Назначение участка, его состав, связь со смежными участками и подразделениями депо. Расчет площади участка депо.
Характеристика и задачи локомотивного депо
Основными задачами сервисного локомотивного депо Пенза являются:
– своевременное выполнение установленных СТМ – сервис тягового подвижного состава заданий по ремонту, техническому обслуживанию и модернизации локомотивов и линейного оборудования;
– производство ремонта, технического обслуживания и модернизации локомотивов согласно технологии и в установленные сроки;
– обеспечение выполнения требований безопасности движения поездов;
– совершенствование технологии ремонта локомотивов и технической оснащенности ремонтных цехов, повышение уровня производительности труда;
– повышение качества ремонта и обеспечение высокого уровня эксплуатационной надежности локомотивов;
– выполнение установленных СТМ – сервис по ремонту тягового подвижного состава – филиалом ОАО «РЖД» технических, экономических и финансовых показателей и нормативов;
– текущее содержание, эксплуатация и своевременный ремонт зданий, сооружений, машин, механизмов, оборудования, технических и транспортных средств в соответствии с установленными нормативами;
– проведение работы по снижению эксплуатационных расходов, эффективному использованию основных фондов;
– оказание услуг по прочим видам деятельности сторонним организациям;
– организация работы по содержанию установленного норматива запаса материальных ценностей мобилизационного резерва и специального запаса;
|
|
– обеспечение защиты окружающей среды, пожарной и промышленной безопасности на опасных производственных объектах и других объектах ремонтного локомотивного депо;
– проведение работы по вопросам организации труда, укрепления трудовой и технологической дисциплины на основе единой политики, проводимой в ОАО «РЖД», внедрения прогрессивных форм организации и мотивации труда, соблюдения требований, норм и правил охраны труда, производственной санитарии и правил пожарной безопасности;
– обеспечение социальной защиты работников, выполнение условий Коллективного договора, оплата труда в соответствии с Положением об оплате труда работников СТМ – сервис по ремонту ТПС - филиала ОАО «РЖД», разработанным на основании Положения о корпоративной оплате труда работников ОАО «РЖД»;
– подготовка, переподготовка и повышение квалификации работников, своевременное укомплектование контингента согласно потребностям на выполняемые объемы работ;
– взаимодействие с другими структурными подразделениями – по вопросам деятельности ремонтного локомотивного депо, с органами местного самоуправления и государственной власти субъектов Российской Федерации – по вопросам обеспечения условий для текущей деятельности и развития ремонтного локомотивного депо, экологии и решения социальных вопросов железнодорожников;
|
|
– ведение учета и предоставление отчетности о показателях работы депо существующим порядком по установленным формам;
– обеспечение в установленном порядке защиты прав и законных интересов ОАО «РЖД» и СТМ – сервис по ремонту ТПС - филиала ОАО «РЖД» в судебных и иных органах;
– ведение делопроизводства и осуществление хранения документов в порядке, установленном в ОАО «РЖД», ведение статистического учета и отчетности.
Ремонтное локомотивное депо обеспечивает функции:
– Соблюдение требований законодательных и иных нормативных актов Российской Федерации, внутренних документов ОАО «РЖД», по ремонту ТПС – филиала ОАО «РЖД», СТМ – сервис, Куйбышевской железной дороги по ремонту ТПС;
– обеспечение выполнения требований безопасности движения поездов, качества ремонта и технического обслуживания локомотивов;
– принятие мер по совершенствованию производственно–экономической деятельности ремонтного локомотивного депо, улучшению использования основных производственных фондов и оборотных средств, рациональному использованию эксплуатационных расходов и материальных ресурсов, повышению производительности труда и снижению себестоимости работ;
|
|
– обеспечение максимального применения Типовых норм затрат рабочего времени на текущих видах ремонта и технического обслуживания локомотивов;
– принятие мер по приведению численности работников к объемам выполняемых работ;
– организация и планирование ритмичного материально–технического обеспечения производственного процесса необходимыми ресурсами по нормам расхода;
– соблюдение правил и норм охраны труда, промышленной, пожарной безопасности и экологического контроля, принятие мер по предупреждению производственного травматизма;
– выполнение установленных финансовых, природоохранных и других показателей;
– проведение работ по стандартизации и метрологии;
– обеспечение защиты экономических интересов ОАО «РЖД» при заключении и исполнении договоров;
– обеспечение соблюдения работниками трудовой и исполнительской дисциплины.
