Цемент диірмендерін аспирациялау
Аспирациялық сорылатын 1 м3 ауамен 50...200 г цемент тартылып әкетіледі (өнімділіктің 2...6 %).
Аспирациялық ауаны тазалау үшін электр және жең түріндегі сүзгілер (фильтр) орнатылады, олар ауаны 98...99 % тазалауға мүмкіндік береді. Жең түріндегі сүзгілердің гидравликалық кедергісі электрсүзгілерге қарағанда жоғары (600...2000 Па), бұл - олардың кемшілігі, бірақ жең түріндегі сүзгілер аз орын алады, орнатқанда және пайдаланғанда арзанырақ болады.
Жасанды маталарды пайдалану олардың пайдалану температурасынан 150 0С дейін көтереді, қажалуға төзімділігін арттырады және жең түріндегі фильтрлерді электрсүзгілермен таласа алатын етті. Электрсүзгілер энергия шығыны бойынша үнемдірек, бірақ аспирациялық ауаның жоғары температурасы мен ылғалдылығының аздығының нәтижесінде ауаның температурасы мен ылғалдылығын реттеп отыру керек. Оған қарамастан суды диірменге себелеп үрлеу күрделі мәселелерді біршама шешуге мүмкіндік береді. Электрсүзгі жақсы жұмыс істеп тұруы үшін ауаның 1 м3-да 50 г артық тозаң болмауы қажет. Тозаңның концентрациясын төмендету үшін электр немесе жеңді фильтрлердің алдына циклон немесе желбезекті іріктегіш орнатылады.
Диірмендерден сорылып алынатын ауаның тозаңдылығын төмендету үшін тозаң тұндыратын шахталардың алдына, қиындысы газ жылдамдығының 1...1,2 м/мин үлкен болмауын қамтамасыз ететін қондырғы орнатылады. Бұл кезде аспирациялық ауадағы тозаңның концентрациясы азайып, 30 г/м3 болады. Аспирациялық шахтаның биіктігі 5...10 м жетеді.
|
|
5.12 Клинкер және цемент қоймалары
Клинкер қоймалары. Халықаралық AUMUND тобы цемент клинкерін сақтауға әртүрлі қоймаларды жасаған:
- дөңгелек орталық тіреусіз; сыйымдылығы 3500…156000 т;
- цилиндрлі силостар, сыйымдылығы 5000…60000 т;
- дөңгелек орталық тіреумен, сыйымдылығы 51000…190000 т;
- тереңдетілген қоймалар, сыйымдылығы 45000…201000 т;
(клинкердің көлемдік салмағы γ=1500 кг/м3).
Дөңгелек орталық тіреусіз қоймаларын темірбетоннан, цилиндр тәріздес диаметрін 40…80 м, биіктігін 10…25 м қылып жасайды, төбесі конус тәрізді (5.23-сурет). Жоғары жағында тасымалдағыштар және сүзгіштер орналастырылады. Клинкерді түсіру 2…4 каналмен жасалады. Қойманы клинкермен толтырғанда ол конус тәрізді болып фракцияларға бөлінеді. Цемент диірмендері жақсы жұмыс істеу үшін өлшемі бірқалыпты материал берілу керек. Сол үшін клинкер бөлшектерінің өлшемдері аралас болу үшін оны ауыспалы бункерлердің әр түрлі тесіктерінен түсіру керек. Дөңгелек клинкер қоймаларының сипаттамасы 5.5-кестеде келтірілген.
|
|
Бетонды және металды цилиндрлі қоймалар. Бұл қоймалардың табанының ауданы төмен болғандықтан толтыру дәрежесі жоғары болады – 75 % жуық. Қойманы арнайы техникасыз тазалап босатуға болады. Клинкердің барлығы өз салмағымен түсіп кетеді. Цилиндрлі қоймалардың диаметрі 15…36 м, цилиндр тәрізді бөлігінің биіктігі 18…36 м, босатылу дәрежесі 73…78 % (5.24-сурет).
![]() |
5.23- сурет. Дөңгелек клинкер қоймалары 2х75000 т |
Орталық тіреуі бар дөңгелек қоймалардың диаметрі үлкен ал биіктігі аласа қылып салынады. Орталық тіреудің үстінде тасымалдағыш транспортерлардың жетегі және сүзгіштер орналасады. Клинкерді төгіп алу үшін 1…3 канал жасалады. Төгіп алу дәрежесі 40…60 % жетеді. Қалған клинкерді техникамен түсіреді. Қоймалардың диаметрі 70…110 м, сыйымдылғы 50 ден 190 мың тоннаға дейін, биіктігі 26…40 м. Бұл қоймалардың шатырының ауданы үлкен болғасын клинкер жақсы салқындайды.
|
|
Тереңдетілген клинкер қоймалары. Созылған және дөңгелек клинкер қоймалардың жер астындағы бөлігі құйғыш (воронка) тәрізді болады. Сол үшін қойманың сыйымдылығы және төгіп алу көрсеткіші (разгружаемость) жоғарылайды. Жер астындағы бөлігінің бұрышы 40…450 болады. Қойманы құрғанда төменгі жақтан жарылыс және тесіктер арқылы су келу мүмкіншілігін еске алу керек. Дренаж арқылы су келу мүмкіншілігін мүлде жою жақсы. Қойманың төбесі болат каркас ретінде жасалады.
5.5 -кесте. Дөңгелек орталық тіреуі жоқ клинкер қоймаларының сипаттамасы
Қойманың өлшемдері, м | Қойманың сыйымдылығы | Босатылу дәрежесі, % |
| |||
D | Н | h | тонна | м3 | ||
40 | 15 20 | 14,1 14,1 | 34900 44300 | 23250 29500 | 80 84 | |
45 | 15 20 25 | 15,8 15,8 15,8 | 45500 57400 69300 | 30300 38800 46200 | 76 80 84 | |
50 | 15 20 25 | 18,7 18,7 18,7 | 57800 72500 87200 | 38500 48300 58200 | 81 84 87 | |
55 | 15 20 25 | 20,5 20,5 20,5 | 71900 89700 108000 | 47900 59800 71700 | 79 82 85 | |
60 | 15 20 25 | 22,1 22,1 22,1 | 88000 109000 130000 | 58700 72800 86900 | 81 84 87 | |
65 | 15 20 25 | 25,0 25,0 25,0 | 106000 131000 156000 | 70700 87300 104000 | 83 86 89 |
|
|
![]() |
а) Дөңгелек орталық тіреусіз қоймалар |
![]() |
б) Бетонды және металды цилиндрлі қоймалар |
![]() |
в) Орталық тіреуі бар дөңгелек қойма |
![]() |
г) «Кротпен» жабдықталған дөңгелек қойма |
![]() |
д) Тереңдетілген клинкер қоймасы |
5.24-сурет. Замануи клинкер қоймалары |
«Кротпен» жабдықталған дөңгелек қоймалар. Бұл қоймаларда клинкерді толық төгіп алу үшін арнайы автоматтандырылған «крот» деген қондырғы пайдаланады. «Крот» жылжымалы конструкция, ол орталық тіреуді айналып жүреді. Арнайы тырнағыш шынжырлар (скребковая цепь) өз салмағының күшімен бункерге түсе алмайтын клинкерді ортадағы орналасқан бункерге тасымалдайды. Тырнағыш шынжыр гидравликалық жүйемен жұмыс істейді, қозғалу автоматикалы программалы контроллермен басқарылады. «Кроттың» артықшылығы ол майда, орташа және ірі клинкердің бөлшектерін араластырып береді, цемент диірменіне біркелкі араласпа беріледі.
Клинкерді ортада төменде орналасқан үш-төрт төгіп алатын құрылғымен түсіріп алады.
Бұл қоймалардың сыйымдылығы 45000…201000 т, диаметрі 40…65 м, жалпы биіктігі 43…64 м, толтырылу дәрежесі 95%. Жоғарыда айтылған заманауи клинкер қоймаларының сызбасы 5.24-суретте келтірілген.
Қоймадағы клинкерді төгіп алатын құрылғылар. Клинкерді төгіп алу үшін AUMUND фирмасы арнайы құрылғыларды пайдаланады. Бұл жерде шаң ұстағыш қондырғылар қажет емес. Қондырғы клинкерді тасымалдап алып кететін пластиналы тасымалдағышпен қосылып пайдаланады. Клинкер тасымалдағышқа жоғарыдан төгілмейді, сол үшін шаң пайда болмайды. Құрылғының өнімділігі клинкер төгілетін тесіктен және тасымалдағыштың қозғалу жылдамдығына байланысты. Қысқа буынды пластиналы тасымалдағыштар кең тараған. Олар горизонтальды одан кейін 280 көтерілу бұрышымен жұмыс істейді. Комплекс оптимальды жобаланса цемент диірмендердің бункерлеріне тікелей клинкерді беруге болады. Тасымалдағыштардың өнімділігін қозғалу жылдамдығымен реттейді. (5.25-сурет).
| ||
Тасымалдау бағыты | Тасымалдау бағыты | |
5.25-сурет. Қоймалардағы клинкерді төгіп алу құрылғылары |
Шаң пайда болмас үшін клинкер төгетін жерде сиретілу (разряжение) жасау керек. Ол үшін сүзгіштер орнатылады (5.26-сурет). Қажетті ауаның мөлшері қойманың диаметріне, клинкердің температурасына байланысты. Ауаға қажеттілігі 12000 м3/сағ (кіші цилиндрлі қоймалар) 60000 м3/сағ дейін өзгереді (үлкен қоймалар).
![]() | ![]() |
Сүзгіш және компрессордың орналасуы | Қойманың төбесі және жоғары жағының құрылысы |
5.26–сурет. Шаңсүзгіштерді орналастыру |
Клинкерді тасымалдауға AUMUND фирмасысының KZB типті ұялы тасымалдағыштарды пайдаланады. Олардың жұмысы сенімді, істеу мерзімі ұзақ, тасымалдау тиімді. Мысалы KZB-250 типті тасымалдағыш сағатына 1000 т дейін клинкерді 60 м биіктікке 28о бұрышпен бере алады. Ұялардың ені 400...3000 мм.
Ұялы KZB-250-Q типті тасымалдағыш сағатына 750 т дейін клинкерді 60 м биіктікке 40о бұрышпен бере алады. Ковшты ВZB тасымалдағышты тар жерде пайдалануға болады. Ол клинкерді 60 м биіктікке 60о бұрышпен бере алады.
Ленталы ковшты BWG типті элеватор цемент, шикізат ұнын тасымалдауға арналған. Ол автоматты тартатын механизммен жабдықталған. Бұл элеватор шикізат ұнын 140 м биіктікке көтере алады, өнімділігі 1500 т/сағ дейін, материалдың температурасы 130 оС дейін.
Цемент сақтайтын силостар. Диірмендерден кейін цементті буферлі қойма ретінде силостарға жібереді, ол жерден дайын өнім ретінде тұтынушыларға беріледі. Цементтердің силостарда сақталу кезінде физико – механикалық сипаттамасы мен маркасын анықтайды. Зауыт “маркасына кепілдеме беретін” цемент шығарғанда, зауыттың 10...15 тәуліктік өнімнің сақталуын қамтамасыз ететін силостардың сыйымдылығы жеткілікті. Сақтау процесінде байланыспаған СаО сөнеді, бұл цементтің қасиеттерін жақсартады. Сақтау сол сияқты ұстасу мерзімдерінің едәуір созылуын қамтамасыз етеді.
Диірмендерде цемент 80...100 0С дейін қызады, ал олардың силостарда сууы өте жай жүреді. Сондықтан цемент диірмендеріне, мұздатылуы ағын сумен жүргізілетін диаметрі 2 м және биіктігі 7 м дейін тік мұздатқыштар (кей кезде бір диірменге екеу) орнатылады. Судың үлестік шығыны цементтің бір тоннасына 0,6...0,7 м3/т.
Цемент силостарға ескі зауыттарда пневматикалық тасымалдығыштармен құбыр арқылы тасымалданады, олар шаң болдырмайды, қарапайым және сенімді. Цемент азғантай қашықтыққа тасымалдағанда жазықтықта пневмоқұбырлар (10...50 м) қолданылады. Пневмотасымалдағыштың камералы қоректендіргіштері әр диірменнің астына орнатылады, бұл диірменнің өнімін есептеуге мүмкіндік береді. Қоректендіргіштерден цемент құбырымен өтіп силостың үстіндегі тұндырғыш циклондарға жіберіледі, ол жерден пневмоқұбырлар арқылы силостарға таратылады.
Сонғы онжылдықтарда цементті элеватор, шнек, ленталы тасымалдағыштармен тасыйтын болды. Себебі электр энергия шығыны төмен. Цементті элеватормен тасымалдауға жұмсалатын энергияны 1-деп алсақ, онда пневокамералы насостармен жумсалатын энергия 2 тең, ал пневмовинтті насостарға жұмсалатын 4 тең.
Силостар дегеніміз колонналарға орналастырылған темірбетон банкалардан тұрады. Диаметрі 10...18 м және биіктігі Н=25...30 м, сыйымдылығы 2500...10000 т цемент. Диаметрі Д=8...12 м силостар блокпен 4...8 силостан екі қатар етіп, ал үлкен диаметрлі силостар 3...4 силостан 1 қатар етіп блоктармен орналастырады. Силостарды екі қатар етіп орналастырғанда цементті сақтау кей кезде қатар тұрған төрт силостың ортасындағы кеңістікті - «жұлдызшаны» пайдаланады. Силостардан цементті жанындағы саңылаулардан (темір жол жолы колонналардың қасынан өтеді) немесе түбіндегі саңылаулардан (теміржол жолы колонналардың ортасынан өтеді) жүк түсіргіш орнату арқылы түсіреді. Егер цементті жанынан түсіретін болса, онда симметриялық емес ауырлық және иілу күші пайда болады да, силос қабырғаларының формасы өзгереді. Сондықтан жүктің 2/3-сін үлкен диаметрлі орталық саңылаудан түсірген жөн. Цементті автоцемент тасымалдағыштарға тиеу үшін бөлек шанақтар салынады, бірақ цементті машинаға тура силостан тиеуді қамтамасыз ететін жүйелер бар.
Силостардың түбі керамика, бетон немесе металдан жасалған кеуек плиталармен қаланады (түбінің ауданының 15...20 %).
Плиталардың астына сусыздандырылған және майынан тазартылған тығыздалған ауа беріледі. Плиталардың 1 м2 - на 0,25 м3/мин. Тығыз ауа арнайы матамен қапталған, тесіктері бар құбырлар арқылы да енгізіледі. Тығыз ауа цементті қопсытып, оны түбіндегі, не жанындағы пневмотүсіргіштер немесе силостарға қабырғалары арқылы енгізілген ауамен тасымалдағыш ауа арқылы ағып түсуге қабілетті етеді. Бір вагон 5...7 минутта толады.
5.13 Цемент өндірісінде шаңсыздандыру
Цемент өндірісінде технологиялық процесте шаң бөлінеді. Ең көп мөлшердегі шаң айналмалы пештің қалдық газдарымен бөлінеді. Сонымен қосылып шаң шикізаттарды, көмірді, клинкерді ұсақтағанда, ұнтақтап кептіргенде, клинкерді салқындатқанда, көмірді, шикізатты, клинкерді, шикізат ұнын, цементті тасымалдағанда, тиегенде, қаптағанда бөлінеді. Шаң пайда болғанда ол материалдың, отынның, өнімнің жоғалуына алып келеді, санитарлық жағдайды нашарлатады, қоршаған ортаны ластайды, айналатын бөлшектер мен механизмдердің жұмыс істеу мерзімін төмендетеді.
Заманауи цемент зауыттарында барлық технологиялық бөлімдерде шаң тазалағыш қондырғылар орналастырады, олар газдағы, ауадағы шаңның мөлшерін төмендетіп жеткілікті концентрациясына апарады.
Атмосфераға тасталатын тазаланған ауа мен газдардың құрамындағы шаңның концентрациясы 80 мг/м3 аспауы керек. Еврозона мемлекеттерінде шаңның концентрациясы 30 мг/м3 аспауы керек. Цемент зауыт төңірегіндегі елді мекендерде ауаның шаңдығы 0,5 мг/м3 кем болуы қажет.
Шаңсыздандыратын құрылғылар екі топқа бөлінеді:
- механикалық шаң ұстағыштар;
- электрлі шаң ұстағыштар.
Механикалық шаң ұстағыштардың жұмыс істеу принциптері келесі:
- шаң өзінің салмағымен шөгетіндер (шаң шөктіргіш камера);
- шаң ортадан тепкіш күштің әсерімен шөгетіндер (циклондар, батареялы циклондар);
- шаң матада фильтрленетіндер (жеңді сүзгілер);
- шаңды бүркілген сумен ұстайтындар (скрубберлер);
Электр сүзгіштерге шаңды электродтарға шөктіріп газды тазалайды.
Шаң ұстағыштардың келесі негізгі көрсеткіштері болады:
- тазалау дәрежесі, ұсталған шаңның газды ағындағы толық шаңның салмағына қатынасы;
- сүзгіштің гидравликалық кедергісі, мм.су бағ.;
- 1000 м3 газға электр энергияның үлестік шығыны.
Сүзгіштің тиімділігі келесі формуламен анықталады:
(5.13)
Мұндағы: η – тиімділік, %
r – тазаланған газдағы шаңның салмағы, мг/нм3;
R–тазаланбаған газдағы шаңның салмағы (концентрациясы), мг/нм3.
Шаң шөктіргіш камералар ірі дисперсті шаңның бөлшектерін ғана шөктіре алады. Майда бөлшектерді ұстау үшін ұзақ уақыт керек. Шаң шөктіргіштердің артықшылықтары:
- құрылысы қарапайым;
- гидравликалық кедергісі төмен (2...10 мм.су бағ.);
Кемшіліктері:
- тиімділігі төмен (15 % дейін);
- жүктемесі төмен 150...350 м3/сағ 1 м2 қимасына.
Шаң шөктіргіштің тиімділігін арттыру үшін онда қозғалатын газды ағынның бағытын өзгертеді (5.27-сурет). Шаң шөктіргіш камераларда газды ағындағы шаңның ірі бөлшектері шөктіріледі. Мысалы, айналмалы пештің жоғарғы салқын жағы шаңды камераға кіріп түрады. Одан кейін газды ағын басқа сүзгіштерде жоғары дәрежеге дейін тазаланады.
Циклондар, батарейлі циклондарда шаңды бөлшектер ортаға тепкіш күш арқылы сепарацияланады. Циклондар өлшемі 5 мкм жоғары бөлшектерді сүзе алады, газды ағынның температурасы 400 °С дейін.
Циклондардың артықшылықтары:
- құрылысы қарапайым;
- жұмысы сенімді;
- капиталдық және эксплуатациялық шығындары төмен.
| ![]() | |
5.28–сурет. Циклонның схемасы: 1-шаң жиналғыш; 3-циклонның конус тәрізді бөлігі; 4-шаңды газ кіретін түтік; 5-тазаланған газ шығатын түтік | ||
5.27-сурет. Шаң шөктіргіш камералар |
Шаңды газ циклонның ішінде спираль тәрізді жоғарыдан төменге қарай қозғалады. Шаңның бөлшектері ортаға тепкіш күш арқылы циклонның қабырғасына тасталады. Циклонның конус тәрізді төменгі бөлігінде газдың спиралінің диаметрі кішірейеді. Бір кезде тазаланған газдың бағыты өзгеріп ол жоғары қарай қозғалып түтін шығаратын түтіктен атмосфераға шығып кетеді. Шаңның бөлшектері циклонның қабырғасымен төменге түсіп шаң жинағышқа келеді. Циклондарда шаңның тазалау дәрежесі 90 % жетеді (5.28-сурет).
Батарейлі циклондарда шаңды газ спираль тәрізді айналып қозғалу үшін винтті күрекшелер орналастырылады. Ал циклондарда газ тангенциалды беріледі. Циклондар шаңды ірі және орташа тазалауға арналған. Циклондар өнімділігі жоғары және тиімділігі жоғары болып бөлінеді. Біріншілері диаметрі үлкен және үлкен көлемдегі ауаны тазалайды. Екіншілерінің диаметрі кіші (560...600 мм). Бұларды топтап ауамен параллельді орналастырады. Циклондар ластанған газдарды алғашқы тазалау сатысына орналасады.
Жеңді сүзгіштер–жоғары тиімді аппараттар. Тазалау дәрежесі 99 % оданда жоғары, шаңдалған газдың температурасы 170...260 °С болуы мүмкін.
Сүзгіштің формасы төртбұрышты немесе дөңгелек болады. Корпустың ішінде диаметрі 100...350 мм, биіктігі 0,5...10 м жеңдер ілінеді. Ауаның немесе газдың тазалануы осы жеңдерден фильтрация кезінде жүреді. Фильтрациялайтын бетте шаңның қабаты жиналған соң оны регенерация жасайды.
Шаңданған ауа кіретін түтіктен камераға келеді. Мұнда сүзгіш жеңдер орналасқан. Шаң жеңнің бетінде ұсталып қалады. Тазаланған ауа жеңнің жоғарғы ашық жағынан тазаланған газдың камерасына келіп атмосфераға тасталады (5.29-сурет).
Сүзгіш жеңдердің регенерациясы тапсырыс цикл бойынша бір жақты импульсты ауамен үрлеу арқылы жасалады. Қысылған ауа жоғарыдан үрлеу коллекторынан беріледі. Импульс ұзақтығы 1,1...1,2 сек. Ауаның қысымы 0,3...0,6 МПа. Қысылған ауа кептіріліп тазаланған болуы керек.
![]() | 5.29-сурет. Жеңді шаң сүзгіш: 1-тірегіш рама; 2-бункер; 3- түсіретін шнек; 4-қозғалтқыш; 5-қарайтын люк; 6- сүзгіш жең; 7- регенерациялайтын торап (узел); 8-сервисті люк |
Жеңді сүзгіштерде лавсандар (130 °С), RTFE (260 °C), полиамид (240 °С), полиэстер (150 °С), m-арамид (200 °С) пайдаланады.
Электрсүзгіштер технологиялық газдар мен аспирациялық ауаны жоғары эффективтік тазалайды. Олардың өнімділігі жүзден миллион м3/сағ дейін. Газдарды тазалау дәрежесі 99,95 % дейін. Гидравликалық кедергісі төмен – 0,2 Па, өлшемі 0,01 мкм дейін бөлшектерді сүзе алады. Электросүзгішке жоғары кернеудегі 80 кВ, 110 кВ және 150 кВ тоқ беріледі.
Аспирациялық ауа (газ) екі электрод арасындағы электрлі далада (поле) қозғалғанда ионданалады (плюс және минус зарядталған иондар пайда болады). Майда шаңның бөлшектері қарама-қарсы зарядты электродтарға қозғалады. Сүзгіштегі сымға (коронирлейтін электрод) тұрақты тоқтың минусы беріледі (5.30-сурет).
![]() | 5.30-сурет. Электр сүзгіштегі коронирлейтін электродтары |
Жоғары вольтты трансформатор Тірегіш изолятор камерасы Сілкігіш жуйе: қозғалтқыш, рама, балғашалар Коронирлейтін электродтардың рамасы Кіретін газоход Газ тарататын тор Шөктіргіш электродтар Корпус Жылуизоляторы Қарайтын люк Тірегіш рама | ![]() |
5.31-сурет. Электр сүзгіштің құрылымы |
Шөктіргіш электродқа (пластина) плюс беріліп заземление жасайы. Шаңның ионизирленген бөлшектері электродтарда шөгеді. Арнайы жүйе электродтарды белгілі уақытта шаңнан қағып тұрады.
Электр сүзгіштегі сиретілу 400 мм.су бағ. жетуі мүмкін. Газдарды сүзгіштегі қозғалу жылдамдығы 1,0...1,5 м/сек. осы жылдамдық газдың сүзгіштің ішінде болатын уақытын жеткілікті қылады. Электр сүзгіштің құрылымы 5.31-суретте келтірілген.
5.14 Цементті тұтынушыларға тиеп жіберу
Жең тәріздес резина аққыштардың көмегімен цемент вагон цементтасығыштар - хопер мен автоцементтасығыштарға тиеледі. Цементтің көп бөлігі тұтынушыларға арнайы теміржол вагондарына немесе автотасымалдағыштарға тиеліп және 10 % шамасы 180 0С дейін қызуға шыдайтын және су өткізбейтін крафт қағаздың бірнеше қабатынан жасалған қапшықтарға салынып жіберіледі. Қапшыққа 50 кг сияды. Семей цемент зауытында 50 кг қап жасайтын өндіріс бар. Онда цементті өздерінің жасаған қаптарына тиейді. Бірнеше зауыттарда цементті 1…2 тонналық Big-Beg қаптарына тиейді.
Қапшыққа салу тозаңданып шашылуды азайтады және цементті ауа – райының әсерлерінен сақтайды, бірақ цементті қымбаттатады.
Цементті қапшықтарға 2 және 4 шүмекті тиегіш машиналармен тиейді, өнімділігі 25...40 т/сағ. Шымкент және басқа зауыттарда өнімділігі 125 т/сағ 14 шүмекті карусельді машиналарды пайдаланады.
Цемент карусельді тиегіш машинаның (5.32-сурет) бункеріне немесе тік қабырғалармен бөлінген ұяшықтарға беріледі.
Ұяшықтар цемент қозғалысына перпендикуляр бағытта вибрацияланады. Сол кезде цементтен ауа бөлініп шығады. Цементтің тығыздалуы қаптарды тығыз толтыруға мүмкіндік береді, бұл қаптардың арту және тасымалдау кезінде жыртылып кетуін болдырмайды. Тиегіш машинаға берер алдында цемент бөтен заттарды бөлетін шнекте еленеді. Тиегіш машинадан цемент артылған қаптар тасымалдағышпен арту платформасына тарату тасмалдағышына қарай жіберіледі. Қаптарды вагондарға тіркеу үшін, көлбеу бұрышын тігінен өзгерте алатын, айналатын жолақ түріндегі тіркегіш басы бар, қысқа тасымалдағыштарды пайдаланады. Артылған цементті вагон немесе автомобиль таразысының көмегімен өлшеу жүргізіледі. Кей кезде силостардың астына тензометрлік таразы қондырғылары орналастырылады.
Шетелдерде механикаландырылған тарату қондырғылары - цемент элеваторлары ірі цемент тұтыну орындарына орнатылған.
Қондырғылар силостардан және темір жолмен немесе су жолымен келіп түсетін цементті тиейтін және түсіретін жабдықтардан тұрады. Мұндай элеватор цементті су жолымен тасымалдағанда өте тиімді. Цементті мұндай элеваторлардан тұтынушыларға жеткізу автоцемент тасымалдағышпен жүргізіледі.
![]() | 5.32-сурет. Цемент тиегіш карусельді машина |
Құрамында силостармен және клинкерді ұнтақтау цехы болатын ұнтақтау қондырғылары салынуда. Шлакопортландцемент шығарғанда ұнтақтау қондырғыларын металлургия зауыттарында орналастырған жөн.
Көптеген цемент зауыттарында ірі өнім тұтынушылары, әдетте, цемент зауытымен қатар орналасады. Бұлар асбестцемент бұйымдарын өндіру, темірбетон конструкциясы, үй құрылысы комбинаттары. Бұндай қатар орналасқан өндірістерге цемент пневмотранспорт көмегімен құбырлар арқылы жеткізіледі.
5.15 Цемент өндірісіндегі бақылау жұмыстары
Қазіргі заманғы цемент зауыттарында сапалы цемент алу үшін барлық технологиялық талаптар мен өндірістік циклдің ережелері мен жүргізілу жағдайларын қатаң қадағалап отыру керек. Ең маңыздысы барлық өндірісті бақылауға алу. Ол үшін төмендегідей жұмыстар жүргізіледі;
- келіп түскен шикізаттың сапасының және қасиеттерінің техникалық жағдайлар мен нормалар талабына сай болуы;
- өндірістің барлық сатыларында материалдар мен жартылай фабрикаттардың қасиетін анықтап, олардың қасиеті сапалы өнім алуға болу және болмауын көрсетіп отыру;
- құралдардың, механизмдердің және қондырғылардың жұмыс режимін тексеріп отыру; олардың жұмысын, материалдардың сапалы өңделуін қамтамасыз етуі қажет;
- алынған цементтің қасиетін, оның стандарт талаптарын сай екенін тексеру.
Бақылауды өндірістің барлық сатыларында жүргізу керек. Ол үшін алдыңғы қатарлы әдістер мен құралдарды қолданады, олар бақылаудың дәлдігін қамтамасыз етеді, әрі бақылау жұмыстарын автоматтандыруға мүмкіндік береді. Өндіріс процестерін дер кезінде бақылауға алу өндірістегі қолайсыз ауытқуларды болдырмауға жағдай жасайды.
Өндірістік бақылаудың тиімділігі мына төмендегі жағдайларға байланысты:
- сынақ алатын жерді дұрыс таңдай білу және технологиялық параметрлерін (температура, ылғалдылығы, қоспаның қозғалғыштығы және т.б.) анықтау;
- алынған сынақ қасиетінің материалдың қасиетіне сәйкес келуі;
- сынақ алудың жиілігі, оның шамасы.
Қазіргі кезде материалдан өңделіп жатқан кезде сынақ алудың автоматты әдістері қолданылады. Бұнда материалдан сынақ алудың жиілігі мен оның шамасы материалдың біртектілігіне, материалдың мөлшеріне, түйір материал болғанда оның түйірлерінің мөлшеріне байланысты.
