Портландцемент. Шикізат материалдары 24 страница
Сілтілі тотықтың әрбір проценті анионды бөлікпен және кальций карбонатымен әрекеттесткенде 4...5 % сұйық фаза пайда болады: KCl – K2SO4 (690 0C); K2CO3 – CaCO3 (745 және 795 0C); K3Na(SO4)2 - CaCO3 (820 0C); K2SO4 – CaCO3 (880 0C). CaCO3 декарбонизацияланып ұшқыш компоненттер төмендегі схемалармен айналдырылғасын (возгонка) сұйық фазаның үлесі төмендеп, масса кристализацияланып, қатайып шор мен сақиналар пайда болады.
R2Ca(CO3) + CaCO3 + SiO2 → R2 CO3 + 2C2S ·CaCO3 → C2S + CaO + + R2O↑+ CO2↑ (4. )
Төменнегізді сақиналардың пайда болу себептері және оны жою жолдары. Төменнегізді (низкоосновные) сақиналар жентектелу алабының басында жиі пайда болады. Бұл сақиналар ашық сұр түсті, толық күйдірілмеген цемент клинкерінен құралады, бос СаО жоғары мөлшерде (5...10 %). Сақинаның беріктігі жоғары, кейбір кезде жентектелу алабының жағылмасының (обмазка) беріктігінен жоғары. Бұл мәселе төмен температурада осы режимде материалды күйдіргенде балқыманың көп мөлшерде пайда болғанын көрсетеді. Декорбанизациялау алабында материал жоғары жылдамдықпен қозғалғанда жылулық процестер химиялық реакциялардан жылдам жүреді. Бұл жағдайда 1200...1300 0C дейін төмен негізгі минералдар пайда болады. Олар балқыманың 50%-не дейін құрайды. Содан кейін кальций оксиді қосылып С2S және С3S кристалданады, сұйық фазаның мөлшері төмендеп шорлар пайда болады. Алғашқы кезде сақина пайда болып, ол уақыт өте өзінен-өзі дамиды, сақинаның бетіндегі температура жоғарылап оған материалдың жаңа порциялары жабысады. Сонымен, бұл сақиналардың пайда болу себебі жентектелу алабының алдындағы материалдың жеткіліксіз дайындалып келуі және бұл жердегі жылылық даланың (поле) контрастының жоғарлығы. Бұл жағдай айналмалы пештің қысқа, жоғары температуралы, ұзақ орналасқан (дальний факел) алаумен жұмыс істегенде байқалады. Бұндай сақиналар пайда болмас үшін отын жағуды реттеу керек, температуралық максимум 12±1 м орналасу қажет, оттықтағы (горелка) газдың жылдамдығын төмендетіп, артық ауаны қысқартып, ауаның көлемін азайтып, екіншілік ауаның температурасын жоғарылатып, алауды материалға жақындатып клинкерді күйдіру керек.
|
|
Клинкерлі сақиналардың пайда болу себептері және оны жою жолдары. Клинкерлі сақиналар жентектелу және салқындату алаптарының түйісінде (стык) пайда болады. Олардың пайда болу механизмі клинкерлі балқыманың тез кристаллизациясымен байланысты. Себебі алаптардың шекарасындағы жоғары контрастты дала (поле). Сақынаның пайда болуына қысқа жылу кернеуі жоғары алау және салқын екіншілік ауа алып келеді. Бұл процесс өзінен-өзі дамиды. Алғашқыда кішігірім сақина пайда болса, оның жиегі (кромка) одан бетер салқындайды, ал сақинаның алдындағы клинкер одан бетер ысыйды, содан соң салқындаған жиегінен сақина тез өсіп кетеді.
|
|
Бұндай сақина пайда болмас үшін ұзын алауда жұмыс істеу керек, екіншілік ауаның температурасын жоғарылатып, кешке ыстық жағынан салқын ауаны кіргіздірмей, тығыздарды жақсарту қажет.
