Расчет сопротивления экструзионной головки
Экструзионная головка – это съемный технологический инструмент, предназначенный для оформления экструдируемого расплава в погонажное изделие, конфигурация поперечного сечения которого определяется геометрией формующего канала (щели, фильеры).
Конструкции формующих головок характеризуются значительным разнообразием.
По направлению потока расплава головки могу быть прямоточными и угловыми. В последних происходит поворот расплава, и изделие выходит из головки под определенным углом к оси входного потока.
По конфигурации формующей щели различают головки плоскощелевые, кольцевые (трубные, рукавные), профильные.
По форме профиля – головки для изделий открытого типа (листы, плоские пленки, стержни, уголки, швеллера и др.), закрытого типа (рукава, трубы, шланги, трубчатые уплотнители), смешанного типа и специальные головки (сложные профили, армированные, комбинированные, гибридные изделия).
1 |
2 |
3 |
4 |
5 |
6 |
7 |
8 |
Рисунок 6 - Схема устройства экструзионной головки
По величине давления различают головки низкого (до 4 МПа), среднего (до 10 МПа) и высокого (более 10 МПа) давления.
При всем разнообразии конструкционного оформления в большинстве формующих головок можно выделить наличие общих элементов .
К ним относятся: корпус 1 с элементом присоединения к цилиндру экструдера (это может быть фланцевое, байонетное или резьбовое соединение); адаптер 2; фильтр-решетка 3;кольцевые зонные электронагреватели 7; регулировочное кольцо 5 (губка в плоскощелевых головках). В головках закрытого типа обязательно присутствует дорн 4 с дорнодержателем 6 и нередко система 5 для подачи воздуха внутрь изделия (труба, пленочный рукав, закрытый профиль).
|
|
Основной геометрической характеристикой формующей головки является ее общий коэффициент сопротивления Кг,определяемый как сумма коэффициентов сопротивления отдельных простых по геометрии участков k1, k2…ki с помощью уравнения:
(12)
где k1, k2…ki – частные коэффициенты сопротивления участков канала с простой геометрической формой, определяемые по формулам, приведенным в таблице
При расчете Кгголовку условно разбивают на участки, отличающиеся конфигурацией, и для каждого участка определяют частный коэффициент сопротивления. Применительно к прямоточной рукавной головке, изображенной на предыдущем рисунке этаоперация будет выглядеть следующим образом
Рисунок 7 - Схема разбиения на элементарные участки потока расплава в головке
|
|
Непрерывный поток разделяется на участки:
lа − участок адаптера: конический круглый канал с большим диаметромна входе; lф − участок фильтра; lр − участок решетки; l1кк − конический кольцевой канал с большим диаметромна выходе; l1цк − цилиндрический кольцевой канал; l2кк − конический кольцевой канал с большим диаметромна входе; l2цк − цилиндрический кольцевой формующий канал.
Обычно на пути течения расплава полимера на выходном конце шнека устанавливают фильтровальные элементы, чаще всего в виде пакета сеток из нержавеющей стали. Фильтрующие элементы устанавливаются непосредственно перед входом в головку и предназначаются для очистки расплава от различного рода твердых включений, неизбежно попадающих в материал на различных стадиях его производства и транспортировки, а также от не полностью проплавленных в канале червяка частиц материала, которые иногда появляются на выходе из этого канала при работе экструдера с максимальной производительностью на некоторых типах материалов (например, на высокомолекулярном полиэтилене высокой плотности). Обычно применяется набор сеток с различным числом отверстий на единицу площади (табл. 2), причем сетки с меньшим числом отверстий располагают дальше от конца шнека, чтобы избежать выдавливания их вместе с расплавом.
|
|
Таблица 4 - Характеристика фильтрующих сеток
Параметр | Тип сетки | ||
Крупная | Средняя | Мелкая | |
Диаметр проволоки, мм | 0,37 | 0,16 | 0,052 |
Размер ячеек, мм | 0,56 | 0,25 | 0,075 |
Число ячеек, шт/см2 | 144 | 576 | 6400 |
Поверхность в свету, % | 34 | 37 | 34 |
На современных экструдерах устанавливают сито-сменные фильтровальные устройства с общей площадью фильтрующего комплекта 500…2000 см2 и числом фильтровальных элементов n = 5…20.
