Классификация заготовительных производств
Детали в механообрабатывающем производстве получают из заготовок. Заготовка – предмет труда, из которого изменением формы, размеров, свойств поверхности и (или) материала изготавливают деталь. На заготовительных операциях заготовку приводят к форме и состоянию наиболее удобным для дальнейшей обработки механической, термической, гальванической или другим видом обработки, связанной с получением готовой детали. Выбор заготовки зависит от формы детали и ее размеров, исходного материала, типа и вида производства, наличия необходимого оборудования, требования к качеству готовой детали, экономичности изготовления. При выборе заготовки необходимо стремиться к выбору такой конструктивной формы заготовки, которая бы максимально приближалась к форме и свойствам готовой детали.
![]() |
Существуют различные способы получения заготовок (рис. 1.1). Каждый из них имеет определенные достоинства и недостатки. Выбор способа получения заготовки определяется экономическими расчетами.
Для минимизации затрат в основном производстве в металлургической промышленности изготавливают некоторые виды полуфабриката, имеющие нормализованную (стандартную) форму и свойства, например сортовой прокат.
Прокат
Прокаткеподвергают до 90 % всей выплавляемой стали и большую часть цветных металлов. Форму поперечного сечения прокатанной полосы называют профилем. Совокупность форм и размеров профилей, получаемых прокаткой, называют сортаментом [58]. Сортамент прокатываемых профилей разделяется на четыре основные группы (рис. 1.2): сортовой прокат, листовой прокат, производство труб и специальный прокат.
|
|
Прокат обычно производится на металлургических предприятиях, однако специальный прокат может получаться и на машиностроительных предприятиях (например, алюминиевые или др. профили).
Прокат может выпускаться с различными добавками, улучшающими те или иные свойства металла. Например, автоматные стали, выпускаемые специально для последующей обработки на станках-авто-матах (токарно-револьверных, автоматах фасонно-продольного точения), содержат специальные добавки, улучшающие обрабатываемость данной стали.
По способу получения и степени точности сортовой прокат делится на горячекатаный, калиброванный и со специальной отделкой поверхности. Самый дешевый прокат – горячекатаный. Горячекатаный пруток (круг) выпускается диаметром от 5 до 270 миллиметров и длиной от 2 (для малого диаметра) до 6 метров и более. Холоднотянутый (калиброванный) прокат выпускается с меньшими допусками по диаметру (толщине для листов) и с меньшей шероховатостью. Но холоднотянутый прокат дороже горячекатаного. Холоднотянутый пруток изготавливают диаметром от 3 до 100 миллиметров нормальной и повышенной точности.
|
|
Еще более точные прутки поставляются по ГОСТ 14955–77. По этому стандарту предусмотрено 7 классов точности: 1, 2, 2а, 3, 3а, 4, 5 и четыре группы шероховатости – А, Б, В, Г (табл. 1.2). Наиболее точный – 1 класс. Данный вид проката чаще всего применяется при производстве инструмента, изготавливаемого методом вышлифовывания (например, быстрорежущих сверл). При этом наружный диаметр, как правило, дополнительно не обрабатывается.
Прокат, поставляемый металлургическими предприятиями, имеет стандартные размеры и допуски (табл. 1.1, 1.3).
