Типовые групповые замерные установки
Введение
Измерение количества добываемой продукции нефтяных и газовых скважин имеет особое значение в системах сбора и подготовки углеводородного сырья. В частности, данные по количественным замерам необходимы при выборе техники и технологии сбора и подготовки нефти, газа и воды, а также при анализе динамики разработки нефтяных и газовых месторождений с целью установления оптимального их режима работы.
Продукция скважин на разных нефтедобывающих предприятиях может измеряться различными способами. В зависимости от способа замера используется соответствующее оборудование, позволяющее наиболее качественно выполнить данный замер.
В данных методических указаниях приведены основные способы измерения расхода потока и замерное оборудование нефтяных скважин. Перед выполнением лабораторных работ требуется ознакомиться с целью работы и ее содержанием. Оформление отчета выполнить в соответствии с требованиями к нему. Для проверки усвоения материала необходимо ответить на ряд предлагаемых контрольных вопросов.
Общие сведения
Способы измерения расхода жидкости и газа
Приборы, предназначенные для измерения расходов жидкости и газа в промышленности, разнообразны как по методам измерения, так и по конструктивному оформлению. Применение прибора того или иного типа зависит от технологических требований, характера измеряемого вещества и экономической целесообразности.
|
|
Наиболее простыми и точными способами измерения расхода являются объемные и массовые (весовые) способы при помощи мерных емкостей.
При объемном способе измерения протекающая в исследуемом потоке (например, в трубе) жидкость поступает в тарированный сосуд («мерник»), время наполнения которого точно фиксируется по секундомеру. Если объем мерника - V , а измеренное время его наполнения - Т, объемный расход будет равен V/t.
При массовом (весовом) способе взвешиванием находят массу (вес) всей жидкости, поступившей в мерник за время Т и соответствующий массовый (весовой) расход.
Однако данные способы пригодны лишь при сравнительно небольших значениях расхода жидкости, так как в противном случае размеры мерников получаются громоздкими и замеры затруднительны; кроме того, этими способами невозможно замерить расход в произвольном сечении длинного трубопровода без нарушения его целостности. Поэтому при трубопроводном транспорте различных потоков пользуются специальными приборами - расходомерами, устанавливаемыми непосредственно на трубопроводе (трубный способ замера), которые также тарируют объемным или массовым (весовым) способом. К таким приборам, в частности, относятся приборы, основанные на измерении скорости течения жидкости, по которым определяют расход потока.
|
|
При нефтепромысловом сборе и транспорте могут использоваться все перечисленные способы замера, но более всего применимы «трубные» способы замера. Расходомеры используют как в составе замерных установок на нефтегазовых скважинах, так и на нефтеперекачивающих станциях и пунктах сбора и подготовки. Ниже рассматриваются основные разновидности расходомеров и замерные нефтепромысловые установки.
Объёмные расходомеры
Данные расходомеры могут быть разделены на две группы.
К первой группе относятся устройства, в которых чувствительный элемент непосредственно преобразует скорость потока в измерительный сигнал (турбинные расходомеры).
Ко второй группе относятся устройства, в которых в потоке создаются промежуточные измерительные параметры, по изменению которых можно судить о величине скорости, а, следовательно, и объемного расхода. Такими промежуточными параметрами могут являться перепад давления, звуковые и ультразвуковые колебания, возбуждаемые или распространяющиеся в потоке, ионизация потока, формирование в движущейся среде ионного тока, создаваемого под действием внешнего магнитного поля.
|
|
Расходомеры переменного перепада давления
Принцип действия расходомеров данного типа основан на измерении перепада давления, образующегося в результате местного изменения скорости потока жидкости, газа или пара.
Для измерения расхода жидкостей, газов и паров по перепаду давления необходимы три элемента:
- устройство, создающее перепад давления в потоке измеряемой среды за счет местного
изменения скорости потока или по величине (сужающие устройства), или по направлению (изогнутые
участки трубы);
- измерительный прибор — дифференциальный манометр, измеряющий перепад давления;
- соединительное устройство, передающее перепад давления от потока к дифмаиометру.
Расходомер Вентури (рис.1).
Расходомер Вентури можно устанавливать как вертикально, так и горизонтально.
