Материалы на основе нанообъектов. Области применения нанопорошков и нанопленок.
Учитывая тот факт, что известные на настоящий момент наноматериалы пришли в современные нанотехнологии из различных областей науки и техники, приемлемой единой классификации, на какой-либо основе, просто не существует.
Наноматериалы:
- Объемные наноструктурированные материалы;
- Нанокластеры, наночастицы, нанопорошки;
- Многослойные наноплёнки, многослойные наноструктуры, многослойные нанопокрытия;
- Функциональные (умные) наноматериалы;
- Нанопористые;
- Фуллерены и их производные нанотрубки;
- Биологические и биосовместные материалы;
- Наноструктурированные жидкости: коллоиды, гели, взвеси, полимерные композиты;
- Нанокомпозиты.
Первые наночастицы были созданы человеком непреднамеренно, случайно, в различных технологических процессах. В настоящее время их стали конструировать и производить специально, что и заложило основу нанотехнологиям. Развитие нанотехнологий привело к принципиальному пересмотру некоторых фундаментальных принципов:
Путь «сверху-вниз» - общая парадигма нанотехнологий ( от заготовки отрезается лишнее)
Нанотехнологии предлагают путь «снизу-вверх» - от малого к большому (от атома к объекту). Это парадигма нанотехнологий.
В основном, в настоящее время, в нанотехнологиях доминируют технологические приемы, пришедшие к нам из макротехнологий. Для создания наночастиц, которые относятся к классу 0-D объектов. Современные нанотехнологии применяют способ диспергирования, т.е. измельчения. Для того чтобы измельчить (диспергировать) любой макроскопический объект до наноразмеров обычное диспергирование не подходит. Чем мельче размер частиц, тем выше активность их поверхности, в результате отдельные частицы объединяются в объемные конгломераты. Поэтому для ультратонкого диспергирования требуется применение определенного типа среды в виде поверхностно-активных веществ, которые снижают силы поверхностного натяжения, а также стабилизаторов. Мылоподобные композиции, которые препятствуют повторному слиянию. При определенных условиях. Когда на границе твердого тела поверхностная энергия сильно снижена процесс диспергации может происходить самопроизвольно, за счет. Например, теплового движения частиц. Этими методами можно получить порошки Ме с размерами частиц десятки нм. Оксидами этих металлов с размерами частиц в 1 нм. А также производить диспергацию полимеров, компонентов керамик и т.д.
|
|
Предпосылкой успешной реализации потенциальных возможностей наноразмерных частиц вещества в потребительских свойствах объемного материала является предварительное решение следующих основных задач:
|
|
• определить верхний предел наноразмерного диапазона дисперсных частиц вещества или структурных элементов материала;
• отработать технологию получения вещества в виде дисперсных частиц наноразмерного диапазона;
• отработать технологию консолидации наночастиц или фрагментирования структурных элементов материала до наноразмерного диапазона.
Основные способы консолидации наночастиц в объемные материалы располагаются в следующей исторической последовательности:
• прессование наночастиц;
• модифицирование традиционных материалов добавками наночастиц;
• совмещение процессов получения наночастиц и их консолидации в моностадийной технологии;
• фрагментирование структурных элементов традиционных материалов до наноразмерного диапазона.
Для консолидации дисперсных частиц нанометрового диапазона используют хорошо отработанные в процессе многолетней производственной практики технологические приемы порошковой металлургии.
Объемный наноструктурированный материал. Консолидация нанопорошков методами порошковой металлургии включает в себя две основные технологические операции — прессование порошкообразной шихты в замкнутой матрице и спекание полученного полуфабриката. Часто эти операции совмещают, проводя спекание под давлением. При использовании порошковых технологий для получения компактных изделий отмечена обратно пропорциональная зависимость плотности прессовок от крупности шихты. Например, относительная плотность заготовок из зерен крупностью 40 мкм составляет 90%, а для шихты из нанопорошка крупностью 25 нм — только 45%. Это является следствием повышенных значений коэффициента трения между наночастицами шихты и шихты со стенками пресс-формы. Для преодоления сил адгезионного сцепления, особенно значимых для наночастиц с их высокоразвитой поверхностью, используют динамические методы ком-пактирования нанопорошков. Хороших результатов достигают при наложении на процесс прессования ультразвукового поля.
|
|
Объемный материал с нанонаполнителем. Исследованиями в области модифицирования традиционных материалов добавками наночастиц занято наибольшее число участников. Повышенный интерес к данному направлению работ вызван тем, что нанораз-мерный наполнитель вводится в технически значимые материалы промышленного производства, не нарушая устоявшийся технологический процесс изготовления этих материалов. Дополнительным стимулом к дальнейшему развитию исследований по модифицированию промышленных материалов традиционной технологии наночастицами является возможность получения максимального положительного эффекта при введении нанодобавок в сверхмалых количествах.
|
|
Для создания возможности практического использования преимуществ наноразмерного состояния вещества в реальных конструкциях дискретные наночастицы, полученные из исходного сырья, независимо от их геометрической формы и метода получения, вводят в матрицу. В качестве матрицы используют промышленные материалы традиционной технологии. Для совмещения наполнителя с матрицей используют также хорошо отработанную в процессе многолетней производственной практики технологию композиционных материалов.
