Критерий работоспособности шлицевых соединений. Метод расчета шлицевых соединений.
Шпоночные соединения. Достоинства и недостатки, область применения. Типы призматических шпонок, способы изготовления шпоночных пазов.
Шпоночные соединения применяют для передачи вращающего момента между валом и ступицей (например, ступицей зубчатого колеса, шкива, маховика и т. п.) с помощью специальной детали — шпонки. Шпоночные соединения подразделяют на ненапряженные, осуществляемые призматическими или сегментными шпонками, и напряженные, осуществляемые клиновыми шпонками.
Достоинства соединений: простота конструкции и низкая стоимость.
Недостатки: вал и ступица ослаблены шпоночными пазами, в зоне которых возникает концентрация напряжений, что снижает усталостную прочность деталей соединений; трудно обеспечить взаимозаменяемость соединения из-за необходимости ручной подгонки шпонки по пазу; ненадежная работа соединения при ударных, реверсивных и циклических нагрузках.
Ширину b и высоту h обыкновенных призматических шпонок выбирают в зависимости от посадочного диаметра вала. Концы шпонок могут быть плоскими или скругленными. Глубина врезания шпонки в ступицу k ~ 0,4h. Призматические шпонки вставляют в паз вала по посадке с натягом, а в паз ступицы по посадке с зазором.
В валу паз изготовляется пальцевой фрезой при единичном или мелкосерийном производстве, а при крупносерийном или массовом дисковой фрезой. Паз в ступице выполняется протяжкой или долбяком.
|
|
Соединения призматическими шпонками: расчет и конструкция.
Шпонки обычно подбирают по диаметру вала, т.к. шпонки стандартизованы.
В расчетах принимают, что шпонка нагружена силой от момента и по этой силе выполняют расчеты. Глубина врезания паза в вале такова, что рассчитывать надо только выступающую часть шпонки. Если шпонка выбирается по стандарту, то она рассчитывается только на смятие.
, lр – рабочая длина шпонки.
, где S – коэффициент безопасности.
Если по каким то причинам шпонку не удалось выбрать по стандарту, ее еще считают на срез: .
Соединения сегментными шпонками: конструкция и расчет.
Сегментная шпонка является разновидностью призматической шпонки, так как принцип работы этой шпонки подобен принципу работы призматической шпонки. Конструкция соединения с помощью сегментной шпонки показана на рис. Глубокая посадка шпонки обеспечивает ей более устойчивое положение, чем у простой призматической шпонки. Однако глубокий паз значительно ослабляет вал, поэтому сегментные шпонки применяют главным образом для закрепления деталей на малонагруженных участках валах, например на концах валов. Аналогично соединению с призматической шпонкой для сегментной шпонки получим
|
|
При длинных ступицах можно ставить в ряд по оси вала две сегментные шпонки.
Бывает, что такие шпонки считают еще и на срез .
Шлицевые соединения. Назначение и типы шлицевых (зубчатых) соединений, их сравнительная оценка. Область применения. Способы центрирования деталей шлицевых соединений, обоснование выбора способа центрирования.
Шлицевые соединения валов со ступицами (зубчатых колес, шкивов и т. п.) применяют для передачи вращающего момента. На валу изготовляют выступы (зубья), входящие во впадины (шлицы) ступицы.
Достоинства шлицевых соединений: высокая несущая способность благодаря значительно большей рабочей поверхности шлицев; высокая усталостная прочность вала вследствие незначительной концентрации напряжений; возможность применения точных и производительных методов обработки шлицев в ступицах (протягиванием) и зубьев на валах (фрезерованием червячными фрезами, шлифованием, как при нарезании зубьев зубчатых колес). Этим достигается высокая точность центрирования шлицевых соединений.
Недостатки: высокая стоимость соединений из-за сложности технологического оборудования (зубофрезерные, протяжные и шлифовальные станки); изготовление шлицевых соединений становится экономически целесообразным лишь при крупносерийном и серийном производствах.
|
|
Различают шлицевые соединения неподвижные и подвижные с возможностью перемещения деталей вдоль оси под нагрузкой или без нагрузки. (Например, шлицевые соединения сверлильных шпинделей станков, карданных валов автомобилей и др.) Шлицевые (зубчатые) соединения стандартизованы. При данном диаметре соединения стандартами установлено число и размеры шлицев (зубьев), а также допуски на их размеры.
В машиностроении применяют прямобочные, эвольвентные и треугольные шлицы.