3 Организация и разработка плана локомотивного депо. Выбор типа здания локомотивного депо
Все устройства и сооружения железнодорожного транспорта, необходимые для перевозок грузов и пассажиров, размещают на так называемой «полосе отчуждения». Часть территории полосы отчуждения занимают устройства локомотивного хозяйства. На этой территории, называемойтяговой или деповской, располагаются здания локомотивного депо и все сооружения, необходимые для нормальной работы.
|
|
Деповская (тяговая) территория размещается обычно вблизи станции или между главными путями (островное положение), или по одну сторону главных путей.
План тяговой территории с размещением всех сооружений, обустройств и тракционных путей называют генеральным.
Здания депо и служебно-бытовые помещения размещают с учетом максимального использования естественного освещения и влияния направления господствующих ветров. Тяговую территорию благоустраивают: озеленяют, хорошо освещают, проезжую часть дорог безрельсового транспорта и пешеходные дорожки асфальтируют.
На деповской территории укладывают рельсовые пути для прохода локомотивов и моторвагонного подвижного состава на станцию и со станции, заезда на специализированные стойла в здании депо, пути отстоя подвижного состава между поездами и в резерве, пути парка колесных пар, треугольника для поворота локомотивов и хозяйственных поездов. При тепловозной тяге дополнительно укладываются пути для реостатных испытаний.
Тяговая территория примыкает к станции обычно двумя путями, по одному из которых осуществляется движение только в депо, по другому — на станцию. Радиусы кривых для путей тяговой территории принимаются не менее 200 м. В трудных условиях допускается уменьшение радиусов кривых до 180 м. Расстояние между осями смежных путей территории локомотивного хозяйства принимают равным 4,8 м (не менее 4,5 м), для путей экипировки — 5,5 м. При обыкновенных стрелочных переводах укладывают крестовины марки 1/9, а при симметричных — 1/6.
Здания и устройства, расположение которых у путей следования локомотивов вызвано технической необходимостью (экипировочные устройства, эстакады слива топлива, здания реостатных испытаний и т.д.), могут находиться от оси ближайшего железнодорожного пути на расстоянии габарита приближения строения С. Указанные сооружения должны быть огнестойкими и иметь несгораемые кровли.
Пути в стойлах депо и смотровых площадках устраивают прямыми и горизонтальными, а перед воротами депо предусматривают прямые вставки на длину локомотива. Расстояние между центрами стрелочных переводов принимают при марке крестовин 1/9 и типе рельсов Р65-30, 39 м; при типах рельсов Р50, Р43-30, 85 м. Длину путей отстоя локомотивов и резерва определяют в зависимости от количества единиц подвижного состава, находящегося одновременно на территории депо, а также от длины локомотива или секции моторва- гонного подвижного состава.
Тяговая территория электровозного депо отличается от территории тепловозного лишь небольшими размерами склада нефтепродуктов; территория депо электропоездов и дизель-поездов — наличием удлиненных экипировочных и обмывочных позиций, а также большей длиной путей отстоя.
Типы локомотивного депо:
– прямоугольно-павильонный тип здания (рис. 3, а) депо имеет наименьшую стоимость постройки, занимает небольшую площадь, что дает возможность удобно расположить ремонтные стойла рядом с участком и отделениями депо. Вследствие минимального периметра наружных стен и площади оконных проемов эксплуатационные расходы на содержание таких зданий (отопление, текущий ремонт) значительно ниже по сравнению со зданиями других типов. Правильное расположение здания на местности относительно частей света и «розы ветров» создает условия для лучшего сохранения тепла в зимнее время, даже в районах с низкой температурой, чтобы ветер доминирующего направления не имел прямого попадания в ворота и на световые проемы. Применение этого типа зданий ограничено, их нельзя построить в стесненных условиях тяговой территории по ширине. Кроме того, в средних секциях здания почти отсутствует естественное освещение и его заменяют люминесцентным.
– прямоугольно-ступенчатый тип (рисунок 2, б, е) здания представляет собой секции, смещенные относительно друг друга в продольном направлении. Секции располагаются с небольшим заходом одна за другую для свободных внутренних проездов и проходов.
|
|
|
|
|
|
Рисунок 2 Типы локомотивных зданий
а — павильонный тип; 6, е — прямоугольно-ступенчатый тип; в, г, д — веерный тип; 1 — ремонтные участки; 2 — ремонтные позиции.