![]() |
Таблица 1.1
Габариты проката (выборочно), поступающего с завода-изготовителя
Вид проката |
Размеры проката, мм
| Допуск на диаметр (толщину листа), мм | ||||
Горяче-катаный | Холодно-тянутый (лист хол. катаный) | Со спец. отделкой поверхности; класс точности, 1/3: | ||||
Лист S = 1 мм S = 3 мм S = 5 мм S = 13…25 мм S = 50 мм S = 100 мм S = 150 мм | 1000 х 2500 1500 х 2000 1500 х 2000 1500 х 3000 1500 х 3000 1500 х 3000 1500 х 3000 | ± 0,11 ± 0,12 +0,4; –05 +0,6; –0,8 +0,6; –1,3 +1,1; –3,1 +1,9; –4,2 | ± 0,11 ± 0,19 ± 0,23 – – – – | |||
Круг (пруток) Ø 1 мм Ø 3 мм Ø 5 мм Ø 20 мм Ø 50 мм Ø 100 мм Ø 120…155мм Ø 160…200мм | L=1500 L=2000 L=2000 L=3000 L=3000 L=3000 L=3000 L=3000 | +0,3; –0,5 +0,4; –0,5 +0,4; –1,0 +0,5; –1,3 +0,8; –2,0 +0,9; –2,5 | –0,075 –0,075 –0,13 –0,16 | –0,005/–0,02 –0,005/–0,02 –0,005/–0,025 /–0,045 /–0,05 | ||
Пример обозначения проката : Пруток 5–Б–h9–Т 20Х13 ГОСТ 14955–77, где 5 – диаметр прутка; Б – группа точности; h9 – допуск на диаметр, Т – термообработан; 20Х13 – марка материала
|
Таблица 1.2
Точность и шероховатость прутков со специальной отделкой
поверхности
Группа шероховатости | Шероховатость Ra, мкм | Класс точности |
А | 0,32 | 1, 2, 2а, 3, 3а |
Б | 0,63 | 2, 2а, 3, 3а, 4 |
В | 1,25 | 2а, 3, 3а, 4 |
Г | 2,5 | 3, 3а, 4, 5 |
Ковка
![]() |
Ковка – вид горячей обработки металлов давлением, при котором металл деформируется с помощью универсального инструмента. Нагретую заготовку укладывают на нижний боек, а верхним бойком последовательно деформируют отдельные ее участки, при этом металл свободно течет в разные стороны [58]. Различают следующие основные операции ковки (рис. 1.3): протяжка, прошивка, отрубка, гибка, штамповка в подкладных штампах.
|
|
Полученные заготовки называют поковками. В дальнейшем их подвергают механической обработке для получения готовых деталей. Ковка широко применяется в мелкосерийном производстве. Наиболее распространена осадка – получение из сортового проката заготовки большего диаметра. Каждое предприятие имеет свой оптимальный набор операций и применяемого стандартного инструмента и приспособлений для ковки.
1.4. Холодная штамповка
Штамповка – обработка металлов давлением с помощью штампа. Штамп – технологическая оснастка, посредством которой заготовка приобретает форму и (или) размеры, соответствующие поверхности или контуру рабочих элементов штампа. Холодная штамповка – процесс, протекающий без предварительного разогрева заготовки. Как правило, после штамповки изменяются исходные физические свойства материала заготовки, которые должны при необходимости восстанавливаться термической обработкой. Холодная штамповка позволяет получить заготовки и детали сложной формы 9…7 квалитета точности и шероховатостью Rz 10… Rz 1,6 (рис. 1.4).
Холодную штамповку подразделяют на объемную штамповку (сортового металла) и листовую штамповку (листового металла). Для производства изделий методом холодной штамповки применяется специальное оборудование, рассчитанное на выполнение одной какой-нибудь операции. Это существенно снижает номенклатуру получаемых деталей. Листовой штамповкой получают заготовки и детали из листового, ленточного и полосового материала способом вырубки, гибки, вытяжки, отбортовки в штампах на прессах.
Одной из разновидностей методов холодной штамповки является поэлементная штамповка. В основе этого метода лежит обработка заготовки из листа последовательным воздействием одного или нескольких инструментов, имеющих простейшую форму: отрезок линии, отрезок окружности определенного радиуса или отрезок кривой специального профиля. Меняя инструмент, можно получить самые разнообразные обработанные поверхности (рис. 1.5).