2 1
Рис. 1. Схема расходомера Вентури
На практике вместо вычисления по формулам расход жидкости часто определяют по так называемым тарировочным кривым, полученным опытным путем и дающим для данного расходомера прямую зависимость между показаниями манометра и измеряемыми расходами жидкости.
Диафрагменный расходомер -используется в основном для измерения расхода газа. Принцип действия основан на изменении перепада давления, обусловленного установленной на газопроводе диафрагмой, имеющей меньшее проходное сечение.
|
|
Применяют диафрагмы двух типов: плоские и камерные.
Плоская диафрагма представляет собой тонкий диск, имеющий отверстие, концентричное оси трубы с острой прямоугольной кромкой со стороны входа потока. Соосность установки диафрагмы, острота входной кромки, ее прямоугольность и технологический допуск на входной диаметр d диафрагмы определяют возможность и точность косвенной градуировки расходомеров переменного перепада давления с нормальными диафрагмами. Поэтому к этим параметрам диафрагмы предъявляют весьма высокие требования. Так, допустимое отклонение оси отверстия диафрагмы от оси трубы должно быть не более 0,015D(d/D-l). где D — диаметр трубопровода.
Давления у плоской диафрагмы отбирают с помощью отдельных сверлений. Для усреднения давлений просверливают несколько отверстий, равномерно распределенных по окружности трубы в плоскости отбора. Выходящие из отверстий трубки объединяются двумя сборными коллекторами, от которых перепад давления передается к дифманометрам.
На нефтяных месторождениях наиболее распространены камерные диафрагмы (рис. 2). Принцип работы их в том, что когда газ проходит через суженное сечение диафрагмы, его скорость увеличивается, а давление уменьшается. За диафрагмой происходит обратное: скорость газа уменьшается, а давление увеличивается, но не до начального.
Давления у камерных диафрагм отбирают из камер, соединенных с трубой кольцевыми щелями. Преимуществом камерных диафрагм является отбор действительных средних давлений и в связи с этим несколько менее жесткие требования к длине прямолинейных участков трубопровода до и после диафрагмы; недостатком — необходимость специальных уплотнительных устройств для герметизации камер.
|
Рис. 2. Камерная диафрагма: 1 - разделительный сосуд; 2 — дифференциальный манометр
Турбинные расходомеры (крыльчато-тахометрические)
Крыльчато-тахометрические (турбинные) расходомеры относятся к скоростным расходомерам и являются наиболее точными приборами для измерения расхода жидкостей. Приведенная погрешность измерения расхода турборасходомерами составляет величину порядка 0.5 - 1.0 % (известны турборасходомеры с приведенной погрешностью 0.1 - 0.2 %).
Приборы просты по конструкции, обладают большой чувствительностью и большими пределами измерений (для одной модификации 10:1 и более), возможностью измерения как малых (от 5.10"9 м3/с), так и больших (до 1 м3/с) расходов жидкостей с широким диапазоном физико-химических свойств, малой инерционностью и вследствие этого относительно малыми динамическими ошибками при измерении средних и мгновенных значений пульсирующих расходов. Их применяют там, где требования к точности измерений имеют превалирующее значение — в ракетной, авиационной технике, химической и нефтедобывающей промышленности.
Принцип действия крыльчато-тахометркческкх расходомеров, предназначенных для измерения потоков, заключается в следующем. В измеряемый поток помещается сбалансированная легкая крыльчатка, вращающаяся в подшипниках, обладающих малым трением. Крыльчатка под давлением движущегося потока совершает вращательное движение. При стационарном режиме скорость ее вращения пропорциональна скорости потока. Конструктивно крыльчатка может быть выполнена аксиальной или тангенциальной (рис. 3).
|
|
Рис. 3 — Типы турбинок а — аксиальная; б — тангенциальная
Измерение числа оборотов крыльчатки может производиться различными способами: электрическим, радиоактивным, фотоэлектрическим и др. Полученный пульсирующий электрический сигнал, число пульсаций которого в единицу времени пропорционально числу оборотов крыльчатки, после усиления подается на частотомер, измерительный сигнал с которого поступает на регистрирующий прибор
К недостаткам турбинных расходомеров существующих модификаций, можно отнести:
- необходимость индивидуальной градуировки и вследствие этого необходимость наличия
градуировочных расходомерных устройств высокой точности;
- влияние изменения вязкости измеряемой среды на показания приборов;
- наличие изнашивающихся опор, что резко сокращает срок службы
- закрутка потока, вызванная влиянием местных сопротивлений.приборов (особенно при измерении
расхода абразивных сред) и приводит к снижению их точности в процессе эксплуатации.
