Подпись) (Ф.И.О.) (должность) (дата)
Nbsp;
ОПЕРАЦИОННАЯ ТЕХНОЛОГИЧЕСКАЯ КАРТА
Сборки и ручной дуговой сварки неповоротных стыков труб диаметром 1420 мм с толщиной стенки 15,7 мм
Характеристика объекта
Наименование монтажной организации | |
Наименование объекта | |
Тип объекта | Капитальный ремонт |
Рабочее давление по проекту | 7,5 МПа |
Вид прокладки трубопровода | Подземный |
Операционная технологическая карта сборки и ручной дуговой сварки электродами с основным видом покрытия неповоротных кольцевых стыковых сварных соединений труб | |||||||||||||||||||||||||||||
Организация | Наименование газопровода | Диаметр, толщина стенки, мм | Километраж | С посо б сварки | Конструктивные элементы сварных соединений | Шифр карты | |||||||||||||||||||||||
1420х15,7 | 1236,1-1262,5 | РД | Труба+труба | ||||||||||||||||||||||||||
Характеристика труб | Предварительный подогрев | Подготовка под сварку, сборка и параметры сварного шва | Сварочные материалы | ||||||||||||||||||||||||||
Номер ТУ | Диа-метр, мм | Толщина стенки, S ст , мм | Марка стали, (класс прочности) | Временное сопротивление разрыву, МПа, (кгс\мм2) | Эквивалент углерода, % | *Подогрев до температуры +100+30 ºС при температуре окружающего воздуха ниже +5 ºС и до +50+30 ºС при наличии влаги на концах труб (согласно таб.10.3 СТО 2-2.2-136-2007).
| Конструктивные размеры шва и форма разделки кромок на листе № 3 | *Прихватки и сварка первого (корневого) слоя шва: электроды типа Э50А марки LB-52U диаметром 2,6÷3,2 мм. *Сварка подварочного слоя шва: электроды типа Э50А марки *Сварка первого заполняющего слоя шва: электроды типа Э60 марки ОК 74.70 диаметром 3,2 мм. *Сварка последующих заполняющих слоев шва: электроды типа Э60 марки ОК74.70 диаметром 3,2÷ 4,0 мм. *Сварка облицовочного слоя шва: электроды типа Э60 марки ОК74.70 диаметром 3,2÷4,0 мм. *Ликвидация подрезов, ремонт забоин кромок: электроды типа Э60 марки ОК74.70 диаметром 3,2 мм. Допускается замена сварочных материалов того же типа, прошедших аттестацию по РД 03-613-03 и внесенных в реестр сварочных материалов ОАО «Газпром» | |||||||||||||||||||||
TУ 1381-016-00186654-2010 | 1420 | 15,7 | - (К60) | 590 (60) | 0,43 | ||||||||||||||||||||||||
TУ 1381-012-05757848-2005 | 1420 | 15,7 | - (К60) | 590 (60) | 0,43 | ||||||||||||||||||||||||
ТУ 14-156-77-2008 | 1420 | 15,7 | - (К60) | 590 (60) | 0,43 | ||||||||||||||||||||||||
ТУ 1381-003-47966425-2006 | 1420 | 15,7 | - (К60) | 590 (60) | 0,43 | ||||||||||||||||||||||||
ТУ 40/48/56/79+ Италия | 1420 | 15,7 | Х70 (К60) | 588.7 (60,0) | 0,41 | ||||||||||||||||||||||||
ТУ 2028404856-79 Германия | 1420 | 15,7 | Х70 (К60) | 588.7 (60,0) | 0,41 | ||||||||||||||||||||||||
Труба ТУ 40/48/56-79 Япония
| 1420 | 15,7 | Х70 (К60) | 588.4 (60,0) | 0,41 | ||||||||||||||||||||||||
Данные по ТУ на трубы приняты согласно сертификатам и «Инструкции по применению стальных труб в газовой и нефтяной промышленности». | |||||||||||||||||||||||||||||
Режимы сварки | Дополнительные требования к прокалке и хранению электродов | ||||||||||||||||||||||||||||
Слои сварного шва | Электроды | Диа- метр, мм | Темпера-тура прокалки, оС | Время прокал-ки, ч | Сварочный ток, А | ||||||||||||||||||||||||
Нижнее | Верти - кальное | Потолочное | |||||||||||||||||||||||||||
Тип | Марка | ||||||||||||||||||||||||||||
