Обозначение предельных отклонений и посадок на чертежах
Предельные отклонения линейных размеров могут быть указаны одним из трех способов:
- условными обозначениями полей допусков (рис. 2.5, а);
- числовыми значениями предельных отклонений (рис. 2.5, б);
- условными обозначениями полей допусков с указанием в скобках числовых значений предельных отклонений (рис. 2.5, в).
При указании предельных отклонений условными обозначениями необходимо обязательно указывать их числовые значения в следующих случаях:
а) для размеров, не включенных в ряды нормальных линейных размеров, например, Æ41,5 Н8 (+ 0,030) (рис. 2.6, б);
б) при назначении предельных отклонений, условное обозначение которых не предусмотрено ГОСТ 25346-89, например, для пластмассовой детали (рис. 2.6, а);
в) при назначении предельных отклонений размеров уступов с несимметричным полем допуска (рис. 2.6, б).
Рисунок 2.5 – Способы указания предельных отклонений линейных размеров на чертежах
а) б)
Рисунок 2.6 – Примеры простановки предельных
отклонений размеров на чертежах
![]() |
Рисунок 2.7 – Пример простановки предельных отклонений на шейке вала, имеющего неодинаковую точность по длине
Предельные отклонения следует назначать для всех размеров, проставляемых на чертежах, не исключая и несопрягаемые неответственные размеры. Если предельные отклонения для размеров не назначены, то это может привести к лишним затратам (когда стремятся получить этот размер более точным, чем нужно) или к увеличению массы детали - перерасходу металла (когда допускают грубые отклонения от номинального размера).
|
|
Точность гладких элементов металлических деталей, если для них отклонения не указывают непосредственно у размеров, а оговаривают общей записью, нормируют либо квалитетами (от 12 до 17 для размеров от 1 до 10000мм), обозначаемыми буквами IT,либо классами точности (точный, средний, грубый и очень грубый), установленными специально для этой цели и обозначаемыми буквой t. Возможные варианты простановки на чертеже размеров, отклонений и шероховатости поверхностей деталей машин приведены в приложениях Д1, Д2.
Расчет и выбор посадок с гарантированным натягом
Посадки с гарантированным натягом предназначены для получения неподвижных неразъемных соединений без дополнительного крепления деталей, хотя иногда и в этом случае используют шпоночные, штифтовые и другие средства крепления. Относительная неподвижность деталей обеспечивается за счет сил сцепления (трения), возникающих на контактирующих поверхностях вследствие их деформации, создаваемой натягом в процессе сборки. Благодаря надежности и простоте конструкции деталей и сборки соединений, эти посадки применяют во всех отраслях машиностроения (например, при сборке осей с колесами на железнодорожном транспорте, вендов со ступицами червячных колес, вкладышей подшипников скольжения с корпусами и т.п.).
|
|
Предельные значения натягов выбранной прессовой посадки должны удовлетворять следующим условиям:
1. При наименьшем натяге должна обеспечиваться прочность соединения, т.е. не должно быть относительного поворота деталей от действия внешнего момента, или осевого усилия, или их совместного действия. Это условие выполняется, если
(2.7)
где MКР - наибольший прикладываемый к одной детали момент кручения;
MТР- момент трения, зависящий от натяга, размеров соединяемых деталей, шероховатости поверхностей и других факторов.
2. При наибольшем натяге должна обеспечиваться прочность соединяемых деталей, т.е. наибольшее напряжение, возникающее в материале детали, не должно превышать допустимого значения.
Величину наименьшего натягаNmin при условии, что сопрягаемые поверхности идеально гладкие, рассчитывают по формуле
|
|
(2.8)
где pэ - удельное эксплуатационное давление по поверхности контакта, Па;
d - номинальный диаметр соединения, м;
Е1 ,Е2 - модули упругости материалов соединяемых деталей (прил.А, табл. А1).
(2.9)
гдеd1, d2 - диаметры колец, мм (рис. 2.9, а);
m1 и m2 - коэффициенты Пуассона для металлов вала и отверстия (прил.А, табл. А. 1).
