Восстановление кузовов грузовых и пас. вагонов при деповском ремонте
Деповский ремонт производят в вагонных депо. Являясь промежуточным между заводскими ремонтами, он предназначен для поддержания вагонов в исправном состоянии до очередного периодического ремонта.
Грузовые: Правка элементов кузова осущ. как в нагретом состоянии, так и в холодном (при незначит. деформ.). Если деформации стоек и раскосов незначит., то правка осуществл. на месте. При больших деформациях стойки, раскосы и другие детали снимаются и выправл. в спец. кондукторах. Места металлических стен полувагонов, пораженные коррозией или поврежд., вырезаются и на их место привариваются накладки.
При ремонте котлов цистерн широко применяются сварочные работы. Сварку в котле цистерны без съема его с рамы рекомендуется производить постоянным током, имея в виду необходимость наложения большого числа потолочных швов. Продольные трещины в котле раздеываются и завариваются с постановкой усиливающих кусковых накладок. Трещины, расположенные в местах пересечения продольных и круговых швов в броневом листе и обечайках, завариваются после зачистки с наружной и внутренней сторон котла и сверловки отверстий с раззенковкой по концам. Старый продольный шов между броневым листом и обечайкой вырубается. С внутренней стороны котла вырубается V-образная фаска по трещине в круглом шве, а с наружной стороны − по трещине броневого листа. Трещины в швах колпака и в продольном шве броневого листа над опорами завариваются наложением шва в два слоя с наружной стороны котла после вырубки старого дефектного шва. Швы соединения колпака с цилиндрич. частью котла, имеющие трещины, подвариваются также наложением шва с внутр. стороны. При угловом расположении трещин ставится кольцеобразная накладка. Места, поврежденные большим количеством трещин, вырезаются и усиливаются сплошной накладкой. При большом количестве повреждений в обечайках и днищах котлов или при толщине котла менее половины альбомной обечайки и днища заменяются новыми. Приварка новой части может производиться как в стык, так и внахлестку. Сливные приборы цистерн всех типов вне зависимости от их состояния полностью разбираются и все детали восстанавливаются до альбомных размеров. После ремонта сливные приборы испытываются гидравлическим давлением 5 атм на спец. стенде. Качество ремонта котлов цистерн проверяется внешним осмотром, обстукиванием молотком сварных швов и гидравлическим испытанием.
|
|
Пассажирские: При поражении коррозией или наличии пробоин в обшивке кузова привариваются накладки с наружной и внутр. сторон с последующей зачисткой швов. Местные плавные вмятины в крыше и металлич. полу глубиной не более 15 мм оставляются без исправл. при отсутствии деформаций в обрешетке крыши и балках пола. Незначит. повреждения в крыше, дающие течь, устраняются пайкой. Полученные от ударов вмятины на боковых стенах, превыш. 5 мм на 1 пог. м длины, выправляются. Вмятины в нижней закругл. части стены ремонтируются накладками в уровень со стеной, привариваемыми дуговой сваркой с зачисткой швов заподлицо. Части гофрир. пола, пораженные коррозией, вырезаются и вместо них привариваются гофрированные накладки (вставки), с перекрытием кромок. На пол изотермического вагона укладываются блоки изоляции, покрываемые слоем рубероида. Швы рубероида склеиваются гудроном, а поверх рубероида вся площадь изоляции пола заливается горячим гудроном слоем 2-3 мм. Доски пола должны быть заранее загрунтованы. При укладке они промазываются по шпунтам или четвертям горячим гудроном и пригоняются плотно, с натягом. Углы соединения пола со стенами кузова промазываются горячим гудроном, после чего прибиваются деревянные угловые штапики. Сверху пол также заливается горячим гудроном слоем 2-3 мм, а затем покрывается оцинкованной сталью, а швы и головки гвоздей пропаиваются припоем.