Келіп түскен бастапқы материалдың химиялық құрамын, оның ылғалдылығын, сондай-ақ әктастың құрамындағы СаСО3 (титр) мөлшерін үнемі бақылап отырады.
Шикізат бөлімшесінде шлам немесе шикізат ұнының келесі көрсеткіштері бақылауға алынады:
- химиялық құрамы, ҚК мен модульдер. Қанығу коэффициентінің мәні көбіне 0,88...0,94 аралығында, п=1,7...2,5, р=1,2...1,6 аралығында жатқаны жөн;
- майдалау ұнтақтығы, ол елегіште қалған қалдықтың мөлшерімен сипатталады (№ 02 елегінде 1...3 %, № 008 елегінде 10...15 %);
- шикізат шламының ылғалдылығы 36...40 % аралығында жатады;
- шламның аққыштығы МХТИ-дің аққыштықты өлшеуіш құралы ТН-2 мен анықтағанда 50...70 мм аралығында болуы керек;
- шикізат ұнының ылғалдылығы 1...2 % аспауы керек;
- шикізаттың титрі 75...80 % аралығында болады.
Күйдіру цехында клинкердің сапасын төмендегі көрсеткіштер бойынша анықтайды:
- байланыспаған әктің (СаОбос) мөлшері қатардағы клинкерде 1...2 %, ал тез қатаятын клинкерде 0,2...0,3 % аспауы керек;
- клинкердің 1 литрінің салмағы 1550...1650 г/л тең болады.
Шымкент, Қарағанды және басқа да цемент зауыттарында жеделдетілген петрографиялық талдаудың көмегімен клинкердегі байланыспаған әкті, минералдық құрамын, ҚК және клинкердің белсенділігін анықтайды.
Ұнтақтау цехында дайын өнім мен оның құрам бөліктерінің төмендегі көрсеткіштерін бақылауға алады:
- ұнтақталып жатқан цементтің құрамындағы клинкердің, гипстің, минералды қоспалардың мөлшері;
- цементтің ұнтақтығы № 008 елегімен тексергенде технологиялық регламент бойынша цементтің түріне қарай белгіленген шамаға сәйкес келуі керек (МСТ 10178-85 бойынша електе қалған қалдықтың мөлшері 15 % аспауы керек);
- минералды қоспалардың ылғалдылығы (шлактың) 1...2 % аспағаны жөн.
Шикізат цехында диірменге материалдың бір қалыпты белгілі бір мөлшерде берілуін қадағалап, бақылап отырады. Шикізатты майдалау мен кептіру процесі бірдей бір уақытта жүретін агрегаттарда кептіргіш агенттің мөлшері мен температурасын, диірмендегі ауаның азаюын, газдың шаң-тозаңдығын тексеріп отырады.
Күйдіру цехында пешке берілетін шикізат пен отынның мөлшерін, пештегі ауаның азаюын, шығатын газдың температурасын, мұздатқыштан шығатын екінші реттегі ауаның температурасын, ауаның артықтық коэффициентін (коэффициент избытка воздуха), мұздатқыштан шыққан клинкердің температурасын бақылауға алады.
Ұнтақтау цехында клинкер мен цемент температурасын, диірмендегі ауаның азаюын, аспирациялық ауаның температурасын, аспирация жүйесінің жұмысын, ұнтақтаудың интенсификаторының берілуін қадағалап отыру керек.
Орталық лаборатория мен техникалық бақылау бөлімі (ОТК) дайын өнімнің төмендегі көрсеткіштерінің стандартқа сәйкестігін анықтап отырады:
- цементтің маркасы;
- ұстасу мерзімі;
- ұнтақтығы;
- көлемінің бір қалыпты, біркелкі өзгеруі;
- SO3 пен шлактың мөлшері;
- клинкердегі MgO мен сілтілердің мөлшері.
Бұл көрсетілген тексерулер МСТ 310-76.1,2,3, МСТ 310-80.4 бойынша жүргізіледі. Бүгінгі таңда қазақстандағы бірнеше цемент зауыттары шетел компанияларының басқаруымен жұмыс істейді, цементтер шет елдерге экспортталады. Сол үшін цементтердің сапасын Ресейлік ГОСТ 31108-2003 және шетелдік ЕN 197-2000 сәйкестігін де зерттейді.
Арнайы цементтер шығарған кезде жоғарыдағы көрсеткіштерден басқа клинкердің минералдық құрамын, цементтің ақтығын, иілгіштігін, гидрофобтылығын, беріктігінің өсу жылдамдығын, меншікті бетін, ұлғаю шамасын, жылу бөлуін, қорғаныш қасиетін және т.б. тексереді.
5.16 Өнімді паспорттандыру
Цементті тұтынушыларға тиеп жіберу «кепілдіктеме маркасы» негізінде жүргізіледі. Цементтің маркасын анықтау әр сағат сайын статистикалық әдіспен алынатын ауыспалы коэффициенттер негізінде диірмендерден байқауға алынатын тәуліктік немесе үш тәуліктік беріктігі бойынша жүргізіледі. Кей кезде «кепілдіктеме маркасы» онда буланғанда жылулық ұлғаю әсерінен үлгілердің тығыздалуы жүретін, арнайы жабық қалыптарда буландырылған үлгілердің беріктігі бойынша анықталады. Буланғаннан (4 сағ) соң, әдеттегі жағдайда қатайған үлгілердің 28 - тәуліктік беріктігіне сәйкес болатын мәліметтер алады. Булау үшін үлгілерді I:I қатынасындағы ерітіндіден дайындайды және 28 – тәуліктік үлгілердің беріктігіне сәйкес келетіндей режимде булайды.
МСТ 22237-76 бойынша тиеліп жіберетін цементке кепілдіктеме маркасы көрсетілген паспорт беріледі. Цементті тиеу кезінде бақылау сынағына байқауға материал алынады, олар орталық лабораторияда үш ай бойына сақталады.
Бақылау сұрақтары.
1. Клинкерді ұнтақтау процесі қалай жүреді? 2. Барабанды диірменнің құрылысы қандай? 3. Ашық және жабық циклдағы ұнтақтаудың арты қшылықтары қандай? 4. Барабанды шарлы диірмендердің өлшемдері және өнімділігі қандай? 5. Барабанды диірменнің өнімділігі неге байланысты? 6. Диірменді қандай ұнтақтағыш денелермен тиейді? Толтырылу коэффициенті қандай? 6. Шарлы құбырлы диірмендерде қандай модернизациялар жасалған? 7. Диірменнің бронды футеровкасы қандай қызмет атқарады? 8. Бронды футеровканың қандай түрлері болады? 9. Бір тонна цемент ұнтақтауға ұнтақтағыш денелердің, бронды футеровканың шығыны қандай? 10. Шарлы құбырлы диірменнің аспирациясы қалай жасалады? 11. Аспирациялық ауа шаңнан қалай тазаланады? 12. Диірменнің аспирациясы не үшін жасалады?13. Қандай жаңа заманауи цемент ұнтақтайтын агрегаттарды білесіз? 14. Полизиус фирмасының білікті (роликті) диірмендері қалай жұмыс істейді? 15. Loesche фирмасының білікті цемент диірменінің құрылысы және жұмыс істеу принципі қандай? 16. Loesche LSKS динамикалық сепараторының құрылысы және жұмыс істеуі қандай? 17. Әр түрлі технологиялық факторлардың диірменнің жұмысына көрсететін әсері қандай? 18. Клинкер минералдарының қаттылығы қандай? 19. Цемент ұнтақтауға электр энергияның шығыны қандай, ол неге байланысты? 20. Цемент ұнтақтау процесін қалай жеделдетуге болады? 21. Камерааралық қабырғалардың түрлері, қызметі қандай? 22. Клинкер сақтайтын қоймалардың түрлері, сыйымдылығы, құрылымы қандай? 23. Цемент өндірісінде шаңсыздандыру жұмыстары қалай жүргізіледі? 24. Шаң сұзгіштердің құрылымы, тазалау дәрежесі қандай? 25. Цементті тұтынушыларға қалай артып жібереді? 26. Цемент қоймаларының өлшемі, сыйымдылығы, құрылымы қандай? 27. Цемент өндірісіндегі бақылау жұмыстары қандай? 28. Дайын өнімді қалай паспорттандырады? 29. Дайын өнімнің қандай көрсеткіштерінің стандартқа сәйкестігін анықтайды? 30. Клинкердің сапасын қандай көрсеткіштерімен анықтайды? 31. Шикізат қоспаның сапасын қандай көрсеткіштерімен анықтайды?
VΙ тарау
Өндірісті автоматтандыру
Шикізат материалдары және цемент ұнтақтағанда қолданылатын құралдар. Цемент өндірісінде жалпы және арнайы құралдардың едәуір түрі қолданылады. Бұл жалпы жеке агрегаттар мен процестерді барынша сапалы басқару мақсатымен бақылау және реттеу жүйесінде іске қосылуға қажетті арнайы технологиялық параметрлердің әртүрлілігіне байланысты. Атап айтқанда, диірменге материал тиеуді бақылау, шикізат шламының тұтқырлық индикаторы (ротационды визкозиметр), деңгейді өлшегіш, ұнтақтау майдалылығын бақылайтын құрал, радиациалық тығыздықты және деңгей өлшегіштер, газоанализаторлар, су, мазут, газ, шикізат шламы, ұнтақ шығынын өлшегіштер, термопаралар және аналитикалық пирометрлер, амперметрлер, манометрлер және т.б. құралдар.
Диірменге материал тиеуді бақылау құралы. Шикізат, клинкер және қатты отын шарлы диірменде ұнтақталады. Ұнтақтауды тиімді басқару үшін диірменге материал тиеуді үздіксіз бақылап отыру қажет. Осы мақсатпен материал тиелу дәрежесіне диірменнің шығаратын шуының белгілі тәуелділігі есептеледі. Бұл тәуелділік әр диірменге тән және майдалағыш денелердің құрамы мен салмағы, қорғауыш футеровканың тозу түрі мен дәрежесі, материалдардың түйіршік құрамы мен ұнтақталғыштығы және басқа сол сияқты түрлі өлшемдердің қызметі болып табылады. Бұл тәуелділік әр түрлі өлшемдегі диірменге материал тиеуді сол сияқты диірменнің ұзына бойына әр түрлі зоналарда материал жағдайын бақылау үшін пайдаланылады.
5.22-суретте сипатталып отырған құралдың сызбасы көрсетілген. Диірмен сақинасының жанына майдалағыш денелердің құрайтын жағынан диірменнің шуын қабылдайтын датчик орнатылған (электроухо). Мұндай датчик түрінде микрофон, дірілдеткіш және индукциялық құралдар қолданылады.
Сақина қасына орнатылған датчик, жұмыс істеп тұрған диірменнің шуын немесе оның акустикалық шағылыстырушы ретінде қарастырылатын қанқасының дірілін қабылдап, оны шу ЭДС-і деп аталатын электр сигналына айналдырады.
Талдаушы (анализатор немесе сайманның электронды блогы) диірменге материал тиеу деңгейіне қатысты ең көп мәлімет беретін, оны ұлғайтатын, түзететін, сүзетін және қосалқы құралдың қабылдау нүктесіне және ЭЕМ–ға беретін қабылдау сигналының бір параметрін бөліп алады.
Шикізат шламының тұтқырлық индикаторы. РВ–3А шламның тұтқырлық индикаторы, сулы әдіспен жұмыс істейтін цемент зауыттарында шикізатты құбырлы шарлы диірмендерде ұнтақтағанда және шикізаттың жұмсақ тау жыныстарын саз-балшық араластырғыш немесе «Гидрофолдарда» өңдегенде шламның тұтқырлығын бақылауды жүргізеді. Оның жұмыс істеу принципі сұйыққа батырылғын дененің айналуға қарсылығының сұйықтық тұтқырлығына тәуелділігіне негізделген. Тұтқырлық индикаторының сезімтал бөлігі бақыланатын сұйықта цилиндрлі немесе шарлы роторды айналдыратын аз қуатты электрқозғалтқыш болып табылады (6.1-сурет).
![]() | 6.1–сурет. Шламның тұтқырлық индикаторы РВ–3А: 1–шламды сынаққа алатын құрал; 2-құбыр; 3-бак; 4-тұтқырлық индикаторының сезімтал бөлігі |
Шикізат диірменінен алғанда шламның жалпы ағынының бір бөлігі шламды сынаққа алатын (1) құралдың ішіне келіп түседі, ал одан құбыр (2) арқылы тұтқырлық индикаторының сезімтал бөлігі (4) орнатылған шламды сынаққа алатын бакқа (3) келіп түседі.
Шикізат шламы бактың жақтауларынан асып төгіліп, шұңқырға құйылады. Осылайша бакта үздіксіз ауысып тұратын шламның тұрақты деңгейі сақталады. Егер шлам араластырғыштан немесе Гидрофолдан арнайы арықша арқылы тасымалданатын болса, онда тұтқырлық индикаторының сезімтал бөлігі арықша қалытқысында орнатылу керек.
Сезімтал бөліктің роторы айналғанда өлшенетін ортада оның тұтқырлығына байланысты қозғалтқыштың білігіндегі момент өзгереді және осыған байланысты басқару орамының эквиваленттік кедергісі өзгереді, бұл көпір диагоналының ағысын өзгертеді.
Егер ротор сипаттамасы берілген технологиялық мәндеріне сәйкес (жайылғыштығы, ылғалдылығы, ұнтақтау майдалылығы) шикізат шламында айналғанда көрсеткіш аспабының тілі 60...80 бөлік диапазонында болса, онда тұтқырлық индикаторы дұрыс іске қосылған деуге болады. Тұтқырлық индикаторы цемент өндірісінің сулы әдіспен жұмыс істейтін көптеген кәсіпорындарында қолданылады.
Деңгей және тығыздық өлшегіштерде өтіп кететін сәуле пайдаланады, деңгейдің және тығыздықтың ядролық индикаторлары пайдаланады. Гамма–квант (цезий Сs-137 изотоптары) дерекнамасы (источник) болаттан жасалған іші қорғасынмен қапталған контейнерде сақталады. Оны силостың немесе бункердің сыртына орналастырады. Клапан ашылғанда гамма сәулелер шашылады. Сәуле силостан немесе бункерден өтіп қабылдағыш детектормен ұсталып, мұнда материалдың бар немесе жоғын, толтырылған дәрежесін көрсетеді.
6.2-суретте клинкер мұздатқыштағы клинкер қабатының қалыңдығын көрсететін құрал көрсетілген.
![]() | 6.2-сурет. Мұздатқыштағы клинкер қабатының қалыңдығын көрсететін ядерлі датчик: 1-детектор; 2-күшейткіш; 3-өзі жазғыш; 4-реттеуші; 5-мұздатқыштың торы; 6-тордың астындағы камера; 7-радиацияның дерекнамасы (источник) |
Бұл құрал мұздатқыштың торының қозғалу жылдамдығын реттеуге мүмкіндік береді.
Автоматикалық жүйелер механизмдерді жұмысқа қосатын кезде және олардың электр блокировкасында пайдаланады. Блокировка механизмдердің іске қосылу немесе тоқтату тізбектілігінде пайдаланады. Тұрған механизмдерді – қоректендіргіш, тасымалдағыш т.б. автоматты ретінде тоқтатады. Сонда қондырғы шикізатпен, клинкермен опырылым (завал) болмайды.
Электр блокировка бірденнен қосуға болмайтын екі механизмді қосуға мүмкіндік бермейді. Мысалы: пештің негізгі және қосалқы жетегін бірдей қоспайды.
Әктасты ұсақтау процесін автоматтандыру. Бұл жүйе тұрақтандырады, авариядан сақтайды, ұсақтағыштың жұмысын жақсартып цехтың өнімділігін жоғарылатады.
Схемада (6.3-сурет) жақты және 2 балғалы ұсақтағыш, колосникті және пластиналы коректендіргіш, тасымалдағыштар, шаңсүзгіштер көрсетілген.
Ұсақтағыштарды қоректендіру электрқозғалқыштағы токтың мөлшерімен бақыланады. Оның саны орталық басқару пультқа компьютерге келіп түседі. Автоматтандырылған жүйе қауіпті жағдайда ұсақтағышты тоқтатады (мысалы майдың қысымы жеткіліксіз, температурасы жоғары болса).
Әктастың ленталы тасымалдағышы металліздегішпен жабдықталған, ол ферромагнитті денелер кездесетін болса оны материалдың ішінен алып тастайды немесе тасымалдағышты тоқтатуға дабыл береді.
Бункердің әктаспен толтырылуын радиактивті деңгейдің сигнализаторы көрсетеді. Бірінші ұсақтау сатыдағы механизмдер бір кнопкамен іске қосылады: майлау стансасы, жеңді сүзгіш, жақты ұсақтағыш, одан кейін бөлек кнопкамен колосникті жабдықтағыш қосылады. Электрблокировка қосудың тізбегін қамтамасыз етеді.
![]() |
6.3-сурет. Әктасты ұсақтау процесін автоматтандыру схемасы: 1-думпкар; 2-түсіргіш; 3-колосникті қоректендіргіш, 4-жақты ұсақтағыш; 5-шынжырлы қоректендіргіш; 6-ленталы тасымалдағыш; 7-бункер; 8-пластиналы қоректендіргіш; 9-балғалы ұсақтағыш; 10-ленталы тасымалдағыш; 11-жеңді сүзгіш; 12-майлау стансасы; 13-металліздегіш |
Жүйені тоқтату кері тізбекте жасалады. Ұсақтағыштың ішіндегі материал толық ұсақталғаннан кейін тоқтату керек. Материалға толып тұрған ұсақтағышты іске қосса авария болып ол сынуы мүмкін.
Ұнтақтағыш-кептіргіш диірменнің жұмысын автоматтандыру. Бұл үш жүйеден құралады (6.4-сурет). Бірінші жүйе диірменге 4 келетін жылутасымалдағышты тұрақтандырады.
![]() | 6.4-сурет. Бір мезгілде кептіріп ұнтақтайтын жүйенің автоматтанды ру схемасы: 1-бункер; 2-жабдықтағыш; 3-оттық; 4-диірмен; 5-циклон |
Циклоннан 5 кейін орнатылған датчик диірменнен өткен газдың мөлшерін өлшеп дроссельді жапқышқа хабар береді. Екінші жүйе диірменге материал беруді тұрақтандырады. Кіретін және шығатын цапфаның арасындағы қысымның айырмашылығын өлшейді. Неғұрлым қысымның айырмашылығы көп болса, соғұрлым диірменге көп материал түседі. Үшінші жүйе дірменнен шығатын газдардың температурасын тұрақтандырады. Диірменге келген материалдың ылғалдылығы өзгерсе, диірменнен шығатын газдардың температурасы да өзгереді.
Болған өзгеріс жөнінен датчик реттегішке сигнал береді, ол орындаушы механизмді-дроссельді іске қосады. Ол диірменге келетін салқын ауаның мөлшерін реттейді. Шикізатттың ылғалдылығы жоғарылағанда диірменге сорылатын ауаның көлемі төмендеп температурасы жоғарылайды. Диірменнен шығатын газдардың температурасын бір қалыпты қылып сақтасада онда бастапқы шикізаттың ылғалдылығы өзгерсе де ылғалдылығы тұрақты ұнтақ алуға болады. Диірменнің редукторының подщипниктерін майлайтын стансаның жұмысы аспаптармен бақыланады. Подшипниктердің жұмысына қауіп туса онда аспаптар диірменді тоқтатуға сигнал береді.
Шикізатты сулы тәсілмен ұнтақтағанда келесі мақсаттар қойылады: шикізат компоненттерінің қатынасын тұрақты сақтап тұру; шикізат шламның ылғалдылығын, ұнтақталу дәрежесін біртекті сақтап тұру.
Диірменнің I камерасының әктаспен толтырылуы шуылдың жиілігімен бақыланады. Микрофон (электроухо) күшейткіш арқылы жабдықтағышпен немесе әктастың салмақты дозаторымен байланысқан. Бірінші датчик Д1 диірменнің қаңқасымен электрмагнитті дірілігін қабылдап оны қажетті дірілмен салыстырады. Нормаға сәйкес келмесе орындаушы механизмге-салмақты өлшегішке немесе бункердің 1 тарелкалы жабдықтағышына қажетті тапсырма береді (6.5-сурет).
![]() |
6.5-сурет. Сулы тәсілдің шикізат диірменінің автоматты реттеуінің схемасы: 1-әктас бункері; 2,3-әктас және шлам жабдықтағыштары; 4-вискозиметр; 5-шлам қабылдағыш; 6-диірмен; 7-насос |
Диірменге су және сазбалшықты шлам беру микрофон Д2 сигналымен орындалады. Бұл микрофон шлам пайда болатын екінші камерада орналасады. Сигнал микрофоннан реттеуші Р2 барады, ол диірменге су және сазбалшықты шлам берудің жылдамдығын реттейді. Шламның соңғы тұтқырлығы вискозиметр арқылы реттеледі. Ол су мен сазбалшықты шламның шығынын реттейді.
Диірменді іске қосардан алдын майлау жүйесін қосады. Майлаудың жеткілікті параметрлері жетілгеннен кейін диірменнің негізгі қозғалтқышы қосылады. Шикізат жабдықтағыштары тек диірмен жұмыс істеп тұрғанда іске қосылады. Диірмен тоқтағанда оларда тоқтайды. Бір мезгілде негізгі және қосалқы жетек іске қосылып кетпес үшін электр бұғаттау (блокировка) жүйесі жасалған.
Шлам қабылдағыштың 5 шламға толтырылуын деңгей өлшегіш Р4 реттеп шлам толған кезде автоматты насостарды іске қосады.
Клинкер күйдіру процесін автоматтандыру басқа процестермен салыстырғанда қиынға түседі. Себебі пеште бірнеше химиялық, жылулық процестер ұзақ уақытта жүреді. Пештің жұмысының бір көрсеткіші өзгерсе, ол бірнеше басқа көрсеткіштерді өзгертеді.
Клинкердің сапасын, белсенділігін, отын шығынын, пештің жұмысын тік функционалды тәуелділікке байланыстыру мүмкін емес. Сол үшін бірнеше тәуелсіз жүйелер жасалған. Олар саны төмендеу параметрлерді байланыстыра алады.
Негізгі кіретін параметрлерге шикізат қоспаның химиялық құрамы, майдалылығы, ылғалдылығы, отынның жылу бөлгіштігі, ұсталған шаң мөлшері, оны пешке қайтарылуы жатады.
Айналмалы пешті автоматтандыру схемасы бес тәуелсіз реттеушіден құралады (6.6-сурет). Екі жүйе пешке берілетін газдың қысымының және шламның деңгейінің Р1, Р2 біртектілігін қамтамасыз етеді. Пештің айналу жылдамдығы және шлам беру жылдамдығының қатынасы біртекті сақталады. Реттеуші Р1 газдың қысымын тұрақтандырады. Радиациялық пирометр 1 жентектеліп пісіп жатқан материалды және жақпаны (обмазка) байқап тұрады. Бұл жүйе реттеуші Р3 және кальцинирлеу алабындағы температураны өлшейтін термопарамен 2 байланысқан. Кальцинирлеу алабында температура төмендесе реттеуші Р3 пешке берілетін газды жоғарылатады. Жүйеге газды талдағыш қосылған. Ол қалдықты түтінді газдағы оттегінің мөлшерін анықтайды. Түтінді газдарда оттегі 0,8 % төмен болса, ол пешке берілетін отынды жоғарылата алмайды, ал 3 % болса, төмендете алмайды. Реттеуші Р3 кальцинерлеу алабындағы температураны газдың жапқышына әсер етіп реттейді. Бұл алаптағы материалдың температурасы оның дайындық дәрежесінің көрсеткіші болып есептеледі. Пештің ішіндегі материалдың температурасын өлшеу қиын. Отқа төзімді кірпіште тереңдетілу жасалады, соған термопараны орналастырады. Солай температураны өлшейді.
Реттеуші Р4 пештің айналу жылдамдығын шламмен қоректендіруін келістіреді. Пеш баяу айналғанда шламның келуі азаяды.
Реттеуші Р5 термопараның көрсеткішімен шаң шөктіргіш камерадағы түтінді газдардың температурасын бақылайды.
![]() |
6.6–сурет. Айналмалы пеште клинкер күйдіру процесін автоматты реттеу схемасы: 1–оптикалық пирометр; 2,5– термопаралар; 3–газды талдағыш; 4–пеш |
Реттеуші құрал ол түтінсорғыштың алдындағы жалюздік жапқыш. Түтінді газдардың температурасы жоғарылап, максимумға жеткенде, электрсүзгіштің жұмысына қауіпті болғанда, жапқыштың жағдайы өзгереді, түтінсорғыштың жасайтын сиретілуі жоғарылайды, пешке сырттан сорылатын салқын ауаның мөлшері өседі.
Пештің автоматикасы тоқтаусыз жұмыс істеуі үшін оның параметрлерін тұрақтандыру керек: шламның химиялық құрамын, ұнтақталу дәрежесін, ылғалдылығын, газдың қысымын, екіншілік ауаның температурасын т.б. Бұдан басқа автоматика электрсүзгіштердің қызып кетпеуінен сақтайды, айналатын механизмдерді майлайды.
Пештің ыстық жағында басқаратын пульт орналасады. Пультта келесі бақылау өлшегіш аспаптар орналасады:
- пештің электрқозғалтқышының, түтінсорғыштың, желдеткіштің, шлам жабдықтағыштың, клинкер тасымалдағыштың электрқозғалтқыштарының тоқ күшін;
- клинкердің жентектелу, кальцинирлеу алабында, газдардың шаң шөктіргішінде, біріншілік ауаның, мұздатқыштан шыққан клинкердің, мұздатқыштың бірінші колосниктерінің, редуктордағы майдың, подшипниктердің температурасын;
- шаңшөктіргіш камерадағы, пештің басындағы, электрсүзгіштен кейінгі, мұздатқыштың ыстық камерасындағы сиректелу;
- біріншілік ауаның шығыны, қалдық газдардың құрамы, газдың шығыны, оның қысымы.
Ескі зауыттарда әрбір өндіріс цехта жұмыс істейтін технологиялық қондырғылар сол цехтағы пульттан басқарылады. Бір болмаса бірнеше операторлар жүздеген аспаптардың көрсеткіштерін талдап үлгере алмайды. Сол үшін процесті басқаруға ЭЕМ пайдаланатын болды.
Бүгінгі таңдағы заманауи цемент зауыттарында бүкіл технологиялық процесс бір орталық пульттан бірнеше операторлармен басқарылады.
Клинкерді күйдіру және мұздатуды басқаратын жүйелер. Клинкердің күйдіру дәрежесін сипаттайтын жанама параметрлердің бірі – оның түйіршіктерінің орташа өлшемі. Бұл параметрді пайдалану оның кесектерінің орташа өлшемі өзгергенде желтартқышты мұздатқыштың торындағы ауамен желдететін клинкер қабатының аэродинамикалық кедергісінің өзгеру тәуелділігіне негізделген, бұның өзі мұздатқыш торының астындағы қысым Рреш мен және сол сияқты клинкер қабатынан өтетін ауаның шығынымен Qв сипатталады. Осылайша, клинкердің орташа диаметрін сипаттайтын параметр, қолда бар техникалық саймандармен өлшеуге болатын үш шамаға пропорционал: Рреш, Qв және Jреш.
6.7-суретте АСУТП–ның техникалық саймандарының жиынтығы көрсетілген. Жүйе пештен шығатын клинкер түйіршіктерінің берілген орташа өлшемінің, бас қозғалтқыш пайдаланатын токтың, қыздыру аймағындағы материал температурасының және пештен шығатын газдар температурасының мәндерін бір қалыпты ұстап тұрады. ЭЕМ–ға енгізілетін бақылау параметрлерін пайдаланып, жүйеге қажетті отын; пештен шығатын газдардың және шламның шығынын есептейді, бұл өлшемдерді басқарады.
АСУТП – да бақыланатын және басқарылатын өлшемдердің шамасы ЭЕМ – ге енгізіледі. Бірінші шама ЭЕМ–ға енгізілетін бастапқы өзгерту белгілеріне сәйкес отынның шығынын реттеуге, екінші шама түтін сорғыштың сұкпа-жапқыш (шибер) орналасуына (бұл кезде түтін сорғышқа түсетін ауырлық ағынның есепті мәніне байланысты әсерлер іске асырылады) арналған. Жүйеде клинкерді орташа өлшемі ауасорғышқа түсетін қысым, мұздатқышқа берілетін ауаның жалпы шығыны және тордың қозғалтқышы пайдаланатын ток бойынша есептеледі.
![]() |
6.7–сурет. Клинкер күйдіру АСУТП–сының техникалық құралдар жиынтығының үлкейтілген тірек сызбанұсқасы: А – пеш; Б – мұздатқыш; В – шаң тұндыратын камера; Г – түтін сорғыш (мұржа); Д – шлам тасымалдайтын құбыр; Е – газ құбырлары |
Желтартқышты мұздатқышты басқару үшін пештің жұмысымен сәйкестендірілген және желтартқыш мұздатқыштың температурасы, ондағы материал қабатының қалыңдығына, пешке қайтарылатын жылу мөлшерінің ұлғаюын қамтамасыз ететін критерий қабылданған.