Вследствие этого данные приборы мало пригодны для измерения расхода загрязненных иди абразивных сред, а также жидкостей, сильно меняющих свою вязкость при числах Рсйнольдса, меньших критических (переход ламинарного течения к турбулентному).
В настоящее время отечественным приборостроением разработаны и осваиваются турбинные расходомеры с безопорными датчиками, с устройствами автоматической коррекции показаний при изменении вязкости измеряемой среды, у которых два последних недостатка отсутствуют.
Влияние местных сопротивлений, закручивающих поток, в значительной мере устраняется, если перед турбинным датчиком установить специальные направляющие или сопловые аппараты, В этом случае для нормальной эксплуатации турбинных датчиков не требуется столь длинных прямых участков трубопровода как для других типов расходомеров.
Сравнительно редко применяют турбинные расходомеры для измерения расхода газов. Электромагнитные (индукционные) расходомеры
Электромагнитные расходомеры могут быть выполнены как с постоянными магнитами, так и с электромагнитами, питаемыми переменным током частотой f. Обе эти разновидности электромагнитных расходомеров имеют свои достоинства и недостатки, определяющие области их применения.
Существенным и основным недостатком электромагнитных расходомеров с постоянным магнитом, ограничивающим их применение для измерения слабопульсирующих потоков, является поляризация измерительных электродов, при которой изменяется сопротивление датчика, а следовательно, появляются существенные дополнительные погрешности. Поляризацию уменьшают, применяя электроды с платиновым или танталовым покрытием, а также угольные и каломелиевые электроды.
Электромагнитные расходомеры малоинерционны по сравнению с расходомерами других типов. Поэтому они незаменимы в тех процессах автоматического регулирования, где запаздывание играет существенную роль, или при измерении быстро меняющихся расходов.
Датчики электромагнитных расходомеров не имеют частей, выступающих внутрь трубопровода, сужений или изменений профиля. Благодаря этому гидравлические потери на датчике минимальны. Кроме того, датчик расходомера и технологический трубопровод можно чистить и стерилизовать без демонтажа. Отсутствие полых углублений исключает застаивание и осаждение измеряемого продукта.
На показания электромагнитных расходомеров не влияют взвешенные в жидкости частицы и пузырьки газа, изменение профиля распределения скоростей потока, а также физико-химические свойства измеряемой жидкости (вязкость, плотность, температура и т.п.), если они не изменяют ее электропроводность.
Датчики электромагнитных, расходомеров можно монтировать в любом положении на расстояниях, равных не менее 20 диаметров трубопровода после местных сопротивлений, нарушающих осесимметричное течение потока, и не менее 8 диаметров до местных сопротивлений.
Конструкция датчиков позволяет применять новейшие изоляционные, антикоррозийные и другие покрытия, что дает возможность измерять расход агрессивных и абразивных жидкостей.
Электромагнитные расходомеры применяют для измерения очень малых (3*10"9 м3/сек) расходов (например, для измерения расхода крови по кровеносным сосудам) и очень больших расходов (3 м /сек) жидкостей. Причем диапазон измерения датчика одного типоразмера достигает величины 10: 1, т.е. достаточно велик.
Электромагнитные расходомеры непригодны для измерения расходов газов, а также жидкостей с электропроводностью менее 10"3 - 10~5 сим/м (10~5 - 10" ом-1 см-1), например, легких нефтепродуктов, спиртов и т. п.
4. Ультразвуковые расходомеры
Предназначены для определения скоростей нестационарных потоков жидкостей и газов разработаны специальные ультразвуковые методы и соответствующая аппаратура. Определение скорости потока в данных системах производится по изменению параметров ультразвуковых колебаний.
