Порядок брошюровки курсового проекта
Курсовой проект брошюруется в общей обложке в следующей последовательности:
· титульный лист (приложение А);
· ведомость проекта (приложение Б)
· индивидуальное задание (приложение В);
· содержание проекта
· разделы проекта, согласно содержания;
· список используемой литературы;
· приложения.
2 МЕТОДИКА ВЫПОЛНЕНИЯ КУРСОВОГО ПРОЕКТА ПО ДИСЦИПЛИНЕ «ТЕХНИЧЕСКОЕ ОБСЛУЖИВАНИЕ АВТОМОБИЛЕЙ» ВВЕДЕНИЕ
В этом разделе должно быть дано обоснование необходимости выполнения технологических разработок по объекту проектирования, а так же краткая его характеристика исходя из задания. Материал раздела рекомендуется излагать в следующей последовательности: · задачи, стоящие перед автомобильным транспортом; · значение технического обслуживания, диагностики и ремонта в обеспечении высокой технической готовности подвижного состава; · задачи, стоящие перед технической службой автотранспортных предприятий; · цель проекта, показать значимость проектных разработок по объекту проектирования; · задача проекта, дать решение тех вопросов, которые являются составными частями курсового проекта. В общей характеристике предприятия рекомендуется, на основании анализа задания, привести основные данные об условиях эксплуатации: · тип автопредприятия по производственному назначению с указанием его производственных функций; [4. табл. 1]
· краткая характеристика подвижного состава ( назначение и классификация, габаритные размеры, радиус поворота, грузоподъемность), категория условий эксплуатации (КУЭ); [4. табл. 7; 5. табл. 2.4 ] · природно-климатическая зона, в которой эксплуатируется подвижной состав; [5. табл. 2.5] · количественный и качественный состав автомобилей, включая их пробег с начала эксплуатации; · среднесуточный пробег автомобилей; · режим работы подвижного состава, включая количество дней работы в году, сменность работы подвижного состава на линии (маршруте), время начала и конца выхода на линию, среднюю дневную продолжительность работы на линии (маршруте). [4. табл. 4, 5, 6] В характеристике объекта проектирования необходимо указать наименование объекта проектирования и его назначение с указанием основных видов работ, выполняемых в нем.
1. ТЕХНОЛОГИЧЕСКИЙ РАСЧЕТ АВТОТРАНСПОРТНОГО ПРЕДПРИЯТИЯ | |||||||||||||||||||||||||||||||||||||||||||||||||||||||||||||||||
Для выполнения технологического расчета принимается группа показателей из задания на проектирование и исходные нормативы ТО и ремонта. Из задания на проектирование принимаются: · тип подвижного состава (модель, марка, габаритные размеры), · Аи - среднесписочное (инвентарное) количество подвижного состава на ATП;
· Lcc - среднесуточный пробег автомобиля; · КЭУ~ категория условий эксплуатации; · природно-климатические условия эксплуатации, · пробег автомобилей с начала эксплуатации в долях от пробега до капитального ремонта (Lкр), · Дрг - количество рабочих дней в году для АТП; · Тп - продолжительность работы подвижного состава на линии.
| |||||||||||||||||||||||||||||||||||||||||||||||||||||||||||||||||
1.1. Корректирование нормативных величин | |||||||||||||||||||||||||||||||||||||||||||||||||||||||||||||||||
|
|
|
|
|
|
|
|
| |||||||||||||||||||||||||||||||||||||||||||||||||||||||||
Цель корректирования – приведение нормативных величин к конкретным условиям работы автомобилей и автотранспортного предприятия.
| |||||||||||||||||||||||||||||||||||||||||||||||||||||||||||||||||
Корректирование пробега до капитального ремонта (КР). | |||||||||||||||||||||||||||||||||||||||||||||||||||||||||||||||||
Корректирование пробега до капитального ремонта выполняется по формуле: | |||||||||||||||||||||||||||||||||||||||||||||||||||||||||||||||||
Lкр = Lкрн · К1 ∙ К2 ∙ К3, км; | (1.1) |
| |||||||||||||||||||||||||||||||||||||||||||||||||||||||||||||||
|
|
|
|
|
|
|
|
| |||||||||||||||||||||||||||||||||||||||||||||||||||||||||
где: Lкрн – нормативный пробег до капитального ремонта, Lкрн в км принимаем по [4, табл. 9]. | |||||||||||||||||||||||||||||||||||||||||||||||||||||||||||||||||
К1 – коэффициент корректирования нормативов в зависимости от категории условий эксплуатации; | |||||||||||||||||||||||||||||||||||||||||||||||||||||||||||||||||
К2 – коэффициент корректирования нормативов в зависимости от модификации подвижного состава и способа организации его работы; | |||||||||||||||||||||||||||||||||||||||||||||||||||||||||||||||||
К3 – коэффициент корректирования нормативов в зависимости от природно-климатических условий.
| |||||||||||||||||||||||||||||||||||||||||||||||||||||||||||||||||
Для выбора К1 необходимо знать категорию условий эксплуатации (см. задание). Ее можно определить по [5. табл. 2.4], а значение К1 в [4, табл. 12]. | |||||||||||||||||||||||||||||||||||||||||||||||||||||||||||||||||
Для выбора К2 воспользуйтесь [4, табл. 13]. Для прицепного состава К2 принимается аналогично автомобилям. | |||||||||||||||||||||||||||||||||||||||||||||||||||||||||||||||||
Для выбора К3 необходимо знать климатический район эксплуатации подвижного состава. Климатическое районирование приведено в [5, табл. 2.5]. После определения климатического района воспользуйтесь [4, табл. 14] для выбора коэффициента К3.
| |||||||||||||||||||||||||||||||||||||||||||||||||||||||||||||||||
При выборе следует обратить внимание на то, что нормативный пробег принимается для базовой модели подвижного состава и принимается по автомобилю (прицепу или полуприцепу), а не по агрегатам. | |||||||||||||||||||||||||||||||||||||||||||||||||||||||||||||||||
При выборе К3 обратите внимание на возможное наличие высокой агрессивности окружающей среды. | |||||||||||||||||||||||||||||||||||||||||||||||||||||||||||||||||
Суммарный расчетный коэффициент К = К1 ∙ К2 ∙ К3 должен быть не менее 0,5. Если расчетный получается меньше, то принимается К = 0,5. | |||||||||||||||||||||||||||||||||||||||||||||||||||||||||||||||||
Скорректированный пробег до капитального ремонта рассчитывается с точностью до целых сотен километров. | |||||||||||||||||||||||||||||||||||||||||||||||||||||||||||||||||
После принятия нормативных величин для одной марки подвижного состава приводится пример расчета, а по остальным – результаты расчета заносятся в таблицу.
| |||||||||||||||||||||||||||||||||||||||||||||||||||||||||||||||||
|
|
|
|
|
|
|
|
| |||||||||||||||||||||||||||||||||||||||||||||||||||||||||
Таблица 1.1- Корректирование пробега до капитально ремонта |
| ||||||||||||||||||||||||||||||||||||||||||||||||||||||||||||||||
Марка, модель п/состава | Lкрн, тыс. км | К1 | К2 | К3 | К | Lкр, тыс. км |
| ||||||||||||||||||||||||||||||||||||||||||||||||||||||||||
| |||||||||||||||||||||||||||||||||||||||||||||||||||||||||||||||||
ГАЗ-53 |
|
|
|
|
|
|
| ||||||||||||||||||||||||||||||||||||||||||||||||||||||||||
|
|
|
|
|
|
|
|
| |||||||||||||||||||||||||||||||||||||||||||||||||||||||||
Корректирование периодичности ТО-1. | |||||||||||||||||||||||||||||||||||||||||||||||||||||||||||||||||
Корректирование выполняется по формуле: | |||||||||||||||||||||||||||||||||||||||||||||||||||||||||||||||||
L1 = L1н · К1 · К3, км; | (1.2) |
| |||||||||||||||||||||||||||||||||||||||||||||||||||||||||||||||
|
|
|
|
|
|
|
|
| |||||||||||||||||||||||||||||||||||||||||||||||||||||||||
где: L1н – нормативная периодичность ТО-1. | |||||||||||||||||||||||||||||||||||||||||||||||||||||||||||||||||
К1 – коэффициент, учитывающий категорию условий эксплуатации. | |||||||||||||||||||||||||||||||||||||||||||||||||||||||||||||||||
К3 – коэффициент, учитывающий климатические условия. | |||||||||||||||||||||||||||||||||||||||||||||||||||||||||||||||||
L1н принимаем по [4, табл. 8 ]. | |||||||||||||||||||||||||||||||||||||||||||||||||||||||||||||||||
К1 принимаем по [4, табл. 12] | |||||||||||||||||||||||||||||||||||||||||||||||||||||||||||||||||
К3 принимаем по [4, табл. 14] | |||||||||||||||||||||||||||||||||||||||||||||||||||||||||||||||||
Корректирование периодичности ТО-1 по кратности к среднесуточному пробегу. | |||||||||||||||||||||||||||||||||||||||||||||||||||||||||||||||||
n1 = L1/lcc | (1.3) |
| |||||||||||||||||||||||||||||||||||||||||||||||||||||||||||||||
|
|
|
|
|
|
|
|
| |||||||||||||||||||||||||||||||||||||||||||||||||||||||||
где: 1cc – среднесуточный пробег автомобиля. | |||||||||||||||||||||||||||||||||||||||||||||||||||||||||||||||||
Коэффициент кратности рассчитывается с точностью до сотых, с последующим округлением до целого значения. | |||||||||||||||||||||||||||||||||||||||||||||||||||||||||||||||||
Расчетная периодичность ТО-1 | |||||||||||||||||||||||||||||||||||||||||||||||||||||||||||||||||
L1p = 1cc · n1, км | (1.4) |
| |||||||||||||||||||||||||||||||||||||||||||||||||||||||||||||||
|
|
|
|
|
|
|
|
| |||||||||||||||||||||||||||||||||||||||||||||||||||||||||
Расчетная периодичность ТО-1 округляется до целых сотен километров.