Отметим, что наноразмеры наполнителя вносят в традиционные технологии дисперсных частиц свою лепту. Все методы синтеза наноразмерного наполнителя приводят к его получению в неравновесном метастабильном состоянии. Свободная энергия ненасыщенных связей периферийных атомов наночастиц реализуется в их избыточной энергии, что обусловливает высокую химическую активность наночастиц. Это создает значительные трудности в осуществлении технологического процесса введения и равномерного распределения химически активного наполнителя в матрице композиционного материала.
Технология совмещения дисперсного наполнителя с матрицей состоит из большого числа операций, что резко увеличивает продолжительность и стоимость технологического цикла производства конечного продукта. Это резко удорожает материал, что делает его промышленное применение дискуссионным.
Принципиальным недостатком рассмотренных выше и принятых всеми мировыми производителями многостадийной технологии промышленного производства объемных наноструктуриро-ванных материалов и материалов с добавками наноразмерного наполнителя является разделение в пространстве и во времени технологических процессов получения наночастиц и их компакти-рования. Они часто выполняются разными предприятиями, что также значительно усложняет организацию производства.
Объемный наноматериал. Нами предложены теоретические основы моностадийной технологии объемных наноматериалов конструкционного назначения. Экспериментальная проверка теоретических положений выполнена на примере углерода в аллотропной модификации графита, что представляло значительный теоретический и практический интерес.
По предлагаемой технологии наноразмерный наполнитель формируется одновременно с матрицей в одном и том же химическом реакторе, т.е. технология является моностадийной: в реактор поступает сырье, а из реактора выходит конечный продукт — объемный наноматериал. Этим предлагаемая технология принципиально отличается от традиционно многостадийной технологии компактирования наноразмерного наполнителя. Предлагаемая технология позволяет практически при тех же экономических затратах получать объемный наноматериал вместо нанопорошка .
Объемный нанофрагментированный материал. Другим направлением реализации преимуществ наноразмерного состояния вещества в свойствах объемного материала является фрагментирование структурных элементов в матрице будущего композиционного материала до наноразмерного состояния. В данном случае наноразмерные структурные элементы не вводятся извне, а формируются в самой матрице будущего композиционного материала.
Теоретической основой фрагментирования является вторичная кристаллизация материалов традиционной технологии, классификационным признаком которой является перестройка кристаллической решетки составляющих материал веществ в твердом состоянии без их плавления.
В случае твердофазной перекристаллизации реакционная среда служит матрицей, скрепляющей образующиеся наночастицы в наноразмерные фрагменты структурных элементов объемного наноматериала. Это означает, что при соответствующей организации технологического процесса получение объемного нанофрагменти-рованного материала также может осуществляться в одну стадию.
Процессы твердофазной перекристаллизации наиболее широко распространены в металловедении, на них основана технология термического упрочнения металлов и их сплавов. На использовании процессов твердофазной перекристаллизации основана также технология ситаллов.
В качестве матрицы в технологии нанофрагментированного материала используют промышленные материалы, которые имеют и самостоятельное применение в качестве конструкционного материала. Фрагментацию структурных элементов матрицы осуществляют различными способами, среди которых можно отметить:
• метод интенсивной пластической деформации металлов с основными модификациями аппаратурного оформления процесса: а) кручение под квазигидростатическим давлением; б) равноканальное угловое прессование; в) всесторонняя изотермическая ковка;
• вторичную кристаллизацию аморфных металлов с выделением наноструктурированных кристаллитов интерметаллидов;
Использование наноразмерных веществ в промышленности возможно благодаря разнообразию принципиально новых свойств этих материалов. Ниже представлен краткий обзор применения этого нового класса веществ в электромашиностроении и электроэнергетике.
Прежде всего, применение наноматериалов позволяет создавать конструкционные материалы с повышенными механическими свойствами.
Изготовление высокопрочных резьбовых изделий из титана и их сплавов. Детали из титана широко используются в авиа- и автомобилестроении. Формирование наноструктуры приводит к повышению долговечности изделия в 1,5 раза.
Использование алюминиевых сплавов эффективно для получения легких (по весу) изделий сложной формы в режиме высокоскоростного сверхпластического формообразования. Применение наноматериала позволяет, в свою очередь, достигать более полного заполнения гравюры штампа, что обеспечивает качественное формообразование и значительно снижает усилия при штамповке изделия. В частности снижается температура процесса до 3500С, что на 1000С меньше температуры формообразования литейных сплавов. В настоящее время таким методом получают поршни сложной формы, которые используются в малогабаритных двигателях внутреннего сгорания.
В качестве жаропрочных материалов применяются изделия, получаемые компактированием наноструктурных легированных нитридных керамик. Они используются для изготовления двигателей внутреннего сгорания, газовых турбин, режущих пластин.
На основе шихты, содержащей наноалмазы, разработаны и используются волоки для холодного волочения проволоки из меди, серебра, золота, платины и др. металлов.