Принцип действия ультразвуковых расходомеров может быть основан на измерении:
1) времени прохождения ультразвуковых колебаний по потоку и против него;
2) сдвига фаз между ультразвуковыми колебаниями, направляемыми по потоку и против него;
3) разности частот ультразвуковых колебаний, создаваемых автоколебательной схемой и
направляемых одновременно по потоку и против него;
4) величины сноса потоком луча ультразвуковых колебаний.
Принципиальная схема ультразвукового расходомера приведена на рисунке 4. Звуковые колебания высокой частоты (20 кГц и выше), создаваемые электроакустическим излучателем (вибратором), проходят через поток измеряемой среды и регистрируются приемником, отстоящим от излучателя на расстоянии. |
Рис.4 — Схема ультразвукового расходометра — излучатель (вибратор); — приемник; — скорость потока
Прибор регистрирует разность времени распространения акустической волны по течению и против течения. На основе этой разницы определяется скорость потока.
Погрешность измерения расхода существующими ультразвуковыми расходомерами составляет величину порядка 2 - 5 % от верхнего предела шкалы. Столь невысокая точность измерений объясняется: зависимостью показаний от профиля скоростей или числа Рейнольдса. Зависимость показаний ультразвуковых расходомеров от числа Рейнольдса объясняется тем, что они измеряют не среднюю скорость потока по сечению трубы, а среднюю скорость по линии ультразвукорого луча. Соотношение между этими скоростями является функцией числа Рейнольдса.
Кроме малой точности измерений, к недостаткам ультразвуковых расходомеров относят большую сложность их измерительной части и вредное влияние ультразвуковых колебаний на физико-химические свойства некоторых промышленных жидкостей и газов.
Основными достоинствами ультразвуковых расходомеров являются:
- высокая надежность датчиков (излучателей и приемников ультразвуковых колебаний),
представляющих собой круглые пластинки кварца или титанита бария, устанавливаемые снаружи
трубопровода или защищенные от непосредственного контакта с измеряемой средой металлическим
(пластмассовым) звукопроводом;
- отсутствие элементов, выступающих внутрь трубопровода, что дает те же положительные эффекты,
как и у электромагнитных расходомеров;
- высокое быстродействие, позволяющее измерять пульсирующие расходы с частотой пульсаций до 10
000гц,
- принципиальная возможность измерять расход, любых жидкостей и газов, в том числе и
неэлектропроводных, что выгодно отличает данные приборы от электромагнитных.
В общем можно отметить, что ультразвуковые расходомеры более приемлемы для измерения высоких расходов. При этом, чем меньше скорость потока по отношению к скорости распространения звука в контролируемой среде, тем, как правило, сложнее и точнее должна быть применяемая аппаратура.
Массовые расходомеры
Массовые расходомеры могут быть разделены на две группы. К расходомерам первой группы относятся такие устройства, в которых измеряется непосредственно массовый расход независимо от свойств и параметров вещества. Такие расходомеры универсальны и могут быть применены для измерения расхода любых веществ.
К расходомерам второй группы относятся устройства, которые по своему принципу действия не являются измерителями массового расхода, но благодаря применению специальных датчиков и корректирующих схем могут определять массовый расход. К таким устройствам, в первую очередь,, относятся различные скоростные расходомеры, снабженные датчиками плотности и соответствующими корректирующими схемами, а также ультразвуковые и некоторые тепловые расходомеры.
Рациональность применения того или иного типа массовых расходомеров определяется эксплуатационными требованиями. В тех случаях, когда необходимо измерять расходы весьма разнообразных веществ, наиболее рациональным является применение расходомеров первой группы.
Универсальные массовые расходомеры являются единственно пригодными устройствами для измерения многокомпонентных потоков, состоящих из двух (или более) несмешивающихся веществ (например, жидкие потоки с газовыми включениями). При наличии двух и более компонентов в контролируемом потоке, весовые соотношения, удельные веса и вязкости которых могут изменяться в широких пределах, удовлетворительный контроль может быть выполнен только с помощью универсальных массовых расходомеров. Это объясняется тем, что с помощью датчика плотности, корректирующего показания расходомера, не представляется возможным с удовлетворительной точностью проводить непрерывный контроль плотности многокомпонентного потока.
