Точіння зовнішніх циліндричних поверхонь
Інструктаж з охорони праці. Знайомство з підприємством
Охорона праці — це система правил і заходів, які забезпечують безпечну роботу на даному виробництві. При роботі на металорізальному верстаті необхідно передбачити ряд вимог, які б дозволили працюючому виконувати поставлене перед ним завдання в умовах, які передбаченні конструкторськими документами.
Основними заходами, які зменшують або попереджають травматизм при роботі на дільниці є автоматизація або механізація технологічного процесу. Крім цього на верстатах встановлюють захисні кожухи на вузлах, які передбачають обертові моменти. Всі захисні кожухи з внутрішньої сторони фарбуються в жовтий колір (сигнальний), а з зовнішньої сторони наноситься знак безпеки по ГОСТ 12.4.025-86 (рівносторонній трикутник жовтого кольору з вершиною доверху в чорній рамці і знаком оклику посередині). Під знаком встановлена таблиця з написом «При ввімкненому верстаті не відкривати».
Для орієнтовної оцінки шуму приймають показник, який називається «рівнем шуму» і вимірюється за шкалою «А» шумоміра. Допустимий рівень шуму в приміщеннях по СН 245-79 становить 71-90 Дб.
Основними заходами, які захищають працюючих від шкідливих дій шуму і вібрацій є установка верстата на віброопори.
Правильне визначення площі дільниці визначає правильну організацію робочого місця згідно з науковою організацією праці. Завдяки цьому зменшується втомленість працюючих і зменшується можливість травматизму.
|
|
Кожне робоче місце обладнане інструментальною тумбочкою і дерев'яним під ставником, а для видалення стружки з верстата застосовують спеціальні вмонтовані в верстат шнекові і магнітні транспортери, а на свердлильних верстатах — спеціальні гачки і щітки.
В цеху застосовується комбіноване освітлення. Освітленість на підлозі при загальному освітленні повинна бути не менше 150 лк для ламп розжарювання не менше 150 лк для люмінесцентних ламп незалежно від місцевого освітлення.
Як лікувально-профілактичні заходи передбачаємо попередній та періодичний (не рідше одного разу на рік) медогляди працівників цеху, заборону допуску до вібраційних робіт осіб, молодших 18 років та таких, що мають відповідні проти покази в стані здоров'я, лікувальну гімнастику та масаж рук.
2.Загальні відомості про підприємство. Характеристика типу виробництва
Машинобудівне підприємство ТОВ «МАГМА» являє собою сучасний виробничий комплекс, створений 20 серпня 2001 вгода, що має у своєму складі спеціалізовані виробництва і випускає складну технічну продукцію.
Підприємство виготовляє нестандартне обладнання для різних галузей промисловості, підйомно-транспортного устаткування, запчастини для підприємств металургійної, гірничодобувної галузей, морських і річкових портів, машин і устаткування коксохімічних підприємств.
|
|
Володіючи сучасним металообробним виробництвом, висококваліфікованими кадрами, підприємство виготовляє унікальне за своїми характеристиками нестандартне обладнання та деталі різних класів точності і типорозмірів масою від декількох кілограмів до 120 тонн.
Наявність інженерів високої кваліфікації в конструкторських і технологічних службах у поєднанні з універсальною виробничою базою і фінансовими можливостями дозволяє підприємству швидко перебудовуватися на освоєння нових унікальних видів продукції.
На підприємстві впроваджена і застосовується система менеджменту якості відповідно до вимог міжнародного стандарту DIN EN ISO 9001:2008, що підтверджено сертифікатом міжнародного сертифікаційного органу TUV Thuringen (Німеччина).
Функціонування системи менеджменту якості дозволило організувати чітку зв'язок комерційних, технічних і виробничих підрозділів на всіх етапах виробництва продукції — від закупівлі сировини, матеріалів та комплектуючих до відвантаження споживачеві кінцевої продукції.
|
|
Контроль якості продукції на всіх етапах виробництва здійснюється фахівцями відділу технічного контролю та лабораторії з контролю виробництва, оснащеної сучасним обладнанням, приладами та методиками, необхідними для виконання необхідного обсягу вхідного контролю, контролю у процесі виробництва та приймально-здавальних випробувань готової продукції.
3.Методи отримання заготівок. Вибір виду заготівки для індивідуального завдання
У сучасному виробництві одним з основних напрямків розвитку технології механічної обробки є використання чорнових заготовок з економічними конструктивними формами, що забезпечують можливість використання найбільш оптимальних способів їх обробки, тобто обробки з найбільшою продуктивністю та найменшими відходами. Цей напрямок вимагає безперервного підвищення точності заготовок та наближення їх конструктивних форм та розмірів до готових деталей, що дозволяє відповідно скоротити область використання обробки різанням, обмежуючі її у ряді випадків чистовими, фінішними операціями.