Из всего разнообразия машин для поэлементной штамповки в мелкосерийном производстве наибольшее распространение получили
|
револьверно-вырубные прессы с программным управлением. На этом оборудовании выполняются следующие операции:
· разделительные (пробивка, отрезка, разрубка);
· формоизменяющие (вытяжка ребер жесткости, пробивка жалюзей);
·
![]() |
вибрационной высечки (обработка отверстий сложной геометрической формы и отверстий, при вырубке которых превышается максимальное усилие пресса).
На наиболее распространенной модели пресса «BEHRENS V20» обрабатываются заготовки размерами 1270 х 1270 мм и толщиной от 1 до 6 мм из стали, меди, алюминия и других материалов и сплавов.
Наличие программного управления позволяет быстро переналаживать данное оборудование.
Погрешности формы могут быть устранены фрезерованием на этом же станке с помощью специального приспособления или на отдельном фрезерном станке.
Метод получил широкое распространение в мелкосерийном производстве.
Запись операции холодной штамповки (холодная высадка заготовок под винты) в технологической документации производится следующим образом:
11 2 020 2122–0011 Холодновысадочная
1. Изготовить деталь согласно операционному эскизу,
где 11 – номер цеха, 2 – участок цеха, 020 – номер операции,
2122–0011 – код операции (высадка), холодновысадочная – название операции.
Горячая объемная штамповка
![]() |
Горячая объемная штамповка – вид обработки металлов давлением, при котором формообразование поковки из нагретой заготовки осуществляют с помощью специального инструмента – штампа. Изделие, полученное технологическим методом штамповки, является штампованной поковкой (рис. 1.6).
В качестве заготовок для горячей штамповки применяют прокат различного профиля: круг, квадрат, прямоугольник, а также периодический профиль. Перед штамповкой прокат разделяется на мерные заготовки различными способами: на круглопильных станках, пресс-ножницами, газовой горелкой и др.
Заготовка, нагретая до оптимальной температуры, помещается в полость одной из половин штампа, где она под силовым воздействием второй половины приобретает заданную форму (копирует форму штампа).
Горячей объемной штамповкой изготавливают заготовки для ответственных деталей станков, автомобилей, сельскохозяйственных машин, тракторов, самолетов, железнодорожных вагонов и др.
По сравнению с ковкой штамповка имеет ряд преимуществ:
· получение поковок сложной формы без напусков;
· значительно меньшие допуски на изготовление;
· после штамповки обрабатываются только сопрягающиеся поверхности;
· высокая производительность.
Главный недостаток штамповки – значительная стоимость штампа, который изготавливается только для одного вида изделия. Поэтому горячая штамповка находит свое применение в крупносерийном и массовом производстве.
Волочение
![]() |
Процесс волочения заключается в протягивании заготовки через постепенно суживающееся отверстие в инструменте, называемом фильерой. Фильера (волока, матрица) представляет собой кольцо (рис. 1.7, а), рабочее отверстие которого состоит из нескольких зон: входной (смазочной) зоны 1, деформирующей зоны 2, калибрующего пояска 3, выходного конуса 4. В зависимости от протягиваемого материала фильеру изготавливают из инструментальной стали, твердого сплава или алмаза (для получения проволоки диаметром менее 0,2 мм).
Сортамент, получаемый волочением, весьма разнообразен: проволока диаметром 0,002…10 мм, фасонные профили (рис. 1.7, б), трубы диаметром 0,3…500 мм с толщиной стенки от 0,05 до 6 мм соответственно. Волочение выполняют на специализированных предприятиях серийного и массового производства.
Литье
Литье – изготовление заготовки или изделия из жидкого материала заполнением им полости заданных форм и размеров с последующим затвердением. Этим способом получают заготовки сложной формы, которые нельзя экономично сделать другими способами, например, коробчатые заготовки (станины станков), кронштейны, шарниры и др.