Айналмалы пеште сақина пайда болудың механизмі. Сонымен зерттеулер нәтижесінде жоғарыдағы айтылған сақиналардың 5 түрінің пайда болуының біріңғай механизмі табылды. Сақиналардың пайда болуы сұйық фазамен байланысты.
Сақиналардың бірінші және екінші түрі шикізат шламынан судың кеуіп, материал қатайып, сілтілі тұздар кристалданып масса цементациясымен байланысты. Үшінші типті материалды – тұзды сақиналар декарбонизация алабында 750…900 0С жоғары қозғалғыш эвтектикалық балқыманың себебінен пайда болады. Ол эвтектика сілтілі тұздар мен кальций карбонатының жүйесінде түзіледі. Карбонатты балқыма материалды үлкен массасына сіңеді, температура жоғарылағанда жүйеден СО2 бөлінеді, балқыманың мөлшері төмендеп тұтқырлығы жоғарылайды, сақинаның материалы қатып қалады.
|
|
Сақинаның тқртінші түрі пайда болғанда силикатты балқыманың негіздігі төмен болғасын 1200…1300 0С сұйық фаза көп мөлшерде құрылады. Сұйық фаза СаО мен әрекеттесіп оның мөлшері төмендейді, одан жоғары негізді силикаттар кристалданып сақина қатып қалады. Күйдірудің соңғы кезеңінде, салқындату алабында клинкерлі балқыма салқындату себебінен жоқ болып кетеді. Клинкер бұл жерге ыстық болып келеді, құрамында балқыма мөлшері көп болады, тез салқындағасын сақина түзіледі.
|
|
4.9.6 Күйдіру пештерінде шаңның түзілуі және оны технологиялық процеске қайтару жолдары
Шаңға өлшемі 1 мм төмен бөлшектерді жатқызады. Күйдіру пештерінде шаң көбіне дайындық алабында материалдың шынжырларға және футеровкаға үйкеліп қажалуынан, механикалық жолмен бұзылуынан пайда болады. Ылғалдылығы 0...5 % материалдың шынжырлар алабының соңында 30...40 % шаң ретінде болады. Шикізат гранулдар қыздыру және кальцилену алабында үйкеліп, бұзылып, шаңға айналып жатады. Жалпы материал жентектелу алабына барғанша оның 60...70 % шаң құрайды. Цемент өндірісінде бүл шаңның көп бөлігі түтінді газбен бірге пештен шығып шаңсүзгіште ұсталады. Кей бір жағдайда клинкер шаңы салқындату алабындада пайда болады. Пештен шығып кететін шаңның мөлшеріне күйдіріліп жатқан шикізаттың түрі, пештегі газдың жылдамдығы, жылу алмастырғыш құрылғылардың, сондай-ақ пештің құрылысы де әсер етеді. Пештің конструкциясына байланысты шаңның мөлшері де әр түрлі болады. Мәселен, пештен шыққан шаң-тозаңның мөлшері цемент өндірудің ылғалды әдісінің ұзын пештерінде 6...30 %, конвейерлі кальцинаторы бар пештерде 1,5...9 %, циклоны жылу алмастырғышы бар пештерде 25...30 % құрайды.
Ылғалды әдістегі ұзын пештердің шаңы құрғақ әдістегі циклонды жылу алмастырғышы бар пештердің шаңына қарағанда майда, ұнтақ келеді.
Шаңның құрамы негізінен күйген саздан және ыдырап үлгермеген әктастан тұрады. Шаңның құрамында 10...20 % клинкер минералдары болады: β және γ-С2S (8...10 %), С2F және С4АF (10...12 %), С3S болмайды. Шаңның құрамында клинкер мөлшері жоғарылағанда бос СаО саны 2...14 %-ке жетеді. Жоғары мөлшерде сілтілер және сульфаттар болады. Сілтілі қосылыстар натрий мен калийдің сульфаты, карбонаты және бикарбонаты ретінде кездеседі. Электрофильтр сүзгішінде ұсталған шаңның құрамында К2О және Nа2О мөлшері 0,3-тен 45 % дейін өзгереді, оның көбі калий тотығы болады. Электрофильтрдің 3 бөлігінде ұсталған шаңда сілтілер мөлшері 1, 2 өрістегі шаңнан 3...4 есе көп. Жалпы электрофильтрде ұсталған шаңда 1...8 % сілтілер, 0,5...7 % кальций сульфаты болады. Шаң тұндырғыш камерада ұсталған шаңның үлестік беті 2500...3200 см2/г құрайды, электрофильтрде - 5300...6300 см2/г.