Вибір виду заготовки для подальшої механічної обробки у багатьох випадках є одним з дуже важливих питань розробки процесу виготовлення деталі. Від вірного вибору заготовки, тобто встановлення її форми, розміру припусків на обробку, точності розмірів (допусків) та твердості матеріалу залежить трудомісткість, а у підсумку, й собівартість процесу обробки та виготовлення деталі у цілому. Вид заготовки у більшості випадків визначає у значній степені подальший процес обробки деталі. Якщо заготовка буде достатньо точно виготовлена з припусками не більшими, ніж це необхідно для обробки, то механічна обробка деталі може бути зведена до мінімальної кількості операцій, мінімальної трудомісткості та собівартості.
|
|
Таким чином, при розробці процесу виготовлення деталі можуть бути два принципові напрямки: а) отримання заготовки, яка найбільше наближається за формою та розмірами до готової деталі, коли на заготівельні цехи приходиться значна доля трудомісткості виготовлення деталі, та відносно менша доля приходиться на механічні цехи; б) отримання грубої заготовки з великими припусками, коли на механічні цехи приходиться основна доля трудомісткості та собівартості виготовлення деталі.
У залежності від масштабу, а відповідно, типу виробництва буде вірним той або інший з розглянутих напрямків або проміжний між ними. Перший напрямок відповідає, як правило, масовому та крупносерійному виробництву. Це пов'язано з тим, що високовартісне сучасне обладнання заготівельних цехів, що забезпечують високопродуктивні процеси отримання точних заготовок, економічно доцільне лише при великих масштабах виробництва. Другий напрямок типовий для одиничного та дрібносерійного виробництва, коли використання дорогого обладнання у заготівельних цехах економічно не вигідно. Вище розглянуте не слід розуміти, як те, що у межах одиничного та дрібносерійного виробництв не можуть бути досягненні доцільні рішення про задовільну якість заготовок. Навпаки, економічно доцільні для будь-якого типу виробництва якості заготовок завжди можуть бути заздалегідь визначені при вірному підході до їх вибору, а відповідно, й до встановленого способу виготовлення заготовок.
Великий вплив на вибір способу отримання заготовки мають час відведений на технологічну підготовку виробництва (проектування, виготовлення та налагодження штампів, моделей, прес-форм та ін.); наявність відповідного технологічного обладнання та бажаний степінь автоматизації процесу. Вибраний спосіб повинен забезпечувати щонайнижчу собівартість деталі. При цьому велике значення має економія металу, що переробляється в стружку. Тому технолог повинен домагатись, щоб обраний спосіб забезпечував виготовлення такої заготовки, яка б за формою і розмірами максимально наближалась до готової деталі. Однак, підвищення точності заготовки при малій програмі випуску може виявитись економічно невигідним, оскільки витрати на оснащення заготівельних процесів можуть перевищувати економію на механічній обробці та матеріалів.
4. Знайомство з завданням відділу технічного контролю. Обов’язки контролера
мета - підвищення якості всіх видів продукції, що випускається, забезпечення відповідності її показників рівню світових досягнень;
показники якості - це точність розмірів, надійність експлуатації, зручність використання, відповідність ГОСТам, вимогам естетики.
Головна операція - звірення параметрів продукції з показниками, вказаними у ГОСТах, кресленнях, технологічній документації;
вироби при цьому оглядаються "на око" або перевіряються за допомогою контрольно-вимірювальних інструментів, приладів: мікрометрів, штангенциркуля, калібрів, лупи, мікроскопа, електровимірювальних приладів тощо;
засобами праці є також переліки "зразків-еталонів" і необхідних ознаки якісних виробів;
контролер одержує партію готових виробів або напівфабрикатів, перевіряє кожен з них, проставляє клеймо-свідоцтво контролю, оформляє супровідну документацію, дефектні відомості;
контролер не тільки виявляє брак, але і вивчає його причини і пропонує заходи його профілактики. Причини можуть бути різними: невідлагоджене обладнання, неякісний матеріал, дефекти заготовок, не кваліфікованість, недбалість, неуважність робітників;
кваліфікований контролер добре знає технологію виробництва, сам процес роботи, розбирається у кресленнях, уміє використовувати контрольно-вимірювальні інструменти;
повинен мати розвинену пам'ять, нормальний зір (не нижче 0,5, без виражених аномалій), стійку зорову працездатність, перешкодостійкість, зібраність, уважність;
фізичне навантаження контролера незначне;
контролери працюють на спеціально обладнаних робочих місцях при хорошому освітленні.
