Методы упрочнения алюминиевых сплавов. Термическая и химико-термическая обработка алюминиевых сплавов.
Неравновесная кристаллизация.
В результате неравновесной кристаллизации химический состав образующихся кристаллов а-твердого раствора по сечению оказывается переменным.
В процессе кристаллизации образуются кристаллы твердого раствора дендритного типа, Поэтому оси первого порядка, возникающие в начальный момент кристаллизации, обогащены более тугоплавким компонентом В.
Развитие зональной ликвации зависит от скорости охлаждения, размера слитка, скорости диффузии, интервала температур кристаллизации и т.
Сплавы, в которых происходит одновременная кристаллизация а и р-фаз при постоянной и самой низкой для данной системы сплавов температуре, называют эвтектическими.
Ликвация– неоднородность химического состава сплавов, возникающая при их кристаллизации. Ликвация возникает в результате того, что сплавы, в отличие от чистых металлов, кристаллизуются не при одной температуре, а в интервале температур. При этом состав кристаллов, образующихся в начале затвердевания, может существенно отличаться от состава последних порций кристаллизующегося маточного раствора. Чем шире температурный интервал кристаллизации сплава, тем большее развитие получает ликвация, причём наибольшую склонность к ней проявляют те компоненты сплава, которые наиболее сильно влияют на ширину интервала кристаллизации (для стали, например, сера, кислород, фосфор, углерод). Ликвация оказывает, как правило, вредное влияние на качество металла, т. к. приводит к неравномерности его свойств.
|
|
Различают дендритную ликвацию, которая проявляется в микрообъёмах сплава, близких к размеру зёрен, и зональную ликвацию, наблюдаемую во всём объёме слитка. Дендритная ликвация выражается в том, что оси дендритных кристаллов отличаются по химическому составу от межосных пространств. Этот вид ликвации может быть в значительной степени устранён при длительном отжиге металла (так называемая гомогенизация) в результате диффузии примесей. Зональная ликвация выражается в наличии в слитке не-скольких зон с различным химическим составом, которые в зависимости от характера отклонений от среднего состава сплава называются зонами положительной или отрицательной ликвации.
4. Пластическая деформация. Текстура деформации. Наклеп. Пластической деформацией называют изменение размеров и формы тела под действием приложенных сил, и сохранение этих изменений после прекращения действия сил. При пластической деформацией происходят процессы скольжения или удвоения. Сначала возникают упругие искажения кристаллической решетки, а при увеличении напряжения — смещение одной части кристалла относительно другой. Плоскостями скольжения есть плоскости с наиболее плотной упаковкой атомов. В процессе скольжения перемещается не вся часть кристалла одновременно, а происходит перемещение дислокаций вдоль плоскости скольжения на расстоянии меньше чем расстояние между атомами. Текстура деформации создает кристаллическую анизотропию, при которой наибольшая разница свойств проявляется для направлений, расположенных под углом 45° друг к другу. С увеличением степени деформации характеристики пластичности (относительное удлинение, относительное сужение) и вязкости (ударная вязкость) уменьшаются, а прочностные характеристики (предел упругости, предел текучести, предел прочности) и твердость увеличиваются (. Также повышается электросопротивление, снижаются сопротивление коррозии, теплопроводность, магнитная проницаемость. Наклёп – это совокупность структурных изменений и связанных с ними св-в при холодной пластичной деформации. В рез-те деф-ции зёрна выстраиваются (вытягиваются в направлении действующей нагрузки. Развивается анизотропия в металле. Под анизотропией понимают различие св-в по различным направлениям в металле. Выше св-ва в направлении пластической деформации (действующей нагрузки).При холодной пластической деформации прочностные хар-ки (твёрдость, предел прочности и растяжений) увеличиваются в 2-3 раза, тогда как хар-ки пластичности (относит. удлинение, относит. сужение) снижаются 30-40 раз. Упрочнение металлов при холодной пластической деф-ции обусловлена увелич. дефектов кристаллич. решётки (вакансий, дислакаций), увеличением числа дислокаций одного знака, а также увеличением угла разориентации м/у блоками.Изменение стр-ры при дорекристаллизационном отжиге.Пластическая деф-ция приводит к переводу металлов в неравновесное состояние, т.е. с повышенным запасом свободной энергии. Как и любая другая сис-ма металл стремиться к уменьшению свободной энергии. Это уменьшение протекает тем интенсивнее, чем выше тем-ра. В зав-ти от тем-ры отжига различают процессы возврата и процессы рекристаллизации.
|
|
|
|
5. Отжиг I. Отжиг 1 рода - это такой вид отжига, при котором не происходит структурных изменений, связанных с фазовыми превращениями.Отжиг 1 рода в свою очередь разделяют на 3 группы:1. Гомогенизация- отжиг, направленный на уменьшение химической неоднородности металлов, образующейся в результате рекристаллизации. В отличие от чистых металлов, все сплавы после кристаллизации характеризуются неравновесной структурой, т.е. их химический состав является переменным как в пределах одного зерна, так и в пределах всего слитка. Химическая неоднородность обусловлена различной температурой плавления исходных компонентов. Чем меньше это различие, тем более заметна химическая неоднородность, получающаяся в слитке. Избавится от нее невозможно, можно только уменьшить. Для этого применяют высокотемпературный отжиг с длительными выдержками (от 2 до 48 часов). При высокой температуре подвижность атомов в кристаллической решетке высокая и с течением времени за счет процессов диффузии происходит постепенное выравнивание химического состава. Однако усреднение химического состава происходит в пределах одного зерна, т.е. устраняется в основном дендритная ликвация. Чтобы устранить зональную ликвацию (химическую неоднородность в пределах части слитка), необходимо выдерживать слитки при данной температуре в течение нескольких лет. А это практически невозможно. В процессе отжига на гомогенизацию происходит постепенное растворение неравновесных интерметаллидных фаз, которые могут образоваться в результате кристаллизации с большой скоростью. При последующем медленном охлаждении после отжига такие неравновесные фазы больше не выделяются. Поэтому после гомогенизации металл обладает повышенной пластичностью и легко поддается пластической деформации.2. Рекристаллизационный отжиг. Холодная пластическая деформация вызывает изменение структуры металла и его свойств. Сдвиговая деформация вызывает увеличение плотности дефектов кристаллической решетки, таких как вакансии, дислокации. Образование ячеистой структуры происходит с изменением формы зерен, они плющиваются, вытягиваются в направлении главной деформации. Все эти процессы ведут к тому, что прочность металла постепенно увеличивается, пластичность падает, т.е. возникает наклеп или нагартовка. Дальнейшая деформация такого металла невозможна, т.к. происходит его разрушение. Для снятия эффекта упрочнения применяют рекристаллизационный отжиг, т.е. нагрев металла до температур выше начала кристаллизации, выдержку с оследующим медленным охлаждением. Температура нагрева зависит от состава сплава. Для чистых металлов температура начала рекристаллизации tp=0,4Тпл, ºК, для обычных сплавов порядка 0,6Тпл, для сложных термопрочных сплавов 0,8Тпл. Продолжительность такого отжига зависит от размеров детали и в среднем составляет от 0,5 до 2 часов. В процессе рекристаллизационного отжига происходит образование зародышей новых зерен и последующий рост этих зародышей. Постепенно старые деформированные зерна исчезают. Количество дефектов в кристаллической решетке уменьшается, наклеп устраняется, и металл возвращается в исходное состояние. Степень деформации определяет размер зерна после отжига. Если она близка к критической (eкр=5-15%), то в результате после отжига в металле возникают крупные зерна, что обычно нежелательно. Поэтому перед рекристаллизационным отжигом деформацию металлов производят со степенью 30-60%. В результате получается мелкозернистая однофазная структура, обеспечивающая хорошее сочетание прочности и пластичности. Увеличение степени деформации до 80-90% вызывает появление в металле текстуры деформации. После рекристаллизационного отжига текстура деформации меняется на текстуру рекристаллизации. Как правило, это сопровождается резким направленным ростом зерна. Увеличение размеров зерна, т.