Величина удельного контактного эксплуатационного давления определяется:
при осевом сдвигающем усилии
(2.10)
при крутящем моменте
(2.11)
при их совместном действие(2.12)
где Р - осевое усилие, Н;
MКР - крутящий момент, Нм;
d, l - номинальные диаметр и длина соединения,м;
n = 1,5-2 - коэффициент запаса прочности соединения на возможные перегрузки и воздействие вибраций;
f - коэффициент трения ( прил. А, табл. А2).
Рисунок 2.8 – Эскизы к расчету посадок с натягом
Наибольший натяг в соединении, обеспечивающий его прочность, определяется на основе теории наибольших касательных напряжений. Условие прочности деталей заключается в отсутствии пластической деформации на контактной поверхности вала и втулки при наибольшем допустимом удельном контактном давлении pдоп. При определении Nmax принимаютpдоп, меньшее из двух значений.
|
|
Для втулки
(2.13)
для вала
(2.14)
гдеsT - предел текучести материалов деталей ( прил.А, табл.А.3).
Таким образом, наибольший расчетный натяг, при котором возникает наибольшее допустимое давлениеPдоп, находят по формуле, аналогичной выражению (2.8)
(2.15)
Прежде чем приступить к выбору посадки по стандарту, в вычисленные значения минимального и максимального натяга следует внести ряд поправок, исходя из условий работы соединения и его конструктивных особенностей (u - поправка на смятие неровностей деталей;ut - поправка на различные температурные условия сборки и работы, а также различные коэффициенты линейного расширения деталей;uц - поправка на деформацию деталей от действия центробежных сил; uуд - поправка на увеличение контактного давления у торцов охватывающей детали и др.).
В общем машиностроении наибольшее влияние на величину предельных натягов оказывают поправки uи uуд .
Поправка u. При определении размеров соединяемых вала и отверстия измерительные наконечники прибора опираются на вершины неровностейих поверхностей. В процессе запрессовки деталей неровности сминаются и фактическое значение натяга оказывается меньше, чем измеренное (рис. 2.8, б), что уменьшает прочность соединения. Величина смятия неровностей зависит от их величины, метода запрессовки, механических свойств материалов деталей и т.п. Практически величину поправки U определяют по следующим формулам:
для материалов с одинаковыми механическими свойствами
u = 2K(Rz1 + Rz2); (2.16)
для материалов с различными механическими свойствами
(2.17)
где К, K1 и K2 ; коэффициенты, учитывающие величину смятия неровностей отверстия втулки и вала (прил.А, табл. А.4);
RZ1, RZ2 - высота неровностей поверхностей отверстия и вала ( прил.А, табл. А5).При малых значениях RZ следует брать меньшие значения коэффициентов.
При механической запрессовке наибольшая прочность соединения создается при малой шероховатости, а при сборке с охлаждением (или нагревом) детали - при большой шероховатости.
Поправкаuуд. При l/d < 1 у торцов охватывающей детали контактные давления больше, чем в середине соединения, причем тем значительнее, чем меньшеl/d и радиус скругления кромок охватывающей детали. Эту поправку приближенно можно найти по графику, показанному на рисунке 2.9. Она должна снижать величину Рдоп, вычисленную по формулам (2.13 и 2.14). При определении Nmin эту поправку не вносят для повышения надежности соединения.
Предельно допустимые натяги [Nmin]и [Nmax] вычисляются по формулам
(2.18)
. (2.19)
Выбор посадки из таблиц системы допусков и посадок осуществляется по величине[Nmin] и [Nmax]. При этом должны соблюдаться следующие условия:
1) максимальный натяг Nmax в подобранной посадке должен быть не более [Nmax]
* (2.20)
2) минимальный натяг Nmin в подобранной посадке с учетом возможных колебаний действующей нагрузки и других факторов должен быть
(2.21)
Рисунок 2.9 – График для определения поправки uуд
3) рассчитывается необходимое (максимальное) усилие при запрессовке собираемых деталей
(2.22)
где fn - коэффициент трения при запрессовке; fn = (1,15-1,2).
Удельное давление pmax при максимальном натяге в посадке определяется по формуле
(2.23)
В некоторых случаях выбранную посадку с натягом проверяют по величине деформации сопрягаемых деталей. Изменение размеров d1и d2 после запрессовки определяется по формулам:
(2.24)
(2.25)
Пример. Для соединения венца со ступицей червячного колеса кранового редуктора рассчитать и выбрать посадку при следующих условиях: d= 300мм;d1 = 80 мм; d2 = 380 мм;
Мкр = 500 Нм; Р =2,0 кН; материал ступицы (вала) - сталь 20, венца - бронза Бр. АЖН-II-6-6; запрессовка механическая.
