Пленочные интегральные микросхемы
Полупроводниковые диоды: виды и характеристики
Янв 8, 2015 | Основы электротехники
Для контроля направления электрического тока необходимо применять разные радио и электро детали. В частности, современная электроника использует с такой целью полупроводниковый диод, его применение обеспечивает ровный ток.
Устройство
Полупроводниковый электрический диод или диодный вентиль – это устройство, которое выполнено из полупроводниковых материалов (как правило, из кремния) и работает только с односторонним потоком заряженных частиц. Основным компонентом является кристаллическая часть, с p-n переходом, которая подключена к двум электрическими контактами. Трубки вакуумного диода имеют два электрода: пластину (анод) и нагретый катод.
Фото — полупроводниковый диод
Для создания полупроводниковых диодов используются германий и селен, как и более 100 лет назад. Их структура позволяет использовать детали для улучшения электронных схем, преобразования переменного и постоянного тока в однонаправленный пульсирующий и для совершенствования разных устройств. На схеме он выглядит так:
Фото — обозначение диода
Существуют разные виды полупроводниковых диодов, их классификация зависит от материала, принципа работы и области использования: стабилитроны, импульсные, сплавные, точечные, варикапы, лазер и прочие типы. Довольно часто используются аналоги мостов – это плоскостной и поликристаллический выпрямители. Их сообщение также производится при помощи двух контактов.
|
|
Основные преимущества полупроводникового диода:
1. Полная взаимозаменяемость;
2. Отличные пропускные параметры;
3. Доступность. Их можно купить в любом магазине электро-товаров или снять бесплатно со старых схем. Цена начинается от 50 рублей. В наших магазинах представлены как отечественные марки (КД102, КД103, и т. д.), так и зарубежные.
Маркировка
Маркировка полупроводникового диода представляет собой аббревиатуру от основных параметров устройства. Например, КД196В – кремниевый диод с напряжением пробоя до 0,3 В, напряжением 9,6, модель третьей разработки.
Исходя из этого:
1. Первая буква определяет материал, из которого изготовлен прибор;
2. Наименование устройства;
3. Цифра, определяющая назначение;
4. Напряжение прибора;
5. Число, которое определяет прочие параметры (зависит от типа детали).
Видео: применение диодов
Принцип работы
Полупроводниковые или выпрямительные диоды имеют довольно простой принцип работы. Как мы уже говорили, диод изготовлен из кремния таким образом, что один его конец p-типа, а другой конец типа n. Это означает, что оба контакта имеют различные характеристики. На одном наблюдается избыток электронов, в то время как другой имеет избыток отверстий. Естественно, в устройстве есть участок, в котором все электроны заполняют определенные пробелы. Это означает, что внешние заряды отсутствуют. В связи с тем, что эта область обедняется носителями заряда и известна как объединяющий участок.
|
|
Фото — принцип работы
Несмотря на то, что объединяющий участок очень мал, (часто его размер составляет несколько тысячных долей миллиметра), ток не может протекать в нем в обычном режиме. Если напряжение подается так, что площадь типа p становится положительной, а тип n, соответственно, отрицательной, отверстия переходят к отрицательному полюсу и помогают электронам перейти через объединяющий участок. Точно так же электроны движутся к положительному контакту и как бы обходят объединительный. Несмотря на то, что все частицы движутся с разным зарядом в разном направлении, в итоге они образуют однонаправленный ток, что помогает выпрямить сигнал и предупредить скачки напряжения на контактах диода.
Если напряжение прикладывается к полупроводниковому диоду в противоположном направлении, ток не будет проходить по нему. Причина заключается в том, что отверстия привлекаются отрицательным потенциалом, который находится в области р-типа. Аналогично электроны притягиваются к положительному потенциалу, который применяется к области n-типа. Это заставляет объединяющий участок увеличиваться в размере, из-за чего поток направленных частиц становится невозможным.
|
|
Фото — характеристики полупроводников
ВАХ-характеристики
Вольт амперная характеристика полупроводникового диода зависит от материала, из которого он изготовлен и некоторых параметров. Например, идеальный полупроводниковый выпрямитель или диод имеет следующие параметры:
1. Сопротивление при прямом подключении – 0 Ом;
2. Тепловой потенциал – VG = +-0,1 В.;
3. На прямом участке RD > rD, т. е. прямое сопротивление больше, чем дифференциальное.