Прихватки и корневой слой шва | Э50А | LB-52U | 2,6 | 300 | 1,0 | 80-90 | 70-90 | 70-80 | Допускается прокаливать электроды не более пяти раз при общем времени прокалки не более 10 ч. После прокалки электроды должны храниться: - в термостатах (термопеналах), сушильных шкафах, прокалочных печах при температуре от +100 °С до +150°С; - в герметичных емкостях в сухих отапливаемых помещениях при температуре воздуха не ниже +15оС и относительной влажности не более 60% в течение не более 2-х суток; после истечения 2-х суток перед использованием электродов требуется повторная прокалка. | ||||||||||||||||||||
3,2 | 90-120 | 90-110 | 80-110 | ||||||||||||||||||||||||||
Подварочный слой шва | Э50А | LB-52U | 2,6
| 80-90 | 70-90 | 70-80 | |||||||||||||||||||||||
3,2 | 90-120 | 90-110 | 80-110 | ||||||||||||||||||||||||||
Первый заполняющий слой шва | Э60 | OK 74.70 | 3,2 | 350 | 2,0 | 90-120 | 90-110 | 80-110 | |||||||||||||||||||||
Последующие заполняющие слои шва | Э60 | OK 74.70 | 3,2 | 100-120 | 90-110 | 80-110 | |||||||||||||||||||||||
4,0 | 130-180 | 110-170 | 110-150 | ||||||||||||||||||||||||||
Облицовочный слой шва | Э60 | OK 74.70 | 3,2 | 100-120 | 90-110 | 80-110 | |||||||||||||||||||||||
4,0 | 130-180 | 110-170 | 110-150 | ||||||||||||||||||||||||||
Ликвидация подрезов, ремонт забоин кромок | Э60 | OK 74.70 | 3,2 | 100-120 | 90-110 | 80-110 | |||||||||||||||||||||||
| |||||||||||||||||||||||||||||
Конструктивные размеры стыка и форма шва
(толщина стенки труб 15,7 мм)
Дополнительные требования и рекомендации |
1. Допустимая минимальная толщина стенки труб - 14,9 мм. 2. Направление сварки всех слоев шва – «на подъем». 3. Сварка каждого слоя шва выполняется одновременно не менее чем 2-мя сварщиками на постоянном токе обратной полярности. 4. Освобождать стягивающие механизмы центраторов после выполнения не менее 2 700 мм (60% периметра) корневого слоя шва. 5. Температура на кромках труб перед сваркой корневого слоя шва (выполнением прихваток) должна быть не ниже +100+30оС при температуре окружающего воздуха ниже +5 оС и не ниже +50+30оС при наличии влаги на концах труб. 6. Температура предыдущего слоя сварного шва перед наложением последующего слоя должна быть в интервале от +50ºС до +250ºС. Если температура опустилась ниже +50ºС, следует произвести сопутствующий (межслойный) подогрев до температуры +100+30оС. 7. Сварка короткой дугой - длина дуги 0,5÷1,0 диаметра электрода (стержня). 8. Сварку следует выполнять за один цикл без перерывов до полного завершения работ. 9. Не допускается оставлять сварное соединение незаконченным. |
|
|
10. Процесс сварки следует начинать и заканчивать на расстоянии не менее 100 мм от заводских продольных швов труб. 11. При проведении работ не должна нарушаться целостность изоляции. 12. Запрещается приваривать крепежные элементы обратного кабеля к телу труб. 13. Присоединение обратного кабеля к телу труб следует выполнять с помощью специальных контактных устройств, исключающих искрообразование. 14. Запрещается производить любые виды работ, связанные с возможным перемещением труб, до полного окончания сварки сварных соединений. 15. Сварочное оборудование, сварочные материалы и сварочные технологии должны быть аттестованы. 16. Сварочные электроды проверены на наличие акта входного контроля, сертификата на конкретную партию, марку и соответствие маркировки и условных обозначений электродов в сертификате и на этикетках упаковки. 17. Допуск сварщиков к выполнению сварочных работ осуществляется после допускных испытаний и оформления допускных листов в соответствии с СТО Газпром 2-2.2-136-2007. |
Перечень и последовательность операций при выполнении работ | |||
№ п/п | Операция | Содержание операций | Оборудование и инструмент |