Пештің ыстық басындағы ауаның сиретілуін бір қалыпта ұстап тұру аспирациялық ауаны жіберетін сұкпа-жапқыш (шибердің) орнын ауыстыру жолымен, ал мұздатқыштан шығатын клинкердің температурасын бір қалыпта ұстап тұру ауаның жалпы шығынын сұкпа-жапқыштың (шибердің) көмегімен өзгерту арқылы іске асырылады.
Сипатталып отырған жүйенің артықшылығы – онда оператор диалогтық (сөйлесу) режимде жұмыс істей алуы. Бұл жүйені пайдалану нәтижесі, жүйе қоспаны күйдіруді және клинкерді мұздатуды тұрақты бір қалыпта ұстап тұратынын және осының нәтижесінде футеровканың (ыстық температура әсерінен қорғайтын қабаттың) төзімділігін, температураның ауытқуының азаюы нәтижесінде арттыруға, отынның үлестік шығынын азайтуға, клинкердің сапасы мен пештің өнімділігін ұлғайтуға және сол сияқты жұмыс жағдайын жақсартуға мүмкіндік береді.
Цемент қоспасын ашық циклды диірмендерде ұнтақтауды басқару жүйесі.
Клинкерді және қосымша материалдарды ұнтақтау негізінде ашық циклды шарлы диірмендерде жүргізіледі. Қоспаның құраушылары клинкер, гипс, қосымша материалдар диірменге өлшегіштермен немесе тарелкалы қоректендіргіштермен үздіксіз беріліп тұрады.
Процесті автоматты реттеудің мақсаты цементтің берілген ұнтақтау майдалығын және құрамын бір қалыпта ұстап тұру болып табылады. Бұл үшін жанама параметр ретінде диірменге материал артуды бақылайтын бірінші камераның бас жағына орнатылған құралды пайдаланады (ДАБС) және осылайша диірменнің өнімділігі мен берілетін қоспаның ұнтақталғыштығын жанама көрсететін мәліметті алады.
6.8–суретте диірменге материал артуды автоматты түрде реттестіретін қарапайым тірек – сызба көрсетілген. Диірменнің бірінші камерасына зат тиеу деңгейі ДАБС құралымен бақыланады, құраушылардың шығыны тарелкалы қоректендіргіштерді пышақтарының орналасуымен (немесе өлшегіштердің материал беруімен), орындау механизмдерімен (ОМ) анықталады.
ДАБС белгісі клинкер шығынын реттегіш сайманын Р2 қабылдау нүктесіне беріледі. Бұл жерге сол сияқты орындау механизміне әсер етіп кері байланыс сигналы (белгісі) беріледі.
Гипс пен қосымша материалдардың (лай, опока және басқалар) шығынын реттейтін саймандарға Р1 және Р3 клинкер шығынының орындау механизмі датчиктерінің белгісі және өзіндік ОМ кері байланысының сигналы беріледі. Осылайша, барлық тарелкалы қоректендіргіштердің пышақтары ДАБС–тың сигналының өзгеруіне пропорционалды орын ауыстырады. Параметрлер қажетті қалыпқа сәйкес болғанда автоматты реттестіру жүйесі ДАБС сигналы мен барлық құраушылардың жалпы шығыны арасында белгілі қатынас ұстап тұрады, бұл – цементтің ұнтақтау майдалылығының диірменнен түскендегі ауытқу көрсеткішін қолмен басқарғандағымен салыстырғанда едәуір азайтады. Бұл жүйе сол сияқты құраушылар арасындағы белгілі қатынасты ұстап тұрады, сөйтіп цемент біршама тұрақтылығына қол жетеді.
![]() | 6.8-сурет. Цемент диірменіне материал артуды автоматты түрде реттестіретін қарапайым-тірек сызбасы |
1970 жылдары ВТ – АСУТП құралдарын қолданып цемент диірмендерін басқару жүйелерін жасап шығару басталды. Мысалы үшін, Ахангаранцементте іске қосылған базалы АСУТП – ны қарастырамыз. Ол НЦУ режимінде белгілі уақыт масштабында жұмыс істейді және келесі қызметтер атқарады:
- жабдықтар мен процестердің жағдайын сипаттайтын, біртекті және дискретті датчиктерден мәліметтер алу;
- мәліметтерді бастапқы өңдеуден өткізу және процесс пен жабдықтардың жағдайын талдау;
- біртекті датчиктердің сигналдарының дұрыстығын талдау;
- болып жатқан жағдайды бағалау және басқару режимін іріктеп алу;
- диірмендердің тұрақты жұмыс режимінде, оларға артық материал тиелгенде қоспаны беру үзіліп қалған жағдайда процесті басқаруды ұйымдастыру;
- камералы насосты басқа жаққа бұру, дискретті датчигінің сигналы бойынша анықталатын диірмендердің сол кездегі өнімділігін, тиеудің жанама параметрі бойынша қосымша материалдар мен клинкер шығынының өзгеруіне басқару әсерін есептеу;
- ОМ – ға басқару әсерін беру;
Технолог–операторға процесс пен жабдықтардың жағдайы туралы мәліметтерді жеткізу (мнемосызбанұсқадағы жарық сигналы, көрсеткіш құралдар, баспаға басып шығаратын құралдар).
Қызмет атқаратын адамдардың талабы бойынша мәліметтерді қабылдау және беру (АСУТП режимі бойынша өндірімділік және ұнтақтау майдалығы бойынша тапсырманы енгізу).
АСУТП – ның техникалық жабдықтарының жинағына (6.9– сурет) автоматтандырудың қосымша жабдықтары, көрсеткіш құралдар, мнемосызбанұсқа қашықтықтан басқару мүшесі, технолог – оператордың басқару орны, т.б. кіреді.
![]() |
6.9–сурет. Цемент қоспасын ұнтақтау АСУТП–ның техникалық жабдықтарының жиынтығы |
Бақылау сұрақтары.
1.Диірменге материал тиеуді қалай бақылады? 2. Ұнтақтағыш-кептіргіш диірменнің жұмысын қалай автоматтандырады? 3. Шикізат шламның тұтқырлығын қалай бақылады? 4. Шикізат диірменінің автоматты реттеуінің схемасы қандай? 5. Айналмалы пеште клинкер күйдіру процесін автоматты реттеу схемасы қандай? 6. Әктасты ұсақтау процесін автоматтандыру қалай жасалады?
VΙΙ тарау
ЕҢБЕК ҚАУІПСІЗДІГІ, ЭКОЛОГИЯ ЖӘНЕ ҚОРШАҒАН ОРТАНЫ ҚОРҒАУ
7.1 Еңбек қауіпсіздігі
Цемент зауытында техника қауіпсіздігі, еңбекті қорғау және өндірісте тазалық сақтау жұмыстарына тікелей директор мен бас инженер басшылық жасайды. Цех немесе бөлімше бастығы сол цехтағы техника қауіпсіздігіне жауап береді. Шебердің негізгі міндетінің бірі ұйымдастырушы ретінде техника қауіпсіздігі мен еңбекті қорғаудың ережелерін бұлжытпай, қатаң түрде орындалуын қамтамасыз ету болып табылады.
Шебер жұмысқа қабылданған жұмысшыларды қауіпсіздік ережелерімен таныстырады және үйретеді, белгілі бір уақытта жұмысшыларға нұсқаулар беріп, олардың техника қауіпсіздігі жөніндегі ережелерді орындауын қадағалап және механизмдер мен қоршаулардың дұрыстығын бақылап, қарап отырады.
Зауытқа жұмысқа кірген жұмысшылар тек техника қауіпсіздігі жөніндегі нұсқауларды және жұмыс орнында жұмыстың қауіпсіз әдісіне үйренгеннен кейін ғана жұмысқа жіберіледі. Әрбір үш ай сайын нұсқауларды қайталап жылына бір рет тікелей жұмыс орнында қауіпсіздік тәсілімен жұмыс істеуге үйретіледі. Жылына бір рет зауыттың инженер-техник қызметкерлерінің техника қауіпсіздігі жөніндегі білімдері тексеріліп тұрады.
Зауытта еңбекті толық қауіпсіздендіру мәселелері технологиялық жабдықтарға қойылатын талаптар келтірілген.
Айналмалы және шахта пештері. Пеш жұмыс істеп тұрған кезде техника қауіпсіздігіне аса көңіл аударған жөн. Пешті іске қосар алдында (розжиг), пештің жұмысына қатысы жоқ адамдар түгел сол бөлмеден шығуға тиісті. Газбен уланып қалмауы үшін шлам бақылаушысы өз орнынан кетуі тиіс, сонымен бірге кальцинатор мен концентратор және циклонды жылуалмастырғыш алаңында болуға тиым салынады: ол тек бір текті отынмен ғана тұтанылуы тиіс. Газбен тұтандырған кезде түтін шығатын мұржаны тексеру қажет, оны желдету қажет.
Желдетуден, яғни ауаны тазартудан соң пешті өзіндік тартуға ауыстырып, түтін мұржасының қалқанын (түтін жолында болатын қалқан жапқыш) шаң шөктіргіш камерадағы тягомер (тарту күшін өлшегіш) жоғарыдағы ауаның сұйылуы 3...5 мм су бағанасын көрсететіндей етіп жабылуы керек. Форсункаға газ жіберер алдында газ өткізгіштің коллектордан форсункаға газ әкелетін бөліктерін газбен үрлеу қажет, ол бақылау ысырмасы мен «тұтандырғыш білтеге» ысырманы 2...3 мин (қоспаның жарылыс қауіпсіздігін анықтау мақсатымен) ашып қою жолымен жүргізіледі. «Тұтатқыш білтеге» ысырманы жауып, штуцер арқылы металл стақанға байқау үшін газдың біраз мөлшері алынады. Оның жануын цехтың бөлмесінен тыс жерде тексереді. Стақандағы газ қалыптағыдай тыныш жанса «Техника қауіпсіздігі» ережелерін басшылыққа ала отырып, тұтандыруға кірісуге болады. Егер тұтандыру кезінде форсункадан шығар кезінде газ жанбаса немесе жалын форсунка ұщынан бөлініп кетсе, онда дереу газ тасымалдағыштағы жұмыс ысырмасын және бақылау ысырмаларын жабу керек, тамызықты алып тастап «тұтандырғыш білтеге» ысырманы ашып, пеш – түтін мұржасы жолындағы түтін тартқышты қосып желдету керек.
Жұмыс істеп тұрған форсункалар шілтерге газ келіп түспеген жағдайда және газ қысымының кенет (0,1 кг/см2 төмен немесе рұқсат етілген жоғары қысымнан жоғары) өзгерген жағдайында, түтін тартқыштың кенеттен тоқтап қалған кезінде немесе тозаң тұтқыш камерадағы сирексіту нөлге дейін төмендегенде дереу өшірілуі тиіс.
Пештегі жөндеу жұмыстарын оны 40 0С дейін суытқаннан кейін барып жүргізуге болады. Жоғары қысым желдеткіші ол кезде тоқтатылуы тиіс, ал пештің электрқозғалтқыштары мен көмірін қамтамасыз ететін шнектердегі сақтандырғыштарды, моторлардың өздігінен қосылып кетпеуі үшін жағдайын зерттеу және жөндеу үшін олардың температурасы 40 0С төмен болуы керек. Ауаның ең жоғарғы температурасы 50 0С аспаған жағдайда ғана жұмысшылар пеште бола алады. Пешті және концентраторды тоқтатпайынша концентраторға заттарды тиеуге болмайды.
Шахталық пештердің эксплуатациясы кезінде ондағы қатып қалған балқымаларды бұзу және шахта күмбезіндегі құлаған жерлерін жөндеу ең қауіпті жұмыс болып табылады. Балқып қатып қалған күйіндіні талқандау кезінде жұмысшылардың күйіп қалмауы үшін ыстық бумен жұмыс істеуге болмайды. Жұмыс тек шахтаға түспей жүргізілуі тиіс және оларды белбеумен немесе арқанмен байлап қоюы керек.
Көміркептіргіш және көмірұнтақтағыш қондырғылар. Көміркептіргіш және көмірұнтақтағыш қондырғылар қауіпті жарылғыш қондырғылар категориясына жатады. Көмір тозаңын дайындайтын қондырғы сұйытылған ауамен жұмыс істеуі керек. Диірменнен шыққан кездегі аэрокөмірқоспаларының температурасы: құнарсыз көмір үшін 100 0С, Москва көмірі – 80 0С, газды және булы -75 0С, ұзын жалынды және қоңыр көмір -70 0С-тан жоғары болмауы керек. Жүйенің бір бөліктерінде тозаңның жануы байқалса, кептіргіш немесе ұнтақтағыш қондырғыны тоқтатып және оны өшіру үшін бу немесе ұнтақтағыш қондырғыны тоқтатып және оны өшіру үшін бу немесе көмірқышқылын жіберу керек. Шанақтағы көмір тозаңының температурасы мен мұржадағы аэроқоспаның температурасын қадағалап отыру керек.
Шанақтар, құбырлар, сепараторлар арнаулы сақтандырғыш қақпақтармен жабдықталуы тиіс. Сақтандырғыш клапандар қалыңдығы 3…5 мм асбест картоны, қалыңдығы 0,5 мм аспайтын жұқа жұмсақ қаңылтыр, қалыңдығы 0,6…1 мм алюминий (парағы) бет тәріздес болып келеді. Клапандар бөлменің жоғарғы бөлігінде, жұмысшыларға қауіпсіз жерге орнатылады. Ондай ыңғайлы жер болмаса, онда сақтандырғыш клапаны бар ағызып немесе бұрып беретін құбырларды қолдану керек.
Ұсақтағыш. Ұсақтағыштардың материал берілетін бөліктерінде қорғаныс қалқаны болуы керек, ол ұсақтағыштан материалдар кесектерінің ұшып шығуын болдырмайды. Ұсақтағыш жұмыс істеп тұрған кезде бір жерге жинаушы тордың жанында тұруға, шығаратын саңылаудың енін реттеуге, өзектерді тазалауға немесе жөндеу жұмыстарын жүргізуге болмайды. Бұл жұмыстардың барлығын машина толық тоқтаған соң, сақтандырғыш электрқозғалтқыштарын алып тастап және «Қоспа! Адамдар жұмыс істеп жатыр» деген тақтайшаны ілгеннен кейін ғана жүргізуге болады.
Құбырлы диірмендер. Жұмыс кезінде диірменнің жанында болуға, айналып тұрған бөлшектерін тазалауға, сақтандырғыш қоршауларға кіруге тиым салынады.
Диірменге техникалық байқау тек ол 40 0С дейін суытылғанда ғана жасалады. Диірменнен майдалағыш денелерді алып түсіру кезінде оның жанында тұруға болмайды.
Цемент сақтайтын силос. Силоста 1 м дейінгі қабатта цемент болса, онда оған төменнен кіру қауіпті. Силосқа тек үйінділер мен қалқаларды құлатқаннан кейін ғана кіруге болады.
Жұмысшыларды силосқа төмен түсіру екі арқанды ауыр жүк көтеретін шығыр арқылы жүргізіледі. Арқанның бір ұшын жұмысшының беліне, бір ұшын шығырға байлайды. Арқанның қалған ұштары біреуі шығырға, екіншісі екінші жұмысшының қолында болады. Цементті құлату жұмысын тек люлька арқылы жүргізеді. Жұмыстың қауіптілігіне байланысты бұл жұмыс цех бастығының бақылауымен ғана жүргізіледі.
7.2 Көмір ұнтақты дайындағанда қауіпсіздік шаралары
Отын-газды ағынның қауіп тілігі-ол оталуы мүмкін. Ұнтақ көмірдің жарылу қауіптілігі келесі факторларға байланысты:
-жарылыс анықтаулы концентрацияда болады-150...1500 г/м3;
-көмірдің ұшқыш компоненттері ғана жарылады; ұшқыштардың мөлшері қауіптілік дәрежесін көрсетеді, антауиттің және кокстың шаңы жарылмайды;
-көмір шаңының ылғалдылығы жарылыс мүмкіндігін төмендетеді;
-көмірдің күлділігі жарылыс мүмкіндігін төмендетеді; күлділік 20% жоғары болса ол көмірдің шаңы жарылмайды;
-көмір қоспасының температурасы жоғарылағанда жарылыс қысымы төмендейді, себебі жоғары температурада ұшқыштар интенсивті ыдырап О2-ні шеттетеді. Ағындағы оттегінің концентрациясы төмендейді, ал 300...4000С ыдырау жылдамдығы жоғарылап жарылыс мүмкіндігі жойылады. Сол үшін төмен температурада жарылыс мүмкіндігі өседі, себебі оттегі концентрациясы жоғары.
-көмірдің ұнтақталу дәрежесі жоғарылағанда реакциялық қабілеті де жоғарылайды, жарылыс мүмкіндігі өседі: 0,17 мм ірі бөлшектер (қоңыр көмір) және 0,12 мм (тас көмір) қауіпсіз.
Көмір шаңының жаналуы (скопление) өзінен-өзі өртену қауіптілігін жорғарылатады. Көмірдің ішкі қабатының бықсып жәй жанып жатқанын (тление) көп уақыт байқамауыңыз мүмкін. Сыртқы қабаты салқындап, ішкі қабаты жанып жатады.
Көмір ұнтақтайтын бөлімде горизонталды жерлерде көмір ұны шөгіп қауіптілікті жоғарылатады. Көмір ұнтағын дайындайтын жүйелер қауіпсіздік клапанмен жабдықталады. Ол деген тік құбырлар, негізгі құбырдар цехтың артына шығарылады. Олар жарылыс кезінде жарылыс қысымды қондырғыны бұзбай ауаға шығарып жібереді.
Өкінішке орай бұл іс-шаралар толық қауіпсіздік жағдайды шеше алмайды. Толық жанып үлгермеген көмір шаңы айналмалы пештің шаң шөктіргіш камераға, электрсүзгішке жиналып жарылыстар болған.
Көмір ұнтақталу бөлімшедегі тағы бір қауіптілік ол ылғал көмірдің бункерінен түспей тоқтап қалуы (зависание). Бункерді тазалағанда барлық қауіпсіздік шараларды сақтау керек, бункерде СО, СО2 газдары жиналып жұмысшы уланып талып қалуы мүмкін.
Технологиялық қондырғыларды «шуровкалармен» тазалайды. Бункерлерді тазалауға электр импульсты тәсіл өңдеп табылған. Электр магнитті импульс материалдың қондырғының бетімен байланысын бұзып, қондырғыны, бункерді тазалап, тоқтамай жұмыс істеуге мүмкіндік береді.
7.3 Экология және қоршаған ортаны қорғау
Экология мәселелері шикізатты кешенді пайдалану жөніндегі бөлімде қарастырылған болатын. Экологиялық күрделі мәселелерді ескеру қоршаған ортаны қорғауға қойылған талаптарды ұлғайтып, атмосфераға тозаңданған ауа мен газдардың шығарылуына және шу деңгейі нормаларына қатаң талаптар қойды.
Осының нәтижесінде тозаңсыздандыру және шуға қарсы қорғаныс шығындары мен құрылысына қаражат жұмсау ұлғайды (зауыт құрылысының құнының 20 % дейін). Қазіргі уақытта тозаңсыздандырғыш қондырғыларды жетілдіруге, олардың жұмысын барынша тиімді етуге әрекет жасалуда. Екінші жағынан, өндіріс технологиясында атмосфераға шығарылатын газдар мен мұздатқыштан шығатын көп мөлшердегі ауаны барынша толық пайдалануға ұмтылу байқалады.
Осыған орай, пештерден шығатын газдарды шикізатты кептіру үшін көбірек пайдалана бастады, желтартқышты мұздатқыштың ауасын пайдалану үлесін ұлғайтатын шешімдер және ауаның мұздатқыштың өзінде тозаңдануын азайтатын әдістер ойлап шығарылды. Мысалы, желтартқышты (клинкерді 80 0C дейін мұздататын) және ішінде ауа клинкермен жанаспайтын (мұздату қабырға арқылы жүргізіледі), сөйтіп ауаның тозаңдануын азайтатын рекуператорлы мұздатқыштарды үйлестіріп, мұздатқыштар жасалған: ауаны қабырға арқылы мұздататын, бұл пештердің мұздатқыштарынан шығатын ауаны тазалау қондырғысынан бас тартуға мүмкіндік беретін тұйықталған жүйелер іске қосылған. Мұздатқыштардың өздері жетілдірілуде.
Тозаңның пайда болуын азайту көлік саймандарындағы артып – түсіру санын азайтады; шаңдататын материалдарды тасымалдағанда тасымалдау қондырғыларының сыртын тығыз қаптап орналастырады. Бұл мақсатпен клинкерді, гипсті және қосымша материалдарды ашық қоймаларда емес, силостарда сақтайды.
Пеш газдарының тиімділігін арттыру үшін тік электрсүзгілерден төрт сөрелі жазық, инерциялық тозаң ұстағыш қондырғысы бар электрсүзгілерге көшеді.
Пеш газдарын тазалауды арттыру мақсатымен және олардың жұмысының тиімділігін қамтамасыз ету үшін буландырғыш мұздатқыштар (себелеп шашылған судың тамшыларын буландыру) орнатылады. Осылайша пештен шығатын газдардың температурасы бір қалыпқа түсіріледі және тозаңның электр кедергісі азайтылады, бұл сүзгілердің тұрақты жұмысын қамтамасыз етеді. Мүмкін болған жағдайда, арзанырақ тозаң ұстағыштарды қолданады. Мысалы, түйіршікті сүзгілер желтартқышты мұздатқыштан шыққан ауаны кептіру қондырғыларынан кейін тазалау үшін құрылады. Бірінші сатыда циклондар орнына желбезекті іріктегіштер қолданылады.
Цемент диірмендерінен кейін үнемдірек электрсүзгілерін орнатады (аз гидравликалық кедергілі). Бірақ ірі диірмендерінен кейін аспирациялық ауаның жоғары температурасына және оның ылғалдылығының аздығына байланысты кондиционерлер орнатуға тура келеді, бұл қондырғыны қымбаттатады. Бұл жағдайда көбіне жең тәріздес сүзгілер қолданылады. Бірақ диірменге мұздататын суды бүркуді пайдалану үшін аспирациялық ауаны кондиционерлемей ақ жұмыс істеуге болады.
Өндірістік шудың деңгейін төмендету үшін цехтарды бөлек жабық ғимараттар түрінде жобалайды. Бірақ бұл құрылыс бағасын арттырады және осыған орай тек пешпен шлам бассейіндері ғана емес, сол сияқты диірмен қондырғыларын да ғимарат сыртына орналастыруға ыңғайлану байқалады. Қабырғалардың дыбыс өткізбеуін қамтамасыз етуді қоршайтын бөліктер ретінде көлемдік салмағы 200…400 кг/м3 арнайы плиталарды пайдаланып жүргізеді.
Клинкерді ұнтақтау цехын желдетуді күшейту жеңді сүзгілерді үрлеу жүйесіндегі циклонды жылу алмастырғыштың газ жолдарында, түтін мұржасында қалқандарды қолдану; түтін тартқыштарды, компрессорларды нөльдік белгі деңгейінде ірге тасқа орналастыру; қозғалту үшін жай жүрісті электрқозғалтқыштарын (500 айналым/мин дейін) пайдалану шудың деңгейін азайтуға жағдай жасайды.
Экологияның және өндірісте тазалық сақтау талаптары өндіріс жайларындағы тозаңның концентрациясын тозаңның құрамына қарай 5...10 мг/м3 мөлшерінде жұмыс істеуге рұқсат етіледі. Қоршаған ортаны қорғауды және тазалық сақтау нормаларын қамтамасыз ету үшін өндіріс жайларында шанақтарды аққыштардан, тасымалдау және ұсақтау жабдықтарына жүк тиейтін орындардан ауаны сорып алу қарастырылады. Одан бөлек, ұсақтау бөлімдерінде ұсақтау алдында тау жыныстары құрамында майдаланатын материалдардың жабысқақтығынан арттыратын ББЗ (ПАВ) бар су себуді қолданады.
Диірмендерден, кептіргіштерден, іріктегіштерден, желтартқышты мұздатқыштардан шығатын, цементті тасымалдау үшін қолданатын ауаны циклондарда түйіршікті, жеңді және электрсүзгілерде тазалайды. Тазалаудың дәрежесін және тиімділігін арттыру үшін екі сатылы тазалауды жиі қолданады (циклон -электрсүзгісі, желбезекті іріктегіш - жеңді сүзгі). Газдарды пештен соң және оларды кептіру – ұнтақтау қондырғыларын пайдаланғаннан соң барынша жабдықталған электрсүзгілерінде тазалайды. Тазалаудың дәрежесін және тиімділігін арттыру үшін сүзгілердің алдында буландырғыш мұздатқыш – кондиционер қондырғысын қолданады, тік сүзгілерден бас тартып, үш және төрт сөрелі сүзгілерді қолданады.
Бақылау сұрақтары.
1. Цемент зауыттарында еңбекті қауіпсіздендіру жұмыстары қалай жасалады? 2. Айналмалы пештері жұмыс істеп тұрған кезде техника қауіпсіздігі қандай? 3. Цемент диірменінде жұмыс істегенде техника қауіпсіздігі қандай? 4. Көмір ұнтақты дайындағанда қауіпсіздік шаралары қандай? 5. Ұсақтағыштарда жұмыс істеген кезде техника қауіпсіздігі қандай? 6. Цемент зауыттарында экология және айналадағы ортаны қорғау шаралары қалай жасалады? 7. Өндірістік шудың деңгейін қалай төмендетуге болады? 8. Көмір ұнтақтайтын бөлімде қандай жағдайда жарылыс болуы мүмкін? 9. Бункерді тазалағанда қандай қауіпсіздік шараларды сақтау керек? 10. Цехта немесе бөлімшеде техника қауіпсіздігіне жауап беретін кім? 11. Жұмысқа қабылдағанда қандай инструктаждар өтіледі?
VІІІ тарау
Портланцементтің гидратациясы және қатаюы
Портланцементтің гидратациялып қатаюы күрделі процесс. Оның негізгі сатылары: портландцемент минералы кристалдарының суда еріп, ерітінділер түзуі; бұл ерітінділерден құрамында су бар жаңа қосылыстардың (кристалгидраттар) кристалдануы және ылғалды-температуралық жағдайларға тұрақты цемент тастарының түзілуі.
Температура, қысым қатаятын жүйенің химиялық құрамы, сұйық және қатты фазалардың ара қатынасы гидратация кезіндегі химиялық реакциялардың жылдамдығы мен механизміне, кристалгидраттардың құрамына үлкен әсерін тигізеді. Ал қатайған цемент тастарының физикалық техникалық қасиеттері кристаллгидраттардың саны мен түрлеріне, кристалдардың формасы мен өлшеміне, кеуектердің саны мен өлшемдеріне байланысты.
8.1 Минерал кристалдарының сумен әрекеттесу механизмі
C3S, C2S, C3A, C4AF минералдары кристалдарының жоғарғы қабаттары сызықша, көлемдік, нүктелік сияқты әр түрлі ақауларға толы болады. Осыған байланысты бұл қабаттар сумен әрекеттесу кезінде химиялық белсенділік танытады. А.А. Байков, С.Д. Окороков, Ю.М. Буттардың зерттеулері бойынша минерал кристалдары сумен жанасқан кезде олардың беткі қабатында, айналасында мынадай процестер жүреді: 1) кристалдың беткі қабаттары су молекулаларын сіңіріп алады (адсорбция), бұл кезде су молекуласы Н+ және ОН- иондарына ажырайды; 2) Н+, ОН- иондары және Н2О диполі кристалдардың беткі қабаттарындағы белсенді орталықтармен әрекеттесіп, әуелі әлсіз, кейін күшті хемосорбциялық байланыстар түзеді; 3) Са2+ ↔ 2Н+ сияқты иондық алмасулардың өрбуінің арқасында кристалдардың құрылымдық бөлшектерінің (Са2+, Al3+, Mg2+, Na+, K+, SiO32- ) бір бөлігі судағы ерітіндіге өтіп, ал Н+, ОН- иондары мен Н2О диполі басқа құрылымдық бөлшектермен гидратты қосылыстар түзеді. Олар Са(ОН)2, САНх, СхSуH2 және т.б.; 4) алмасу иондарымен бірге гидратты Са(ОН)+, H4SiO32-, ерітіндіге өтіп, оны қанықтырады; 5) қаныққан ерітінділер кристалдана бастайды.
8.2 Минералдардың гидратациясы және оның кинетикасы
Үш кальцийлі силикат пен алиттің гидратациясы. C3S пен алиттің гидратациясы кезінде кальцийдің гидросиликаты мен кальций тотығының гидраты (Са(ОН)2) түзіледі, яғни бұл минерал суда әр түрлі затқа бөліне отырып ериді. Зерттеулер бойынша қалыпты жағдайдағы C3S-тің (су минерал қатынасы С:М 0,4...0,7 тең) гидратациялану реакциясы 1...1,5 жылда толық аяқталады, ал түзілген өнімді былай көрсетуге болады:
2(СаО·SiO2) + 5H2O = 3CaO·2SiO2·H2O + 3Ca(OH)2 + Q (8.1)
Q=320…335 кДж/кг
3СаО·SiO2 + 3H2O = 2CaO·SiO2·2H2O + Ca(OH)2 + Q (8.2)
Реакциядан бөлінген жылудың мөлшері түзілген кальций гидросиликатының түрлеріне байланысты 320-дан 500 кДж/кг-ға дейін өзгеріп отырады.
