Анализ технического контроля.
Виды тех. контроля:
- стационарный: осуществляется на постоянном специальном рабочем месте для проверки объектов;
- летучий, или скользящий: осуществляется непосредственно на рабочем месте обработки или сборки путем периодических проверок;
- предварительный: применяется с целью предупреждения брака. Предварительному контролю подвергаются материалы, заготовки, полуфабрикаты, детали до начала обработки или сборки;
- промежуточный – операционный: осуществляется на различных стадиях изготовления заготовок, деталей и сборки изделий. Основная цель – проверка качества выполнения каждой производственной операции по технологическому процессу и исключение брака на последующих операциях;
- окончательный – заключительный: контролю подвергаются все детали, узлы и изделия после заключительных операций технологического процесса обработки или сборки. Наиболее ответственная форма предупреждения выпуска недоброкачественной продукции;
- сплошной: проверке подвергаются все без исключения представленные заготовки, детали, узлы и изделия;
- выборочный: проверке подвергается некоторая часть из партии деталей или изделий в зависимости от условий производства;
- статистический: наиболее активный способ предотвращения потерь от брака. Применяется для анализа и регулирования качества продукции, хода технологического процесса и состояния производственного оборудования. В основу положен выборочный метод, основанный на теории вероятностей и математической статистике;
|
|
- инспекционный: осуществляется для повторного выборочного контроля объектов, ранее сданных производством и принятых ОТК, а также для выборочных наблюдений за работой изделий в эксплуатации в течение установленого гарантийного срока;
- пооперационный: производится после каждой операции, когда качество последующей операции зависит от предыдущей;
- групповой: осуществляется после группы неответственных операций или когда характер технологического процесса исключает возможность проверки объектов после каждой операции;
- непрерывный: применяется непосредственно в процессе обработки деталей. Осуществляется автоматизированный контроль размеров и поднастройка оборудования в процессе обработки;
- полуавтоматический: контроль размеров обработки постоянно отслеживается с применением ЦОУ (цифровое отсчетное устройство). Подналадка оборудования осуществляется вручную;
- автоматизированный приемосдаточный: применяется для окончательного контроля изделий с использованием автоматизированных измерительных комплексов;
- визуальный: осуществляется только внешним осмотром;
|
|
- геометрический: производится проверка размеров и геометрических элементов объекта;
- метрологический: осуществляется проверка элементов, от которых зависит качество, структура, твердость и т.п.;
- предупредительный: осуществляется на всех этапах производства с целью предупреждения брака;
- производственный: применяется для выявления брака при проверке объектов, предъявленных на контроль после завершения определенного производственного этапа или операции. Различают производственный контроль, выполняемый рабочими, наладчиками и мастерами или работниками ОТК.
Для обеспечения требуемого качества продукции необходимо вести контроль не только качества материала и покупных комплектующих изделий, но и соблюдения режимов технологических процессов, контролировать геометрические параметры, качество обработки деталей и сборочных единиц.
Технический контроль - один из важнейших элементов системы управления качеством продукции. Его главная цель - предотвратить выпуск продукции, не соответствующей требованиям нормативно-технической документации.
Эффективность и качество проведения контроля во многом зависят от организации контрольных работ.
|
|
Обеспеченность подразделения рабочими.
В первую очередь при изучении показателей трудовых ресурсов обращается внимание на то, как организация обеспечена необходимым персоналом. С этой целью рассматриваются: состав и структура промышленно-производственного персонала; обеспеченность организации и ее подразделений рабочими, административно - управленческим персоналом;
обеспеченность квалификационным составом работающих; движение рабочей силы.