1. | Очистка труб | · Очистить наружную поверхность и всю внутреннюю полость труб от возможных загрязнений (снег, лёд, грунт и др.). | Скребок, лопата, щетка, газовая горелка |
1.1 | Контроль очистки внутренней полости труб и их наружной поверхности | · Руководителю сварочных работ, имеющему не ниже II -го уровня профессиональной подготовки специалиста сварочного производства: - произвести осмотр полости труб; - проверить очистку наружной поверхности торцов труб от налипания грунта, снега, льда, остатков изоляционного покрытия. · При наличии загрязнений повторно произвести операцию очистки. | Фонарик |
2. | Подготовка к сборке | · Осмотреть кромки и поверхности снаружи и изнутри труб на предмет отсутствия трещин и расслоений. · Дефекты наружной поверхности тела труб механического происхождения (риски, продиры, царапины) устранить механическим способом шлифмашинкой, при этом толщина стенки труб не должна выходить за пределы минусового допуска, равного минус 0,8 мм (согласно ТУ), что должно быть подтверждено результатами проведенной ультразвуковой толщинометрии. · Шероховатость поверхности после шлифовки должна быть не более RZ40. · Свариваемые кромки труб с забоинами до 5,0 мм включительно отремонтировать сваркой электродами с основным видом покрытия типа Э60 марки ОК 74.70 диаметром 3,2 мм (тип электродов должен соответствовать классу прочности основного металла труб) на постоянном токе обратной полярности с обязательным предварительным подогревом дефектного участка до температуры +100+30оС независимо от температуры окружающего воздуха. · Зачистить отремонтированные поверхности кромок труб шлифованием, при этом должна быть восстановлена первоначальная форма разделки кромок. · Плавные вмятины на концах труб глубиной до 49 мм (3,5% от диаметра) включительно, а также овальность концов труб до 14 мм (1% от диаметра) устранить с помощью безударных разжимных устройств (калибраторов) с обязательным местным подогревом независимо от температуры окружающего воздуха до температуры от +150оС до +200оС. · Правка концов труб ударным инструментом запрещена. · После правки плавных вмятин, с целью выявления возможных расслоений, выполнить ультразвуковой контроль поверхности трубы в границах, превышающих размеры вмятин на величину не менее 40 мм. · Концы труб с рисками, задирами, царапинами глубиной более минусового допуска на толщину стенки; с забоинами более 5,0 мм, любыми вмятинами глубиной более 49 мм должны быть обрезаны. После резки выполнить ультразвуковой контроль поверхности трубы по всему периметру на ширине не менее 40 мм от торцов трубы. · При наличии расслоений отрезать «катушку» длинной не менее 300 мм от торца трубы и произвести ультразвуковой контроль в аналогичном порядке. | Машина для кислородной резки «Комета», шаблон сварщика УШС-3, линейка, штангенциркуль, шлифмашинка, шлифкруги, дисковые щетки, источник сварочного тока DCW 400ESW, DCW 480ESW, УЗК дефектоскоп "СКАРУЧ" |
2. | Подготовка к сборке | · Данные по ультразвуковому контролю резаных торцов труб зафиксировать в журнале контроля сварных соединений неразрушающими методами по данному объекту. · Косина реза торцов труб должна быть не более 2,0 мм, угол разделки кромок 30о-5. Контроль параметров разделки кромок выполняется при помощи измерительных инструментов. · После вырезки дефектных участков, а также во всех случаях резки труб (в том числе изготовлении «катушек») с целью выявления возможных расслоений произвести ультразвуковой контроль