Специальные магниевые сплавы: с особыми физическими свойствами.
Магниевые сплавы широко применяют в авиастроении, ракетной технике, при изготовлении различных транспортных машин, так как при малой объемной массе они имеют высокую удельную прочность, что позволяет снизить массу двигателей и агрегатов и других узлов машин. Ценным свойством магниевых сплавов является то, что они хорошо поглощают механические вибрации. Большая группа сплавов разработана на основе системы Mg— Al— Zn с добавками марганца. сплавы на основе магния разделяются на литейные и деформируемые. Из литейных магниевых сплавов изготовляют литые детали, из деформируемых — прессованные и катаные полуфабрикаты, поковки и штамповки. Магниевые сплавы являются самым легким конструкционным металлич. материалом. Уд. вес их в зависимости от состава находится в пределах 1,76—2,0 г/см3, примерно в 4 раза меньше стали ив 1,5 раза меньше алюминия и его сплавов. Использование М. с. позволяет уменьшить вес и значительно повысить жесткость конструкций. Литейные М. с. по уд. прочности при комнатной темп-ре превосходят алюминиевые литейные сплавы, высокопрочные чугуны и нек-рые марки сталей. Магниевые сплавы отлично обрабатываются режущим инструментом, вдвое быстрее, чем алюминий и в десять раз быстрее, чем углеродистые стали. Однако при работе с магниевыми сплавами необходимо соблюдать правила противопожарной безопасности. Недостаток магниевых сплавов — пониженная коррозион. стойкость по сравнению с алюминиевыми сплавами
|
|
23.Кристаллическое строение; основные свойства и назначение титана. Технология производства; основные примеси и маркировка титана Классификация титановых сплавов. Принципы их легирования. Маркировка. ГОСТ . Тi- лёгкий металл серебристо-белого цвета. Существует в двух кристаллических модификациях: α-Ti с гексагональной плотноупакованной решёткой, β-Ti с кубической объёмно-центрированной упаковкой, температура полиморфного превращения α↔β 883 °C. Температура плавления 1660±20 °C. Tитан имеет твердость по Бринеллю 175 МпаПо плотности и удельной теплоемкости титан занимает промежуточное место между двумя основными конструкционными металлами: алюминием и железом.механическая прочность примерно вдвое больше, чем чистого железа, и почти в шесть раз выше, чем алюминия. Но титан может активно поглощать кислород, азот и водород, которые резко снижают пластические свойства металла. С углеродом титан образует тугоплавкие карбиды, обладающие высокой твердостью. обладает низкой теплопроводностью, которая в 13 раз меньше теплопроводности алюминия и в 4 раза - железа.пожароопасен,активно ввзаим с кислародом,водородом и тд. Основная часть титана расходуется на нужды авиационной и ракетной техникии и морского судостроения. исходным материалом для производства титана и его соединений служит диоксид титана со сравнительно небольшим количеством примесей. чаще применяют так называемый синтетический рутил или титановыйшлак, получаемые при переработке ильменитовых концентратов. Для получения титанового шлака ильменитовый концентрат восстанавливают в электродуговой печи, при этом железо отделяется в металлическую фазу (чугун), а не восстановленные оксиды титана и примесей образуют шлаковую фазу. Богатый шлак перерабатывают хлоридным или сернокислотным способом
|
|
Концентрат титановых руд подвергают сернокислотной или пирометаллургической переработке. Продукт сернокислотной обработки — порошок диоксида титана TiO2. Пирометаллургическим методом руду спекают с коксом и обрабатывают хлором, получая пары тетрахлорида титана TiCl4:
Образующиеся пары TiCl4 при 850 °C восстанавливают магнием: классификация титановых сплавов основана на структуре, которая формируется при отжиге по промышленным режимам. Она включает:
1.a-сплавы, структура которых представлена a -фазой.
|
|
2. Псевдо-a-сплавы, структура которых представлена a - фазой и небольшим количеством b -фазы (не более 5%) или интерметаллидов.