С. Брунауэр, О.П. Мчедлов-Петросянның зерттеулері бойынша минералдардың реакция кезінде бөлетін жылуы төменде кестеде көрсетілген.
8.1- кесте. Жекелеген минералдардың толық гидратацияланғанда бөлетін жылуының мөлшері
Сусыз минералдар | Гидратациялық өнімдер | Бөлінетін жылу, кДж |
3СаО·SiO2 2СаО·SiO2 3СаО·Al2O3 3СаО·Al2O3 3СаО·Al2O3 4СаО·Al2O3·Fе2O3 СаО | 3СаО·SiO2·3Н2О 2СаО·SiO2·2Н2О 3СаО·Al2O3·6Н2О 3СаО·Al2O3·(8-11,6)Н2О 3СаО·Al2O3·3CaSO4·32H2O 4СаО·Al2O3·13Н2О+4СаО·Fе2O3·13Н2О Са(ОН)2 | 500 260 865-895 985-1090 1450 419 1170 |
Реакцияның механизмі мен жылдамдығы уақытқа байланысты өзгереді. Бұны минералдың гидратация кезіндегі жылу бөлу кинетикасы және рентген әдісімен анықталған C3S–тің реакцияға қатыспаған бөлшектерінің саны көрсетілген (8.1-сурет) қисықтан байқауға болады.
Жылу бөлу жылдамдығы, Дж/кг·сағ | ![]() | 8.1-сурет. Үш кальцийлі силикаттың өте майда кристалдарының жылу бөлу жылдамдығымен гидратациялану дәрежесінің өзгеруі: а)гидратация кезіндегі жылу бөлу жылдамдығын көрсетеді: б) гидратациялану дәрежесін көрсетеді; в) гидратация кезіндегі құрылымдардың сызбанұсқасы; 1-C3S-тің бөлшектері; 2-бөлшекті қоршаған гидратты фазалар; 3-қабық астындағы ірі кристалдардың бастамалары; 4-ұсақ бөлшекті гидратты фазалар; 5-қабық сыртындағы ірі кристалдар |
Гидратациялану дәрежесі | ![]() | |
Гидратациялану ұзақтығы, сағ | ||
![]() |
Жылу бөлу кинетикасын көрсететін қисықтағы бірінші шыңы (пик) алит пен C3S-тің сумен өте жылдам әрекеттесетінін көрсетеді. Егер осы қисықты шартты түрде 4 сатыға бөлсек, 1-сатысында минералдың жоғарғы қабатындағы бөлшектері гидратталған қосылыстардың өте жұқа қабығына (пленка) оранады. Осының салдарынан оның ішкі қабатына судың жетуі қиындап, реакцияның жылдамдығы төмендейді. Бұл кез екінші сатысына сәйкес келеді. Бұл тоқырау (индукциялық) кезеңі деп аталады. Реакциясының механизмі де өзгереді, оның жылдамдығы Н2О мен C3S-тің химиялық әрекеттесу жылдамдығымен анықталады. Бұл кезеңде кальций гидросиликаты мен Са(ОН)2 кристалдары пайда болып, өсе бастайды. Кристалдар белгілі бір өлшемге жеткенде жоғары тартылыс энергиясы азайып жұқа қабықтар бұзылады да, кристалдардың ішкі қабатындағы бөлшектері сумен әрекеттесуге мүмкіндік алады. Осы кезден үшінші саты басталады. Бұл кезеңде де реакцияның жылдамдығы су мен минералдаң әрекеттесу жылдамдығымен анықталады және ол өте жоғары болғандықтан процесс тез жүре бастайды. Гидратация процесінің тез жүретіндігі сонша түзілген қосылыстар олардың айналасында жұқа қабықтардың түзілуіне жеткізбей бірден кристалға айналады.
Процестің төртінші сатысында реакцияның жылдамдығы тағы да біртіндеп азая бастайды. Бұның себебі, үшінші сатыда өте көп түзілген кристаллгидраттар енді сумен әрекеттеспеген аздаған бөлшектердің айналасына жиналып, қалың, тығыз қабат түзеді. Сөйтіп, олардың сумен әрекеттесуі тағы да қиындайды.
Алит пен C3S-тің сумен әрекеттесуі нәтижесінде түзілген кальций гидросиликаттарының құрамы қатаю жағдайларына байланысты өзгереді. C3S-тің гидратациясы кезінде ең бірінші 3СаО·SiO2·H2O фазасы түзіледі. Ал 2...6 сағат өткен соң ол келесі сызбанұсқа бойынша ыдырап басқа гидраттар түзіледі.
C3SHx →(0,8-1,5)CaO·SiO2·H2O+CH (8.3)
Екінші кезекте түзілген гидраттар ерітіндіде Ca(OH)2 молекулаларымен қосылып, үшінші кезектегі гидросиликаттарды түзеді:
(0,8-1,5)CaO·SiO2+H2O+Ca(OH)2→(1,5-2)CaO·SiO2·H2O (8.4)
Жоғары негізді үшіншілік кальций гидросиликаттары талшықтар тәрізді кристалданады. Олар сыртқы гидратты қабыршақты құрады, оларды тек микроскоппен ғана көруге болады.
Микроскопта гидратталмаған өзекпен біріншілік гидраттың шекарасы көрінеді, ал біріншілік және екіншілік (ішкі) гидрат, және үшіншілік (сыртқы) гидраттың арасындағы фазааралық шекара практикалық жағдайда көрінбейді (8.2-сурет).
Тұрақты 25 0С температурада C3S гидратациялану дәрежесі әр уақытта әр түрлі болады: 1 тәулікте 25...35 %-ке, 10 тәулікте 55...65 %, 28 тәулікте 78...80 %-ке тең.
Кальций гидросиликаты кристалдарының өлшемі 1 мкм-ден де аз, жалпы меншікті беті 350...450 м2/г тең. Сонымен, судың цементке қатынасы 0,4...0,7-ге (В/Ц 0,4...0,7)-тең болғанда түзілетін кальций гидросиликаттарының құрамындағы СаО-ның SiO2-ге молекулалық қатынасы 1,5...3 тең; кейбір жағдайларда афвиллиттің (C3S2H3) түзілгені де байқалған.
![]() | 8.2-сурет. C3S туйіршегінің сумен гидратациялану схемасы: 1-гидратталмаған өзек; 2-біріншілік гидрат C3SHx; 3-екіншілік майда кристалды гидросиликат (ішкі гидрат); 4-үшіншілік жақсы кристалданған (сыртқы продукт); 5-бөлек ірі кристалдар, дендриттер |
Кальций гидросиликаты кристалдарының морфологиясы, құрамы, майдалығы (дисперстілігі) ерітіндідегі және алит кристалдарындағы бөгде иондарға байланысты. Мысалы, ерітіндіде Ca(OH)2 және С3А-ның болуы C3S-тің гидратациясын баяулатады да, ал CaCl2, басқа да хлорид, бромид, нитрит иондарының, негіздік сульфаттардың, карбонаттардың, гипстің қатысуымен реакция тез жүреді, өйткені жаңа гидраттық фазалар кристалдарының түзілуіне байланысты тоқырау (индукционный) кезеңінің ұзақтығы қысқарады, ал реакция жылдамдығының баяулауы, керісінше осы жаңа гидраттар түзілу процесінің баяулауына байланысты. Al3+, Mg2+, Ba3+, Ti4+ сияқты иондардың C2S кристалл торына енуі де оның гидратациялық белсенділігін арттырады.
C3S-тің сумен әрекеттесуіне температурада әсер етеді. Қалыпты С/К (В/Т) жағдайда C3S-тің гидратациялану дәрежесі 12 сағаттан кейін 5 0С - 0 %, 25 0С – 30 %, 52 0С – 60 % тең болады. Бұл температураны көбейте отырып, C3S-тің гидратациялану дәрежесін арттыруға болатындығын көрсетеді. Реакция өнімдерінің ішіндегі жоғары температуруға төзімділері мыналар:
80-120 120-175 175-200
----→ [C2SH(B); CH] ------→ [C2SH(А); CH] ------→
200
→ [C2SH2; C2SH(А); C3SH(С); CH] ----→ C3SH2 (8.5)
Белит және екі кальцийлі силикаттың гидратациясы. C2S пен оның қатты ерітінділерінің сумен әрекеттесу реакциясы құрамы әр түрлі кальций гидросиликаты және шамамен Ca(OH)2 түзілуімен жүреді.
2(2CaO·SiO2)+3H2O→3,3CaO·SiO2·2,3H2O+0,7Ca(OH)2 (8.6)
Бөлінетін жылудың мөлшері шамамен 250...290 кДж/кг тең. Түзілген кальций гидросиликаттарының химиялық құрамы C2S-тің сумен әрекеттескен уақытына байланысты. Гидратациялану дәрежесінің үлкеюімен бірге кальций гидросиликатының негіздік қасиеті, яғни құрамындағы СаО-ның саны өседі. Температура 80...150 градусқа дейін көтерілгенде, кальцийдің 1,85...2,0 негізді гидросиликаттары түзіледі.
CSH бірінші кристалдары ине тәріздес, олар C2S сумен әрекеттескен бөлшектерінің айналасына жиналады. Бұдан кейін оның табақша тәріздес кристалдары түзіледі. 25 оС-тағы C2S-тің гидратациясы кезінде түзілген гидраттардың меншікті беті 250...350 м2/г тең, бұл C3S-тікінен 100...200 м2/г кем.
C2S-тің сумен әрекеттесу реакциясының жылдамдығы C3S-тің реакциясына қарағанда аз және минерал кристалдарының құрылымына, судағы ерітіндінің құрамына қарай және реакцияның жүру жағдайларына байланысты өзгеріп отырады. Осыған орай C2S гидратациялану дәрежесі 1 тәуліктен кейін 5...10 %, 10 тәуліктен кейін 10...20 %, 28 тәуліктен кейін 30...50 % тең болады, ал қалыпты жағдайда C2S-тің толық гидратациясы 5...6 жылда аяқталады.
Зерттеушілердің айтуы бойынша, синтетикалық жолмен алынған C2S портландцементтің құрамындағы белитке қарағанда сумен жай әрекеттеседі. Егер минералдың құрамында BaO, P2O5, Cr2O3, Fe2O3, Na2O кездесетін болса, бұлар оның гидратациялық белсенділігін арттырады. C2S ерітіндісінің сумен әрекеттесу процесінің күрделілігі, бір жағынан оның әртүрлі жағдайларға тұрақты α, α′, β және γ модификацияларының болуына байланысты. Көптеген зерттеушілердің айтуы бойынша, α, α′, β-C2S-тің гидратациялық белсенділігі жоғары, бірақ біркелкі емес, ал γ-C2S-те төмен. Судағы ерітіндіде еріген кальций сульфаты мен кальций хлоридінің болуы да C2S-тің гидратациясына үлкен әсер етеді, бұл жағдайда реакцияның жылдамдығы жоғары болады.
Кальций алюминатының гидратациясы. С3А сумен әрекеттескен кезде кальцийдің әр түрлі гидроалюминаты, бастапқы кезде 25 0С-тан төмен температурада көбіне
4CaO·Al2O3·19H2O мен 2CaO·Al2O3·8H2O түзіледі.
2(3CaO·Al2O3)+27Н2О=2CaO·Al2O3·8H2O+4CaO·Al2O3·19H2O (8.7)
Бөлінетін жылудың мөлшері түзілген заттың құрамына қарай 865-тен 1000 кДж/кг-ге дейін өзгеріп отырады.
С3А сумен әрекеттескенде оның бөлшектерінің бетінде бірден кальций гидроалюминатының кристалдары түзген борпылдақ қабық пайда болады. Бірақ бұл реакцияның жүруіне кедергі жасамайды, өйткені борпылдақ қабықтан су өтіп, басқа бөлшектермен әрекеттесе алады. Сондықтан С3А-ның гидратациясы басқаларға қарағанда өте тез жүреді және 1 тәуліктен кейін оның гидратациялану дәрежесі 70...80 % тең болады.
С3А гидратациясы мына реакциялар бойынша да жүруі мүмкін:
4(3CaO·Al2O3)+60H2O=3(4CaO·Al2O3·19H2O)+Al2O3·3H2O (8.8)
Бүл реакцияда пластина тәрізді С4АН19 қосылып субмикрокристалды гиббсит Al2O3·3H2O түзіледі, бүл кейін пластиналы минералға өзгереді. Кей бір зерттеулердің мәліметі бойынша біріншілік минерал болып С3АН6 пайда болады:
3CaO·Al2O3 + 6H2O = 3CaO·Al2O3·6H2O (8.9)
Бұл минералдың кристалдары куб сияқты болады, оларда С3А бөлшектерінің бетінде су өткізетін борпылдақ қабық түзеді. 25 0С жоғары температурада алдында түзілген табақша формалы кальций гидроалюминаты тұрақсыз болғандықтан ыдырап, орнына С3АН6 және АН3 минералдары түзіледі.
Судағы еріген SO2-4 иондарының қатысымен бұл реакцияның нәтижесінде кальцийдің гидросульфоалюминаты немесе эттрингит деп аталатын минерал түзіледі (ГСАК-3):
3CaO·Al2O3+3СаSO4+32H2O = 3CaO·Al2O3·3СаSO4·32H2O (8.10)
Эттрингиттің кристалдары ине тәріздес немесе призма тәріздес болып кристалданады. Бүл кристалдар С3А бөлшектерінің айналасында және туйіршектердің аралығындада түзіледі.
Ерітіндіде SO42- иондарының мөлшері төмен болса (эттрингит түзуге жетпесе) онда эттрингит кристалдарымен гидроалюминаттар бір-бірімен әрекеттесіп төмен негізді гидросульфоалюминат түзеді (ГСАК-1):
2(3CaO·Al2O3·6Н2О)+ 3CaO·Al2O3·3СаSO4·32H2O+10H2O =
=3(3CaO·Al2O3·СаSO4·18H2O) (8.11)
Төмен негізді гидросульфоалюминат (ГСАК-1) пластина тәрізді кристалдар түзеді. Ерітіндідегі SO42- иондарының қатысында С3А-ның гидратациялану жылдамдығы азаяды.
Оның гидратациясына ерітіндідегі басқа сульфат, хлорид, нитрит иондар да үлкен әсерін тигізеді, бұлардың көмегімен реакцияның жылдамдығы артады.
Кальций алюмоферритінің гидратациясын былай жазып көрсетуге болады:
4CaO·Al2O3·Fe2O3+13H2O=4CaO·Al2O3·Fe2O3·13H2O (8.12)
4CaO·Al2O3·Fe2O3+13H2O=3CaO(Al,Fe)2O3·6H2O+Ca(OH)2+
+Fe2O3·3H2O (8.13)
C4AҒ-тің гидратациялану жылдамдығы бастапқы кезде үлкен. Оның 3 тәуліктен кейінгі гидратациялану дәрежесі 50...70 % болады. Бұдан кейін C4AҒ бөлшектері жаңадан түзілген кристалгидраттардың жұқа қабығына оранады да, реакцияның жылдамдығы бәсеңдейді.
Егер судағы ерітіндіде Са(ОН)2 мен CaSO4 болса, онда жоғары және төмен сульфатты гидросульфоалюминаттар түзіледі, ал олардың құрамына Fe2O3 қатты ерітінді түрінде енеді.
Клинкердің басқа фазаларының гидратациялануы. Клинкердің құрамындағы байланыспаған CaO, MgO суда еріп Са(ОН)2 (портландит) және Mg(OH)2 (брусит) түзеді. Бұл процесс өте жай жүреді. Түзілген заттардың көлемі бастапқыларға қарағанда үлкен болғандықтан, бұл кейін цемент тасының көлемінің біркелкі өзгермеуіне соқтыруы мүмкін.
Клинкердің шыны тәріздес фазасы сумен әрекеттесіп кальций алюмоферритінің қатты ерітіндісін және гидрогранаттар түзеді.
8.3 Клинкер минералдарының гидратациялық өнімдері
Клинкер минералдары сумен әрекеттесіп құрылымы мен құрамы әр түрлі кальцийдің гидросиликатын, гидроалюминатын, гидроалюмоферритін түзеді.
Кальцийдің гидросиликаттары С2S пен С3S гидратациясы кезінде түзілетін кальцийдің гидросиликаттарының (КГС) құрамы мен кристалдану дәрежесі әр түрлі. Көптеген зерттеушілер цементтегі КГС өзінің құрылымы бойынша табиғи минерал тоберморитке ұқсайтындығын айтады. Тобермориттің құрамы С5S6Н5, ал қарапайым торының өлшемі 11,3 Å тең. Дегенмен, мұндай ұқсастық онша сәйкес келе бермейтіндіктен барлық КГС-ті тоберморит сияқты минералдар деп те атайды. Ал зерттеушілер Д. Джеффри, Х. Тейлор цемент тасының КГС–тарын жақсы кристалданбаған тобермориттерге бөледі: СаО–ның SіО2 қатынасы 1) СаО·SіО2 < 1,5; 2) СаО·SіО2 > 1,5 СSН (ІІ), тоберморит гелі.
СSН (І) құрамында 0,5...2,5 дейін Н2О молекулалары бар, кристалдары көбіне өзгеріске (деформацияға) ұшыраған жұқа табақшалар фольга түрінде кристалданады. Кристалдарының меншікті беті 130...380 м2/г. Егер қыздырса, ол СSН (І) волластонитке айналады.
Екінші гидросиликатты СSН (ІІ) алатын болсақ, бұның құрамындағы кальций тотығының СаО кремний тотығына SіО2 молекулалық қатынасы шамамен 1,5...2 болады, ал судың Н2О 2...4 молекуласы қатынасады. Оның кристалдары талшықтар түрінде кристалданады, кристалл жазықтықтарының аралығы 9,8...10,6 Å; қыздырған кезде β-С2S айналады.
Тоберморит гелі. Кейде оны үшінші гидрат «В фазасы» деп те атайды. Бұндағы СаО-ның SіО2 қатынасы 1,5 тең кейде үлкен (СаО:SіО2 ≥ 1,5) болады.
Гидратация процесінің бірінші сатысында әуелі аз негізді гель түзіледі. Уақыт өтіп, С3S пен С2S гидратациялану дәрежесі артқан сайын, оның негіздік қасиеті де артады. Бұндай өзгеріс оның коллойдты бөлшектерінің құрылымының өзгерісімен, ерітіндідегі Са2+ иондарының адсорбциясымен, кальций гидроксидінің аморфты бөлшектерінің түзілуімен байланысты болуы мүмкін. Осының нәтижесінде гельдің химиялық құрамы мен физикалық құрылымы оның барлық жерінде бірдей бола бермейді. Гельдің бөлшектері, суретте көрсетілгендей әр түрлі формада біріккен массалар құрайды. Бөлшектердің формасы домалақ, құбыршақ, ине, талшық тәрізді болуы мүмкін. Олардың бөлшектері 1,0...0,1 мкм (8.3-сурет).
![]() |
8.3-сурет. Қатайған цемент тасындағы гельді құрылымдардың типтері: Ι-дөнгелек бөлшектер; ΙΙ, ΙΙΙ, ΙУ-құбырлы, чешуйкалы, талшықты бөлшектер; V-цемент тасындағы гель; 1-гельдің бөлшектері; 2-гель көлеміндегі кеуектер |
Егер цементтің гидратациясын жоғары температуралы автоклавта өткізсе, кальцийдің мынадай екі негізді гидросиликаттары: С8S3Н3, С6S3Н, С9S6Н, С5S2Н–А (α–гидрат), С2SН–В (β–гидрат), С2SН–С (γ–гидрат), С3SН (үшкальцийлі гидросиликат) және төменгі негізді гидросиликаттар: С6S6Н (ксонотлит), С4S3Н (фошагит), С3S2Н3 (афвиллит) түзіледі. Бүл гидросиликаттардың кей біреулері автоклавта әкті-құмды бұйымдар қатайғанда пайда болады.
Кальцийдің гидроалюминаттары. Бұлардың ішіндегі ең маңыздылары мыналар: С3АН6, С4АНх, С2АН8, С4А3Н3.
С3АН6 құрамы тұрақты, кристалдары куб немесе октаэдр түрінде кристалданады. С4АНх құрамындағы СаО мен SіО2 тұрақты, ал су молекулаласының мөлшері 7-ден 19 дейін өзгеріп отырады. Бұлар гексагонал табақшалар түрінде кристалданады. С2АН8 және С4А3Н3 минералдары да жұқа гексагоналды табақшалар түрінде кристалданады.
Кальцийдің гидроалюмоферриттері. С4АҒ, С2Ғ және басқа кальцийдің алюмоферриттері сумен әрекеттескенде түзілетін алюмоферриттер С4АН13, С3АН6 құрылымдары жағынан бастапқы заттарға келеді. Олардың қатты ерітінділері 4СаО·(Аl1-х, Ғех)2О3 ·19Н2О гексагональды кристалдар, 3СаО·(Аl1-х, Ғе)2О3·6 Н2О ине тәріздес кристалдар түрінде кристалданады.
Құрамы күрделі қосылыстар. Цемент гидратациясының өнімдері бір – бірімен де реакцияға түсіп, құрамы айнымалы күрделі қосылыстар түзеді. Енді соларды қарастырайық.
Эттрингит немесе кальцийдің жоғары сульфатты гидросульфоалюминаты (3СаО·АІ2О3·СаSO4·(31...32)Н2О оның кристалдары ұзын инелер тәрізді немесе қысқа призмалар тәрізді. Құрамы тұрақты.
Эттрингитке ұқсас кальцийдің жоғары сульфатты гидросульфоферриті деп аталатын қосылыс кездеседі. Оның химиялық формуласы 3СаО·Ғе2О3·3СаSO4·32 H2O.
Кальцийдің аз сульфатты гидросульфоалюминаты 3СаО·АІ2О3 СаSO4·(11...12)Н2О. Бұл да тұрақты қосылыс болып табылады. Кристалдары гексоганальды табақшалар тәрізді. Құрамында темір қатысатын кальцийдің моносульфаты да бар. Құрамы 3СаО·Ғе2О3 СаSO4·12Н2О
Барлық гидросульфоалюминаттарды мынадай қатарға орналастыруға болады:
3СаО·3Са(ОН)2·32Н2О ↔ 3СаО·Аl2О3·3СаSO4·32H2O
↕ ↕
4CaO·Аl2О3·13H2O ↔ 4CaO·Аl2О3 ·SO3 ·12H2O (8.14)
↕
3CaO·Аl2О3·12H2O
Кальцийдің гидрохлоралюминаты ерітіндіде СаСІ2 молекулалары болған кезде ғана түзіледі. Кристалдары ине және табақшалар тәрізді, құрамы мынадай:
3СаО·Аl2О3·3СаСl2·30Н2О және 3СаО·АІ2О3·СаСl2·(10...12)Н2О
Кальцийдің гидрокарбоалюминаты 3СаО·Аl2О3·СаСО3·11Н2О немесе 4СаО·Аl2О3·СО2·11Н2О. Ол цемент қамырына енгізілген кальций карбонаты СаСО3 бөлшектерінің айналасында немесе СО2 газының әсерімен түзіледі.
Кальций гидрогранаттарының қатты ерітінділерінің құрамы тұрақсыз. Олар С3АН6 және С3ҒН6 минералдарындағы су Н2О молекуласының кремний тотығының О2 молекуласымен орын алмасуынан пайда болады. Судың барлық 6 молекуласы да ауысқанда (6Н2О→3SiO2) сусыз гранаттар С3АS3 (гроссуляр), С3Ғ S3 (андратит) түзіледі. Ал бір бөлігі ғана ауысатын болса, онда құрамы келесі формулаға 3СаО(Аl, Ғе)2О3хSіО2(6-2х)Н2О сай қатты ерітінділер тұзіледі. Олардың кристалдарының формасы куб, октаэдр, трапеция тәріздес.
Портландцемент гидратациясы
Жоғарыда біз жекелеген минералдардың гидратациясын қарастырған болатынбыз. Енді олардың цементтің құрамында бәрінің бір уақыттағы сумен әрекеттесуін алатын болсақ, онда олардың әрқайсысының өзіне тән реакциясы жүреді деп айтуға болады. Бірақ бұл тек бастапқы кезде ғана. Өйткені судағы ерітіндіде аталған минералдың құрамындағыдан басқа да иондар кездеседі. Осының нәтижесінде цементтің гидратациясы өте күрделі процесс болып табылады. Кейбір зерттеушілердің тұжырымдаулары бойынша кристалдар әуелі суда еріп, қаныққан ерітінді түзеді, ал кейін бұл ерітіндіден түзілген өнім кристалданады. Бұлар: А. Ле Шателье, П.А. Ребиндер, В.Б. Ратинов, Ю.М. Бутт және т.б. Ғалымдардың екінші тобына А.А. Байков, Д. Джеффри, Х. Функ, В.В. Тимашев және т.б. жатады. Бұлардың айтуынша цемент гидратациясының механизмі топохимиялық механизм болып табылады, яғни кристалдардың тек сыртқы бетіндегі бөлшектері ғана су молекуласын немесе иондарын қосып алып, гидратты бөлшектерге айналады да ерітіндіге өтеді. Сөйтіп, бұл процесс цементтің барлық бөлшектері гидраттанып болғанша қайталанады. Ал ерітінді қаныққан кезде, бөлшектер кристалдана бастайды.
Портландцементтік сумен әрекеттесу (гидратациялану) процесін 3 сатыға бөлуге болады: 1-бастапқы (әуелгі) сатысы, ұзақтығы 1...3 сағат; 2-эттрингиттің түзілуі, ұзақтығы шамамен 24 сағ; 3-соңғы қатаю сатысы. Осы кездегі минералдардың түзілуі төмендегі қисықта көрсетілген (8.4-сурет).
![]() | 8.4-сурет. Цементтің сумен әрекеттесуі нәтижесіндегі гидраттардың түзілу сызбанұсқасы: 1-цемент тасының кеуектілігі; 2-цемент тасының беріктігі; 3-кальцийдің моносульфаты; 4-үшсульфатты кальций гидросульфоалюминаты; 5-кальцийдің қысқа талшықты гидросиликаттары; 6-кальцийдің ұзынталшықты гидросиликаттары; 7-созылмалы цемент қамыры; 8-ұстасып қалған цемент тасы; 9-берік цемент тасының кристалдық құрылымы; 10-қосылыстарының бәрі тұрақтанған цементтасының кристалдық құрылымы |
Минуттар Сағаттар Тәуліктер Гидратациялану уақыты | |
![]() |
Цемент сумен қосылған кезден бастап, оның құрамындағы минералдардың кристалдары суда ери бастайды. Қалыпқа кұйылған цемент қамырының тесіктерінде қалған суда әуелі көп мөлшерде Са2+ иондары, содан соң SО2-4, K+, Nа+ иондары еріп, су осы иондармен қанығады. Кейін бұл ерітіндіге алюминийдің, кремнийдің де аздаған иондары өтеді. Сөйтіп судың иондық құрамы уақыт өткен сайын, гидратациялану дәрежесі артқан сайын өзгеріп отырады. Бұл әсіресе тұтастығыш заттың (цементтің) химиялық минералдық құрамына, ұсақмайдалығына (дисперсность) байланысты. Жекелеген элементтердің судағы мөлшерінің уақыт өткен сайын көбеюі цемент минералдарының біртіндеп еритіндігінен, кейін олар бір-бірімен, бастапқы заттың элементтерімен реакцияға түсетіндіктен азая бастайды. Бұл реакцияның нәтижесінде сулы қосылыстар кристаллогидраттар түзіледі.
Ерітінді С3S-тің гидролизі, яғни суда еріп Са(ОН)2 молекулаларын түзуінің арқасында Са2+ иондарына тез қанығады. Кейбір зерттеушілер судың Са(ОН)2 молекулаларымен шектен тыс қанығуы 10 минуттан 180 минутқа дейін созылады десе, кейбіреулері керісінше айтады. Сол сияқты ерітінді SО42- иондарымен де өте тез қанығады.
Оның себебі, клинкерді ұнтақтаған кезде қосылған гипс (СаSO4·2H2О)суда жақсы ериді. Бұлардың судағы концентрациясы бірдей өзгереді дерлік, өйткені екеуі де эттрингиттің құрамына енеді.
Са(ОН)2 молекулаларының судағы ерігіштігі су, Nа, К иондарымен қаныққан сайын азая бастайды да, ал SіО2-нің ерігіштігі, керісінше артады.
Nа+ мен К+ иондарының саныартқан сайын суда ОН иондарының концентрациясы артып, сутектік көрсеткіші (рН) 11...12-ге тең болады.
Ерітінді шектен тыс қаныққан кезде одан Са(ОН)2 мен эттрингит кристалдана бастайды (8.5-сурет). Кальций гидроксиді тез үлкейетін жұқа гексагональды табақшалар, ал эттрингит өте қаныққан ерітіндіде қысқа-қысқа призмалар, кейін иондардың концентрациясы азайған кезде ұзарған призмалар түрінде кристалданады. В. Лерч, А.Е. Шейкин, Н. Заседателевтердің зерттеулері бойынша, гидратация процесінің жылдамдығы цементтің құрамындағы кальций сульфатына байланысты. SО3-тің мөлшері аздау болса, цементтің жылу бөлу жылдамдығы бірінші кезде жоғары болады. Бірақ түзілген эттрингиттің кристалдары цементтің бөлшектерін қаптап алып, су жібермейді. Осының салдарынан цементтің сумен әрекеттесу процесі бәсеңдейді. Бұнымына 8.5-суреттен көре аласыз.