В настоящее время наиболее распространены давно применяемые прямобочные шлицевые соединения (около 80%) по ГОСТу 1139-80. В поперечном сечении профиль прямобочных шлицев очерчивается окружностью выступов зубьев D, окружностью впадин d, и прямыми, определяющими постоянную толщину зубьев b. Стандартом предусмотрены три серии соединений: легкая, средняя и тяжелая. С переходом от легкой к средней и тяжелой сериям при одном и том же внутреннем диаметре d, увеличивают наружный диаметр D и число зубьев z, что повышает несущую способность соединений. Соединения с прямобочными шлицами выполняют с центрированием по наружному диаметру D, по внутреннему диаметру d, и по боковым граням b.
|
|
При выборе способа центрирования руководствуются величиной и характером нагрузки на соединение, требованиями по точности центрирования деталей соединения. Несущую способность шлицевых соединений и износостойкость шлицев можно значительно увеличить повышением твердости рабочей поверхности (боковых граней) шлицев путем закалки их до высокой твердости. Однако после закалки происходит искажение сопрягаемых поверхностей, которое можно устранить лишь последующим шлифованием, которое не всегда можно выполнить. Наружное шлифование шлицевых валов по диаметру D выполняется легко; сложнее шлифовать отверстия в ступицах по диаметру d и боковые грани зубьев шлицевых валов; невозможно шлифовать боковые грани шлицев и впадины между шлицами по диаметру D у ступиц.
Наиболее надежным (но и более сложным в изготовлении) является соединение, в котором вал и ступица закалены до высокой твердости после нарезки зубьев. В этом случае для получения необходимой точности сопряжения ступицу и вал центрируют по диаметру d. Менее надежным, но и более простым в изготовлении является соединение, в котором отверстие ступицы не закалено и поэтому может быть окончательно получено протягиванием, а вал с предварительно нарезанными зубьями закаливается и шлифуется по наружному диаметру D. В этом случае центрирование осуществляют по D. И, наконец, самое простое в изготовлении, но и менее надежное центрирование по боковым поверхностям зубьев применяют в тихоходных механизмах при больших вращающих моментах. Вал и ступица в этом случае не закалены и зубья на них окончательно нарезают (протягивают) без шлифования.
Более перспективны соединения с эвольвентными зубьями (шлицами). Их выполняют с центрированием по боковым, рабочим поверхностям или по наружному диаметру; наиболее распространен первый способ центрирования из-за простоты его получения. Профиль эвольвентных шлицев очерчивается, как и профиль зубьев эвольвентных зубчатых колес, окружностью вершин, окружностью впадин и эвольвентами с углом зацепления 30° (у зубчатых колес 20°) при уменьшенной высоте зуба h = m (у зубчатых колес h = 2,25m). Размеры эвольвентных шлицев определяются по ГОСТу 6033-88.
Достоинства эвольвентных шлицевых соединений по сравнению с прямобочными: выше прочность на изгиб благодаря утолщению зубьев у основания; меньше концентрация напряжений, поэтому выше сопротивление усталости; выше прочность на смятие благодаря увеличенному числу зубьев; при производстве требуется меньшая номенклатура фрез, так как эвольвентные шлицы одинакового модуля можно нарезать одной фрезой или долбяком, в то время как при изготовлении прямобочных шлицев для каждого размера и числа зубьев требуется отдельная фреза; при обработке зубьев (шлицев) могут быть использованы совершенные технологические процессы, применяемые для изготовления зубьев зубчатых колес.
Недостатки: более дорогие эвольвентные протяжки для малых диаметров ступиц, шлифование эвольвентных шлицев более сложно, чем прямобочных.
Шлицевые соединения треугольного профиля применяют редко при стесненных габаритах в радиальном направлении. Эти соединения центрируют по боковым сторонам зубьев. Размеры шлицев треугольного профиля установлены отраслевыми стандартами (ОСТ) и нормалями. В основном их применяют в кинематических (приборных) механизмах. При необходимости беззазорного соединения применяют конические соединения треугольного профиля с конусностью 1 : 16 на валу.
Критерий работоспособности шлицевых соединений. Метод расчета шлицевых соединений.
Критерии: 1) смятие 2) износ 3) возможен срез зубьев
Основными видами отказов шлицевых соединений являются смятие и износ рабочих поверхностей. Износ является следствием работы сил трения при взаимных микроперемещениях контактирующих поверхностей в процессе работы. Особенно большой износ в шлицевых соединениях наблюдается при скудной загрязненной смазке, больших напряжениях смятия. Износостойкость соединения повышают с помощью увеличения твердости контактирующих поверхностей закалкой, уменьшения зазоров между зубьями, а также применяя смазочный материал и хорошее уплотнение от загрязнения.
Расчет шлицевых соединений ведется по двум критериям: 1) смятие (если только присутствует вращающий момент) 2) износостойкость (если еще изгибающий момент и радиальные силы).
Упрощенный расчет на смятие:
где kPH – коэффициент, учитывающий неравномерность распределения нагрузки между зубьями из-за ошибок изготовления, h – рабочая высота зубьев, l – рабочая длина зубьев.
Для прямобочного профиля:
где f – величина фаски.
Дата добавления: 2018-10-26; просмотров: 533; Мы поможем в написании вашей работы! |
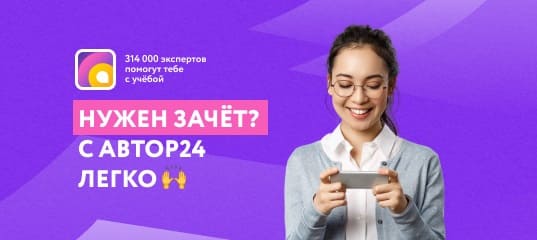
Мы поможем в написании ваших работ!