|
|
|
|
Система технического обслуживания и ремонта колёсных пар вагонов
Основным техническим документом определяющим требования к КП является “Инструкция по осмотру, освидетельствованию, ремонту и формированию вагонных КП”. Она определяет контроль технического состояния и своевременность изъятия из эксплуатации КП, угрожающих безопасности движения поездов, а также контроль за качеством подкатываемых и отремонтированных КП. Инструкцией установлена система технического обслуживания КП состоящая из: 1)осмотра КП под вагонами, находящимися в эксплуатации, и замене неисправных; 2)освидетельствование (контроля) КП, которое может быть обыкновенным или полным; 3) полное освидетельствования. Под вагонами КП осматривают осмотрщики вагонов, а при текущем отцепочном ремонте – мастер иди бригадир. Осмотр КП выполняется: 1)на станциях форм-ния и расформ-ния поездов с ходу в момент прибытия, после прибытия и перед отправлением; 2)в пунктах подготовки вагонов к перевозкам; 3)перед постановкой вагонов в поезд; 4)при текущем отцепочном и профилакт. ремонте вагонов. Освидетельствование КП. КП с буксовыми узлами, выкаченные из-под тележек поступают в деповской или текущий отцепочный ремонт, подлежат входному техническому контролю при котором: 1)их размерный контроль, проверка клейм и производственный осмотр до очистки с целью выявления ослабления ступиц колес и трещин в осях и колесах по внешним признакам; 2)механическая очистка средней части оси и ее магнитная дефектоскопия; 3)контроль буксовых узлов грузовых вагонов. Обыкновенное освидетельствование КП выполняется при каждой подкатке КП под вагоны, если перед этим они не подвергались полному освидетельствованию. Полное освидетельствование КП – основной вид техн. состояния КП по результатам которого им назначается ремонт без смены элементов и со сменой элементов. Выполняется: 1)при формировании и переформировании КП; 2)при опробовании КП на сдвиг; 3)при капитальном ремонте; 4)при деповском и текущем отцепочном ремонте; 5)после крушений и аварий поездов; 6)после сходов вагонов с рельс; 7)при неясности клем и знаков; 8)при полной ревизии букс. КП проходят ремонт: 1) без смены элементов, кот. вып-ся в условиях вагонных депо и вагоноремонтных заводах; 2) со сменой элементов, в условиях вагоноремонтных заводах и вагоноколесных мастерских. Основной задачей, решаемой при ремонте без смены элементов, является восстановление геометрии поверхности катания колеса и гребня обточкой на колесотокарных станках. При обточке КП ободьям придается альбомный профиль, которых контролируется токарем с помощью максимального шаблона. Наличие на поверхности катания участков с дефектами термомеханического происхождения вызывает большие ударные нагрузки при обработке, отрицательно сказывающиеся на режущем инструменте и оборудовании, вынуждает снижать параметры режимов резания или дополнительно врезаться резцом на глубину 1,5-2 мм, что срезает полезный слой металла и сокращает срок службы КП.
|
|
22.Неисправности буксовых узлов вагонов
Основными неисправностями буксовых узлов с роликовыми подшипниками являются: износы, изломы сепараторов, разрушение деталей крепления подшипников, обводнение смазки, ослабление натяга внутренних и лабиринтных колец, изломы и разрывы внутренних и упорных колец подшипников.
Износ и разрушение сепараторов, как правило, происходят из-за обводнения или недостаточного количества смазки в подшипниках, а также из-за механических повреждений сепараторов, не выявленных при полной ревизии буксы. В настоящее время необходимо обязательно проводить вихретоковый контроль сепараторов, обращая особое внимание на состояние мест перехода от перемычек к основанию. Причинами попадания влаги в смазку является неправильное ее хранение и нарушение технических требований к монтажу буксы.
Основная причина разрушения торцового крепления подшипников на шейке оси – нарушение требований монтажа букс: завышение зазоров между кольцами, неправильный подбор и установка гаек М110. Следует тщательно контролировать состояние резьбы гаек и шеек осей. Проворот колец происходит из-за нарушения температурных режимов при монтаже букс, применение несовершенных измерительных приборов и инструментов или неправильной их настройки.
Изломы колец происходят из-за нарушений требований неразрушающего контроля колец без снятия их с шеек осей, а также из-за значительных нагрузок на подшипники.
Колесная пара идет юзом при отжатых тормозных колодках, слышны скрежет, пощелкивание, виден дым или искрение со стороны лабиринтного кольца при движении вагона – Разрушение подшипника, проворот внутреннего кольца заднего подшипника на шейке оси.
Букса смещена вдоль шейки оси, вздутие краски, окалина, деформация смотровой и крепительной крышек – Разрушение подшипника, повреждение торцевого крепления подшипника на шейке оси.