SО3-тің мөлшері көбейген сайын цементтің жылу бөлу жылдамдығы азайып, жылу бөлу біраз уақытқа созылады. Өйткені, эттрингит кристалдарынан түзілген қабық белгілі бір уақыт өткен соң, бұзылады да, цементтің басқа бөлшектері сумен әрекеттесуге мүмкіндік алады. Осы кезде қайтадан едәуір жылу бөліне бастайды. Суреттегі қисық сызықтардың экстремумдары осыны көрсетеді.
Сумен қосылғаннан бастап шамамен 1 сағ өткен соң өлшемі 0,1мкм болтындай кальцийдің бірінші кезектегі гидросиликаттарының кристалдары түзіле бастайды. Ал кальцийдің талшықты гидросиликаттары эттрингитпен Са(ОН)2-нің кристалдарымен бірге цемент бөлшектерінің айналасында қабық түзеді. Егер бұл гидросиликаттардың кристалдары түтікше тәрізді болса, олар суды жақсы өткізетін борпылдақ қабық түзеді.
Процестің екінші сатысында гидраттар түзіледі.
Процестің тоқырау кезеңі (реакция жылдамдығының бәсендеген, аз уақыты) 1...3 сағатқа созылады. Одан соң эттрингит пен Са(ОН)2 (портландит) өскен кристалдары қабықты бұзып шығып, гидраттар — эттрингит тағы түзіле бастайды.
Жылу бөлу жылдамдығы, Дж/К·сағ | ![]() | 8.5-сурет. Құрамындағы кальций сульфатының мөлшеріне байланысты цементтің жылу бөлу жылдамдығы: 1-құрамындағы SО3 - 1,25 %; 2-құрамындағы SО3 - 2,40 %; 3-құрамындағы SO3 – 3,00 %
|
Гидратациялану мерзімі, сағ |
Басталған 4...6 сағаттан соң гидратациялану процесінің жедел, жылдам сатысы басталады да, жаңадан гидраттар түзіледі. Түзілген гидраттардың сыртында тағы да қабықтар пайда болады, бұрыңғы бұзылған қабықтар жөнделе бастайды. Сөйтіп, эттрингит кристалдарының келесі бұзып шыққанына дейін процесс тағы да баяулайды. Эттрингит кристалдарының қабықтың астында өсіп, оны бұзып шығуы ерітіндідегі SO42- -иондарының концентрациясы азайғанға дейін жалғасады. Эттрингиттің түзілуіне бір тәуліктей уақыт кетеді. Егер осыған сульфат-иоңдардың бәрі жұмсалып, ал ерітіндіде байланыспаған С3АНх гидроалюминаттар қалса, онда бұлармен эттрингит әрекеттесіп, кальцийдің моносульфатын келесі реакция бойынша түзеді.
3СаО·Аl2О3·3СаSO4·31Н2О + 2(3СаО· АІ2O3·13Н2О) →
3(3СаO·Аl2О3 ·СаSO4·12Н2O) + 21H2O (8.15)
Осының нәтижесінде эттрингит азайып, Са(А,Ғ)Н13 қатты ерітіндісі көбейе бастайды. Бұл сатыдағы кальций гидросиликаттарының кристалдары ұзын талшықты болып келеді. Әсіресе бөлшектердің сыртқы қабатындағы кристалдардың формасы оның ішкі, гидраттанбаған ядросына жақын орналасқан қабатындағы кристалдарға қарағанда айқын, жақсы көрінеді. Осы кристалдармен бірге біршама тоберморит гелі түзіледі. Цемент тасының негізгі кристалдық қаңқасы (каркас) осы кезеңде түзіле бастайды (суретті қараңыз). Гидратацияның үшінші сатысы 28 - тәулікке дейін созылады. Процестің жылдамдығы су молекулаларының гидраттанбаған цемент бөлшектерінің ядросын қоршап, біртіндеп тығыздалып, қатайып келе жатқан қабық арқылы диффузиялануына байланысты. Гидратация өнімдерінің құрамы цемент тасының кеуектеріндегі суда еріген иондардың концентрациясы және гидраттардың өзара реакциясының өнімдерімен анықталады. Кальций моносульфатының, портландиттің, кальцийдің гель тәрізді гидросиликатының С4(А,Ғ)Н13 мөлшері көбейіп, эттрингиттікі азаяды.
Портландцемент гидратациясының жылдамдығы. ІІортландцемент гидратациясының жылдамдығы жекелеген минералдардың гидратациялану жылдамдығымен анықталады. Байланысқан суды анықтау әдісін қолдана отырып, Ю.М. Бутт жеке минералдарды олардың гидратациялану дәрежесінің азаюына қарай мынадай қатарға орналастырды: 1) портландцемент гидратациясының бастапқы кезінде: С3А > С4АҒ > С3S > С2S;
2) соңғы кезінде: С3S > С3А > С4АҒ > С2S.
С3А мен С4АҒ минералдары сумен бастапқы кезде жақсы әрекеттесіп, гидраттар түзсе, 3 айдан кейін ең үлкен гидратациялану дәрежесі С3S минералында болады.
Бұл минералдарпортландцементтің құрамында сумен әрекеттескенде әрқайсысы бір-бірінің гидратациялық процесіне үлкен әсерін тигізеді. Сондықтан жоғарыда көрсетілген минералдардың қатары барлық уақытта сақтала бермейді. Егер цемент тек мына 4 тотықтан -СаО, Аl2О3, SiО2, Fе2О3 - тұратын болса, онда С3А > С4АF > С3S > С2S қатары сақталады. Ал егер цементтің құрамында кальций сульфаты (СаSО4) болса, онда С3А-ның гидратациялану процесі баяулап, минералдардың қатары да басқаша болады: С3S (алит) > С3А > С4АF > С2S (белит).
Цемент гидратациялану реакциясының кинетикасы су молекулалары мен онда еріген иондардың гидраттанбаған ядросын қоршаған реакция өлшемдері — гидраттанған бөлшектерден тұратын қабық арқылы диффузияланумен анықталады.
8.5 Беріктігі жоғары цементті синтездеу
Егер клинкер минералдарының әрқайсысынан жеке үлгілер жасап, олардың қатаю кезіндегі беріктігін тексерсе, келесі жәйлерді көруге болады.
8.6-суретте көрсетілгендей қатаю процесінің бастапқы кезінде ең жоғары беріктікті С3S минералынан жасалған үлгілер көрсетеді, ал ең төмен беріктік С2S-тің үлгілерінде. С3А-дан жасалған мономинералды тастың қатаю процесінің соңғы кезінде ешқандай беріктігі болмайды десе де болады. С4АҒ минералынан жасалған үлгінің беріктігі С3А минералы үлгісінің беріктігінен үлкен, С3S- минералы үлгісінің беріктігінен кіші. Енді осы үлгілердің беріктігін 6 айдан кейін тексергенде, С2S-тен жасалған үлгінің беріктігі басқаларға қарағанда өте жоғары екендігі байқалған.
Қысымға беріктігі МПа | ![]() | Гидратацияланған заттың салмағы, % | ![]() |
Қатаю ұзақтығы, тәул | Қысымға төзімділігі, МПа | ||
8.6-сурет. Мономинералды тастар беріктігінің уақытқа байланысты өсуі | 8.7-сурет. Цементтің гидратациялану дәрежесінің цемент тасының беріктігіне тигізетін әсері |
Цемент тасының беріктігі оның физикалық құрылымымен анықталады, яғни гидратталған қатты фазаларының концентрациясына (8.7-сурет) және материалдың кеуектілігіне (8.8-сурет) байланысты. Бұны келесі суреттердегі қисықтардан көруге болады.
Көптеген зерттеушілер бір-біріне жақын, туыс минералдардан олардың гидратациялану дәрежесі бірдей болған кезде, беріктігі де бірдей цемент тастарын алуға болатынын дәлелдеген. Мәселен, Ф. Лоуренс С3S пен С2S қамырынан жасалған үлгілердің созған кезде анықталған беріктігінің бірдей екендігін көрсетті.
С3S пен С2S-тің гидратациялану дәрежесі бірдей болған. Бұндай көрсеткіштерді құрамындағы гидраттарының көлемдік концентрациясы бірдей цемент тастарын зерттеу кезінде де алған.
Гидратациялану дәрежесімен қатар цементтің беріктігіне оның кеуектілігі де үлкен әсер етеді; кеуектілігі артқан сайын цемент тасының беріктігі кеми береді.
Қасиеттерінің өзгеруі | ![]() | 8.8-сурет. Цемент қамыры мен цемент тасы қасиеттерінің қатаю процесі кезінде өзгеруі:1-цемент тасының беріктігі; 2-су тегі көрсеткішінің (рН) мәні; 3-гидратациялану дәрежесі; 4-температурасы және жылу бөлгіштігі; 5-электр тогын өткізгіштік қабілеті; 6-кеуектілігі |
Минут Сағаттар Тәуліктер Жыл Қатаю ұзақтығы |
Цемент тасының беріктігіне құрамындағы гидраттардың кристалданып, кеуектерді толтыру қабілетінің де әсері аз емес. Гидрат кристалдары үлкейіп, кристалдану дәрежесі артқан сайын бұл кристалдардың саны да, бір-бірімен жанасуы да азаяды. Осының салдарынан цемент тасының беріктігі кеми бастайды.
Сонымен, цемент тасының беріктігі оның кеуектілігіне, құрамындағы гидраттарға, олардың кристалдану дәрежесіне, яғни температураға, әр түрлі қоспаларға, цемент бөлшектерінің майдалығына байланысты.
8.6 Кейбір технологиялық факторлардың цемент гидратациясына тигізетін әсері
Клинкердің кристалдық құрамы мен минералдық әсері.
Портландцементтің гидратациясы құрамында С3S неғұрлым көп болса, соғұрлым тез жүреді. Бірақ С3S-тің цемент құрамыдағы мөлшері 65...75 %-тей ғана болады, өйткені алитті цементтің бір жылдан кейінгі беріктігі белитті цементтің беріктігінен едәуір аз. С3А-ның цемент құрамындағы саны 14...16 %-тей болса, эттрингит пен кальцийдің гидросиликаттары тез түзіледі. Бұл алғашқы кезде цемент беріктігін арттырады. Кальцийдің алюмоферриті цемент гидратациясына айтарлықтай әсер етпейді.
Цемент құрамындағы сілтілік фазалар (Nа2SО4, К2SО4, NС8А3, КС8A3) цемент тасының бастапқы беріктігін арттыратын кальцийдің төмен негізді гидросиликаттарын түзуге мүмкіндік жасайды. Бірақ бұлар уақыт өткен сайын керісінше әсер етуі мүмкін, яғни цемент тасының беріктігін азайтуға әкеліп соқтыруы мүмкін. Өйткені, төмен негізді силикаттар жоғары негізді силикаттарға айналып, қайтадан кристалданады. Бұл цемент тасының қалыптасып келе жатқан физикалық құрылымын өзгерістерге ұшыратады. Осының салдарынан цемент тасының беріктігі кемиді.
Цемент құрамындағы оның ұстасу мерзімін реттеу мақсатымен енгізілген кальций сульфаты да оның беріктігін арттыруға едәуір жағдай жасайды. Себебі, кальций сульфатының қатысуымен С3S-тің гидратациялану жылдамдығы жоғарылап, эттрингит кристалдарын түзеді.
Технологиялық регламент бойынша СаО-ның цементтегі саны 1...2 %-тен аспауы керек. Олай болмаған күнде ол цемент тасының ұзарып ұлғаюына, ақыр соңында толық бұзылуына әкеп соғуы мүмкін. Бұндай жағдайды төменде келтірілген қисықтан да көруге болады (8.9-сурет). Байланыспаған СаО жоғарылағанда цемент тасы 3...4 %-ке ұлғаяды.
Портландцементтің құрамында кездесетін Р2О5, Сг2О3 мөлшері 0,2...0,5 %, ВаО, ТіО2, Мn2О3 тотықтарының 0,5...2 %-тей мөлшерде болуы да цементтің гидратациялану процесінің жылдамдығы мен цемент тасының беріктігін арттырады.
Гидратация процесінің барысына клинкердің алыну жағдайлары да ықпалын тигізеді. Клинкер пештегі газдың тотықтырғыш немесе тотықсыздандырғыш жағдайларында алынуы мүмкін. Тотықсыздандырғыш жағдайында алынған клинкердің құрамындағы алит пен С4АҒ-тің кристалдарының түрі өзгерген, бүлінген. Бұл цементтің гидратациялану белсенділігін төмендетеді.
Цементтің гидратациясы клинкердің салқындау жағдайына да байланысты. Беріктігі жоғары цемент алу үшін клинкерді 1200...1250 0С-қа дейін баяу салқындатып, кейін 80...100 °С-қа дейін арнайы салқындатқыштардың көмегімен өте тез салқындатады. Сөйтіп, цемент тасының жоғары беріктігін қамтамасыз ететін минералдардың түзілуіне жағдай жасайды.
Цемент түйіршіктерінің әсері. 8.10-суретте цемент түйірлерінің майдалығының гидратацияға тигізетін әсері көрсетілген.
Цемент түйіршіктері неғұрлым майда болған сайын, соғұрлым гидратация процесі жақсы жүреді. Мәселен, өлшемдері 0...5 мкм-дей түйіршіктерден тұратын цементтің сумен әрекеттескеннен 24 сағат өткендегі беріктігі 70...80%болады. Ал өлшемдері 5...10, 10...20, 20...60 мкм түйіршіктерден тұратын цементтер баяу қатаяды. Біртәуліктегі беріктігі алдыңғымен салыстырғанда аз. Бірақ кейін олар ең жоғары беріктікке ие болады, яғни, түйіршіктері іріленген сайын цемент тасының қатаюы баяулайды. Соған байланысты оның жоғары беріктігі де кешірек қалыптасады.
Ұлғаюы, мм/м | ![]() | Қысымға беріктігі, МПа | ![]() |
Байланыспаған СаО, % | Қатаю ұзақтығы, тәул | ||
8.9-сурет. Байланыспаған кальций тотығының цемент тасының қатаюына тигізетін әсері | 8.10-сурет. Түйірлері әртүрлі цементтердің қатаю процесінің кинетикасы: 1 –3 мкм-ден де аз; 2 – 3-9 мкм; 3 – 9-25 мкм; 4 – 25-50 мкм |
Өлшемі 0...5 мкм фракция цементтің 1 тәуліктегі, 7...30 мкм (негізгі фракция) – 28 тәуліктегі беріктікті қамтамасыз етеді. Фракция 30...60 мкм 28 тәуліктен кейін гидратацияланады, ал фракция 60...200 мкм ұзақ ұақыт қатайып цемент тасының тығыздығын қамтамасыз етеді.
Осы жағынан алғанда түйіршіктер өлшемдерінің ең тиімдісі 0...30 мкм. Осындай түйіршікті цементтің сапасы ең жоғары болады. Түйіршіктері майдаланған сайын цементтің гидратациялық белсенділігінің артуы майда түйіршіктердің меншікті бетінің үлкендігінің және олардың кристалдық құрылымдарының өзгеріске ұшырап, яғни ақауға толы болатындығының нәтижесі. Өте майда түйіршікті цементтен алынған цемент тасының беріктігі басқаларға қарағанда аздау, өйткені бұндай цементтің физикалық құрылымы борпылдақ, үгілмелі болады, түзілген гидраттар, цемент гелі жақсы кристалданбайды. Ал ірі түйіршікті цементтің кейін тығыз, берік цемент тасына айналуының себебі, гидратация жай жүріп, су еріген иондарға аз қанығатындықтан СSН түзіледі. Сосын СSН-тың ине, талшық тәрізді кристалдары цемент гелімен қосылып кристалдар құрылымын тығыздай түседі (8.11-сурет).
![]() | ![]() |
8.11-сурет. Қатайған цементтегі СSН-фазалар |
Қорыта келе айтқанда, тез қатаятын беріктігі жоғары цемент тасын алуүшін цементтің минералдық құрамына (түйіршіктерінің өлшемдеріне) аса назар аударған жөн.
Температураның әсері. Температура жоғарылаған сайын цемент гидратациясының жылдамдығы да, жылу бөліп шығару жылдамдығы да артады. Осының нәтижесінде, жоғары температурада алынған цемент тасының беріктігі қалыпты жағдайда қатайған цемент тасының беріктігіне қарағанда тез өседі. Жоғары температурада минералдардың гидратациясының механизмі де, түзілетін гидраттардың құрамы да өзгермейді. Өзгерістер қатайған цемент тасының кристалл құрылымында байқалады. Өйткені жоғары температурада гидратациялану жағдайында реакция өнімдері гидраттардың кристалдану дәрежесі жоғары. Мәселен, температураны 95 0С-қа дейін көтергенде гидратация нәтижесінде түзілген тоберморит гелі жақсы кристалданған қосылыстарға айналады, кальций гидроксидінің Са(ОН)2 ірі кристалдары түзіледі.
Сол себепті бетондар мен цементтен алынған басқа да бұйымдардың қатаюын тездету үшін практикада булау, буға ұстау және автоклавта жоғары қысымның көмегімен қатайту әдістерін кеңінен қолданады.
Химиялық қоспалардың әсері. Судың құрамында аз мөлшерде болса да басқа еріген заттардың болуы цемент гидратациясы жылдамдығының өзгеруіне, түзілген кристалл гидраттардың құрамының өзгеруіне, қатайып келе жатқан цемент тасынан судың буға айналу процесінің өзгеруіне әкеліп соғуы мүмкін. Барлық химиялық қосылыстардың қоспалардың көмегімен цемент қамырының қатаю процесінің ұстасу процесінің барысын өзгертуге (тездетуге немесе баяулатуға), цемент тасының кристалдық құрылымын өзгертуге, кеуектілігін өзгертуге, азайтуға, цементтен алынатын бұйымдардың құрылыс-техникалық қасиеттерін реттеуге болады. В.Б. Ратинов, Ф. Вавржин, У.А. Аяпов, К.К. Карибаев және басқалардың жүргізген зерттеулерінің нәтижесінде барлық химиялық қоспалар өздерінің тигізетін әсеріне қарай жеке топтарға, кластарға бөлінген.
Бақылау сұрақтары.
1. Минерал кристалдары сумен жанасқан кезде қандай процестер жүреді? 2. Минерал кристалдарының сумен әрекеттесу механизмі қандай? 3. Минералдардың гидратациясының реакцияларын жазыңыз. 4. Алит және белит гидратацияланғанда қандай гидросиликаттар пайда болады? 5. Алит және белит минералдардың гидратациялық өнімдерінің құрылымы қандай? 6. Минералдардың гидратациялық жылдамдығы қандай? 7. Температура т.б. факторлар гидратацияға қандай әсер етеді? 8. Алюминаттар және алюмоферриттер қандай гидраттар құрады? 9. Кальций гидросульфоалюминаттарының құрамы және құрылымы қандай? 10. Химиялық қоспалардың цемент гидратациясына әсері қандай? 11. Түйірлері әртүрлі цементтердің қатаю процесінің кинетикасы қандай? 12. Портландцементтің гидратациясы қалай жүреді?
ІХ тарау
ЦЕМЕНТ ТАСЫ МЕН БЕТОННЫҢ КОРРОЗИЯСЫ
Бетон немесе цементтен алынған басқа да бұйымдар уақыт өте келе коррозияға ұшырайды, яғни сыртқы қоршаған ортаның әсерінен бүліне бастайды. Бетонның коррозиясын туғызатын себептер ішкі және сыртқы болып бөлінеді.
Бетонның коррозиясын тудыратын ішкі себептер - оның су өткізгіштігі, цемент құрамындағы сілтілердің толықтырушылар құрамындағы кремнеземмен (кремний тотығы SіO2) реакцияға түсіп, бұл екеуінің температуралық ұлғаюының бірдей болмауы.
Коррозияның сыртқы себептеріне төмендегілер жатады: өзен, теңіз суларының бетонды үнемі шайып, жуып тұруы және судың қысымы; өндірістік және тұрмыстық ағын сулардың әсері; температураның жыл мезгілдерінде және күнделікті ауысып тұруы - жылу алмасуы; бетондардың бір ылғалданып, бір кебуі: механикалық құбылыстардың әсері - толқындардың ұруы, жел қағу, қажалуы, биологиялық бактериялардың әсері.
Бетонның бүлінуінің сыртқы себептерін физикалық және химиялық деп те бөледі.
9.1 Физикалық коррозия
Физикалық коррозия көбіне қоршаған ортаның температурасы мен ылғалдылығының өзгеріп отыруынан, бетонның кеуектерінде, капиллярларында әр түрлі тұздардың жиналып, кристалдануынан туындайды.
Мәселен, теңіз құрылыстарында пайдаланылған бетонға температура мен тұздардың ерітіндісі бірдей әсер етеді. Бетон кеуексіз болмайды, aл теңіз жағдайында төмен температурада кеуектерге жиналған су қатып, көлемі ұлғая бастайды. Қатқан кезде судың көлемі шамамен 9 % үлкейеді. Сөйтіп кеуектер мен капиллярлардың қабырғаларын гидравликалық қысымның күшімен бүлдіріп бұза бастайды. Қатып калған су бөлшектері бөлініп шығады. Сол себепті ерітіндідегі тұздар концентрациясы үлкейеді де, осының нәтижесінде пайда болған осмостық қысым бетонның бұзылуына әкеледі Зерттеушілердің, айтуы бойынша осмостық қысымның мәні 1...2 МПа болады. Атмосферадағы үнемі жылу алмасу бетонның құрылымын босаңсытып, беріктігін төмендетеді, ал оның ұлғайтушы қысымы (давление расширения) оның соңғы созылу беріктігінен асып кеткенде бетон толық бұзылады. Бетон коррозиясына оның кеуектілігінің де әсері аз емес. Өте майда кеуектердегі су - 80 °С-тан төмен температурада ғана қатады, сондықтан олар онша қауіпті емес. Бетон және цементтен жасалған бұйымдар үшін ең қатерлілері - капиллярлар, үлкенірек кеуектер. Бұйымдардың кеуектілігін азайта отырып, олардың аязға төзімділігін арттыруға болады. Кеуектілікті бетонның су қабылдағыштығын, су цемент қатынасын азайту арқылы, әр түрлі пластификаторлар, гидрофоб қоспалар, ауаны тартып алатын қоспаларды пайдалану арқылы азайтуға болады.
Қарапайым цементтен алынған бетон жоғары температурада шыдамсыз. 150...200 0С әуелі гидраттары бүлініп, 500 0C жоғары қарай бетон толық бұзылады. Соңдықтан оларды 250 ОС жоғары температурада қолданбайды.
Бетонның жоғары температураға яғни ыстыққа төзімділігін арттыру үшін шамот, туф, трепел сияқты қоспалар қосады. Бұларды цементтің 1 салмақтық бөлшегіне олардың 0,5...2 салмақтық бөлшегі сәйкес келетіндей етіп қосады. Бұл қоспалар 800 0С-тан жоғары температурада цемент құрамындағы CaO, Ca(OH)2, CaСО3 қосылыстармен әрекеттесіп, ыстыққа, судың әсеріне төзімді қосылыстар түзеді.
Атмосфералық температураның, ауа райының өзгеруінен бетонның біресе ылғалданып, біресе кеуіп қалуы, көлемнің өзгеруіне, ісінуіне немесе шөгуіне - әкеп соқтырады. Бетонның ісінуін сызықтық ісіну коэффициенті арқылы, ал шөгуін сызықтық шөгу коэффициенті арқылы анықтайды. Бұл екі коэффициенттің өлшем бірліктері бірдей: мм/мм немесе г/г. Коэффициенттер бетонның бір қалыпты кеуіп немесе бір қалыпты ылғанданған, дымқылданған кезінде оның салыстырмалы салмақтың ылғалдылығының қалай өзгеретіндігін көрсетеді. Олардың орташа мәні 0,03, 0,005 мм/мм тең.
Бетонның бұндай көлемдік өзгерістерін әр түрлі толықтырғыштар қолдану арқылы болдырмауға болады.
Бетон кеуектерінде жиналған судың кұрамындағы тұздардың кристалдануы да қауіпті. Әсіресе ауа райы ыстық, әрі құрғақ болса, кеуектердегі су үнемі буға айналып ұшып кетеді де, оның кұрамындағы Na2SO4, Nа2СО3, MgSO4 сияқты тұздар қалып қояды. Сөйтіп олардың кристалдануының әсерінен кеуектер мен капилляр тесіктердің қабырғалары бұзыла бастайды. Сондықтан барлық уақытта бетонның кеуектілігін азайтуға, сыртқа қараған ашық кеуектерін болдырмауға тырысады.
9.2 Химиялық коррозия
Сулы ортаның, газдың бетонға, цемент тасына тигізетін әсері химиялық коррозия болып табылады. Өйткені су және суда еріген қышқылдар, тұздар, негіздер бетонның, цемент тасының бөлшектерімен химиялық жолмен әрекеттеседі. Осының салдарынан бетон біртіндеп бұзыла бастайды. Бетонның химиялық коррозиясын В.М. Москвин үш түрге бөледі: 1) кермектігі аз судың әсерінен болатын коррозия; цемент тасының бөлшектері суда еріп, бірге ағып кетеді; 2) цемент тасы мен су бөлшектерінің реакцияға түсіп, ерігіш немесе тұтастырғыш қасиеті жоқ заттар түзуінің әсерінен болған коррозия; цемент тасының кристалдық құрылымы бұзылады; 3) цемент тасының, бетонның кеуектерінде, капилляр тесіктерінде, жарықтарында тұздар жиналып, олардың кристалдануынан пайда болатын коррозия (тұздар коррозиясы).
Бетон құрамындағы әктің суда біртіндеп еріп, шайылып кетуі ерітіп ажырату коррозиясы деп аталады. Цемент тасының құрамындағы гидросиликаттар, алюминаттар, ферриттер, сульфоалюминаттар суда біраз ерігіш келеді. Мысалы, Са(ОН)2-нің ерігіштігі 1,3 г/л тең. Ағын су бетонның кеуектеріне, капиллярларына, жарықтарына кіріп кальций гидроксидін ерітеді. Ал еріген кальций гидроксидінің бөлшектері сумен бірге шайылып, ағып кетеді. Осының салдарынан кеуектердегі сұйықтық пен цемент құрамдастарының арасындағы химиялық тепе-теңдік бұзылады, бетон бүліне бастайды. Бетонның ерітіп ажырату коррозиясына мына төмендегі жағдайлар септігін тигізеді. Олар цемент құрамындағы жоғарыда аталған қосылыстардың еру жылдамдығы, судың жылдамдығы, цемент тасының химиялык және минералдық құрамы, бетонның тығыздығы, судың химиялық құрамының белсенділігі, бетонның қолдану жағдайлары. Кей кезде судың пайдасы да тиюі мүмкін. Мәселен, мына реакция Са(ОН)2 + Са(НСО3)2 = 2СаСО3+2Н2О бойынша түзілген кальций карбонаты бетонның кеуектерінде жиналып, оның тығыздығын арттыра түседі. Судың белсенділігі оның гидрокарбонатты (уақытша) қатаңдығына байланысты. Оның өлшем бірлігі мг-экв/л. Сондықтан агрессивті су әсер ететін жағдайларда гидравликалық қоспасы бар цементті, өте тығыз бетондарды қолданады. Мысалы, пуццоланды цементінен алынған бетон су өткізбейді. Өйткені құрамындағы белсенді кремнезем кальций тотығымен қосылып, суда ерімейтін гидросиликаттар түзеді.
Сульфатты коррозия. Жер асты суларында еріген сульфаттар бетонның құрамындағы кальцийдің гидроксидімен, гидроалюминатымен реакцияга түсіп, көлемі бастапқылардікіне (Са(ОН)2, С3АНх) қарағанда үлкен қосылыстар түзеді. Осының салдарынан бетон ісініп, кейбір жерлері қисайып, бұзыла бастайды. Мысалы,
Ca(OH)2+Na2SO4∙10H2O → CaSO4∙2H2O+2NaOH+ 8H2O (9.1)
Реакциядан түзілген кальций сульфаты, судың құрамындағы натрий сульфаты гидроалюминаттармен қосылып, кальцидің гидросульфоалюминатын түзеді 3CaО·Аl2O3∙3CаSO4∙31H2O. Ал бұның көлемі гидроалюминаттардың көлемінен 2 еседей үлкен. Бетонды бұзылуға әкеп соғатын ішкі кернеу күштері осындайдан пайда болады.
Гидросульфоалюминаттар гипспен сылаған жерде де пайда болуы мүмкін. Көбіне сульфатты коррозиясына теңіз су құрылыстарына пайдаланған бетон бұйымдар ұшырайды. Өйткені, теңіз суларындағы сульфаттың концентрациясы SO42- ионымен есептегенде шамамен 2,7 г/л тең. Теңіз суының әсерімен келесі реакция жүреді
MgSO4 + Ca(OH)2 + 2H2O → Mg(OH)2 + CaSO4∙2H2O (9.2)
Бұндағы пайда болған гипс кальцийдің гидроалюминаттарымен қосылып, тағы да гидросульфоалюминаттар түзеді, кристалдану нәтижесінде бетон бұзылады. Бірақ теңіз суында сульфаттардан басқа еріген хлорлы тұздар да болады. Ал хлорды ерітіндіде гипс пен гидросульфоалюминат жақсы ериді. Осының арқасында гидросульфоалюминат пен гипс хлорлы ерітіндіде еріп кристалдануға үлгермей шайылып кетеді. Сол себептен бетонның көлемі ұлғаймайды.