5.Знайомство з обов’язками майстра дільниці металорізувального обладнання
Здійснює, згідно з чинними законодавчими і нормативними актами, які регулюють виробничо-господарську діяльність підприємства, керівництво виробничою дільницею. Забезпечує виконання в зазначені строки завдань з обсягу виробництва продукції (робіт, послуг) заданої номенклатури (асортименту), підвищення продуктивності праці, зниження трудомісткості продукції, на основі повного завантаження устаткування і використання його технічних можливостей, раціонального витрачання сировини, матеріалів, палива, енергії і зниження витрат.
Організовує підготовку виробництва, забезпечує розміщення робітників і бригад, контролює додержання технологічних процесів, оперативно виявляє і ліквідує причини їх порушення. Бере участь у розробленні нових та в удосконаленні діючих технологічних процесів, режимів і графіків виробництва. Перевіряє якість продукції, що випускається, або виконуваних робіт, вживає заходів, щодо запобігання браку та підвищення якості продукції (робіт, послуг). Бере участь у прийманні закінчених робіт, пов’язаних з реконструкцією дільниці, ремонтом технологічного устаткування, механізацією та автоматизацією виробничих процесів і ручних робіт.
6.Задачі виробничо-диспечерського відділу. Знайомство з обов’язками інженера(техніка) підготовки виробництва
Забезпечення ритмічної роботи підприємства і рівномірного випуску продукції
Забезпечення виконання робіт, відповідно до вироблених програм, договірних зобов'язань, календарних графіків та змінно-добових завдань
Максимальне використання виробничої сили підприємства.
Здійснює з використанням засобів обчислювальної техніки, комунікацій та зв’язку підготовку виробництва, контроль за забезпеченням виробництва комплектуючими виробами, матеріалами, інструментом, за своєчасним оформленням необхідної технічної документації; розробляє місячні виробничі програми та змінно-добові завдання на закріпленій дільниці роботи.
Бере участь у розробленні та впровадженні нормативів для оперативного планування виробництва.
Контролює комплектність незавершеного виробництва, додержання встановлених норм заділів і календарних випереджень у роботі виробничих підрозділів.
Розраховує календарні графіки завантаження устаткування з урахуванням більш ефективного використання виробничих потужностей, стежить за їх виконанням.
Аналізує роботу цехів і дільниць, вишукує можливості скорочення циклу виготовлення продукції виконання робіт (послуг), виявляє виробничі резерви, розроблює пропозиції щодо їх використання.
Контролює виконання плану виробництва і вживає заходів до забезпечення ритмічної роботи, запобігання та усунення порушень ходу виробничого процесу, ефективного використання устаткування, створення сприятливих умов трудовим колективам для виконання виробничої програми.
7.Задачі конструкторського відділу. Обов’язки конструктора
Діяти від імені відділу, представляти інтереси підприємства у взаємовідносинах з іншими структурними підрозділами підприємства, організаціями.
Здійснювати взаємодії з керівниками (співробітниками) усіх (окремих) структурних підрозділів підприємства.
Знайомитися з проектами рішень керівництва підприємства, що стосуються діяльності очоленого ним структурного підрозділу.
Вносити на розгляд керівництва пропозиції по поліпшенню діяльності підприємства і очоленого ним структурного підрозділу зокрема.
Брати участь у підготовці проектів наказів, інструкцій, указівок, а також кошторисів, договорів і інших документів, зв'язаних з діяльністю структурного підрозділу.
У межах своєї компетенції підписувати і візувати документи.
Самостійно вести листування зі структурними підрозділами підприємства, а також іншими організаціями з питань, що входять у його компетенцію.
Подавати пропозиції директору підприємства про залучення до матеріальної і дисциплінарної відповідальності
Призначення на посаду інженера-конструктора і звільнення від неї проводиться наказом керівника підприємства.
Інженер-конструктор підпорядковується безпосередньо начальнику бюро.
Посадові обов'язки:
Інженер-конструктор:
1. Розроблює ескізні, технічні і робочі проекти особливо складних, складних і середньої складності виробів, використовуючи засоби автоматизації проектування, забезпечує в процесі проектування відповідність розроблюваних конструкцій технічним завданням, стандартам, нормам техніки безпеки, вимогам найбільш економної технології виробництва, а також застосування в проектах стандартизованих і уніфікованих деталей і складальних одиниць.
2. Проводить патентні дослідження і визначає показники технічного рівня виробів, які проектуються.
3. Розроблює кінематичні схеми, загальні компонування і теоретичні погодження окремих елементів конструкцій на основі принципових схем і ескізних проектів, перевіряє робочі проекти і проводить контроль креслень за фахом або профілем роботи, знімає ескізи складних деталей з натури і виконує складні деталювання.