по всему периметру на ширине не менее 40 мм от торцов трубы. · Перенести с внутренней на наружную поверхность труб на расстоянии 100÷150 мм от торцов маркером (несмываемой краской) номера труб в соответствии с сертификатами и зафиксировать эти данные в сварочном журнале по данному объекту. · Произвести сошлифовку механическим способом шлифмашинкой резаных торцов труб на глубину не менее 0,5÷1,0 мм; выполнить притупление 1,8±0,8 мм. · Сошлифовать внутреннее усиление заводских швов заподлицо с внутренней поверхностью труб на расстоянии 10÷15 мм. · Наружное усиление заводских швов удалить механическим способом (шлифованием) до остаточной величины от 0,5 до 1,0 мм на расстоянии от 10 до 15 мм от торца труб, обеспечивая плавный переход от металла шва к основному металлу. · Зачистить до чистого металла свариваемые кромки и прилегающие к кромкам внутреннюю и наружную поверхности труб на ширину не менее 15 мм. | разжимное приспособление, газовая горелка, термометр ТК-5.06, термокарандаш |
2.1 | Контроль под-готовки кромок труб к сборке | · Руководителю сварочных работ, имеющему не ниже II -го уровня профессиональной подготовки специалиста сварочного производства, проверить геометрические параметры и качество зачистки свариваемых кромок труб перед сборкой согласно требованиям п.2 данной тех. карты - «Подготовка к сборке». | Набор для проведения ВИК. |
3. | Сборка стыков | · Произвести сборку стыка при помощи наружного звенного центратора. · Центратор не должен оставлять недопустимых дефектов (риски, царапины и др.) на поверхности тела труб. · Величина смещения кромок на должна превышать 3,0 мм (20% от толщины стенки, но не более 3,0 мм). Общая протяжённость участков со смещением должна быть не более 1/6 (743 мм) периметра свариваемого соединения. · Величина зазора должна составлять при сварке первого (корневого) слоя шва электродами диаметром: -2,6 мм -2,0÷3,0 мм; -3,2 мм - 2,5÷3,5 мм. · Заводские продольные швы труб должны быть смещены не менее чем на 100 мм и располагаться по возможности в верхней половине периметра сварного соединения. · При технической невозможности смещения заводских швов расстояние между швами согласовать с органами технического надзора Заказчика. · Определить исходную величину и направление магнитного поля по периметру соединения в восьми контрольных точках перед выполнением прихваток. · Для снижения влияния магнитного дутья и улучшения стабильности горения дуги при остаточной намагниченности трубопроводов до 20 Гс необходимо: -провести симметричное заземление труб; -обеспечить каждый пост сварки отдельным обратным кабелем с минимальным расстоянием между местом крепления обратного кабеля и местом сварки; -располагать сварочные кабели параллельно свариваемым кромкам; -не допускать контакта электрододержателя или оголенного сварочного кабеля с поверхностью газопровода; -производить сварку в направлении крепления обратного кабеля, наклон электрода при сварке должен быть в сторону, противоположную отклонению сварочной дуги. · При остаточной величине магнитного поля более 20 Гс провести циклическое перемагничивание установкой ЛАБС-7К2. При необходимости для снижения остаточной намагниченности использовать П-образные постоянные магниты. Для этого установить магниты на участок сварного соединения, подлежащий размагничиванию, при этом сварное соединение должно | наружный центратор типа Ж08А7985, шлифмашинка, шлифкруги, дисковые щетки, металлическая щетка, шаблон сварщика УШС-3, индикатор магнитного поля НВ-1200Б, установка размагничивания типа ЛАБС-7К2, комплект |