Сульфатты коррозия кезінде бетонның бұзылу себебі тек кристалданудың физикалық күшімен емес, осмотикалық күштермен байланысты болуы мүмкін. Ол гельдің ісініп және шөгуімен байланысты болады. Цементтің сульфатқа төзімділігін жоғарылату үшін тек кальций алюминаттарын төмендетпей, бетонның кеуектеріндегі сұйықтың осмотикалық қысымын төмендетсе де болады. Ол үшін цементтің гидратациялануының ерте кезеңінде Са(ОН)2 мөлшерін төмендету керек, оны басқа қосылыстарға байланыстыру қажет.
Сульфатты коррозия кезінде агрессивті ортаның агрессивтілік санының мөлшері ол судың құрамындағы Cl иондарын есептей отырып SO42- ионының саны. Теңіз суларының белсенділігі ондағы сульфат SO42- және Сl- иондарының концентрациясымен анықталады.
Цементтердің сульфатқа төзімділігін құрамында алюминаттың санын азайту арқылы арттырады.
Магнезиалды коррозия. Суда еріген барлық магний тұздары бетон құрамындағы кальций гидроксидімен қосылып, магний гидроксидін және суда еритін кальций тұзын түзеді. Магний гидроксидінің тұтастырғыш қасиеті жоқ. Хлорлы магний кальций гидроксидімен келесі реакция бойынша әрекеттеседі:
MgCl2 + Ca(OH)2 → CaCl2 + Mg(OH)2 (9.3)
Бұл әрекеттесу нәтижесінде бетон бұзылады. Магний гидроксидінің ерігіштігі өте аз, ерімейді десе де болады. Сондықтан ол өте қауіпті болып саналады, өйткені реакция аяғына дейін, цементтің құрамындағы барлық Са(ОН)2 таусылғанша жүреді.
Магнезиалды коррозиясы кезінде судың белсенділігі құрамындағы Mg2+ және SO42- иондарының санымен өлшенеді.
Бетонның сульфатты және магнезиалды коррозияға төзімділігін жоғарылату үшін цемент құрамындағы үшкальцийлы алюминатты төмендету керек, үшкальцийлы силикаттың мөлшері де жоғары болмауы керек. Себебі ол гидратацияланғанда көп мөлшерде Са(ОН)2 бөлінеді, бүл гидроксид агрессивті ортамен тез әрекеттеседі. Сол үшін тағыда бетонның тығыздығын жоғарылату керек.
Қышқылдық коррозия. Қышқылдық коррозия қышқылдардың әсерінен туындайды. Қышқылдар да цемент құрамдастарымен сумен шайылып кететін ерігіш тұздар түзеді. Кышқылдар коррозиясына ұшыраған бетонның бүліну жылдамдығы реакцияның нәтижесінде түзілетін өнімдердің ерігіштігіне байланысты. Судың белсенділігі сутек көрсеткішімен (СК) анықталады. Егер СК 6 болса, онда судың бетонға тигізетін әсері үлкен деп саналады. Портландцементтер қышқылға төзімсіз. Олардан жасалған бетонды бұзу үшін кез-келген қышқылдың (азот, күкірт, тұз қышқылдары) 1 %-тік судағы ерітіндісі жетіп жатыр.
Көмір қышқылдық коррозия қышқылдық коррозияға жатады.
СО2
Ca(OH)2 → CaCO3 + H2O (9.4)
Судағы еріген көмір қышқыл газы кальций гидроксидімен қосылып, кальций карбонатын түзеді. Кейін СаСО3 суда еріп, бетонды ерітіп ажырату коррозиясына ұшыратуы мүмкін.
Бұндай коррозияға пуццоланды, глиноземді цементтер төзімді. Сондай-ақ бетонға 25 % ұсақ әктасты қосу арқылы да көмір қышқылдық коррозияны болдырмауға, болмаса оның әсерін әлсіретуге болады.
Органикалық қышқылдардың ішінен бетонға өте қауіптілері сүт және сірке қышқылдары.
Бақылау сұрақтары.
1 Коррозияның сыртқы себептеріне не жатады?2. Цемент тасының, бетонның физикалық коррозиясы қалай жүреді? 3. Бетонға жоғары температураның әсері қандай? 4. Бетонның кеуектілігі оның төзімділігіне әсері қандай? 5. Бетонның химиялық коррозиясын В.М. Москвин қандай түрлерге бөледі? 6. Химиялық коррозияның зияндығы қандай? 7. Сульфатты коррозия кезінде қандай реакциялар жүреді? 8. Қышқылдық коррозия кезінде қандай реакциялар жүреді? 9. Магнезиалды коррозия кезінде қандай реакциялар жүреді? 10. Цемент пен бетонның коррозияға төзімділігін қалай жоғарылатуға болады? 11. Бетонның коррозиясын тудыратын ішкі себептері қандай?
X тарау
ПОРТЛАНДЦЕМЕНТТІҢ ҚҰРЫЛЫС - ТЕХНИКАЛЫҚ ҚАСИЕТТЕРІ
Цемент қамырының, цемент ерітінділерінің, бетон қоспаларының, олардан жасалған бұйымдардың өздеріне ғана тән құрылыс-техникалық қасиеттері болады. Әйтсе де бұларға цемент қасиеттерінің тигізетін әсері зор. Олар: цементтің минералдық құрамы, ұнтақтылығы, түйіршіктерінің майдалылығы, көлемінің бір қалыпты өзгеруі. Бетон қоспаларына тән қасиеттер - оның өміршеңдігі, ұстасу мерзімдері, қалып құюға ыңғайлылығы, қалыпты қоюлығы, су қабылдағыштығы. Цементтен істелген бұйымдардың қасиеттеріне беріктігі, шөгуі, ісінуі, су өткізбейтін қабілеті, жарықтарға бой алдырмауы, ұзақ уақытқа шыдауы, жылжымалылығы, ығыспалылығы жатады.
Цемент тасының беріктігі. Цемент тасының ең маңызды қасиеті болып оның механикалық беріктігі саналады. Цемент тасының механикалық беріктігі қысымға беріктігі, майыстырған кездегі беріктігі, созылған кездегі беріктігі болып үшке бөлінеді. Цементтің қасиеттері және тасының сыналу жолдары МСТ 10178-85 көрсетілген. Портландцементті беріктігі бойынша 400, 500, 550, 600 маркалы портландцементтер деп бөледі. Шлакопортландцементтің маркалары 300, 400, 500.
Цементің белсенділігі деп оның қысымға беpіктігін айтады. Оны цемент сумен араласып, қатая бастағаннан 28 тәулік өткен соң анықтайды. Өндірістерде цементтің белсенділігін арнайы жедел әдіспен 16...18 сағ өткеннен кейін-ақ анықтай береді.
Цементтің белсенділігіне, яғни қысымға беріктігіне оның минералдық құрамы үлкен әсер етеді. Үшкальцийлі силикат цементтің қатаю жылдамдығына, 28 тәуліктен кейінгі беріктігіне өте көп ықпалын тигізеді. Екі кальцийлі силикат жай қатайғанымен, оның бір жылдан кейінгі беріктігі өте жоғары болады. Үш кальцийлі алюминат пен төрткальцийлі алюмоферрит цемент беріктігінің бастапқы кезде тeз өсуін қамтамасыз етеді, кейін олардың айтарлықтай әсері жоқ. Егер цементтің 28 тәуліктен кейінгі беріктігін 1 бүтінге баласақ, онда 3 тәуліктен кейін беріктігі 0,36, 7 тәуліктен кейін — 0,65, 1 жылдан кейін 1,5, 25 — жылда — 2,25 болады.
Цементтің беріктігіне су цемент қатынасы да әсер етеді. Осы қатынас неғұрлым аз болса, цементтің беріктігі соғұрлым жоғары болады. Өйткені, судың қажетті мөлшерден көп болуы цементтің кеуектілігін арттырады. Ал кеуектілігі артса, тығыздыгы кемиді, онымен бірге беріктігі де кемиді. Цементтің ұнтақтығы електен өткізгенде електе өтпей қалған калдығымен немесе меншікті бетімен өлшенеді. Бұлардың бәрі МСТ 10178-85 көрсетілген. Мысалы, портландцементтің № 008 електе қалған қалдығы 15 %-тен аспауы керек. Меншікті беті 300...350 м2/кг. Егер оны 400...450 м2/кг дейін көтерсе, тез қатаятын цемент алуға болады. Бірақ ұнтақ болған сайын цемент су қабылдағыш келеді, әрі ауада белсенділігін жоғалта бастайды.
Цементтің белсенділігіне оның гранулометриялық құрамы, яғни түйіршіктерінің өлшемдері де әсерін тигізеді. Түйіршіктерінің өлшемі әр түрлі цементтен тығыз цемент тасын алуға болады.
Цементтің беріктігі қоймаларда сақталу жағдайларына да байланысты. Себебі, ауаның құрамындағы көмір қышқыл газы СО2 мен су буы цемент бөлшектерімен әрекеттесе бастайды. Мысалы, тез қатаятын цементті қоймада 1 ай сақтаса, ол кәдімгі цементке айналады. Осындайларды болдырмау үшін цементке 0,25 %-тей асидол-мылонафт, амин қышқылын, т.б. гидрофобты қоспаларын қосады.
Цемент қамырының қалыпты қоюлығы оның маңызды қасиеттерінің бірі болып табылады. Бұны Тетмайер кежабының (пестик Тетмайера) көмегімен Вик құрылғысында анықтайды. Цемент қамырының қалыпты қоюлығының көмегімен тиімді су-цемент қатынасын табады.
Цементке қажетті су дегеніміз қоюлығы қалыпты цемент қамырын алуға қажетті су мөлшері. Портландцементке қажетті судың мөлшері 24...28 %-тей.
Цементтердің суды қажет етуі оның минералдық құрамына, ұнтақтығына, құрамындағы қоспалардың түріне байланысты. Цемент ұнтақ болған сайын суды көп қажет етеді.
Цемент қамыры қоюланып, жылжымалылық, қозғалғыштық қасиетін жоғалта бастағанда оны ұстаса бастады деп айтады (начало схватывания). Цемент қамырынан ұстаса бастаған кезде қалыптар құю қиындай бастайды, ал ұстасып қалған соң тіпті мүмкін емес. Сондықтан, қалыпқа құйып болмай жатып қатып қалмас үшін цемент қамырының ұстасу мерзімін гипстің көмегімен реттейді. Ол үшін клинкерді диірменде майдалаған кезде клинкер массасының 3...5 %-індей гипсті қосып майдалайды. Кейін цементті сумен араластырғанда гипс үш кальцийлі алюминатпен қосылып кальцийдің гидросульфоалюминатын түзеді ГСАК-3 немесе эттрингит. Оның формуласы 3СаО·Аl2О3·3CaSO4·31Н2O. Осы гидросульфоалюминаттың түйірлері цемент бөлшектерін жұқа қабықпен қоршап, олардың тез гидратациялануына жол бермейді. Сөйтіп ұстасу мерзімін баяулатады. Гипстен басқа натрий фосфатын, бypa, қант қосу арқылы, температураны төмендету, су-цемент қатынасын көбейту арқылы да цементтің ұстасу мерзімінің жылдамдығын бәсеңдетуге болады. Ал температураның жоғарылауы, цемент құрамында су мөлшерінің азаюы, кальцийдің хлорлы тұздары, керісінше, ұстасу мерзімін тездетеді.
Кейбір жағдайда цемент жалған ұстасып қалуы да мүмкін, яғни цемент бір сәтте ұстасып қалады. Оның себебі, ұнтақтау кезінде диірмендегі температура жоғары болса екі сулы гипс CaSO4·2Н2О ыдырап, CaSO4·0,5Н2О түзіледі. Ал жарты сулы гипс сумен тез әрекеттесуге бейім. Бірақ жалған ұстасу цементтің беріктігіне кесірін тигізбейді; бұндай жағдайда цемент қамырын жақсылап араластырса ары қарай қалыпты күйіне түседі.
Цементтің ұстасу мерзімін Вик инесінің көмегімен анықтайды. Сынақты қалыпты қоюлықтағы цемент қамырымен өткізеді. МСТ бойынша портландцемент сумен араластырылғаннан бастап 45 минут өткеннен кейін ұстаса бастау керек, ал 10 сағатқа жетпей толық ұстасу керек (конец схватывания).
Бетонның, цементтен істелген басқа да бұйымдардың жарамдылығын олардың көлемдерінің өзгерістеріне қарап та байқауға болады. Өйткені бұлардың көлемдерінің өзгерісі кейде бір қалыпты болмауы мүмкін. Цемент көлемінің бір қалыпты өзгермеуі оның құрамында күйдірген кезде кальций тотығы СаО мен магний тотығының байланыспаған бос бөлшектерінің қалатындығынан. МСТ талаптары бойынша клинкер құрамындағы магний тотығының мөлшері 5 %-тен аспауы керек. Сапалы клинкер құрамында бос кальций тотығының мөлшері 1...2 %-тен аспайды. Бұлар екі тотық сумен өте жай әрекеттеседі. Бұлардың гидратациясы барлық клинкерлік минералдар гидратацияланып, түзілген гидраттар кристалданғаннан кейін, бетон бұйымы қатып қалғаннан кейін барып басталады. Ал реакцияның өнімдері — Са(ОН)2 мен Mg(OH)2 көлемдері бастапқылардыкіне (СaO, MgO) қарағанда 2 еседей үлкен. Осыдан цемент тасының ішкі кернеу күші туындап, кей жағдайда бұлар бұйымдарды бұзылуға дейін апарады.
Цемент көлемінің өзгерісін байқау үшін қалыңдығы 1 см-дей диаметрі 7...8 см болатын күлшелер дайындап, оларды бір тәуліктен соң 4 сағат суда қайнатады. Егер күлшелердің бетінде үлкен радиалды жарықтар, бетінің қисаюы, толып жатқан майда жарықтар байқалмаса, цемент жарамды болып саналады. Басқаша болған жағдайда цементті қашан көлемінің өзгерісі бір қалыпты болмайынша қоймада сақтайды.
Қатаю кезінде бөлінетін жылу. Цемент тасының қатаю процесі жылу бөле отырып жүреді. Цемент ерітінділерінің, бетонның қолдану жағдайларына, мезгілдеріне байланысты бөлінген жылу пайдалы да, пайдасыз да болуы мүмкін. Мысалы, қыс кезінде пайдалы, өйткені бетонды қатырмай, гидратация процесінің жүруіне жағдай жасайды. Басқа уақытта бетонның ішкі қабатында жылу кернеулігін тудыруы мүмкін, бұл кезде қатерлі жарықтар пайда болады.
Гидратация кезінде бөлінетін жылу цементтің мннералдық құрамына байланысты. C3S, C3A минералдары C2S, C4АF минералдарына қарағанда жылу көп бөліп шығарады.
Тығыздығы мен көлемдік массасы. Портландцементтің тығыздығы 3000...3200 кг/м3 құрамына байланысты өзгереді. Көлемдік массасы борпылдақ күйінде 900...1000 кг/м3, тығыздалғанда 1400...1700 кг/м3 тең.
Тығыздығы жоғары цементті мұнай бұрғыларының жан-жағын тығындауға, ядролық сәулелерден қорғайтын үй-жабдықтар салуға қолданады. Барий тотығын, барий карбонатын қосу және құрамындағы С4АҒ пен С2Ғ-тің мөлшерін көбейту арқылы цементтің тығыздығын арттыруға болады. Тығыздығы төмен цементтерге шлакты цемент пен пуццоланды цементтері жатады.
Ісіну мен шөгуі. Цемент бұйымдары, бетон қоршаған ортаның ылғалдылығы олардың ылғалдылығынан аз болса кеуіп, шөге бастайды. Кеуектердегі, капиллярлардағы, адсорбциялық су кеуіп, буға айналады. Осыдан бетонда әр түрлі жарықтар тудыратын, кей кезде бұзылуға дейін апаратын капиллярлық күштер пайда болады.
Бетонның сызықтық өлшемдерінің кішірейіп, шөге бастауы химиялық процесстің әсерінен де болуы мүмкін. Ондай шөгуді контракция деп атайды. Клинкерлік минералдардың гидратациясы цемент қатайғаннан кейін тоқтаусыз жүре беретіндігі белгілі. Ал бұның нәтижесінде жаңа гидраттар түзіліп, цемент гелін біртіндеп тығыздай түседі. Сөйтіп цемент гелінің көлемі бірте-бірте кішірейіп, контракция туындайды. Бетонның шөгуі цементтің құрамы мен майдалылығына да байланысты. Мәселен, алитті, әрі ірі түйіршікті цементтердің шөгуге бейімділігі аз. Сондай-ақ, ұнтақ толтырғыштарды қолдану, құрамындағы судың мөлшерін азайту цемент көлемінің шөгуіне жол бермейді. Бетондардың шөгуін болдырмау үшін майда және ірі толықтырғыштар қосады.
Бетон үшін оның ісінуі де қауіпті. Коршаған ортаның ылғалдылығы бетонның ылғалдылығынан көп болған жағдайда бетон өзіне ылғал тартып, құрамындағы судың мөлшері көбейіп, осының салдарынан ісіне бастайды. Бұндай кездерде де бетонды бүлдіретін ішкі кернеу күштері пайда болады.
Әр түрлі механикалық күштердің әсерінен, температураның, ауаның ылғалдылығының өзгеруінен, көлемінің шөгуінен бетонда жарықтар пайда болуы мүмкін.
Цемент бұйымдары, бетон кейде механикалық күштердің әсерінен ығысып кетіп, қайтадан орнына келмеуі мүмкін. Цемент тасының, бетонның, ығыспалдылығы оның беріктігіне байланысты. Цемент тасының беріктігі неғұрлым жоғары болса, ығыспалылығы соғұрлым төмен болады. Әр түрлі қоспалар (ПАВ) қосып та бетон жарықтарының алдын алуға болады.
Бақылау сұрақтары.
1. Цемент тасының беріктігі неге байланысты? 2. МСТ 10178-85 бойынша портландцементтің маркалары қандай? 3. Портландцементтің тығыздығы және көлемдік массасы қандай? 4. Цемент тасының беріктігі қалай өседі? 5. Цементтің ұстасу мерзімін қалай анықтайды? 6. Цементтің ұстасу мерзімі қандай болу керек? 8. Гидратация кезінде бөлінетін жылу неге байланысты? 9. Контракция деп нені атайды? 10. Цемент қамырының қалыпты қоюлығы қандай, ол неге байланысты? 11. Вик құрылғысы не үшін пайдаланады? 12. Цемент бұйымдарының, бетонның ісінуі мен шөгуі қандай жағдайда болады, мөлшері қандай? 13. Цемент көлемінің өзгерісін қалай анықтайды?
XІ тарау
АРНАЙЫ ЦЕМЕНТТЕР. ШЛАКТЫ, ПУЦЦОЛАНДЫ ЖӘНЕ ГЛИНОЗЕМДІ ЦЕМЕНТТЕР
Арнайы цементтер
Арнайы цементтерге портландцемент клинкерінің негізінде жасалған цементтер жатады: жылдам қатаятын және жоғары маркалы, ақ және түсті, сульфатқа төзімді, пластификацияланған және гидрофобты, тампонажды, жолға төсейтін, асбестцемент бұйымдарға арналған т.б. Бүл портландцементтерді клинкердің минералдық құрамын өзгертіп, әр түрлі қоспаларды қосып дайындайды.
11.1.1 Жылдам қатаятын және жоғары маркалы цементтер
Цемент өндірісінде портландцементпен қатар қасиеті және өндіру технологиясымен ерекшеленетін басқа да цемент түрлерін өндіреді. Олар портландцементтің ерекше түрлеріне жатады. Жоғары маркалы цементтерге маркалары М 500, М 550, М 600 цементтер жатады.
Тез қатаятын портландцемент ол қатаюы жылдам жүретін минералды қоспалар қосылатын портландцемент. Тез қатаятын портландцемент өндіру үшін шикізаттар өте сапалы, оның құрамында зиянды қоспалар болмау керек, болмаса өте төмен мөлшерде болуы керек. Шикізат құрамындағы зиянды қоспаларға магний карбонаты МgCO3, доломит, сілтілер Na2O, K2O, кукірт тотығы SO3 , көп мөлшерде Р2О5 тағы басқалар жатады.
Тез қатаятын цемент өндірісінде шикізат қоспасы біртекті және таза болуы керек. Шикізат қоспасын өте жуқалап майдалау қажет. Нөмірі № 02 електе қалдық қалмауы, ал № 008 електе қалдық 5...6 % аспауы керек.
Портландцемент клинкерін пеште куйдіргенде күлсіз отынды пайдаланып, ыстық клинкерді өте жылдам суытады. Клинкерді куйдіру процесі жоғары температурада тез мерзімде жургізілсе клинкердің құрамы жақсарып, өте активті формада клинкер минералдары пайда болады. Олардың құрылымы оптималды жағдайда пайда болып цементтің гидратациялануын жылдамдатып, маркасын арттырады. Жоғары температуралы алапта клинкер ұзақ болса онда минералдардың өлшемі жоғары болып, гидратациялану белсенділігі төмендеп кетеді.
Цементтің механикалық беріктігін жоғарылату үшін клинкердің минералогиялық құрамына көп көңіл бөліп, гипс мөлшерін жоғарылатып, цементті, жұқа етіп ұнтақтау қажет. Жоғары маркалы тез қатаятын жақсы цемент алу үшін клинкер 60...70 % активті минералдардан тұруы қажет, C3S > 50 %, ал C3A – 8 % шамасында болуы керек. Мундай клинкер алу ұшін оның қанығу коэффициенті жоғары ҚК = 0,93...0,96 болу керек. Қанығу коэффициенті жоғарылағанда клинкердің куйдірілу процесі қиындайды, температура жоғарылайды, пештің өнімділігі төмендейді, отын шығыны артады. Мундай жағдайда минерализатор қоспаларды пайдаланған дұрыс. Ондай қоспалар ретінде СаF2, Na2SiF6, CaCl2, фосфорлы шлак, фосфогипс пайдалануға болады. Олар клинкер пайда болу температураны төмендетеді, суйық фазаның мөлшерін жоғарылатып оның қасиеттерін жақсартады.
Ұнтақтау кезінде клинкерге қосылатын гипс цементтің тек ұстасу мерзімін реттемей ол цементтің беріктігін жақсартады, оның мөлшері SO3 –пен есептегенде 3,5 % аспауы керек. Тез қатаятын портландцементті өте майда етіп ұнтақтайды, оның меншікті беті 350...450 м2/кг болады (қатардағы цементте 250...300 м2/кг). Ұнтақтауды диірменде жабық циклда жүргізеді.
Тез қатаятын цементтің 2 түрлі маркасы өндіріледі: М400, М500, оның беріктігіне 28 тәуліктен басқа қосымша 3 тәулікте талап қойылады. МСТ 10178-85 бойынша тез қатаятын М400 және М500 цементтің 3 тәуліктен кейінгі беріктігі қысуда (сығуда) - 24,5 МПа және 27,5 МПа кем емес, иілуде (майысуда) - 3,9 және 4,4 МПа кем емес, ал 28 тәуліктен соң қысуда – 39,2 және 49 МПа, майысуда 5,4 және 5,9 МПа кем емес болуы керек.
Тез қатаятын цементті пайдалану бетонның маркасын жоғарылатады, бұл бұйымның массасын төмендетуге және бетонды үнемдеуге 8...30 %, құрышты (сталь) 15 % дейін төмендетуге әкеледі және бұйымның бағасын 3...15 % дейін төмендетеді.
11.1.2 Ақ және түсті портландцементтер
Ақ цементтің жай порландцементтен айырмашылығы – түсі, сондықтан мұндай цементті алуда барлық технологиялық процесс ақтығын қамтамасыз ететін талапқа бағынады.
Ақ және түсті портандцементтерді өндіру үшін, әдетте барынша таза карбонаттар мен құмды саздарды қолданады, әктастың саздың және құмның құрамындағы бояғыш тотықтар – темір, марганец,титан өте аз мөлшерде болуы керек. Шикізат қоспасына және цементке темір түсіп кетпеу үшін шикізат материалдарын майдалау, шикізатты және цемент клинкерін ұнтақтау арнайы фарфорлы, кремнийлі және басқа плиталармен футеровкаланған майдалау құрылғысы мен диірмендерде жүргізіледі. Майдалағыш дене ретінде кремнийлі тастар немесе «уралит» қызмет етеді. Темір құрамдас күлдің отыруынан құтылу үшін күйдіруді сұйық немесе газтәріздес отынмен жүргізеді. Бұл кезде балқыманың құрамын азайту салдарынан шикізат қоспасын күйдіруді біршама жоғары 1600...1650 OС температурада жүргізеді. Нәтижесінде пештің өнімділігі төмендейді, ал цементтің бағасы жоғарылайды. Пештен шыққан клинкерді 1250 ден 250 OС –та тотықсыздандырғыш ортада салқындату жолымен немесе оны сумен 1600 – дан 500 OС дейін жылдам суыту арқылы ағартады. Ағарту кезінде темір тотығы Fe3O4-ке айналады, соның әсерінен темір қоспаларының бояғыш қабілеттілігі төмендейді де, цементтің ақтығы жоғарылайды.
Ақ цементтің сапасы ашықтық коэфициентінің мөлшерімен анықталады, ашықтық коэфициенті алынған цементтің ақтығының /пайыздық/ эталондық «молочное стекло МС-20» ақтығына қатынасы.
Ақ цемент өзінің ақтық дәрежесі бойынша МСТ 965-89 талаптарымен 3 сортқа бөлінеді: АЦ-1, АЦ-2, АЦ-3 бұларға сай ақшыл коэфициенттері 80; 75 және 68 (фарфордың ашықтық коэфициенті 70...90, ал кәдімгі портландцементтің ақтығы 20...40).
Бұл цементтің қысқандағы мықтылық шегі бойынша 2 маркасы - М400, М500 және 2 түрі болады: ақ портландцемент және минералдық қоспасы бар ақ портландцемент. Минералдық қоспа ретінде ақшыл доломит, күйдірілген ақ каолин және т.б с.с шөкпелі жыныстар қолданылады. Активті минералдық қоспалардың мөлшері 20 % аспау керек, ал инертті қоспа ең көп болғанда 10 %. Ақ цементтің ұстасу мезгілдері: басы - ең ертесі 45 минут, аяғы- ең кеші 12 сағат.
Ақ түсті портландцементтер міндетті түрде арнаулы контейнерде немесе көп қабатты қағаз қабында қоймада сақталып және тұтынушыларға тасылулары керек.
Ақ және түрлі түсті ерітінділер және бетондар алу үшін өздеріне сәйкес түсті толтырушылар - ақ және түсті мрамордың, граниттің ізбестің қоқымдарын, ақ құм және т.б.с.с тау жынысынан алынатын минералдық өнімдері қолданады.
МСТ 15825-80 бойынша түсті портландцементтерді ақ немесе кәдімгі жай клинкерді бояушы пигменттермен қоса ұнтақтау арқылы алады. Минералдық пигменттер ретінде қолданылатындар: сары түсті цемент алу үшін- охра, қызыл түстіге-темір сурикі, ал жасыл үшін – темір купоросы және т.б., бұлардың қосқандағы мөлшері 10 % аспау керек, ал органикалық пигменттерде - 0,5 пайыздан.
Ақ және түсті портландцеметтер мықтылығы зор, мәңгілік өңдеуші материал. Оларды архитектуралық өңдеу, әсемдеу жұмысына керек құрылыс ерітінділерде, бетондарды алу үшін қолданады.
11.1.3 Сульфатқа төзімді портландцементтер
Бұл цемент тасы сульфатты су әсеріне тұрақты болып келеді. Мұндай цемент алу үшін клинкердегі жоғары негізді кальций алюминатының мөлшерін төмендету керек 3CaO·Al2O3. Сульфатқа төзімді цементтің минералды қоспасыз және минералды қоспамен екі түрі өндіріледі. Минералды қоспасы бар сульфатқа төзімді цементке түйіршіктелген доменді немесе электротермофосфор шлагы 10...20 %, немесе шөгінді жынысты қоспалар 5...10 % қосылады.
Сульфатқа төзімді цементтерді өндіруде МСТ 22266-97 талабы бойынша клинкер құрамы мынадай болуы керек (11.1-кесте).
11.1-кесте. Сульфатқа төзімді портландцементтердің минералдық құрамы
Минерал мөлшері, % | Сульфатқа төзімді портландцемент клинкерінің құрамында минералдар мөлшері, % | |||
Сульфатқа төзімді портланд цемент | Минералды қоспасы бар сульфатқа төзімді ПЦ | Сульфатқа төзімді шлакопорт- ландцемент | Пуццоланды портланд- цемент | |
С3S, % артық емес | 50 | нормалан байды | нормаланбайды | |
С3А, % артық емес | 5 | 5 | 8 | 8 |
С3А+C4AF, % артық емес | 22 | 22 | нормаланбайды | |
MgO, % артық емес | 5 | 5 | 5 | 5 |
Сульфатқа төзімді портландцементтің маркасы М400, минералды қоспалар қосылған сульфатқа төзімді портландцементтің М400 және М500 маркалары өндіріледі, сульфатқа төзімді шлакопортландцементтің және пуццоланды портландцементтердің маркалары М300 және М400 өндіріледі.
