Технологические решения в фанерном производстве
При проектировании производства фанеры используют обычно типовые схемы, строго увязанные с имеющимся технологическим оборудованием. Основной вариант следующий: хранение сырья на складе, гидротермическая обработка, окорка, раскрой сырья на чураки, лущение шпона, рубка, сушка, починка, склеивание шпона по длине и ширине, сортирование шпона, хранение, нанесение клея, сборка пакетов, холодная подпрессовка, склеивание шпона, обрезка, шлифование, сортирование, починка, упаковка, хранение готовой продукции на складе.
Процесс подготовки сырья к лущению включает операции разделки, окорки и гидротермической обработки, причем последовательность их выполнения может быть различной. Сырье подвергается гидротермической обработке как в окоренном, так и в неокоренном виде. Тот и другой способы имеют свои достоинства – в первом случае ускоряется процесс прогрева чураков при гидротермической обработке и меньше загрязняются бассейны, во втором – создаются лучшие условия для работы окорочного оборудования.
Гидротермическая обработка производится для повышения пластичности древесины и может осуществляться путем прогрева в воде или пропаривания. Последний способ применяется, как правило, в тех случаях, когда нежелательно изменение цвета древесины (например, при производстве строганого шпона из древесины ценных пород). Гидротермическая обработка древесины может осуществляться при жестких режимах (температура выше 60°С) или мягких (температура 40°С) в бассейнах, загружаемых пучками.
|
|
Окорка сырья способствует повышению производительности лущильных станков, повышению качества шпона и создает условия для комплексного использования отходов.
Разделка кряжей на чураки может производиться групповым или индивидуальным способом. В первом случае все кряжи независимо от качества раскраивают по одной, заранее установленной, схеме. Во втором случае каждый кряж раскраивается по индивидуальной, наиболее выгодной, схеме с учетом расположения пороков. Такой способ позволяет улучшить использование сырья, поэтому является более предпочтительным.
Технологический процесс изготовления шпона включает лущение чураков, рубку ленты шпона, сушку, сортировку, починку и склеивание кусков шпона в полноформатные листы. Для лущения чураков в нашей стране используются лущильные станки отечественного производства типа ЛУ-17, а также финского. Раскрой ленты шпона на форматные листы выполняется ножницами различной конструкции. Наибольшее распространение в нашей стране получили отечественные автоматические ножницы типов НФ-18, НФ-18-3. Прирезка кускового шпона производится ножницами типов НФ-18-2, НФ-18-4, НФ-10-2. В деревоперерабатывающей отрасли широкое распространение получило также импортное оборудование. Наиболее перспективным оборудованием для рубки ленты шпона являются ножницы роторного типа, которые обеспечивают высокую точность формирования размера листа и имеют высокую производительность.
|
|
Как правило, лущильные станки и ножницы комплектуются в линию, в которую включаются также конвейеры-петлеукладчики и укладчики листов форматного шпона.
Для сушки шпона наибольшее распространение получили ленточные сетчатые и роликовые сушилки. В ленточных сушилках шпон транспортируется между парными непрерывно движущимися металлическими сетками. Такие сушилки используются в основном для сушки шпона в виде, непрерывной ленты, а также строганого шпона.
В роликовых сушилках листы шпона перемещаются системой приводных парных роликов. По схемам циркуляции агента сушки сушилки могут быть с продольной поперечной циркуляцией и с сопловым дутьем перпендикулярно поверхности шпона. Последние наиболее перспективны, так как значительно интенсифицируют процесс сушки.
По виду агента сушки сушилки разделяются на паровые и газовые. Более прогрессивными являются газовые сушилки, поскольку производительность их в 2…3 раза выше, чем паровых.
|
|
Сухой шпон можно сортировать как ручным, так и механизированным способом. При ручном способе и ограниченных производственных площадях сортировку выполняют на специальной площадке. Однако в связи с большим количеством перекладок шпона ухудшается его качество.
При наличии достаточных площадей шпон сортируют непосредственно у сушильного агрегата или с ленточного конвейера, установленного под углом 90° к сушилке. В последнем случае наряду с сокращением количества перекладок улучшаются условия труда, однако резко возрастает потребность в производственной площади.
