речовин деревини утворюються більш прості речовини. При сухій перегонці утворюються тверді, рідкі і газоподібні продукти. Рідкі і газоподібні речовини виділяються одночасно в вигляді паро газової суміші, тверді речовини (деревне вугілля) залишаються в апараті.
Процес сухої перегонки деревини поділяється на чотири стадії: перша стадія – сушка деревини до температури 120 – 150ْ, друга стадія – початок розпаду деревини і зміна її хімічного складу при температурі 150 – 275ْ, третя стадія – утворення, випаровування і відгонка основних продуктів розкладу при температурі 275 – 450ْ, четверта стадія – прокалювання і відгонка залишків летких речовин при температурі 450 – 550ْ.
Смолоскипидарне виробництво – різновидність сухої перегонки деревини. В якості сировини служать осмоли: пневий, каровий, стовбурний, гілковий, колодний. Основною сировиною є пневий сосновий осмол. В залежності від часу, що пройшов з моменту рубання насадження, розрізняють пні: свіжі, до 5 років, пристигаючі, 5 – 10 років, стиглі, більше 10 років. Для переробки найбільш підходять пні в віці 10 – 15 років після рубання.
По вмісту каніфолі пне вий осмол ділиться на три сорти: 1 – жирний, вміст каніфолі не менше 21%, 2 – середній, вміст каніфолі від 16 до 21%, 3 – сухий, вміст каніфолі від 13 до16%. По вологості пне вий осмол також поділяється на сухий – з вмістом вологи до 20%, напівсухий – з вологістю більше 25%.Осмол заготовляють ручним і вибуховим способом, при допомозі корчувальних машин і тракторів. Вихід пневого осмолу 8 – 20м³ з1га. Існують смолоскипидарні установки двох типів: металічні реторти або цегляні печі. В лісохімічній промисловості особливо широко поширені мінські реторти і в’ятські котли. Установки типу мінська реторта будуються з однією чи двома ретортами. Установка складається з реторти обмурованої цегляним кожухом, скипидарної і смоляної конденсаційних систем і технологічного обладнання. Загрузочна ємкість реторти 20 скл.м³.
|
|
Технологічний процес проходить слідуючим чином: реторту оглядають і підготовлюють до роботи, пневий осмол очищують від грунту, гнилі і заболоні, розпилюють і розколюють на куски товщиною 10 – 12 і довжиною до 35 – 40 см. Реторту завантажують осмолом вертикальними рядами з нахилом до центру, спочатку через нижній боковий люк, закінчують через верхній люк. Обидва люки закривають кришками. Після всіх підготовчих робіт реторту розігрівають при невеликій подачі палива (на протязі 1год. роботи). Потім подачу палива збільшують і форсують нагрівання топки. З появою перших крапель води і скипидару (через 6 – 8 год.) подачу палива зменшують і ведуть її рівномірно.
|
|
Відгонка скипидару іде 48 – 50 годин при температурі 95 – 200ْ. Після чого на протязі 16 – 18 годин проходить відгонка смоли, потім випалювання вугілля. Реторта охолоджується 20 – 24 години. Повний оборот реторти 3,5 – 4 доби, за місяць проходить сім – вісім обертів. Продуктивність установки з однією ретортою складає 140 – 160 м³ осмолу в місяць. Із 1 скл. м³ осмолу в реторті отримуємо: 15 – 18 кг. скипидару, 40 – 45 кг. смоли, 60 – 65 кг. вугілля і 6 – 7 оцтово – кальцієвого порошку ( із під скипидарної води).
Деревна смола – рідина темного кольору з характерним запахом. Використовується деревна смола для просмолювання підводної частини дерев’яних суден і човнів, просочування канатів і оснастки, виготовлення змащувальних мастил, отримання вару і пеку. Вар використовується при виготовленні взуття, пек при заливці електрокабелів, акумуляторів при виготовленні пластмас.
106
Деревне вугілля використовують для виготовлення електровугільних виробів, сірководню, при виробництві кольорових металів, як паливо.
|
|
Виробництво дьогтю та деревного вугілля.