3. | Сборка стыков | · располагаться между полюсами магнитов, а полюса магнитов должны быть противоположны полюсам намагниченных труб. · Проверить индикатором магнитного поля правильность установки магнитов. · Для уменьшения величины магнитного поля необходимо переместить магниты по поверхности труб на некоторое расстояние от места размагничивания, для увеличения величины магнитного поля магниты следует приблизить к месту размагничивания. | П-образных магнитов, линейка |
4. | Условия предварительного и сопутствующего (меж- слойного) подогрева. | · Произвести предварительный подогрев до температуры 100+30 ºС при температуре окружающего воздуха ниже +5 ºС и/или до +50+30 ºС при наличии влаги на концах труб. · Оборудование для предварительного подогрева должно обеспечивать равномерный прогрев свариваемых соединений по толщине стенки и периметру в зоне шириной не менее 150 мм (т.е. не менее 75 мм в каждую сторону от свариваемых кромок) и, если необходимо, подогрев в процессе выполнения прихваток и межслойный подогрев в процессе сварки. · Максимальная температура нагрева в месте начала заводского изоляционного покрытия не должна превышать +100 ºС. · При выполнении предварительного подогрева не должна нарушаться целостность изоляционного покрытия труб. · При применении газопламенных нагревательных устройств (горелок) применять термоизоляционные материалы (термоизолирующие пояса) и/или боковые ограничители пламени. | газопламенный подогреватель (Кольцо), термоизолирующие пояса, боковые ограничители пламени |
4.1 | Контроль температуры предварительного и сопутствующего (межслойного) подогрева | · Контроль температуры предварительного подогрева свариваемых соединений выполнять непосредственно перед выполнением прихваток, первого (корневого) слоя шва на наружной поверхности в местах, равномерно расположенных по периметру, на расстоянии от 10 до 15 мм в обе стороны от свариваемых кромок. · Количество мест контроля температуры подогрева назначается по количеству прихваток (4 прихватки). · Контроль межслойной температуры в процессе сварки производить непосредственно перед наложением последующего слоя шва. · Максимальная температура нагрева трубы в месте начала заводского изоляционного покрытия не должна превышать +100оС. | Термометр ТК-5.06, термокарандаш |
5. | Прихватки и сварка | · Работы по сборке и сварке выполнять под непосредственным руководством мастера (прораба), имеющего не ниже II-го уровня профессиональной подготовки специалиста сварочного производства в соответствии с ПБ 03-273-99. Он же осуществляет пооперационный контроль качества выполненных слоев сварных швов. · К сварке должны быть допущены сварщики, прошедшие аттестацию в соответствии с «Правилами аттестации сварщиков и специалистов сварочного производства» (ПБ 03-273-99) и имеющие удостоверение установленного образца с допуском к сварке МГ, согласно СТО Газпром 2-2.2-136-2007. · При скорости ветра более 10 м/сек и/или выпадении осадков использовать инвентарное укрытие. · По окончании сборки выполнить предварительный подогрев стыка до +100+30оС независимо от температуры окружающего воздуха. · Выполнить прихватки стыка электродами типа Э50А марки LB-52U диаметром 2,6÷3,2 мм. Прихватки выполнять на тех же режимах, что и для сварки корневого слоя шва. · Возбуждать дугу при сварке следует только с поверхности разделки кромок свариваемых элементов. Не допускается зажигать дугу на поверхности металла труб. · Прихватки выполняются не ближе 100 мм от продольного шва трубы. К качеству прихваток предъявляются такие же требования, как и к корневому слою шва. Количество прихваток – 4 шт, длина прихватки – 100÷200 мм. · Начальный и конечный участки каждой прихватки обработать шлифмашинкой для обеспечения плавного перехода при сварке первого (корневого) слоя шва.