| |||||||||||||||||||||||||||||||||||||||||||||||||||||||||||||||||
Результаты расчета записать в таблицу. | |||||||||||||||||||||||||||||||||||||||||||||||||||||||||||||||||
|
|
|
|
|
|
|
|
| |||||||||||||||||||||||||||||||||||||||||||||||||||||||||
Таблица 1.2- Корректирование периодичности ТО-1 |
| ||||||||||||||||||||||||||||||||||||||||||||||||||||||||||||||||
Марка, модель п/состава | L1н км | L1 км | K1 | K3 | lcc км | n1 | L1p км | ||||||||||||||||||||||||||||||||||||||||||||||||||||||||||
|
|
|
|
|
|
|
| ||||||||||||||||||||||||||||||||||||||||||||||||||||||||||
|
|
|
|
|
|
|
|
| |||||||||||||||||||||||||||||||||||||||||||||||||||||||||
Корректирование периодичности ТО-2. | |||||||||||||||||||||||||||||||||||||||||||||||||||||||||||||||||
Корректирование выполняется по формуле: | |||||||||||||||||||||||||||||||||||||||||||||||||||||||||||||||||
L2 = L2н · K1 · K3, км; | (1.5) |
| |||||||||||||||||||||||||||||||||||||||||||||||||||||||||||||||
|
|
|
|
|
|
|
|
| |||||||||||||||||||||||||||||||||||||||||||||||||||||||||
где: L2н – нормативная периодичность ТО-2. | |||||||||||||||||||||||||||||||||||||||||||||||||||||||||||||||||
L2н принимаем по [4, табл. 8]. | |||||||||||||||||||||||||||||||||||||||||||||||||||||||||||||||||
Корректирование периодичности ТО-2 по кратности к периодичности ТО-1. | |||||||||||||||||||||||||||||||||||||||||||||||||||||||||||||||||
n2 = L2/L1р | (1.6) |
| |||||||||||||||||||||||||||||||||||||||||||||||||||||||||||||||
|
|
|
|
|
|
|
|
| |||||||||||||||||||||||||||||||||||||||||||||||||||||||||
Коэффициент кратности рассчитывается с точностью до сотых, с последующим округлением до целого значения. | |||||||||||||||||||||||||||||||||||||||||||||||||||||||||||||||||
Расчетная периодичность ТО-2. | |||||||||||||||||||||||||||||||||||||||||||||||||||||||||||||||||
L2р = L1р · n2, км | (1.7) |
| |||||||||||||||||||||||||||||||||||||||||||||||||||||||||||||||
|
|
|
|
|
|
|
|
| |||||||||||||||||||||||||||||||||||||||||||||||||||||||||
Расчетная периодичность ТО-2 округляется до целых сотен километров. | |||||||||||||||||||||||||||||||||||||||||||||||||||||||||||||||||
В большинстве случаев расчетную периодичность ТО-2 проще определить по следующей зависимости: | |||||||||||||||||||||||||||||||||||||||||||||||||||||||||||||||||
L2р = L1р · 4, км | (1.8) |
| |||||||||||||||||||||||||||||||||||||||||||||||||||||||||||||||
|
|
|
|
|
|
|
|
| |||||||||||||||||||||||||||||||||||||||||||||||||||||||||
Результаты расчета занесены в таблицу. | |||||||||||||||||||||||||||||||||||||||||||||||||||||||||||||||||
|
|
|
|
|
|
|
|
| |||||||||||||||||||||||||||||||||||||||||||||||||||||||||
Таблица 1.3- Корректирование периодичности ТО-2 | |||||||||||||||||||||||||||||||||||||||||||||||||||||||||||||||||
Марка, модель | L2н | K1 | K3 | L1р | n2 | L2р |
| ||||||||||||||||||||||||||||||||||||||||||||||||||||||||||
п/состава | км | км | км |
| |||||||||||||||||||||||||||||||||||||||||||||||||||||||||||||
|
|
|
|
|
|
|
| ||||||||||||||||||||||||||||||||||||||||||||||||||||||||||
|
|
|
|
|
|
|
|
| |||||||||||||||||||||||||||||||||||||||||||||||||||||||||
Корректирование трудоемкости ежедневного обслуживания. | |||||||||||||||||||||||||||||||||||||||||||||||||||||||||||||||||
tео = tеон · К2 · К5, чел.ч | (1.9) |
| |||||||||||||||||||||||||||||||||||||||||||||||||||||||||||||||
|
|
|
|
|
|
|
|
| |||||||||||||||||||||||||||||||||||||||||||||||||||||||||
где: tеон – нормативная трудоемкость ЕО. | |||||||||||||||||||||||||||||||||||||||||||||||||||||||||||||||||
К2 – коэффициент, учитывающий модификацию подвижного состава и организацию его работы. | |||||||||||||||||||||||||||||||||||||||||||||||||||||||||||||||||
К5 – коэффициент, учитывающий размеры АТП и число технологически совместимых групп п/состава. | |||||||||||||||||||||||||||||||||||||||||||||||||||||||||||||||||
tеон принимаем по [4, табл. 11] | |||||||||||||||||||||||||||||||||||||||||||||||||||||||||||||||||
К2 принимаем по [4, табл. 13] | |||||||||||||||||||||||||||||||||||||||||||||||||||||||||||||||||
К5 принимаем по [3, табл. 2.12] | |||||||||||||||||||||||||||||||||||||||||||||||||||||||||||||||||
Результаты расчета по корректированию оформить в таблицу: | |||||||||||||||||||||||||||||||||||||||||||||||||||||||||||||||||
|
|
|
|
|
|
|
|
| |||||||||||||||||||||||||||||||||||||||||||||||||||||||||
Таблица 1.4- Корректирование трудоемкости ежедневного обслуживания | |||||||||||||||||||||||||||||||||||||||||||||||||||||||||||||||||
| Марка, модель | tеон | К2 | К5 | tео |
|
| ||||||||||||||||||||||||||||||||||||||||||||||||||||||||||
| п/состава | чел.ч | чел.ч |
|
| ||||||||||||||||||||||||||||||||||||||||||||||||||||||||||||
|
|
|
|
|
|
|
| ||||||||||||||||||||||||||||||||||||||||||||||||||||||||||
Корректирование трудоемкости ТО-1 | |||||||||||||||||||||||||||||||||||||||||||||||||||||||||||||||||
Корректирование выполняется по формуле: | |||||||||||||||||||||||||||||||||||||||||||||||||||||||||||||||||
|
|
|
|
|
|
|
|
| |||||||||||||||||||||||||||||||||||||||||||||||||||||||||
t1 = t1н · К2 · К5, чел.ч | (1.10) |
| |||||||||||||||||||||||||||||||||||||||||||||||||||||||||||||||
|
|
|
|
|
|
|
|
| |||||||||||||||||||||||||||||||||||||||||||||||||||||||||
где: t1н – нормативная трудоемкость ТО-1. | |||||||||||||||||||||||||||||||||||||||||||||||||||||||||||||||||
К2 – коэффициент, учитывающий модификацию подвижного состава и организацию его работы. | |||||||||||||||||||||||||||||||||||||||||||||||||||||||||||||||||
К5 – коэффициент, учитывающий размеры АТП и количества технологически совместимых групп п/состава. | |||||||||||||||||||||||||||||||||||||||||||||||||||||||||||||||||
t1н принимаем по [4, табл. 11] | |||||||||||||||||||||||||||||||||||||||||||||||||||||||||||||||||
К2 принимаем по [4, табл. 13] | |||||||||||||||||||||||||||||||||||||||||||||||||||||||||||||||||
К5 принимаем по [3, табл. 2.12] | |||||||||||||||||||||||||||||||||||||||||||||||||||||||||||||||||
Результаты расчета по корректированию оформить в таблицу: | |||||||||||||||||||||||||||||||||||||||||||||||||||||||||||||||||
|
|
|
|
|
|
|
|
| |||||||||||||||||||||||||||||||||||||||||||||||||||||||||
Таблица 1.5- Корректирование трудоемкости ТО-1 | |||||||||||||||||||||||||||||||||||||||||||||||||||||||||||||||||
| Марка, модель | t1н | К2 | К5 | t1 |
|
| ||||||||||||||||||||||||||||||||||||||||||||||||||||||||||
| п/состава | чел.ч | чел.ч |
|
| ||||||||||||||||||||||||||||||||||||||||||||||||||||||||||||
|
|
|
|
|
|
|
| ||||||||||||||||||||||||||||||||||||||||||||||||||||||||||
|
|
|
|
|
|
|
|
| |||||||||||||||||||||||||||||||||||||||||||||||||||||||||
Корректирование трудоемкости ТО-2 | |||||||||||||||||||||||||||||||||||||||||||||||||||||||||||||||||
Корректирование выполняется по формуле: | |||||||||||||||||||||||||||||||||||||||||||||||||||||||||||||||||
t2 = t2н · К2 · К5, чел.ч | (1.11) |
| |||||||||||||||||||||||||||||||||||||||||||||||||||||||||||||||
|
|
|
|
|
|
|
|
| |||||||||||||||||||||||||||||||||||||||||||||||||||||||||
где: t2н – нормативная трудоемкость ТО-2, [4, табл. 11]. | |||||||||||||||||||||||||||||||||||||||||||||||||||||||||||||||||
К2 – коэффициент, учитывающий модификацию подвижного состава и организацию его работы, [4, табл. 13]. | |||||||||||||||||||||||||||||||||||||||||||||||||||||||||||||||||
К5 – коэффициент, учитывающий размеры АТП и число технологически совместимых групп п/состава, [3, табл. 2.12]. | |||||||||||||||||||||||||||||||||||||||||||||||||||||||||||||||||
Результаты расчета по корректированию оформить в таблицу: | |||||||||||||||||||||||||||||||||||||||||||||||||||||||||||||||||
t2 = 2000 · 1,6 · 0,8=, чел.ч | |||||||||||||||||||||||||||||||||||||||||||||||||||||||||||||||||
Таблица 1.6- Корректирование трудоемкости ТО-2 | |||||||||||||||||||||||||||||||||||||||||||||||||||||||||||||||||