4. Проводить технічні розрахунки в процесі проектування і техніко-економічний аналіз ефективності конструкцій, які проектуються, розроблює інструкції з експлуатації конструкцій, пояснювальні записки до них, карти технічного рівня, паспорти (в тому числі патентні й ліцензійні), програми випробувань, технічні умови, повідомлення щодо змін у раніше розроблених кресленнях та іншу технічну документацію.
5. Вивчає й аналізує конструкторську документацію, що надходить від інших підприємств і організацій, з метою її використання в процесі проектування і конструювання.
6. Погоджує розроблювані проекти з іншими підрозділами підприємства, представниками замовника та органів нагляду, економічно обґрунтовує розроблювані конструкції.
7. Участь у монтажі, наладці, випробуваннях та здачі в експлуатацію дослідних зразків, у складанні заявок на винаходи і промислові зразки, а також у роботах, які включають удосконалення, модернізації, уніфікації конструйованих виробів, їх елементів і розроблення проектів стандартів.
8. Підготовка відгуки і висновки на проекти стандартів, раціоналізаторські пропозиції і винаходи, які стосуються окремих елементів і складальних одиниць.
9. Виконує окремі службові доручення свого безпосереднього керівника.
Права:
Інженер-конструкторимеетправо:
1. Знайомитися з проектами рішень керівництва підприємства, що стосуються його діяльності.
2. Вносити пропозиції по вдосконаленню роботи, пов'язаної з передбаченими справжньою інструкцією обов'язками.
3. В межах своєї компетенції повідомляти безпосередньому керівнику про всі виявлені недоліки в діяльності підприємства та вносити пропозиції щодо їх усунення.
4. Запитувати особисто або за дорученням керівництва підприємства від керівників підрозділів та фахівців інформацію та документи, необхідні для виконання його посадових обов'язків.
5. Залучати фахівців усіх структурних підрозділів до виконання покладених на нього завдань.
6. Вимагати від керівництва підприємства сприяння у виконанні своїх посадових обов'язків.
Відповідальність
Інженер-конструктор несе відповідальність:
1. За неналежне виконання або невиконання своїх посадових обов'язків, передбачених цією посадовою інструкцією - в межах, визначених чинним законодавством України.
2. За правопорушення, скоєні в процесі здійснення своєї діяльності - в межах, визначених чинним адміністративним, кримінальним та цивільним законодавством України.
3. За спричинення матеріального збитку - в межах, визначених чинним трудовим законодавством про працю України.
8.Задачі технологічного відділу. Обов’язки інженера (техніка) технолога
Для здійснення технологічного процесу складається схема або технологічна карта, в якій описуються всі технологічні операції переробки сировини чи напівфабрикатів в готову продукцію. Першим етапом побудови технологічної схеми є технологічна картка, яка являє собою графічне зображення переліку виробничих операцій.
Якісно-кількісна схема — це технологічна блок-схема з нанесеними на ній відомостями про якість і кількість кожного із продуктів, які одержують в даному процесі. В технологічну схему (карту) входить також схема, в якій вказується послідовність розміщення обладнання, що застосовується в технологічному процесі (як основного так і допоміжного, включаючи і транспортне). виробництва і готує висновки про доцільність їх використання в умовах підприємства.
Розроблює, застосовуючи засоби автоматизації проектування, та впроваджує технологічні процеси і режими виробництва на продукцію, яку виробляє підприємство (цех, дільниця), і на всі види різних за складністю робіт.
Запроваджує порядок виконання робіт та операційний маршрут проходження виробів (деталей, складальних одиниць).
Розроблює плани розміщення устаткування, технічного оснащення та організації робочих місць, розраховує виробничі потужності та завантаження устаткування.
Бере участь у розробленні технічно обґрунтованих норм часу (виробітку), в опрацьовуванні конструкцій виробів на технологічність, розраховує нормативи матеріальних витрат (технічні норми витрат сировини, напівфабрикатів, матеріалів, інструментів, технологічного палива, енергії), економічну ефективність проектованих технологічних процесів.
Розроблює технологічні нормативи, інструкції, схеми складання, маршрутні карти, карти технічного рівня та якості продукції та іншу технологічну документацію, вносить зміни до технічної документації у зв'язку з корекцією технологічних процесів і режимів виробництва.
Узгоджує розроблену документацію з цехами та відділами підприємства.
Складає технічні завдання на проектування пристроїв, оснастки і спеціального інструменту, передбаченого технологією, бере участь у розробленні керуючих програм (для устаткування з числовим програмним керуванням), в опрацьовуванні розроблених програм, корекцією їх у процесі доопрацювання, складанні інструкцій на роботу з програмами.