Схемы планов локомотивных депо даны на рисунке 2. Здания депо по принятой классификации относятся к группе промышленных и строятся в соответствии с требованиями по прочности, устойчивости, долговечности, внутреннему благоустройству, экономичности и архитектурной выразительности.
Степень огнестойкости здания определяют категорией пожарной опасности. Здания локомотивного депо и экипировки тепловозной тяги отнесены к категории В, а электрической тяги и склады песка — к категории Д.
Основные элементы зданий — фундаменты, колонны, стены, перекрытия, крыша, зенитные или аэрационные фонари, перегородки, лестницы, окна, двери, ворота. Колонны устанавливаются на расстоянии (шага) 6 м между осями (иногда 12 м).
|
Рисунок 3 Схематические планы ремонтных депо
I - IV типов: участок ТР-2; 2 — участок ТР-1 и ТО-3; 3 — ремонтные мастерские; 4 — служебно-бытовые помещения
В последние годы получили наибольшее распространение прямоугольно – павильонные и прямоугольно – ступенчатые типы здания депо. Такая конструкция зданий позволяет использовать их при перспективном развитии – пристраивают новые секции с последующими рядами павильона или ступени.
Проектом принимаю депо прямоугольно – павильонного типа. Депо имеет наименьшую стоимость постройки, занимает небольшую площадь, что дает возможность удобно расположить ремонтные позиции рядом с участком и отделениями депо. Вследствие минимального периметра наружных стен и площади оконных проемов эксплуатационные расходы на содержание таких зданий (отопление, текущий ремонт) значительно ниже по сравнению со зданиями других типов. Правильное расположение здания по местности относительно частей света «розы ветров» создает условия для лучшего сохранения тепла в зимнее время, даже в районах с низкой температурой, чтобы ветер доминирующего направления не имел прямого попадания в ворота и на световые проемы. Применение этого типа здания ограничено, их нельзя построить в стесненных условиях тяговой территории по ширине. Кроме того, в средних секциях здания почти отсутствует естественное освещение и его заменяют люминесцентным.
Назначение участка, его состав, связь со смежными участками и подразделениями депо. Расчет площади участка депо.
Участок ТР-3предназначен для осмотра, ремонт и ревизия основных узлов ходовых частей, рессорного подвешивания, ударно-сцепных устройств, песочного оборудования, тяговых двигателей, вспомогательных машин, пуско-тормозных резисторов, крышевого оборудования, индивидуальных электропневматических и электромагнитных контакторов, силовых блоков п блоков управления реостатным тормозом, аккумуляторных батарей, пневматического оборудования, автостопа и радиосвязи. Все обнаруженные неисправности устраняют. Производят замену или ремонт деталей, имеющих допуски и износы свыше предельных допустимых в эксплуатации.
Размеры каждого отделения участка депо определяется в зависимости от принятой технологии работ в них и количество выбранного оборудования и рабочих мест в соответствии с объемом работы.
Компоновка производственных помещений при планировки депо имеет большое значение, для создания наилучших условий выполнения всех трудовых процессов, по ремонту подвижного состава, его узлов, агрегатов и деталей. Учитывается производственная взаимосвязь участка, рациональной планировкой уменьшают длину транспортных путей при перемещении узлов, деталей, инструментов, материалов и агрегатов, приближают потребителей к источнику электрической энергии сжатого воздуха, горячей воды, пара.
Важным показателем рациональной планировки отделений и участков депо является обеспечение хороших санитарно – гигиенических и производственных условий труда, возможность дальнейшего развития производственных помещений при увеличении объема работы. При установке оборудования необходимо обеспечить поточность технологического процесса ремонта узлов, агрегатов и деталей локомотива, исключить встречное их перемещение. Про – ходы между станками и другими технологическим оборудованием должны быть не менее одного метра с учетом ограждения движущихся частей. Шкафы стеллажи и верстаки устанавливаются вплотную к стенам.
При определении габаритных размеров стойловых участков необходимо составить схемы расположения локомотивов или секций на ремонтных позициях в соответствии с принятым технологическим процессом, учитывая при этом установку необходимого оборудования, а так же создания проходов и проездов в соответствии с требованиями техники безопасности.
На участке работает 68 рабочих, 4 бригадира 2 мастера и 1 старший мастер 61 слесарь.
Участок ТР – 1 связан со смежными участками с такими как электроаппаратный, аккумуляторный, кип, токоприемников, автотормозной.