е. снижение механических свойств, может вызвать также слишком большая температура отжига или большая выдержка. Поэтому при назначении режимов отжига необходимо использовать диаграмму рекристаллизации. Рекристаллизационный отжиг может применяться как предварительная, промежуточная, так и как окончательная термообработка. Как предварительная термообработка он применяется перед холодной деформацией, если исходное состояние металла неравновесное и имеет какую-то степень упрочнения. Как промежуточная операция рекристаллизационный отжиг применяется между операциями холодной деформации, если суммарная степень деформации слишком велика и запасов пластичности металла не хватает. Как окончательный вид отжига его применяют в том случае, если потребитель требует поставки полуфабрикатов в максимально пластичном состоянии. В некоторых случаях потребителю требуется полуфабрикат, сочетающий определенный уровень прочности с необходимым запасом пластичности. В этом случае вместо рекристаллизационного отжига используют его разновидность - отжиг на полигонизацию. Отжиг на полигонизацию проводят при температуре, которая ниже температуры начала рекристаллизации. Соответственно при такой температуре происходит лишь частичное устранение наклепа за счет процессов возврата второго рода, т.е. происходит уменьшение плотности дефектов кристаллической решетки, образование ячеистой дислокационной структуры без изменения формы зерен. Степень уменьшения наклепа зависит, прежде всего, от температуры. Чем ближе температура к порогу рекристаллизации, тем меньше наклеп, тем больше пластичность и наоборот.3. Отжиг для снятия внутренних напряжений. Внутренние напряжения в металле могут возникать в результате различных видов обработки. Это могут быть термические напряжения, образовавшиеся в результате неравномерного нагрева, различной скорости охлаждения отдельных частей детали после горячей деформации, литья, сварки, шлифовки и резания. Могут быть структурными, т.е. появившиеся в результате структурных превращений, происходящих внутри детали в различных местах с различной скоростью. Внутренние напряжения в металле могут достигать большой величины и, складываясь с рабочими, т.е. возникающими при работе, могут неожиданно превышать предел прочности и приводить к разрушению. Устранение внутренних напряжений производится с помощью специальных видов отжига. Этот отжиг проводится при температурах ниже температуры рекристаллизации: tотж=0,2-0,3Тпл º К. Повышенная температура облегчает скольжение дислокаций и, под действием внутренних напряжений, происходит их перераспределение, т.е. из мест с повышенным уровнем внутренних напряжений дислокации перемещаются в области с пониженным уровнем. Происходит как бы разрядка внутренних напряжений. При нормальной температуре этот процесс будет длиться в течение нескольких лет. Увеличение температуры резко увеличивает скорость разрядки, и продолжительность такого отжига составляет несколько часов.
|
|
6. Отжиг II рода. При отжиге 2-го рода в металле или сплаве происходят качественные или количественные изменения фазового состава при нагревании и обратные изменения при охлаждении. В твердом состоянии протекают разнообразные фазовые превращения: полиморфное, эвтектоидное, перитектоидное, растворение одной фазы в другой при нагревании и обратное выделение при охлаждении и др. Отжиг 2-го рода можно проводить с полным изменением фазового состава, когда фазы, существовавшие при комнатной температуре, исчезают при нагревании, а фазы, стабильные при повышенной температуре, исчезают при охлаждении. Отжиг 2-го рода в технологии цветных металлов и сплавов не используют так широко, как для сталей и чугунов. Во многих промышленных цветных металлах и сплавах, например однофазных латунях, бронзах и электротехнических никелевых сплавах, отсутствуют фазовые превращения в твердом состоянии и к ним отжиг 2-го рода в принципе неприменим. Другие цветные сплавы претерпевают фазовые превращения в твердом состоянии, но отжиг 2-го рода вызывает такое изменение свойств, что применение его нецелесообразно. В зависимости от типа фазовых превращений различают две разновидности отжига 2-го рода: гетерогенизирующий отжиг и отжиг с фазовой перекристаллизацией. Гетерогенизирующий отжиг применяют к сплавам, в которых из матричной фазы вследствие изменения равновесной растворимости при понижении температуры выделяется другая фаза или несколько фаз. В подавляющем большинстве сплавов матричной фазой является твердый раствор на базе основного металла, а избыточной — соединение. К таким материалам относятся все термически упрочняемые сплавы на алюминиевой, магниевой, медной, никелевой и других основах, например дуралюмин, электрон, бериллиевая бронза, нимоник. Среди цветных сплавов эта группа — самая многочисленная. В двойных системах поведение сплавов такого типа при гетерогенизирующем отжиге тесно связано с ходом кривой сольвуса (смотрите, например, рисунок Системы с различными фазовыми превращениями). Относительное количество фазы, которая полностью переходит в твердый раствор при нагревании и выделяется при обратном медленном охлаждении, обычно не превышает 10 — 15% от всего объема сплава. При таком фазовом превращении не происходит коренной ломки структуры по всему объему, как при отжиге углеродистых сталей с нагревом выше точки А3. Тип кристаллической решетки матричной фазы при растворении в ней или выделении из нее другой фазы не меняется. Отжиг, включающий только процессы растворения и выделения, приводит лишь к изменению концентрации компонентов в матричной фазе и к изменению количества, размера, а также формы частиц выделяющейся фазы. На этих изменениях и основано применение гетерогенизирующего отжига.Смягчающий гетерогенизирующий отжиг.Во многих сплавах гетерогенизация структуры при выделении избыточных фаз из матричного раствора, происходящая при медленном охлаждении с температуры отжига, приводит к разупрочнению, которое используют в разных целях. Полный смягчающий отжиг применяют ко всем термически упрочняемым алюминиевым сплавам (типа дуралюмин, авиаль и др.). Цель отжига — смягчить материал, сделать его пластичнее перед штамповкой, гибкой, отбортовкой и другими операциями холодной обработки давлением. Ускоренное охлаждение на воздухе горячекатаных рулонов с температуры горячей прокатки приводит к частичной закалке (подкалке). Гетерогенизирующий смягчающий отжиг рулонов, например дуралюмина, позволяет при последующей холодной прокатке повысить степень обжатия без промежуточных отжигов. Гетерогенизирующий отжиг можно проводить, нагревая сплав до окончательного растворения избыточной фазы (выше t0 на рисунке Системы с различными фазовыми превращениями, д) с последующим очень медленным охлаждением. Медленное охлаждение необходимо, чтобы наиболее полно снизить концентрацию твердого раствора и избежать выделения фазы в слишком дисперсной форме с малыми расстояниями между ее частицами. Чем ниже концентрация матричного раствора и больше расстояние между выделениями, тем больше разупрочнение при отжиге. Для экономии времени более выгодно при отжиге недогревать сплав до t0. Температуру нагрева выбирают так, чтобы за сравнительно короткое время выдержки была достигнута концентрация матричного раствора, близкая к равновесной, а вторая фаза скоагулировала. После этого проводят медленное охлаждение. Большинство термически упрочняемых алюминиевых сплавов подвергают полному смягчающему отжигу при 380 — 420 °С в течение 10 — 60 мин с последующим охлаждением со скоростью не более 30 град/ч. При полном отжиге, кроме основного гетерогенизирующего процесса, может проходить и рекристаллизация, вносящая свой вклад в разупрочнение. Например, это происходит тогда, когда из-за низкой температуры окончания горячей прокатки лист был наклепан. Однако режим отжига для полного смягчения выбирают, исходя из требований гетерогенизации структуры, предусматривая медленное охлаждение. Для чисто рекристаллизационного отжига однофазных сплавов скорость охлаждения не имеет значения. Неполный (сокращенный) смягчающий отжиг термически упрочняемых алюминиевых сплавов проводят при температуре ниже температуры полного отжига. При этом уже во время выдержки концентрация матричного раствора получается настолько низкой, что можно использовать быстрое охлаждение на воздухе или в воде. Из-за более низкой температуры сокращенного отжига время выдержки при этой температуре должно быть больше, чем при полном отжиге, однако общая продолжительность термообработки уменьшается из-за последующего быстрого охлаждения.