Проводить патентні дослідження і розраховує показники технічного рівня проектованих об'єктів техніки і технології.
Бере участь у проведенні експериментальних робіт, спрямованих на впровадження нових технологічних процесів у виробництво, в складанні заявок на винаходи та промислові зразки, а також у розробленні програм впровадження нової техніки, організаційно-технічних заходів для своєчасного освоєння виробничих потужностей, удосконалення технології і контролює їх виконання.
Проводить контроль за додержанням технологічної дисципліни в цехах та правильної експлуатації технологічного устаткування.
Вивчає передовий вітчизняний та світовий досвід у галузі технології виробництва, розроблює і бере участь у реалізації заходів щодо підвищення ефективності виробництва, спрямованих на скорочення витрат матеріалів, зниження трудомісткості продукції, підвищення продуктивності праці.
Аналізує причини браку і випуску продукції низької якості і знижених сортів, бере участь у розробленні заходів щодо їх запобігання та усунення, а також у розгляді рекламацій на вироблену підприємством продукцію.
Розроблює методи технічного контролю і випробування продукції.
Бере участь у розробленні патентних та ліцензійних паспортів, замовлень на устаткування, заявок на винаходи і промислові зразки.
Розглядає раціоналізаторські пропозиції щодо удосконалення технології.
9.Технологічна підготовка виробництва
Виробництво виробів без належної технічної підготовки подовжує терміни освоєння (виходу на планову рентабельність) у 2 - 2,5 рази. У цьому випадку рентабельний період скорочується тому що настає моральне старіння продукції, падіння попиту на неї і найчастіше зниження ціни на неї.
Основними задачами технічної підготовки виробництва на промисловому підприємстві є: формування прогресивної технічної політики, спрямованої на створення більш прогресивних видів; створення умов для високопродуктивної, ритмічної і рентабельної роботи підприємства; послідовне скорочення тривалості технічної підготовки виробництва, її трудомісткості і вартості при одночасному підвищенні якості усіх видів робіт.
Перед технічною підготовкою стоять такі основні завдання: освоєння виробництва та випуск виробів високої якості при мінімальних термінах, трудових і матеріальних затратах на підготовку виробництва; запровадження для всіх підприємств і організацій системного підходу у виборі методів і засобів технічної підготовки, які відповідають останнім досягненням науки, техніки та виробництва; досягнення високої гнучкості виробництва, яка дала б змогу безперервно вдосконалювати виробництво та швидко переналагоджувати його на випуск нових виробів; здійснення раціональної організації механізованого і автоматизованого виконання робіт.
10.Основи проектування технологічного процесу механічної обробки деталі
Задачі технологічного проектування: проектування ТП виготовлення деталей (складання) повинно дати детальний опис процесів виготовлення з необхідними техніко-економічними розрахунками і обґрунтуванням вибраного варіанту (оскільки їх зазвичай буває декілька). Наприклад поверхня деталі може бути оброблена різними методами і в різній послідовності, один і той же вузол може бути зібраний з використанням різних методів досягнення точності. Тому із різних варіантів ТП виготовлення одного і того ж виробу, рівноцінних з технічної точки зору, вибирають найбільш ефективний і рентабельний.
Вирішення задач проектування ТП залежить від багатьох факторів, являє собою трудомісткий процес і вимагає оптимізації навіть для простих деталей, тому і виконується в декілька стадій. Степінь поглиблення розробок залежить від типу виробництва. Дуже детальні розробки необхідні для масового і серійного виробництв, схематичні - для одиничного.
При проектуванні ТП виготовлення деталей машин необхідно враховувати основні напрямки в сучасній технології машинобудування, які зводяться до наступного:
1. Максимальне скорочення обробки металу різанням шляхом виготовлення заготовок з найбільшою точністю. В результаті цього економиться метал, інструмент, електроенергія, скорочується машинний парк, трудомісткість і вартість обробки.
2. Інтенсифікація ТП і підвищення продуктивності шляхом використання верстатів високої продуктивності, агрегатних верстатів, автоматизованого обладнання, використання твердосплавного і мінералокерамічного інструменту, швидкодіючих пристроїв, підвищених режимів обробки, використання сучасних більш досконалих методів обробки.
3. Досягнення найбільш продуктивними методами обробки високої точності розмірів і форми деталей, якості їх поверхонь.
4. Розвиток і впровадження технології зміцнення - підвищення експлуатаційних властивостей деталі і зміцнення її поверхні термічними, хіміко-термічними, наплавленням твердих сплавів, пластичним деформуванням та іншими засобами.
5. Висування при проектуванні на перший план оптимального ТП, уніфікація ТП.