Для производства отливок применяют материалы и сплавы, имеющие хорошую текучесть в жидком виде. Для повышения литейных свойств в исходные материалы добавляют соответствующие присадки. Процесс получения отливок выполняется в следующей последовательности: изготовление формы; плавка материала, заливка жидкого материала в форму; охлаждение и затвердение материала в форме; извлечение заготовки из формы; удаление литниковой системы и зачистки отливки. Для ответственных заготовок дополнительно производится искусственное или естественное старение.
Наиболее часто применяются следующие виды литья (рис. 1.8): литье в землю, литье в оболочковые формы, литье по выплавляемым моделям, литье в кокиль, литье под давлением, центробежное литье, непрерывное литье.
Выбор того или иного способа литья зависит от типа производства, сложности конфигурации, размеров, и материала детали, требуемой точности и шероховатости поверхности, экономической целесообразностью.
Литье в песчано-глинистые формы. Для производства отливок используются сплавы черных металлов: серые, высокопрочные, ковкие и другие виды чугунов; углеродистые и легированные стали; сплавы цветных металлов; медные (бронзы и латуни), цинковые, магниевые и алюминиевые сплавы; сплавы тугоплавких металлов: титановые, молибденовые, вольфрамовые и др.
По чертежу готовой детали проектируется чертеж отливки, учитывающий особенности процесса литья: усадку, формовочные уклоны, галтели, припуск на механическую обработку и др. Кроме того, прорабатывается литниковая система, через которую жидкий металл будет поступать в форму. Затем изготавливаются модели и стержневые ящики (деревянные для единичного производства, металлические для крупносерийного и массового производства). Литейная форма, состоящая из двух полуформ, изготавливается в следующей последовательности: уплотнение формовочной смеси для точного отпечатка модели в форме и придание форме достаточной прочности; устройство вентиляционных каналов для выводов газов из полости формы, образующихся при заливке; извлечение модели из формы; отделка и сборка формы.
В форму заливается жидкий металл, который охлаждается заданное время (минуты для небольших деталей, часы и сутки для объемных деталей). Охлажденная деталь выбивается из формы, форма при этом разрушается. Полученная таким образом отливка дополнительно обрабатывается: удаляются прибыли, литники, облой по месту сопряжения полуформ. После чего производится очистка отливок: удаление пригара, остатков формовочной и стержневой смеси.
Преимущества литья в песчаные формы – наиболее простой способ литья, универсальность метода, формовочные материалы недефицитны и дешевы, возможность получения отливки любой конфигурации, из любых металлов и любой массы.
Недостатки литья в песчаные формы: грубая поверхность отливки, большой припуск на механическую обработку, большой расход металла на литники, очень низкие санитарно-гигиенические условия труда. Кроме того, для данного вида литья характерно образование горячих и холодных трещин, пустот, газовых раковин и пористости в отливке, коробление отливки под влиянием внутренних напряжений.
Литьем в песчаные формы получают заготовки для деталей в автотракторной промышленности, в сельскохозяйственном машиностроении, в станкостроении, при изготовлении промышленных роботов и др. Данный вид литья часто применяется в опытном, единичном и мелкосерийном производстве.
Литье в оболочковые формы является улучшенной модификацией литья в глинисто-песчаные формы. Отливки получают в тонкостенных формах-оболочках толщиной 6…15 мм, изготовленных из песчано-смоляных смесей. Смесь состоит из кварцевого песка и 6…7% формальдегидной порошкообразной смолы. Смола при 70°С размягчается и при температуре 120°С плавится, превращаясь в клейкую массу. При температуре 200…300°С смола становится твердой и при повторном нагреве не расплавляется. При температуре 450°С смола выгорает. Учитывая эту особенность смолы, строится техпроцесс литья. Формовочная смесь засыпается на нагретую металлическую плиту с закрепленной на ней моделью. Под действием тепла подмодельной плиты формовочная смесь, расплавляясь, обволакивает модель слоем заданной толщины. Затем освобожденную от нерасплавленной смеси плиту нагревают в печи до температуры отвердевания. После охлаждения модель отделяют от полученной полуформы и жестко соединяют с другой половиной полуформы. В полученную форму заливают металл. После охлаждения металла форма легко разрушается, освобождая отливку.