Влияние температуры отжига после холодной прокатки на предел прочности дуралюмина Д16 при двух скоростях охлаждения (по данным В. А. Ливанова и С. М. Воронова): 1 — охлаждение с печью до 209 °С; 2 — охлаждение на воздухе которого из β-фазы более полно выделяется пластичная α-фаза. На рисункепоказано, что для максимального разупрочнения дуралюмина Д16 температура отжига в случае охлаждения с печью должна быть около 380 — 400 °С, а в случае охлаждения на воздухе — около 350 — 370 °С. При более высоких температурах нагрева S-фаза и CuAl2 быстро переходят в алюминивый раствор и при последующем охлаждении на воздухе происходит подкалка, повышающая прочность. Сокращенный смягчающий отжиг большинства алюминиевых сплавов проводят при 350 — 370 °С с выдержкой 2 — 4 ч и охлаждением на воздухе или в воде. Смягчающий гетерогенизирующий отжиг применяют не только к алюминиевым сплавам. Если, например, (α + β)-латунь в результате ускоренного охлаждения из β-области после горячей обработки давлением имеет пониженную пластичность (из-за большого количества хрупкой β´-фазы), то этот недостаток можно устранить отжигом с медленным охлаждением, во время которого из β-фазы более полно выделяется пластичная α-фаза. Гетерогенизирующий отжиг для повышения коррозионной стойкости. Если двухфазная структура с определенной степенью дисперсности и оптимальным распределением частиц избыточной фазы обеспечивает повышенную стойкость против коррозии, то такую структуру получают гетерогенизирующим отжигом. Например, максимальную стойкость против коррозии под напряжением магналия марки АМг6 обеспечивает двухфазная структура, в которой β-фаза (Al3Mg2) равномерно распределена в зернах алюминиевого раствора. Этого достигают гетерогенизирующим отжигом магналия при 320 °С перед последней холодной нагартовкой. Явление перегрева в литых сплавахи.Границы зерен в технических литых сплавах весьма стабильны. В однофазном литом сплаве при нагреве зерно практически не укрупняется. Фазовый наклеп, возникающий при растворении одной фазы в другой, в принципе способен нарушить стабильность границ и вызвать рост зерна матричной фазы. В термически упрочняемых алюминиевых, магниевых и медных сплавах количество вторых фаз относительно мало, и объемные изменения при растворении этих фаз не приводят к достаточно сильному фазовому наклепу. Поэтому в этих сплавах в литом состоянии нагрев при переходе через границу растворимости в однофазную область, за редкими исключениями, не приводит к сильному росту зерна основного твердого раствора. Особый случай представляет (α + β)-латунь. После нагрева до температур выше температуры полного перехода из (α + β)- в β-состояние возможен сильный перегрев (рост зерна), причем иногда β-зерна достигают нескольких сантиметров в диаметре Условия для роста зерна при нагреве литой (α + β)-латуни обеспечиваются фазовым переходом из (α + β)- в β-состояние. В литых двухфазных латунях относительное количество α-фазы может составлять значительную долю от всего сплава, во всяком случае гораздо большую долю, чем относительное количество вторых фаз в термически упрочняемых алюминиевых и магниевых сплавах и во многих бронзах. Это вытекает из характера диаграммы состояния Cu — Zn. Растворяющейся при нагреве фазой является α-фаза, относительное весовое количество которой при комнатной температуре может изменяться от 0 до 100% в зависимости от содержания цинка. При нагревании двухфазной латуни с большим количеством α-фазы растворение ее в β-фазе, по-видимому, приводит к такому фазовому наклепу, который обеспечивает условия для роста зерна. Перегрев (α + β)-латуни часто сопровождается пережогом, причем по границам зерен преимущественно окисляется цинк. Поверхность зерен в слитке на рисунке была покрыта тонким белым слоем из окиси цинка. В литой однофазной α-латуни, не претерпевающей фазовых превращений в твердом состоянии, перегрев не наблюдается, а опасен только пережог. В некоторых случаях малые добавки обусловливают сильный рост зерна основного твердого раствора при нагреве литого сплава, хотя этот сплав содержит сравнительно небольшое количество избыточных фаз. Например, при нагреве отливок из магниевого сплава МЛ5 до 415 °С растворение избыточной фазы Mg17Al12, количество которой весьма невелико, не приводит к росту зерна. Если же в этот сплав попали всего лишь тысячные доли процента циркония (> 0,002%), то при нагреве до 415 °С зерно в отливке сильно укрупняется. Природа этого интересного явления не установлена. Отжиг с фазовой перекристаллизацией. Фазовая перекристаллизация, включающая полиморфное или эвтектоидное превращение, приводит к коренной перестройке структуры по всему объему сплава (рисунок Системы с различными фазовыми превращениями). Полиморфное превращение в металлах можно использовать для устранения текстуры и изменения размера зерна. В этом отношении интересным примером является термическая обработка урана (так называемая pтермообработка). Уран ниже 668 °С имеет ромбическую α-решетку, а от 668 до 774 °С — тетрагональную β-решетку. В начальный период развития атомной техники было установлено, что если изделие из поликристаллического урана подвергается многократным нагревам и охлаждениям в температурном интервале α-фазы, то оно меняет свои размеры. В литом изделии с крупным зерном возникает шероховатость поверхности. Обработанное давлением изделие (пруток, проволока, пластина) сильно удлиняется, «растет» в одном направлении, сокращаясь в другом. . Наиболее важным фактором, определяющим величину «роста» урана, является текстура, которая возникает при обработке давлением в α-области. Преимущественная ориентировка кристаллов в урановом изделии приводит к сильной анизотропии термического расширения, из-за которой при термических циклах возникают напряжения и направленное изменение размеров изделия. Для предотвращения вредного явления «роста» урана необходимо устранить текстуру, которая создается при обработке давлением в α-области. Если урановый стержень с резко выраженной текстурой нагреть до температуры β-области (выше 668 °С) и затем охладить, то произойдет фазовая перекристаллизация, причем α-кристаллы, образующиеся при полиморфном превращении β → α, не получают резко выраженной предпочтительной ориентировки. Следовательно, фазовая перекристаллизация устраняет текстуру, в результате чего во всех направлениях коэффициент термического расширения становится одинаковым. После такой термообработки скорость «роста» уранового стержня при воздействии теплосмен резко снижается. Чем больше размер зерна, тем ярче выражена шероховатость поверхности уранового изделия, возникающая при воздействии многократных термических циклов. Зерна урана можно измельчить при фазовой перекристаллизации. Размер α-сзерен уменьшается с ускорением охлаждения из (состояния. По аналогии с ураном полиморфное превращение в других цветных металлах и твердых растворах может быть использовано для устранения текстуры и измельчения зерна. Эвтектоидное превращение в цветных сплавах пока редко используют как основу отжига 2-го рода. В заключение заметим, что при полиморфном или эвтектоидном превращении нагрев выше критической точки может привести к сильному росту зерна деформированного, а также литого металла или сплава.