Основная унифицированная длина участка ТР – 1 равна 84 м, ширина 24 м высота 10,8 м (от головки рельсов до низа конструкций перекрытия) из условия установки здесь мостового крана грузоподъёмностью 2 т. Участок проектируем на деве сквозных пути. На одном пути два локомотива и установлен станок типа КЖ – 20М для обточки бандажей колесных пар без выкатки их из под локомотива. На втором пути размешаем скатпускную канаву для одиночной выкатки КМБ или колесной пары. Расстояния при этом от стены до оси крайнего пути и между осями смежных путей равно соответственно 5 – 7, 7 – 5 м. Полученные данные сводим в таблицу 1
Таблица 1 Каткая характеристика основных участков локомотивного депо
Вид ремонта | Число путей | Число стойл | Длина цеха м | Ширина цеха м | Высота цеха м | Площадь цеха м | Обьем цеха м |
1 | 2 | 3 | 4 | 5 | 6 | 7 | 8 |
ТР – 3 | 1 | 1 | 108 | 30 | 13,2 | 3240 | 42768 |
ТР – 2 | 3 | 1 | 84 | 24 | 10,8 | 2016 | 21773 |
ТР – 1 | 2 | 4 | 84 | 24 | 10,8 | 2016 | 21773 |
Объем работы участка ТР – 1
При текущем ремонте ТР-1 производится осмотр, ремонт и ревизия основных узлов ходовых частей, рессорного подвешивания, ударно-сцепных устройств, песочного оборудования, тяговых двигателей, вспомогательных машин, пуско-тормозных резисторов, крышевого оборудования, индивидуальных электропневматических и электромагнитных контакторов, силовых блоков п блоков управления реостатным тормозом, аккумуляторных батарей, пневматического оборудования, автостопа и радиосвязи. Все обнаруженные неисправности устраняют. Производят замену или ремонтдеталей, имеющих допуски и износы свыше предельных допустимых вэксплуатации.
Перед постановкой на ремонтное стойло локомотивная бригада выполняет опробование электровоза под напряжением; при этом проверяют работу вспомогательных машин, силовых и низковольтных цепей, регулятора напряжения, действие автотормозов, электропневматического тормоза, песочниц, наличие тока возбуждения при сборе схемы электрического торможения.
О всех неисправностях делают записи в журнале технического состояния электровоза и в книге ремонта. До постановки электровоза на ремонтное стойло ходовые части очищают и обдувают сжатым воздухом. Перед началом ремонта колесные пары электровоза вывешивают.
По каждому виду оборудования выполняют следующие работы:
– рамы и сочленения тележек. Осматривают рамы, тщательно проверяя, нет ли трещин в местах сопряжений продольных балок (боковин) и поперечных балок и в местах крепления кронштейнов подвески кузова. Осматривают межтележечное сочленение, проверяя прочность затяжки болтов, состояние направляющих пластин и упорных планок цилиндрических штоков возвращающего устройства. Проверяют плотность посадки шарового соединения в направляющих: суммарный вертикальный зазор не должен превышать 2 мм. Контролируют состояние и крепление грязезащитного меха и кожуха, крепление маслоподводя-щнх трубок. Смазывают все трущиеся поверхности межтележеч-ного сочленения;
– колесные пары. При каждом ТР-1 осматривают все колесные пары, обязательно проворачивая их при осмотре на 360". При осмотре колесных пар проверяют:
па бандажах — нет ли трещин, отколов, раковин, плен, выбоин, ползунов, вмятин и раздавленных мест, ослабления бандажей на ободе центра (путем остукивания молотком), сдвига (по контрольным рискам на бандаже и ободе центра), предельного проката бандажей, подреза и остроконечного наката гребней, ослабления бандажных колец, на колесных центрах – нет ли трещин в ступицах, спицах и ободах, признаков ослабления или сдвига ступиц на оси;
на осях –нет ли поперечных или продольных трещин, плен, протертых мест или других дефектов на открытых частях оси. Замеряют межбандажное расстояние: оно должно быть 1440+3 мм. Колесные пары должны полностью удовлетворять требованиям Инструкции по освидетельствованию, формированию и ремонту колесных цар локомотивов, а также нормам допусков и изноеов;
– зубчатая передача и карданный привод. На каждом ТР-1 производится прослушивание работы опорных подшипников, подшипников шестерни и зубчатого зацепления. Осматривают кожух зубчатой передачи, проверяют плотность соединения верхней п нижней частей кожуха, убеждаются в том, что в кожухе нет трещин, исправен воздушный сапун;
– проверяют прочность затяжки, целостность деталей и масленки внешних карданных муфт тяговых двигателей;
– добавляют смазку в опорные подшипники, подшипники малой шестерни и игольчатые подшипники внешней карданной муфты в соответствии с картой смазки.