6. Більш широке впровадження поточного методу не тільки в масовім, а й у серійнім виробництві.
12.Порядок проектування технологічних процесів
Розробка технологічного процесу виготовлення деталі здійснюється в певній послідовності (етапи проектування):
1. отримання завдання на проектування техпроцесу;
2. встановлення виду (типу) виробництва та організаційної форми виконання технологічного процесу з розрахунком величини партії деталей, що запускаються у виробництво одночасно (для серійного виробництва), визначення такту випуску деталей (для потокового виробництва);
3. технологічний контроль робочого креслення і технічних умов з вивченням службового призначення виробу і деталі в ньому, а також аналіз деталі на технологічність;
4. вибір виду заготовок, визначення їх розмірів та припусків;
5. вибір баз, необхідних для обробки заготовок;
6. вибір маршрутів (методів) обробки окремих поверхонь заготовки;
7. вибір маршруту виготовлення деталі в цілому;
8. розробка окремих операцій техпроцесу, включаючи вибір типів і визначення технічних характеристик верстатного обладнання, пристосувань, ріжучого і вимірювального інструменту, режимів обробки, а також встановлення норм часу на обробку по кожній операції і визначення кваліфікації роботи
9. оцінка техніко-економічної ефективності спроектованого технологічного процесу;
10. Оформлення документації технологічного процесу.
Перші два етапи проектування техпроцесу є фактично заданими даними. При виконанні третього етапу проектування техпроцесу слід, загалом, враховувати, що проектування техпроцесу передує детальне вивчення робочого креслення деталі, технічних умов її виготовлення і умов її роботи у виробі. Перевіряється достатність проекцій, правильність простановки розмірів, вивчаються вимоги по точності і шорсткості обробки поверхонь, а також інші вимоги технічних умов. Нерідко конструктори завищують точність і шорсткість поверхонь деталі, що ускладнює техпроцес її виготовлення. У таких випадках технологом можуть бути запропоновані відповідні корективи й на основі спільного з конструктором обговорення питання знаходиться правильне вирішено
ії.1. Робочі креслення деталі і складальної одиниці, в яку вона входить, з детальними даними про форму і розміри деталі, з вказівкою допусків і посадок та шорсткості поверхні.
2. Технічні вимоги на виготовлення деталі, що визначають вимоги точності і якості обробки, а також можливі особливі вимоги (твердість, структура матеріалу, термічна обробка, балансування, припасування за масою, гідравлічні випробовування і т.д.).
3. Програмне завдання і термін, протягом, якого повинна бути виконана програма випуску деталей.
4. Дані про наявність обладнання або про можливості його придбання.
9.Методи обробки поверхонь. Визначення технологічних баз
Основним видом обробки на машинобудівних заводах є верстатна обробка, що виконується на металорізальних верстатах. При обробці заготовок в механічних цехах технологічний процес розділяється на окремі операції, що виконуються на різних верстатах із застосуванням різноманітних різальних інструментів і пристосувань. Щоб виконати обробку поверхні заготовки і одержати деталь заданої форми, необхідно закріпити заготовку і різальний інструмент та переміщувати їх в процесі обробки один відносно одного. При цьому на верстаті повинно виконуватись два рухи:
1. головний рух різання, при якому лезо інструменту врізується в метал і відділяє від нього стружку;
2. рух подачі необхідний для підводу під лезо нових шарів металу.
Точіння
Точіння площин
Точіння площин виконують на верстатах токарної групи. На них обробляють торцеві поверхні деталей типу вал, диск, шків та ін. тіла обертання, а також площини насосів та інших деталей.
Процес точіння виконується при обертанні заготовки (головний рух — швидкість різання V, яка вимірюється у м/хв) та подачі S інструмента у мм/об у напрямку, перпендикулярному до осі заготовки. Залежно від конструкції верстата заготовка може обертатися навколо горизонтальної чи вертикальної (наприклад, на токарно-карусельних верстатах) осі шпинделя.
Особливістю точіння поверхонь є зміна швидкості різання під час переміщення різця відносно осі шпинделя. При точінні з напрямком подачі S від периферії до центра вона зменшується, а навпаки — збільшується.
Процес точіння площин (підрізання торців) забезпечує точність 9-10-го квалітетів при шорсткості Ra (6,3…1,25) мкм
Точіння зовнішніх циліндричних поверхонь
Подача при точінні здійснюється переміщенням інструмента уздовж осізаготовки, перпендикулярно до неї, під кутом, або по складній кривій при обробці фасонних поверхонь і вимірюється у міліметрах на один їїоберт S, мм/об.