7.Закалка с полиморфным превращением. Выбор режимов термической обработки на основании изотермических и термокинетических диаграмм распада переохлажденного твердого раствора. Закалка – термообработка, при которой сталь приобретает неравновесную структуру, что прежде всего выражается в повышении твердости стали. К закалке относят: термообработку на сорбит, тростит и мартенсит. Степень неравновесности продуктов закалки с увеличением скорости охлаждения повышается и возрастает от сорбита к мартенситу.Преимуществом истинной закалки является возможность получения из мартенсита за счет последующего отпуска продуктов с комплексами свойств, которые другими видами термообработки получить невозможно.Истинная закалка получила широкое применение как предварительная обработка перед отпуском.Важна критическая скорость закалки. От нее зависит прокаливаемость стали, т. е. способность закаливаться на определенную глубину. Критическая скорость закалки зависит от стабильности аустенита, которая определяется количеством растворенных в нем углерода и легирующих элементов. Введением в сталь углерода и легирующих элементов повышается прокаливаемость, которую оценивают с помощью цилиндрических образцов по глубине залегания в них полумартенситного слоя Основные параметры при закалке – температура нагрева и скорость охлаждения. Температуру нагрева для сталей определяют по диаграммам состояния, скорость охлаждения – по диаграммам изотермического распада аустенита.Время нагрева зависит от размеров детали и теплопроводности стали, определяют экспериментально.Одной из целей легирования конструкционных сталей является уменьшение критической скорости закалки и получение сквозной прокаливаемости изготовленных из них деталей при закалке не только в воде, но и в более мягких охлаждающих средах. От резкости охлаждающей среды зависит уровень термических и фазовых напряжений и вероятность образования трещин в детали. В связи с изложенным при закалке предпочтительны мягкие закалочные среды. При закалке режущего инструмента из высокоуглеродистой стали с целью уменьшения внутренних напряжений применяют охлаждение в двух средах.Если тонкий образец сплава С0 , находящегося при температуре Тзак в состоянии ненасыщенного твердого раствора, быстро перенести в термостат с температурой T1 < T0, то α-раствор окажется пересыщенным, так как при температуре Т1насыщенным является раствор состава точки г. Степень пересыщенности можно характеризовать отношением C0/C1.
При температуре Т1 пересыщенный α-раствор состава С0 одновременно является переохлажденным относительно температуры 70, выше которой стабильна одна α-фаза, а ниже — двухфазная смесь α + β. Степень переохлаждения ∆Т = Т0 — Т1. Чем ниже температура термостата, в которой мы переносим образец, нагретый до температуры Тзак тем больше степень переохлаждения и степень пересыщенности твердого раствора. Термодинамическим стимулом распада переохлажденного раствора является разность ∆Fоб между его свободной энергией F1 и свободной энергией двухфазной смеси F2.
8. Отпуск, выбор режимов термической обработки на основании эксплуатационных требований. Отпуск – проводится с целью снятия внутренних напряжений, снижения твердости и увеличения пластичности и вязкости закаленных сталей Характеризуется нагревом до температуры ниже критической А1 .Скорость охлаждения роли не играет. Происходят превращения, уменьшающие степень неравновесности структуры закаленной стали. Также термическую обработку подразделяют на предварительную и окончательную. Предварительная – применяется для подготовки структуры и свойств материала для последующих технологических операций (для обработки давлением, улучшения обрабатываемости резанием).Окончательная – формирует свойство готового изделия. Различают три вида отпуска:1. Низкий отпуск с температурой нагрева Тн = 150…300oС.В результате его проведения частично снимаются закалочные напряжения. Получают структуру – мартенсит отпуска. Проводят для инструментальных сталей после закалки токами высокой частоты или после цементации.2. Средний отпуск с температурой нагрева Тн = 300…450oС.Получают структуру – троостит отпуска, сочетающую высокую твердость 40…45HRC c хорошей упругостью и вязкостью. Используется для изделий типа пружин, рессор.3. Высокий отпуск с температурой нагрева Тн = 450…650oС..Получают структуру, сочетающую достаточно высокую твердость и повышенную ударную вязкость (оптимальное сочетание свойств) – сорбит отпуска. Используется для деталей машин, испытывающих ударные нагрузки. Комплекс термической обработки, включающий закалку и высокий отпуск, называется улучшением. Изменение внутренней структуры1 стали в процессе нагревания при различных видах термообработки зависит от содержания в ней углерода. Поэтому выбор температуры нагрева производят по специальной диаграмме ( 49), которая является частью более полной диаграммы состояния железоуглеродистых сплавов. По горизонтальной оси на ней указано содержание углерода в процентах, а по вертикальной — температура нагрева стали в градусах Цельсия. Заштрихованные участки диаграммы показывают оптимальные температурные интервалы нагрева стали при различных видах термообработки. В процессе отпуска уже закаленная сталь нагревается до температуры ниже линии PSK, выдерживается при этой температуре и охлаждается на воздухе или в масле. Главная цель отпуска — снизить хрупкость закаленной стали.
Температура нагрева при отпуске колеблется от 75 до 650°С.
Выбор той или иной температуры зависит от назначения изготовляемой детали. При повышении температуры нагрева твердость и прочность закаленной стали снижаются, а вязкость увеличивается.
В практике термообработки различают три вила отпуска: низкий, который выполняется при температурах до 250°С, средний — при температурах до 450°С и высокий — при температурах до 650°С. Высокий отпуск обеспечивает более полное снятие остаточных напряжений, высокую вязкость и достаточную прочность стали.
9. Закалка без полиморфного превращения. Выбор режимов термической обработки на основании диаграммы фазового состояния сплава. Закалка без полиморфного превращения применима к любым сплавам, в которых одна фаза полностью или частично растворяется в другой. Например, в сплаве С0 на рисунке при нагревании до Тзак β-фаза растворяется в матричной α-фазе. При обратном медленном охлаждении β-фаза выделяется из α-фазы, в которой концентрация компонента В уменьшается в соответствии с ходом сольвуса nb.
Так как составы α- и β-фаз различны, то выделение β-фазы связано с диффузионным перераспределением компонентов. При достаточно быстром охлаждении диффузионное перераспределение, необходимое для зарождения и роста кристаллов β-фазы, не успевает пройти и β-фаза не выделяется из α-раствора. После такой термообработки (закалки) сплав при комнатной температуре состоит из одной α-фазы, как и при температуре нагрева под закалку. Следовательно, закалка без полиморфного превращения состоит в фиксации при более низкой температуре состояния, свойственного более высокой температуре. При температуре нагрева под закалку Тзак в сплаве С0 твердый раствор ненасыщенный. После закалки α-раствор при комнатной температуре имеет такой же состав, как и при температуре закалки, но он уже пересыщенный, так как состав насыщенного раствора соответствует точке b. Таким образом, при закалке без полиморфного превращения образуется пересыщенный твердый раствор. Такая закалка к чистым металлам принципиально неприменима. Рассмотренную на примере сплава С0 закалку без полиморфного превращения широко применяют к алюминиевым, магниевым, никелевым, медным и другим сплавам, а также к некоторым легированным сталям. Закалкой далеко не всегда фиксируют однофазное состояние. Например, в сплаве С2 при любых температурах, вплоть до эвтектической, содержится β-фаза. При температуре закалки Тзак в этом сплаве находятся насыщенный твердый раствор состава точки m и нерастворенный избыток β-фазы. При достаточно медленном охлаждении из-за выделения β-фазы из α-раствора его состав должен изменяться по линии mb. При быстром охлаждении происходит закалка: β-фаза не успевает выделиться из α-раствора и состав его при комнатной температуре так же, как и при температуре закалки, определяется точкой m. Следовательно, закаленный сплав С2 содержит пересыщенный α-раствор состава точки т и избыточную β-фазу, нерастворившуюся при нагреве под закалку. Закалкой сплава С2 зафиксировано состояние, которое было стабильным при температуре закалки. Начинающие изучать термическую обработку иногда ошибочно считают, что закалка применима лишь к такому сплаву, ордината которого на диаграмме состояния пересекает линию фазового равновесия в твердом состоянии, например к сплаву С0 на рисунке. Но, как было показано на примере сплава С2, это совсем не обязательно. Принципиально закалка без полиморфного превращения возможна всегда, когда в равновесном состоянии при разных температурах имеется различие в химическом составе фаз.