Решение. 1.По формуле (2.12) определить минимальное удельное давление[pэmin]
где n = 2; f = 0,05 (прил. А, табл. А.2); l = 0,06 м.
2. По формуле (2.8) определить наименьший расчетный натяг Nmin, предварительно определив коэффициенты Ляме С1 и C2:
где m1 = 0,3; m2= 0,33 (прил.А, табл. А.1).
где E1 = 2,0*1011 Па; E2 = 1,0*1011 Па (прил. А, табл. А.1).
3. Определить минимальный натяг [Nmin], обеспечивающий передачу заданного крутящего момента и осевой силы
Учитывая, что сборка и эксплуатация червячного колеса осуществляется с небольшой разницей температур, а скорость вращения колеса невысокая, примем поправкиut иuц ,равными 0.
Поправку u определим из выражения (2.17)
где K1 = 0,15; K2 = 0,7 (прил.А, табл. А4); RZ1 = 10 мкм Rz2 = 20мкм; (прил.А, табл.А5)при точности изготовления вала по 7-му квалитету, а отверстия - по 8-му).
Nmin = 41 + 31 = 72 мкм.
4. По выражениям (2.13 и 2.14) определить [pдоп]:
гдеsT1 = 2,6-108 Па;sT2 = 3,9-108 Па (прил.А, табл. А.3).
5. ОпределитьN1maxпо формуле (2.15), приняв для расчета меньшее значение [pдоп]:
6. Определить максимально допустимый натяг [Nmax] с учетом поправок u и uуд. Поправку uуд определяют по графику (рис. 2.9). При l/d = 60/300 = 0,2 и d1/d = 80/300 =0,26 находим
Uуд = 0,55.
[Nmax]= Nтах uуд + u = 1290 – 0,55 + 31 = 709 + 31 = 740 мкм.
7. По стандарту ГОСТ 25347-82 (прил. Е, Ж, Ж1) выберем посадку 300Н8/s7; Æ300Н8 (+0,081); Æ300 s7 ;
Nmax= 222 мкм; Nmin= 89 мкм;
Nmax < [Nmax ]; Nmin >[Nmin].
8. Определить усилие запрессовки по формуле (2.22):
,
где fn =1,2 f = 1,2*0,05 =0,06;
;
Pn = 0,06×22,7×106 - 3,14×0,3×0,06 =43000 Н = 43 кН.
9. Определить величину деформации венца Dd2 до формуле (2.25)
На практике, особенно в единичном и серийном производстве, часто не прибегают к расчету посадок с натягом, а пользуются опытом применения посадок в аналогичных конструкциях машин. Можно рекомендовать следующую область применения посадок с натягом в конструкциях общего машиностроения:
1. H7/р6 (предпочтительная) применяется при сравнительно небольших нагрузках для соединения тонкостенных деталей (например, посадка на вал уплотнительного кольца, фиксирующего положение внутреннего кольца подшипника у кранового двигателя).
2. H7/s6, H7/р6 (предпочтительные) и H8/s7 используют в соединениях без крепежных деталей при небольших нагрузках (например, для соединения кондукторных втулок с корпусом кондуктора, шатунных втулок с шатуном дизеля или пневматического двигателя), а при использовании крепления применяются для работы в условиях больших нагрузок (например, посадка на шпонке зубчатых колес и муфт в прокатных станах, бумагоделательных машинах и нефтеоборудовании).
3. ПосадкиH7/u7, H8/u8 применяют в соединениях без крепежных деталей при значительных нагрузках, в том числе и знакопеременных (например, для соединения ступицы и венца червячного колеса; втулок подшипников скольжения в изделиях тяжелого машиностроения), а при использовании крепления применяют для работы в узлах с большими нагрузками.
4. ПосадкиH8/х8, H8/z8 имеют самые большие натяги и применяются в соединениях с большими нагрузками или для деталей из материалов с относительно небольшим модулем упругости.