Починка шпона выполняется на полуавтоматических шпонопочиночных станках. Для получения форматных листов из кускового шпона применяют ребросклеивание. Перед ребросклеиванием кромки кусков шпона выравниваются на кромкофуговальных станках или гильотинными ножницами. Предпочтительнее использовать для этой цели гильотинные ножницы, поскольку они более производительны, однако кромкофуговальные станки дают более чистую и прямолинейную кромку. Станки эффективны при склеивании на ребро без применения клеевой нити или гуммированной ленты.
|
|
Для соединения по длине листы шпона склеивают на ус. Операцию производят на усовочных станках типов УС и 2УС, а склеивание – на узкоплитных прессах.
Процесс склеивания фанеры включает следующие операции: нанесение клея на шпон, сушку шпона с нанесенным клеевым слоем (для фенолоформальдегидных клеев), сборку пакетов, выдержку перед подпрессовкой (кроме фенолоформальдегидных клеев), склеивание пакетов в прессе.
Наносить клей на шпон можно контактным, экструзионным способами, а также способами налива или распыления. Наибольшее распространение получил контактный способ нанесения с применением вальцовых клеенаносящих станков.
Операции сборки пакетов и их подпрессовки могут выполняться на отдельном участке или в составе поточной линии. Склеивают фанеру на многоэтажных гидравлических прессах. Прессы могут применяться как в качестве позиционного оборудования, так и в составе линий.
Обработка фанеры включает операции обрезки, шлифования, починки и сортировки. Обрезка фанеры производится на круглопильных станках. Фанеру можно обрезать как пачками, так и по одному листу. В первом случае обеспечиваются высокая производительность и качество обрезки, однако увеличиваются переобрез и трудоемкость операций загрузки и выгрузки пачек фанеры.
Шлифуют фанеру на цилиндровых и широколенточных шлифовальных станках. Из отечественного оборудования наибольшее распространение получили цилиндровые станки. При этом производительность широколенточных станков в 3…4 раза выше, чем цилиндровых. Починка фанеры производится вставками или замазками (шпатлевками). Применение шпатлевок более предпочтительно вследствие малой трудоемкости процесса. Наносят шпатлевку вручную шпателем или вальцовыми станками. Сортировка фанеры обычно выполняется вручную.
Отделка фанеры может производиться различными способами. Наибольшее распространение получили следующие: метод печатания текстуры с последующим лакированием; метод ламинирования; облицовывание стекловолокнистыми материалами, пропитанными полиэфирными смолами, или рулонными пленками.
Возможны некоторые варианты технологического процесса:
– при переработке хвойного и ольхового сырья гидротермическая обработка кряжей может выполняться после их окорки, что позволяет несколько сократить время гидротермической обработки, исключить загрязнение бассейна корой;
– при лущении чураков хвойных пород после раскроя ленты шпона на листы может быть предусмотрено подсортирование сырого шпона на заболонный и ядровый, поскольку вследствие большой разницы влажности требуется для получения одинаковой конечной влажности шпона сушка при различных режимах;
– сушка шпона может быть предусмотрена после получения ленты шпона на лущильном станке, что позволит увеличить выход шпона на 2...3 % при его раскрое;
– при переработке сырья больших диаметров, особенно высокого качества, проводят вырезку участков ленты шпона, содержащих крупные дефекты, за счет чего исключается операция починки шпона и ее заменяют ребросклеиванием полос шпона в форматные листы;
– при изготовлении большеформатной фанеры вследствие невозможности изготовления цельных наружных слоев фанеры в технологический процесс добавляется операция, обеспечивающая склеивание на ус наружных слоев из двух слоев шпона;
– при изготовлении большеформатной фанеры соединением двух листов на мини-шипы предусматриваются дополнительные операции по формированию на торцовых кромках мини-шипов, нанесение клея на их поверхности и запрессовки;
– при изготовлении строительной, опалубочной фанеры, фанеры для производства контейнеров и кузовов должна быть предусмотрена операция антисептирования шпона или самой фанеры;
– при изготовлении декоративной фанеры необходимо облицовывание фанеры пленками на основе пропитанных текстурных бумаг.
Выбор варианта технологического процесса изготовления фанеры зависит, таким образом, от вида сырья, ассортимента продукции, имеющегося технологического оборудования.
4.3.4. Технологические решения в производстве древесно-стружечных
плит
Сырьем для производства древесно-стружечных плит могут служить неделовая и тонкомерная древесина, кусковые и мягкие отходы лесопиления, деревообработки, фанерного производства, лесозаготовок, а также технологическая щепа. В зависимости от вида используемого сырья, вида связующего и назначения плит технологический процесс может строиться по-разному. В общем виде технологический процесс производства древесно-стружечных плит включает следующие этапы:
– подготовку сырья;
– изготовление стружки;
– сушку стружки;
– сортировку стружки;
– приготовление связующего;
– смешивание стружки со связующим;
– формирование стружечных пакетов;
– холодную подпрессовку стружечных пакетов;
– горячее прессование плит;
– кондиционирование плит;
– форматную обрезку;
– шлифование и сортировку.
