Отделочные способы обработки зубчатых поверхностей
Повышение точности и чистоты зубчатых поверхностей достигается шевингованием, шлифованием, притиркой, обкаткой и приработкой. Шлифованием и притир-кон обрабатываются закаленные зубчатые поверхности, а шевингованием, обкаткой и приработкой — сырые или закаленные до твердости HRC 32—35.
Шевингование — это процесс снятия с боковых поверхностей зубьев тонкой волосообразной стружки толщиной 0,001—0,005 мм при помощи специального инструмента — шевера. Шевер представляет собой косозубое или прямозубое колесо, на зубьях которого в поперечном направлении нанесены канавки, образующие режущие кромки. Эти кромки и соскабливают волосообразную стружку.
Известно несколько способов шевингования цилиндрических колес, но наибольшее распространение получила обработка дисковым шевером (рис. 7.16).
Дисковые шеверы обычного назначения для обработки цилиндрических прямозубых и косозубых колес регламентируются ГОСТом. Предусматривается три класса точности шеверов: А, В и С. Для колес 6-й степени точности рекомендуются шеверы класса А, 7-й степени точности — класса В и 8-й степени точности — класса С.
Колеса 6-й и 7-й степеней точности можно получить в том случае, если числа зубьев шевера и колеса не имеют общих множителей.
В процессе шевингования (рис. 7.17) зубья шевера 1 и обрабатываемого колеса 2 находятся в зацеплении и образуют зубчатую передачу со скрещивающимися осями.
|
|
Шевер приводит во вращение обрабатываемое колесо, которое получает еще и осевое возвратно-поступательное перемещение — продольную подачу. Продольная подача (snp = 0,15—0,3 мм/об. д) позволяет равномерно снять припуск по всей длине зуба. Стол станка имеет вертикальное перемещение для создания давления шевера на колесо. Это перемещение стола называется радиальной подачей. Она составляет sp =0,025— 0,04 мм/ход стола. После окончания каждого хода стола шевер изменяет направление вращения и обрабатывает другую сторону зуба.
Величину угла скрещивания при шевинговании следует выбирать в пределах γ = 10—20°. При обработке колес с закрытыми венцами в крайних случаях можно принимать величину угла γ = 5°. Однако при шевинговании с γ = 5° степень точности обработки понижается.
Имеется несколько схем шевингования. Наиболее часто применяют шевингование с диагональной подачей. В данном случае при перемещении обрабатываемого колеса его ось не совпадает с осью шевера, что значительно сокращает продольный ход шевера относительно колеса и уменьшает машинное время. Кроме того, из-за непрерывного изменения точек контакта зубьевшевера с обрабатываемой поверхностью они изнашиваются равномерно по всей длине, благодаря чему стойкость инструментаувеличивается.
|
|
Диагональноешевингование можно производить на специальныхили спомощью приспособлений на любых шевинговальных станках.
Чистовая обработка колес, зубья которых образованы горячим накатыванием, осуществляется новым способом шевингования — путем снятия больших припусков. Этот способ получил название «герак».Шевингование ведется кромочным шевером, который представляет собой зубчатое колесо, сопрягаемое с обрабатываемым колесоми составляющее с ним винтовую пару. Шевингование этим способом производится на специальных станках.
Величина припуска под шевингование зависит от модуля и диаметра обрабатываемою колеса и находится в пределах 0,06—0,2 мм на сторону по толщине зуба. Этот припуск снимается за 12—20 двойных ходов стола, после чего осуществляется дополнительно несколько проходов без радиальной подачи для выкатывания обрабатываемой поверхности: 2—4 прохода — для колес 7-й степени точности и 4—6 проходов — для колес 6-й степени точности.
Наибольшие допустимые скорости резания при шевинговании различных сталей— 105—150 м/мин.
В некоторых случаях шевингование зубчатых колес осуществляют перед их термической обработкой с целью уменьшения возникающих деформаций. При снятии больших припусков создается наклеп, который при термической обработке колес приводит к значительному короблению их и нарушению полученной ранее точности. Шевингование зубьев уменьшает наклеп и деформации в3,5 раза по сравнению с соответствующими погрешностями, полученными при фрезеровании зубьев за один проход. Поэтому после термической обработки колес операцию шлифования зубьев можно заменить хонингованием и притиркой.
|
|
Шлифование. Термически обработанные зубчатые поверхности подвергают шлифованию. Это позволяет получать зубчатые колеса 6—7-й степеней точности, а на некоторых моделях зубошлифовальных станков — 5-й и даже 4-й. Шлифованием можно устранить все виды искажения профиля зубьев после термической обработки.