Виробництво дьогтю проводиться в процесі сухої перегонки берести або осикової кори. Дьоготь кращої якості і з великим виходом отримується із берести знятої з ростучих дерев в процесі сокоруху в насадженнях, призначених в рубку в найближчі 2 роки. Бересту знімають, не пошкоджуючи луб і камбій, із середньої частини стовбура дерев діаметром 12 см. Сировина більш низької якості – береста знята з березових дров, кряжів, гілок. З 1 га. сиро ростучого лісу можна заготовити до 2 т. берести, на лісосіці під час рубки – до 8 т.
Суху бересту підсушують і пресують в тюки. Для сухої перегонки берести використовують в основному казанні установки, що мають 2,4,6 казанів. Казан виготовляється із листової сталі (3 мм.) прямокутної форми з розмірами 1,4×0,7×0,7 м. і ємкістю 0,7 м³. В задній стінці казана, в 150 мм. від верху, робиться отвір і патрубок для виходу паро газової суміші. Передня стінка казана – кришка. Казани вмуровуються в цегляну кладку, кожен казан має окрему топку. Обігрів стінок казана проводиться топочними газами. Для охолодження паро газової суміші в установці є холодильник, для збору дьогтю – дерев’яні чани - відстійники.
|
|
Технологічний процес відгонки дьогтю розпочинається із завантаження тюка берести в казан. Потім казан закривають кришкою на глиняному розчині, замазують зверху глиною. На початку відгонки в топці розводять сильний вогонь, з появою перших крапель рідини подачу палива зменшують щоб дьоготь не пригорів. Процес відгонки дьогтю продовжується 18 – 20 год. Повний оберт казана 24 – 26 год. Дьоготь 2 – 3 доби відстоюється в чанах – відстійниках, потім через нижній кран зливається вода. Кращою тарою для зберігання дьогтю – осикові емальовані бочки ємкістю 150 – 200 л.
Дьоготь – темна, густа, масляниста речовина з густотою від 925 до 970 кг/м³, із специфічним запахом. Із 1 т. берести можна отримати 270 -300 кг. дьогтю. На перегонку 1т. берести витрачається 6 – 7 скл.м³ палива. Дьоготь використовується в шкіряній промисловості для жирування шкір, в фармацевтичній промисловості (дьогтьове мило, мазі від хвороб шкіри), для змазування взуття і збруї.
Процес вуглевипалювання оснований на термічному розкладанні деревини, мета процесу – отримання деревного вугілля. Вугілля випалюють в печах, печі бувають пересувні і стаціонарні. Стаціонарні печі поділяються на печі періодичної і безперервної дії.
Вуглевипалювальна установка має три камери, одна з них для сушіння дров, дві для піролізу. Дрова завантажують в металічних контейнерах – решітках, що вміщають 8,5 м³ дров. В кожну камеру поміщається 10 контейнерів. Стіни камери залізобетонні, підлога із бетону. Плити даху зйомні, залізобетонні. Підйом і встановлення плит, завантаження контейнерів з деревиною і вивантаження готового деревного вугілля виконується консольно – козловим краном. Сушіння дров в сушильній камері і обвуглювання деревини в камерах проходить гарячими топочними газами. Камери обладнані системою підвідних і відвідних каналів. Середній оборот однієї камери вуглевипалювання 5 діб. Продуктивність установки по переробці березової деревини близько 12000 м³ (вихід вугілля хорошої якості 10700 м³) в рік.
Теплова здатність деревного вугілля в залежності від вмісту в ньому вуглецю складає 5,9 – 7,8 ккал. Деревне вугілля використовується в процесі виплавки металів із руд, в ковальській справі, в виробництві сірководню, чорного пороху, активованого вугілля, в медицині, сільському господарстві, в цукровій, виноробній і інших галузях промисловості.
Дата добавления: 2019-07-15; просмотров: 271; Мы поможем в написании вашей работы! |
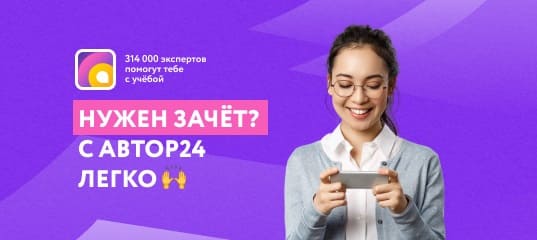
Мы поможем в написании ваших работ!