Весьма перспективно использование нанопорошков металлов в композиционных материалах, содержащих пластмассы и полимеры. Данный прием позволяет изготавливать пластиковые магниты, электропроводную резину, токопроводящие краски и клей и другие электропроводящие композиционные материалы. Например, на основе нанопорошка Ni получен эластичный слоистый электропроводящий материал, содержащий Ni и каучук в соотношении 2:1 частей по массе, имеющий низкое, стабильное и хорошо воспроизводимое при многократном сжатии электрическое сопротивление проводящих слоев. Материал может быть использован для коммутирования жидкокристаллических и катодолюминесцентных индикаторов, светодиодов и интегральных микросхем к печатным платам.
Разработаны полимерные материалы с добавками нанопорошков металлов с контролируемым уровнем горючести. Определено, что механизм разложения полимеров зависит от содержания наноприсадок: при концентрациях порядка 0,005% металл ускоряет термоокисление материала, а при содержании металла 1% данный процесс замедляется. В качестве добавок использовали нанопорошки Al, Си, Fe.
Эффективно применение в композиционных материалах наноразмерного алмаза. Так, добавление наноалмаза повышает микротвердость композиционного материала на основе алюминия в 4-5 раз, а на основе меди — в 3-10 раз. Присадки алмазосодержащей шихты в резину, керамику, пластмассу показали существеные улучшения их характеристик: повышение износостойкости, снижение коэффициента трения, увеличение предельных нагрузок.
Нанопорошки
Нанопорошки уже в настоящее время нашли широкое применение в различных материалах и технологиях электромашиностроения.
С разработкой порошковых материалов с наноразмерными частицами стало возможно создание сухих смазочных материалов, твердосмазочных покрытий, карандашей твердой смазки и т. п. Они обладают низким коэффициентом трения, достаточно высокими магнитными свойствами и высокой дисперсностью и, следовательно, практически не оказывают абразивного воздействия на герметизируемую деталь (вал, шток и др.). Магнитопорошковые сухие смазки могут быть удержаны в рабочем зазоре магнитным полем, выполняя в этом случае функцию герметизатора магнитной псевдожидкости. Данная продукция изготавливается из нанопорошков железа, никеля, алмазосодержащей шихты.
Увеличению эффективности процессов холодной и горячей обработки металлов давлением способствует применение нанопорошков различного состава в штамповочных смазках. Например, использование нанодисперсных материалов в качестве исходных компонентов при горячем прессовании позволяет получать материалы с уникальными прочностными характеристиками: прочность материалов повышается в 2-3 раза, а твердость в 6-10 раз, положительно влияют на качество отливок из стали, сплавов полунепрерывных слитков из алюминиевых сплавов. В качестве модифицирующих добавок используются нанопорощки А1203, SiC, TiN, TiCN, WC и др.
Возможна интенсификация процесса спекания промыщленных порошков путем добавления в качестве активаторов спекания нанопорошков алюминия, никеля, железа, нитрида алюминия и др. Введение всего 0,5-5% масс наноматериалов в промышленные смеси позволяет снизить температуру спекания на 400-800 °С и сократить его время в несколько раз. При этом повышаются твердость и ударная вязкость конечной продукции. Использование добавок из нанопорошков экономически эффективно, поскольку количество этого материала составляет несколько процентов, а разработанная технология изготовления твердых сплавов практически не отличается от традиционной. В настоящее время по данной методике получают твердые сплавы на основе никелида титана со связкой из нанопорошка карбонитрида титана, корундовую и циркониевую керамику с добавлением 1-3% и 0,5-5% нанопорошка алюминия, соответственно. Кварц спекали с добавлением нанопорошка вольфрама.
Добавки наноматериалов в качестве гидродинамических пластификаторов позволяют получать при формовании высокоплотные изделия. Присадки из нанопорошков интенсифицируют процесс спекания, упорядочивают синтез соединений, что позволяет снизить температуру обжига на 300-400°С; существенно уменьшают размер пор в изделиях и повышают, тем самым, шлакоустойчивость огнеупоров.
Кроме того, нанопорошки металлов добавляют в качестве присадок в абразивные суспензии ипасты для притирочно-доводочных работ. Это позволяет в процессе приработки партрения заполнить впадины и микротрещины частицами дисперсной фазы, что способствует выравни- ванию трущихся поверхностей, залечиванию дефектов, а также разделяет поверхности трения высокодисперсными частицами.
Для финишного полирования по 13-14 классам шероховатости эффективны пасты из наноалмаза с размером частиц до 10 нм. Они используются в качестве тонкого полирующего материала при доводочных операциях в процессе изготовления особо точных деталей из различных материалов и сплавов; при полировке ювелирных изделий и полупроводниковых пластин кремния и германия; при изготовлении оптики, лазеров, стекол и зеркал специального назначения(телескопы, микроскопы, лазеры и т.д.).
Получение и применение нанокомпозитных материалов в электротехнике является мощным средством энергосбережения. Отличительной особенностью нанотехнологий является производство материалов с наноструктурными компонентами при более низких температурах.