Швидкість різання при точінні залежить від етапу обробки, матеріалу заготовки та різальної частини інструмента і в середньому становить 50…250 м/хв. Точіння забезпечує досягнення точності від 12-14-го квалітетів з шорсткістю поверхні Ra (25…6,3) мкм при чорновій обробці до 8-9-го квалітетів при чистовому точінні із шорсткістю Ra 0,4 мкм.
Розточування
Розточування отворів виконують в основному на верстатах токарної, розточувальної груп. Розточування виконується різцями різних конструкцій, які можуть бути закріплені як безпосередньо у різцетримачеві верстата, так і в спеціальних оправках. Швидкість різання забезпечується обертанням заготовки, а подача — переміщенням інструмента. На верстатах розточувальної групи обертається інструмент, а подача здійснюється як рухом шпинделя з інструментом, так і рухом стола із заготовкою.
Чистове розточування забезпечує точність обробки отвору за 8-10-м квалітетами при шорсткості поверхні Ra (0,8…2,5) мкм
З механіки відомо, що тверде тіло має шість ступенів вільності: три пов'язані з переміщенням тіла уздовж трьох взаємно перпендикулярних осей координат OX, OY, OZ і три — з можливим його поворотом відносно цих осей. При установці деталі для обробки кожен зі ступенів вільності пов'язується шляхом притиску деталі до відповідної нерухомої точки (опори). Кожна опора зв'язує один ступінь вільності деталі, отже для позбавлення деталі всіх ступенів вільності необхідно, щоб у пристрою було шість нерухомих опорних точок (правило шести точок). При порушенні правила шести точок настає невизначеність базування.
Ці точки знаходяться в трьох взаємно перпендикулярних площинах (базах) I, II та III: точки 1, 2 і 3, розташовані в площині XOY, позбавляють деталь трьох ступенів вільності — можливості переміщувати уздовж осі OZ і обертатися навколо осей OX, OY; точки 4 і 5, розташовані в площині XOZ, позбавляють деталь двох ступенів вільності — можливості переміщувати уздовж осі OY і обертатися навколо осі OZ; точка 6, розташована на площині YOZ, позбавляє деталь шостого ступеня вільності — можливості переміщувати уздовж осі OX. Сили затиску, що діють у напрямках, перпендикулярних до трьох площин, притискають деталь до шести нерухомих опор. Число нерухомих опор у пристрою не повинне бути більше шести, тому що в протилежному випадку створюється хитке положення оброблюваної деталі в пристрої.
14.Визначити методи обробки кожної поверхні деталі
Обраний варіант базування є основою для визначення послідовності обробки поверхонь заготовки. Разом з тим, визначаючи послідовність обробки, враховують: а) конструктивні особливості деталі; б) вимоги до її якості; в) методи одержання заданих розмірів; г) властивості заготовки (матеріал, маса, розміри, припуски на обробку); д) можливості обладнання; ж) необхідність у термічній обробці; з) організацію виробничого процесу та ін.
Обробку заготовки починають, як правило, з підготовки технологічних баз. У комплекті баз у першу чергу обробляють поверхню (або сполучення поверхонь), що позбавляє заготовку більшого числа ступенів вільності (установочна або подвійна напрямна база).
На початку ТП необхідно прагнуть зняти з заготовки найбільші припуски для того, щоб створити кращі умови для перерозподілу залишкових напружень у заготовці і розкрити можливі дефекти на ранній стадії обробки.
Високі вимоги до точності форми, розмірів і відносного положення поверхонь деталі обумовлюють вести обробку заготовки в кілька Тпр. В окремих випадках попередню й остаточну обробку поверхні виконують послідовно при одній установці заготовки. Частіше ці етапи розділяють, відносячи остаточну обробку поверхонь на кінець ТП.
У кінець ТП виносять також обробку легко пошкоджувальних поверхонь (наприклад, зовнішніх нарізок).
На послідовність обробки поверхонь заготовки впливають термічна і хіміко-термічна обробка. Неминуче деформування заготовки в результаті такої обробки змушує передбачати в ТП попередню та остаточну обробку і починати останню з “виправлення” технологічних баз. Поверхні, виправлення яких після термічної обробки важко (наприклад, кріпильні отвори в корпусних деталях), обробляють після її виконання. Деякі види хіміко-термічної обробки ускладнюють процес механічної обробки. Так, при цементації, якщо потрібно обробити тільки окремі поверхні заготовки, інші захищають або нанесенням міді, або додатковим припуском, що видаляється після цементації, але до загартування.
Впливає на послідовність обробки поверхонь і необхідність дотримання черговості в утворенні різних конструктивних елементів деталі. Наприклад, кріпильні різьбові отвори потрібно обробляти після того, як буде остаточно оброблена поверхня заготовки, з яким вони сполучені. У противному випадку нарізка в отворах буде зіпсована.