Ввиду того, что в целом ряде объектов приходится выполнять автоматический контроль именно таких многокомпонентных потоков, в настоящее время ощущается острая потребность в массовых расходомерных системах универсального применения.
Принцип действия универсальных расходомеров основан на том, что потоку измеряемого вещества сообщается дополнительное движение, чтобы создать в потоке инерционные эффекты, по которым судят о величине массового расхода. В связи с этим данные расходомеры называют ещё инерционными. В зависимости от того, какое именно дополнительное движение сообщается потоку (при помощи вращающегося или колеблющегося звена), на чувствительном элементе прибора возникает или усилие Кориолиса, или гироскопический, или инерционный момент.
Существуют инерционные расходомеры двух типов: расходомеры с вращающимся или колеблющимся участком трубопровода сложной конфигурации. К ним относятся гироскопические и кориолисовы расходомеры; турборасходомеры.
Массовые турборасходомеры получили широкое применение за рубежом и успешно осваиваются отечественной промышленностью из-за простоты конструкции и достаточно высокой точности измерения массового расхода.
Принципиальная схема массового турборасходомера одной из наиболее распространенной конструкции приведена на рис.5. Прибор работает следующим образом: ведущая турбинка 6, принудительно вращаемая с постоянной угловой скоростью двигателем 7, закручивает поток измеряемого вещества, создавая в нем инерционный момент, пропорциональный массовому расходу. Закрученный поток, проходя через ведомую турбинку 5, жестко связанную с упругим элементом 2. поворачивает ее па определённый угол. При постоянной угловой скорости вращения ведущей турбипки массовый расход характеризуется деформацией упругого элемента и углом поворота ведомой турбинки, который преобразуется в пропорциональный электрический сигнал.
2
Рис.5 — Схема массового турборасходометра
1 — корпус прибора; 2 •— упругое звено с чувствительным элементом; 3 — усилитель; 4 — регистратор (отсчетнос устройство); 5 — ведомая турбина; 6 — ведущая турбина; 7 — приводной электродвигатель
Погрешность измерения массового расхода турборасходомерами может быть доведена до ± (0.5 - 1)% от верхнего предела измерений. Повышение точности лимитируется трудностями поддержания постоянства числа оборотов ведущей турбинки, нестабильностью характеристик упругих элементов, воспринимающих действие инерционного момента, и изменением к. п. д. приводного двигателя при изменении нагрузки (расхода).
Кроме того, на показания турборасходомеров влияет изменение вязкости измеряемой среды, а их надежность ограничивается наличием изнашивающихся опор.
Типовые групповые замерные установки
В настоящее время на нефтяных промыслах широко применяются блочные автоматизированные групповые замерные установки (АГЗУ), предназначенные для измерения дебита нефти, газа и воды
нефтяных скважин; контроля за работой скважины и, при необходимости, автоматической ее блокировки.
Существуют различные типы АГЗУ, которые можно классифицировать следующим образом:
- по методам измерения: объемные («Спутник А», «Спутник Б», «Спутник AM», «БИУС» и др.);
весовые («Спутник В»); массовые («Спутник ГМ», «Спутник ГМН», «Спутник BMP», «АСМА-СП» и
др.);
- по устройствам переключения на замер: с многоходовым переключателем; с трехходовыми
клапанами;
- по режиму измерения: накопительный, импульсный с поочередным подключением на замер; и
с одновременным измерением дебита всех скважин;
- по числу измеряемых параметров: одно-, двух- и трехпараметровые;
- по способу монтажа: стационарные и передвижные.
В Западной Сибири наибольшее распространение получили установки типа «Спутник», некоторые из которых рассмотрены ниже.
Дата добавления: 2019-03-09; просмотров: 1049; Мы поможем в написании вашей работы! |
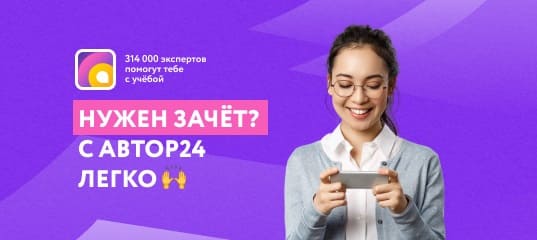
Мы поможем в написании ваших работ!