Если все параметры соответствуют, то получается такой график:
Фото — ВАХ идеального диода
Такой диод использует цифровая электротехника, лазерная индустрия, также его применяют при разработке медицинского оборудования. Он необходим при высоких требованиях к логическим функциям. Примеры – лазерный диод, фотодиод.
На практике, эти параметры очень отличаются от реальных. Многие приборы просто не способны работать с такой высокой точностью, либо такие требования не нужны. Эквивалентная схема характеристики реального полупроводника демонстрирует, что у него есть серьезные недостатки:
|
|
Фото — ВАХ в реальном полупроводниковом диоде
Данная ВАХ полупроводникового диода говорит о том, что во время прямого включения, контакты должны достигнуть максимального напряжения. Тогда полупроводник откроется для пропуска электронных заряженных частиц. Эти свойства также демонстрируют, что ток будет протекать нормально и без перебоев. Но до момента достижения соответствия всех параметров, диод не проводит ток. При этом у кремниевого выпрямителя вольтаж варьируется в пределах 0,7, а у германиевого – 0,3 Вольт.
Работа прибора очень зависит от уровня максимального прямого тока, который может пройти через диод. На схеме он определяется ID_MAX. Прибора так устроен, что во время включения прямым путем, он может выдержать только электрический ток ограниченной силы. В противном случае, выпрямитель перегреется и перегорит, как самый обычный светодиод. Для контроля температуры используются разные виды устройств. Естественно, некоторые из них влияют на проводимость, но зато продлевают работоспособность диода.
Еще одним недостатком является то, что при пропуске переменного тока, диод не является идеальным изолирующим устройством. Он работает только в одном направлении, но всегда нужно учитывать ток утечки. Его формула зависит от остальных параметров используемого диода. Чаще всего схемы его обозначают, как IOP. Исследование независимых экспертов установило, что германиевые пропускают до 200 µА, а кремниевые до 30 µА. При этом многие импортные модели ограничиваются утечкой в 0.5 µА.
Фото — отечественные диоды
Все разновидности диодов поддаются напряжению пробой. Это свойство сети, которое характеризуется ограниченным напряжением. Любой стабилизирующий прибор должен его выдерживать (стабилитрон, транзистор, тиристор, диодный мост и конденсатор). Когда внешняя разница потенциалов контактов выпрямительного полупроводникового диода значительно выше ограниченного напряжения, то диод становится проводником, в одну секунду снижая сопротивление до минимума. Назначение устройства не позволяет ему делать такие резкие скачки, иначе это исказить ВАХ.
Транзисторы представляют собой полупроводниковые приборы с двумя или более р—«-переходами, позволяющие усиливать электрические сигналы и имеющие три и более выводов.
Транзисторы подразделяются на биполярные и униполярные {полевые) (рис. 2.33).
Биполярные транзисторы имеют трехслойную структуру с чередующимися типами электропроводности. Различают также прямые (р—п—р) и обратные (п—р—п) транзисторы (рис. 2.34). Каждый слой имеет вывод: эмиттер Э, базу (или основание) Б и коллектор К. Переход между базой и эмиттером называется эмиттер-ным, а между базой и коллектором — коллекторным.
В зависимости от общего электрода используются три схемы включения транзисторов: с общим эмиттером ОЭ (для обеспечения наибольшего усиления), с общей базой ОБ (для достижения наибольшей стабильности в работе) и с общим коллектором ОК (для обеспечения высокого входного и низкого выходного сопротивлений) (рис. 2.35).