Фундаментальной проблемой наноразмерных веществ является определение механизма процесса межзеренного взаимодействия нанокристаллических порошков. Для осуществления качественного процесса формирования наноматериалов необходимо использование комплекса оборудования для магнито-импульсного прессования порошков, что значительно расширяет возможности получения и изучения механизма образования плотных керамических материалов на основе оксидных нанокристаллических порошков. Получение практически 100% плотности на стадии формирования, что невозможно при использовании традиционных методов прессования, похволяет понизить температуру спекания нанокристаллов и уменьшить влияние процессов рекристаллизации на образование нанокерамики. Разработка технологии производства нанокерамики и других магнитных наноматериалов с повышенными механическим и функциональными свойствами позволяет получать новые материалы для магнитопроводов электрических машин.
Дешевые, легкие и прочные наноматериалы со временем вытеснят большинство металлов и пластмасс. Углеродные нанотрубки в сто раз прочнее стали при том, что в десять раз легче ее и в тысячи раз электропроводнее. Toyota уже добавляет их в бамперы автомобилей, но массового применения пока еще нет. Это связано тем, что пока нанотрубки получают примитивными, малопроизводительными методами, что обусловливает их слишком высокую для повседневного применения цену: $50-100 за грамм.
Перспективно использование наноматериалов для создания защитных, декоративных и износостойких поверхностных покрытий. Уже разработаны технологии получения мелкодисперсных покрытий из Pd, Ir, Rh, Со, Ni, Ag, Си на керамических, кварцевых, металлических, пластмассовых, композиционных изделиях с формой любой сложности. Покрытия из наноматериалов более плотные и коррозионностойкие, однородны по толщине, сохраняются на деталях сложного профиля, лучше паяются по сравнению с гальваническими или полученными вакуумным напылением покрытиями.
Получены покрытия из двухфазного композиционного наноматериала, состоящего из металлической матрицы и внедренных дисперсных частиц алмаза. В качестве матриц может использоваться широкий круг металлов: хром, никель, цинк, медь, серебро, золото, кобальт. Композиционные металл-алмазные покрытия характеризуются существенным увеличением адгезии и когезии, повышением микротвердости, износостойкости, коррозионностойкости, уменьшением пористости, хорошими антифрикционными свойствами, высокой рассеивающей способностью.
Например, при нанесении хром-алмазных покрытий срок службы прессовой оснастки для холодного прессования порошков металлов увеличивается в 15-20 раз, матриц и пуансонов для глубокой вытяжки металлов — в 2,5-4 раза, ножовочных полотен — в 4-8 раз, газораспределительных валов двигателей внутреннего сгорания — в 2-2,5 раза. После нанесения кобальт-алмазных покрытий на записывающие головки магнитофонов их износостойкость повышается в 6 раз. По сравнению с металлическими покрытиями стойкость алмазосеребряных наноматериалов повышается в 3 раза, ал-мазо-никелевых — в 4-5 раз.
Среди многообразия материалов, применяемых в электромашиностроении, ведущая роль принадлежит электротехническим сталям. По накопленным в процессе эксплуатации электрических машин данным, потери в стали энергетических электрических машин составляет 10-20% от общих потерь, а масса электротехнической стали составляет 40-50% от общей массы машины.
Как показывает опыт, имеются большие возможности широкого воздействия на свойства электротехнических сталей. Так, например, присадка кремния существенно изменяет свойства материала, вызывая образование больших кристаллов, для которых характерна меньшая площадь петли гистерезиса. Соответственно, для получения минимума потерь и требуемой для проведения магнитного потока через магнитопровод магнитной проницаемости материалов содержание кремния целесообразно увеличивать. Так, увеличение содержания кремния с 1 до 4% приводит к возрастанию удельного сопротивления сплава 2,5-3 раза, что приводит к соответствующему уменьшению потерь от вихревых токов. При этом предел текучести увеличивается почти в пять раз, а предел прочности – в 2,5 раза.
Создание новых материалов магнитопровода становится возможным при использовании нанотехнологий путем синтеза их по принципу многофазных композиционных материалов. Для получения высококонцентрированных многофазных сред, определяющих свойства материала, необходимые для создания роторов турбогенераторов, работающих при высоких центробежных нагрузках, применяются материалы, содержащие фуллереновские компоненты. Подтверждается прогноз о том, что перевод магнитных сплавов в нанокристаллическое состояние позволяет получить новый класс магнитных материалов, у которых потери на перемагничивание стремятся к нулю.
Для турбогенераторов с высокими частотами вращения эффективность работы зависит, в том числе и от диаметра ротора. Практический интерес, в этом случае, представляет получение легкого и прочного материала для ротора, что может быть достигнуто, например, при использовании матрицы карбида титана или алюмоборонитридной керамики с наноструктурными компонентами. Это позволяет рассчитывать на изготовление ротора турбогенератора с внешним диаметром до 400мм при частоте вращения до 60 000об/мин.
Ферриты, на основе оксидов циркония и железо-кобальта, имеет магнитную проницаемость 40-90μ0, что в свою очередь позволит создать новые типы электромеханических преобразователей энергии, характеризующихся уникальными параметрами, особенно по прочностным показателям.