| Марка, модель | t2н | К2 | К5 | t2 |
|
| ||||||||||||||||||||||||||||||||||||||||||||||||||||||||||
| п/состава | чел.ч | чел.ч |
|
| ||||||||||||||||||||||||||||||||||||||||||||||||||||||||||||
|
|
|
|
|
|
|
| ||||||||||||||||||||||||||||||||||||||||||||||||||||||||||
|
|
|
|
|
|
|
|
| |||||||||||||||||||||||||||||||||||||||||||||||||||||||||
Корректирование трудоемкости общей диагностики | |||||||||||||||||||||||||||||||||||||||||||||||||||||||||||||||||
Корректирование выполняется по формуле: | |||||||||||||||||||||||||||||||||||||||||||||||||||||||||||||||||
| (1.12) |
| |||||||||||||||||||||||||||||||||||||||||||||||||||||||||||||||
где: t1 – скорректированная трудоемкость ТО1-1. | |||||||||||||||||||||||||||||||||||||||||||||||||||||||||||||||||
| |||||||||||||||||||||||||||||||||||||||||||||||||||||||||||||||||
| |||||||||||||||||||||||||||||||||||||||||||||||||||||||||||||||||
Результаты расчета по корректированию оформить в таблицу: | |||||||||||||||||||||||||||||||||||||||||||||||||||||||||||||||||
|
|
|
|
|
|
|
|
| |||||||||||||||||||||||||||||||||||||||||||||||||||||||||
Таблица 1.7- Корректирование трудоемкости общей диагностики | |||||||||||||||||||||||||||||||||||||||||||||||||||||||||||||||||
| Марка, модель | t1 | | tд1 |
|
| |||||||||||||||||||||||||||||||||||||||||||||||||||||||||||
| п/состава | чел.ч | чел.ч |
|
| ||||||||||||||||||||||||||||||||||||||||||||||||||||||||||||
|
|
|
|
|
|
| |||||||||||||||||||||||||||||||||||||||||||||||||||||||||||
|
|
|
|
|
|
|
|
| |||||||||||||||||||||||||||||||||||||||||||||||||||||||||
Корректирование трудоемкости поэлементной диагностики | |||||||||||||||||||||||||||||||||||||||||||||||||||||||||||||||||
Корректирование выполняется по формуле: | |||||||||||||||||||||||||||||||||||||||||||||||||||||||||||||||||
| (1.13) |
| |||||||||||||||||||||||||||||||||||||||||||||||||||||||||||||||
|
|
|
|
|
|
|
|
| |||||||||||||||||||||||||||||||||||||||||||||||||||||||||
где: t2 – скорректированая трудоемкость ТО-2. (прил. 4). | |||||||||||||||||||||||||||||||||||||||||||||||||||||||||||||||||
где | |||||||||||||||||||||||||||||||||||||||||||||||||||||||||||||||||
| |||||||||||||||||||||||||||||||||||||||||||||||||||||||||||||||||
Результаты расчета по корректированию оформить в таблицу: | |||||||||||||||||||||||||||||||||||||||||||||||||||||||||||||||||
|
|
|
|
|
|
|
|
| |||||||||||||||||||||||||||||||||||||||||||||||||||||||||
Таблица 1.8- Корректирование трудоемкости поэлементной диагностики | |||||||||||||||||||||||||||||||||||||||||||||||||||||||||||||||||
| Марка, модель | tд2н |
| tд2 |
|
| |||||||||||||||||||||||||||||||||||||||||||||||||||||||||||
| п/состава | чел.ч | чел.ч |
|
| ||||||||||||||||||||||||||||||||||||||||||||||||||||||||||||
|
|
|
|
|
|
| |||||||||||||||||||||||||||||||||||||||||||||||||||||||||||
|
|
|
|
|
|
|
|
| |||||||||||||||||||||||||||||||||||||||||||||||||||||||||
Корректирование удельной трудоемкости текущего ремонта | |||||||||||||||||||||||||||||||||||||||||||||||||||||||||||||||||
Корректирование выполняется по формуле: | |||||||||||||||||||||||||||||||||||||||||||||||||||||||||||||||||
tтр = tтрн · К1 · К2 · К3 · К4ср · К5, чел.ч/1000 км | (1.14) |
| |||||||||||||||||||||||||||||||||||||||||||||||||||||||||||||||
|
|
|
|
|
|
|
|
| |||||||||||||||||||||||||||||||||||||||||||||||||||||||||
где: tтрн – нормативная удельная трудоемкость ТР. | |||||||||||||||||||||||||||||||||||||||||||||||||||||||||||||||||
К1-5 – коэффициенты корректирования. | |||||||||||||||||||||||||||||||||||||||||||||||||||||||||||||||||
Рекомендуется принять значения нормативных величин по: | |||||||||||||||||||||||||||||||||||||||||||||||||||||||||||||||||
tтрн [4, табл. 11] | |||||||||||||||||||||||||||||||||||||||||||||||||||||||||||||||||
К1, К2, К3, К5 соответственно в [4, табл. 12, 13, 14,] [3, табл. 2.12] | |||||||||||||||||||||||||||||||||||||||||||||||||||||||||||||||||
| |||||||||||||||||||||||||||||||||||||||||||||||||||||||||||||||||
К4ср = | (1.15) |
| |||||||||||||||||||||||||||||||||||||||||||||||||||||||||||||||
| |||||||||||||||||||||||||||||||||||||||||||||||||||||||||||||||||
|
|
|
|
|
|
|
|
| |||||||||||||||||||||||||||||||||||||||||||||||||||||||||
где: А1, А2, Аn – количество автомобилей в интервале пробега, для которого принимается значение коэффициента К4 [3, табл. 2.11] | |||||||||||||||||||||||||||||||||||||||||||||||||||||||||||||||||
Результаты расчета по корректированию оформить в таблицу: | |||||||||||||||||||||||||||||||||||||||||||||||||||||||||||||||||
|
|
|
|
|
|
|
|
| |||||||||||||||||||||||||||||||||||||||||||||||||||||||||
Таблица 1.9 - Значение коэффициента К4 | |||||||||||||||||||||||||||||||||||||||||||||||||||||||||||||||||
Пробег с начала эксплуатации в долях от Lкр | 0,5 | 0,5…0,75 | 0,75…1 | более 1,0 | кол. КР |
| |||||||||||||||||||||||||||||||||||||||||||||||||||||||||||
Количество автомобилей в % |
|
|
|
|
|
| |||||||||||||||||||||||||||||||||||||||||||||||||||||||||||
Количество автомобилей |
|
|
|
|
|
| |||||||||||||||||||||||||||||||||||||||||||||||||||||||||||
К4 |
|
|
|
|
|
| |||||||||||||||||||||||||||||||||||||||||||||||||||||||||||
К4ср |
|
|
| ||||||||||||||||||||||||||||||||||||||||||||||||||||||||||||||
|
|
|
|
|
|
|
|
| |||||||||||||||||||||||||||||||||||||||||||||||||||||||||
|
|
| К4ср = |
|
|
|
|
| |||||||||||||||||||||||||||||||||||||||||||||||||||||||||
|
|
|
|
|
|
|
|
| |||||||||||||||||||||||||||||||||||||||||||||||||||||||||
Таблица 1.10 - Корректирование удельной трудоемкости текущего ремонта | |||||||||||||||||||||||||||||||||||||||||||||||||||||||||||||||||
Марка, модель | tтрн | К1 | К2 | К3 | К4ср | К5 | tтр | ||||||||||||||||||||||||||||||||||||||||||||||||||||||||||
п/состава | |||||||||||||||||||||||||||||||||||||||||||||||||||||||||||||||||
|
|
|
|
|
|
|
| ||||||||||||||||||||||||||||||||||||||||||||||||||||||||||
|
|
|
|
|
|
|
|
| |||||||||||||||||||||||||||||||||||||||||||||||||||||||||
|
|
|
|
|
|
|
|
| |||||||||||||||||||||||||||||||||||||||||||||||||||||||||
1.2. Средний пробег до капитального ремонта |
| ||||||||||||||||||||||||||||||||||||||||||||||||||||||||||||||||
|
|
|
|
|
|
|
|
| |||||||||||||||||||||||||||||||||||||||||||||||||||||||||
| |||||||||||||||||||||||||||||||||||||||||||||||||||||||||||||||||
Lкрс = | , тыс. км | (1.16) |
| ||||||||||||||||||||||||||||||||||||||||||||||||||||||||||||||
|
|
|
|
|
|
|
|
| |||||||||||||||||||||||||||||||||||||||||||||||||||||||||
где: А′u – число автомобилей, не прошедших капитальный ремонт; | |||||||||||||||||||||||||||||||||||||||||||||||||||||||||||||||||
А″u – число автомобилей, прошедших капитальный ремонт. | |||||||||||||||||||||||||||||||||||||||||||||||||||||||||||||||||
А′u и А″u принимаем по фактическому пробегу (см. задание) | |||||||||||||||||||||||||||||||||||||||||||||||||||||||||||||||||
Точность расчета – до целых сотен километров. | |||||||||||||||||||||||||||||||||||||||||||||||||||||||||||||||||
|
|
|
|
|
|
|
|
| |||||||||||||||||||||||||||||||||||||||||||||||||||||||||
Таблица 1.11- Расчет среднего межремонтного пробега | |||||||||||||||||||||||||||||||||||||||||||||||||||||||||||||||||
Марка, модель п/состава | Lкр, тыс. км | A′u
| А′′u
| Lкрс тыс. км |
|
| |||||||||||||||||||||||||||||||||||||||||||||||||||||||||||
|
| ||||||||||||||||||||||||||||||||||||||||||||||||||||||||||||||||
|
|
|
|
|
|
| |||||||||||||||||||||||||||||||||||||||||||||||||||||||||||
|
|
|
|
|
|
|
|
| |||||||||||||||||||||||||||||||||||||||||||||||||||||||||
1.3. Расчет годового пробега парка | |||||||||||||||||||||||||||||||||||||||||||||||||||||||||||||||||
|
|
|
|
|
|
|
|
| |||||||||||||||||||||||||||||||||||||||||||||||||||||||||
1.3.1 Корректирование удельного простоя в техническом обслуживании и ремонте. | |||||||||||||||||||||||||||||||||||||||||||||||||||||||||||||||||