10. Теория и технология старения. Режимы старения.
Старение – термическая обработка, при которой главным процессом является распад пересыщенного твердого раствора. В результате старения происходит изменение свойств закаленных сплавов. В отличие от отпуска, после старения увеличиваются прочность и твердость, и уменьшаетсяпластичность.
Старение сплавов связано с переменной растворимостью избыточной фазы, а упрочнение при старении происходит в результате дисперсионных выделений при распаде пересыщенного твердого раствора и возникающих при этом внутренних напряжений.Режимы старения
1.Естественное(без нагрева от 0-30),длительная выдержка
2.Искусственное старение требует повышен.Т
Граница между естественным и искусственным старением условно. Гораздо чаще старение делят по структуре на зонное(естественное) и фазовое(искусственное). Для многих изделий критерием оптимальности режима старения служит не структура,а комплекс свойств, которые она обеспечивают. В зависимости от комплекса свойств искусственное старние делят на:
Полное искусственное старение. Т и время обеспечмвает достижение максимальной прочности.Неполное искусственное старение. Т более низкая или выдержка более короткая, чем при полном старении. Это обеспечивает повышение прочности(по сравнению с закаленным состоянием) при сохранении пластичности.
Перестаривание проводятся при более высокой Т или с большей выдержкой по сравнению с полным старением. С целью получить сочетание повышенной прочности и др.свойств
Стабилизирующее старение. Разновидность перерывания с целью стабилизации свойств и размеров изделий. Исходя из условий необходимо оценивать параметры ТО и даже в ущерб величине св-ва проводить ТО в таких режимах тем-ры, которые будут соответствовать для того,чтобы обеспечить гарант.уровень св-в и размеров.
Ступенчатое старение предполагает выдержку при разных Т. Цель выдержки на низкотемпературной ступени создание большого числа ЗГП и центров кристаллизации, а на высокотемпературной ступени получение необходимой степени распада пересыщенного твердого р-ра и определенных размеров выделений.
Возврат после старение.
После обработка на возврат как и после обычной перезакалки сплав способен упрочниться в рез-те естественного старения. Повторная обработка на возврат его вновь разупрочнит.
Обработкой на возврат можно растворять и ЗГП и кристаллы метастабильных фаз.
Для каждого сплава и режима старения необходимо подбирать свою Т т время выдержкт для обработки на возврат. Цель обработки на возврат восстановление св-в пластичности перед формообразован. ПД если перезакалка нежелательна из-за корабления.
11.Кристаллическое строение; основные свойства и назначение алюминия. Технология производства; основные примеси и маркировка алюминия. Классификация алюминиевых сплавов. Конструкционные алюминиевые сплавы. Основные системы легирования. Маркировка. ГОСТ . Атомн.номер 13, атомн масса 26,9815; крист.решетка ГЦК; серебристо-белый Ме
Алюминий лучший проводник тепла и электричества.Чистый Ал пластичный,относительно мягкий и непрочный. Уд.прочность алюм.сплавов высокая.
Ал имет большое сродство к кислороду. Поэтому пожары вызванные возгоранием Ал, нельзя тушить водой. Чистый Ал устойчив на воздухе, в горячей и холодной воде на его поверхности образуется тонкая защитная пленка, которая препятствует дальнейшей коррозии.
Ал хорошо сваривается,обраб.давлением,но плохо обр-ся резанием и хар-ся большой литейной усадкой.Экструзия-деформация материала путем выдавливания через головку спец.сечения.Профилиров.позволяет получать прутки, трубы, листы..
Мех.примеси удаляют переплавкой сырого Ал, а хим.примеси удаляютэлектр.рафинированием.Примеси оказывают существенное влияние на св-ва Ал.
Железо почти не растворено в Ал; явл-ся вредной примесью,понижает пластичность и электропроводность Ал.Кремний не образует хим.соединений с Ал.Кремний как примесь,не всегда может быть обнаружен металлографически. Кремний,как и др.растворимые в Ал элементы упрочняют Ал. Присутствие эв-ки вокруг зерен Ал явл-ся неблагоприятным в отношении мех.св-в.Маркировка и назначение Ал:
-особой чистоты А999; -высокой чистоты А995, А99,А97,А95; -технической чистоты А85,А8,А7,А6,А5,А0Ал один из наиболее важных материалов современ.техники. Его используют в чистом виде,сплавах и соединениях.
Классификация алюм.сплавов:
-по хим.составу1ХХХ Ал вплоть до техн.чистоты 2ХХХ сплавы Ал-медь 3ХХХ- Ал-марганец 4ХХХ- Ал-кремний 5ХХХ Ал- магний 6ХХХ Ал-магний-кремний 7ХХХ Ал-цинк-магний 8ХХХ остальные сплавы- по технологии изготовления*деформируемые-обладают высокой пластичностью. Основа стр-ры сплава -тв.р-р легир.элементов в Ал.
*литейные- обладают хорошей жидкотекучестью,герметичностью
*свариваемые-обл.способностью образованиянеразъемного соединения,св-ва которго близки к св-вам маиртцы сплава.*композиционные- пены
- по назначению и свойствам
*герметичные-силумины *высокопрочные-авиали,дюролюмины *коррозионностойкие-магналины *теплостойкие и жаропрочные- легиров медью*легкие и сверлегкие-легиров литием *радиационно-стойкие-легиров литием
Методы упрочнения алюминиевых сплавов. Термическая и химико-термическая обработка алюминиевых сплавов.
Т1- для улучшения прочности и обработки резанием применяют искусственное старение(175)
Т2-для снятия литейных и остаточных напряжений и повышение пластичности(300)
Т3- для повышения прочности(510-545)
Т4-естественное иди искусственное(150-200)
Т5-полное старение
Т6-кратковременное старение
Т7-для стабилизации стр-ры и объема под закалку и стабилизирующий отпукс(230-250)
Т8- для повышения пластичности и стабилизации размеров под закалку и смягчающий отпуск(240-260)
Гомогенизация- ТО сплавов с неоднородной термодинамической неустойчивой стр-рой. Т нагрева должна быть выше Т полного растворения легирующих компонентов в Ал и ниже Т равновесного солидуса.В условиях неравновесного кристалл.в стр-ре сплава возможно присутствие эвтектики.След-но Т нагрева должна быть ниже Т эвтектики.
Зоны Гинье-Престона – нанообъемы тв.р-ра альфа, с повышением содержания легиров. Эл-та,преимущественно сосредоточенные в определенной кристаллографич плоскости основного Ме.
Соднрж легир эл-та в ЗГП, как и их размер возрастает по мере развития процесса старения. Форма выдел при старении и распред их в пределах кристаллита альфа опр-ся поверхностной энергией данной кристаллогр.плоскости и энергией упругой деформации.