Так как основные параметры электротехнических материалов энергетического оборудования зависят от соотношения μ и ρ, то, варьируя величины этих свойств материала, можно достигнуть желаемых рабочих характеристик оборудования, особенно таких, как низкая удельная масса, низкие потери, высокие прочностные показатели, обеспечивающие работу при высоких частотах вращения. Выбор того или иного диапазона соотношения параметров связан с требованиями к конкретному режиму эксплуатации и с показателями эффективности.
Уникальный комплекс электромагнитных свойств нашел применение при создании большого круга магнитных наноматериалов, а именно: жидких магнитов, лент магнитной и видеозаписи, кредитных карт, магнитных экранов, дисков памяти, сердечников высокочастотных трансформаторов, постоянных магнитов и магнитопроводов, материалов электроконтактов и др.
В качестве материала для магнитной записи используется порошок y-Fe203. Повышение плотности записи обеспечивается при использовании наноматериала, состоящего из игольчатых частиц с размером длинной оси 300-500 нм и короткой оси 50-70 нм.
При изготовлении электроконтактов для низковольтной аппаратуры использование нанопорошков ZnO обеспечивает электрокоррозионную стойкость, низкую склонность к свариванию, малую величину контактного сопротивления, существенно упрощает технологию изготовления, уменьшает содержание серебра в конечном изделии, повышает экологические показатели при изготовлении и эксплуатации вследствие замены токсичного CdO.
После аварии на Чернобыльской АЭС снова возобновляется интерес к атомной энергетике как обеспечивающей при необходимом уровне надежности работы условия экологической безопасности и эффективности энергетики. Безопасность ядерных реакторов и повышение их мощности определяют перспективы развития энергетического сектора России в целом и атомной энергетики в частности. Создание надежной безопасности АЭС станет возможным только на основе разработок принципиально нового класса функциональных материалов. Главной задачей этих материалов является безусловное обеспечение ими работоспособности системы безопасности АЭС независимо от влияния человеческого фактора, наличия или отсутствия дополнительных энергоресурсов и других обстоятельств, характерных, в частности, и для возможных террористических проявлений.
Впервые в мире было получено семейство оригинальных по составу и свойствам функциональных материалов на основе компонентов системы AlFeSiSrBaYGeLaGdEuSmO, представляющих собой принципиально новый класс материалов. Внедрение этого класса материалов позволит создать новое поколение систем безопасности в атомно-энергетическом секторе.
Атомная энергетика является сегодня высокотехнологичной отраслью и играет системообразующую и природоохранную роль в топливно-энергетическом комплексе (ТЭК) России. В проектируемых и вновь сооружаемых АЭС с реакторами ВВЭР – 1000 и ВВЭР – 1500 безопасность этих сложных технических систем, защита населения и окружающей среды от последствий за проектных аварий обеспечивается устройством локализации расплава активной зоны, которое входит в состав технических средств, специально предусмотренных на АЭС для управления тяжелыми авариями, образующих четвертый – последний уровень глубокоэшелонированной защиты. Использование специальных функциональных материалов, взаимодействующих с расплавом активной зоны, обеспечивает длительную (в течение 60 лет проектного срока эксплуатации АЭС) и эффективную работоспособность устройства локализации расплава. Это позволяет существенно уменьшить радиационные последствия тяжелых аварий. Механизм защитного действия нового класса материалов основан на окислении содержащихся в расплаве сильных восстановителей, прежде всего циркония и урана, которые в противном случае способны к образованию водорода при взаимодействии с парами воды. Кроме этого, при взаимодействии с расплавом активной зоны эти материалы должны понижать температуру расплава за счет общего эндотермического эффекта и создавать благоприятные условия для теплоотвода из устройства локализации, а также понижать плотность оксидной фазы расплава активной зоны до пространственной инверсии ее с металлической фазой расплава. Последнее свойство позволяет предотвратить эффект фокусировки тепловых потоков на водоохлаждаемой поверхности устройства локализации и создает благоприятные условия для последующей подачи воды на поверхность расплава. Понижение плотности расплава обеспечивается за счет растворения в оксидной фазе легких компонентов, входящих в состав функционального материала. Кроме того, эти материалы выполняют и ряд других функций, обеспечивающих эффективную работу систем безопасности, в частности создают условия для надежной подкритичности системы, уменьшают выход наиболее опасных радионуклеидов. Важным требованием, которому должны удовлетворять новые функциональные материалы, является прогнозируемость их поведения при широком варьировании параметров внешних химических, термических и механических воздействий.
Удовлетворить всем этим требованиям можно только на основе многокомпонентной системы со сбалансированным химическим и фазовым составом, строго определенной структурой.