Выбор способа формирования соединения (под прессом или с нагревом охватывающей детали) зависит от конструкции деталей,ихразмеров, величины требуемого натяга и др.
Выбор посадок с зазором
Посадки с зазором предназначены для подвижных и неподвижных соединений деталей. В подвижных соединениях зазор служит для обеспечения свободы перемещения деталей, размещения слоя смазки, компенсации температурных деформаций и погрешностей формы, расположения поверхностей, погрешностей сборки и др. Для наиболее ответственных соединений, которые должны работать в условиях жидкостного трения, зазоры подсчитываются на основе гидродинамической теории трения [3].
Если работа соединения допускается в условиях полужидкостного, полусухого или сухого трения, то выбор посадок чаще всего производится по аналогии с посадками известных и хорошо работающих соединений. При этом следует вносить поправки с учетом конкретных условий работы соединений и их параметров.
В неподвижных соединениях посадки с зазором применяются для обеспечения беспрепятственной сборки деталей (особенно сменных). Их относительная неподвижность обеспечивается дополнительным креплением: шпонками, болтами штифтами и т.д. Выбор посадки для неподвижного соединения производится таким образом, чтобы наименьший зазор обеспечивал компенсацию отклонений формы и расположения сопрягаемых поверхностей, если они не ограничиваются полями допусков размеров этих поверхностей. Кроме того, наименьший зазор должен включать запас на его регулирование, если это необходимо в соединении, а также запас на свободное вхождение деталей, что особенно важно при механической и автоматической сборке. Практически можно рекомендовать следующую область применения посадок с зазором:
1. Посадки с нулевым зазором (скользящие посадки), получаемые сочетанием отверстия H с валом h, применяют, главным образом, в неподвижных соединениях при необходимости частой разборки (сменные детали), если требуется легко передвигать или поворачивать детали одну относительно другой при регулировке или центрировании деталей.
2. ПосадкуH6/h5 применяют для особо точного центрирования, например, для пиноли в корпусе бабки станка.
3. Посадку Н7h6 применяют для сменных колес в станках; для соединений с коротким рабочим ходом, например, для хвостовиков пружинных клапанов в направляющих; для соединения деталей, которые должны легко передвигаться при затяжке; для точного направления при возвратно-поступательном движении, например, плунжер насоса высокого давления.
4. Посадку H8/h7 используют для центрирующих поверхностей при пониженных требованиях к соосности.
5. ПосадкиН8/h8, H9/h9, H9/h8 применяют для неподвижно закрепленных деталей при невысоких требованиях к точности механизмов, небольших нагрузках и необходимости обеспечить легкую сборку (зубчатые колеса, шкивы и другие детали, соединяющиеся с валом на шпонке; корпуса подшипников качения, центрирование фланцевых соединений), а также в подвижных соединениях при медленных и редких поступательных и вращательных перемещениях (перемещающиеся зубчатые колеса, зубчатые торцовые муфты).
6. Посадку H11/h11 используют для относительно грубо центрируемых неподвижных соединений (центрирование фланцевых крышек, фиксация накладных кондукторов), для неответственных шарниров.
7. ПосадкаH7/g6 (предпочтительная) применяется в подвижных соединениях для обеспечения герметичности (например, золотниковые механизмы, шпиндели точных станков, подвижные шестерни на валах в коробках передач, шатунная головка с шейкой коленчатого вала, сменные втулки кондукторов, изделия на пальцах приспособлений пря механической обработке). В особо точных механизмах применяют посадку H6/g5и дажеH5/g4.
8. ПосадкуH7/f6 применяют в подшипниках скольжения при скоростях до 150 рад/с и невысоких нагрузках. Для подшипников скольжения при нескольких опорах или разнесенных опорах при невысокой точности центрирования применяются посадкиH8/f8 , H9/f9.
9. ПосадкиH7/e7, H7/e8, и H8/e8 применяются в подшипниках при высокой частоте вращения более 150 рад/с или осложненных условиях монтажа (например, в электродвигателях, механизмах передач автомобилей, коренных шейках коленчатого вала и шейках распределительного вала двигателя внутреннего сгорания).