Буксовый узел. Осматривают крышки всех букс, проверяют плотность прилегания, целостность и надежность крепления буксовых шпилек. Проверяют состояние сайлентблоков буксовых направляющих, защитных кожухов, изоляционных втулок;
– устраняют течь масла из стаканов, в зимний период эксплуатации удаляют конденсат, добавляют масло до контрольной отметки. На каждом ТР-1 производят ревизию буксовых заземляющих устройств;
– рессорное подвешивание. Проверяют щеки рессор "первичного подвешивания ультразвуковым дефектоскопом. Осматривают первичное и вторичное рессорное подвешивание, балансиры, рессорные подвески. Листовые рессоры, имеющие трещины, изломы в хомуте или листах, сдвиг листов или ослабление хомута, заменяют. Цилиндрические рессоры с трещинами или изломами в витках, а также при отсутствии зазора между витками также заменяют. Проверяют состояние ванн, боковых опор, поводков, защитных чехлов ванн вторичного рессорного подвешивания, определяют уровень масла в ваннах, доливают масло до контрольных отметок. Запрессовывают смазку в трущиеся части рессорного подвешивания;
– тормозная рычажная передача. Осматривают тормозную рычажную передачу, проверяют состояние и крепление предохранительных скоб, тросов, тормозных башмаков и колодок. Тормозные колодки толщиной менее 20 мм заменяют;
– проверяют наличие шплинтов и шайб у валиков;
– производят ревизию всех автоматических регуляторов выхода штоков тормозных цилиндров: выходы штоков должны быть в пределах 60 — 120 мм. Проверяют параллельность расположения тормозных колодок по отношению к бандажу и зазор между колодками п бандажом, который должен составлять 7—12 мм. Смазывают все трущиеся поверхности;
– проверяют работу ручных тормозов;
– ударно-сцепные устройства. Производят осмотр обеих автосцепок без разбора их механизма. Проверяют автосцепки комбинированным шаблоном. Состояние автосцепки должно отвечать требованиям действующей инструкции МПС по ремонту и содержанию автосцепных устройств.
Проверяют высоту н наклон горизонтальной оси автосцепки: высота ее от головки рельса должна быть в пределах 980 — 1080 мм. Голова автосцепки должна свободно (от руки) перемещаться в поперечном направлении. Регулируют длину цепочек расцеппых механизмов, убеждаются в исправном действии рас-цепного рычага, в надежности крепления валика. Все детали автосцепки, не удовлетворяющие техническим требованиям, предусмотренным инструкцией МПС по ремонту и содержанию автосцепных устройств, заменяют. Фрикционный аппарат должен быть разжат между упорами в буферном брусе. Допускается перекос фрикционного аппарата или односторонний износ упоров, при котором зазор между упорами по одной стороне или по диагонали не превышает 3 мм. Проверяют крепление предохранительной плиты фрикционного аппарата;
– тяговые двигатели. Перед осмотром и ремонтом тяговых двигателей электровоз должен быть вывешен для свободного вращения якорей тяговых двигателей. Включив тяговые двигатели, определяют на слух, как работают якорные подшипники и щеточный узел. При ненормальной работе щеточного узла (вибрация щеток, повышенный шум, потемнение коллектора) замеряют величину биения коллектора, которая должна быть не более 0,1 мм; в случае превышения этого значения коллектор обтачивают.