Весь набор сеток поддерживается решеткой, устанавливаемой между цилиндром и головкой, служащей для спрямления потока расплава, выходящего с последнего витка шнека. Она представляет собой стальной диск толщиной примерно 1/5 диаметра цилиндра. В этом диске просверлены отверстия диаметром по 3…6 мм. На рис. 6 показаны решетки нескольких конструкций.
Рисунок 8 - Решетки и сетки различных типов
При производстве листов или пленок через плоскощелевую головку используется решетка с отверстиями в виде узких щелей (в центре рисунка), которые должны быть расположены параллельно плоскости щели головки. При расчете коэффициента сопротивления в головке сопротивления в решетке и фильтре также должны учитываться. Коэффициент сопротивления решетки, см3:
|
|
(13)
(14)
где z – число отверстий в решетке;
do – диаметр отверстий, см;
δр − толщина решетки, см.
Коэффициент сопротивления фильтра, см3
(15)
(16)
где n – число фильтровальных элементов;
F – площадь фильтровального элемента, см2;
δф – толщина фильтрующих элементов, см;
Расчетные формулы и схемы для расчета коэффициента сопротивления и скорости сдвига простейших каналов приведены в таблице.
Таблица 5 - Расчетные формулы и схемы для расчета коэффициента сопротивления и скорости сдвига простейших каналов*
Тип канала | Расчетная схема | Коэффициент сопротивления K, см3 | Скорость сдвига • расплава, γ , с-1 | Номер формулы |
Цилиндрический круглый | ![]() |
![]() | 32Q/πd3 | (1) |
Конический круглый | ![]() |
![]() | ![]() | (2) |
Кольцевой цилиндрический | ![]() | ![]() | ![]() | (3) |
Конический кольцевой | ![]() | ![]() ![]() | ![]() | (4) |
Прямоугольный щелевой | ![]() |
![]() | ![]() | (5) |
Клиновидный щелевой | ![]() |
![]() | ![]() | (6) |
Произвольное поперечное сечение | ![]() |
![]() | ![]() | (7) |
* L – длина канала; Q – производительность, см3/с; все размеры в см.
Зная скорость сдвига расплава и температуру переработки, эффективную вязкость можно определить по логарифмической зависимости эффективной вязкости от градиента скорости сдвига
Таблица 6 - Коэффициенты в уравнении зависимости эффективной вязкости расплава от скорости сдвига для различных полимеров
Полимер | Температура, оС | А | В |
ПЭВП | 150 | 0,556 | 4,028 |
170 | 0,520 | 3,848 | |
190 | 0,503 | 3,732 | |
210 | 0,489 | 3,638 | |
Полипропилен | 190 | 0,751 | 4,591 |
210 | 0,742 | 4,483 | |
230 | 0,736 | 4,415 | |
250 | 0,711 | 4,284 | |
Полиамид | 160 | 0,301 | 3,619 |
180 | 0,007 | 3,375 | |
Полистирол | 180 | 0,774 | 4,697 |
200 | 0,709 | 4,455 | |
220 | 0,684 | 4,270 | |
240 | 0,672 | 4,167 |
Температуру расплава полимеров в различных участках экструдера можно найти по таблице
Таблица 7 - Режимы переработки полимеров экструзией
Материал | Изделие | Температура, оС | Давление (бар) | |||||
Зона 1 | Зона 2 | Зона 3 | Зона 4 | Головка | Фильера | |||
АБС | Трубы, листы, профили | 175 | 195 | 205 | 205 | 200 | 210 | 150…200 |
170 | 175 | 180 | 180 | 180 | 190 | 200…250 | ||
ПЭНП (ПЭВД) | Трубы, пустотелые корпуса | 125 | 125 | 130 | 130 | 130 | 135 | 100…150 |