15.Призначення операційної карти
У маршрутному технологічному процесі зміст операцій викладається тільки в маршрутній карті без вказівки переходів (допускається включати режими обробки, тобто рядок зі службовим символом - Р). Застосовується в одиничному й дрібносерійному типах виробництва.
В операційному технологічному процесі маршрутна карта містить тільки найменування всіх операцій у технологічній послідовності, включаючи контроль і переміщення, перелік документів, застосовуваних при виконанні операції, технологічне встаткування й працезатрати. Самі операції розробляються на операційних картах. Застосовується в крупносерійному і масовому типах виробництв.
У маршрутно-операційному технологічному процесі передбачається короткий опис змісту окремих операцій у маршрутній карті, а інші операції оформляються на операційних картах. Усі види технологічних документів містять єдину форму основного напису.
16.Вибір обладнання по операціям технологічного процесу
Вибираючи обладнання при проектуванні робочого технологічного процесу, орієнтуються на обладнання, яке єв цеху з урахуванням фактичного завантаження окремих його груп. В умовах одиничного виробництва проектування нових технологічних операцій для дуже завантаженого унікального обладнання, що лімітує загальний випуск заводської продукції, може бути застосоване лише у виняткових випадках, коли ніякі інші верстати, а також методи обробки не можуть бути використані. В будь-яких інших випадках слід застосовувати інше наявне обладнання, що забезпечує якісну обробку деталей. При проектуванні технологічних процесів для підприємств, що створюються, можливості технолога обмежені лише економічними міркуваннями.
Вибір верстата для реалізації операції виконують за такими критеріями:
- тип виробництва;
- технологічні можливості, щодо реалізації включених до операції методів обробки (склад технологічних переходів);
- габарити робочої зони;
- кількість розміщуваних інструментів;
- потужність двигунів;
Згідно з класифікацією верстатів, верстатне обладнання поділяться на такі види: верстати широкого або загального призначення (універсальні), верстати високої продуктивності, верстати спеціалізовані та спеціальні.
Верстати широкого або загального призначеннязастосовують у дрібносерійному та одиничному виробництвах. Верстати високої продуктивностімають обмежені технологічні можливості. Однак, завдяки підвищеній потужності і жорсткості, на них можна вести обробку на більш високих режимах різання й більш концентрованими методами. До верстатів цього виду належать: токарні багато різцеві, круглошліфувальні, що працюють методом поперечної подачі, безцентрово-шліфувальні, барабанні, карусельні, фрезерні та ін. Такі верстати призначені для великосерійного та масового виробництв. Спеціалізовані верстатистворюють на базі верстатів високої продуктивності встановленням додаткових шпинделів та інших вузлів, за допомогою яких вони можуть бути пристосовані для виконання конкретних операцій при обробці конкретних деталей в умовах масового виробництва. Спеціальні верстатипроектують та виготовляють на особливе замовлення та використовують для виконання певної операції. Проектування та виготовлення верстатів цієї групи є дуже дорогим. Тому вони виправдовують себе лише у масовому виробництві. Особливі групи складають агрегатні верстати, що застосовуються в серійному та масовому виробництвах, та верстати з числовим програмним управлінням, які використовують в умовах дрібно та інколи середньо серійного виробництв. Вибір технологічного обладнання повинен базуватись на аналізі витрат на реалізацію технологічного процесу в межах життєвого циклу виробів при заданий їх якості. Результати аналізу оцінюють відношеннями: основних та штучних часів, приведених витрат при виконанні робіт на різних верстатах..
Практика показує, що найбільш багатоваріантним є обладнання для токарної обробки. Питання про вибір токарного, токарно-револьверного, токарного одно чи багатошпиндельного напівавтомата може бути вирішене без складних розрахунків, за допомогою графіків та діаграм, що встановлюють межу економічного використання цих верстатів при різних програмах випуску виробів. У кожному конкретному випадку, вибираючи модель, користуються паспортами верстатів, а при їх відсутності — каталогами металорізального та іншого обладнання.
Дата добавления: 2019-01-14; просмотров: 216; Мы поможем в написании вашей работы! |
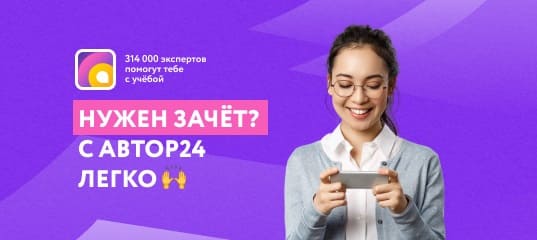
Мы поможем в написании ваших работ!