3. (a+b) -сплавы, структура которых представлена a - и b -фазами; сплавы этого типа также могут содержать интерметаллиды.4. Псевдо-b-сплавы со структурой в отожженном состоянии, представленной a -фазой и большим количеством b -фазы; в этих сплавах закалкой или нормализацией из b -области можно легко получить однофазную b -структуру.5. b-сплавы, структура которых представлена термически стабильной b -фазой.6. Сплавы на основе интерметаллидов.Среди наиболее популярных титановых сплавов, стоит отметить следующие металлы с соответствующей маркировкой:
ВТ5 и ВТ5-1 – свариваемый сплав с содержанием алюминия 4%-6%;ОТ4, ОТ4-0 и ОТ4-1 – алюминиево-магниевый титановый сплав, отличающийся отличной свариваемостью;
ВТ18, ВТ20 – жаростойкие сплавы с повышенным содержанием алюминия до 8%;
ВТ22 – безалюминиевый титановый сплав, легированный ванадием (около5%) и молибденом (около 5%);ВТ8, ВТ9 – термостойкие алюминиевые титановые сплавы с содержанием алюминия в промежутке от 4,5% до 7%;ВТ6, ВТ6С – алюминиевые сплавы с включением ванадия (3,5%-6%);
ВТ15 – один из самых прогрессивных титановых сплавов, в состав которого входит хром (около10%), молибден (7%-8%) и алюминий (около3,5%).Почти все ти сплавы легируют алюминием т.к лн доступен и дешев,повышает прочность,жаропрочность и сопр ползучести,снижается склонность к водородной хрупкости. Элементы, эквивалентные алюминию, упрочняют титановые сплавы в основном в результате растворного упрочнения, а β-стабилизаторы – из-за увеличения количества более прочной β-фазы.
|
|
24.Методы упрочнения титановых сплавов . Термическая и химике термическая обработка титановых сплавов . метод газового азотирования титановых сплавов приводит к получению на поверхности нитридов титана высокой твердости и износостойкости. Процесс проводят в основном при 700…900°С в аммиачной среде.способ модификации поверхности изделий из титановых сплавов включающий электроискровое легирование поверхностного слоя и последующее оксидирование или азотирование. Электроискровое легирование проводят нитридообразующими элементами или сплавами на их основе. Затем осуществляют термическое оксидирование в окислительной воздушной среде при температуре 600…800°С в течение 2-16 часов или диффузионное азотирование, которое проводят в каталитически приготовленных газовых аммиачных средах при температуре 500…680°С в течение 15-40 часов.Наиболее близким техническим решением является способ поверхностной обработки изделий из титана и титановых сплавов ,включающий термообработку при 950°С в активной газовой среде, состоящей из 10% (мас.) азота и 90% (мас.) аргона, и последующее частичное удаление газонасыщенного слоя травлением. Время нагрева 7200 с, толщина упрочненного слоя до 35 мкм.
Титан и α-сплавы титана не упрочняются термической обработкой, и их подвергают только рекристаллизациоиному отжигу. Температура отжига α + β-сплавов должна быть выше температуры рекристаллизации, но не превышать температуры превращения α + β → β, так как и в β-области происходит сильный рост зерна. Отжиг при температурах, соответствующих β-области, мало влияет на σв и σ0,2, но сильно снижает δ и ψ. Вязкость разрушения К1с возрастает при повышении температуры обработки в α + β-области при сохранении высоких значении δ и ψ. Для обеспечения высокой конструктивной прочности следует применять отжиг на 20–30 °С ниже температуры α + β → β-превращення (псевдо β-отжиг). Для снятия внутренних напряжений, возникающих при механической обработке α- и α + β-сплавов, применяют неполный отжиг при 550–600 °С; α + β-сплавы могут быть упрочнены закалкой с последующим старением.