Открыв люки тяговых двигателей, отсоединяют траверсу со щеткодержателями, производят продувку двигателей сжатым воздухом, одновременно прокручивая траверсу. Производят ревизию щеткодержателей без нх демонтажа, проверяют нажатие нажимных пружин, которое должно быть в пределах 1,8—2,2 кгс, очищают корпуса от нагаров и оплавлений, щеткодержатели с трещинами и неисправными нажимными пружинами заменяют. Щетки осматривают, проверяют легкость хода их в гнезде, надежность заделки шунтов, наличие демпферной и опорной прокладок под нажимными пружинами. Щетки высотой менее 21 мм, а также имеющие сколы, изломы, ослабления шунтов или их надрыв на площади свыше 25% заменяют щетками аналогичной марки. Проверяют правильность установки щеткодержателей: расстояние корпуса щеткодержателя от рабочей поверхности коллектора должно быть в пределах 2—4 мм. Осматривают кронштейны щеткодержателей и проверяют их крепление. Изоляторы протирают, закопченные места промывают бензином, при наличии повреждения глазури или трещин кронштейн заменяют. Осмотрев коллектор, удаляют следы перебросов дуги и кругового огня. Недопустимо затягивание пластин коллекторов. В этом случае производят продорожку коллектора н снятие фасок с последующей шлифовкой. Прочищают волосяной или стеклянной щеткой изоляционное пространство между пластинами, поверхность коллектора протирают салфетками, потемневшие пластины очищают бензином. Проверяют состояние конуса коллектора, зачищают следы перебросов, протирают внешнюю и внутреннюю поверхности конуса, устраняя грязь и пыль, восстанавливают изоляционное покрытие эмалью 1201. Осматривают стеклобандаж якоря, изоляцию полюсных катушек в допустимых для осмотра местах, состояние выводных концов и подводящих кабелей. Наконечники, имеющие следы перегревов и оплавлений, пропаивают в переносных тиглях с последующей зачисткой. Проверяют крепление главных и
дополнительных полюсов и подшипниковых щитов; ослабшие болты подтягивают. Проверя-
т крепление замков крышек смотровых люков, состояние уплотнений (в зимний период эксплуатации), крепление вентиляционных патрубков.
Замеряют сопротивление изоляции якоря и катушек полюсов мегомметром: оно должно быть не ниже 2,5 МОм. Добавляют смазку в якорные подшипники.
Вспомогательные машины. Открыв крышки коллекторных люков вспомогательных машин, продувают их сжатым воздухом;
– производят осмотр щеткодержателей, убеждаются в том, что нажатие нажимных пружин находится в пределах 0,46—0,53 кгс; очищают корпуса от нагаров и оплавлений. Щеткодержатели с трещинами и неисправными нажимными пружинами заменяют. Щетки осматривают, проверяют легкость хода их в гнезде, надежность заделки и целостность шунтов. Щетки высотой менее 15 мм, а также имеющие сколы, изломы, ослабления шунтов или их падрыв на площади свыше 25% должны быть заменены новыми аналогичных марок. Проверяют правильность постановки щеткодержателей: расстояние корпуса щеткодержателя от рабочей поверхности коллектора должно быть 1,6—3,5 мм. Осматривают кронштейны щеткодержателей и проверяют их крепление. Изоляторы протирают, закопченные места промывают бензином, при наличии трещин, неустранимых следов сплошных перекрытий изоляторы заменяют. Осмотрев коллектор, удаляют следы переброса дуги и кругового огня, нродороживают коллектор при наличии затянутых пластин п снимают фаски с последующей шлифовкой. Поверхность коллектора протирают сухой ветошью. Применение бензина недопустимо. Прочищают стеклянной щеткой изоляционное пространство между пластинами. Проверяют состояние конуса коллектора, зачищают следы перебросов, протирают поверхность конуса, восстанавливают покрытие эмалью 1201.
Проверяют состояние и крепление выводных концов, осматривают соединительные коробки. Проверяют крепление замков внешних и внутренних крышек мотор-вентиляторов, крышек мотор-компрессоров и генераторов, натяжение ремней генераторов и посадку шкивов. Замеряют сопротивление изоляции вспомогательных машин мегомметром: оно должно быть не ниже 5 МОм. Добавляют смазку в подшипники. Мотор-вентилятор пуско-тормозных резисторов 1Аи 2732/4. Включив мотор-вентилятор, определяют на слух, как работают якорные подшипники и крыльчатка вентилятора.