Транзисторы предназначены для генерации, усиления и преобразования электрических сигналов. В импульсных схемах они работают в режиме «ключа», когда транзистор может находиться только в двух состояниях: включенном (открытом), либо выключенном (закрытом). Переход из одного состояния в другое происходит очень быстро, что отвечает основным требованиям большого быстродействия.
По конструкции полевые транзисторы различают с управляющим р—л-переходом и с изолированным затвором с встроенным или индуцированным каналом (рис. 2.36). У таких транзисторов электрод, от которого начинают движение основные носители заряда, называется истоком; электрод, к которому движутся основные носители заряда, — стоком, а электрод, к которому прикладывают управляющее напряжение, — затвором.
По материалу изготовления транзисторы бывают кремниевые или германиевые; по механизму движения носителей заряда — диффузионные, или дрейфовые.
Униполярные (биполярные) транзисторы могут быть маломощными СРтах< 0,3 Вт), средней мощности (от 0,3 до 1,2 Вт) и мощными (свыше 1,2 Вт). В зависимости от предельной частоты они бывают (рис. 2.37) низкочастотными (fm3X< 3 МГц), среднечастотными (3... 30 МГц), высокочастотными (от 30 до 300 МГц) и сверхвысокочастотными (свыше 300 МГц).
По функциональному назначению транзисторы в радиоэлектронных схемах разделяют на двухпереходные биполярные (усилительные, импульсные, малошумящие, высоковольтные, фототранзисторы) и полевые (униполярные) с каналом и управляющим затвором в виде р—л-перехода, с встроенным или индуцированным каналом и изолированным затвором.
Кроме того, транзисторы различают по мощности и частоте. В зависимости от максимальной мощности Рктах, рассеиваемой коллектором, различают транзисторы малой, средней и большой мощности, а по частоте — низкочастотные, среднечастотные, высокочастотные и сверхвысокочастотные.
В настоящее время используется система обозначения транзисторов, состоящая из четырех элементов.
Первый элемент— буква или цифра — обозначает материал транзистора (Г или 1 — германий или его соединения; К или 2 — кремний или его соединения; А или 3 — галлий или его соединения).
Второй элемент— буква — обозначает тип транзистора (Т — биполярные транзисторы; П — полевые транзисторы).
Третий элемент— цифра — указывает назначение и качественные свойства прибора (табл. 2.13), а также порядковый номер разработки.
Четвертый элемент— буква — обозначает разновидность типа прибора (деление на параметрические группы).
Так, например, КТ324А обозначает кремниевый маломощный высокочастотный транзистор, разновидность А; ГТ905Б — германиевый большой мощности высокочастотный транзистор, разновидность Б.
Таблица 2.13
Условное обозначение третьего элемента транзисторов
Частота транзистора, МГц | Обозначение третьего элемента при мощности рассеяния, Вт | ||
малой (до 0,3) | средней (от 0,3 до 1,5) | большой (более 1,5) | |
Низкая (до 3) Средняя (3...30) Высокая (30...300) Сверхвысокая (выше 300) | 101 ...199 201 ...299 301 ...399 | 401 ...499 501 ...599 601 ...699 | 701 ...799 801... 899 901 ...999 |
Система обозначения транзисторов, разработанных до 1964 г., состоит из трех элементов. Первый элемент — буква, обозначающая транзистор; второй элемент — число, указывающее назначение и качественные свойства (табл. 2.14), а также порядковый номер разработки транзистора; третий элемент — буква, обозначающая разновидность типа прибора.
Таблица 2.14
Условное обозначение второго элемента транзисторов, разработанных до 1964 г.
Частота транзистора, МГц | Обозначение второго элемента при мощности рассеяния, Вт | |||
германиевых | кремниевых | |||
до 0,25 (малая) | более 0,25 (большая) | до 0,25 (малая) | более 0,25 (большая) | |
Низкая (до 5) Высокая (более 5) | 1...99 401 ...499 | 201 ...299 601 ...699 | 101 ...199 501 ...599 | 301 ...399 701... 799 |
При монтаже транзисторов необходимо соблюдать следующие правила.