Применяют: 1. Простой отжиг(дорекристаллизационный.Т нагрева ниже Т рекр) нагрев до наименьших Т,обеспечивающих полное разупрочнение,затем охлаждение по заданному режиму 2.изотермический отжиг(для повышения жаропрочности и пластичности. Т нагрева будет немного ниже Ас3,пройдет полигонизация и рекристаллизация, затем остуживание до Т,ниже начала рекр-ции и изотермическая выдержка при данной Т. 3. Двойной отжиг(Т нагрева ниже Ас3) полигонизация и рекрист затем охл до комн Т. Второй нагрев до Т меньше т-ры начала рекр.
В процессе старения закаленных сплавов происходит их упрочнение, обусловленное распадом α″-фазы и остаточной β-фазы. Повышение прочности при распаде α″-фазы невелико. Упрочнение, связанное с образованием ω-фазы, использовать нельзя из-за возникновения высокой хрупкости сплавов. Чтобы избежать хрупкости, связанной с образованием ω-фазы, применяют более высокую температуру старения: 450–600 °С.
25.Конструкционные титановые сплавы: высокопластичные: средней прочности: высокопрочные термически упрочняемые; жаропрочные. Титановые сплавы имеют высокую удельную прочность σв/γ, жаропрочность, значительную коррозионную стойкость во многих агрессивных средах. Для повышения прочности сплавы легируют марганцем, железом, алюминием, молибденом, хромом, ванадием и др. элементами. По структуре титановые сплавы подразделяют на α-сплавы, псевдо α-сплавы, α+β-сплавы, псевдо β-сплавы и β-сплавы.
По механическим характеристикам различают сплавы высокопластичные - малопрочные, средней прочности, высокопрочные, для эксплуатации при низких температурах и литейные.
К высокопластичным относятся сплавы марок ОТ4-0, ОТ4-1 и АТ-2 с пределом прочности на растяжение до 70 кгс/мм2, деформируемые в холодном состоянии. У сплавов средней прочности (марки ОТ4, АТ-3, 4201, НТ-50, ВТ5, ВТ5-1, ВТ6С, ВТ4, АТ-4, ТС5, ВТ20 и ОТ4-2) предел прочности на растяжение 75-100 кгс/мм2. Они хорошо свариваются и отличаются удовлетворительной термической стабильностью. Высокопрочные титановые сплавы - термически упрочняемые (марки ВТ6, АТ-6, ВТ3-1, ВТ14, ВТ16, ВТ22, ВТ25, ВТ15 и ТС6). Высокая прочность (180-200 кгс/мм2) достигается не только легированием, но и дисперсным упрочнением при закалке и старении. Высокопрочные сплавы отличаются высокой жаростойкостью и жаропрочностью до температуры 4000С. Сплав ВТ22 обладает высокой прочностью в отожженном состоянии. Используется для изготовления крупногабаритных изделий. Поставляется в виде проката, поковок и штамповок. В последнее время получают широкое распространение β-титановые сплавы. Они обладают высокой технологической пластичностью в закаленном состоянии, что обеспечивает им хорошую обрабатываемость давлением. Типичным представителем β-титановых сплавов является сплав ВТ15.