|
|
|
|
|
|
|
|
| |||||||||||||||||||||||||||||||||||||||||||||||||||||||||
Корректирование выполняется по формуле: | |||||||||||||||||||||||||||||||||||||||||||||||||||||||||||||||||
|
|
|
|
|
|
|
|
| |||||||||||||||||||||||||||||||||||||||||||||||||||||||||
dТОР = dТОРН· К‘4ср, дн./1000 км | (1.17) |
| |||||||||||||||||||||||||||||||||||||||||||||||||||||||||||||||
|
|
|
|
|
|
|
|
| |||||||||||||||||||||||||||||||||||||||||||||||||||||||||
где: dТОР - скорректированный удельный простой в ТО и ремонте; | |||||||||||||||||||||||||||||||||||||||||||||||||||||||||||||||||
dТОРН -нормативный удельный простой в ТО и ремонте; | |||||||||||||||||||||||||||||||||||||||||||||||||||||||||||||||||
К′ 4ср - средний расчетный коэффициент корректирования. | |||||||||||||||||||||||||||||||||||||||||||||||||||||||||||||||||
Средний расчетный коэффициент корректирования рассчитывается по формуле: | |||||||||||||||||||||||||||||||||||||||||||||||||||||||||||||||||
| |||||||||||||||||||||||||||||||||||||||||||||||||||||||||||||||||
| (1.18) |
| |||||||||||||||||||||||||||||||||||||||||||||||||||||||||||||||
|
|
|
|
|
|
|
|
| |||||||||||||||||||||||||||||||||||||||||||||||||||||||||
где А1, А.2, Аn- количество автомобилей в интервале пробега, для которого принимается значение коэффициента К4' (см. [3. табл. 2.11]); | |||||||||||||||||||||||||||||||||||||||||||||||||||||||||||||||||
К'14, К'n4 - коэффициент корректирования, учитывающий пробег с начала эсплуатации | |||||||||||||||||||||||||||||||||||||||||||||||||||||||||||||||||
К'4 принимаем по [3. табл. 2.11] | |||||||||||||||||||||||||||||||||||||||||||||||||||||||||||||||||
К'4 для прицепного состава принимается, как и для автомобилей по их функциональному назначению. | |||||||||||||||||||||||||||||||||||||||||||||||||||||||||||||||||
dторн принимаем по [3, табл. 2.6]. | |||||||||||||||||||||||||||||||||||||||||||||||||||||||||||||||||
Результаты расчета приведены в таблицу. | |||||||||||||||||||||||||||||||||||||||||||||||||||||||||||||||||
Таблица 1.12 - Корректирование удельного простоя в ТО и ремонте | |||||||||||||||||||||||||||||||||||||||||||||||||||||||||||||||||
Марка, модель п/состава | dторн дн/1000 км | А1 | А2 | А3 | А4 | К'4ср | dтop дн/1000 км |
| |||||||||||||||||||||||||||||||||||||||||||||||||||||||||
К'4 | К'24 | К'34 | К'44 |
| |||||||||||||||||||||||||||||||||||||||||||||||||||||||||||||
|
|
|
|
|
|
|
|
| |||||||||||||||||||||||||||||||||||||||||||||||||||||||||
|
|
|
|
| |||||||||||||||||||||||||||||||||||||||||||||||||||||||||||||
|
|
|
|
|
|
|
|
| |||||||||||||||||||||||||||||||||||||||||||||||||||||||||
1.3.2 Расчет коэффициента технической готовности. | |||||||||||||||||||||||||||||||||||||||||||||||||||||||||||||||||
|
|
|
|
|
|
|
|
| |||||||||||||||||||||||||||||||||||||||||||||||||||||||||
Значение коэффициента технической готовности по каждой марке (модели) подвижного состава предлагается рассчитать по пробегу за цикл эксплуатации. Расчет коэффициента технической готовности выполняется по формуле: | |||||||||||||||||||||||||||||||||||||||||||||||||||||||||||||||||
αт=Дэ/(Дэ + Дтор + Дкр), | (1.19) |
| |||||||||||||||||||||||||||||||||||||||||||||||||||||||||||||||
где αт - расчетный коэффициент технической готовности; | |||||||||||||||||||||||||||||||||||||||||||||||||||||||||||||||||
Дэ - дни эксплуатации в цикле; | |||||||||||||||||||||||||||||||||||||||||||||||||||||||||||||||||
Дтор - дни простоя за цикл в ТО и ремонте; | |||||||||||||||||||||||||||||||||||||||||||||||||||||||||||||||||
Дкр - дни отсутствия авто на АТП по причине кап. ремонта. | |||||||||||||||||||||||||||||||||||||||||||||||||||||||||||||||||
Дни эксплуатации в цикле рассчитывается по формуле: | |||||||||||||||||||||||||||||||||||||||||||||||||||||||||||||||||
|
|
|
|
|
|
|
|
| |||||||||||||||||||||||||||||||||||||||||||||||||||||||||
Дэ = Lкрс/1сс, | (1.20) |
| |||||||||||||||||||||||||||||||||||||||||||||||||||||||||||||||
|
|
|
|
|
|
|
|
| |||||||||||||||||||||||||||||||||||||||||||||||||||||||||
где 1СС- среднесуточный пробег. | |||||||||||||||||||||||||||||||||||||||||||||||||||||||||||||||||
Дни простоя в ТО и ремонте рассчитывается по формуле: | |||||||||||||||||||||||||||||||||||||||||||||||||||||||||||||||||
|
|
|
|
|
|
|
|
| |||||||||||||||||||||||||||||||||||||||||||||||||||||||||
ДТОР = dтop·Lкрс/l 000 | (1.21) |
| |||||||||||||||||||||||||||||||||||||||||||||||||||||||||||||||
|
|
|
|
|
|
|
|
| |||||||||||||||||||||||||||||||||||||||||||||||||||||||||
Дни отсутствия автомобилей на АТП по причине нахождения на капитальном ремонте: | |||||||||||||||||||||||||||||||||||||||||||||||||||||||||||||||||
Дкр = dKp + dтран, | (1.22) |
| |||||||||||||||||||||||||||||||||||||||||||||||||||||||||||||||
где dKp - дни нахождения авто на капитальном ремонте на спец. АРЗ; | |||||||||||||||||||||||||||||||||||||||||||||||||||||||||||||||||
dтран - дни транспортировки авто на кап. ремонте. | |||||||||||||||||||||||||||||||||||||||||||||||||||||||||||||||||
dтран = (0,15...0,20) dKp | (1.23) |
| |||||||||||||||||||||||||||||||||||||||||||||||||||||||||||||||
|
|
|
|
|
|
|
|
| |||||||||||||||||||||||||||||||||||||||||||||||||||||||||
dKp принимается по (3, табл. 2.6) | |||||||||||||||||||||||||||||||||||||||||||||||||||||||||||||||||
|
|
|
|
|
|
|
|
| |||||||||||||||||||||||||||||||||||||||||||||||||||||||||
Таблица 1.13 - Расчет коэффициента технической готовности парка | |||||||||||||||||||||||||||||||||||||||||||||||||||||||||||||||||
Марка, модель п/состава | Lкр, | Дэ, | dтop | Дтор, | dKp, | dтран, дн | Дкр, дн | αт | |||||||||||||||||||||||||||||||||||||||||||||||||||||||||
тыс. км | дн | км | дн | ||||||||||||||||||||||||||||||||||||||||||||||||||||||||||||||
|
|
|
|
|
|
|
|
| |||||||||||||||||||||||||||||||||||||||||||||||||||||||||
|
|
|
|
|
|
|
|
| |||||||||||||||||||||||||||||||||||||||||||||||||||||||||
1.3.3 Расчет коэффициента выпуска подвижного состава. | |||||||||||||||||||||||||||||||||||||||||||||||||||||||||||||||||
|
|
|
|
|
|
|
|
| |||||||||||||||||||||||||||||||||||||||||||||||||||||||||
Коэффициент выпуска автомобилей рассчитывается по формуле: | |||||||||||||||||||||||||||||||||||||||||||||||||||||||||||||||||
|
|
|
|
|
|
|
|
| |||||||||||||||||||||||||||||||||||||||||||||||||||||||||
αв = Дрг·αт·Ки/365, | (1.24) |
| |||||||||||||||||||||||||||||||||||||||||||||||||||||||||||||||
|
|
|
|
|
|
|
|
| |||||||||||||||||||||||||||||||||||||||||||||||||||||||||
где αв - коэффициент выпуска автомобилей; | |||||||||||||||||||||||||||||||||||||||||||||||||||||||||||||||||
Дрг - дни работы в году авто на линии; | |||||||||||||||||||||||||||||||||||||||||||||||||||||||||||||||||
Ки - коэффициент внеэксплуатационного простоя. | |||||||||||||||||||||||||||||||||||||||||||||||||||||||||||||||||
Коэффициент внеэксплуатационного простоя характеризует организацию работы подвижного состава и учитывает простой по причине отсутствия водителей, отсутствия работы, простоя без топлива, по причине бездорожья и т.д. | |||||||||||||||||||||||||||||||||||||||||||||||||||||||||||||||||
Рекомендуется принять Ки = 0,93 -:- 0,97 | |||||||||||||||||||||||||||||||||||||||||||||||||||||||||||||||||
Коэффициенты рассчитываются с точностью до тысячных. После приведения примера расчета для одного автомобиля (при наличии автопоездов и для них) результаты расчета рекомендуется оформить в таблице. | |||||||||||||||||||||||||||||||||||||||||||||||||||||||||||||||||
Таблица 1.14 Расчет коэффициента выпуска подвижного состава | |||||||||||||||||||||||||||||||||||||||||||||||||||||||||||||||||
|
| Марка, модель п/состава | Дрг | αт | αв |
|
| ||||||||||||||||||||||||||||||||||||||||||||||||||||||||||
|
|
|
|
|
|
|
| ||||||||||||||||||||||||||||||||||||||||||||||||||||||||||
|
|
|
|
|
|
|
|
| |||||||||||||||||||||||||||||||||||||||||||||||||||||||||