Также как инарезание, шлифование зубьев осуществляется методом копирования профиля шлифовального круга и методом обкатки.
Обработка методом копирования производится профильным кругом (рис. 7.18, а), получающимвращение, возвратно-поступательное движение параллельно оси обрабатываемого колеса и подачу на глубину шлифования на каждый двойной ход. После нескольких двойных ходов круг выводится из зацепления с колесом, которое поворачивается на один или несколько зубьев. Затем цикл обработки повторяется. Прямозубые колеса с внешними зубьями и открытыми венцами 6—7-й степеней точности шлифуются на станках моделей 5860 и 5961. Прямозубые и косозубые колеса с внутренними зубьями и открытыми венцами 6—7-й степеней точности обрабатываются на станках моделей 5868 и 5860В.
|
|
Шлифование методом обкатки осуществляется дисковыми и тарельчатыми кругами (рис. 7.18, б и в) и абразивным червяком.
В мелкосерийном производстве прямые и косые внешние зубья колес с открытыми венцами 6—7-й степеней точности обрабатываютодним двусторонним конуснымкругом. На станках мод. 5831 шлифуют отдельно каждуюсторону впадины, а настанках мод. 584 — одновременно обе стороны впадины. Ось обрабатываемого колеса вертикальная. Деление иобкатка осуществляются с помощью червячной делительной пары стола.
У тарельчатых кругов (рис. 7.18, в) рабочей поверхностью является узкая круговая ленточка, которую легко править алмазом. Круги, установленные под углом α, равным углу зацепления, получают только вращательное движение. Обрабатываемое колесо совершает обкаточное движение, возвратно-поступательное (вдоль оси) и осуществляет поворот.
Круги правят алмазом 2, который закреплен в рычаге 1. Между алмазом и кругом имеется зазор. Через определенные промежутки времени ролик 3 попадает во впадину диска 4, и рычаг 1 под действием пружины прижимает алмаз 2 к шлифовальному кругу. Если износ круга в пределах допуска, то контакты 5 не замыкаются. При большом износе круга происходит замыкание контактов и включается механизм, автоматически смещающий круг на величину износа.
Наиболее высокую точность колес (4—5-ю степени) получают при обработкена станках типа«Мааг». Режущим инструментом являются здесь два шлифовальных круга тарельчатой формы. Они расположены под углом друг к другу таким образом, что внешние очертания их режущих кромок образуют форму зуба рейки. Угол наклона кругов сохраняется в процессе шлифования постоянным и
равен 15 или 0°. Обрабатываемое колесо обкатывается вокруг шлифовальных кругов, которые благодаря этому шлифуют обе стороны впадины зуба.
Для получения необходимого обкаточного движения обрабатываемого колеса относительно воображаемой зубчатой рейки вместо эталонной шестерни и рейки применяют специальные ленточные или другие механизмы. При обкатке с помощью ленточного механизма (рис. 7.19) на ось с обрабатываемым колесом 3 насаживают диск 2, охватываемый стальной лентой 1. Стол станка, несущий диск 2 и колесо 3, получает возвратно-поступательное перемещение по стрелкама — б. Диск, обкатываясь по ленте, сообщает колесу движение, подобное качению по репке. Диаметр диска должен быть равен диаметру основной окружности колеса. После того как профиль зуба прошлифовандо заданного размера, механизм деления поворачиваетколесо па один зуб. Перед этим круги выводятся из зацепления с колесом, и возвратно-поступательноедвижениепрекращается. Износ шлифовальных кругов автоматическикомпенсируется при помощи электромагнитногоаппарата.
Наиболее производительна обработка цилиндрических колес спрямыми и косыми зубьями абразивным червяком на станках моделей 5А830 и5А832. По сравнению с другими способами зубошлифования обработка червячным кругом позволяет в 3—5 раз увеличить производительность труда.
Абразивным червяком диаметром 270—350 мм шлифуют колеса модулем 0,5—4 мм и наружным диаметром до 240 мм. У колес модулем до 1,5 мм можно образовывать зубья без предварительного нарезания их. При обработке этим способом получают колеса 5—6-й степеней точности.
Колеса скосыми зубьями шлифуют с максимальным углом наклона спирали 45°. При обработке прямозубых колес заготовку поворачивают на угол, равный углу подъема витка на червяке.
Хонингование применяют для отделки зубьев закаленных зубчатых колес. Кинематическая схема процесса та же, что ипри шевинговании, но вместо металлического шевера используется абразивный хон, который изготовляют в виде косозубого или прямозубого цилиндрического колеса из мелкозернистого карбида кремния зеленого на органической связке.