В странах Азии лотос почитается священным растением прежде всего потому, что поверхность листьев этого растения отталкивает воду, грязь и пыль. В этом эффекте сочетаются две характеристики – повышенная гидрофобность и способность к самоочищению. Гидрофобность проявляется в том, что поверхность лотоса отталкивает воду, в результате чего даже микроскопические капельки воды на таких поверхностях превращаются в круглые «бисеренки», которые при малейшем наклоне скатываются с поверхности, оставляя ее сухой. Так называемый краевой угол (контактный угол, угол смачивания) на таких поверхностях превышает 1400, а в некоторых случаях даже достигает 1700, т.е. поверхность практически не смачивается. Вопреки распространенному мнению, самоочищающиеся поверхности типа лотоса являются не гладкими, а имеют сложную, шероховатую структуру, причем неровности (неоднородности) имеют микро и даже наноразмеры. Реальная поверхность листьев лотоса состоит из кристаллов воска (естественно являющихся гидрофобными, в виде «узелков» высотой 5-10мкм, расположенных на расстоянии 10-15мкм друг от друга.
Многообещающие перспективы в технической реализации и использования эффекта лотоса заключаются именно в том, чтобы путем комбинации наночастиц и гидрофобных полимеров (типа полипропилена или полиэтилена) получать сверхгидрофобные материалы и покрытия. Для практического применения очень удобно нанесение на поверхность аэрозолей, при высыхании которых происходит самоорганизация вещества, приводящая к образованию наноструктурированного покрытия или слоя. Аэрозоли этого типа уже получили название «лотос спрей» и их очень удобно использовать, разбрызгивая на любые шероховатые поверхности ( включая бумагу, кожу, текстильные изделия и каменную кладку). Эффект лотоса с нанопокрытием также применяется при изготовлении специальной аппаратуры, в которой важно обеспечить полное выливание жидкости из сосуда (например пипетки и т.д.).
Защита от коррозии является глобальной задачей. Так только в США экономический ежегодный ущерб от коррозии составляет около 300 миллиардов долларов.
Ржавчина представляет собой естественно образующуюся смесь различных окислов и гидроокислов железа, содержащую соли и ионы железа, которые автокаталитически увеличивают скорость коррозии. В этом смысле весьма перспективными представляются так называемые органические металлы (органические и металлорганические соединения с высокой электропроводностью). Нанопокрытия (особенно, если им удастся придать способность к самозалечиванию) могут оказаться исключительно важными и востребованными.
Очистка промышленных отходящих газов является важным направлением химического катализа. Как известно, в процессе работы технологического оборудования происходит накопление отработанных масел, утилизация которых в настоящее время осуществляется сжиганием. Отходящие при этом газы содержат сажу, оксиды углерода, азота, серы, механические примеси. Снижение уровня вредных веществ в отходящих газах путем варьирования режимов сжигания и установка фильтров не дает необходимого эффекта. Введение непосредственно в топочное устройство вместе с топливом микроскопических количеств каталитически активных на-нопорошков простых и сложных оксидов переходных и редкоземельных металлов представляет собой принципиально иной подход к решению данной проблемы. Благодаря малым размерам и высокой удельной поверхности нанопорошка, происходит эффективное дожигание сажи в отходящих газах технологических печей.
Например, катализаторы глубокого окисления, содержащие нанопорошки оксидов неблагородных металлов (состав CuCrCoNiCe — 60:30:5:2:3), показали степень очистки отходящих газов печей от угарного газа и метана в пределах 94-99%.
Созданные на основе наноматериалов каталитические нейтрализаторы выхлопных газов автомобильных двигателей позволили снизить содержание оксида углерода для дизельного двигателя в 7-40 раз, для бензинового — более чем в 10 раз.
Переработка промышленных отходов — еще одно направление использования наноструктурных катализаторов. Например, при добавлении в катализатор 1% порошка железа можно достигнуть высокой эффективности в процессах глубокой переработки вязких отходов нефтяной промышленности до получения бензинов и других углеводородов. Кроме того, железо образует оксид железа III, который является эффективным катализатором для обезвреживания таких соединений, как СО, NOx, S02.
Для решения широкого круга технологических и экологических задач целесообразно применение наноматериалов в качестве высокоэффективных адсорбентов в современных мембранных технологиях (мембраны, микрофильтры). В частности, нанооксиды показали высокую активность в процессах тонкой комплексной доочистки питьевой воды от тяжелых металлов и органических загрязнений. Эти наноматериалы позволяют извлекать из водных сред широкий спектр примесей неорганического и органического происхождения; очищать стоки гальванических производств, предприятий добычи, транспортировки и переработки нефти и нефтепродуктов. Производимые анофильтры позволяют выделять из воды одновалентные и многовалентные ионы, понижать степень ее жесткости, очищать от солей, микробов, пестицидов, гербицидов и углеводородов.
Нанопорошки адсорбентов, благодаря различию в скоростях адсорбции отдельных ионов, можно также использовать для извлечения и селективного выделения отдельных ценных компонентов из буровых вод и водных промышленных отходов.
Для очистки жидкостей от взвешенных примесей разработаны фильтры с использованием нанокристаллических мембран. Основным узлом данных устройств являются фильтро-элементы, представляющие собой полые цилиндры из пористого полиэтилена, на внешнюю поверхность которых нанесены пористые покрытия из нанодисперсных нитридов, оксидов, оксинитридов титана, алюминия, циркония. В результате полученные мембраны обладают высокими фильтрующими характеристиками, достаточно высокой производительностью по фильтрату, способностью к многократной гидродинамической регенерации без разборки и длительным сроком эксплуатации.