Производят осмотр и ремонт мотор-вентиляторов в том же объеме, что и остальных вспомогательных машин. При этом заменяют щетки высотой менее 14 мм, проверяют нажатие пружин щеткодержателей (оно должно составлять 0,95—1,2 кгс) и замеряют расстояние от корпуса щеткодержателя до рабочей поверхности коллектора, которое должно быть в пределах 1,6—3,2 мм. Для очистки деталей от грязи и следов перебросов применять бензин недопустимо;
– проверяют плотность прилегания крышек смотровых люков, а также зазор между крыльчаткой и воздухопроводом, который должен быть не менее 1 мм, легкость вращения крыльчатки и плотность ее посадки на валу. Протирают разделительную изоляционную плиту и опорные изоляционные подставки. Отсоединив подводящие кабели в коробке зажимов, замеряют сопротивление изоляции корпуса двигателя вентилятора относительно кузова электровоза мегомметром на 2500 В: оно должно быть не менее 30 МОм. Замеряют сопротивление обмоток якоря и полюсов относительно корпуса двигателя вентилятора мегомметром на 500 В: оно должно быть не ниже 5 МОм. Добавляют смазку в подшипники;
– проверяют состояние и плотность прилегания главных контактов, производят их зачистку и шлифовку. Замеряют раствор главных контактов в выключенном состоянии: он должен быть в пределах 24—28 мм. Проверяют работу пневматического привода и удерживающего устройства. Протирают все изоляционные части выключателя. Осмотрев вспомогательные блокировки, зачищают контакты, имеющие подгары и оплавления;
– осматривают и зачищают дугогасптельные контакты; контакты с износом более 3 мм заменяют. Определяют раствор главных контактов (должен быть 15—17 мм) и раствор дугогаснтель-ных (19 — 21 мм). Не допускается поперечное смещение дугогаси-тельных контактов более чем на 1,5 мм. Проверяют зазор между дугогасительным рогом подвижного контакта и изоляционным держателем верхнего дугоприемного рога: он должен быть равен 2—3 мм ;
– производят проверку состояния и крепления гибких шунтов, шин, изоляционных держателей и дугогасительных катушек. Проверяют (вручную) последовательность замыкания дугогасительных н мостиковых контактов; в момент касания дугогасительных контактов раствор мостиковых'должен быть не менее 6 мм;
– проверяют работу пневматических приводов, их плотность, а также плотность подводящих воздухопроводов. Осматривают низковольтные блокировки, проверяют раствор и замыкание их контактов;
– осматривают коммутирующие конденсаторы и конденсаторы фильтра, убеждаются в том, что нет утечки масла, проверяют крепление выводов, а также автоматические предохранители. Осмотрев измерительные транедукторы, проверяют затяжку кон-некторных соединений. Осматривают шунт-датчик тока возбуждения, проверяют крепление подводящих кабелей;
– у датчика тормозного усилия проверяют плавность хода пневматического штока, в случае заедания пневматический привод разбирают и промазывают манжеты маслом МВП. Проверяют крепление штеккерных соединений магнитного потенциометра;
– осматривают регулятор управления, проверив надежность крепления кассет в кабинах. Осмотрев переключатель тормоза РР015 и ограничитель тормозного момента, проверяют работу микровыключателей;
– убеждаются в исправности системы вентиляции шкафов силового импульсного преобразователя и регулятора управления. Осматривают реле управления и давления в цепях реостатного тормоза. Проверяют правильность сбора электрической схемы реостатного тормоза.
– уроизводят проверку действия управляющего регулятора тормоза и импульсного преобразователя, исходя из заводской Инструкции по проверке
реостатного тормоза, установлению и устранению дефектов;
– контроллер машиниста. Осмотрев контроллер, проверяют состояние кулачковых включателей, раствор и провал их контактов, зачищают подгоревшие и оплавленные контакты. Убеждаются в легкости хода и отсутствии заеданий кулачковых барабанов: реверсивного, управления и ослабления возбуждения;
– проверяют работу блокирующих устройств во всех режимах управления, осматривают электромагнитную защелку. Проверяют четкость фиксации по позициям штурвала машиниста, работу возвращающего устройства штурвала, затяжку коннекторных соединений, крепление подводящих проводов и деталей. Смазывают трущиеся части в соответствии с картой смазок;
– осматривают пусковые и демпферные резисторы мотор-компрессоров, очищают изоляторы, проверяют крепление перемычек и подводящих кабелей;
– осматривают аварийную панель мотор-веитиляторов и панель отключения поврежденных тяговых двигателей, убеждаются в том, что ножн устанавливаются правильно, контакты не перегреваются, надежно закреплены подводящие кабели.
– осмотрев релейный шкаф, проверяют контакты реле управления, подвижных частей реле на отсутствие заеданий и перекосов, крепление стоек, перемычек и подводящих проводов. Проверяют работу автоматических защитных выключателей трехкратным переключением. Включают в контрольную розетку разъединительные диоды цепей управления, чтобы убедиться в их исправности;
– производят ревизию одного мотор-калорифера вентиляции и отопления кабин машиниста.