Методы упрочнения связаны с созданием препятствий перемещению дислокаций. Этого можно достичь за счет термической обработки сплавов определенного вида: перекристаллизации; диствердения; мартенситного превращения, особенно характерного для сталей; пластической деформации (наклеп).
Перекристаллизация — это изменение типа кристаллической решетки, происходящее при полиморфном превращении. Упрочнение достигается за счет измельчения зерна в процессе изменения типа кристаллической решетки, т.е. при образовании новой фазы. Так, в исходном состоянии сплав имеет крупнозернистое строение. При его нагреве до температуры tx (рис. 2.27) начинается (а -» у)-превращение. Вновь образующаяся у-фаза возникает по границам исходной а-фазы и имеет меньшую величину зерна. Превращение заканчивается при нагреве до температуры t при этом структура сплава представлена только мелкозернистой у-фазой. При охлаждении происходит обратное (у -» а)-превращение и вторичное измельчение зерна. Дисперсионное твердение — это упрочнение сплава за счет выделения из пересыщенного твердого раствора большого количества мельчайших частиц второй дисперсной (очень мелкой) фазы. Прочность возрастает за счет того, что эти частицы препятствуют перемещению дислокаций. Дисперсионное твердение возможно для сплавов типа твердый раствор с ограниченной растворимостью (рис. 2.28). В исходном состоянии частицы второй фазы крупные. Упрочнение достигается нагревом до получения однофазной структуры(температуры tx ) при этом частицы второй фазы растворяются в твердом растворе. Образованную однофазную структуру фиксируют последующим быстрым охлаждением, т.е. закалкой. В результате пластической деформации происходит искажение кристаллической решетки, зерна металла деформируются и приобретают определенную ориентацию. До деформации зерно имеет равноосную форму, а после деформации зерна сначала вытягиваются в направлении действующих сил, а затем дробятся, т.е. измельчаются (рис. 2.30), что и приводит к повышению прочности. Деформированный металл находится в неравновесном состоянии. В таком металле даже при комнатной температуре могут самопроизвольно протекать процессы, приводящие его в более устойчивое состояние. Если же деформированный металл нагреть, то скорость этих процессов возрастает. Небольшой нагрев (для железа до 300…400°С) ведет к снятию искажений кристаллической решетки, но микроструктура остается без изменений — зерна по-прежнему сохраняют вытянутую форму. Прочность несколько снижается, а пластичность повышается. Такая обработка называется возвратом или отдыхом.
13.Литейные алюминиевые сплавы. Сплавы высокой герметичности: силумины двойные и многокомпонентные . Для изготавливают фасонных деталей прим литейные Al сплавы. Они имеют низ плотность и высшую удельную прочность.Качество литейных Аl сплавов определяется не только мех св-ми, но и технологическими: жидкотекучестью, герметичностью, склонностью к горячим трещинам, степенью изменения мех св-в в зависимости от сечения отливки. Большинство этих хар-ик опред хс сплава и его чистотой % примесей. Способы литья, модифицирование и легирование расплава, ТО изделия способны влиять на свойства сплава. Герметичные сплавы силумины — система Al-Si + л.э.Лучшими литейными свойствами обладают сплавы системы Al-Si — силумины герметичные конструкционные сплавы. Стр-ра силуминов близка к эвтектической, что обуславливает их высокую жидкотекучесть, высокую герметичность и малую усадку. Силумины хорошо обрабатываются резанием, свариваются. Двойные сплавы Al-Si не упрочняются ТО. Единственным способом повышают мех. св-тв является модифицирование. . Модифицирование изменяет условия первичной кристаллизации сплава. В силумин, в качестве модификатора, добавляют или Nа около 1%, или галогениды Na. Модификатор способствует кристаллизации мелкозернистой структуры. Легируемые силумины систем Al-Si-Mg + л.э. и Al-Si-Cu-Mg + л.э. подвергают ТО.Растворимость Si в Аl убывает с понижением T: от 1,6% Si при 577°С при 224°С только 0,01%Si. Si имеет решетку алмаза и отличается хрупкостью. Растворимость Аl в Si весьма незначительная. Кристаллизация сплавов Al-Si завершается образуется Э при 577°С. Эвтектическая составляющая обеспечивает высокие литейные св-ва двойным сплавам Al-Si и сложным Al-Si-л.э. с содерж 4-13%Si. В этих сплавах с ростом содержит Si возраст прочность частицы Si тормозят скольжение, но падает пластичность. С целью улучшения мех св-в Al-Si сплавов проводят их модифицирование. Недостатки: повышенная газовая пористость, пониженная жаропрочность. Марки: АК7, АК12, АК6М3, АК12ММгН, АК5М7.
14.Литейные алюминиевые сплавы. Конструкционные высокопрочные и жаропрочные и коррозионно-стойкие . Для изготовления фасонных деталей прим литейные Al сплавы. Они имеют низ плотность и высокую удельную прочность. Качество литейных Аl сплавов определяются не только мех св-ми, но и технологичность: жидкотекучестью, герметичностью, склонностью к горячим трещинам, степенью изменения мех св-в в зависимости от сечения отливки. Большинство этих хар-ик определяется химическим составам сплава и его чистотой % примесей. Способы литья, модифицирование и легирование расплава, ТО изделия способны влиять на свойства сплава.Коррозионно -стойкие сплавы магналины – система Al-Mg; высокопрочные и жаропрочные сплавы система Al-Cu.Сплавы системы Al-Mg из-за отсутствия в стр-ре эвтектических фаз имеют недостаточно высокие литейные свойства, чувствительны к примесям Fe и Si, обладают малой плотностью. Достоинством сплавов этой группы является высокая коррозионная стойкость коррозионно-стойкие конструкционные сплавы. Сплавы Al-Mg хорошо обрабатываются резанием и полируются. Легирование Be уменшает склонность расплава к окислению в процессе плавки и литья. Легирование Ti и Zr способствует измельчению зерна и тормозит естественное старение улучшает мех св-ва. Старение этих сплавов процесс нежелательный, т.к. оно понижает их вязкость, пластичность и повышает склонность к межкристаллитной коррозии и коррозии под напряжением в ходе старения пересыщ тв р-р распад неравномерно по объёму зерна. Поэтому эти сплавы упрочняются только закалкой без последующего старения. Для обеспечения оптимальных мех св-в закалка. Недостатком сплавов системы Al-Mg явл их низкая жаропрочность. Сплавы применяют для изготовления силовых деталей ,а также используют вместо дефицитных бронз ,латуней, коррозионностойких сталей для деталей, работают в различных климатических условиях, включая воздействие морской воды и тумана.Сплавы системы Al-Cu обладают низкой коррозионной стойкостью, невысокими литейными св-ми. Сплавы этой группы хар-ся высокой прочностными св-ми при норм и повышении Т конструкционные высокопрочные и жаропрочные сплавы. Они хорошо поддаются обработке резанием и свариваются. Система Al-Cu: Аl образует с Сu ограниченный р-р с решеткой ГЦК. Растворим Cu в Аl убывает с понижением Т.Система Al-Mg магналины: Аl обр с Mg ограниченный р-р с решеткой ГЦК. Растворимость Mg в Al убывает с понижением Т. Магналины – наиболее прочные среди литейных сплавов.
Марки: АМг10, АМ5.
15.Деформируемые алюминиевые сплавы. Сплавы, не упрочняемые термической обработкой. Эти сплавы характеризуются сравнительно невысокой прочностью(ненамного больше прочности А1),высокой пластичностью и коррозионной стойкостью, хорошей свариваемостью.
К этой группе относят сплавы систем А1-Мn(АМц)и Al-Mg(АМг).