Хонингование позволяет устранить поверхностные дефекты зубьев (забоины, риски), снизить погрешности основного шага ипрофиля, уменьшить биение, атакже улучшить шероховатость обрабатываемой поверхности.
Оптимальный припуск под хонингование, установленный ЭНИМСом,— 0,005—0,02 ммна сторону, практически же оставляют припуск 0,01—0,015 мм на сторону. Процесс осуществляетсяпри обильной подаче охлаждающей жидкости.
При обработке хон иколесо соединяют в плотном зацеплении или с боковым зазором. Наибольшая эффективность процесса достигается при угле между осями хона иобрабатываемого колеса γ = 15—18°.
Хонингованиюподвергают колеса, точность которых должна соответствовать 6—7-й степеням. В этом случае xoн должен быть изготовлен по 5—6-й степеням точности.
Для хонингования цилиндрических зубчатых колос могут быть использованы модернизированные шевинговальные станки (например, мод. 5714). Модернизация станка заключается в повышении скорости резания( v = 7—10м/сек) и обеспечении тарированного прижатия обрабатываемого колеса к хону.
Длительность хонингования зубьев колес диаметром до 300 мм — 40—60 сек., достигаемая шероховатость поверхности— 10—11-й классы.
Притирка зубьев широко осуществляетсяи крупносерийноми массовом производстве при изготовлениитермическиобработанных колес ответственных передач.
Процесс притиркизаключается в том, что обрабатываемоеколесо вращается взацеплении свращающимися чугунными шестернями-притирами, смазанными пастойиз смеси мелкого абразивного порошка и масла.
Применяют два способа притирки: припервом — оси обрабатываемого колеса ипритира параллельны; при втором — оси обрабатываемого колеса ипритиров скрещиваются под небольшим углом.
Притирка колеса 1 по первому способу (рис. 7.20, а) производится одним притиром 2 того же модуля и заключается по взаимном обкатывании зубьев обрабатываемого колеса и притира, на рабочую поверхность которого нанесена абразивная паста. В процессе притирки колесо 1 вращается (от электродвигателя) и одновременно совершает небольшие осциллирующие движения в радиальном направлении, а притир 2, увлекаемый колесом, помимо вращения совершает возвратно-поступательное движение в осевом направлении. Вращения колеса и притира реверсируются.
При втором способе притирки (рис. 7.20, б) происходит взаимное обкатывание зубьев колеса 1 и зубьев трех чугунных притиров 2, 3 и 4 одновременно. В большинстве случаев для притирки колеса с прямыми зубьями притиры 3 и 4 делают косозубыми с углом наклона зубьев 5—10о, причем у одного притира направление зубьев правое, а у другого — левое. Притир 2 делают прямозубым. Для притирки косозубых колес притир делают косозубым с одинаковым, но противоположно направленным наклоном зубьев; oсь его остается параллельной оси колеса 1. Притиры 3 и 4 также делают косозубыми с углом наклона зубьев колеса на величину необходимого угла скрещивания. Скорость вращения обрабатываемого колеса должна составлять 30—60 м/мин.
Необходимое давление на боковые поверхности зубьев во время притирки создается гидравлическими тормозами, действующими на шпиндели притиров.
Притирка — высокопроизводительный способ отделки зубчатых колес. Колесо сродного размера притирается обычно за 2—4 мин., при этом шероховатость поверхности соответствует 9—10-му классам. Однако с помощью притирки можно исправить сравнительно небольшие погрешности предыдущей обработки, так как припуск на притирку составляет не более 0,03 мм на сторону. При наличии ошибок в шаге и профиле зуба более 0,04 — 0,05 мм притирка становится неэффективной. Так как в процессе термической обработки колета толщина зубьев, как правило, увеличивается на 0,03—0,04 мм, то в этих случаях припуска на притирку можно не оставлять.
Если подготовленное под притирку колесо имеет 7-ю степень точности, а притир —5-ю, то в результате притирки получают колесо 6-й степени точности.
Притирку цилиндрических колес осуществляют на станках моделей 573, 5735 и ЕЗ-8.
Дата добавления: 2018-11-24; просмотров: 1017; Мы поможем в написании вашей работы! |
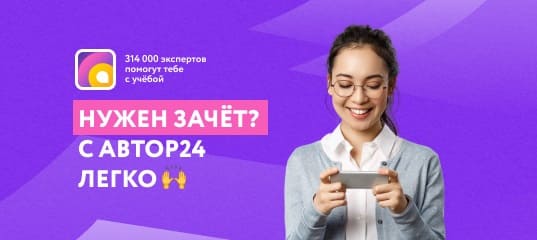
Мы поможем в написании ваших работ!