Наличие на предприятии порошковой металлургии и технологий изготовления деталей и узлов из неметаллических материалов и полимеров.
Получение порошков.В задачи порошковой металлургии, входит производство порошков и получение из них заготовок или готовых деталей. При изготовлении спеченных изделий применяют порошки размером от 0,5 до 500 мкм. Получают порошки механическими и физико-химическими способами.
К механическим способам получения порошков относятся: распыление жидкого металла, размол стружки и других отходов металлообработки в вихревых или шаровых мельницах. При использовании механических способов исходный материал измельчается без изменения химического состава. К физико-химическим способам получения порошков относятся: восстановление металлов из оксидов, осаждение металлических порошков из водного раствора, соли и др. Получение порошка при этом связано с изменением химического состава исходного сырья или его состояния.
Физико-химические способы более универсальны и более экономичны: используют отходы производства в виде окалины, оксидов и т.д. Порошки ряда тугоплавких металлов (W, Mo), а также порошки их сплавов могут быть получены только физико-химическими способами.
Металлические порошки характеризуются химическим составом, а также физическими и технологическими свойствами (текучестью, прессуемостью и спекаемостью).
Приготовление смеси и формообразование заготовок. Для получения качественных заготовок или деталей, порошки предварительно обжигают, разделяют по размерам частиц, потом смешивают. Обжиг порошка способствует восстановлению оксидов, удалению углерода и других примесей, устранению наклепа, что улучшает его прессуемость. Обжиг проводят при температуре, равной 0,5 - 0,6 температуры плавления в защитной или восстановительной атмосфере.
|
|
Порошки с размером частиц 50 мкм. и более разделяют по группам просеиванием на ситах, более мелкие - воздушной сепарацией.
В ряде случаев в порошковую массу вводят технологические наполнители: пластификаторы, улучшающие прессуемость и обрабатываемость (раствор каучука в бензине, парафине, воске), летучие вещества и др.
Подготовленные порошки смешивают в шаровых, вибрационных мельницах и другими способами.
Заготовки из металлических порошков формообразуют прессованием (холодное, горячее, гидростатическое), экструдированием, прокаткой.
Холодное прессование делится на одностороннее и двустороннее. В первом случае порошковая шихта прессуется пуансоном в пресс-форме с поддоном. Объем порошка при этом резко уменьшается, увеличивается контакт между частицами, происходит их механическое сцепление. Прочность заготовки повышается, а пористость уменьшается. Таким способом получают заготовки простой формы и небольшой высоты, т.к. вследствие неравномерности распределения давления по высоте заготовки она имеет различную прочность, плотность и пористость по высоте.
|
|
Для формообразования заготовок сложной формы применяют двустороннее прессование с помощью двух подвижных пуансонов. При такой схеме требуемое давление для получения равномерной плотности снижается на 30 - 40.
Горячее прессование совмещает формование и спекание заготовок. Процесс осуществляется в графитовых пресс-формах с индукционным или электроконтактным нагревом. Благодаря высокой температуре давление можно существенно уменьшить. Горячее прессование отличается малой производительностью и большим расходом пресс-форм, поэтому используется, главным образом, при переработке жаропрочных материалов, твердых сплавов и тугоплавких металлов.
Гидростатическое прессование заключается в обжатии порошка, помещенного в эластичную (например, резиновую) оболочку с помощью жидкости под давлением до 2 ГПа. Этим методом получают крупногабаритные заготовки типа труб, цилиндров.
Экструдирование - процесс формования заготовок путем выдавливания шихты из замкнутого объема (схема, аналогичная прямому прессованию металлов). Для этого исходный порошок замешивают с пластификатором до консистенции пластилина. Этим способом получают прутки, трубы и другие изделия.
|
|
Прокатка - один из наиболее производительных и перспективных способов переработки порошковых материалов. Осуществляется она путем обжатия порошковой шихты между валками. Этим способом получают пористые компактные ленты, полосы и листы толщиной 0,02…3 мм и шириной до 300 мм из железа, никеля, титана, нержавеющей стали и др. При этом процесс прокатки легко совмещается со спеканием и другими видами переработки. Для этого полученную заготовку пропускают через печь, а затем прокатывают с целью калибровки.
Спекание и окончательная обработка заготовок. Для повышения прочности сформованные из порошков заготовки подвергают спеканию. Спекание производится в печах электросопротивления или индукционных в нейтральной или защитной среде при температуре 0,6 - 0,9◦С температуры плавления порошка. Процесс спекания длится 30 - 90 мин., при этом происходят восстановление поверхностных оксидов, диффузионные явления и образуются новые контактные поверхности.
Для повышения физико-механических свойств спеченных заготовок и повышения точности размеров их могут подвергать последующему калиброванию - повторному прессованию или экструдированию и спеканию, пропитке смазочными материалами, термической или химико-термической обработке. Спеченные материалы можно подвергать ковке, прокатке, штамповке при повышенных температурах, а также обработке резанием - точению, сверлению, фрезерованию. Последнюю выполняют без использования смазочно-охлаждающей жидкости во избежание проникновения ее в поры и возникновения процесса внутренней коррозии металлов.
|
|
Технологические основы конструирования спеченных деталей сводятся к следующим требованиям:
- не допускать значительной разностенности во избежание коробления детали из-за усадки;
- избегать выступов, пазов и отверстий с перпендикулярным расположением к оси прессования;
- избегать острых углов в местах сопряжений, предусматривать радиусы закругления не менее 0,25 мм;
- наружные и внутренние резьбы получать обработкой резанием;
- толщину стенок детали задавать не менее 1 мм.
Дата добавления: 2018-11-24; просмотров: 549; Мы поможем в написании вашей работы! |
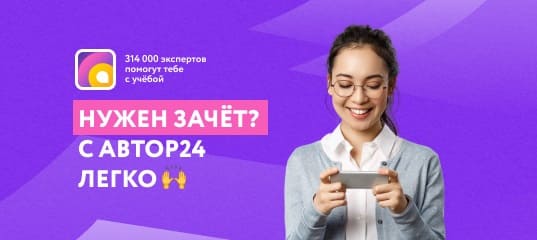
Мы поможем в написании ваших работ!