26. Современные конструкционные титановые сплавы с интерметаллидным упрочнением и с эффектом запоминания формы; «пожаробезопасные» эвтектоидного типа. В последние годы большое внимание уделяется титановым сплавам, содержащим в своей структуре большее или меньшее количество химического соединения различного типа. В настоящее время имеется несколько направлений создания н использования сплавов со специальными свойствами, представляющими интерес для современного машиностроения.К ним следует отнести жаропрочные сплавы на основе алюминидов титана Т13А1 и Т1А1 сплавы на основе никелида титана с эффектом запоминания формы, имеющие достаточно высокие характеристики пластичности ; сплавы эвтектического типа, рекомендуемые как «пожаробезопасные» для изготовления дисков, лопаток и корпусов самолетных двигателей . Структура «пожаробезопасных» сплавов состоит в значительной мере из эвтектоида. который имеет низкую температуру плавления и предотвращает перегрев деталей и конструкций, способный вызвать загорание металла в экстремальной ситуации. В качестве низкоплавких эвтектоидообразующих элементов используют Сu. Fe н др. Для повышения прочности и жаропрочности эти сплавы дополнительно легируют Аl Sn. Zr. Мо. V и др. К таким материалам относятся, например, сплавы Ti-35% V-50% Сr. которые используются как «пожаробезопасные» в литом состоянии.Титановые сплавы с интерметаллидным типом упрочнения, структура которых гетерогенизирована химическими соединениями или представляющая собой исключительно химические соединения, должны иметь более высокие свойства, чем традиционные титановые сплавы на основе твердых растворов.Следует считать, что развитие жаропрочных и высокопрочных титановых сплавов будет осуществляться именно в этом направлении.
27. Принципы создания легких конструкционных сплавов. Базовые элементы и их механические свойства. Системы легирования. Основные группы легких и ультралегких сплавов. Маркировка. Их свойства и области применения. конструкционные сплавы на основе алюминия, магния, титана, бериллия. Л. с. характеризуются более высокой удельной прочностью (отношение показателей прочности к плотности материала), чем, например, конструкционные сплавы на основе железа или никеля. Так, при одинаковом пределе прочности (Лёгкие сплавы450 Мн /м3)Дуралюминвтрое легче котельной стали, т. е. его удельная прочность примерно в 3 раза выше. Л. с. широко применяются в самолётостроении, ракетостроении, судостроении, транспортном машиностроении, приборостроении, химическом аппаратостроении, автомобилестроении, электротехнике, строительстве, ядерной энергетике, а также для производства бытовых изделий.
легирующие элементы для титановых сплавов подразделяются на три группы: α-стабилизаторы, повышающие Тпп (Al, С, N); β-стабилизаторы, понижающиеТпп(эвтектоидообразующие: Cr, Mn, Те, Со, Ni, Cu, Si и ризоморфные: V, Nb, Та, Mo, W); По фазовому составу титановые сплавыклассифицируются на α-, псевдо α-, α + β, псевдо β, β-сплавы и сплавы на основе интерметаллидов. Основными легирующимиэлементами легких алюимн сплавов являются: медь (4,5 % массы), магний (1,6 %) и марганец (0,7 %). В качестве других легирующих добавок в магниевых сплавах используются Cd, Sn, Cu, Ni, Ag, In, La, Gd и другие РЗММаркировка магниевых сплавов состоит из буквы, обозначающей соответственно сплав (М), и буквы, указывающей способ технологии переработки (А – для деформируемых, Л – для литейных), а также цифры, обозначающей порядковый номер сплава. Сплавы нормальной прочности. К ним относятся сплавы системы Алюминий + Медь + Магний (дуралюмины), которые маркируются буквой Д. Дюралюмины (Д1, Д16, Д18) характеризуются высокой прочностью, достаточной твердостью и вязкостью. Для упрочнения сплавов применяют закалку с последующим охлаждением в воде. Закаленные дуралюмины подвергаются старению, что способствует увеличению их коррозионной стойкости.Маркируются титановые сплавы в зависимости от того кто занимается разработкой.Маркировка титановых сплавов разнообразна.( ВТ3, ВТ4, ВТ5 (ВТ5Л, ВТ14Л))