Пленка, получаемая | 125 | 135 | 135 | 145 | 145 | 145 | 100…170 | |
Экструзией с раздувом, Плоская пленка | 155 | 165 | 180 | 195 | 195 | 200 | 150…250 | |
Изоляция проводов | 160 | 210 | 230 | 240 | 230 | 235 | 250…350 | |
Мононити | 160 | 200 | 220 | 240 | 230 | 240 | 250…350 | |
ПЭВП (ПЭНД) | Трубы, пустотелые корпуса | 140 | 160 | 165 | 165 | 165 | 170 | 100…170 |
Листы | 220 | 190 | 170 | 165 | 165 | 170 | 100…170 | |
Пленка, получаемая экструзией с раздувом | 140 | 160 | 170 | 180 | 180 | 185 | 150…200 | |
Изоляция проводов | 200 | 210 | 240 | 250 | 240 | 245 | 250…400 | |
Мононити | 200 | 210 | 240 | 250 | 240 | 250 | 250…400 | |
Полипропилен | Трубы | 180 | 200 | 215 | 225 | 225 | 235 | 150…200 |
Плоские пленки | 190 | 220 | 245 | 265 | 265 | 265 | 200…300 | |
Мононити | 200 | 230 | 250 | 270 | 270 | 270 | 300…400 | |
ПВХ пластикат (порошок) | Гранулят | 140 | 150 | 160 | 160 | 155 | 155 | 50…100 |
Оплетенная проволока | 210 | 185 | 175 | 155 | 180 | 190 | 150…250 | |
ПВХ пластикат (гранулят) | Шланги, профили | 180 | 170 | 160 | 150 | 160 | 160 | 60…120 |
Оплетенная проволока | 200 | 189 | 170 | 150 | 180 | 190 | 150…250 | |
ПВХ винипласт (порошок) | Гранулят | 185 | 175 | 165 | 165 | 160 | 160 | 75…150 |
Трубы, профили | 190 | 180 | 170 | 165 | 170 | 180 | 100…200 | |
ПВХ винипласт (гранулят) | Трубы, профили, плиты | 155 | 165 | 175 | 190 | 180 | 185 | 100…200 |
Полиамид | Шланги | 275 | 245 | 235 | 225 | 225 | 225 | 150…250 |
Оплетенная проволока | 260 | 270 | 280 | 290 | 290 | 300 | 250…300 | |
Нити, мононити | 265 | 275 | 290 | 300 | 300 | 300 | 250…350 | |
ПММА | Плиты | 160 | 165 | 170 | 170 | 170 | 180 | 50…100 |
ПФ | Трубы, профили | 170 | 190 | 205 | 200 | 200 | 200 | 50…100 |
Таблица 8 - Сводная таблица расчетов коэффициентов сопротивления головки и потерь давления
№ участка | Параметр | Вязкость, η, расчетное значение, Па·с | Потери давления, ∆P, расчетное значение, Па | ||
Расчетная формула | Расчетное значение | ||||
1 | Скорость сдвига, с-1 | ![]() | 145,5594 | ![]() | ![]() |
Коэффициент cопротивл., см3 | ![]() | 0,08015 | 296,5287 | 82214,36 | |
2 | Скорость сдвига, с-1 | ![]() | 365,023 | ![]() | ![]() |
Коэффициент cопротивл., см3 | ![]() | 0,019025 | 191,0781 | 223193,3 | |
3 | Скорость сдвига, с-1 | 32Q/πd3 | 0,905703 | ![]() | ![]() |
Коэффициент cопротивл., см3 | ![]() | 12,26793 | 3361,714 | 6089,429 | |
4 | Скорость сдвига, с-1 | ![]() | 10,81562 | ![]() | ![]() |
Коэффициент cопротивл., см3 | ![]() | 0,03151 | 1027,362 | 724537,2 | |
5 | Скорость сдвига, с-1 | 32Q/πd3 | 463,7199 | ![]() | ![]() |
Коэффициент cопротивл., см3 | ![]() | 0,002995 | 170,4236 | 1264461 | |
| Суммарный коэффициент сопротивления, см3 | Суммарная потеря давления в экструзионной головке, Па | |||
| | ||||
96,85942
| 2300495
|
Дата добавления: 2019-02-22; просмотров: 1296; Мы поможем в написании вашей работы! |
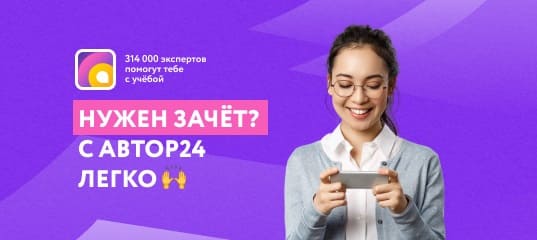
Мы поможем в написании ваших работ!