Анализ обеспеченности трудовыми ресурсами начинается с изучения структуры и состава персонала. Структура трудовых ресурсов анализируется по каждому подразделению предприятия и может рассматриваться по таким признакам, как возраст, пол, уровень образования, результаты работы, квалификация, степень выполнения норм и т.д. Поэтому наиболее ответственный этап в анализе обеспеченности предприятия рабочей силой - изучение ее движения. Движение трудовых ресурсов - это распределение, перераспределение, высвобождение, подготовка и переподготовка трудовых ресурсов. Это постоянное изменение количественных и качественных признаков, характеризующих ту часть населения, которая выступает носителем рабочей силы. Особое внимание при анализе движения рабочей силы уделяют причинам увольнения работников с предприятия. К основным причинам относят: призыв в армию, сокращение штата, выход на пенсию, перевод на другие предприятия, окончание сроков договора найма, смерть работника, по собственному желанию, поступление в учебное заведение с отрывом от производства, прогулы и другие нарушения трудовой дисциплины. При анализе движения рабочей силы определяют коэффициенты общего оборота (Копв), оборота по приему (Кпр), по выбытию (Кв), текучести кадров (Кт), постоянства кадров (Кпост).
|
|
Текучесть рабочих играет большую роль в деятельности предприятия. Постоянные кадры, длительное время работающие на предприятии, совершенствуют свою квалификацию, осваивают смежные профессии, быстро ориентируются в любой нетипичной обстановке, создают определенную деловую атмосферу в коллективе, активно влияя на производительность труда. Текучесть кадров мешает правильной организации труда, повышению квалификации рабочих, снижает трудовую дисциплину.
Высокая текучесть кадров является отрицательным показателем работы предприятия и часто является следствием плохой работы хозяйственных руководителей, общественных партийных организаций по улучшению условий труда и быта трудящихся. Причинами ухода чаще всего являются: слабая работа по улучшению условий труда, недостатки в организации оплаты труда рабочих, нормировании труда, отсутствие жилья и др.
2.11. Перспектива развития технологической базы, как ее представляют в предприятии, подразделении.
Техническое развитие производства отображает процесс формирования и совершенствования технико-технологической базы предприятий, что должно быть постоянно сориентированным на конечные результаты его производственно-хозяйственной, коммерческой или другой деятельности .
Поддержки технико-технологической базы осуществляются путем: капитального ремонта оборудования; замены сработанного оборудования новым такого же технического уровня; технического довооружает предприятия.
Развитие технико-технологической базы включает: модернизацию; реконструкцию; техническое перевооружение; расширение; новое строительство.
Технический уровень оборудования (производительность (мощность); надежность и долговечность; удельное металосодержание; средний срок эксплуатации; часть прогрессивных видов оборудования в общем количестве; частица технически и экономически устаревшего оборудования в общем парке).
Уровень механизации и автоматизации производства (степень охватывания работ механизированным трудом; часть объема продукции, что производится с помощью автоматизированных средств труда). Для углубления аналитической оценки уровня технического развития предприятия применяются также другие показатели, а именно: механическая вооруженность труда (отношение среднегодовой стоимости машин и оборудования к количеству рабочих в самом загруженном изменении); коэффициент физического срабатывания оборудования; коэффициент технологической оснащенности производства (количество применяемых устройств, оснастки и инструментов в расчете на одну оригинальную деталь конечного изделия); уровень утилизации отходов производства; повышение качества изготовления продукции, обеспечение ее конкурентоспособности на мировом и отечественном рынках; разработка и широкое внедрение ресурсосберегающих (в первую очередь энергосберегающих) технологий; сокращение к максимально возможному уровню расходов ручного труда, улучшения, ее условий и безопасности; осуществление всесторонней экологизациипроизводства согласно с современными требованиями к охране окружающей среды. В процессе экономического управления техническим развитием предприятия одним из главных заданий является разработка и осуществление программ (планов) технического развития.
Выводы и предложения.
Под организационной структурой фирмы понимается ее организация из отдельных подразделений с их взаимосвязями, которые определяются поставленными перед фирмой и ее подразделениями целями и распределением между ними функций. Организационная структура предусматривает распределение функций и полномочий на принятие решений между руководящими работниками фирмы, ответственными за деятельность структурных подразделений.