Расчет годового пробега по марке подвижного состава производится по формуле: | |||||||||||||||||||||||||||||||||||||||||||||||||||||||||||||||||
Lг = 365 ∙ Аи · 1сс · αв, км | (1.25) |
| |||||||||||||||||||||||||||||||||||||||||||||||||||||||||||||||
|
|
|
|
|
|
|
|
| |||||||||||||||||||||||||||||||||||||||||||||||||||||||||
где: Аи – списочное число подвижного состава. | |||||||||||||||||||||||||||||||||||||||||||||||||||||||||||||||||
1сс – среднесуточный пробег, км | |||||||||||||||||||||||||||||||||||||||||||||||||||||||||||||||||
αв – коэффициент выпуска подвижного состава | |||||||||||||||||||||||||||||||||||||||||||||||||||||||||||||||||
Расчет годового пробега ведется с точностью до целых сотен километров. | |||||||||||||||||||||||||||||||||||||||||||||||||||||||||||||||||
|
|
|
|
|
|
|
|
| |||||||||||||||||||||||||||||||||||||||||||||||||||||||||
Таблица 1.15- Расчет годового пробега подвижного состава | |||||||||||||||||||||||||||||||||||||||||||||||||||||||||||||||||
| Марка, модель | Аи | 1сс | αв | 1г |
| |||||||||||||||||||||||||||||||||||||||||||||||||||||||||||
| п/состава | км | тыс. км |
| |||||||||||||||||||||||||||||||||||||||||||||||||||||||||||||
|
|
|
|
|
|
| |||||||||||||||||||||||||||||||||||||||||||||||||||||||||||
|
|
|
|
|
|
|
|
| |||||||||||||||||||||||||||||||||||||||||||||||||||||||||
1.4. Расчет производственной программы по обслуживанию автомобилей и выбор способа производства | |||||||||||||||||||||||||||||||||||||||||||||||||||||||||||||||||
|
|
|
|
|
|
|
|
| |||||||||||||||||||||||||||||||||||||||||||||||||||||||||
Расчет количества уборочно-моечных работ (УМР). | |||||||||||||||||||||||||||||||||||||||||||||||||||||||||||||||||
Количество ежедневных обслуживаний рассчитывается по автомобилям. | |||||||||||||||||||||||||||||||||||||||||||||||||||||||||||||||||
|
|
|
|
|
|
|
|
| |||||||||||||||||||||||||||||||||||||||||||||||||||||||||
Nео = Lг/1сс | (1.26) |
| |||||||||||||||||||||||||||||||||||||||||||||||||||||||||||||||
|
|
|
|
|
|
|
|
| |||||||||||||||||||||||||||||||||||||||||||||||||||||||||
Годовое количество уборочно-моечных работ не совпадет с годовым количеством ежедневных обслуживаний. | |||||||||||||||||||||||||||||||||||||||||||||||||||||||||||||||||
Количество УМР за год следует рассчитать по формулам (16, 17): | |||||||||||||||||||||||||||||||||||||||||||||||||||||||||||||||||
- для грузовых автомобилей | |||||||||||||||||||||||||||||||||||||||||||||||||||||||||||||||||
|
|
|
|
|
|
|
|
| |||||||||||||||||||||||||||||||||||||||||||||||||||||||||
Nумр = (0,75-:-0,8) · Nео | (1.27) |
| |||||||||||||||||||||||||||||||||||||||||||||||||||||||||||||||
|
|
|
|
|
|
|
|
| |||||||||||||||||||||||||||||||||||||||||||||||||||||||||
- для легковых автомобилей и автобусов | |||||||||||||||||||||||||||||||||||||||||||||||||||||||||||||||||
Nумр = (1,10-:-1,15) ∙ Neo | (1.28) |
| |||||||||||||||||||||||||||||||||||||||||||||||||||||||||||||||
|
|
|
|
|
|
|
|
| |||||||||||||||||||||||||||||||||||||||||||||||||||||||||
Сменная программа уборочно-моечных работ. | |||||||||||||||||||||||||||||||||||||||||||||||||||||||||||||||||
Для ее расчета сменной программы УМР рекомендуется воспользоваться формулой: | |||||||||||||||||||||||||||||||||||||||||||||||||||||||||||||||||
|
|
|
|
|
|
|
|
| |||||||||||||||||||||||||||||||||||||||||||||||||||||||||
Nумс = Nумр/(Дргу · Ссм) | (1.29) |
| |||||||||||||||||||||||||||||||||||||||||||||||||||||||||||||||
|
|
|
|
|
|
|
|
| |||||||||||||||||||||||||||||||||||||||||||||||||||||||||
где: Дргу – количество дней работы в году зоны УМР. (Необходимо задать с учетом дней работы в году авто на линии). | |||||||||||||||||||||||||||||||||||||||||||||||||||||||||||||||||
Ссм – число смен работы за сутки зоны уборочно-моечных работ. | |||||||||||||||||||||||||||||||||||||||||||||||||||||||||||||||||
Числом смен также необходимо задать с учетом обеспечения выполнения уборочно-моечных работ в межсменное время. | |||||||||||||||||||||||||||||||||||||||||||||||||||||||||||||||||
На основании сменной программы необходимо определиться со способом организации выполнения уборочно-моечных работ. | |||||||||||||||||||||||||||||||||||||||||||||||||||||||||||||||||
Под термином определиться следует понимать, применяется поточная линия для выполнения работ или нет, а также какие работы будут выполняться механизированным способом, а какие – вручную. Напоминаем: в состав уборочно-моечных работ входят уборочные, моечные, сушильно-обтирочные работы. | |||||||||||||||||||||||||||||||||||||||||||||||||||||||||||||||||
|
|
|
|
|
|
|
|
| |||||||||||||||||||||||||||||||||||||||||||||||||||||||||
Таблица 1.16- Расчет программы уборочно-моечных работ | |||||||||||||||||||||||||||||||||||||||||||||||||||||||||||||||||
| Марка, модель п/состава | Lг тыс. км | 1сс км | Nео
| Nумр
| Nумс
|
|
| |||||||||||||||||||||||||||||||||||||||||||||||||||||||||
|
|
| |||||||||||||||||||||||||||||||||||||||||||||||||||||||||||||||
|
|
|
|
|
|
|
|
| |||||||||||||||||||||||||||||||||||||||||||||||||||||||||
|
|
|
|
|
|
|
|
| |||||||||||||||||||||||||||||||||||||||||||||||||||||||||
Годовое количество КР рассчитывается по формуле: | |||||||||||||||||||||||||||||||||||||||||||||||||||||||||||||||||
|
|
|
|
|
|
|
|
| |||||||||||||||||||||||||||||||||||||||||||||||||||||||||
NКР = Lг/Lкрс | (1.30) |
| |||||||||||||||||||||||||||||||||||||||||||||||||||||||||||||||
|
|
|
|
|
|
|
|
| |||||||||||||||||||||||||||||||||||||||||||||||||||||||||
Годовое количество ТО-2 рассчитывается по формуле: | |||||||||||||||||||||||||||||||||||||||||||||||||||||||||||||||||
|
|
|
|
|
|
|
|
| |||||||||||||||||||||||||||||||||||||||||||||||||||||||||
N2 = Lг/L2р - NКР | (1.31) |
| |||||||||||||||||||||||||||||||||||||||||||||||||||||||||||||||
|
|
|
|
|
|
|
|
| |||||||||||||||||||||||||||||||||||||||||||||||||||||||||
Годовое количество ТО-1 рассчитывается по формуле: | |||||||||||||||||||||||||||||||||||||||||||||||||||||||||||||||||
|
|
|
|
|
|
|
|
| |||||||||||||||||||||||||||||||||||||||||||||||||||||||||
N1 = Lг/L1р – NКР – N2 | (1.32) |
| |||||||||||||||||||||||||||||||||||||||||||||||||||||||||||||||
|
|
|
|
|
|
|
|
| |||||||||||||||||||||||||||||||||||||||||||||||||||||||||
Рассчитывается сменная программа. | |||||||||||||||||||||||||||||||||||||||||||||||||||||||||||||||||
ТО-1. | |||||||||||||||||||||||||||||||||||||||||||||||||||||||||||||||||
|
|
|
|
|
|
|
|
| |||||||||||||||||||||||||||||||||||||||||||||||||||||||||
N1с = N1/(Дрт · Сст) | (1.33) |
| |||||||||||||||||||||||||||||||||||||||||||||||||||||||||||||||
|
|
|
|
|
|
|
|
| |||||||||||||||||||||||||||||||||||||||||||||||||||||||||
Дрт и Сст необходимо задать исходя из дней работы в году авто на линии, авторемонтной мастерской и обеспечения выполнения работ в межсменное время. | |||||||||||||||||||||||||||||||||||||||||||||||||||||||||||||||||
Чаще встречается режим работы 253 дня в году и 1 смена в сутки (вторая). [7, стр. 52, 53] | |||||||||||||||||||||||||||||||||||||||||||||||||||||||||||||||||
ТО-2 | |||||||||||||||||||||||||||||||||||||||||||||||||||||||||||||||||
N2с = N2/(Дрт · Сст) | (1.34) |
| |||||||||||||||||||||||||||||||||||||||||||||||||||||||||||||||
|
|
|
|
|
|
|
|
| |||||||||||||||||||||||||||||||||||||||||||||||||||||||||
В зоне ТО-2 наиболее распространен режим работы 253 дня в году и 1 смена (первая). [7, стр. 52, 53] | |||||||||||||||||||||||||||||||||||||||||||||||||||||||||||||||||
На основании сменной программы по ТО необходимо определиться со способом организации выполнения работ. | |||||||||||||||||||||||||||||||||||||||||||||||||||||||||||||||||
Рекомендуется: Техническое обслуживание проводится на поточных линиях при сменной программе не менее для: | |||||||||||||||||||||||||||||||||||||||||||||||||||||||||||||||||