Корпус буксы наклонен по отношению к шейке оси, боковая рама тележки опирается на корпус буксы одним краем – Проворот внутреннего кольца переднего подшипника на шейке оси.Выброс смазки на диск и обод колеса, потеки смазки через смотровую и крепительную крышки, наличие валика смазки с металлическими включениями на лабиринтной части корпуса буксы – Разрушение подшипника, повреждение торцевого крепления подшипников на оси, обводнение смазки.При остукивании смотровой крышки ниже ее центра слышно дребезжание или двойной металлический отзвук (отбой) – Повреждение торцевого крепления подшипников на оси.Появление дыма, запаха из буксы – Неисправность полиамидного сепаратора подшипника.Повышеный нагрев корпуса буксы, в сравнении с другими буксами этогоже вагона – Излишнее количество смазки (после ремонта или ревизии буксы), начало разрушения подшипников.
23. Изготовление литых деталей тележек грузовых вагонов
Боковины и надрессорные балки представляют собой монолитные детали сложной формы, которые отливают из стали выплавленной в мартеновских и электропечах. Технологический процесс изготовления литых боковин и надрессорных балок предусматривает следующие операции:
- приготовление формовочных и стержневых смесей;
- приготовление жидкого металла;
- формовку, разливку металла по формам;
- охлаждение отливок;
- выбивку опок;
- обрубку и зачистку отливок;
- термическую и механическую обработку;
- контроль качества.
Формовочные и стержневые смеси приготавливаются в закрытых бегунах, с механизированной дозировкой составляющих и автоматическим управлением. Исходным материалом для формовочной смеси служат: горелая земля и кварцевый песок, которые смешивают с огнеупорной глиной, древесно-угольным песком и сульфитной щёлочью. Стержневая смесь приготавливается из сухого кварцевого песка, молотой глины, сульфитной щёлочи и специального крепителя. Литейные формы для боковин и надрессорных балок состоят из верхней и нижней полуформ. В каждой полуформе заформовывают по 2 боковые рамы или надрессорные балки. Формы изготавливаются на встряхивающих пневматических формовочных машинах или способом дифференциального прессования на специальных формах. После окончания формовки из полуформ удаляют модели отливок, для удаления газов создаются газоотводные каналы, устанавливают холодильники и другие технические элементы. На этом процесс изготовления полуформ завершается.
Собранные формы заливают из ковшей при температуре стали 1440-1470°С. Затем формы охлаждают. После охлаждения из форм выбивают стержни на механических инерционных решётках, после чего отливки направляют на очистку в проходных камерах оснащенных дробемётными аппаратами. Очищенные отливки поступают для обрезки приливов и исправление дефектов. Термическая обработка боковин осуществляется в специальных печах с нагревом до температуры 915±5°С, выдержка в них в течение 4-х часов. Остывание на воздухе. Надресорные балки после нагрева до 900°С выдерживают в печи 2,5 часа. После термообработки
производится зачистка полостей буксовых проемов боковины и сверление отверстий в кронштейнах подвеса башмаков. Далее сверлятся отверстия под заклепки фрикционных планок и крепятся планки с помощью гидравлической скобы. При обработке надрессорной балки выполняются следующие операции: а) сверление двух отверстий для крепления державки “мертвой точки” рычажной передачи тормоза; б) расточку подпятника (основание, торец наружного борта и торец шкворневого прилива); в) приклепку державки.
24.Неисправности кузовов вагонов
1. Обрыв сварного шва соединения стойки с обвязкой или балкой рамы, обрыв раскоса
2. Повреждения крыши, обшивки, пола, потолочных или боковых люков, в результате чего груз может намокнуть, выпасть на путь или быть похищенным, неисправность кровли, создающая опасность отрыва ее листов.
3. Отсутствие двери или дверного упора, повреждение крепления или изгиб дверных рельсов или повреждение направляющих, угрожающие падением двери на путь.
4. Перекос кузова более 75 мм.
5. Зазор между шкворневой балкой и боковой рамой тележки у груженых цистерн менее 30 мм.
6. Уширение кузова вагона более 75 мм на одну сторону.
7. Отсутствие крышки люка или створки двери у полувагона, обрыв хотя бы одного шарнирного соединения в крышке люка, неисправность запора крышки люка или торцевых дверей, которая может вызывать самопроизвольное их открывание или падение.
8. Излом верхней обвязки полувагона.
9. Повреждения бортов, досок и металлического настила пола, петель и запоров у платформы, которые могут вызвать падение бортов, груза или выход их за габарит.
10. Специализированные платформы, груженые крупнотоннажными контейнерами, у которых в узлах крепления контейнера хотя бы один фитинговый упор отсутствует либо не фиксируется в вертикальном рабочем положении, погнут, имеет трещину.