Создание высокоэффективной малогабаритной аппаратуры для очистки нефтесодержащих сточных вод стало возможным благодаря сочетанию нанопорошков адсорбентов с высокоемкими волокнистыми материалами (углеткани, базальтовые волокна и др.). Один прибор, содержащий три слоя наноадсорбента, разделенных слоями волокнистого материала, обеспечивает очистку эмульсий нефтепродуктов с исходной концентрацией 200-300 мг/л до уровня санитарных норм.
Использование нанопорошков металлов позволяет производить микропористые материалы с открытой пористостью 35-70%. Получены микропористые материалы состава Ni3Al, NiAl, Ti3Al, которые эффективны при изготовлении испарителей, сепараторов и фильтров в системах терморегулирования.
Действие керамических датчиков влажности также основано на адсорбционных свойствах наноматериалов. В них используются нанопорошки диоксида циркония, развитая поверхность которых оказывает основное воздействие на процесс поглощения влаги из потока воздуха. В результате, полученные структуры с широким набором пор позволяют значительно превысить технологические параметры применяемых в настоящее время датчиков влажности.
Одним из важнейших направлений применения наноматериалов является создание различных средств защиты, где они используются в качестве компонентов свето- и теплопо-глощающих составов, поглотителей электромагнитного излучения, радиационной защиты.
Многие возлагают надежды на нанотехнологии в решении проблемы энергетического кризиса. Нанотехнологии могут повысить эффективность солнечных батарей, помочь в улучшенном катализе нефти, создать новые источники хранения энергии и улучшить старые (аккумуляторы, батарейки, топливные элементы). Благодаря нанотехнологиям уже сделаны солнечные батареи, толщина которых не превышает толщины оберточной бумаги. Это поколение солнечных батарей отличается от аналогичных источников питания неизмеримо меньшим весом, большей гибкостью и долговечностью. Не забудем и протопливные ячейки. Эксперименты по переходу на экологически чистое водородное топливо в развитых странах проводятся уже сейчас.
Перспективно использование наноматериалов в различных источниках энергии при создании средств прямого преобразования энергии; полупроводниковых, эмиссионных, коммутационных материалов; материалов для водородной энергетики.
В частности, использование нанопорошков Zr02, стабилизированных иттрием, снижает температуру синтеза керамики на 100-200 °С, что значительно уменьшает энергозатраты при производстве топливных элементов и повышает ресурс работы термического оборудования. Это, в свою очередь, позволяет применить принципиально новые технологии изготовления топливных элементов. Кроме того, появляется возможность снижения в 1,5-2 раза количества топливных элементов в энергоустановке или рабочей температуры до 800 °С.
В будущем развитие энергетики будет связано с массовой заменой твердых видов топлива и горючих веществ на водород. Ключевой проблемой является накопление и хранение газообразного водорода. При этом не может быть и речи о сжижении водорода под давлением или его охлаждении до свехнизких температур. Высокоперспективными материалами для этих целей представляются нанопористые вещества со специфически большой активной поверхностью. Это могут быть углеродные нанотрубки, металлорганические сотовые структуры. Из этих структур создаются крупные по размеру и легкие пористые вещества с открытыми порами и каналами нанометрового размера. который необходимо будет аккумулировать в специально создаваемых устройствах, и именно в этом наноматериалы ( в частности сложные фуллерены) могут оказаться исключительно полезными. Уже в настоящее время создаются емкости-хранилища водорода на основе фуллеренов с 10% эффективностью.
Солнце в среднем ежедневно производит количество энергии, превышающее годовой расход энергии в такой стране как Германия в 80 раз. В принципе, техническая утилизация солнечной энергии осуществляется двумя основными методами: так называемый фотогальванический метод ( то есть прямое преобразование солнечной энергии в электрическую) и соляротермический метод ( так иногда называют использование солнечного излучения для получения горячей воды, для отопления отдельных помещений и т.п.). Нанотехнологии могут сыграть важную роль в разработке многих устройств такого типа, прежде всего за счет нанесения на поверхность стекол солнечных батарей или коллекторов нанослоев некоторых веществ, позволяющих повысить степень поглощения падающего на поверхность солнечного излучения.