Технологические схемы производства древесно-стружечных плит условно разделяют по двум характерным признакам: по конструкции плит и способу формирования стружечного ковра (на поддонах и без поддонов). Наибольшей простотой отличается технологический процесс изготовления однослойных и многослойных плит. За исключением операции формирования стружечного ковра, при изготовлении однослойных и многослойных плит по этой схеме применяется однотипное оборудование.
В нашей стране получило распространение производство трехслойных древесно-стружечных плит. Характерной особенностью технологического процесса производства трехслойных плит является наличие двух потоков изготовления стружки и подготовки пресс-массы (Рис. 18). При этом потоки внутреннего и наружного слоев отличаются друг от друга как по типам применяемого оборудования, так и по технологическим режимам. Наружные слои трехслойных древесно-стружечных плит изготовляются из высококачественной резаной стружки с повышенным содержанием связующего. Их качество выше, чем одно- и многослойных плит, хотя технология изготовления сложнее. Особенностью производства пятислойных ДСтП является наличие трех самостоятельных потоков.
![]() |
Рис. 18 Технологическая схема производства трехслойных древесно-стружечных плит |
Начальной стадией технологического процесса производства древесно-стружечных плит является подготовка сырья. При переработке неделовой тонкомерной древесины ее разделывают на чураки длиной 1 м на станках типа ДЦ-10. На разделку по длине кругломерная древесина должна подаваться поштучно, поэтому перед станком ДЦ-10 устанавливают разобщитель бревен. После разделки по длине чураки большого диаметра раскалывают на механических или гидравлических дровокольных станках. Для обнаружения металлических включений применяют электронные металлоискатели. Резаную стружку получают путем переработки чураков на дисковых стружечных станках или станках с ножевым валом. В нашей стране наибольшее распространение получили станки с ножевым валом типов ДС-6, ДС-8. Как правило, специальная резаная стружка, полученная на таких станках, калибруется по длине и ширине. Для этой цели отечественной промышленностью выпускаются молотковые дробилки типа ДМ-7, которые используются для калибрования стружки как для наружных, так и для внутреннего слоев.
В производстве древесно-стружечных плит с микроструктурной поверхностью микростружку для наружных слоев получают в лопастных мельницах или в стружечных станках, оснащенных зубчато-ситовыми барабанами.
Кругломерное сырье и кусковые отходы перерабатывают в щепу на дисковых и барабанных рубильных машинах. Отечественная промышленность выпускает ряд дисковых рубильных машин с различными расположением патрона и производительностью. Барабанная рубильная машина предназначена для переработки в щепу отходов лесозаготовок, лесопиления, мелких кусковых отходов деревообработки длиной не менее 100 мм, а также шпона-рванины.
Щепа, полученная на рубильных машинах, разделяется на фракции. Для этой цели используются гирационные сортировки типов СЩ-1, СЩ-1М и СЩ-120. Крупная фракция возвращается на повторное измельчение, а отсортированная кондиционная щепа направляется в бункер запаса. Превращение щепы в стружку осуществляется с помощью центробежных стружечных станков типов ДС-5 и ДС-7, которые просты по конструкции и имеют высокую производительность.
Для хранения межоперационных запасов щепы и стружки, а также дозированной подачи их на очередной этап технологического процесса разработаны вертикальные бункеры. Щепа из бункера поступает по ленточным конвейерам к стружечным станкам.
Для сушки измельченных древесных частиц на отечественных производствах используют сушильные барабаны. Смесь стружки и топочных газов движется по трубе циклонной приставки снизу вверх, при этом влажность стружки снижается от 120 до 20…30 %. Сушильные барабаны устанавливаются с отрицательным углом от 2 до 3° для повышения коэффициента заполнения барабана и увеличения продолжительности пребывания высушиваемой стружки в барабане.
После сушки стружка разделяется на фракции с помощью механических сортировок и подается через вертикальные бункеры и дозаторы в смесители. Дозирование стружки при подаче в смеситель может осуществляться по объему и массе.
Дозирование компонентов, приготовление и подача связующего в смесители производятся с помощью установок ДКС-1 и ДКС-2 непрерывного действия конструкции ВНИИДМАШ. Для смешивания стружки со связующим применяют высокооборотные смесители с безвоздушным распылением связующего.