1. Крепление транзисторов должно производиться за корпус. Изгиб внешних выводов необходимо выполнять на расстоянии не ближе 10 мм от проходного изолятора (если нет других указаний). Изгиб жестких выводов мощных транзисторов запрещается.
2. Пайка выводов должна осуществляться на расстоянии не ближе 10 мм от корпуса прибора.
3. Мощность паяльника должна быть не более 60 Вт, время пайки—не более 3 с, а температура — не выше 200 °С.
4. В процессе монтажа необходимо исключить прохождение тока через транзисторы и обеспечить надежный теплоотвод.
5. Не допускается располагать транзисторы вблизи тепловыделяющих элементов (сетевых трансформаторов, мощных резисторов), а также в сильных электромагнитных полях.
При эксплуатации транзисторов требуется выполнять следующие правила.
1. Полярность напряжения внешнего источника питания, подключаемого к электродам транзистора, следует выбирать с учетом структуры транзистора и его рабочей схемы.
2. При подключении транзистора к источнику питания необходимо первым присоединять вывод базы, а последним — вывод коллектора. Отключение транзистора должно производиться в обратном порядке. Запрещаетсяподавать напряжение на транзистор с отключенной базой.
3. Для увеличения надежности и долговечности транзисторов рабочие напряжения, сила тока, мощность и рабочая температура должны быть меньше предельно допустимых (около 0,7 их значений).
4. Не разрешается использовать транзисторы на совмещенных предельных режимах (например, по току и напряжению).
5. С целью защиты транзисторов от перенапряжений в их схемы должны быть включены стабилизирующие, демпфирующие и ограничивающие диоды.
6. Запрещается проверка схем на полупроводниковых приборах омметрами или другими приборами, которые могут вызвать перегрузку диодов и транзисторов.
Пленочные интегральные микросхемы
Пленочная интегральная микросхема представляет собой схему, элементы которой образованы совокупностью пленок различных материалов, нанесенных на общее основание (подложку).
На практике широко применяются пленочные микросхемы, состоящие из резисторов, конденсаторов и соединительных проводников. Составные части пленочных микросхем (пленочные элементы) получают путем последовательного нанесения на подложку пленок из токопроводящих, магнитных, диэлектрических и других материалов.
Пленочные элементы имеют ряд преимуществ по сравнению с навесными объемными микроэлементами. Так, например, резисторы обладают малым уровнем шумов, большим удельным сопротивлением, конденсаторы — повышенной стабильностью, хорошим температурным коэффициентом. Метод напыления тонких пленок позволяет создавать не только функциональные микросхемы, но и полосковые СВЧ-элементы, электронно-управляемые переключатели мощности и различного рода ЛС-цепи с распределенными параметрами.
Свойства пленок во многом зависят от физических и химических свойств подложек. В качестве подложек используются специальные сорта стекла (С-41-1, С-48-3), высокоглиноземистая керамика (22ХС), ситалл (СТ-1, СТ-50-1) и бериллиевая керамика. Применяемые для изготовления микросхем подложки должны обеспечивать хорошие теплопроводность и механическую прочность при небольшой толщине, высокое удельное электрическое сопротивление (не менее 1014 Ом-см) и малую диэлектрическую проницаемость (не более 10... 15), физическую и химическую стойкость при высоких температурах и хорошую чистоту обрабатываемой поверхности (12... 14-й класс). Подложки могут быть квадратной или прямоугольной стандартной формы. Толщина подложек в зависимости от их размера составляет 0,6; 1 и 1,6 мм.
Комплекс работ, связанных с определением оптимальных геометрических размеров пленочных элементов микросхемы, их формы, методов соединения, а также последовательности нанесения слоев пленки на подложку, называется топологией.