Нанопленки
К нанопленкам (нанопокрытиям) относятся двумерные образцы наноматериалов, которые характеризуются наноразмерной толщиной. В свою очередь, к нанопроволокам (наностержням, нановолокнам, нанонитям) относятся одномерные образцы наноматериалов, которые характеризуются наноразмерным диаметром. И нанопленки, и нанопроволоки могут быть подобны по строению объемным образцам наноструктурных материалов, в частности, им может быть присуща нанокристаллическая или нанокомпозиционная структура. Вместе с тем и нанопленки в силу их наноразмерной толщины, и нанопроволоки в силу их наноразмерного диаметра могут значительно отличаться от объемных образцов по свойствам. Существуют разнообразные технологии получения нанопленок, которые аналогичны традиционным тонкопленочным технологиям. Среди них наиболее широкое распространение получили технологии осаждения вещества на подложку из парогазовой фазы или плазмы, а также из растворов. Кроме того, используются технологии обработки поверхности, основанные на таких процессах, как азотирование и гидрирование, обработка атомами бора или титана и т.п. В технологиях осаждения вещества на подложку из парогазовой фазы или плазмы толщина и структура пленки могут регулироваться за счет изменения параметров потока осаждаемых атомов. Разновидностью этих технологий является ионно-стимулированное осаждение, когда используется, помимо пучка атомов или молекул для создания материала пленки, пучок высокоэнергетических ионов или лазерное излучение для активации поверхности. При этом возникает дополнительная возможность варьировать толщину и структуру пленки за счет изменения состояния поверхности подложки. Среди технологий осаждения вещества на подложку из растворов особенно эффективно электролитическое (электрохимическое) осаждение, обеспечивающее расширенный спектр возможностей по регулированию параметров процесса осаждения. На практике важная роль отводится технологиям осаждения, позволяющим получать эпитаксиальные нанопленки. Такие пленки формируются в процессе эпитаксии, т.е. в процесс роста, при котором кристаллическая ре- шетка создаваемой пленки закономерно ориентирована относительно кристалла-подложки. Различают гомоэпитаксию, когда материалы пленок и подложки идентичны, и гетероэпитаксию, когда сочетаются разнородные вещества.
В настоящее время тонкие пленки, состоящие из аморфного гидрогенизированного кремния (a-Si : H) или из наночастиц кремния (nc-Si), рассматриваются как весьма перспективные элементы солнечных батарей на монокристаллическом кремнии (c-Si), способные повысить эффективность их преобразования.
Увеличение эффективности преобразования определяется уменьшением скорости рекомбинации неосновных носителей на лицевой поверхности солнечной батареи вследствие пассивации поверхностных дефектов, таких, например, как оборванные связи атомов кремния .
Кроме того, ширина запрещенной зоны пленок a-Si : H и nc-Si составляет 1.4−2.5 эВ, что существенно больше ширины запрещенной зоны кристаллического кремния. Поэтому такие пленки могут использоваться как антиотражающие покрытия, способные без заметного поглощения пропускать фотоны из длинноволновой области солнечного спектра, эффективно поглощая более высокоэнергетичные (солнечные элементы с лицевой гетероповерхностью).
В этой связи отметим весьма перспективную схему солнечного элемента, на лицевой поверхности которого сформировано многослойное покрытие из легированных пленок nc-Si, с наночастицами, подобранными таким образом, что ширина запрещенной зоны максимальна у внешней пленки и уменьшается от слоя к слою в направлении лицевой поверхности пластины c-Si, в которой организован p−n-переход.
Кроме отмеченных возможностей пленок nc-Si, укажем на еще один перспективный способ повышения эффективности солнечной батареи. Этот способ связан с трансформацией коротковолновой составляющей солнечного спектра в длинноволновую при взаимодействии света с пленкой nc-Si наночастицы которой могут люминесцировать в красной области спектра (light down conversion).
В представленной работе изучалась возможность увеличения эффективности преобразования солнечного элемента (СЭ) за счет пассивации поверхностных дефектов на его лицевой поверхности при нанесении на нее пленки из наночастиц кремния, за счет просветляющего действия пленки и за счет даун-конверсии освещающего излучения в этой пленке.
Фотовольтаические параметры СЭ определялись из вольт-амперных характеристик, интегральных по спектру излучения, освещающего его лицевую поверхность, и из анализа спектрального отклика, полученного при освещении СЭ световыми монохроматическими источниками с дискретным набором длин волн.
Нанесение тонких пленок nc-Si на лицевую поверхность коммерческой солнечной батареи без антибликового покрытия и без текстурирования этой поверхности приводит к увеличению эффективности до 12% относительно первоначальной величины в зависимости от толщины нанесенной пленки.
Обнаружено, что нанесение пленок nc-Si повышает внутреннюю квантовую эффективность (IQE) солнечной батареи, причем наибольшее увеличение IQE достигается в длинноволновой области спектра.
Из анализа темновых вольт-амперных характеристик p−n-перехода солнечного элемента с чистой лицевой поверхностью и с поверхностью, покрытой пленками nc-Si и PLnc-Si, сделан вывод о том, что одной из причин увеличения эффективности солнечной батареи является пассивация поверхностных состояний, которая проявляется в существенном уменьшении обратных токов через p−n-переход.
Из анализа спектров отражения от лицевой поверхности солнечной батареи установлено, что второй главной причиной увеличения эффективности является существенное уменьшение отражения света от нее при нанесении пленок nc-Si и PLnc-Si.
Дата добавления: 2018-11-24; просмотров: 2030; Мы поможем в написании вашей работы! |
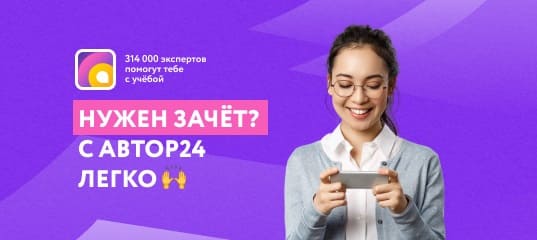
Мы поможем в написании ваших работ!