Формирование пакетов из стружечно-клеевой смеси и их прессование происходят на автоматической линии - главном конвейере. Наибольшее распространение в производстве древесно-стружечных плит получили четыре типа главных конвейеров: 1) для формирования пакетов и прессования плит на жестких металлических поддонах; 2) формирования стружечного ковра и горячего прессования плит на непрерывной гибкой стальной ленте; 3) формирования стружечного ковра на непрерывной ленте из гибких синтетических поддонов и горячего прессования плит без поддонов; 4) формирования стружечного ковра и горячего прессования плит на гибких проницаемых металлических поддонах
Для подпрессовки стружечных пакетов использован одноэтажный гидравлический пресс ПР-5 с верхней подвижной плитой и верхним расположением цилиндров.
Для горячего прессования плит в конвейере устанавливаются многопролетные гидравлические прессы типа ПР-6 (ПР-6А, ПР-6Б - модернизированные) или Д4743.
После горячего прессования перед механической обработкой плиты необходимо кондиционировать или охлаждать с целью выравнивания температуры, влажности и внутренних напряжений по сечению.
Плиты обрезают по формату на четырехпильных форматно-обрезных станках. Станки представляют собой два спаренных двух-пильных агрегата, расположенные перпендикулярно друг другу. Отрезаемые рейки измельчаются фрезами и удаляются пневмотранспортной системой.
После обрезки плиты поступают на участок калибрования и шлифования. Для осуществления этих операций на отечественных производствах используют линии типов ДЛШ-50М и ДЛШ-100, основным агрегатом которых является калибровочно-шлифовальный широколенточный станок ДКШ-1. Шлифованные и сортированные плиты транспортируют на склад автопогрузчиками и укладывают на деревянные поддоны в штабели высотой до 4,5 м. Штабели устанавливают на расстоянии не менее 1,5 м от дверей и 0,5 м - от стен. Между штабелями должны быть проезды шириной не менее 2,5 м, ширина главного проезда - не менее 5 м. Температура помещения должна быть не ниже 10°С, а относительная влажность воздуха - не выше 65 %. Площадь склада определяют исходя из 5…7 суточного запаса плит.
4.3.5. Технологические решения в производстве изделий из массивной
древесины
Мебельное производство
Технология изготовления сравнительно сложного изделия состоит из нескольких этапов, которые применительно к условиям деревообработки принято называть стадиями. Стадии в свою очередь делятся на операции. Операция – законченная часть технологического процесса, выполняемая на одном рабочем месте. Определение содержания и последовательности операций является основой разработки технологического процесса. Также операция является основной единицей производственного планирования. По операциям технологического процесса определяют потребность и квалификацию рабочих, вид оборудования, затраты труда и т.п. Являясь неделимой с точки зрения планово-организационных отношений, операция с точки зрения технологии может состоять из нескольких частей, называемых переходами. Переход - часть технологической операции, выполняемая одними и теми же средствами технического оснащения при неизменных технологических режимах и установке.
Также операции могут делиться на проходные и позиционные. Проходными называют операции, при выполнении которых обработка детали производится с одного до другого ее конца, то есть она перемещается через станок, проходя его из конца в конец. Позиционными называют операции, требующие закрепления детали в станке, причем необходимое для обработки движение получает инструмент.
Следует отметить, что все изделия из древесины состоят из четырех конструктивных элементов: бруски, щиты, рамки, коробки. Если учесть, что рамки и коробки, в свою очередь, собираются из брусков и щитов, то практически можно считать, что изделия состоят из комбинаций двух конструктивных элементов: брусков и щитов.
Поступающее в производство сырье – пиломатериалы, черновые заготовки и др. обязательно должны пройти этап сушки. Сушка может быть произведена в досках или после раскроя досок в заготовках. Поэтому технологический процесс производства изделий из массивной древесины может начинаться как с раскроя пиломатериалов на заготовки, так и с процесса сушки пиломатериалов.
В некоторых случаях отдельные стадии могут отсутствовать (гнутье, склеивание). Нанесение защитно-декоративных покрытий может осуществляться перед сборкой, что особенно характерно для щитовых деталей.
Общую структуру технологического процесса производства изделий из массивной древесины можно представить в виде схемы Рис. 19.
Стадии технологического процесса для брусковых и щитовых деталей в значительной степени отличаются друг от друга, как по виду операций, так и по применяемому оборудованию.