ТО-1 - 6÷7 ТО-2 – 2÷3 | |||||||||||||||||||||||||||||||||||||||||||||||||||||||||||||||||
обслуживаний технологически совместимых автомобилей. | |||||||||||||||||||||||||||||||||||||||||||||||||||||||||||||||||
|
|
|
|
|
|
|
|
| |||||||||||||||||||||||||||||||||||||||||||||||||||||||||
Таблица 1.17- Расчет производственной программы по ТО-2 | |||||||||||||||||||||||||||||||||||||||||||||||||||||||||||||||||
Модель, марка п/состава | Lг тыс. км | L2р км | N2 | Дрт | Сст | N2с | Примечание | ||||||||||||||||||||||||||||||||||||||||||||||||||||||||||
|
|
|
|
|
|
|
| ||||||||||||||||||||||||||||||||||||||||||||||||||||||||||
|
|
|
|
|
|
|
|
| |||||||||||||||||||||||||||||||||||||||||||||||||||||||||
Таблица 1.18- Расчет производственной программы по ТО-1 | |||||||||||||||||||||||||||||||||||||||||||||||||||||||||||||||||
Модель, марка п/состава | Lг тыс. км | L1р км | N2 | N1 | Дрт | Сст | N1с | Прим. | |||||||||||||||||||||||||||||||||||||||||||||||||||||||||
|
|
|
|
|
|
|
|
| |||||||||||||||||||||||||||||||||||||||||||||||||||||||||
|
|
|
|
|
|
|
|
| |||||||||||||||||||||||||||||||||||||||||||||||||||||||||
В примечании указать принятый способ организации выполнения работ – на поточной линии, специализированных или универсальных постах. | |||||||||||||||||||||||||||||||||||||||||||||||||||||||||||||||||
Расчет годового количества сезонных обслуживаний выполняется по формуле: | |||||||||||||||||||||||||||||||||||||||||||||||||||||||||||||||||
|
|
|
|
|
|
|
|
| |||||||||||||||||||||||||||||||||||||||||||||||||||||||||
Nсо = 2 · Аи | (1.35) |
| |||||||||||||||||||||||||||||||||||||||||||||||||||||||||||||||
|
|
|
|
|
|
|
|
| |||||||||||||||||||||||||||||||||||||||||||||||||||||||||
Расчет программы работ на постах поэлементной диагностики. | |||||||||||||||||||||||||||||||||||||||||||||||||||||||||||||||||
|
|
|
|
|
|
|
|
| |||||||||||||||||||||||||||||||||||||||||||||||||||||||||
Nд2 = 1,2 · N2 | (1.36) |
| |||||||||||||||||||||||||||||||||||||||||||||||||||||||||||||||
|
|
|
|
|
|
|
|
| |||||||||||||||||||||||||||||||||||||||||||||||||||||||||
Сменная программа на постах Д-2 | |||||||||||||||||||||||||||||||||||||||||||||||||||||||||||||||||
Nд2с = Nд2/(Дрд ·Ссд) | (1.37) |
| |||||||||||||||||||||||||||||||||||||||||||||||||||||||||||||||
|
|
|
|
|
|
|
|
| |||||||||||||||||||||||||||||||||||||||||||||||||||||||||
где: Дрд – число дней работы в году постов Д-2. | |||||||||||||||||||||||||||||||||||||||||||||||||||||||||||||||||
Ссд – число смен работы в сутки постов Д-2. | |||||||||||||||||||||||||||||||||||||||||||||||||||||||||||||||||
Дрд и Ссд следует задаться с учетом обеспечения выполнения диагностики перед ТО-2, при необходимости перед ТР, и выборочно после ТР. | |||||||||||||||||||||||||||||||||||||||||||||||||||||||||||||||||
|
|
|
|
|
|
|
|
| |||||||||||||||||||||||||||||||||||||||||||||||||||||||||
Таблица 1.19- Расчёт производственной программы на постах Д-2 | |||||||||||||||||||||||||||||||||||||||||||||||||||||||||||||||||
Марка, модель п/состав | N2 | Nд2 | Дрд | Ссд | Nд2с |
| |||||||||||||||||||||||||||||||||||||||||||||||||||||||||||
|
|
|
|
|
|
| |||||||||||||||||||||||||||||||||||||||||||||||||||||||||||
|
|
|
|
|
|
|
|
| |||||||||||||||||||||||||||||||||||||||||||||||||||||||||
Расчёт программы работ на постах общей диагностики. | |||||||||||||||||||||||||||||||||||||||||||||||||||||||||||||||||
Годовое количество обслуживаний на постах Д-1. | |||||||||||||||||||||||||||||||||||||||||||||||||||||||||||||||||
|
|
|
|
|
|
|
|
| |||||||||||||||||||||||||||||||||||||||||||||||||||||||||
Nд1 = 1.1 · N1 + N2 | (1.38) |
| |||||||||||||||||||||||||||||||||||||||||||||||||||||||||||||||
|
|
|
|
|
|
|
|
| |||||||||||||||||||||||||||||||||||||||||||||||||||||||||
Сменная программа на постах Д-1 | |||||||||||||||||||||||||||||||||||||||||||||||||||||||||||||||||
Nд1с = Nд1/(Дрд · Ссд), | (1.39) |
| |||||||||||||||||||||||||||||||||||||||||||||||||||||||||||||||
|
|
|
|
|
|
|
|
| |||||||||||||||||||||||||||||||||||||||||||||||||||||||||
где: Дрд – число дней работы в году постов Д-1. | |||||||||||||||||||||||||||||||||||||||||||||||||||||||||||||||||
Ссд – число смен работы в сутки постов Д-1. | |||||||||||||||||||||||||||||||||||||||||||||||||||||||||||||||||
Дрд и Ссд следует задаться с учётом обеспечения выполнения диагностики перед ТО-1, выборочно при выпуске авто на линию и после ТО-1. | |||||||||||||||||||||||||||||||||||||||||||||||||||||||||||||||||
|
|
|
|
|
|
|
|
| |||||||||||||||||||||||||||||||||||||||||||||||||||||||||
Таблица 1.20- Расчёт производственной программы на постах Д – 1 | |||||||||||||||||||||||||||||||||||||||||||||||||||||||||||||||||
Марка, модель п/состава | N2 | N1
| Nд1
| Дрд
| Ссд
| Nд1с
|
| ||||||||||||||||||||||||||||||||||||||||||||||||||||||||||
| |||||||||||||||||||||||||||||||||||||||||||||||||||||||||||||||||
|
|
|
|
|
|
|
| ||||||||||||||||||||||||||||||||||||||||||||||||||||||||||
|
|
|
|
|
|
|
|
| |||||||||||||||||||||||||||||||||||||||||||||||||||||||||
|
|
|
|
|
|
|
|
| |||||||||||||||||||||||||||||||||||||||||||||||||||||||||
1.5. Расчет трудоемкости работ по обслуживанию автомобилей | |||||||||||||||||||||||||||||||||||||||||||||||||||||||||||||||||
|
|
|
|
|
|
|
|
| |||||||||||||||||||||||||||||||||||||||||||||||||||||||||
Трудоемкость работ ежедневного обслуживания включает в себя уборочные, моечные и обтирочные работы, выполняемые вручную (моечные – с помощью ручной шланговой мойки). | |||||||||||||||||||||||||||||||||||||||||||||||||||||||||||||||||
При применении механизации хотя бы одного из видов работ, трудоемкость рассчитывается по работам, выполняемым вручную. | |||||||||||||||||||||||||||||||||||||||||||||||||||||||||||||||||
Трудоемкость работ при использовании механизации рассчитывается по формуле: | |||||||||||||||||||||||||||||||||||||||||||||||||||||||||||||||||
|
|
|
|
|
|
|
|
| |||||||||||||||||||||||||||||||||||||||||||||||||||||||||
tумр = tео · Пр, чел.ч | (1.40) |
| |||||||||||||||||||||||||||||||||||||||||||||||||||||||||||||||
|
|
|
|
|
|
|
|
| |||||||||||||||||||||||||||||||||||||||||||||||||||||||||
где: Пр – процент работ выполняемых вручную. | |||||||||||||||||||||||||||||||||||||||||||||||||||||||||||||||||
Пр принимается на основании рекомендаций. | |||||||||||||||||||||||||||||||||||||||||||||||||||||||||||||||||
|
|
|
|
|
|
|
|
| |||||||||||||||||||||||||||||||||||||||||||||||||||||||||
Таблица 1.21- Примерное распределение трудоемкости ЕО по видам работы (в процентах) | |||||||||||||||||||||||||||||||||||||||||||||||||||||||||||||||||
Виды работ | Легковые автомобили | Автобусы | Грузовые автомобили | Прицепы и п/прицепы |
|
| |||||||||||||||||||||||||||||||||||||||||||||||||||||||||||
Уборочные | 30 | 45 | 23 | 25 |
|
| |||||||||||||||||||||||||||||||||||||||||||||||||||||||||||
Моечные | 55 | 35 | 65 | 65 |
|
| |||||||||||||||||||||||||||||||||||||||||||||||||||||||||||
Обтирочные | 15 | 20 | 12 | 10 |
|
| |||||||||||||||||||||||||||||||||||||||||||||||||||||||||||
Всего | 100 | 100 | 100 | 100 |
|
| |||||||||||||||||||||||||||||||||||||||||||||||||||||||||||
|
|
|
|
|
|
|
|
| |||||||||||||||||||||||||||||||||||||||||||||||||||||||||
Механизировать возможно не все работы, а только часть этих работ. Необходимо также для распределения рабочих в организационной части проекта знать процент работ каждого вида выполняемых ручным способом. | |||||||||||||||||||||||||||||||||||||||||||||||||||||||||||||||||
После приведения примера расчета результаты рекомендуется оформить в таблице: | |||||||||||||||||||||||||||||||||||||||||||||||||||||||||||||||||
|
|
|
|
|
|
|
|
| |||||||||||||||||||||||||||||||||||||||||||||||||||||||||
Таблица 1.22- Расчет трудоемкости уборочно-моечных работ | |||||||||||||||||||||||||||||||||||||||||||||||||||||||||||||||||
Марка, модель | Процент ручных работ в т.ч. | tео | tумр |