11. Трещины в котлах цистерн, которые вызывают течь груза, продольные и поперечные трещины в опорных листах и местах их приварки к котлам безрамных цистерн длиной более 300 мм.
12. Неисправности сливных приборов у цистерн, приводящие к потере груза, отсутствие запорных крышек сливных приборов.
13. Открытые крышки сливных приборов, крышки колпаков и откидных колпаков специальных цистерн.
14. Отсутствие, ослабление или обрыв пояса котла цистерны, сдвиг котла.
15. Неисправности и повреждения, нарушающие прочность крепления поручей, подножек и переходных площадок.
16. Открытые загрузочные люки, не зафиксированные специальным фиксатором штурвалы привода механизма разгрузки у вагонов для перевозки цемента, трещины в сварных соединениях кронштейнов крепления привода механизма разгрузки, обрыв крепления крышки загрузочного люка вагона-хоппера для зерна.
17. Трещины и пробоины кузовов, неисправности механизмов разгрузки, приводящие к потере груза, у вагонов для перевозки минеральных удобрений, окатышей и агломерата.
18. Открытые переездные площадки у платформ для перевозки автомобилей.
19. В вагонах-думпкарах кроме указанных неисправностей не допускаются:
• повреждение механизма открывания бортов, механизма блокировки, проворачивания собачки, отогнутый или не совпадающий с опорой более 15 мм шип;
• отсутствие противовеса валика или шплинта в рычагах механизма открывания бортов или валика опоры кузова;
• ослабление болтов крепления корпуса амортизатора;
• излом ушка разгружающего цилиндра, обрыв упоров от перемещения кузова.
25.Неисправности рам вагонов
Наиболее распространёнными неисправностями рам грузовых вагонов является образование в них различных трещин и надрывов. Трещины обычно встречаются в местах соединения ударной розетки и концевой балки, на хребтовой балке в местах расположения передних и задних упоров автосцепного устройства и между ними, в сварных швах, соединяющих шкворневую и хребтовую балки. Трещины в промежуточных поперечных балках встречаются редко и в основном в полувагонах. Признаком наличия трещин в элементах рам вагонов, как и в других узлах и деталях, является скопление в местах их образования валиков пыли, ржавчины, зимой инея и т.п. Образованию трещин и изломом в хребтовой балке часто предшествует вертикальный её прогиб. Поэтому в четырех, шести и восьмиосных грузовых вагонах он допускается не более 100 мм. Об обрыве шкворневой балки вместе соединения её с хребтовой может свидетельствовать отсутствие зазора в скользунах соответствующих концов шкворневой балки. Обрыв угловой стойки полувагона в соединении с нижней боковой обвязкой кузова является признаком возможного излома хребтовой балки в месте её сочленения с концевой балкой, а обрыв шкворневой стойки в месте соединения с нижней обвязкой является признаком возможного излома хребтовой балки в зоне пятника или нарушения сварочного соединения её со шкворневой балкой. На обрыв хребтовой балки может указывать, также обрыв любой промежуточной стойки или раскоса кузова вместе соединения с нижней обвязкой. Обрыв одного из раскосов в средней части является, как правило, следствием прогиба хребтовой балки сверх допустимой величины. Крытые вагоны имеют такие же признаки излома и повышенного прогиба хребтовой балки, как и полувагоны. В вагонах-хопперах о возможном изломе хребтовой балки в консольной части свидетельствует обрыв угловой или шкворневой стоек кузова вместе соединения их с верхней обвязкой. Причинами появления в элементах рас различных трещин и изломов являются значительные толчки и удары, воспринимаемые вагонами, особенно при небрежном их роспуске с горок. Кроме трещин и изломов, рамы некоторых типов вагонов могут иметь значительные коррозионные повреждения. Коррозии подвергаются места рам, плохо окрашенные при ремонте вагонов, а также рамы вагонов-ледников от воздействия на них соляного раствора и рамы кислотных цистерн от действия кислот. Не допускается к эксплуатации вагоны, имеющие в раме хотя бы одну из следующих неисправностей:
- излом или трещину, выходящую с горизонтальной полки на вертикальную стенку хребтовой, боковой шкворневой или концевой балок, трещины в узлах сочленения хребтовой и шкворневой балок длиной более 120 мм.
- продольную трещину в любой балке рамы длиной более 300 мм.