Технологическая схема производства щитовых элементов корпусной мебели представлена на Рис. 20.
В технологии производства корпусной мебели существует многообразие технологических схем, вызванное применением новых синтетических облицовочных материалов и методов облицовывания.
Рис. 19 Структурная схема производства изделий из массивной древесины
Рис. 20 Структурная схема производства щитовых деталей
Выбор технологических процессов изготовления изделий является основной и наиболее сложной операцией проектирования. В ходе разработок должны быть выбраны наиболее рациональные способы и средства изготовления каждой детали изделия. При большом разнообразии способов и средств производства при изготовлении мебели одни и те же детали можно изготовить по различным технологическим процессам с использованием различного оборудования, инструмента и приспособлений. При этом трудоемкости изготовления определенных деталей могут различаться в несколько раз.
Существенного снижения трудоемкости изготовления можно добиться при изменении конструкции изделия и его элементов. Поэтому перед разработкой технологического процесса изготовления изделия и его элементов необходим анализ технологичности конструкции. Особенно это важно при освоении новой продукции на действующем производстве с использованием конкретного оборудования и др. При выборе технологического процесса для нового строительства используется расчетный набор мебели. Количественными показателями технологичности, характеризующими эффективность конструктивно-технологических решений, являются трудоемкость (нормо-ч), материалоемкость (р.), себестоимость (р.).
Качественный анализ уровня технологичности изделия производится путем проверки соответствия конструкции изделия следующим требованиям, обеспечивающим снижение трудоемкости: стандартизация и унификация составных частей изделия, элементов деталей и др.; возможность применения типовых технологических процессов, что позволяет повысить уровень механизации и автоматизации производства, сократить сроки технологической подготовки производства; рациональное членение изделия на составные части для возможности параллельной сборки узлов, сокращения цикла общей сборки; ограничение и сокращение номенклатуры используемых материалов, в результате чего упрощается снабжение производства необходимыми материалами.
Технологичность конструкции в значительной степени зависит от выбора материала. Например, при применении ДСтП можно отказаться от рамочной конструкции. При применении ламинированных ДСтП для изготовления щитовых элементов мебели снижается трудоемкость их изготовления за счет исключения таких операций, как подготовка облицовок, шлифование и облицовывание пластей, крашение и отделка пластей, комплектация щитов по текстуре и цвету.
В результате выбора рациональной конструкции изделия, включая вид соединения его элементов, повышается технологичность изделия: переход от опорных скамеек на вертикальные проходные опорные щиты, переход от секционной к универсально-сборной мебели, что исключает необходимость применения сдвоенных горизонтальных и вертикальных щитов, шкантовых соединений, соединений на стяжках и т. д.
Выбор варианта обработки зависит от многих факторов: формы, размеров и материала деталей, требуемой точности обработки и шероховатости поверхности, масштаба выпуска, требований к отделке и др. В проектах реконструкции приходится еще учитывать существующую производственную обстановку: наличный парк оборудования и его состояние, размеры и форму помещений и т. п.
Состав операций процесса и последовательность их выполнения определяются прежде всего формой детали. В соответствии с этим осуществляется и выбор типов оборудования. Размеры детали оказывают влияние на выбор конкретной марки станка данного типа оборудования, инструмента и оснастки. Материал детали влияет на выбор режимов обработки, размеры припусков, вид режущего инструмента. Повышенные требования к точности обработки и шероховатости поверхности обусловливают необходимость применения оборудования высокой точности и введения в технологический процесс дополнительных операций.
Существенное влияние на выбор способов и средств изготовления изделий оказывает объем производства. Так, при небольшом объеме производства и частой сменяемости изделий целесообразно применять универсальное легко переналаживаемое оборудование. При массовом производстве изделий эффективно использование специализированного и специального оборудования, включая автоматические и полуавтоматические линии, обрабатывающие центры.
Схемы технологических процессов выбирают в результате анализа типовых схем, достижений передовых производств в этой области, результатов научно-исследовательских работ и изобретений. Анализ включает оценку технической, организационной и экономической целесообразности различных способов.
Техническая целесообразность вариантов выявляется при сопоставлении таких показателей, как качество изготовления изделий, степень использования сырья и материалов, производительность труда и оборудования, уровень интенсивности использования оборудования, использование производственных площадей, квалификация рабочих и др.
Основными показателями при организационном анализе являются длительность производственного и технологического циклов, сменность работы оборудования, коэффициент загрузки оборудования, размеры партии деталей и др.