Преимущества метода: литье отличается высокой чистотой поверхности и высокой точностью размеров отливок сложной конфигурации (± 0,2 мм на 100 мм длины). Хорошая газопроницаемость формы обеспечивает отсутствие газовых пор. Легко удаляется отливка из формы, так как при выгорании смолы создается тонкая газовая рубашка, которая защищает поверхность отливки от пригара смеси. Форма легко разрушается. Расход формовочной смеси в 5…10 раз меньше, чем при литье в земляные формы.
Недостатком метода является дороговизна эпоксидной смолы, а также ограничение размеров и массы отливок.
Данный способ применяется для отливки чугунных коленчатых валов автомобилей, чугунных ребристых цилиндров для тяжелых мотоциклов, литого режущего инструмента и других отливок.
Литье по выплавляемым моделям. В качестве материала для модели используют легкоплавкие модели из смеси парафина и стеарина, из пенопласта и др.
Модель (или блоки моделей) соединяют с литниковой системой и погружают в клейкую огнеупорную суспензию, сушат, снова погружают в суспензию до тех пор, пока не образуется форма толщиной 5…8 мм. Модель выплавляют из формы горячим воздухом или паром при температуре 120…150°С. Готовую форму прокаливают при температуре 850…900 °С, при которой остатки легкоплавкого сплава выгорают. Форма при этом превращается в прочную керамическую оболочку. Форму заливают металлом. После остывания металла форму разбивают, остатки формы удаляют в специальных растворах.
Преимущества. Отсутствие у формы разъема обеспечивает повышенную точность отливки. Важным преимуществом способа является возможность получения отливок самой сложной формы практически из любых сплавов. Высокая точность и чистота отливки позволяет исключить механическую обработку. Недостатком способа является длительный технологический процесс и высокая стоимость отливки.
Применяется способ в массовом и серийном производстве. Способ незаменим при изготовлении отливок из труднообрабатываемых сплавов (жаропрочных, магнитных, инструментальных), лопаток реактивных двигателей, челноков швейных машин, головок режущего инструмента (рис. 1.9) и т.п.
Литье в металлические формы (кокиль). Металлические формы (кокили) изготавливают из чугуна, стали и других сплавов. Кокили применяют в основном для получения отливок из цветных металлов, реже – из стали и чугуна.
Конструкции кокилей весьма разнообразны, они могут быть разъемными, неразъемными, но чаще всего кокиль изготавливают из двух половин. Внутренняя рабочая часть кокиля соответствует внешней конфигурации отливки. После затвердевания металла кокиль раскрывают и из него вынимают отливку. Чтобы уменьшить скорость охлаждения отливок, избежать образования закаленного слоя и повысить стойкость кокиля, на его внутреннюю поверхность наносят теплоизоляционные, противопригарные покрытия. Покрытия, в зависимости от назначения, могут быть тонкостенные (до 0,5 мм для цветных металлов) и футерованные (с толщиной покрытия до 100 мм для чугунов). Кокиль – форма многократного использования. В нем можно получить до 300 стальных отливок или несколько тысяч отливок из алюминиевого сплава.
Преимущества. Кокиль обеспечивает получение отливок с высоким качеством металла, повышенной точностью и чистотой поверхности.
Недостатки – высокая стоимость кокиля и трудоемкость его изготовления. Можно отливать заготовки только относительно простой конфигурации. При литье в металлические формы из-за быстрого охлаждения уменьшается жидкотекучесть расплава. Возможно возникновение газовой пористости из-за отсутствия газопроницаемости формы. Литье в металлические формы применяется и как самостоятельный способ, и в других способах литья (литье под давлением, центробежное литье).
