Технология производства различных железобетонных конструкций
Бетон – искусственный каменный материал, полученный в результате уплотнения, твердения бетонной смеси заданной подвижности, состоящей из минерального вяжущего воды, заполнителей и добавок.
Получение бетонных и железобетонных изделий включает следующие технологические этапы: входной контроль качества всех используемых материалов (вяжущего, заполнителей, добавок, арматуры, закладных деталей и т.д.); расчет состава бетонной смеси и его лабораторную проверку; приготовление бетонной смеси на заводе или строительной площадке; транспортировку ее к месту изготовления конструкции; укладку в форму (опалубку) и уплотнение; твердение бетона; раскрытие формы (снятие опалубки); отправку готовых изделий на строительную площадку или склад готовой продукции.
Расчет состава бетонной смеси проводят с использованием графиков и таблиц на основании следующих данных: условий эксплуатации будущей конструкции, с учетом которых подбирают необходимые исходные материалы; показателей качества компонентов; проектируемого класса бетона; подвижности бетонной смеси, которую выбирают в зависимости от размеров бетонируемой конструкции, густоты армирования и способа уплотнения. Правильность расчета проверяют в лабораторных условиях по соответствию подвижности смеси и прочности бетона заданным значениям.
По способу изготовления конструкции подразделяют на монолитные и сборные. При бетонировании монолитных конструкций: фундаментов, стен, перекрытий, гидротехнических сооружений, дорожных покрытий, бетонную смесь приготавливают на заводе (товарный бетон) и транспортируют к месту укладки на строительную площадку, где бетон твердеет в естественных условиях. Сборные конструкции (балки, плиты, колонны, панели, фермы и т.д.) получают на специализированных заводах (ЖБИ, ЖБК, КСМ) откуда их транспортируют на строительную площадку для монтажа.
|
|
Приготовление бетонной смеси включает подготовку материалов, их дозирование и перемешивание в специальных бетоносмесителях. Полученная бетонная смесь должна обладать связностью, однородностью и удобоукладываемостью (формуемостью) . Контроль удобоукладываемости проводят по двум показателям: подвижности и жесткости. Подвижностьопределяют для пластичных бетонных смесей, замеряя осадку в сантиметрах отформованного усеченного стандартного конуса. Этот показатель является статической характеристикой структурной прочности бетонной смеси, т.к. ее осадка происходит под действием собственной массы. В зависимости от величины осадки конуса (ОК) различают низкопластичные смеси ОК 1 – 9 см, пластичные – ОК 10 – 20 и литые – ОК более 20 см. При значении осадки конуса менее 1 см удобоукладываемость характеризуется жесткостью. Жесткость – динамический показатель вязкости бетонной смеси, потому что при его определении используют механическое воздействие – вибрацию, под действием которой отформованная бетонная смесь равномерно заполняет определенный объем. Если необходимое время вибрации составляет от 5 до 40 с – смесь жесткая, при более 40 с – сверхжесткая.
|
|
Удобоукладываемость зависит от объема и вязкости цементного теста, обеспечивающего связность и однородность смеси, а также пористости, крупности и формы заполнителя. При высоком содержании воды вязкость цементного теста снижается и не обеспечивает равномерного взвешенного распределения заполнителя по всему объему, в связи с чем наблюдается расслоение бетонной смеси и, как следствие, неоднородность свойств бетона в конструкции.
Наблюдаемое в этом случае водоотделение приводит к формированию пористой, дефектной структуры, особенно поверхностного слоя бетона. Такие отрицательные явления наблюдаются чаще всего при приготовлении и особенно транспортировке и уплотнении пластичных, литых смесей. Поэтому для повышения их однородности и связности увеличивают расход цемента, вводят пластификаторы и суперпластификаторы, увеличивают расход мелкого заполнителя или применяют минеральные водоудерживающие, гидрофильные добавки типа бентонитовой глины.
|
|
Для получения бетонов высоких марок используют бетонные смеси с низким водосодержанием. Их качественную удобоукладываемость обеспечивают за счет увеличения крупности заполнителей, отсутствия лещадных и игловатых зерен в щебне, введения добавок пластификаторов и суперпластификаторов. После приготовления бетонную смесь транспортируют к месту укладки. На территории завода для этой цели используют бункеры, бетонораздатчики, для получения монолитного железобетона – автосамосвалы, автобетоносмесители, автобетоновозы. Одним из прогрессивных методов непрерывной подачи бетонной смеси на строительные площадки, полигоны и в цеха завода является транспортировка по трубопроводам с использованием специальных бетононасосов.