В зависимости от топологии для изготовления микросхемы используются различного рода трафареты, выполняемые с помощью фотолитографии или электроискровым методом из медной фольги, никеля, стали и других материалов толщиной 0,07...0,15 мм. Трафареты накладывают на подложку, закрывая ту ее часть, которая не предназначена для напыления. Наиболее сложным процессом при нанесении пленочных элементов является совмещение трафаретов, так как для изготовления отдельных микросхем иногда требуется наложение до 15 трафаретов.
Пленки по толщине разделяют на толстые (несколько десятков микрон) и тонкие (единицы микрон).
Толстые пленки наносят на подложку методом шелкографии, вжигания и электрохимического осаждения. Достоинством толстопленочных микросхем является возможность применения для их изготовления простейшей технологии без использования дорогостоящего оборудования.
Тонкие пленки в отличие от толстых позволяют создавать пре„ цизионные пассивные элементы с параметрами более широкого диапазона, однако их производство требует больших затрат на специальное вакуумное оборудование. Нанесение тонких пленок осуществляется путем термического испарения в вакууме, распыления бомбардировкой ионами и химического осаждения (табл. 3.2).
Таблица 3.2
Способы получения тонких пленок и области их применения
Способ | Область применения | Примечание |
Термическое испарение в вакууме: резистивное; электровакуумной дугой; лазерным лучом; электронной бомбардировкой | Изготовление резисторов, конденсаторов, катушек индуктивности и электропроводников | Метод позволяет получить пленки большой чистоты и однородного состава, а также легко контролировать и регулировать как мощность нагревания, так и скорость напыления |
Распыление бомбардировкой ионами: катодное испарение; реактиное испарение; ионно-плазменное испарение | Изготовление резисторов, конденсаторов и проводников | Метод позволяет получить пленки, обладающие высокой адгезией |
Химическое осаждение | Получение пленок из серебра, платины, золота, радия и палладия |
Термическое испарение в вакууме основано на том принципе, что все вещества при температуре выше абсолютного нуля способны испаряться. Концентрация паров будет тем больше, чем выше температура материала. Для получения паров вещества нужной концентрации применяются специальные устройства — испарители. Наибольшее распространение получили испарители прямого и косвенного подогрева. В этих испарителях металл при нагревании сначала плавится, а затем испаряется. Пары металла используют для напыления пленочных элементов микросхемы.
Испарители прямого подогрева состоят из проволоки или ленты испаряемого металла, через которые пропускают электрический ток большой величины (до 106 А/см2). Испарители такого типа применяют при резистивном испарении и испарении электровакуумной дугой для напыления тугоплавких металлов при изготовлении резисторов и других элементов. Достоинствами испарителей прямого подогрева являются простота их конструкции и чистота испаряемого металла.
Испарители косвенного подогрева являются более универсальными. При их использовании необходимый для распыления металл подогревают в специальных подогревателях (тиглях), а затем испаряют при помощи электронной бомбардировки или лазерного луча.
Наиболее совершенным способом нагрева испаряемого металла является электронная бомбардировка. При этом способе испаряемый металл, являясь анодом электронной пушки, бомбардируется электронами и нагревается до температуры парообразования. Подложки для напыления вместе с трафаретами (рисунками микросхемы) располагают вокруг анода. Поскольку подложка имеет более низкую температуру, чем анод, пары металла анода конденсируются на подложке в виде пленки, образуя рисунок микросхемы.
Хорошие результаты по напылению однородных пленок обеспечивает испарение металла с помощью лазерного луча. Мощности лазерного луча достаточно, чтобы легко расплавить и превратить в газообразное состояние любые тугоплавкие металлы, причем сам лазерный источник может находиться вне стеклянного колпака вакуумной камеры.