– в зимний период эксплуатации осматривают силовое оборудование отопления состава, протирают его, просушивают. Замеряют сопротивление изоляции цепей отопления состава: оно должно быть не менее 10 МОм;
– проверяют взаимодействие и последовательность выключения всех аппаратов цепей управления;
– токоприемники. Производят ревизию одного токоприемника со вскрытием пневматического привода, старую смазку удаляют, рабочую поверхность протирают и смазывают смазкой ЦИАТИМ-203. Осматривают рамы токоприемников и детали приводного механизма; трещины, прожоги и вмятины глубиной более 5 мм ликвидируют. Проверяют состояние шарниров, рычагов, кронштейнов, пружин, надежность их крепления и шплинтовки осей и валиков. Валики, оси, втулки, имеющие предельный износ, заменяют. Осматривают шарнирные соединения, смазывают подшипники, производят подъем и опускание токоприемника вручную и проверяют, нет ли заедания в шарнирных соединениях. Проверяют крепление шунтов и подводящих шин. Полозы осматривают, проверяют состояние медных накладок. Полозы, имеющие трещины в каркасах или погнутые концы, толщину накладок менее 3 мм, а также полозы с отстающими от каркаса концами крайних накладок, заменяют. Медные накладки зачищают от наплавов личным напильником, ослабленные накладки закрепляют. Проверяют плотность прилегания накладок к полозу, плавность перехода рабочей поверхности на скосы. Установку полозов на токоприемнике по уровню проверяют с помощью линейки длиной 1000 мм. Перекос полоза свыше 20 мм не допускается. Производят подмазку полозов графитом. Проверяют работу вторичного подвешивания полоза, состояние кареток и кулис; смазывают стаканы кареток и кулисный механизм смазкой МВП. Осматривают изоляторы; изоляторы с трещинами и отколами заменяют; протирают изоляторы, воздухопод-водящие рукава и токонесущие части. Проверяют пневматический привод и подводящий трубопровод на утечку воздуха. Определяют величину подъема токоприемника при давлении воздуха 3,5 кгс/см2, проверяют статические характеристики обоих токоприемников в пределах рабочей высоты 400—1000 мм и регулируют нажатие полоза на контактный провод: при подъеме оно должно составлять 8—10 кгс, при опускании 10—12 кгс; перепад нажатий при подъеме и опускании у одного токоприемника не должен превышать 2 кгс.
– крышевое оборудование. Осматривают разъединители и за-землитель, удаляют с ножей старую смазку, проверяют правильность включения, площадь прилегания контактов; протирают изоляторы. Проверяют крепление силовых шунтов и токонесущих штанг, восстанавливают контрольную окраску мест их соединений.
– пневматическое оборудование на каждом ТР-1 производят ревизию одного компрессора со вскрытием и осмотром клапанных коробок. Осматривают и прочищают всасывающие фильтры, выполняют ревизию вспомогательного компрессора, ремонтируют, регулируют и испытывают предохранительные клапаны в соответствии с установленными сроками. Проверяют состояние обратных клапанов и переключающего клапана. Производят ревизию крана машиниста с проверкой состояния золотника, манжет уравнительного поршня, притирают клапан, заменяют смазку. Выполняют ревизию крана № 254 проверяют его регулировку и чувствительности, осматривают резиновые манжеты, заменяют смазку;
– осматривают тормозные цилиндры, не вскрывая их, проверяют плотность цилиндров, смазывают шток, проверяют работу ручного насоса. Производят ревизию золотниково-питательного клапана- проверяют работу тифонов и свистков, крепление главных резервуаров, холодильников и резервуаров управления.
– проверяют плотность тормозной и напорной магистралей, работу пневматического и тормозного оборудования.
Дата добавления: 2021-06-02; просмотров: 669; Мы поможем в написании вашей работы! |
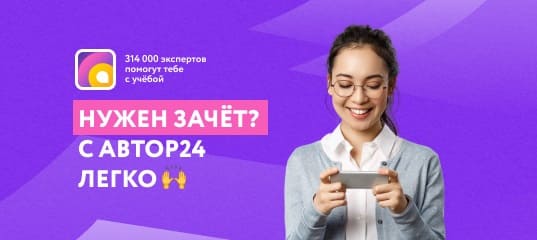
Мы поможем в написании ваших работ!