Следует отметить, что технические и организационные показатели не выражают совокупности затрат общественного труда. Поэтому помимо этих показателей должны быть сопоставлены экономические показатели различных технологических вариантов.
Наиболее важными общими экономическими показателями являются экономия от снижения себестоимости продукции и срок окупаемости дополнительных капитальных вложений. К частным экономическим показателям относятся трудоемкость (станкоемкость), съем продукции с 1 м2 производственных площадей, энергоемкость продукции, приведенные затраты на единицу продукции, себестоимость обработки детали.
Кроме указанных показателей при выборе оптимального варианта необходимо учитывать следующие факторы:
1) план перспективного развития производства (в проектах реконструкции), т. е. может быть принят вариант технологического процесса, имеющий несколько большие затраты на единицу продукции, но в дальнейшем обеспечивающий объем производства и рентабельность, предусмотренную планом;
2) технологическую специализацию производства (цеха), при которой повышенные затраты компенсируются экономией на других производствах, цехах;
3) требования техники безопасности и промышленной санитарии, причем не может быть принят вариант технологического процесса, не обеспечивающий этих требований.
Сравнение вариантов значительно облегчается тем, что в ряде случаев достаточно определить относительную эффективность только для существенно различающихся операций, а не для всего технологического процесса. Кроме того, предварительный анализ технических и организационных показателей позволяет без громоздких расчетов исключить из рассмотрения заведомо неэффективные варианты.
При широком диапазоне варьирования технических характеристик и режимов работы оборудования анализ технологических процессов должен проводиться на базе математического моделирования с использованием ЭВМ. Критерием оценки оптимальности технологических процессов могут быть приняты удельные приведенные затраты на единицу продукции.
В качестве исходных материалов при разработке технологических процессов используется следующая технологическая документация: производственная программа, чертежи изделий, спецификации и технические описания изделий, ГОСТы или ТУ на выпускаемые изделия. В качестве справочной, нормативной и технической документации литературы рекомендуется использовать ГОСТы, нормали и ТУ на материалы, инструмент, контрольно-измерительные приборы, ГОСТы на допуски и посадки, шероховатость поверхности, припуски на обработку и усушку, нормы расхода основных и вспомогательных материалов, типовые технологические процессы и режимы изготовления элементов изделий, справочные и нормативные материалы для расчета режимов обработки и нормирования трудовых затрат, каталоги производимого оборудования и его паспортные данные, информационные материалы о зарубежном оборудовании и опыте изготовления аналогичных изделий, тарифно-квалификационный справочник и др.
В проектах реконструкции производств или их участков и цехов к исходным данным добавятся результаты анализа существующей организации производства и состояния оборудования, зданий и др.
Выбор оптимального варианта изготовления деталей облегчается использованием разрабатываемых ВПКТИМ и Гипродревпромом типовых технологических процессов (ТП) изготовления деталей и сборочных единиц мебели. Каждый такой процесс, распространяемый на определенную стадию технологического процесса, содержит сведения о рациональном составе и последовательности операций этапа, применяемых при этом материалах и оборудовании, режимах выполнения операций. Подробная регламентация выполнения режимов операций типовых процессов содержится в типовых режимах изготовления мебели (РМ).
Выбор технологического оборудования неразрывно связан с выбором того или иного варианта технологического процесса, причем часто именно оборудование определяет характер технологического процесса.
При выборе оборудования в производстве мебели необходимо также ориентироваться на наиболее совершенные модели станков, агрегатов, автоматических линий, характеризующихся необходимой точностью и высокой производительностью. При этом выбор должен основываться на использовании главным образом серийно выпускаемого оборудования и лишь в виде исключения допускать применение нетипового. Импортное оборудование может использоваться при наличии фондов или закупленного оборудования зарубежных фирм. При реконструкции производства следует использовать имеющееся оборудование, если оно не устарело физически и морально.
Дата добавления: 2019-07-15; просмотров: 469; Мы поможем в написании вашей работы! |
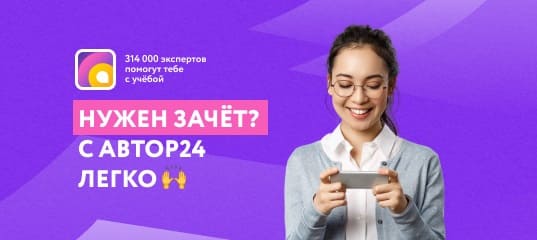
Мы поможем в написании ваших работ!