10. Посадки H8/d9, H9/d9 применяют для поршней в цилиндрах паровых машин и компрессоров, а также при невысоких требованиях к точности: трансмиссионные валы в подшипниках, сальники, холостые шкивы на валах.
11. Посадки низкой точности H11/d11, D11/h11предназначены для подвижных соединений, не требующих точности перемещения и работающих в условиях пыли и грязи. Например: крышки подшипников в распорные втулки в корпусах; грубые направляющие прямолинейного движения; направление шпинделей по внутреннему диаметру грунд-букс; шарниры и ролики на осях.
Выбор переходных посадок
Переходные посадки H/n,H/m, H/k,H/js используются в неподвижных разъемных соединениях для центрирования деталей, которые при необходимости могут двигаться вдоль вала или быть сменными. Эти посадки характеризуются малыми зазорами и натягами, что позволяет собирать детали при небольших усилиях. Для обеспечения неподвижности одной детали относительно другой их дополнительно крепят шпонками, стопорными винтами и другими крепежными средствами.
Сочетание выборкой точности центрирования с относительной легкостью сборки и разборки соединения возможно лишь при небольших изменениях натяга и зазора. Поэтому переходные посадки предусмотрены только в 4-8 квалитетах. Обычно применяют посадки, в которых точность вала на один квалитет выше точности отверстия.
В переходных посадках при сочетании наибольшего предельного размера вала и наименьшего предельного размера отверстия всегда получается натяг, а при сочетании наибольшего предельного размера отверстия и наименьшего предельного размера вала - наибольший зазор.
Выбор переходных посадок определяется требуемой точностью центрирования и легкостью сборки и разборки соединения. Точность центрирования вращающихся деталей определяется величиной радиального биения, которая будет зависеть от величины зазора в соединении, от погрешностей формы и расположения поверхностей сопрягаемых деталей и износа деталей при повторных сборках и разборках. Для компенсации указанных погрешностей при выборе переходных посадок следует максимально допустимый зазор в соединении уменьшить в 2-3 раза и по нему выбрать посадку.
На практике выбор переходных посадок чаще всего производят по аналогии с известными и хорошо работающими соединениями. Расчеты выполняются редко и в основном как проверочные. Они могут включать:
· расчет вероятности получения зазоров и натягов в соединении;
· расчет наибольшего зазора по допустимому эксцентриситету соединяемых деталей;
· расчет прочности деталей (только для тонкостенных деталей) и усилия запрессовки при наибольшем натяге.
При высоких требованиях к точности центрирования, а также при больших, особенно ударных нагрузках и вибрациях, назначают посадки с большим средним натягомH/n и H/m. Чем чаще требуется разборка - сборка узла, тем с меньшим натягом следует выбирать переходные посадки, т.е. применять посадки H/k,H/js.
ПосадкуH7/n6 применяют для зубчатых колес, муфт, кривошипов и других деталей, работающих при больших нагрузках, ударах и вибрации; в соединениях, разбираемых только при капитальном ремонте; для установочных колец на валах электрических машин, кондукторных втулок, установочных пальцев, штифтов. Сборка таких соединений производится под прессом.
Посадка H7/m6 применяется для соединений, редко подвергающихся разборке: подшипники качения в тяжелом машиностроении, цилиндрические штифты.
Посадка H7/k6 в среднем дает незначительный зазор (1-5 мкм) и обеспечивает хорошее центрирование, не требуя значительных усилий для сборки и разборки. Она применяется чаще других переходных посадок: для посадки шкивов, зубчатых колес, муфт, маховиков, для втулок подшипников и вращающихся на валах зубчатых колес и т.д.
ПосадкаH7/js6имеет большие средние зазоры и применяется взамен предыдущей для облегчения сборки.
Дата добавления: 2018-04-15; просмотров: 1696; Мы поможем в написании вашей работы! |
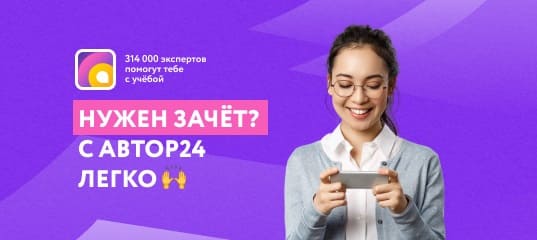
Мы поможем в написании ваших работ!