Сульфатқа төзімді портландцементтерді және шлакопортландцементтерді өндіргенде пайдаланатын шлактардың құрамында Al2O3 мөлшері 8 % аспауы керек. Сульфатқа төзімді портландцементтерді сулы ортада коррозияға шыдамды бетондар және темір бетондар жасауда пайдаланылады.
Цементтегі күкірт қышқылы ангидридінің мөлшері 4,0 % аспауы керек.
Үлгіні ыстық суда қыздыру сынағында цемент, көлемі өзгеруінің бірқалыптылығын көрсетуі керек. Цементтің ұстасуының басталуы 45 минуттан ерте болмауы керек, аяқталуы 10 сағаттан кеш болмауы қажет. Гипсті тас МСТ 4013, туйіршектелген домналы немесе электротермофосфорлы шлагы МСТ 3476 сай болу керек. Қаптап буу және белгілеу МСТ 22235 сай жүргізіледі. Цементті сақтау және тасымалдау МСТ 22235 бойынша жүргізіледі.
11.2-кесте. Сульфатқа төзімді портландцементтерде минералды қоспалардың мөлшері
Портландцементтер
| Туйіршектелген домналы немесе электротермофос- форлы шлак | Активті минералды қоспалар | |
Шөгінді (глиежден басқа) | басқалары (және глиеж) | ||
Сульфатқа төзімді портландцемент | Қосылмайды | Қосылмайды | Қосылмайды |
Минералды қоспасы бар сульфатқа төзімді портландцемент | 10%-дан кем емес, 20%-дан артық емес | 5%-дан кем емес, 10%-дан артық емес | Қосылмайды |
Сульфатқа төзімді шлакопортланд- цемент | 21%-дан кем емес, 60%-дан артық емес | 5%-дан кем емес, 10%-дан артық емес | Қосылмайды |
Пуццоланды портландцемент | - | 20%-дан кем емес, 30%-дан артық емес | 25%-дан кем емес, 40%-дан артық емес |
11.1.4 Беттік активті қоспалар қосылған цементтер
Пластификацияланған портландцементтер. Цементтің құрылыс – техникалық қасиеттерін жақсарту мақсатында оған 0,3 % беттік активті қоспалар қосылады. Беттік активті қоспалар (БАҚ - ПАВ) клинкер дәндерінде адсобцияланып, оны жұмсартады, түйіршіктердің жабыспауына ықпал етеді, яғни ұнтақтау процесін жақсартады. Пластификацияланған портландцементте МСТ 10178-85 бойынша 1:3 цементті-құмды араласпаның стандартты конустың аққыштығы 125 мм жоғары болады.
Пластифицирленген қоспа ретінде техникалық лигносульфонаттарды (ЛСТ) (бұрынғы аталуы сульфитті – дрожды бражка (СДБ) қолданады. Техникалық лигносульфонаттардың молекулдары цемент дәндерінде адсорбцияланып, қабықша пайда болып, гидратталған цемент түйіршіктерінің бір-біріне жабысуын баяулатады.
Сондықтан мұндай цемент негізінен жасалған бетон мен құрылыс қоспалар өте жылжымалы болып келеді. Бұл 8...10 % дейін цементтің шығынын төмендетуге мүмкіншілік туғызады. Сонымен қатар суда аз қосылады. Бұл бұйымның суыққа төзімділігін жоғарылатады. Мұндай цементтер монолитті бетон, гидротехникалық құрылыс, жол және аэродромды жабындарда қолданылады.
МСТ 10178-85 бойынша пластифицирленген цементтердің М400, М500, М550 және М600 маркалары өндіріледі. Ол маркалы цементтердің 28 тәуліктен кейін иілуде (майысуда) беріктігі – 5,4; 5,9; 6,1; 6,4 МПа кем емес, ал 28 тәуліктен соң қысуда – 39,2, 49, 53,9 және 58,8 МПа кем емес болуы керек.
Гидрофобті портландцементтер. Гидрофобті қоспалар ретінде асидол-мылонафт (0,08...0,12 %), мылонафт (0,1...0,25 %), олеин қышқылы (0,06...0,1 %), петролатум (0,3 % дейін) т.б. қолданылады. МСТ 10178-85 бойынша мұндай цементтер 5 минут бойы су сіңірмеуі қажет. Гидрофобты қоспалар қосылған цементтер төменгі гигроскопиялық қасиетімен ерекшеленеді, ұзақ жерге тасуға қолайлы болып келеді, ұзақ уақыт маркасын жоғалтпай турады.
Гидрофобты қоспалар қосылған цементтер муздатуға және сульфатты агрессияға төзімді болады. Бетонның денесінде өте майда, су толтырылмайтын, мұз қатпайтын кеуектер пайда болып, бул бетондар өте төзімді болады. Гидрофобты цемент негізінен жасалған бетон мен құрылыс қоспалар өте жылжымалы болып келеді. Бұл бетон құрамында 8...10 % дейін цементтің шығынын төмендетуге мүмкіншілік туғызады. Сонымен қатар бетонға су мөлшері аз қосылады, беріктік, сульфатты агрессиясына, аязға төзімділік жоғарылайды.
Бұл цементтер сыртқы жол және аэродром құрылыстарында, гидротехникалық бетондар үшін пайдаланылады.
Беттік активті қоспалар цемент диірмендерінің өнімділігін 10...20 % жоғарылатады, электрэнергияның ұлестік шығынын төмендетеді. Цемент ұнтақтағанда БАҚ жоғары мөлшерде қосылып кетсе цементтің гидратацияланып қатаюы баяулап кетеді.
11.1.5 Асбестцемент бұйымдарына арналған цемент
Асбестцемент бұйымдарына арналған цементтің клинкерінің құрамына ерекше талаптар қойылады. Клинкердің құрамында C3S мөлшері 50 % кем емес, C3A мөлшері 3...8 % арлығында, ұстасу мезімінің басталуы 1 сағат 30 минуттан ерте емес болу керек. Бүл цементтің үлестік беті 220...320 м2/кг арлығында болу керек. Асбестцемент бұйымдарына арналған цементтің маркалары М400 және М500 өндіріледі. Бүл цементке минералды қоспаларды қосуға болмайды. Клинкерде бос СаО мөлшері 1 % кем болу керек. Сол кезде асбестцемент бүйымдары тез гидратацияланып қатаяды, сапасы жоғары болады, цементтің технологиялық сулармен жоғалуы төмендейді. Бүл цемент және оның негізіндегі бетондар сульфатты агрессияға және аязға төзімділігімен ерекшеленеді.
11.1.6 Аэродром және жол бетондарына арналған портландцемент
Бұл цементтер майысуда және соғуда жоғары беріктілікке ие, аз үгітіледі, суыққа төзімді және аз шөгеді. Бұл цементтер МСТ 10178 – 85 талаптарына сай болуы керек. Активті минералдар ішінен тек түйіршіктелген доменді шлактар 15 % дейін қосылады. Цементтің ұстасуының басталуы 2 сағаттан ерте емес, аяқталуы 10 сағ кеш емес болу керек. Клинкердегі С3S мөлшері 52 % кем емес, C3A мөлшері 8 % жоғары емес болу керек. Бүл цементтің М400 және М500 маркалары өндіріледі. Бұл цемент бір және екі қабатты жол және аэродром үшін бетон бұйымдарында қолданылады. МСТ 10178-85 бойынша бүл цементтің белгісінде Н әріпі қойылады. Ол клинкердің құрамы нормаланғандығын белгілейді. Мысалы ПЦ 500 Д5-Н- МСТ 10178-85.
Тампонажды портландцементтер
Бұл цемент мұнай және газды ұнгімелерді тампонаждау үшін арналған. Бұл цемент жер асты суларына төзімді болып келеді. Ұнгімелерді дұрыс жүргізу тампонирлеуге байланысты. Ұнгімеде тампонажды цементке температура, қысым, су және кеннің жыралары әсер етеді. Сол себептен тампонажды цементке үлкен техникалық талаптар қойылады. Таза тампонажды цемент қамыры жоғары аққыштыққа ие болуы қажет, өйткені ол құбырлар мен ұнгіме арасына жақсы енуі керек. Цемент қамырының аққыштығы су - цемент қатынасы 0,4...0,5 аралығында ұнгімедегі температура мен қысымға қарамай жақсы болуы керек. Тампонажды цементтің негізгі қасиеті – беріктігі болып табылады. Өйткені құбыр колонналары ұнгімеге жақсы бекітіліп, мунайды жер асты суларынан қорғауы керек.
Мұнай және газ шаруашылығының дамуы салдарынан тампонажды цементке сұраныс өсіп отыр. Сонымен қатар оның түрлері де байытылды.
МСТ 1581 – 96 бойынша тампонажды портландцементтің екі түрі өндіріледі. Бірінші "мұздай", ал екіншісі "ыстық" ұнгімелерді цементтеуге арналған.
Мұздай ұнгімелерге арналған цемент меншікті беті 300...350 м2/кг етіп ұнтақталған алитті клинкерден алады, С3S мөлшері 60 %, ал ыстық ұнгімелерге арналған түрін төмен алюминатты клинкерден өндіреді. Тампонажды портландцемент құрамына 20 % түйіршіктелген доменді немесе электротермофосфор шлагын, 12 % активті минералды қоспалар, 10 % кварц құмын немесе әктас қосуға болады.
Мұздай ұнгімелерге арналған цементтің ұстасу мерзімінің басталуы 2 сағаттан ерте емес, аяқталуы 10 сағаттан кеш емес, ал ыстық ұнгімелерге арналған цементтің ұстасуының басталуы бір сағат 45 минуттан ерте емес, аяқталуы 348 К – де 5 сағаттан кем емес.
Тампонажды цементтің негізгі ерекшелігі – майысу негізіндегі беріктігі. Мұздай ұнгімелерге арналған цементінің екі тәуліктен кейінгі беріктігі 2,7 МПа кем емес, ал ыстық ұнгімелерге арналған цементінің бір тәуліктен кейінгі беріктігі 3,5 МПа кем емес болуы керек. Цемент аққыштығы 180 мм шамасында болуы қажет.
Тампонажды цемент пен қатар көптеген сульфатқа, температураға, қышқылға төзімді түрлі арнайы цементтер өндіріледі. Арнайы тампонажды цементтің бұрғылауға арналған ауырланған, тығыздығы 4 г/см3 түрі де бар. Ауырлатқыш ретінде темір рудасын, магнетит, гематит пайдаланылады, цемент 70 % болады. Сонымен қатар салмағы жеңілденген цементтерде өндіріліп пайдаланады. Жеңілдеткіш қоспалар ретінде трепел, диатомит, опока т.б. материалдар пайдаланады. Құрамында 2...3 % асбест немесе мақта өндірісінің қалдығы қосылған жіптік цементте өндіріледі. Бұл цементтер ұнгімелер қабырғаларының майда жырықтарын бекітіп тастайтын қабық түзеді.
Цемент ерітіндісі жоғары аққыштығымен құбырлардың кеңістігіне цемент ерітіндісінің еркін айдауға-кіруіне және бойлауына мүмкіншілік беру қасиетіне ие болуы керек. Пластификацияланбаған цемент қамырының ағындылық қасиеті 200 мм аз болмайтындай, ал пластификацияланған цемент қамырының аққыштығы 220 мм-ден кем болмау керек. Тампонажды цементтің аққыштығы 0,4...0,5 су/цемент қатынасында ұнгімедегі температура мен қысымға байланыссыз сақталу қажет. Цементті өндіріс қазіргі кезде тампонажды портландцементті «суық» немесе «ыстық» ұңғымаларды цементтеуге шығарады. Бұндай цементтерді сынау (22 ±2) және (75 ±3) оС температураларда жүргізілуі тиіс.
«Суық» ұңғымаларға арналған цементтерді алитті клинкерлерден (60 % С3S шамасында) алады. Олардың ұлестік беті 300...350 м2/кг болу керек. «Ыстық» ұңғымалар үшін цементтерді төмен алюминатты клинкерлерден алады.
Тампонажды цементтерге қойылатын талаптар.
МСТ 1581-96 бойынша тампонажды цементтер заттық құрамы бойынша мынандай түрлерге бөлінеді:
- I, I-G, I-Н түрі (тип I, I-G, I-Н) - қоспасыз цемент;
- II түрі (тип II) - қоспасы бар цемент (минералды қоспа 6...20 %, клинкер 80...94 %);
- III түрі (тип III) – арнайы қоспасы бар цемент (арнайы қоспа 11...70 %, клинкер 30...89 %); құмды цемент (цемент қамырының тығыздығын реттеуші қоспалы цемент (жеңілдеткіш немесе ауырлатқыш).
Цемент қамырының тығыздығы бойынша тампонажды цементтердің III түрі екіге бөлінеді: жеңілдетілген (Ж); ауырлатылған (А) болып бөлінеді.
Тампонажды цемент пайдаланатын температурасы бойынша: төмен және кәдімгі температура (15...50) 0С; бірқалыпты температуралы (51...100) 0С; жоғары температуралы (101...150) 0С болып бөлінеді.
Клинкерде магний тотығының құрамы 5 % көп болмауы керек.
Сульфатқа төзімділігі бойынша тампонажды цемент: кәдімгі; сульфатқа төзімді (СТ) болып бөлінеді.
Сульфатқа төзімді тампонажды цемент өндіргенде технологиялық регламент бойынша химиялық құрамы сәйкес келетін портландцемент клинкері қолданылады.
Сульфатқа төзімді I, II, III түрлі тампонажды цемент дайындауда клинкер құрамында С3А 5 % артық емес, С3А + С4АҒ құрамы 22 % көп болмайтындай клинкер қолданылуы қажет.
2 тәуліктен кейінгі «суық» ұңғымаларға арналған цементінің беріктігі майыстыру (иілу) кезінде 2,7 МПа - дан, ал «ыстық» ұңғымаларға – 1 тәуліктен кейін – 3,5 МПа - дан аз болмауы қажет.
Талапқа сәйкес цементтердің қасиеті 11.3- кестеде келтірілген.
11.3-кесте. Тампонажды цементтерге қойылатын талаптар
Көрсеткіштердің атауы | Қолдану температурасына және түрлеріне байланысты цементтердің мәні | ||||
Қалыпты және төменгі |
Бірқалыпты және жоғары | ||||
I, II түрі | III түрі-жеңілдетілген | I, II түрі | III түрі-жеңілдетілген | III түрі-ауырлатылған | |
1 Майыстыру /иілу/ кезіндегі беріктік шегі, МПа, кем емес: 1 тәуліктен кейін 2 тәуліктен кейін | - 2,7 | - 0,7 | 3,5 - | - 1,0 | - 2,0 |
2 Ұнтақталу дәрежесі - 6613 МСТ бойынша №008 елеугіштегі қалдық көп болмау керек, % - ұлестік беті, м2/кг, кем емес | 12,0 270 | 10,0 - | 15,0 250 | 12,0 - | 12,0 230 |
3 Цемент қамырынан судың бөлінуі, мл, көп емес | 8,7 | 7,5 | 8,7 | 7,5 | 10,0 |
4 Цемент қамырының аққыштығы, мм, аз емес: -пластификацияланбаған -пластификацияланған | 200 220 | - - | 200 220 | - - | - - |
5 Консистенция 30Вс мөлшеріне дейінгі қоюлану уақыты, мин, кем емес /Берден консистенциясы/ |
90 |
Майысу (иілу) кезіндегі беріктігін анықтау үшін қалыпты температурадағы тампонажды цемент үшін 40х40х160 мм өлшемдегі үлгі-балкаларда анықтайды. Жоғары температуралы цементтер үшін өлшемі 20х20х100 мм ұлгеше балкаларды пайдаланады.
Шлакты портландцемент
Шлакты портландцемент дегеніміз сумен арласқан соң өз беріктігін ылғалды ортада құрайтын гидравликалық тұтастырғыш зат. Портландцемент клинкерін және түйіршіктелген домналы немесе электротермофосфорлы шлакты ұнтақтап алғанда пайда болады. Шлакопортландцементте шлактың құрамы 21...80 % арасында болады. Ұстасу жылдамдығын реттеу үшін ұнтақталу кезінде гипс қосады, SО3 дайын өнімде 3,5 % асып кетпеуі тиіс. Шлакопортландцементті бетонды және темірбетонды, суасты және жер асты құрылысында қолданылады. Шлакопортландцементті құрылыс бетондарын және темірбетон бұйымдарын буландыру арқылы алады.
Шлактық портландцементті өндіруінің технологиялық схемасы, пуццоландық портландцементті алғандай, екі технологиялық белестен тұрады. Алдымен портландцементтік клинкердің алынуы, сосын шлактық портландцементінің ұнтақталуы. Шлактық портландцементтің ұнтақтылығы портландцементтегідей. Дегенмен өндірісте оның ұнтақ тылық дәрежесін жоғарылатуға барынша тырысады. Себебі, ұнтақтылығы жоғары болған сайын қатаю жылдамдығы өсіп, мықтылығы жоғарылай түседі.
Шлактық портландцементтің қатаю процесі портландцементтегіге қарағанда баяу және едәуір күрделі жүреді. Оның қатаю процесін екі кезеңге бөлуге болады. Алдымен цементтің клинкерлік бөлімі мен гидратациясынан пайда болган қүрамдарымен бірлі-жарым гидратталынған граншлактар арасында химиялық әрекеттесу жүреді. Бұл қатаю процесін жеңілдету үшін кейде СаС12, Са(NО3)2, ВаС12 т.б. тұз ерітінділерін қосады. Оның үстіне ыстық бумен өңдеу арқылы қатаю процесін керегінше жеделдетуге болады.
Шлактық портландцементтің мықтылық шамасын толық
пайдалану үшін оның қатаюын міндетті түрде ылғалдылық ортада ұзақтау откізу керек.
Портландцементпен салыстырғанда, бұл цемент сульфатты суға төзімді. Оның себебі, ол қатайған кезде Са(ОН)2 аздау бөлінеді де сульфатты түздар ерітіндісімен әрекеттесуге Са(ОН)2 жетімсіз болады, гидратация үстінде бөлініп шыққан Са(ОН)2 төменгі негізді кальций гидроросиликаттарын құруға түгелдей жұмсалынады.
Шлактық портландцемент қатайғанда жылу көп бөлініп шықпайды. Сондықтан, оны массивті ғимараттарды салуга қолдану қауіпсіз.
ШПЦ аязға төзімділігі бойынша жетерліктей жарамды. Бірақ құрғақ климатты жерде, судың ауыспалы деңгейінде, бірде мүздап, бірде еріп және бірде суланып, бірде кеуіп түратындай жағдайда оның шыдамдылығы портландцементтегідей емес. Қатаю мезгіліндегі оның көлемдік деформациясы (отыруы және ісінуі) портландцементтегіден аздау. Қалған басқа қасиеттері бойынша портландцементтегіге ұқсас.
ШПЦ тығыздығы шлактың мөлшеріне байланысты 2800...3000 кг/м3 аралығында, сусымалы тығыздығы 900...1200 кг/м3 (бос салғанда), 1400...1800 кг/м3 (тығыздап салғанда). МСТ 10178-85 бойынша шлакопортландцемент үш маркалы өндіріледі: М300, 400 және 500, игендегі мықтылық шегі маркаларына сәйкес: 4,4; 5,4; 5,9 МПа. ШПЦ әдетте көпір және гидротехникалық құрылыста, агрессивті ортада пайдаланатын түрлі бүйымдарға қолданады. Ал, темірбетон зауыттарында бетон және темірбетон бұйымдары мен конструкцияларын жасарда шлактық портландцементтер өте кең қолданылады.
Қышқыл шлактарға тұтастырғыштығын жақсарту үшін сілтілі және сульфатты активизаторлар гипс және әк қосады. Шлакопортландцемент портландцементке қарағанда баяу қатаяды. Ылғал ортада температура жоғары болса қату жылдамдығы жоғары болады, ал температура төмен болса баяу қатаяды. Ылғалды жылы жерде өңделсе шлакопортландцементтің қату жылдамдығын жақсартады. Стандартқа сай қату жылдамдығы және бірегей беттің өзгеруі шлакопортландцементтікі портландцементтікімен бірдей.
Тез қатаятын шлакопортландцемент құрамында 30...50 % шлак бар. Бұл цементтің 3 тәуліктегі сығу кезіндегі беріктігі 16,6 МПа, ал 28 тәулікте 39,2 МПа кем емес болу керек.
Клинкер өндіріп алу үшін түйіршіктелген немесе түйіршіктелмеген шлак қосуға болады, ал ұнтақтау кезінде қоспа ретінде түйіршіктелген шлакты қосуға болады.
Пуццоланды портландцемент
Пуццоланды портландцемент деп минералдық құрамы нормалданған (С3А < 8 %) клинкерді, гипсті және активті минералдық қоспаларды біріктіре ұнтақтап немесе оларды ұнталған қалпында араластырып алатын, суда, ылғалды жерде де қатая беретін гидравликалық тұтастырғышты айтады. Қоспалардың активтігі жоғары болған сайын олардың цементке қосылар мөлшері аздау болады да цементтің сапасы жақсылау болады. Орташа мөлшермен шөкпелік жыныстық қоспаны (опока, диатомит, трепел және т.б.) 20...30 %, вулкандық тау жыныстарын 25...40 % қосады.
Активті минералды қоспаларды тікелей бетон араласпасына дайындар кезде сулап немесе құрғақ ұлпа күйінде қосуға болады.
Пуццоландық цементтің қатаю мезгілінде 2 процесс жүреді. Біріншісі - портландцемент клинкерінің минералдарының гидратациясы, екіншісі - активті минералдық қоспалардың С3S гидролизінен шығатын Са(ОН)2 әрекеттесу. Осының нәтижесінде Са(ОН)2 суда ерімейтін кальций гидросиликатына қосылады. Бұл қосындылар цемент тасының тығыздығын асырады. Бірақ активті минералдар қалыпты температурада бастапқы мезгілде кальций гидроксидімен баяу әрекеттеседі. Сондықтан пуццоландық цементтің бастапқы уақыттағы мықтылығы қоспасы жоқ порландцеметтегіден едәуір төмен болады. Дегенмен, біртіндеп қатая келе мықтылығы жетерліктей ұлғаяды. Бұл цемент әсіресе, суда немесе ылғалды ортада жақсы қатайып, мықтылығын ұлғайтады. Термиялық ылғалдықта, әсіресе, автоклавта өңдегенде оның мықтылығы жылдам көтеріледі.
Пуццоландық портландцемент 2 маркада шығарылады: М300 және 400. Пуццоландық портландцементтің су талапкерлігі 28...43 пайыз, яғни портландцементтегіден едәуір жоғары. Сондықтан оның аязға және ауаға төзімділігі төмен.
Пуццоландық портландцемент төмендеу температурада нашар қатаяды, ал қысқы кезде оны тіпті қолдануға болмайды.
Пуццоландық цемент тасының тығыздығы жоғары болатындықтан, оның су өткізбейтіндігі және тұщы суға тұрақтылығы жоғары. Сондай-ақ қатайған пуццоландық портландцементте Са(ОН)2 және 3СаО·Аl2O3·6H2O жоқ болғандықтан ол сульфатты суда да төзімді.
Пуццоландық портланцемент су астында және жер астында орналасатын үйлердің, метролардың, гидротехникалық биналардың бөліктеріне жұмсалатын бетон және темір бетон бұйымдары мен конструкцияларын жасауға пайдаланылады.
Пуццоланды портландцементтің өндіру технологиялық сызба қарапайым, портландцемент өндірсінен қағидалы айырмашылығы жоқ. Дегенмен енгізілетін қоспаның көбеюі технологиялық сызбаға қосымша бөлім қосуды және олардың қосылуымен кептіруді талап етеді. Уатқыштар үлгісі қоспа түріне байланысты таңдалады. Трепелдер, диатомиттер және болбыр жыныстарды білікті ұсақтағыштарда ұсақтайды. Белсенді минералды қоспалар жоғары ылғалдылыққа ие. Сондықтан оны 2 % дейінгі ылғалдылыққа кептіру міндетті технологиялық операциясы болып табылады. Кептіру үшін кептіргіш барабандарды қолданады, жылудың шығынын үнемдеу мақсатында және өндірісті арттыру үшін, қалқу қабатты материалдарды кептіру үшін оларды реакторлы қондырғылармен ауыстыру ұсынылады.
Пуццоланды портландцементтің ұнтақталуы шарлы диірменде ашық немесе тұйық циклда жүргізіледі. Клинкерді трепелмен немесе диатомитпен қосып ұнтақтағанда диірменнің өнімділігін 5...10 % арттырады, вулкан текті қоспалармен ұнтақтағанда диірменнің өнімділігі өзгермейді.
Глиноземді цемент
Глиноземдік цемент - тез катаятын гидравликалық байланыстырушы зат. Оны оптималды мелшерде бокситтен және әк тасынан тұратын шикізат араласпасын балқығанына дейін немесе куйдіріп алған өнімді ұнтақтау арқылы алады. Оның құрамында төменгі негізді кальцийлік алюминаты басым болады.
Портландцементтен және басқа цементтерден айырмашылығы – оған гипс те және активті минералдық заттар да қосылмайды.
Глиноземдық цементтің химиялық құрамы кеңаралық мөлшерде
сипатталынады, %: А12О3 – 35...50; SiO2 – 5...15; Fе2О3 – 5...15; СаО – 35...45; ТіО2 -1,5...2,6; MgO - 0,5...1,5.
Минералдық құрамы шикі араласпаның химиялық құрамына және өндіру тәciлiнe байланысты. Оның ең маңызды минералдарына мыналар жатады: СаО·А12О3 (СА);
12СаО·7А12О3 (С12А7); СаО·2А12О3 (СА2). Мұның ішіндегі глиноземдық цемент үшін ең маңыздысы СаО·А12О3 - кальций моноалюминаты. Осы минералдың арқасында глиноземдық цемент тез қатаяды.
Глиноземдық цемент көп әктілі (СаО>40 %) және аз әктілі (СаО < 40 %) болып eкiгe бөлінеді. Осыған сай минералдың құрамында және қатаю процесінде аздаған өзгерістер болады. Сондьқтан шикі араласпаның химиялық құрамын дайын өнімде СА мөлшері едәуір басым болатындай етіп дайындайды. Бокситтің құрамында құмның көрсетілген мөлшерден көп болғаны жарамсыз. Ceбeбi баяу қатаятын 2CaO·SiO2пайда болады да, глиноземдық цементтің сапасын төмендетіп жібереді.
Глиноземдык цементті өндipy.Оны екі тәсілмен өндіредi. Біріншici, ұнтақталған шикi араласпаны айналмалы пеште балқытуға жеткізе күйдіруге (1150...1250 °С) негізделген, ал eкіншici - вагранкада, электрлік және домналық пештерде (1500...1600 °С) түгел epiтin балқытуға негізделген.
Толық epiтiп қорытылған масса жайлап суытылады. Ceбeбi баяу суытылған кездегі құралған кристалдық кальций алюминатының байланыстырушы қасиеті жоғарылау болады. Бipaқ алынған клинкердің қаттылығы тiптi биік болады. Сондықтан оны қуатты ұсақтаушыларда алдын-ала екі стадиялық жүйе бойынша ұсақтап, сонан кейін доңғалақ диірменде ұнтақтайды. Қорытылған клинкерді ұнтақтауға кететін электрлік энергия балқыта алынған клинкерді ұнтақтауға жұмсалатын энергиядан eкi ece көп. Ұнтақтау процесін №008 електе 10 % пайыздан көп калмайтындай етіп жүргізеді.
Глиноземдік цементтің қатаюы кәдімгі портландцементтің қатаю процесіне ұқсас. Дегенмен, қатаюының химиялык негізінде бipaз ерекшелігі бар. Атап айтқанда, бip кальцийлік алюминат глиноземдік цементтің қатаю кезеңінде гидратацияланады, сөйтіп алдымен майда тілік сияқты 10 сулы гидроалюминат - СаО·А12О3·10Н2Окристалдарын құрады. Бұл жана құрылған қосынды мына темендегі жалпы химиялык теңдеу бойынша тұрақтылау екі кальцийлік гидроалюминатка көшеді.
2(СаО·А12О3) +11Н2О = 2СаО·Аl2О3·8Н2О + 2А1(ОН)3 (11.1)
СаО·А12О3 - температурасы 20...25 °С жағдайда қатайғанда үш кальцийлік гидроалюминаттың куб тәрізді кристалдары құралуы да мүмкін 3СаО·А12О3·6Н2О
2CaO·Al2O3·8H2O+CaO·Al2O3+H2O=3CaO·Al2O3·6H2O+2Al(OH)3
(11.2)
Химиялық жаңа құрама (қосынды) 3СаО·А12О3·6Н2О цемент тасының структурасын бостау eтiп құрайды. Ал, бұл гидраттык қосынды глиноземдык цемент жоғарылау температурада қатайганда пайда болады. Сондыктан жылу бумен өңдеу немесе кыздыру процестері глиноземдык цементтің мықтылығын және басқа құрылыстық қасиетін нашарлатып жібереді.