28. Композиционные материалы с металлической матрицей. Методы их производства и назначение. Композиты с металлической матрицей – композиты ,матрицей в которых является металл или металлический сплав. Упрочнителями служат волокна бора, углеродные волокна, нитевидные кристаллы тугоплавких соединений , вольфрамовая или стальная проволока. Матричный материал выбирают из учета назначения композиционного материала (коррозионная стойкость, сопротивление окислению и др.). В качестве матриц используют легкие и пластичные металлы, алюминий, магний и их сплавы. Количество упрочнителя составляет по объему 30-50%. По характеру структуры композиционные материалы подразделяются на волокнистые, упрочненные непрерывными волокнами и нитевидными кристаллами, дисперстноупрочненнные материалы, полученные путем введения в металлическую матрицу дисперсных частиц упрочнителей, слоистые материалы, созданные путем прессования или прокатки разнородных материалов. К композиционным материалам также относятся сплавы с направленной кристаллизацией эвтектических структур. Комбинируя объемное содержание, можно, в зависимости от назначения, получать материалы с требуемыми значениями прочности, жаропрочности, модуля упругости, абразивной стойкости, а также создавать композиции с необходимыми магнитными, диэлектрическими, радиопоглощающими и другими специальными свойствами.Важнейшими технологическими методами изготовления композиционных материалов являются: пропитка армирующих волокон матричным материалом; формирование в пресс-форме лент упрочнителя и матрицы, получаемых намоткой; холодное прессование обоих компонентов с последующим спеканием; электрохимическое нанесение покрытий на волокна с последующим прессованием; осаждение матрицы плазменным напылением на упрочнитель с последующим обжатием; пакетная диффузионная сварка монослойных лент компонентов; совместная прокатка армирующих элементов с матрицей и др. Композиционные материалы широко используют в качестве конструкционных, теплозащитных, режущих, износостойких, электротехнических и других материалов в строительстве, машиностроении, атомной и металлургической промышленности. Металлы, армированные волокнами, применяются в авиационной и ракетной технике.
29. Дисперсно-упрочненные (порошковые) композиционные материалы на основе алюминия, магния, никеля, кобальта, хрома. При дисперсном упрочнении частицы блокируют процессы скольжения в матрице. Эффективность упрочнения при условии минимального взаимодействия с матрицей зависит от вида частиц, их объемной концентрации, а также от равномерности распределения в матрице. Применяют дисперсные частицы тугоплавких фаз типа Аl2О3, SiO2, BN, SiC, имеющие малую плотность и высокий модуль упругости. КМ обычно получают методом порошковой металлургии, важным преимуществом которого является изотропность свойств в различных направлениях.В промышленности обычно применяют дисперсноупрочненные КМ на алюминиевой и реже на никелевой основах. Характерными представителями этого вида композиционных материалов являются материалы типа САП (спеченная алюминиевая пудра), которые состоят из алюминиевой матрицы, упрочненной дисперсными частицами оксида алюминия. Алюминиевый порошок получают распылением расплавленного металла с последующим измельчением в шаровых мельницах до размера около 1 мкм в присутствии кислорода. С увеличением длительности помола пудра становится мельче и в ней повышается содержание оксида алюминия. Дальнейшая технология производства изделий и полуфабрикатов из САП включает холодное прессование, предварительное спекание, горячее прессование, прокатку или выдавливание спеченной алюминиевой заготовки в форме готовых изделий, которые можно подвергать дополнительной термической обработке.Сплавы типа САП удовлетворительно деформируются в горячем состоянии, а сплавы с 6 – 9 % Аl2О3 – и при комнатной температуре. Из них холодным волочением можно получить фольгу толщиной до 0,03 мм. Эти материалы хорошо обрабатываются резанием и обладают высокой коррозионной стойкостью.Марки САП, применяемые в странах СНГ, содержат 6 – 23 % Аl2О3. Различают САП-1 с содержанием 6 – 9, САП-2 с 9 – 13, САП-3 с 13 – 18 % Аl2О3. С увеличением объемной концентрации оксида алюминия возрастает прочность композиционных материалов. При комнатной температуре характеристики прочности САП-1 следующие: = 280 МПа, 0,2 = 220 МПа. САП-3 при той же температуре имеет = 420 МПа, 0,2 = 340 МПа.Материалы типа САП обладают высокой жаропрочностью и превосходят все деформируемые алюминиевые сплавы. Даже при температуре 500оС они имеют не менее 60 – 110 МПа. Жаропрочность объясняется тормозящим действием дисперсных частиц на процесс рекристаллизации. Характеристики прочности сплавов типа САП весьма стабильны. Испытания длительной прочности сплавов типа САП-3 в течение 2 лет практически не повлияли на уровень свойств как при комнатной температуре, так и при нагреве до 500°С. При 400°С прочность САП в 5 раз выше прочности стареющих алюминиевых сплавов.