| |||||||||||||||||||||||||||||||||||||||||||||||||||||||||||||
п/состава | Убор. | Моеч. | Обтир. | Всего | чел.ч | чел.ч |
| ||||||||||||||||||||||||||||||||||||||||||||||||||||||||||
|
|
|
|
|
|
|
| ||||||||||||||||||||||||||||||||||||||||||||||||||||||||||
|
|
|
|
|
|
|
|
| |||||||||||||||||||||||||||||||||||||||||||||||||||||||||
Годовая трудоемкость уборочно-моечных работ рассчитывается по формуле: | |||||||||||||||||||||||||||||||||||||||||||||||||||||||||||||||||
Тумр = tумр · Nvмр, чел.-ч | (1.41) |
| |||||||||||||||||||||||||||||||||||||||||||||||||||||||||||||||
|
|
|
|
|
|
|
|
| |||||||||||||||||||||||||||||||||||||||||||||||||||||||||
Таблица 1.23- Расчет годовой трудоемкости уборочно-моечных работ | |||||||||||||||||||||||||||||||||||||||||||||||||||||||||||||||||
Марка, модель п/состава | tумр | Nумр | Тумр |
|
| ||||||||||||||||||||||||||||||||||||||||||||||||||||||||||||
чел.ч | чел.ч |
|
| ||||||||||||||||||||||||||||||||||||||||||||||||||||||||||||||
|
|
|
|
|
| ||||||||||||||||||||||||||||||||||||||||||||||||||||||||||||
Всего по парку |
|
|
|
|
| ||||||||||||||||||||||||||||||||||||||||||||||||||||||||||||
|
|
|
|
|
|
|
| ||||||||||||||||||||||||||||||||||||||||||||||||||||||||||
Годовая трудоемкость общей диагностики рассчитыватся по формуле: | |||||||||||||||||||||||||||||||||||||||||||||||||||||||||||||||||
Тд1 = tд1 · Nд1, чел.ч | (1.42) |
| |||||||||||||||||||||||||||||||||||||||||||||||||||||||||||||||
|
|
|
|
|
|
|
|
| |||||||||||||||||||||||||||||||||||||||||||||||||||||||||
Таблица 1.24- Расчет годовой трудоемкости общей диагностики | |||||||||||||||||||||||||||||||||||||||||||||||||||||||||||||||||
| Марка, модель | tд1 | Nд1 | Тд1 |
|
| |||||||||||||||||||||||||||||||||||||||||||||||||||||||||||
| п/состава | чел.ч |
| чел.ч |
|
| |||||||||||||||||||||||||||||||||||||||||||||||||||||||||||
|
|
|
|
|
|
| |||||||||||||||||||||||||||||||||||||||||||||||||||||||||||
Годовая трудоемкость поэлементной диагностики рассчитывается по формуле: | |||||||||||||||||||||||||||||||||||||||||||||||||||||||||||||||||
Тд2 = tд2 · Nд2, чел.ч | (1.44) |
| |||||||||||||||||||||||||||||||||||||||||||||||||||||||||||||||
|
|
|
|
|
|
|
|
| |||||||||||||||||||||||||||||||||||||||||||||||||||||||||
|
|
|
|
|
|
|
|
| |||||||||||||||||||||||||||||||||||||||||||||||||||||||||
Таблица 1.25- Расчет годовой трудоемкости поэлементной диагностики | |||||||||||||||||||||||||||||||||||||||||||||||||||||||||||||||||
| Марка, модель | tд2 | Nд2 | Тд2 |
|
| |||||||||||||||||||||||||||||||||||||||||||||||||||||||||||
| п/состава | чел.ч | чел.ч |
|
| ||||||||||||||||||||||||||||||||||||||||||||||||||||||||||||
|
|
|
|
|
|
| |||||||||||||||||||||||||||||||||||||||||||||||||||||||||||
| Всего по парку |
|
|
|
|
| |||||||||||||||||||||||||||||||||||||||||||||||||||||||||||
|
|
|
|
|
|
|
|
| |||||||||||||||||||||||||||||||||||||||||||||||||||||||||
Годовая трудоемкость ТО-1 рассчитывается по формуле: | |||||||||||||||||||||||||||||||||||||||||||||||||||||||||||||||||
|
|
|
|
|
|
|
|
| |||||||||||||||||||||||||||||||||||||||||||||||||||||||||
Т1 = t1 · N1, чел.ч | (1.45) |
| |||||||||||||||||||||||||||||||||||||||||||||||||||||||||||||||
|
|
|
|
|
|
|
|
| |||||||||||||||||||||||||||||||||||||||||||||||||||||||||
Таблица 1.26- Расчет годовой трудоемкости ТО-1 | |||||||||||||||||||||||||||||||||||||||||||||||||||||||||||||||||
| Марка, модель | t1 | N1 | Т1 |
|
| |||||||||||||||||||||||||||||||||||||||||||||||||||||||||||
| п/состава | чел.ч |
| чел.ч |
|
| |||||||||||||||||||||||||||||||||||||||||||||||||||||||||||
|
|
|
|
|
|
| |||||||||||||||||||||||||||||||||||||||||||||||||||||||||||
| Всего по парку |
|
|
|
|
| |||||||||||||||||||||||||||||||||||||||||||||||||||||||||||
|
|
|
|
|
|
|
|
| |||||||||||||||||||||||||||||||||||||||||||||||||||||||||
Годовая трудоемкость ТО-2 рассчитывается по формуле: | |||||||||||||||||||||||||||||||||||||||||||||||||||||||||||||||||
|
|
|
|
|
|
|
|
| |||||||||||||||||||||||||||||||||||||||||||||||||||||||||
Т2 = t2 · N2, чел.ч | (1.46) |
| |||||||||||||||||||||||||||||||||||||||||||||||||||||||||||||||
|
|
|
|
|
|
|
|
| |||||||||||||||||||||||||||||||||||||||||||||||||||||||||
Трудоемкость дополнительных работ сезонного обслуживания рассчитывается по формуле: | |||||||||||||||||||||||||||||||||||||||||||||||||||||||||||||||||
|
|
|
|
|
|
|
|
| |||||||||||||||||||||||||||||||||||||||||||||||||||||||||
tсо = Ссо · t 2 чел-ч | (1.47) |
| |||||||||||||||||||||||||||||||||||||||||||||||||||||||||||||||
|
|
|
|
|
|
|
|
| |||||||||||||||||||||||||||||||||||||||||||||||||||||||||
где: tсо - трудоемкость дополнительных работ сезонного обслуживания. | |||||||||||||||||||||||||||||||||||||||||||||||||||||||||||||||||
Ссо – процент дополнительных работ по сезонному обслуживанию от трудоемкости ТО-2, (1, п. 2.11.2). | |||||||||||||||||||||||||||||||||||||||||||||||||||||||||||||||||
Нормативы трудоемкости СО составляют от трудоемкости ТО-2: 50 % для очень холодного и очень жаркого сухого климатических районов; 30 % для холодного и жаркого сухого районов: 20 % для прочих районов. [1, п. 2.11.2] | |||||||||||||||||||||||||||||||||||||||||||||||||||||||||||||||||
Годовая трудоемкость сезонного обслуживания рассчитывается по формуле: | |||||||||||||||||||||||||||||||||||||||||||||||||||||||||||||||||
|
|
|
|
|
|
|
|
| |||||||||||||||||||||||||||||||||||||||||||||||||||||||||
Тсо = tco · Nco, чел.ч | (1.48) |
| |||||||||||||||||||||||||||||||||||||||||||||||||||||||||||||||
|
|
|
|
|
|
|
|
| |||||||||||||||||||||||||||||||||||||||||||||||||||||||||
Таблица 1.27- Расчет годовой трудоемкости ТО-2 и сезонного обслуживания | |||||||||||||||||||||||||||||||||||||||||||||||||||||||||||||||||
Марка, модель п/состава | t2 чел.ч | N2
| T2 чел.ч | tсо чел.ч | Nсо
| Tсо чел.ч |
| ||||||||||||||||||||||||||||||||||||||||||||||||||||||||||
| |||||||||||||||||||||||||||||||||||||||||||||||||||||||||||||||||
|
|
|
|
|
|
|
| ||||||||||||||||||||||||||||||||||||||||||||||||||||||||||
Всего по парку |
|
|
|
|
|
|
| ||||||||||||||||||||||||||||||||||||||||||||||||||||||||||
|
|
|
|
|
|
|
|
| |||||||||||||||||||||||||||||||||||||||||||||||||||||||||
Годовая трудоемкость работ по текущему ремонту рассчитывается по формуле: | |||||||||||||||||||||||||||||||||||||||||||||||||||||||||||||||||
|
|
|
|
|
|
|
|
| |||||||||||||||||||||||||||||||||||||||||||||||||||||||||
Ттр = tтр · Lг/1000, чел.ч | (1.49) |
| |||||||||||||||||||||||||||||||||||||||||||||||||||||||||||||||
|
|
|
|
|
|
|
|
| |||||||||||||||||||||||||||||||||||||||||||||||||||||||||
|
|
|
|
|
|
|
|
| |||||||||||||||||||||||||||||||||||||||||||||||||||||||||
Таблица 1.28- Годовая трудоемкость работ по текущему ремонту | |||||||||||||||||||||||||||||||||||||||||||||||||||||||||||||||||
Марка, модель п/состава | tтр, чел.ч/1000 км | Lг, тыс. км | Tтр, чел.ч |
| |||||||||||||||||||||||||||||||||||||||||||||||||||||||||||||
| |||||||||||||||||||||||||||||||||||||||||||||||||||||||||||||||||
|
|
|
|
| |||||||||||||||||||||||||||||||||||||||||||||||||||||||||||||
|
|
|
|
|
|
|
|
| |||||||||||||||||||||||||||||||||||||||||||||||||||||||||
1.6. Распределение трудоемкости обслуживания по производственным зонам предприятия | |||||||||||||||||||||||||||||||||||||||||||||||||||||||||||||||||
|
|
|
|
|
|
|
|
| |||||||||||||||||||||||||||||||||||||||||||||||||||||||||
Трудоемкость работ в зоне ЕО (ΣТЕО) принимается равной трудоемкости УМР | |||||||||||||||||||||||||||||||||||||||||||||||||||||||||||||||||
Трудоемкость работ в зоне диагностики принимается равной | |||||||||||||||||||||||||||||||||||||||||||||||||||||||||||||||||
|
|
|
|
|
|
|
|
| |||||||||||||||||||||||||||||||||||||||||||||||||||||||||
ΣТд = Тд1 + Тд2, чел. ч | (1.50) |
| |||||||||||||||||||||||||||||||||||||||||||||||||||||||||||||||
|
|
|
|
|
|
|
|