Литье под давлением. Литье под давлением – наиболее производительный способ изготовления отливок из цветных металлов с высокой точностью и чистотой поверхности. Расплавленный металл заполняет стальную пресс-форму под давлением до 3000 атм., быстро затвердевает и образует отливку. Процесс заливки длится несколько секунд. Существует несколько разновидностей этого способа. Различают литье под высоким давлением и литье под низким давлением.
Преимущества метода. Высокая производительность (до 3000 отливок в час), высокая точность и чистота поверхности, возможность автоматизации процесса и встраивания в автоматические линии.
Недостатки: высокая стоимость оборудования и пресс-форм, ограниченная масса отливок, газоусадочная пористость отливок.
Применяется способ в массовом производстве для отливки заготовок сложной формы с различными выступами, приливами и отверстиями: корпусов электродвигателей из силумина, блоков цилиндров двигателей внутреннего сгорания, а также литья из других цветных сплавов.
Центробежное литье. При этом способе отливки получают свободной заливкой во вращающиеся формы. Отливки формируются под действием центробежных сил. Центробежные силы отбрасывают заливаемый металл к стенкам формы, где он затвердевает, образуя пустотелую отливку. Центробежным литьем в промышленности получают чугунные и стальные трубы, кольца, зубчатые колеса и другие отливки типа тел вращения. Отливки получаются большой плотности и с высокими механическими свойствами. Центробежным литьем можно получать тонкостенные отливки из сплавов с низкой текучестью. К недостаткам центробежного литья относится трудность получения качественных отливок из сплавов, склонных к ликвации, и невозможность выполнения отверстий точных размеров. Размеры отверстий отливок, изготавливаемых этим способом, зависят от количества залитого в форму металла.
Непрерывное литье. Жидкий металл, проходя через кристаллизатор, охлаждается, быстро затвердевает. Затвердевший металл в виде непрерывной ленты вытягивают с определенной скоростью, которую затем разрезают на куски заданной длины. Этим способом получают отливки с параллельными образующими из чугуна, медных, алюминиевых и других сплавов. Благодаря направленному затвердению сплава отливки не имеют неметаллических включений, усадочных раковин и пористости.
Литье выжиманием применяют для получения тонкостенных крупногабаритных отливок типа панелей размерами до 1000…2500 мм с толщиной стенки 2…5 мм из алюминиевых и магниевых сплавов. Металл заливается между двумя параллельными, в размер отливки, полуформами, излишки которого вместе с включениями выжимаются в специальную емкость.
Литье вакуумным всасыванием. Водоохлаждаемая литейная форма, опирающаяся на керамический поплавок, заполняется расплавленным металлом из печи за счет разрежения, создаваемого в форме вакуумным насосом. Во время непродолжительной выдержки формируется отливка.
Способ применяется для получения втулок, вкладышей подшипников скольжения и других отливок простой формы из дорогих и дефицитных бронз и латуней. Преимущество – получение качественных отливок без расхода металла на литники и прибыли.
Литье намораживанием. Суть способа в том, что образование отливки происходит в результате последовательного затвердевания металла – его "намораживание" на затравку. На поверхность жидкого металла помещают керамический поплавок с отверстием, соответствующим сечению отливки. В мениск выступающего из отверстия металла вводят затравку. При ее подъеме из отверстия поплавка за счет сил поверхностного натяжения постепенно вытягивается жидкий металл, затвердевающий ("намораживащийся") и образующий отливку. Скорость вытягивания должна быть синхронизирована со скоростью охлаждения и затвердения металла.
Способ применяется для получения лент шириной 100 мм и более, труб с внутренними и наружными ребрами и других изделий сложного профиля из алюминиевых сплавов.
Жидкая прокатка – совмещенный способ литья и прокатки, при котором жидкий металл пропускается между двумя охлаждаемыми валками. В зазоре между валками происходит кристаллизация металла. Затвердевший металл в пластичном состоянии выжимается из зазора в виде ленты. Так получаются ленты из алюминия, чугуна и других сплавов шириной 750 мм и толщиной 0,7…2,5 мм.