Смесь подают в очищенную и смазанную форму или опалубку, в которые согласно проекта, устанавливают арматуру. После заполнения объема, производят уплотнение бетонной смеси для равномерного распределения и придания заданных формы и размеров. Основные методы уплотнения связаны с вибрационным воздействием, под влиянием которого проявляются тиксотропные свойства смеси – способность снижать вязкость (разжижаться) в результате нарушения сцепления между компонентами под влиянием вибрации и восстанавливать структурную целостность и прочность после снятия механического воздействия.
|
|
При бетонировании монолитных конструкций используют пластичные смеси, которые уплотняют глубинными и поверхностными вибраторами. Сборные железобетонные конструкции выполняют из бетона высоких классов, поэтому для уплотнения сверхжестких и жестких бетонных смесей применяют более массированное воздействие с использованием пригруза: вибропрокат и виброштампование . Для низкопластичных и пластичных смесей используют вибрационный и безвибрационный – ударный, основанный на циклическом подъеме формы со смесью и падения с заданной высоты. Литые смеси заполняют форму под действием собственной массы (наливной). С целью ускорения твердения и повышения прочности используют дополнительное вибровакуумирование, позволяющее за счет создаваемой разности верхнего и нижнего по отношению к поверхности изделия давления отвести часть воды, повысив плотность бетона. Для изготовления полых изделий (труб, колонн) применяют центробежныйспособ формовки, основанный на равномерном распределении по внутренней поверхности вращаемой формы и уплотнении подаваемой бетонной смеси под действием центробежной силы.
Для защиты бетонной поверхности и производства прочных тонкостенных конструкций используют набивной метод, предусматривающий подачу в форму или на поверхность конструкции, бетонной смеси под давлением – торкрет бетон. К бетонным дорожным изделиям: бордюрные камни, тротуарные плитки предъявляют высокие требования по износостойкости и морозостойкости. Для обеспечения заданных свойств необходимо работать со сверхжесткими бетонными смесями или с сухими, укладываемыми и уплотняемыми прессованием в формах в сухом состоянии с последующим предельно минимальным водонасыщением паром или раствором химических добавок. Таким образом, получают изделия прочностью до 80 МПа, водопоглощением менее 2%, морозостойкостью более F1000 и низкой истираемостью.
После формовки бетон в конструкциях твердеет и приобретает проектируемую прочность искусственного камня. Режим твердениязависит от способа получения конструкций: монолитные–в естественных условиях , сборные –с использованием термовлажностной обработки при нормальном и повышенном давлении в автоклавах.
В зависимости от климатических условий монолитные конструкции твердеют при низкой положительной и отрицательной температурах, положительной оптимальной 20±5ºС и при высокой температуре и низкой влажности. Так как интенсивность процесса твердения (гидратации) зависит от температурно-влажностных условий, то каждый из режимов имеет свои технологические особенности.
Для обеспечения твердения при низкой положительной температуре необходимо использовать высокомарочные быстротвердеющие цементы, добавки ускорители твердения или комплексные состоящие из ускорителей и пластификаторов, позволяющие ускорить набор прочности за счет сокращения расхода воды. В связи с переходом воды при отрицательной температуре в твердофазовое кристаллическое состояние, исключающее возможность прохождения химических реакций гидратации, методы зимнего бетонирования предусматривают использование определенного вида энергии для сохранения воды в жидком состоянии.
В зависимости от вида используемой энергии способы подразделяют на безобогревныеи обогревные. Первые используют энергию гидратации цемента – метод «термоса» или способность некоторых солей (NaCl, CaCl2, K2CO3) при растворении в воде снижать температуру замерзания раствора – методпротивоморозных добавок. По способу «термоса» получают массивные железобетонные фундаменты, защищенные с трех сторон слоем земли и с четвертой – наружной – плитным теплоизоляционным материалом определенной расчетной толщины. Для ускорения набора прочности применяют быстротвердеющие цементы, добавки ускорители твердения, или повышают начальную температуру бетонной смеси до укладывания ее в опалубку за счет подогрева воды и заполнителей на заводе или кратковременного электропрогрева при помощи электродов непосредственно на строительной площадке.
Дата добавления: 2019-03-09; просмотров: 156; Мы поможем в написании вашей работы! |
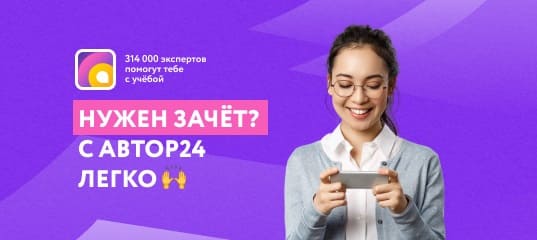
Мы поможем в написании ваших работ!