| |||||||||||||||||||||||||||||||||||||||||||||||||||||||||
Трудоемкость работ в зоне ТО-1 рассчитывается по формуле: | |||||||||||||||||||||||||||||||||||||||||||||||||||||||||||||||||
|
|
|
|
|
|
|
|
| |||||||||||||||||||||||||||||||||||||||||||||||||||||||||
ΣТ1 З = с · Т1 + Тсоп1, чел. ч | (1.51) |
| |||||||||||||||||||||||||||||||||||||||||||||||||||||||||||||||
|
|
|
|
|
|
|
|
| |||||||||||||||||||||||||||||||||||||||||||||||||||||||||
с – коэффициент, учитывающий способ организации выполнения работ в зоне ТО-1. | |||||||||||||||||||||||||||||||||||||||||||||||||||||||||||||||||
Тсоп1 – трудоемкость сопутствующего текущего ремонта, выполняемого в зоне ТО-1. | |||||||||||||||||||||||||||||||||||||||||||||||||||||||||||||||||
с = 1 при организации производства ТО-1 без применения поточной линии. | |||||||||||||||||||||||||||||||||||||||||||||||||||||||||||||||||
с = 0,75-:-0,80 при применении поточной линии на ТО-1. | |||||||||||||||||||||||||||||||||||||||||||||||||||||||||||||||||
|
|
|
|
|
|
|
|
| |||||||||||||||||||||||||||||||||||||||||||||||||||||||||
Тсоп1 = 0,10 · Т1, чел.ч | (1.52) |
| |||||||||||||||||||||||||||||||||||||||||||||||||||||||||||||||
Таблица 1.29- Расчет трудоемкости работ в зоне ТО-1 | |||||||||||||||||||||||||||||||||||||||||||||||||||||||||||||||||
Модель, марка п/состава | Т1 чел.ч | с | Тд1 чел.ч | Тсоп1 чел.ч | Т13 чел.ч |
| |||||||||||||||||||||||||||||||||||||||||||||||||||||||||||
| |||||||||||||||||||||||||||||||||||||||||||||||||||||||||||||||||
|
|
|
|
|
|
| |||||||||||||||||||||||||||||||||||||||||||||||||||||||||||
Всего по парку |
|
|
|
|
|
| |||||||||||||||||||||||||||||||||||||||||||||||||||||||||||
|
|
|
|
|
|
|
|
| |||||||||||||||||||||||||||||||||||||||||||||||||||||||||
Трудоемкость работ в зоне ТО-2 рассчитывается по формуле: | |||||||||||||||||||||||||||||||||||||||||||||||||||||||||||||||||
|
|
|
|
|
|
|
|
| |||||||||||||||||||||||||||||||||||||||
ΣТ2 З = с · (Т2 + Тсо) + Тсоп2, чел.ч | (1.53) |
| |||||||||||||||||||||||||||||||||||||||||||||
|
|
|
|
|
|
|
|
| |||||||||||||||||||||||||||||||||||||||
где: с – коэффициент, учитывающий способ организации выполнения работ в зоне ТО-2. | |||||||||||||||||||||||||||||||||||||||||||||||
Тсоп2 – трудоемкость сопутствующего текущего ремонта, выполняемого в зоне ТО-2. | |||||||||||||||||||||||||||||||||||||||||||||||
с = 1 при организации производства ТО-2 без применения поточной линии. | |||||||||||||||||||||||||||||||||||||||||||||||
с = 0,75-:-8,0 при применении поточной линии на ТО-2. | |||||||||||||||||||||||||||||||||||||||||||||||
|
|
|
|
|
|
|
|
| |||||||||||||||||||||||||||||||||||||||
Тсоп2 = 0,20 · Т2, чел.ч | (1.54) |
| |||||||||||||||||||||||||||||||||||||||||||||
|
|
|
|
|
|
|
|
| |||||||||||||||||||||||||||||||||||||||
Таблицу 1.30- Расчет трудоемкости работ в зоне ТО-2 | |||||||||||||||||||||||||||||||||||||||||||||||
Модель, марка п/состава | Т2 чел.ч | Тсо чел.ч | с | Тд2 чел.ч | Тсоп2 чел.ч | Т23 чел.ч | |||||||||||||||||||||||||||||||||||||||||
|
|
|
|
|
| ||||||||||||||||||||||||||||||||||||||||||
Всего по парку |
|
|
|
|
|
| |||||||||||||||||||||||||||||||||||||||||
|
|
|
|
|
|
|
|
| |||||||||||||||||||||||||||||||||||||||
Годовая трудоемкость работ в зоне ТР рассчитывается по формуле: | |||||||||||||||||||||||||||||||||||||||||||||||
|
|
|
|
|
|
|
|
| |||||||||||||||||||||||||||||||||||||||
ΣТтр з = С3·Ттр – Тсоп1 – Тсоп2, чел.ч | (1.55) |
| |||||||||||||||||||||||||||||||||||||||||||||
|
|
|
|
|
|
|
|
| |||||||||||||||||||||||||||||||||||||||
где: Ттр – годовая трудоемкость работ в зоне ТР. | |||||||||||||||||||||||||||||||||||||||||||||||
С3 – суммарная доля постовых работ по ТР [5. табл.2.15]
| |||||||||||||||||||||||||||||||||||||||||||||||
Таблица 1.31- Годовая трудоемкость работ в зоне текущего ремонта | |||||||||||||||||||||||||||||||||||||||||||||||
Марка, модель п/состава | Ттр чел.ч | Сз | Тсоп1 чел.ч | Тсоп2 чел.ч | Ттрз чел.ч | ||||||||||||||||||||||||||||||||||||||||||
|
|
|
|
|
| ||||||||||||||||||||||||||||||||||||||||||
|
|
|
|
|
| ||||||||||||||||||||||||||||||||||||||||||
Если объектом проектирования являются отдельные участки или ремонтные цеха, то годовая трудоемкость принимается исходя из процентного соотношения по видам работ к Ттр [4. табл. 16]. При этом следует учесть, что на малых АТП объем отдельных видов работ может не обеспечивать загрузку даже одного рабочего. В связи с этим по необходимости производится совмещение работ по технологически совместимым группам и формируются соответствующие участки, на которых эти работы будут выполняться | |||||||||||||||||||||||||||||||||||||||||||||||
Трудоемкость работ каждого производственного отделения (участка), относящегося к зоне текущего ремонта, определяется по формуле | |||||||||||||||||||||||||||||||||||||||||||||||
| (1.56) |
| |||||||||||||||||||||||||||||||||||||||||||||
|
|
|
|
|
|
|
|
| |||||||||||||||||||||||||||||||||||||||
Суммарная трудоемкость обслуживания автомобилей определяется по формуле: | |||||||||||||||||||||||||||||||||||||||||||||||
|
|
|
|
|
|
|
|
| |||||||||||||||||||||||||||||||||||||||
ΣТ = ΣТЕО + ΣТд + ΣТ1 + ΣТ2 + ΣТтр, чел.ч | (1.57) |
| |||||||||||||||||||||||||||||||||||||||||||||
|
|
|
|
|
|
|
|
| |||||||||||||||||||||||||||||||||||||||
| |||||||||||||||||||||||||||||||||||||||||||||||
|
|
|
|
|
|
|
|
| |||||||||||||||||||||||||||||||||||||||
|
|
|
|
|
|
| |||||||||||||||||||||||||||||||||||||||||
|
|
|
|
|
|
|
|
| |||||||||||||||||||||||||||||||||||||||
1.7. Расчет численности производственных рабочих | |||||||||||||||||||||||||||||||||||||||||||||||
|
|
|
|
|
|
|
|
| |||||||||||||||||||||||||||||||||||||||
В разделе рассчитывается общее число исполнителей, необходимое для выполнения производственной программы АТП, исходя из суммарной трудоемкости обслуживания автомобилей, а так же на объекте проектирования. | |||||||||||||||||||||||||||||||||||||||||||||||
При расчете численности производственного персонала различают явочное и списочное – Ря и Рсп число исполнителей. | |||||||||||||||||||||||||||||||||||||||||||||||
Явочное число рабочих (число рабочих мест). | |||||||||||||||||||||||||||||||||||||||||||||||
|
|
|
|
|
|
|
|
| |||||||||||||||||||||||||||||||||||||||
Ря = Тг/Фн | (1.57) |
| |||||||||||||||||||||||||||||||||||||||||||||
|
|
|
|
|
|
|
|
| |||||||||||||||||||||||||||||||||||||||
где: Тг – годовой объем работ (трудоемкость); | |||||||||||||||||||||||||||||||||||||||||||||||
Фн – номинальный годовой фонд времени рабочего места. | |||||||||||||||||||||||||||||||||||||||||||||||
Тг принимается по предыдущим расчетам для проектируемой зоны, цеха, установка. Фн принимаем согласно рекомендациям. [5. п. 2.2.3] Номинальный годовой фонд времени мастерской, участка, рабочего или оборудования определяется по формуле (16), но на год
| |||||||||||||||||||||||||||||||||||||||||||||||
Списочное число исполнителей. | |||||||||||||||||||||||||||||||||||||||||||||||
|
|
|
|
|
|
|
|
| |||||||||||||||||||||||||||||||||||||||
Рсп = Тг/Фд | (1.59) |
| |||||||||||||||||||||||||||||||||||||||||||||
где: Тг – годовой объем работ (трудоемкость); | |||||||||||||||||||||||||||||||||||||||||||||||
Фд – действительный годовой фонд времени штатного рабочего. Действительный фонд времени рабочего определяют по формуле
| |||||||||||||||||||||||||||||||||||||||||||||||
Тг принимается по предыдущим расчетам для проектируемой зоны, цеха, участка. | |||||||||||||||||||||||||||||||||||||||||||||||
Окончательно число исполнителей на объекте проектирования принимается после распределения трудоемкостей по производственным подразделениям с учетом нагружения рабочих на 95 – 115%. | |||||||||||||||||||||||||||||||||||||||||||||||
Дата добавления: 2019-07-15; просмотров: 155; Мы поможем в написании вашей работы! |
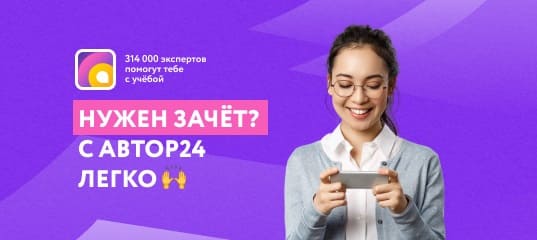
Мы поможем в написании ваших работ!