Жидкая штамповка занимает промежуточное положение между литьем и объемной штамповкой. Порцию жидкого металла заливают в металлическую форму (матрицу), в которую затем опускается металлический пуансон, выдавливающий металл и заставляющий его заполнять все полости формы. В результате между формой и пуансоном образуется отливка.
Способ пригоден для сплавов на медной, алюминиевой, магниевой и цинковой основе. Отливки приобретают высокую плотность и механические свойства благодаря интенсивному теплоотводу и горячему деформированию литой структуры в процессе кристаллизации.
Дефекты отливок
![]() |
Причин возникновения брака в литейном производстве довольно много: неудачная конструкция самой детали или литниковой системы, некачественные формовочные материалы, плохое качество шихты, нарушения технологии при формовке, заливке форм и охлаждении отливок (рис. 1.10).
Частично дефект обнаруживается при контроле отливок после литья: несоответствие по геометрии, дефекты поверхности, несплошности в теле отливки. Однако часть дефектов (усадочные и газовые раковины, различные включения) трудно определить без применения соответствующей диагностической аппаратуры. При дальнейшей обработке резанием для ответственных деталей необходимо выполнять входной контроль.
Запись литейной операции (литье в песчаные формы) в технологической документации производится следующим образом:
98 1 020 1065–0004 Литейная
1 . Отлить заготовку согласно чертежу на отливку
В последние годы наметилась тенденция увеличения доли керамических деталей в изделиях. Существует ряд материалов (ситаллы, гранулят плавленных горных пород и др.), изделия из которых получают литьем под давлением. Разработаны соответствующие технологические процессы литья для таких материалов. Типовые техпроцессы состоят из ряда основных и подготовительных операций. Основной блок операций для получения детали «Сферическая опора» (рис. 1.11) выглядит следующим образом:
005 2 41 271020 Технохимическая
Приготовить шликер по ТТП 01200-00075
010 1 42 140019 Литейная
Отлить деталь по ТТП 01212-00062
020 2 42 928017 Контрольная
Произвести рентгеновский контроль всех заготовок
025 1 24 730020 Термическая
Произвести утильный обжиг по ТТП 01250-00096
030 1 11 397002 Слесарная
Зачистить литник
035 1 24 730020 Термическая
Произвести окончательный обжиг по ТТП 01250-00097
Каждый из указанных типовых технологических процессов (ТТП) содержит несколько операций. Таким образом, весь технологический процесс получения деталей из керамических материалов может содержать несколько десятков операций.
Сварка
Принцип действия сварки основан на явлении притягивания одного тела при попадании в зону действия межатомных связей другого тела и образования между ними прочной межатомной связи.
Реальные тела имеют весьма неровные поверхности и всегда покрыты слоем адсорбированных (притянутых) газов, паров воды, окислов и т.д. Поэтому реальные тела при соприкосновении не свариваются друг с другом. Чтобы сварить два металлических тела, надо, во-первых, тщательно очистить свариваемые поверхности; во-вторых, привести в соприкосновение эти тела, обеспечив тем самым расстояние между поверхностями атомов порядка 2…4 ангстрем. Для этого применяют два основных средства: нагрев и давление. Нагрев помогает размягчить металл, чтобы при сдавливании легко сминались неровности на свариваемых поверхностях, и возникало взаимодействие поверхностных атомов. Если заготовки в зоне сварки нагреваются до расплавления, то взаимодействие жидкого металла свариваемых заготовок происходит без внешнего давления, жидкий металл сливается в один объем (в одну каплю). В зависимости от того, прикладываются к заготовкам в процессе сварки давление или нет, существующие способы сварки делятся на две группы: сварка давлением и сварка плавлением.