Марганец, в отличие от остальных элементов,не только не ухудшает коррозионной стойкости алюминиевого сплава,но несколько улучшает ее. Сплавы А1-Мn превосходят чистый Аl высокой прочностью и коррозионной стойкостью.
Магний является полезным л.э.Он уменьшает плотность А1 сплава(Mg легче А1),повышает прочность,не снижая его пластичность.Поэтому Al-Mg сплавы более прочные и легкие,чем чистый А1.
Это сплавы для получения изделий глубокой вытяжкой,сваркой,от которых требуется высокая коррозионная стойкость. Из сплавов данной группы изготавливают емкости для жидкостей (сварные бензобаки),трубопроводы для масла и бензина, корабельные конструкции, детали вагонов, рамы транспорт, ср-в, заклепки ...
Сплавы этой группы используют в отожженом, нагартованном и полунагартованном состоянии.
Для устранения дендритной ликвации деформируемых сплавов проводят гомогенизационный отжиг слитков при 450..520°С в течение 4...40 ч с последующим охлаждением на воздухе или в печи.
Деформированные заготовки подвергают рекристаллизационному отжигу при 350...500С в течение 0,5...2ч для снятия наклёпа и получения мелкозернистой структуры.
16.Деформируемые алюминиевые сплавы. Сплавы, упрочняемые термической обработкой. Авиали; ковочные сплавы . Деформируемые - обладают высокой пластичностью основа структуры сплава - твердый раствор легирующих элементов в алюминии. Для деформируемых сплавов характерна структура твердого раствора с наибольшим содержанием эвтектики. Деформируемые алюминиевые сплавы применяют для получения листов, ленты, фасонных профилей, проволоки и различных деталей штамповкой, прессованием, ковкой. Термически упрочняемые сплавы приобретают высокие механические свойства и хорошую сопротивляемость коррозии только в результате термической обработки. Сплавы на основе алюминия, легированные медью и марганцем, имеют среднюю прочность, но хорошо выдерживают воздействия высоких и низких температур, вплоть до температуры жидкого водорода.Сплавы системы алюминий-цинк-магний имеют высокую прочность, хорошо свариваются, но при значительной концентрации цинка и магния склонны к самопроизвольному коррозионному растрескиванию. Надежны сплавы средней прочности и концентрации.Сплавы системы алюминий-магний-кремний (авиали) сочетают хорошую коррозионную стойкость со сравнительно большим эффектом старения. Анодная обработка этих сплавов позволяет получать красивые декоративные окраски. авиали – сплавы, легированные магнием и кремнием, например АД31/6063, АД33/6061, АД35/6082; Ковочные сплавы- ним относятся сплавы, легированные медью, магнием и кремнием (АК6, АК8/2014). ковочные сплавы АК6, АК8 системы Аl—Mg—Si—Сu обладают хорошей пластичностью и стойкостью к образованию трещин при горячей пластической деформации. По химическому составу близки к дуралюминам, отличаясь более высоким содержанием кремния. Сплавы склонны к коррозии под напряжением. Детали следует анодировать или защищать лакокрасочными покрытиями.Сплавы удовлетворительно соединяются точечной и шовной сваркой, а сплав АК8 — аргонодуговой. Прочность сварного шва составляет 0,6—0,7 σв основного материала. Сплавы хорошо обрабатываются резанием.
17.Деформируемые алюминиевые сплавы. Дюралюмины; высокопрочные и жаропрочные сплавы. Деформируемые - обладают высокой пластич основа структуры сплава - твердый раствор легирующих элементов в алюминии. Для деформируемых сплавов характерна структура твердого раствора с наибольшим содержанием эвтектики. Деформируемые алюминиевые сплавы применяют для получения листов, ленты, фасонных профилей, проволоки и различных деталей штамповкой, прессованием, ковкой. Главным легирующим элементом этих сплавов — дюралюминов — явл медь с содерж в основном от 3 до 6 %. Mg также служит основным легирующим элементов с содержанием от 0 до 2 %. Высокая прочность сплавов обеспечивается за счет дисперсного упрочнения. Сплавы этой серии имеют очень хорошие усталостные характеристики. Дюралюмины маркируют буквой Д, после которой стоит цифра, обозначающая условный номер сплава. Термическая обработка дюралюминов состоит в закалке, естественном или искусственном старении. Для закалки сплавы нагревают до 500 °С и охлаждают в воде. Естественное старение производят при комнатной температуре в течение 5—7 сут. Искусственное старение проводят при 150 —180 °С в течение 2—4 ч.Высокопрочные сплавы Al – Zn – Mg – Cu (В93, В95, В96Ц) более прочны, чем дюралюминий, обладают лучшей коррозионной стойкостью и применяются для изготовления шпангоутов, лонжеронов, стрингеров. Алюминиевые сплавы часто применяются для изготовления поковок штамповок лопастей винта самолета, рам, поясов лонжеронов, крепежных деталей. Это сплавы АК1, АК6, АК8, АК4.Жаропрочные алюминиевые сплавы системы Al – Cu – Mn (Д20, Д21) и Al – Cu – Mg – Fe – Ni (АК – 4 – 1) применяют для изготовления поршней, головок цилиндров, дисков, лопаток компрессоров и т.д., работающих при температурах до 300°С. Жаропрочность достигается за счет легирования Ni, Fe, Ti, (Д20, Д21, АК – 4 – 1).
18.Деформируемые алюминиевые сплавы. Сплавы повышенной пластичности и коррозионной стойкости. Деформируемые - обладают высокой пластичностью основа структуры сплава - твердый раствор легирующих элементов в алюминии. Для деформируемых сплавов характерна структура твердого раствора с наибольшим содержанием эвтектики. Деформируемые алюминиевые сплавы применяют для получения листов, ленты, фасонных профилей, проволоки и различных деталей штамповкой, прессованием, ковкой.
Буквы АМц и АМг показывают, что сплавы относятся к группам, в которых основными легирующими элементами являются марганец и магний соответственно. Сплавы АМг отличаются высокой коррозионной стойкостью в растворах кислот и щелочей. Сплавы АМг1, АМг2, АМг3, АМг4 имеют высокую коррозионную стойкость к основным видам коррозии как в отожженном так и в нагартованном состонии. Сплавы АМг5, АМг6 склонны к коррозии под напряжением и межкристаллитной коррозии. Для защиты от коррозии листы и плиты из этих сплавов плакируются, а заклепки из АМг5п ставят только анодированными. Сплавы повышенной пластичности- ним относятся технический титан ВТ 1-00, ВТ 1-0 и низколегированные сплавы с алюминием ОТ4-0 и ОТ4-1. Предел прочности в отожженном состоянии сплавов составляет 600 МПа, относительное удлинение 10 - 30%. Коррозионностойкие сплавы повышенной пластичности АВ (авиаль), АД 31, АД 33 относятся к системе AL -Mg - Si. Они упрочняются закалкой (520-530 °С) и искусственным старением (160-170 °С, время выдержки 10-12 ч). Эти сплавы удовлетворительно свариваются, обрабатываются резанием в закаленном и состаренном состоянии. Сравнительно недавно разработан еще один класс высокопрочных сталей повышенной пластичности, названный трип-сталями*. Сочетание высокой прочности и пластичности создается подбором определенного состава стали, режимом термической обработки и температурной деформации
19.Кристаллическое строение; основные свойства и назначение магния. Технология производства; основные примеси и маркировка магния. Классификация магниевых сплавов. Основные системы легирования. Маркировка. ГОСТ . Строение магния:в элементарной ячейке гексагональной плотноупакованной решетки содержится семнадцать атомов, которые расположены в углах ячейки и центрах шестигранных оснований призмы и три атома в средней плоскости призмы.