Сплавы типа САП применяют в авиационной технике для изготовления деталей с высокой удельной прочностью и коррозионной стойкостью, рабо-тающих при температурах до 300 – 500°С. Из них изготавливают штоки поршней, лопатки компрессоров, оболочки тепловыделяющих элементов и трубы теплообменников. Принято считать, что упрочнение дисперсными частицами или дисперсионное упрочнение имеет наибольшее значение для цветных металлов, в частности для дуралюминов, сплавов на основе кобальта, никеля, меди. Однако в последние годы разработаны новые сплавы на основе железа, прочность которых в значительной мере определяется дисперсионным твердением. Широкое применение нашли микролегированные конструкционные стали и мартенситно-стареющие стали. Микролегированные конструкционные стали содержат небольшие количества Ti, V, Zr, Nb, которые образуют с углеродом и азотом твердые дисперсные частицы карбонитридов. Растворенный в железе алюминий образует с азотом твердые частицы A1N.Состав мартенситно-стареющих сталей подобран таким образом, что при старении в безуглеродистой мартенситной матрице образуются твердые интерметаллидные соединения типа Ni3Ti, FeAl и др., способствующие упрочнению.Частицы дисперсной фазы действуют как препятствия движению дислокаций в кристаллической решетке. Различают два вида выделений. К первому относятся мелкодисперсные выделения, сохраняющие связь с матрицей (когерентные или частично когерентные частицы), которые перерезаются дислокациями (перерезаемые частицы). Для движения дислокаций в этом случае требуется дополнительное усилие, необходимое для прохода сквозь области с разной энергией дефектов упаковки.Потеря когерентности и идеального сопряжения решеток матрицы и выделения приводит к изменению характера движения дислокаций. Некогерентные выделения образуются на более поздних стадиях распада твердого раствора, они обычно крупнее когерентных и характеризуются большей жесткостью и большими расстояниями между собой, значительно превышающими их диаметр. Дислокации под действием приложенного напряжения выгибаются между частицами и проходят дальше, оставляя кольца дислокаций вокруг частиц.Наибольшее упрочнение при сохранении вязкости, пластичности и конструктивной прочности достигается при условии достаточно высокой дисперсности частиц и их некогерентности с матрицей. Обычно модуль сдвига частиц более чем в 2 раза больше модуля сдвига матрицы. Дислокации не перерезают и не деформируют частицы, а огибают некогерентные выделения с увеличением уровня напряжения. Чем меньше расстояние между дисперсными частицами, тем выше упрочнение.Механизм упрочнения феррито-перлитых сталей также обусловлен тем, что деформация начинается в феррите, а перлитные колонии препятствуют движению дислокаций. Чем больше перлитной составляющей, чем выше ее дисперсность и меньше расстояние между отдельными пластинками цементита, тем выше степень упрочнения. Однако, увеличивая прочность, перлит резко отрицательно влияет на ударную вязкость и повышает температуру вязко-хрупкого перехода.
Дата добавления: 2019-07-17; просмотров: 128; Мы поможем в написании вашей работы! |
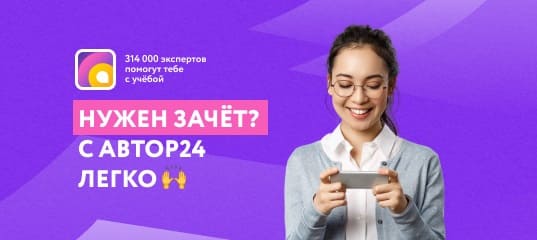
Мы поможем в написании ваших работ!