Все управление идет сверху вниз и все службы не имеют права принимать самостоятельное решение. Такие схемы соподчиненности являются наиболее простыми и понятными для работников. Каждое звено четко представляет себе круг своих полномочий и ответственности; упрощается процесс поддержания дисциплины; каналы делового обращения очень просты и непосредственны. Но данная структура имеет и свои недостатки: централизация не способствует повышению квалификации работников более низкой ступени; работники высших ступеней не всегда обладают специальными знаниями; расширение компании приводит к созданию высоких структур, что затрудняет управляемость и мобильность в принятии решений. Отсутствие логистики. С позиции менеджмента организации логистику можно рассматривать как стратегическое управление материальными потоками в процессе снабжения: закупки, перевозки, продажи и хранения материалов, деталей и готового инвентаря (техники и прочего). Понятие включает в себя также управление соответствующими потоками информации, а также финансовыми потоками. Логистика направлена на оптимизацию издержек и рационализацию процесса производства, сбыта и сопутствующего сервиса как в рамках одного предприятия, так и для группы предприятий. Отсутствие действующих средств механизации автоматизации при транспортировке деталей, их складировании и контроле, ведет к удлинению производственного цикла изготовления деталей. Скопление большого количества универсальных станков на небольших площадях и их установка на жестких монолитных фундаментах, приводит к значительному шуму в процессе работы, а это, в свою очередь, вызывает утомляемость рабочих, снижает эффективность использования человеческого труда. Также снижается фондовая отдача оборудования, которую нельзя повысить только за счет экстенсивных факторов труда. Таким образом, анализ действующего металлообрабатывающего оборудования в механообрабатывающем производстве показывает, что прогрессивное оборудование составляет 30-35% от общего количества станочного парка.
Гибкие производственные системы не исключают и неавтоматизированные методы обработки с сохранением универсального оборудования, за счет его переоснащения прогрессивными блоками и узлами (быстросменные и быстродействующие многопозиционные головки для сверления, нарезания резьбы и т. д.) с последующей его компоновкой в ГПС по модульному принципу.
В процессе работы на универсальном оборудовании рабочий лишен возможности активного участия и слежения за работой механизмов станков, режущего инструмента, полагаясь в основном на свой производственный опыт и интуицию. При группировании оборудования необходимо учитывать срок эксплуатации, который связан с величиной физического износа, степенью морального износа, прогрессивностью, точностью и рядом других технико-эксплуатационных характеристик. Необходим переход на многосменную работу (по скользящему графику) для повышения темпов роста производительности труда с наиболее эффективным использованием высокопроизводительного и дорогостоящего оборудования, с учетом его быстрой окупаемости, с тем чтобы моральный износ не опережал физический. Необходимо при этом учитывать и стоимость оборудования, которое является определяющим фактором при решение вопроса, связанного с фондоотдачей. Необходимо проводить оптимизацию структуры действующего станочного парка по группам с учетом вышеуказанных характеристик, избавляться от станков устаревшей конструкции с низкой производительностью, малой точностью, узким диапазоном технологического применения, учитывать интегральный коэффициент использования оборудования с учетом интенсивной и экстенсивной нагрузки оборудования в общем итоге комплексного анализа состояния станочного парка. Кроме того, с переходом к автоматизированному производству, присутствие рабочего у станка только противоречит основным принципам автоматизации, но и не может дать ощутимых результатов в виду ограниченности физических возможностей человека по наблюдению и регулированию процессов обработки деталей.
Дата добавления: 2018-11-24; просмотров: 712; Мы поможем в написании вашей работы! |
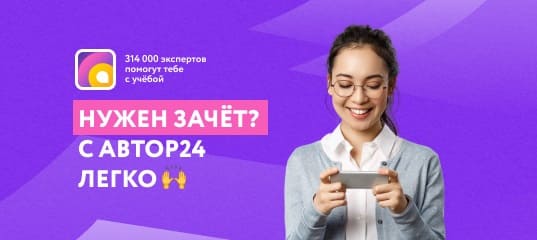
Мы поможем в написании ваших работ!