Основные свойства: химический элемент IIА группы третьего периода, атомный номер 12, атомная масса 24,305. Электронная конфигурация нейтрального атома 1s 2 2s 2 p 6 3s 2, согласно которой магний в стабильных соединениях двухвалентен (степень окисления +2). Простое вещество магний — легкий, серебристо-белый блестящий металл.
Назначение:основная часть добываемого магния используется для получения различных легких магниевых сплавов. В состав этих сплавов, кроме магния, входят алюминий, цинк, цирконий. Такие сплавы достаточно прочны и находят применение в самолетостроении, приборостроении и для других целей.
Высокая химическая активность металлического магния позволяет использовать его при магниетермическом получении таких металлов, как титан, цирконий, ванадий, уран и др. При этом магний реагирует с оксидом или фторидом получаемого металла, например:
2Mg + TiO2 = 2MgO + Ti.
2Mg + UF4 = 2MgF2 + U.
Широкое применение находят многие соединения магния, особенно его оксид, карбонат и сульфат.Получение:Обычный промышленный метод получения металлического магния — это электролиз расплава смеси безводных хлоридов магния MgCl2, натрия NaCl и калия KCl. В этом расплаве электрохимическому восстановлению подвергается хлорид магния: MgCl2 (электролиз) = Mg + Cl2.
Расплавленный металл периодически отбирают из электролизной ванны, а в нее добавляют новые порции магнийсодержащего сырья. Так как полученный таким способом магний содержит сравнительно много — около 0,1% примесей, при необходимости «сырой» магний подвергают дополнительной очистке.
Классификация магниевых сплавов:В зависимости от способа получения изделий магниевые сплавы делят на литейные и деформируемые.
Литейные магниевые сплавы ГОСТ 2856-79 применяют для изготовления деталей литьем. Их маркируют буквами МЛ и: цифрами, обозначающими порядковый номер сплава, например МЛ5. Деформируемые магниевые сплавы ГОСТ 14957-76 предназначены для изготовления полуфабрикатов (листов, прутков, профилей) обработкой давлением. Их маркируют буквами МА и цифрами, обозначающими порядковый номер сплава, например МА5.
20.Методы упрочнения магниевых сплавов. Термическая и термомеханическая обработка магниевых сплавов. Основными элементами, вводимыми в магниевые сплавы для упрочнения, являются алюминий и цинк. Эти элементы ограниченно растворяются в магнии, и поэтому при определенном химическом составе магниевые сплавы можно термически обрабатывать.
Алюминий образует с магнием соединение, а цинк - соединение MgZn,, которые и являются упрочняющими фазами, выделяющимися из пересыщенного твердого раствора при искусственном старении.Характерными особенностями закалки и старения магниевых сплавов являются: 1) длительная выдержка при температуре закалки.
2) возможность закалки с охлаждением на воздухе.
3) длительная выдержка при искусственном старении.
4) необходимость применения при нагреве под закалку специальной защитной среды.
Термическая обработка:Магниевые сплавы подвергают термической обработке, которая позволяет повысить их механические свойства, снять внутренние напряжения в отливках и при этом стабилизировать размеры литых деталей, а также улучшить обрабатываемость резанием. Применяют следующие виды термической обработки: продолжительную выдержку при высокой температуре с последующей закалкой (гомогенизация), отпуск (искусственное старение), отжиг.
В процессе продолжительной выдержки при высокой температуре основная масса включений переходит в твердый раствор, а оставшаяся часть сфероидизируется и улучшаются пластические свойства сплава. Последующая закалка фиксирует однородную структуру, что повышает прочность и пластичность.Процесс старения представляет собой распад пересыщенного твердого раствора с образованием высокодисперсной смеси продуктов распада, обеспечивающей мелкокристаллическое строение отливки.
Термомеханическая обработка:Термомеханическая обработка является одним из методов повышения прочности стареющих деформируемых магниевых сплавов. В практике используют при вида термомеханической обработки: низкотемпературную, высокотемпературную, комбинированную. При низкотемпературной обработке деформация осуществляется в температурной области ниже порога рекристаллизации. Она заключается в закалке с температуры твердого раствора, холодной деформации с последующим старением. Высокотемпературная обработка - нагрев до температуры образования перенасыщенного твердого раствора, горячая пластическая деформация и старение. Комбинированная обработка - нагрев при температуре 490-50 в течение 2ч, подстуживание на воздухе до 300-350, деформирование при этой температуре, деформация вхолодную, старение при 175 в течение 2,5ч.
21.Конструкционные магниевые сплавы средней и повышенной прочности; жаропрочные: сверхлегкие. В зависимости от механич. св-в литейных магниевых сплавов условно делят на 3 группы: 1) сплавы средней прочности (предел прочности при 20° не менее 16 кг/мм2); 2) высокопрочные (при 20° не менее 21 кг/мм2); 3) жаропрочные, пригодные для работы при повышенных температурах (до 250—400° в зависимости от химич. состава).
Сплавы средней прочности МЛЗ и МЛ7-1 системы Mg—Al—Zn термич. обработкой не упрочняются. Сплав МЛЗ отличается повыш. герметичностью. Сплав МЛ7-1 характеризуется повышенным сопротивлением ползучести по сравнению со сплавом МЛ5 и применяется для деталей, длительно работающих при темп-рах 150—200°. Сплав обладает удовлетворит, литейными св-вами и свариваемостью. Отливки получают литьем в песчаные формы.
К высокопрочным относятся сплавы МЛ4, МЛ5, МЛ6 системы Mg—Al—Zn и сплавы МЛ 12 и МЛ 15 системы Mg—Zn—Zr. Для высоко нагруж. деталей широко применяется сплав МЛ5 обладающий хорошими технологич. св-вамиЖаропрочные :
К жаропрочным литейным магниевым сплавам относятся сплавы на основе системы магний — редкоземельный металл — цирконий марок МЛ9 (АМТУ 447-59), МЛ10 (АМТУ 488-63), МЛН (АМТУ 488-63), сплавы марок МЛ 14 (АМТУ 436-59) и ВМЛ1 на основе системы Mg—Th—Zr и сплав ВМЛ2.
Наилучшие св-ва при 20° имеют сплавы МЛ10 и ВМЛ2, обладающие наиболее благоприятным сочетанием высокой прочности и хорошей пластичности. Сплав МЛ9 превосходит сплавы МЛ10 и ВМЛ2 по пределу текучести. Гарантируемые пределы текучести сплавов МЛ9 и МЛ 10 в среднем в 1,5 раза превосходят предел текучести наиболее применяемого литейного сплава MJ15 и находятся на одном уровне с высокопрочными механич. свойства и повышенную плотность.
Сверхлегкие:
Особенностями сверхлегких сплавов являются низкая плотность, повышенная пластичность и обрабатываемость давлением при температурах, значительно более низких, чем обычных магниевых сплавов, высокая удельная жесткость и высокий предел текучести при сжатии, отсутствие чувствительности к надрезу, незначительная анизотропия механических свойств, высокая теплоемкость, хорошие механические свойства при криогенных температурах. Сверхлегкие сплавы могут также использоваться для создания легких композиционных сплавов
Дата добавления: 2019-07-17; просмотров: 312; Мы поможем в написании вашей работы! |
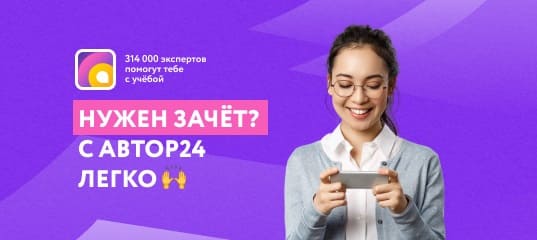
Мы поможем в написании ваших работ!