- вертикальные, продольные или напольные трещины, если они проходят более чем через одно отверстие для болтов или заклепок.
- излом угольника, обрыв сварного шва или более одной заклепки крепления балок рамы.
Рамы пасс вагонов в процессе эксплуатации воспринимают значительно меньше сжимающих и растягивающих усилия, чем те же узлы в грузовых вагонах. Однако в вертикальных и горизонтальных элементах швеллеров, угольниках и коробочках конструкциях также возникают трещины. Встречаются трещины и в сварных соединениях хребтовой балки с поперечными и особенно с концевыми балками. В концевых балках возможна вмятины и изгибы в местах установки буферных комплектов. К элементов рамы пассажирских вагонов имеют место коррозионные повреждения вследствие нарушения антикоррозионных покрытий или применения металлов, недостаточно стойких против коррозии. Так же, как и у грузовых вагонов, рамы цельнометаллических пассажирских вагонов истираются в местах нахождения поглощающих аппаратов, и если эта протертость более допустимой, такой вагон отцепляют в ремонт. Наблюдаются ослабление элементов крепления упоров автосцепного устройства, прогибы элементов рам пассажирских вагонов. Так прогиб шкворневой балки допускается не более 50 мм, концевых балок в горизонтальной плоскости – не более 30 мм, а поперечных рам в горизонтальной плоскости – не более 20 мм и в вертикальной плоскости – не более 30 мм.
26.Изготовление рам вагонов
Технологический процесс предусматривает сборку и сварку технологических сборочных единиц рамы, общую сборку, сварку, зачистку швов после сварки, правку и контроль качества сварных швов после правки, механическую обработку и монтажно-сборочные работы на раме, контроль геометрических параметров рамы. При изготовлении рам вагонов следует вначале выполнять сборку и сварку составных частей, а затем уже общую. Хребтовую балку, шкворневые балки, поперечные балки, металлический пол собирают и сваривают на отдельных специальных рабочих местах параллельно процессу общей сборки рамы. Хребтовые балки изготовляют раздельным способом (сборка и сварка элементов на разных рабочих местах) или совмещенным (сборка и сварка на одном рабочем месте). Если длина хребтовой балки больше, чем длина проката, поставляемого промышленностью, производят стыковку профилей под углом 45 или 90 °. Первый способ применяют при ручной дуговой и полуавтоматической сварке. Швы накладывают с двух сторон с разделкой кромок. Такой способ малопроизводителен и рекомендуется для мелкосерийного производства. Второй способ соединения стыков применяется при контактной стыковой электросварке. Стыковую сварку прокатных профилей из малоуглеродистой и низколегированной стали (уголков, швеллеров, двутавров, труб, зетов и т. п.) выполняют на универсальных и специализированных машинах типов К-190П, K-19QM, МСГУ-500. Кондуктор для сборки и сварки. На одном конце кондуктора установлены откидные упоры, ограничивающие продольное перемещение элементов, на другом — торцовый прижим с силовым цилиндром 5. Для ограничения перемещений в поперечном направлении и соблюдения прямолинейности по всей длине хребтовой балки предусмотрены боковые упоры-фиксаторы 3 и прижимы 2. Сборочно-сварочный стенд предназначен для сборки и сварки хребтовой балки на одном рабочем месте.