Сүзгіштерде ұсталынған айналмалы пештердің шаңын өндірістік процеске қайтару керек. Цемент зауыттарында шаңды айналмалы пештерге әр түрлі тәсілдермен қайтарады: 1) құрамындағы сілтілердің мөлшері төмен болса шикізат лайына немесе шикізат ұнына қосып араластырады; 2) шаң онша көп болмаған жағдайда оны пештің ыстық соңынан үрлейді; 3) шаңды сол күйінде немесе түйірлендіріп пешке шынжыр аспалардан кейін береді; 4) пешке құрамы тұрақтандырылып, жеке пеште күйдіріледі; 5) шаңды сілтіден айырып пешке береді. Ірі зауыттарда шанды жеке пеште күйдірген тиімді.
Шикізат шламына немесе шикізат ұнына пешке беруден алдын қосылған электрофильтр шаңы шихтамен жақсы араласып сапасы жоғары клинкер алуға мүмкіндік береді. Құрғақ тәсілдегі шикізат ұнының және электрофильтр шаңының физикалық қасиеттері жақын, сол үшін шаңды технологиялық процеске қайтару оңай. Шаңды жабдықтағышпен құбыр арқылы пешке береді, немесе пневмотасымалдағышпен шикізат ұнының силосына қайтарады. Шаңды жақсы араласу үшін тіптен шикізат диірменіне де қайтаруға болады.
Құрамындағы сілтілер саны 2,0... 3,6 % шаңды пешке осы тәсілмен қайтарғанда клинкер күйдіру процестері нашарлаған жоқ. Ал шаңның құрамында сілтілі сульфаттар басым болса олар клинкер пайда болу процестерін жеделдетіп минерализатор ролін атқарады. Шаңның майда ұнтақтылығы СаО-ның тез байланысуына алып келеді, сілтілер төмен температурада сүйық фазаның пайда болуына себеп болады. Бұл факторлар сілтілердің клинкер куйдіру процесіне көрсететін зиянды әсерін төмендетеді немесе жояды. Клинкер құрамындағы сілтілер сульфаттары оптималды мөлшерде минералдардың формасын жақсартады, сілтілер көбейіп кетсе кристалдану нашарлап, формасы дұрыс емес дефектілі кристалдар пайда болады.
Құрғақ шаңды пешке құбыр арқылы бергенде бірнеше қиындықтар туады. Шаң құбырға жабысып тесігін бітеп тастайды, сүйық шлам құрғақ шаң қосылғасын тез қоюланып шынжырларға жабысып қалады, шламды сақиналар пайда болуына алып келеді. Бүл жүйе дұрыс жұмыс істеу үшін шаңды сумен араластырып құбыр арқылы пешке беруге болады. Қиындықтары көп болған соң бүл тәсіл кең тарамады.
Кең тараған тәсіл ол шаңды пештің ыстық жағынан үрлеп беру, немесе шынжырлар алабына құбырмен жіберу. Бүл тәсілде шаңның реакциялық қабілеттілігі, берілетін шаңның мөлшері, пайдаланатын отынның түрі және жентектелу алабының жылулық кернеуі үлкен рөл атқарады.
Пештің ыстық соңынан үрлейтін шаңның мөлшері 8...10 % болғаны жөн. Бұл кезде пештің өнімділігі жоғарылап, температура төмендеп футеровканың төзімділігі асады, клинкер күйдіруге жүмсалатын отын шығыны төмендейді. Бүл тәсілдің кемшілігі – пештің ішіндегі көрінім төмендейді, пештен шығатын шаң мөлшері жоғарылайды.