Глиноземдык цементті әкпен араластыруга болмайды, ceбeбi әк Са(ОН)2 суда бip кальцийлік алюминатпен өте тез әрекеттесіп үш кальцийлі гидроалюминат құрады:
СаО·А12О3 +2Са(ОН)2 +4Н2О = 3СаО·А12О3·6Н2О (11.3)
Осының нәтижесінде мықтылығы нашар үш кальцийлі гидроалюминаттың глиноземдык цементке тигізетін тepic әcepi күшейіп кетеді, оның сапасын тiптi нашарлатып жібереді. Осы себеп бойынша оны портландцементпен де араластыруга болмайды. Демек портландцемент қатайғанда пайда болатын Са(ОН)2, глиноземдық цемент қатайғанда пайда болатын А1(ОН)3 немесе кальций гидроалюминатымен тездете әрекеттесіп мықтылығы төмен 3СаО·А12О3·6Н2О құрады. Осының нәтижесінде реакция өрісінде Са(ОН)2 және А1(ОН)3 калмайды. Сондыктан, СаО·А12О3 және 3CaO·SiO2 гидролизі жылдамдатылады, ұстасу процесі лезде бiтедi, ал цемент тасының мыктылығы өте төмен болып шығады. Портландцементтің немесе глиноземдык цементтің қатаю процестерін тездетудің қажеті болғанда, жоғарыдағы айтылған жагдайларды еске алған жөн.
Глиноземдық цементтің қасиеттері. Глиноземдык цемент шапшаң қатайғанымен, баяу ұстасады. Ұстacy мезгілінің басы 30 мин ерте емес те, соңы 12 сағ кеш болмайды. Ұстасуын тездету үшін Са(ОН)2, CaSO4, NaOH, Na2SO4, H2SO4, NaCO3 және т.б. ерітінділерді қосады. Ал, ұстасу мезгілін баяулату үшiн хлорлық натрийді, калийді және барийді, тұз қышкылын қосады.
Глиноземдык цементке 10...20 % түйіршіктелген шлак қосқанда оның мықтылығы темендемейді. Одан көбірек қосып сондай-ақ тез қатаятын, бipaқ мыктылығы аздап төмендеу шлактық глиноземдық цемент алуға болады.
Глиноземдық цемент қатаю жағдайына өте сезімтал келеді. Бұл негізінде алынған бетонды ең аз дегенде 1 тәулік ылғалды жерде сақтау керек. Қатаю кезінде бетонның температурасы 25 °С аспағаны жөн. Олай болмағанда бетонның мыктылығы жылдам төмендеп кетеді. Осыған орай оның қатаю мезгілінің бастапкы 2...3 күннің ішінде, барлык гидратациялық жылудың 70...80 % бөлінеді. Оның үстіне бөлініп шығатын жылудың мөлшері жоғары экзотермиялык цементтегіден едәуір көп. Осы себептен глиноземдық цементті суық кездерде қолданған орынды. Бipaқ температура тiптi төмендеп кетсе, катаю тоқтап калады. Ал, массасы зор құрылыс бөлшектерін жасауға, күні ыстык аудандарда немесе жылумен өңдейтін бетон және темірбетон жасауға қолдануға глиноземдык цемент жарамайды.
Бұл цементтің нормальды қатаюы үшін температурасы 15...16 °С ылғалды орта керек.
Жоғарыда айтылған үш кальцийлік гидроалюминаттың зияндығын кетipyi үшін П.П. Будников глиноземдык цементке 20 ...30 % ангидрид қосуды ұсынған. Сонда ангидрит үш кальцийлік гидроалюминатпен мына төмендегі теңдеу бойынша әрекеттеседі:
3СаО·А12О3·6Н2О+3CaSO4+25Н2О=3СаО·А12О3·3CaSO4·31Н2О
(11.4)
осының нәтижесінде глиноземдық цементтің құрылыстық қасиеті жақсарады, массивті бетон биналарын соғу үшін де мүмкіндік туады. Құрылыста CaSO4 қосылған глиноземдық цементті ангидритті-глиноземдық цемент деп атайды. Бұл цемент жоғарыланған температурада қатайғанда, таза глиноземдык цементке қараганда мықтылығын едәуір көтеріңкі көрсетеді.
Глиноземдық цементтің маркасы құрамы 1:3 жылжымалы ерітіндіден жасалған өлшемі 40x40x160 мм үлгілерді 6 сағ соң суға салып, сақтап үш тәулігінде қысуға сынағандағы ең кішi мықтылык шегіне сай. МСТ 769-77 бойынша қазipri үш маркалык глиноземдық цемент шығарылады: М400, 500 және 600 маркаларына сай 3 сөткелік мықтылық нормасымен қатар бip сөткелік мықтылығы да нормаладанады. Ол - 23, 28, 33 МПа.
Глиноземдық цемент ұстасу мезгілі біткен соң, жеделдете қатая бастайды. Сумен араластырғаннан бастап бip сөтке өткен соң оның мықтылығы 28 сөткелік мықтылығының 80...90 % құрайды. Yш сөтке қатайғаннан кейін мықтылығы баяу өседі. 100 % қабылданған үш сөткелік мықтылығы 7 сөткеден кейін 120 % болады, 28 сөткеден кейін - 140 % және екі айдан кейін - 160 % болады. Ал, игендегі мықтылығы мұндай өспейді, қайта төмендеп кетуімүмкін.
Глиноземдық цементтен жасалған бетон және темірбетон бұйымдарының, конструкцияларының тығыздығы жетерліктей жоғары, су өткізбейді. Құрамында суда жeңiл еритін қосындылар жоқ. Сондықтан, оның минералданған суда төзімдігі биiк. Бipaқ ол сілтілердің әcepiнe шыдай алмайды, тез бұзылады.
Глиноземдық цементтің соншама жақсы қасиеттері болғанымен, оны алу үшін қaжeттi боксит жынысы сирек, бағасы портландцементтегіден 5...6 есе қымбат. Сондықтан, ол құрылыста портландцемент сияқты кең тараған емес. Құрылыста оның ерекше арнаулы касиеттерін: бip-eкi сөткелік мықтылығының жетерліктігін, қатайган кезде, әcipece бipiншi күндері, жылуды көп бөлiп шығаратындығын, агрессивтік ортаға төзімділігін және т.б. ерекшеліктерін толық пайдалануға мүмкіншілік бар жағдайда қолдану орынды болады. Оны жеделдеткен құрылыста, апатты жұмыстарда, ауыспалы кeyiп-құрғап, epiп-мұздап тұратын жағдайда пайдаланатын үй мен биналарды соғуға, мұнайлық және газдық ұңғымаларды тампондауға, отқа төзімді бетондар және кеңеюші цементтер жасауға қолдануға тиімдi.
Портландцементті және глиноземді клинкерлердің негізінде көлемі өзгеретін цемент, ұлғаюшы цементтер, су өткізбейтін ұлғаюшы цемент, гипсті-глиноземдық ұлғаюшы цемент, кернелуші цементтер т.б. өндіріледі.
Бақылау сұрақтары.
1. Қазақстанда қандай арнайы цементтер өндіріледі? 2. Жылдам қатаятын және жоғары маркалы цементтердің минералдық құрамы қандай болу керек? 3. Жылдам қатаятын цементтерге қандай талаптар қойылады? 4. Жылдам қатаятын және жоғары маркалы цементтердің өндіру технологиясында қандай өзгешіліктер болады? 5. Ақ портландцементтің клинкерінің химиялық және минералдық құрамында қандай өзгешіліктер болады? 6. Ақ және түсті портландцементтердің өндіру технологиясында қандай өзгешіліктер болады? 7. Сульфатқа төзімді цементтердің қандай маркалары, түрлері бар? 8. Сульфатқа төзімді портландцементтің минералдық құрамына МСТ 22266-97 қандай талаптар қояды? 9. Сульфатқа төзімді портландцементтің төзімділігі неге байланысты? 10. Беттік активті қоспалар қосылған цементтерге қандай талаптар қойылады? 11. Пластифицирленген және гидрофобты цементтерге қандай қоспаларды қосады, қандай мөлшерде? 12. Пластифицирленген және гидрофобты цементтердің қандай артықшылықтары бар? 13. Асбестцемент бұйымдарына арналған цементтерге қандай талаптар қойылады? 14. Аэродром және жол бетондарына арналған портландцементтерге қандай талаптар қойылады? 15. Тампонажды портландцементтер қайда пайдаланады, олардың түрлері қандай? 16. Тампонажды портландцементтерге қандай талаптар қойылады? 17. Шлакты портландцементтердің құрамы, маркалары қандай? 18. Шлакты портландцементтердің өндіру технологиясы, артықшылығы қандай? 19. Пуццоланды портландцементтерге қандай қоспаларды қосуға болады, қандай мөлшерде, макасы қандай? 20. Глиноземді цементтердің ерекшеліктері, құрамы қандай? 21. Глиноземді цементтерге қойылатын талаптар қандай?
ӘДЕБИЕТТЕР
1 Бажиров, Н.С. Химия и технология шлаковых цементов: учебное пособие / Н.С. Бажиров. – Шымкент, 2007. – 160 с.
2 Богданов, В.С. Механическое оборудование предприятий промышленности строительных материалов: учебник / В.С. Богданов. – Белгород, 1998. – 180 с.
3 Богданов, В.С. Основы расчета машин и оборудования предприятий строительных материалов и изделий: учебник / В.С. Богданов, Р.Р. Шарапов, Ю.М. Фадин и др. – Старый Оскол: ТНТ, 2013. – 680 с.
4 Бутт, Ю.М. Химическая технология вяжущих материалов: учебник / Ю.М. Бутт, М.М. Сычев, В.В. Тимашев. – М.: Высшая школа, 1980. – 472 с.
5 Бутт, Ю.М. Практикум по химической технологии вяжущих материалов: учебник / Ю.М. Бутт, В.В. Тимашев. – М.: Высшая школа, 1973. –504 с.
6 Горшков, В.С. Физико-химические методы исследования вяжущих веществ. / В.С. Горшков, В.В. Тимашев, В.Г. Савельев. - М.: Высшая школа, 1981. – 335 с.
7 Дуда, В. Цемент / В. Дуда. – М.: Стройиздат, 1981. – 463 с.
8 Журавлев, М.И. Механическое оборудование предприятий вяжущих материалов и изделий на их базе: учебник / М.И. Журавлев, А.А. Фоломеев. – М.: Высшая школа, 1983. – 239 с.
9 Карибаев, К.К. Поверхностно-активные вещества в производстве вяжущих материалов: монография / К.К. Карибаев – Алма-Ата: Наука, 1980. – 336 с.
10 Классен, В.К. Обжиг цементного клинкера: монография / В.К. Классен.- Красноярск: Стройиздат, -1994.–323 с.
11 Классен, В.К. Технология и оптимизация производства цемента: краткий курс лекций: учеб. пособие / В.К.Классен. – Белгород: Изд-во БГТУ, 2012. – 308 с.
12 Классен, В.К. Техногенные материалы в производстве цемента: монография / В.К. Классен, И.Н. Борисов, В.Е. Мануйлов; – Белгород: Изд-во БГТУ, 2008. – 126 с.
13 Кожамуратов, С.К. Портландцемент өндірісінің технологиясы: оқулық / С.К. Кожамуратов, Б.Т. Таймасов. – Алматы: Рауан, 1994. – 222 с.
14 Кравченко, И.В. Химия и технология специальных цементов: учеб. пособие / И.В. Кравченко, Т.В. Кузнецова, М.Т. Власова, Б.Э. Юдович. – М.: Стройиздат, 1979. - 208 с.
15 Кузнецова, Т.В. Физическая химия вяжущих материалов: учебное пособие / Т.В. Кузнецова, И.В. Кудряшев, В.В. Тимашев. – М.: Высшая школа, 1989. –384 с.
16 Лисиенко, В.Г. Вращающиеся печи: теплотехника, управление, экология / В.Г.Лисиенко, Я.М. Щелоков, М.Г Ладыгичев.: Справочное издание: В 2-х книгах. Книга 1 / Под ред. В.Г.Лисиенко. - М.: Теплотехник, 2004. – 688 с.
17 Лисиенко, В.Г. Вращающиеся печи: теплотехника, управление, экология / В.Г.Лисиенко, Я.М. Щелоков, М.Г Ладыгичев.: Справочное издание: В 2-х книгах. Книга 2 / Под ред. В.Г.Лисиенко. - М.: Теплотехник, 2004. – 592 с.
18 Лугинина, И.Г. Химия и химическая технология неорганических вяжущих материалов: учебное пособие / И.Г. Лугинина. – Белгород: Изд-во БГТУ им. Г.Шухова, 2004.– Ч. 1. – 240 с. – Ч. 2. – 199 с.
19 Пащенко, А.А. Вяжущие материалы. 2-ое издание: учебник / А.А. Пащенко, В.П. Сербин, Е.А. Старчевская. – Киев: Вища школа, 1985. – 440 с.
20 Попов, К.М., Каддо М.Б. Строительные материалы: учебник / К.М. Попов, М.Б. Каддо. – М.: Высшая школа, 2001. – 367 с.
21 Попов Л.М. Лабораторный контроль строительных материалов и изделий: справочник / Л.М. Попов. – М.: Стройиздат, 2001. – 320 с.
22 Правила технической эксплуатации цементных заводов. – М.: Госстройиздат, 1987. – 252 с.
23 Рояк, С.М. Специальные цементы: учебное пособие / С.М. Рояк, Г.С. Рояк. – М.: Стройиздат, 1983. – 279 с.
24 Сидоров, В.И. Химия в строительстве: учебник для вузов / В.И.
Сидоров, Э.П.Агасян, Т.П.Никифорова и др. – М.: АСВ, 2007. – 312 с.
25 Строительные материалы: Справочник. / Под ред. А.С. Болдырева, П.П.Золотова. – М.: Стройиздат, 1989. - 567 с.
26 Сулименко, Л.М. Технология минеральных вяжущих материалов и изделий на их основе: учебник. Изд. 3-е перераб. и допол. / Л.М. Сулименко. – М.: Высшая школа, 2000. – 304 с.
27 Таймасов, Б.Т. Цементы на основе техногенных отходов и магматических пород: монография / Б.Т. Таймасов, Б.О. Есимов, С.В. Терехович, Р.К. Куралова. – Шымкент: Изд-во NORIS, 2002. – 163 с.
28 Таймасов, Б.Т. Технология производства портландцемента: учебное пособие / Б.Т. Таймасов. – Шымкент: Изд-во ЮКГУ, 2004. –293 с.
29 Таймасов, Б.Т. Тұтастырғыш заттардың химиялық технологиясынан лабораториялық практикум: оқу құрал / Б.Т. Таймасов. - Шымкент: ОҚМУ, 2007. – 157 б.
30 Таймасов, Б.Т. Тұтастырғыш заттардың арнайы технологиясы: оқу құрал / Б.Т. Таймасов, А.Ж. Әлжанова, М.С. Даулетияров. - Шымкент: ОҚМУ, 2012. – 108 б.
31 Таймасов, Б.Т. Лабораторный практикум по дисциплине ХТВМ. Часть 2: учебное пособие / Б.Т. Таймасов. – Шымкент: Изд-во ЮКГУ, 2006. – 111 с.
32 Таймасов, Б.Т. Специальная технология вяжущих материалов: учебно-методическое пособие / Б.Т. Таймасов, А.Ж. Альжанова, М.С. Даулетияров. - Шымкент: Изд-во ЮКГУ им.М. Ауезова, 2012. - 113с.
33 Тейлор, Х. Химия цемента. Пер. с англ.- М.: Мир, 1996. – 560 с.
34 Теория цемента /Под ред. А.А.Пащенко. – Киев, Будивельник, 1991. –168 с.
35 Худякова Т.М. Специальная технология вяжущих материалов. Учеб. пособие. – Шымкент, Изд-во ЮКГУ. 2010. – 160с.
36 Шетел фирмаларының рекламмалық проспекттері: KHD Humboldt Wedag, HAZEMAG, Polisius, Thissen Krupp, Claudius Peters, Aumund, Schenck (Германия), FLSmidth (Дания), Loesche (Франция).
37 Журналдар: «Цемент и его применение», «Техника и технология силикатов», «Строительные материалы ХХ1 века», «Строительные материалы», «Промышленность Казахстана».
МАЗМҰНЫ
Кіріспе..............................................................................................3
І тарау Тұтастырғыш заттардың жалпы сипаттамасы
1.1 Цемент өндірісінің қысқаша тарихы.....................................5
1.2 Тұтастырғыш материалдар өндірісінің Қазақстандағы және шет елдегі заманауи жағдайы. Саланың өркендеуінің келешегі ....9
1.3 Тұтастырғыш заттардың, цементтердің және
қоспалардың жіктелуі.........................................................................15
1.4 Құрғақ құрылыс қоспалардың жіктелуі және құрамы........18
Бақылау сұрақтары........................................................................20
ІІ тарау Портландцемент. Шикізат материалдары
2.1 Портландцементтің құрамы және жалпы сипаттамасы.... 21
2.2 Портландцемент клинкерінің химиялық құрамы.............22
2.3 Клинкердің минералдық құрамы...........................................24
2.4 Қанығу коэффициенті және модульдер.............................28
2.5 Клинкердің құрылымы..........................................................30
2.6 Клинкердің химиялық-минералдық құрамын анықтау тәсілдері ..............................................................................................31
2.7 Портландцемент өндірісіне қажетті шикізаттар...............32
2.8 Шикізат пен техногенді өнімдерді комплексті түрде пайдалану, шикізаттың басқа түрлері............................................37
2.9 Шикізат қоспаларының құрамын есептеу тәсілдері......43
Бақылау сұрақтары........................................................................49
ІІІ тарау Шикізат қоспасын дайындау технологиясы
3.1 Клинкер шығарудың тәсілдері..............................................50
3.2 Шикізат өндіру және тасымалдау .......................................53
3.3 Шикізат материалын ұсақтау..............................................58
3.4 Біртектілеу қоймалары...........................................................63
3.5 Құрғақ тәсілмен шикізат материалдарын ұнтақтау ............65
3.5.1 Орташа жүрістегі диірмендердің жіктелуі және кинематикалық схемасы....................................................................65
3.5.2 Ортажүрісті диірменнің құрылысы және жұмыс
істеу принципі....................................................................................67
3.5.3 Шикізат материалдарды білікті диірменде ұнтақтау жұмысының сипаттамасы.................................................................69
3.5.4 Шетел фирмаларының кептіргіш-ұсақтағыштары........76
3.5.5 Құрғақ тәсілдегі сепараторлар...........................................82
3.6 Шикізатты ылғал әдісімен ұнтақтау.....................................85
3.7 Шикізат қоспасын түзету және біртектілеу.........................92
3.8 Шикізат шламның қасиеттері.................................................95
Бақылау сұрақтары.......................................................................102
IV тарау Шикізат қоспасынан клинкер алу
4.1 Шикізат қоспасы компоненттерінің термиялық өзгерістері...........................................................................................103
4.2 Шикізат шламын сусыздандыру...........................................103
4.3 Жеке компоненттердің қыздыру кезіндегі өзгерістері.......104
4.4 Қатты күйдегі реакциялар ....................................................109
4.5 Сұйық фазада жүретін реакциялар....................................117
4.5.1 Сұйық фазаның құрамы, құрылымы және мөлшері...117
4.5.2 Клинкер балқымасының қасиеттері.................................119
4.5.3 Клинкердің сұйық фазалық жентектелуі.........................123
4.5.4 Үш кальцийлі силикаттың кристалдануы......................125
4.6 Клинкер салқындату кезінде жүретін процестер...............126
4.7 Клинкер түзілу процесінің термохимиясы..........................127
4.8 Әр түрлі технологиялық факторлардың клинкер күйдіру процесіне тигізетін әсері ................................................................130
4.9 Сулы әдістің пештерінде клинкер куйдірудің технологиялық процесі................................................................................................148
4.9.1 Ішкі жылуалмастырғыштармен жабдықталған айналмалы пештердің құрылымы және жұмыс істеуі.......................................148
4.9.2 Газ бен материалдың пеште қозғалуы. ...........................152
4.9.3 Газ бен материалдың температурасы. Жылу алмасу.....153
4.9.4 Сулы әдістің айналмалы пештерінің технологиялық алаптарында жұретін процестер ...................................................154
4.9.5 Пештің ішінде сақиналардың пайда болуы..................158
4.9.6 Күйдіру пештерінде шаңның түзілуі және оны технологиялық процеске қайтару жолдары....................................165
4.9.7 Клинкер пайда болу процесін реттеп жеделдету........168
4.9.8 Айналмалы пештің жылу балансы және өнімділігі.....170
4.9.9 Сулы әдістің айналмалы пешінің алаптары бойынша жылулық процестер .........................................................................173
4.9.10 Сулы тәсілді пештің материалдық және жылу балансы173
4.10 Конвейерлі кальцинаторлы, шламды шоғырландырғышты, бүркүіш кептіргішті және шахталы пештер..................................176
4.11 Құрғақ тәсілдің пештері......................................................180
4.11.1 Циклонды жылу алмастырғышы бар пештердің құрылымы және жұмыс істеуі........................................................180
4.11.2 Циклонды жылу алмастырғыштармен және декарбонизатормен жабдықталған пештер .................................184
4.11.3 Заманауи құрғақ тәсілді декарбонизаторлы пештердің түрлері................................................................................................186
4.11.4 Қалдықты түтінді газда NOx мөлшерін төмендету жолдары және жылуалмастырғыштардың жұмысын оңтайландыру...........188
4.11.5 Кедергісі төмен циклонды жылуалмастырғыштар.......189
4.11.6 Материалдың түсіп кетуі және салқын ауаның сорылуы (қосылуы) отын шығынына әсері....................................................192
4.11.7 Құрғақ тәсілдегі пештерді шикізат ұнымен қоректендіретін жүйелер..................................................................194
4.11.8 Құрғақ тәсілді пеш жүйесінің материалдық және жылу балансы .............................................................................................194
4.11.9 FLSmidth компаниясының ILC жылуалмастырғышының жұмысы.............................................................................................196
4.11.10 Құрғақ тәсілдің жылуалмастырғыштарында настыль пайда болу.........................................................................................198
4.11.11 Циклондардың бітеліп қалу (зарастание) себептері ..201
4.11.12 Декарбонизаторлы пеш жүйесін басқаруының принципиалды схемасы...................................................................202
4.12 Клинкерді салқындату және клинкерлік мұздатқыштар.204
4.12.1. Клинкерді салқындатудың мақсаттары .........................204
4.12.2 Рекуператорлы (планетарлы) және барабанды мұздатқыштар...................................................................................204
4.12.3 Колосникті итергіш мұздатқыштар................................207
4.12.4 Клинкер түсірмейтін торлы мұздатқыштар...................210
4.12.5 Колосникті тордың жұмыс істеу принципі....................213
4.12.6 Мұздатқыштағы клинкер ұсақтағыштар........................214
4.12.7 Клинкерлі шаңдату және оны жою жолдары................216
4.13 Клинкер өндірудің басқа тәсілдері ...................................219
4.14 Клинкер өндірісіндегі қолданылатын отындар ............223
4.14.1 Айналмалы пештегі «қысқа», «ұзын», «ұзақ» алаптар. Ауаның артықшылық коэффициенті. Пештегі жылуалмасу........223
4.14.2 Қатты, суйық және газтәрізді отындар. Олардың қасиеттері. Отын ретінде қалдықтарды пайдалану ......................225
4.14.3 Қатты отынды жағуға дайындау.....................................228
4.14.4 Жалын кеңістігінде отын жағуды оңтайландыру..........229
4.14.5 Айналмалы пеште отын жағуды оңтайландыру............231
4.14.6 Айналмалы пештің жанарғы құрылғылары …….......234
4.15 Энергия үнемдейтін, ресурс- энергия шығыны төмен технологиялар...................................................................................236
4.15.1 Портландцемент өндірісінің аз энергиялы ресурс үнемдейтін технологиясы ..............................................................236
4.15.2 Портландцемент өндірісінің ресурс үнемдейтін
карьерсіз технологиясы...................................................................238
Бақылау сұрақтары.....................................................................243
V тарау Клинкер мен қоспаларды ұнтақтау
5.1 Клинкерді ұнтақтау процесінің теориялық негіздері...... 244
5.2 Барабанды диірмендерде ұнтақтау....................................248
5.3 Клинкер мен қоспаларды ұнтақтау және цемент алу.......260
5.4 Жаңа заманауи цемент ұнтақтайтын агрегаттар...............264
5.5 Полизиус фирмасының білікті (роликті) диірмендері......264
5.6 Loesche фирмасының білікті цемент диірменінің құрылысы және жұмыс істеу принципі........................................266
5.7 Loesche LSKS динамикалық сепараторы, ыстық газдың генераторы және қалақтық қоректендіргіш...................................271
5.8 Шарлы құбырлы диірмендерді модернизациялау.............274
5.9 Әр түрлі технологиялық факторлардың диірменнің жұмысына көрсететін әсері.............................................................275
5.10 Ұнтақтау процесін ПАВ қоспаларымен жеделдету.......284
5.11 Цемент диірмендерін аспирациялау….............................286
5.12 Клинкер және цемент қоймалары. ...................................286
5.13 Цемент өндірісінде шаңсыздандыру ...............................293
5.14 Цементті тұтынушыларға артып жіберу..........................298
5.15 Цемент өндірісіндегі бақылау жұмыстары…..................300
5.16 Өнімді паспорттандыру.....................................................302
Бақылау сұрақтары.....................................................................303
VΙ тарау Өндірісті автоматтандыру........................304
VΙΙ тарау ЕҢБЕК ҚАУІПСІЗДІГІ, ЭКОЛОГИЯ ЖӘНЕ ҚОРШАҒАН ОРТАНЫ ҚОРҒАУ
7.1 Еңбек қауіпсіздігі .............................................................317
7.2 Көмір ұнтақты дайындағанда қауіпсіздік шаралары.......320
7.3 Экология және қоршаған ортаны қорғау..........................321
Бақылау сұрақтары.....................................................................323
VІІІ тарау Портланцементтің гидратациясы
және қатаюы
8.1 Минерал кристалдарының сумен әрекеттесу механизмі324
8.2 Минералдардың гидратациясы және оның кинетикасы..325
8.3 Клинкер минералдарының гидратациялық өнімдері........331
8.4 Портландцемент гидратациясы..........................................334
8.5 Беріктігі жоғары цементті синтездеу.................................339
8.6 Кейбір технологиялық факторлардың цемент гидратациясына тигізетін әсері......................................................340
Бақылау сұрақтары.....................................................................344
ІХ тарау ЦЕМЕНТ ТАСЫ МЕН БЕТОННЫҢ КОРРОЗИЯСЫ
9.1 Физикалық коррозия ............................................................345
9.2 Химиялық коррозия..............................................................347
Бақылау сұрақтары..................................................................... 350
X тарау ПОРТЛАНДЦЕМЕНТТІҢ ҚҰРЫЛЫС –
ТЕХНИКАЛЫҚ ҚАСИЕТТЕРІ.......................................................351
Бақылау сұрақтары..................................................................... 355
XІ тарау АРНАЙЫ ЦЕМЕНТТЕР. ШЛАКТЫ,
ПУЦЦОЛАНДЫ ЖӘНЕ ГЛИНОЗЕМДІ ЦЕМЕНТТЕР
11.1 Арнайы цементтер.............................................................356
11.1.1 Жылдам қатаятын және жоғары маркалы цементтер..356
11.1.2 Ақ және түсті портландцементтер................................357
11.1.3 Сульфатқа төзімді портландцементтер .......................359
11.1.4 Беттік активті қоспалар қосылған цементтер.............360
11.1.5 Асбестцемент бұйымдарына арналған цемент ...........362
11.1.6 Аэродром және жол бетондарына
арналған портландцемент................................................................362
11.1.7 Тампонажды портландцементтер...................................362
11.2 Шлакты портландцемент...................................................366
11.3 Пуццоланды портландцемент...........................................367
11.4 Глиноземді цемент..............................................................369
Бақылау сұрақтары.......................................................................373
ӘДЕБИЕТТЕР...............................................................................374
МАЗМҮНЫ...................................................................................377
Бақытжан Таймасов,
Айсұлу Жаңабайқызы Әлжанова
Тұтастырғыш заттардың
химиялық технологиясы
Ғылыми редактор, техника ғылымдарының кандидаты,
доцент Айтөреев М.Ж.
|
Басуға 18.04.2013ж. қол қойылған. Қағаз пішімі 60х84 1/16
Офсеттік басылым. Көлемі 24,0 б.т. Таралымы 300 экз. Тапсырыс № 250.
М.Әуезов атындағы ОҚМУ баспаханасы.
Шымкент қ. Тәуке хан даңғылы, 5
Дата добавления: 2019-02-22; просмотров: 1347; Мы поможем в написании вашей работы! |
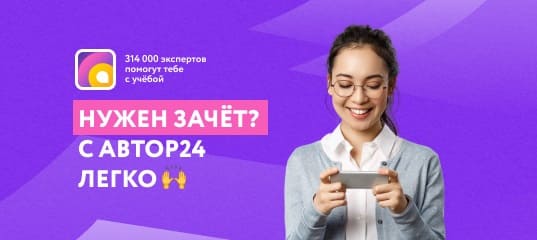
Мы поможем в написании ваших работ!