Распыление бомбардировкой ионами.Широкое практическое применение получил способ катодного испарения. Он очень удобен для получения тонких пленок на подложках из материалов, чувствительных к нагреву (например, диэлектриков, изоляционных смол), так как напыление может осуществляться на холодную подложку. Этот способ основан на явлении тлеющего разряда в атмосфере аргона или водорода при понижении давления до 10"1 мм рт. ст. Между катодом, которым является распыляемый материал, и анодом помещают подложку. Если на анод приложить высокое по отношению к катоду напряжение (порядка нескольких киловольт), возникает тлеющий разряд и катод начинает испарять металл, который осаждается на подложке, находящейся у анода.
Метод химического осаждения, используемый для получения металлических пленок на подложке микросхемы, почти не отличается от методов получения гибких печатных плат.
Рассмотрим технологию изготовления тонкопленочных интегральных микросхем с помощью термического испарения металла в вакуумной камере (рис. 3.9), имеющего наиболее широкое практическое применение.
Вакуумная камера состоит из колпака /, под которым с помощью вакуумного 4 и диффузионного 5 насосов создается необходимое разрежение. Под колпак помещают распыляемое вещество 2 с нагревателем. Процесс получения пленки заключается в следующем.
На предварительно очищенные подложки в соответствии с топологией микросхем накладывают трафареты 7 и помещают их в
вакуумную камеру. Далее с помощью вакуумных насосов создается нужное для напыления разреженное давление, после чего начинается разогрев распыляемого материала. Продолжительность напыления пленки составляет от нескольких секунд до нескольких минут.
Наиболее легкими по выполнению компонентами тонкопленочных интегральных микросхем являются резисторы. Для получения резистивных пленок могут использоваться тантал, хром, вольфрам, титан, платина, нихром и другие металлы. Сопротивление резистора зависит от удельного сопротивления металла, формы и толщины пленки. Обычно пленки имеют толщину 200... 800А. Диапазон тонкопленочных резисторов составляет от единиц ом до единиц мегаом, мощность рассеяния резисторов — 1 Вт/см2 площади резистивной пленки. Чаще всего резисторы изготовляют путем вакуумного напыления пленки из сплава хрома и никеля на подложку при температуре 300 "С. Выводы резисторов обычно напыляют с использованием алюминия, меди или золота.
Тонкопленочные конденсаторы изготовляются путем нанесения двух слоев металла, разделенных слоем диэлектрика. Конденсаторы с большим числом обкладок практического применения не нашли из-за трудоемкости их изготовления. В качестве диэлектрика конденсатора используют в основном пленки из окиси титана или тантала. Пленка диэлектрика наносится методом катодного испарения в среде кислорода. В качестве диэлектрика могут использоваться также полимерные пленки. Для обкладок конденсатора чаще всего используется пленка из алюминия.
Электрические параметры наносимых элементов контролируются автоматически в процессе напыления. Контроль толщины пленки проводится с учетом изменения интенсивности отраженного света. Пленка 8 (см. рис. 3.9) в процессе напыления освещается источником света 3. Интенсивность отраженного света изменяется с ростом толщины пленки. Фотоэлемент 6 включен в цепь индикатора, по которому и определяется достаточность напыления, т. е. толщина пленки. Этот метод позволяет контролировать также толщину металлических, диэлектрических и других пленок, способных отражать источник света. Индикатор проградуирован в соответствующих единицах измерения (например, для измерения сопротивления резистивной пленки — ом или килоом).
Изготовление активных элементов (диодов, транзисторов) из пленок не получило практического применения из-за сложности выполнения и низких параметров. Поэтому для этой цели широко используются гибридные интегральные микросхемы.
Дата добавления: 2018-10-27; просмотров: 648; Мы поможем в написании вашей работы! |
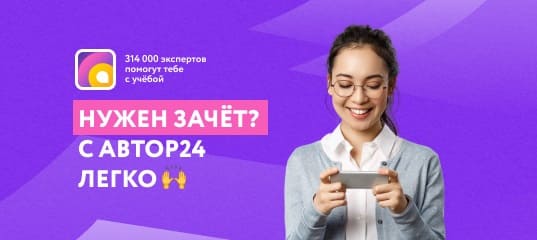
Мы поможем в написании ваших работ!