*Замерить температуру сварного соединения и, при необходимости, выполнить предварительный подогрев до +100+30ºС независимо от температуры окружающего воздуха. · Выполнить ручную дуговую сварку корневого слоя шва сварного соединения электродами типа Э50А марки LB-52U диаметром 2,6÷3,2 мм на режимах согласно разделу «Режимы сварки».Участки корневого слоя шва следует равномерно распределять по периметру стыка, начало и конец каждого участка должны быть обработаны механическим способом шлифмашинкой и иметь плавный переход для сварки оставшейся части корневого слоя шва. · Снять центратор, замерить температуру сварного соединения и, при необходимости, выполнить предварительный подогрев до +100+30 ºС независимо от температуры окружающего воздуха и закончить сварку оставшейся части корневого слоя шва. | газопламенный подогреватель (Кольцо), термоизолирующие пояса, боковые ограничители пламени, |
5. | Прихватки и сварка | · Обработать механическим способом корневой слой шва. · Осуществить визуальный контроль корневого слоя шва. · Дефектные участки в корневом слое шва исправлять до сварки заполняющих слоев! · В процессе сварки каждый слой и свариваемые кромки, а также после завершения сварки облицовочный слой и прилегающие к нему поверхности труб на расстоянии 10 мм должны быть зачищены от шлака и брызг наплавленного металла шлифмашинкой. · Замерить температуру сварного соединения и, при необходимости, выполнить сопутствующий (межслойный) подогрев до +100+30ºС независимо от температуры окружающего воздуха. · Выполнить подварку изнутри трубы в нижней четверти периметра сварного соединения и в местах видимых дефектов способом «на подъем» электродами типа Э50А марки LB-52U диаметром 2,6÷3,2 мм, соблюдая требования правил охраны труда. · Подварочный слой выполняется перед заполняющим и должен иметь ширину 8÷10 мм и высоту усиления 1÷3 мм. · Обработать механическим способом подварочный слой шва. · Осуществить визуальный контроль подварочного слоя шва. · Замерить температуру сварного соединения и, при необходимости, выполнить сопутствующий (межслойный) подогрев до +100+30ºС независимо от температуры окружающего воздуха. · Выполнить сварку первого заполняющего слоя шва сварного соединения электродами с основным видом покрытия типа Э60 марки ОК 74.70 диаметром 3,2 мм. · Замерить температуру сварного соединения и, при необходимости, выполнить сопутствующий (межслойный) подогрев до +100+30 ºС независимо от температуры окружающего воздуха. · Выполнить сварку последующих заполняющих и облицовочного слоев шва сварного соединения электродами типа Э60 марки ОК 74.70 диаметром 3,2÷4,0 мм на режимах согласно разделу «Режимы сварки». · Сварка должна выполняться непрерывно за один цикл без перерывов до полного завершения работ. · Не допускается применять присадки, подаваемые в зону сварки или закладываемые в разделку. · Сварка производиться со смещением «замков» на каждом последующем слое по отношению к предыдущему на 30 мм начало и на 70 мм место окончания сварки слоя, кроме того «замки» должны быть удалены от заводских сварных стыков труб не менее чем на 100 мм. · Облицовочный слой шва должен перекрывать основной металл