Общую сборку рамы из предварительно сваренных частей выполняют на стационарных стендах (кондукторах) или в поворотных стендах-кантователях, которые оснащены быстродействующими механизированными прижимами для жесткого фиксирования и закрепления сопрягаемых частей рамы. Рамы кузовов всех вагонов собирают в перевернутом положении. Вследствие этого продольные и поперечные элементы рамы со стороны настила пола располагаются в одной плоскости, что обеспечивается точностью основной базовой поверхности кондуктора (стенда). На собранной раме проверяют правильность положения элементов. Зазоры между элементами устанавливают в зависимости от толщины свариваемого металла и способов сварки в пределах 0,5—2 мм. У собранной рамы проверяют геометрические размеры, а затем ее передают на сварку. Раму сваривают при положительной температуре окружающей среды. Места на раме, подлежащие сварке, очищают от окалины и загрязнений. Если сварку выполняют вручную, то следует избегать наложения швов в вертикальном и потолочном положении, так как при этом трудно обеспечить надлежащее качество соединения. При сварке в среде защитных газов не должно быть сквозняков, влияющих на стабильность сварочной дуги. Для предотвращения деформаций сварку выполняют одновременно не менее двух сварщиков, которые располагаются симметрично на противоположных сторонах рамы. Минимальное расстояние между двумя одновременно работающими сварщиками установлено 4— 5 м по условиям безопасности от воздействия теплового излучения. Для наложения открытых швов, доступных для продвижения сварочного полуавтомата, применяют полуавтоматическую сварку в среде углекислого газа. Для поворота рам и установки их в наиболее удобное положение при сварке применяют кантователи (двухстоечные, кольцевые или с домкратами). Правка рамы вагона после сварки для устранения деформации осуществляется в зависимости от ее конструктивных особенностей в холодном состоянии на прессах или при помощи переносных домкратов с местным подогревом пламенем газокислородных горелок. После правки рамы проверяют качество сварных швов в соединениях элементов. Все швы осматривают и проверяют соответствие их размеров чертежным с помощью шаблонов. При внешнем осмотре выявляют наличие резких наплывов, непроваров, кратеров (прожогов) и пор. Наплывы удаляют, непровары и прожоги заваривают. Дефектные участки швов выплавляют или вырубают и затем заваривают вновь. Помимо наружного осмотра, швы наиболее ответственных соединений проверяют дефектоскопом, просвечивают рентгеновскими или гамма-лучами или ультразвуком. Дефектоскопированием контролируют швы соединений листов хребтовой балки с листами шкворневой и концевой балок, соединений раскосов с листами шкворневых балок, стыковые швы хребтовой балки, выявляют внутренние дефекты сварных швов — газовые включения, непровары, трещины. После проверки качества сварных швов раму передают на позиции монтажа подвагонного оборудования.
27. Изготовление кузовов вагонов
При взаимодействии пути и подвижного состава возникают контактные напряжения в точках соприкосновения колес с рельсами. В результате этих напряжений при движении колес по рельсам происходит естественный износ трущихся поверхностей, а также их упругие и пластические деформации и усталостные разрушения.
Износ поверхности катания колеса является следствием естественного, нормального изнашивания и истирания тормозными колодками. В обычных условиях возникает равномерный прокат. Характерные признаки неравномерности проката — местный наплыв на наружную грань, сужение фаски, смятие фаски, местное уширение дорожки качения. При несимметричной насадке колес на ось, значительной разнице диаметров колес, - перекосах рамы тележки или неправильной установке колесной пары в тележке, а также под воздействием центробежной силы при длительном следовании вагона по участкам пути с крутыми кривыми у колесной пары колеса изнашиваются по-разному.
При этом появляются тонкий гребень, вертикальный подрез гребня и остроконечный накат. В последнем случае износ гребня сопровождается активной пластической деформацией металла от основания к вершине гребня из-за высокого контактного давления в месте взаимодействия его с головкой рельса.
К дефектам поверхности катания относят ползуны (плоские места), которые появляются в результате скольжения (юза) колеса по рельсу при заклинивании колесных пар вследствие действия неисправных тормозных устройств вагона, неправильного управления тормозами с локомотива или при контакте со съемным башмаком на сортировочной горке.
Характерными дефектами поверхности катания являются выщербины — выкрошившиеся участки, иногда с наличием трещин или расслоений, идущих з глубину металла.
Внутренние дефекты металлургического происхождения приводят к местному уширению обода колеса — раздавливанию его в зоне фаски или к поверхностному отколу у наружной грани.
Трещины и изломы в ободе, диске и ступице колеса являются следствием дефектов металлургического и прокатного производства — неудовлетворительной термообработки, неметаллических включений и расслоений металла, неровностей от прокатки, а также возникают от действия ударных сил.
Износы осей в условиях нормальной работы являются естественными износами. Но и при этом при подшипниках скольжения образуются сверхдопустимые конусность и овальность шейки, а неправильная подгонка подшипников приводит к неравномерному износу галтелей и маломерности буртов.
Дата добавления: 2019-07-15; просмотров: 535; Мы поможем в написании вашей работы! |
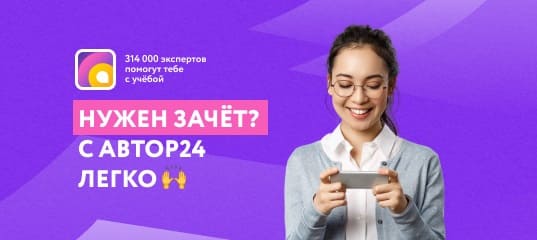
Мы поможем в написании ваших работ!