Влияние постоянных примесей на углеродистые стали.
Основной продукцией черной металлургии является сталь, причем приблизительно 85% изготавливается углеродистой стали и 15% легированной. Углеродистая сталь является основным металлическим материалом российской промышленности.
Получаемая в промышленности углеродистая сталь имеет сложный химический состав (табл. 2.4.). Содержание железа в ней находится в пределах 97,0 – 99,5% в нее попадает некоторое количество элементов, связанное с технологией производства (марганец, кремний) или невозможностью полного их удаления из состава металла (сера, фосфор, кислород, азот, водород), случайные примеси (хром, никель, медь) и, кроме того, некоторые неметаллические включения.
В зависимости от способа выплавки (конверторный, мартеновский, в электропечах) стали различаются содержанием примесей.
Постоянными примесями в стали считаются такие, которые попадают в нее в процессе получения, разливки, а также из исходных материалов, топлива, футеровки печей и атмосферы.
Марганец в виде оксида МnO2 – пиролюзита – постоянно находится в железных рудах, следовательно, он присутствует в сталях и чугунах. Марганец также попадает в стали при раскислении ее ферромарганцем при выплавке, часть марганца взаимодействует с основными компонентами стали и в процессе кристаллизации переходит в ее фазовые составляющие – феррит и цементит.
Аналогично воздействует на свойства стали кремний, растворяющийся только в феррите. Кремний в виде соединения SiO2 – кремнезема – всегда имеется в железной руде (эту часть руды называют пустой породой). К раскислителям, которыми пользуются при выплавке стали, относится кремнийсодержащий материал - ферросилиций, активно вступающий с закисью железа в реакцию обмена. Поэтому присутствие небольшого количества кремния в стали также является технологически неизбежным.
|
|
К постоянным примесям в стали относятся фосфор и сера. Эти элементы оказывают существенное влияние на механические, технологические и другие свойства стали, поэтому их количество в различных марках строго регламентируется.
Сера присутствует в небольших количествах в железных рудах и металлургическом топливе и поэтому попадает в сталь во время металлургического процесса. Сера находится в стали в связанном состоянии в виде механических примесей (FeS и MnS), которые по-разному взаимодействуют с компонентами стали и соответственно влияют на ее свойства. Сульфид железа существенно снижает прочность и пластичность стали. Это отрицательно сказывается при технологической обработке стали в горячем состоянии (800 – 1200 °С) и проявляется в виде явления красноломкости. Температура плавления MnS существенно выше 1620 °C и присутствует в стали в виде мелких включений, которые не оплавляются в процессе ее обработки. Количество серы вызывает охрупчивание стали, и поэтому содержание ее жестко отслеживается. Для ответственных деталей содержание серы может быть не более 0,03 – 0,04% , а в обычных сталях допускается 0,05%.
|
|
Постоянные примеси – марганец и кремний – оказывают в какой-то степени положительное влияние на механические свойства стали, а фосфор и сера ухудшают их и являются очень вредными примесями.
При выплавке и разливке стали в нее из окружающей атмосферы попадают кислород, азот, водород и другие газы.
Кислород в кристаллической решетке железа не растворяется, поэтому в стали он присутствует в виде зерен оксидов железа FeO, Fe2O3 и оксидов других элементов. Эти неметаллические включения снижают прочностные и пластические свойства стали.
Азот в очень малых количествах способен растворяться в феррите, упрочняя и одновременно охрупчивая его. Некоторое количество азота в стали образует с железом нитриды, которые располагаются в стали в виде включений и также охрупчивают ее.
При выплавке стали в нее попадает водород, растворяется в ней и, так как он не образует с железом гидридов, выходит из нее по мере снижения температуры. Некоторое количество оставшегося водорода в стали охрупчивает ее. Этот не растворившийся водород в стали образует флокены (микроскопические трещины овальной формы, имеющие на изломе вид белых пятен). Их появление свидетельствует о внутренних разрывах в металле. Для предотвращения флокенов сталь после горячего деформирования медленно охлаждают или длительно выдерживают при 250°С.
Дата добавления: 2019-02-22; просмотров: 502; Мы поможем в написании вашей работы! |
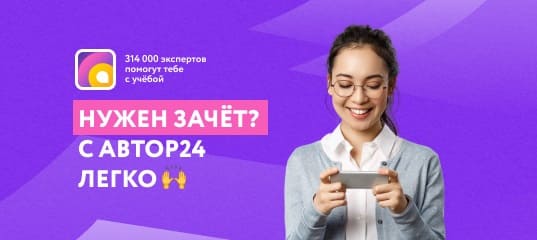
Мы поможем в написании ваших работ!