на 2,5-3,0 мм в каждую сторону от разделки кромок и иметь усиление 1-3 мм и ширину шва согласно эскизу (в зависимости от разделки кромок). · Минимальное допустимое число слоев шва – 5. · По окончании сварки сварное соединение накрыть сухим влагонепроницаемым теплоизолирующим поясом до полного остывания. · После полного остывания сварного стыка обработать механическим способом (абразивным кругом) участки поверхности облицовочного слоя шва с чешуйчатостью, при которой превышение гребня над впадиной составляет более 1,0 мм, участки с превышением усиления шва более 3 мм, а также при отсутствии плавного перехода от усиления к основному металлу. · Провести внешний осмотр сварного шва. · Исправить обнаруженные наружные дефекты, подрезы глубиной более 0,5 мм устранить наплавкой ниточных валиков. · Температура сварного соединения пред ремонтом обнаруженных наружных дефектов облицовочного слоя шва, а также наплавкой ниточных валиков должна быть не ниже +100+30ºС независимо от температуры окружающего воздуха. · Валики наплавляются электродами с основным видом покрытия типа Э60 марки ОК 74.70 диаметром 3,2 мм на режимах раздела «Режимы сварки» на постоянном токе обратной полярности методом «на подъем» после зачистки места дефекта абразивным инструментом. | источники сварочного тока DCW 400ESW, DCW 480ESW, шлифмашинка, шлифкруги, дисковые щетки, металлическая щетка, термометр ТК-5.06, установка размагничивания типа ЛАБС-7К2, комплект П-образных магнитов, термокарандаш, шаблон сварщика УШС |
6. | Клеймение | · Нанести клейма сварщиков (клеймо бригады), на расстоянии 100÷150 мм от шва в верхней полуокружности трубы несмываемой краской, маркером, термокарандашом. | Кисть, краска, маркер, термокарандаш. |
7. | Контроль качества | · В процессе сварки осуществлять пооперационный контроль качества выполнения слоев шва. · По окончании сварки произвести визуальный и измерительный контроль в объеме 100% периметра сварного соединения. · Облицовочный слой должен иметь плавные переходы к основному металлу, не иметь подрезов глубже 0,5 мм, а также наплывов. · Наружные поры, свищи и не заваренные кратеры не допускаются. · Выполнить контроль качества сварных соединений неразрушающими методами в соответствии с проектом, СТО Газпром 2-2.4-083-2006 и «Временными требованиями...» · Произвести испытания согласно проектных решений. | Набор для ВИК, шаблон сварщика УШС-3; РПД-200; УЗК дефектоскоп "СКАРУЧ". |
Данная технологическая карта составлена на основании СТО Газпром 2-2.4-083-2006; СП 86.13330.2012; ГОСТ 16037-80; СТО Газпром 2-2.2-136-2007, «Временные требования к организации сварочно-монтажных работ, применяемым технологиям сварки, неразрушающему контролю качества сварных соединений и оснащенности подрядных организаций при строительстве, реконструкции и капитальном ремонте магистральных газопроводов ОАО «Газпром» | |||||||||||||||
| Карта разработана: | Инженер по сварке | Дата: | « | . » | 2015 г. | |||||||||
|
| должность | подпись | ФИО | |||||||||||
|
| ||||||||||||||
С содержанием карты ознакомлены:
№№ | Ф.И.О. | Подпись | №№ | Ф.И.О. | Подпись | №№ | Ф.И.О. | Подпись |
1 | 5 | 9 | ||||||
2 | 6 | 10 | ||||||
3 | 7 | 11 | ||||||
4 | 8 | 12 |
Руководитель работ ____________________ __________________________ __________________________ __________________
подпись) (Ф.И.О.) (должность) (дата)
Дата добавления: 2018-10-27; просмотров: 771; Мы поможем в написании вашей работы! |
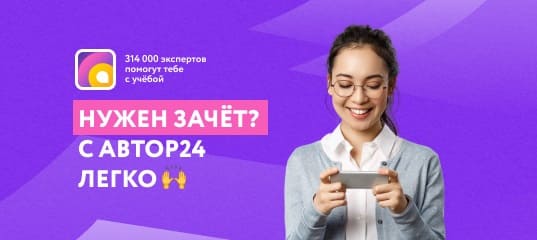
Мы поможем в написании ваших работ!