Сваркой называется технологический процесс получения неразъемных соединений посредством установления межатомных связей между соединяемыми частями при их нагревании и (или) пластическом деформировании. Существует большое количество разнообразных технологических процессов сварки (рис. 1.12), охватывающих различные отрасли народного хозяйства. В каждом конкретном случае применяется соответствующее данному способу сварки технологическое оборудование, оснастка и инструмент.
Сварка может применяться как основной технологический процесс (рис. 1.13, а), как заготовительное производство при последующей механообработке (рис. 1.13, б) и как встроенный процесс в другие виды механообработки (рис.1.13, в).
Как основной технологический процесс, сварка применяется в судостроении при изготовлении цельносварных корпусов судов, при про-
![]() |
кладке нефте- и газопроводов, при строительстве домен и больших резервуаров для хранения жидкости и газов.
Сварка трением используется, например, для получения заготовки сверла, обрабатываемой затем методами резания.
В механообработке сварка очень часто встраивается в технологический процесс для получения неразъемного соединения двух или нескольких деталей для получения более сложной детали, изготовление которой механообработкой или затруднено, или связано с большим расходом металла.
Для получения качественного сварного соединения производят подготовку свариваемых заготовок под сварку. Очищают свариваемые кромки от ржавчины, окалины, масла, влаги, наличие которых приводит к образованию пор, включений и других дефектов. Для этого вводят подготовительные операции, гарантирующие получение качественных заготовок, например, пескоструйную операцию.
При сборке заготовок под сварку необходимо обеспечить требуемую точность базирования и закрепления с помощью сборочно-сварочного приспособления.
В общем случае различают ручную сварку (рис. 1.14) и автоматическую. Ручная сварка применяется в единичном и мелкосерийном производстве, автоматическая – в крупносерийном и массовом.
Преимущества ручной сварки:
· универсальность способа, ею можно сваривать все металлы, любые конструкции во всех пространственных положениях;
· большая оперативность способа позволяет производить сварку во многих ситуациях (при авариях, при ремонте в полевых условиях и т.п.);
· простота процесса и оборудования;
· возможность получения высококачественных соединений.
Недостатки ручной сварки:
· качество шва зависит главным образом от квалификации сварщика;
· тяжелые условия выполнения сварки (в условиях сквозняков из-за сильной вентиляции или под открытым небом в зимних условиях);
· низкая производительность.
Наиболее производительной является автоматическая сварка. При автоматической дуговой сварке все сварочные операции (вместо сварщика) выполняет автомат: зажигание дуги и поддержку стабильного ее горения, защиту сварочной ванны от вредного влияния воздуха, подачу сварочной проволоки и флюса в зону сварки, передвижение дуги вдоль шва, заварку кратера по окончании сварки.
Преимущества автоматической сварки:
· автоматическая сварка производительнее ручной в 10 и более раз за счет непрерывности процесса и применения более высоких сварочных токов;
· данный способ обеспечивает более эффективное использование тепла и в связи с этим больший КПД;
· большие токи и отсутствие разбрызгивания металла позволяет сваривать заготовки большой толщины.
Недостатки автоматической сварки:
· автоматическая сварка возможна только в нижнем положении;
· ограничено применение сварки – в основном только для прямолинейных швов и швов небольшой кривизны;
· при сварке под флюсом затруднен контроль за процессом.
Дата добавления: 2019-02-12; просмотров: 1615; Мы поможем в написании вашей работы! |
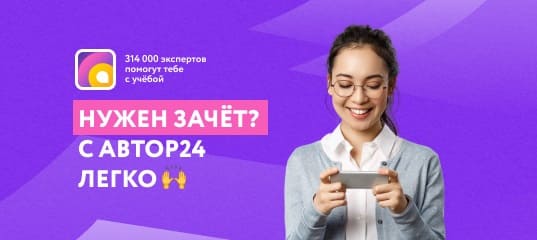
Мы поможем в написании ваших работ!