Жентектелу алабына шаң көп мөлшерде берілсе пештегі температура төмендеп байланыспаған СаО жоғарылауы мүмкін. Берілген шаң толық клинкермен әрекеттеспей клинкердің сапасы төмендеуі мүмкін. Салқындату алабында клинкерге қонған шаң өнімнің сапасын төмендетеді.
Шаңға су қосып, тарелкалы грануляторда гранулдап пештің салқын жағынан құбыр арқылы шламмен қосып, немесе құбырмен шынжырлар алабына беруге болады. Грануляторда алынған гранулдардың беріктігі жоғары, термиялық шыдамды болады. Бұл тәсілдің кемшілігі ол отын шығынының жоғарылауы және гранулятор соғу және эксплуатациялау үшін шығындардың қажеттілігі. Гранулдың құрамындағы суды кептіруге қосымша жылу жумсалады.
Электр сүзгілерінде ұсталған шаңды аралас тұтастырғыш заттар алуға, силикат кірпіш пен бетон өндірісінде жартылай әктің орнына қолдануы мүмкін. Бірақ шаңдағы сілтілердің мөлшері 2...4 % аспауы керек. Құрамындағы сілтілердің мөлшері өте жоғары болса, әрі сілтілер карбонаттар түрінде болса, шаңды шлакты сілтілі тұтастырғыш заттар өндіруде сілтілі компонент ретінде қолданады, онымен қатар бұндай шаң тыңайтқыш есебінде де қолданылуы мүмкін.
Пештің жентектелу алабының соңында және салқындату алабында клинкерлі шаң пайда болады. Оның бірнеше себебі бар. Біріншіден жентектелу алабындағы клинкердін жеткіліксіз агломерациясы. Қанығу коэффициент, n, p жоғары болғанда клинкердің майда бөлшектері іріленбей шан ретінде қалып кетеді. Бұл майда бөлшектер ірі гранулдарға жабысып үлгермеген. Бүл себептен 1...3 % клинкерлі шаңның пайда болуы мүмкін.
Мұндай клинкерлі шаң пайда болмас үшін материал пеште 1300...1450 0С ұзағырақ ұақыт болу керек. Ол үшін жентектелу алабының ұзындығын отын мен ауаның пешке берілу жылдамдығын өзгертіп реттеуге болады.
Клинкерлі шаң пайда болудың екінші себебі ол күйдірілген материалдың бетінің пештің салқындату алабында футеровкаға және мұздатқышта үйкелуі. Ірі бөлшектерге жабысқан шаң үйкелген кезде бөлініп ауамен алып кетіледі.
Үшіншіден, клинкерлі шаңның пайда болуы материалдағы сілтілі сульфаттар мен байланыстар. Жоғары сілтілі шихталарды күйдіргенде клинкердің кеуектігі жоғарылап беріктігі төмендейді. Бұл клинкер үйкеліп салқындату алабында және мұздатқышта шаң пайда болады.
Клинкерлі шаң пайда болудың төртінші себебі β–C2S–тің полиморфты γ - C2S өзгеруі. Бұл кезде фазаның көлемі 10 % ұлғайып клинкер шашылып кетеді. Бұл процес β–C2S жақсы стабилизацияланбағанда болады.
Дата добавления: 2019-02-22; просмотров: 316; Мы поможем в написании вашей работы! |
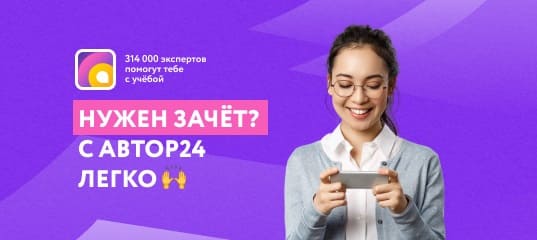
Мы поможем в написании ваших работ!