III. Определяем толщину определяемого металла с учетом припуска на черновое обтачивание.
Nbsp;
Технологическая часть
Для определения оптимальной величины производственной партии деталей существующих
несколько формул, предложенных разными авторами.
В стадии проектирования технологических процессов величину производственной партии
деталей можно определить ориентировочно по следующей формуле:
где N - производственная программа изделий в год;
n - число деталей в изделии;
t - необходимый запас деталей в днях для обеспечения непрерывной сборки;
t - 2-3 дня – для крупных деталей, хранение которых возможно на одноярусных
стеллажах, подставках, лагах ( например, рамы, кузова и кабины а/м, балки мостов,
крупные корпусные детали и т. д.).
t =5 дней – для средних деталей, хранение которых возможно на многоярусных
стеллажах;
t = 10-30 дней – для мелких деталей, хранение которых возможно в контейнерах
и другой таре;
Фдн=253 – число рабочих дней в году.
Разработка технологического процесса
Восстановления детали.
Исходные данные при разработке технологического процесса восстановления деталей.
а). Характеристика детали и условий ее работы.
1). Класс детали – прямые круглые стержни и стержни фасонной поверхностью;
2). Материал – сталь 25XГМ ( X – хром 1%; Г – марганец 1%; М – молибден 1 %);
3). Твердость – 61…66 HRC3;
4). Базовая поверхность – центровые отверстия или наружные цилиндрические поверхности;
|
|
5). Характер повреждений – механические;
6). Характер нагрузок – периодический и динамический;
7). Характер деформаций - износ, скручиваний, изгиб;
б). Выбор способов восстановления деталей:
1). Износ шлицев по толщине.
а). Метод наплавки вибродуговой;
б). Метод напыления;
в). Метод пластического деформирования;
2). Износ отверстия под роликовый подшипник.
а). Гальваника;
б). Наплавка вибродуговая;
в). Напыления;
3). Износ шеек под передний подшипник.
а). Наплавка вибродуговая;
б). Напыление;
в). Гальваника.
Дефект | Способ устранения | № Операции | Наименование и содержание операции | Установочные базы | ||
Износ шлицев по толщине | Пластическое деформирование | 1 | Токарная операция (обработка детали) | Центровые отверстия | ||
2 | Сглаживание | Центровые отверстия | ||||
3 | (наносим новые шлицы) | Центровые отверстия | ||||
4 | Мойка | |||||
5 | Контрольное измерение | |||||
Износ отверстий под роликовый подшипник | Вибродуговая наплавка | 1 | Токарная операция ( снятие поврежденного слоя металла) | Центровые отверстия | ||
2 | Вибродуговая наплавка | Центровые отверстия | ||||
3 | Токарная операция ( восстановление под размер) | Центровые отверстия | ||||
4 | Мойка (промыть деталь в содовом растворе) | |||||
5 | Измерительный контроль | |||||
Износ шеек под передний подшипник
| Вибродуговая наплавка | 1 | Токарная операция ( снятие поврежденного слоя металла) | Центровые отверстия | ||
2 | Вибродуговая наплавка | Центровые отверстия | ||||
3 | Токарная операция ( восстановление под размер) | Центровые отверстия | ||||
4 | Шлифовка шеек | Центровые отверстия | ||||
5 | Мойка (промыть деталь в содовом растворе) |
План технологических операций восстановления деталей
Наименование и содержание работы | Оборудование | Приспособление | Инструменты | |
Рабочий | Измерительный | |||
1 | 2 | 3 | 4 | 5 |
1. Токарная Выправить центровые отверстия ( при необходимости) | Токарный винторезный станок 1к62 | Приспособление Для крепления первичного вала КПП | Сверло центровочное Комбинированное Р 18 | |
2. Токарная Проточить изношенные шейки или отверстия | Токарный винторезный станок 1к62 | Поводковый патрон с поводком, центрами | Проходной резец с пластинкой Т15К6 | |
3. Наплавка Наплавить шейки вибродуговой наплавкой | Переоборудованный токарный - винторезный станок1К62. Выпрямитель ВСА-600/300 | Наплавочная головка УАНЖ -5. Приспособление для крепления первичного вала | ||
4. Наплавка Наплавить металл под отверстие | Переоборудованный токарный - винторезный станок1К62. Выпрямитель ВСА-600/300 | Наплавочная головка УАНЖ -5. Приспособление для крепления первичного вала | Штангенциркуль ШЦ-125-0,1 | |
5. Токарная Проточить наплавленные шейки | Токарный винторезный станок 1к62 | Поводковый патрон с поводком, центрами | Проходной резец с пластинкой Т15К6 | Штангенциркуль ШЦ-125-0,1 |
6. Шлифовальная Шлифовать шейки | Круглошлифоваль-ный станок 3Б151 | Поводковый патрон с поводком, центрами | Шлифовальный круг ПП600*40*305 24А25ПСМ25КВ А | Скобы 8113-0106 |
7. Фрезерная Фрезеровать шлицы | Горизонтально фрезерный станок 6М82Г | Тиски | Цилиндрическая фреза Т5К10 | Штангенциркуль ШЦ-125-0,1 |
8. Мойка Промыть деталь | Ванна с содовым раствором | Подвеска для мойки деталей | ___ | ___ |
|
|
а). Токарная операция.
Исходные данные
1.1. Деталь – первичный вал коробки передач Зил-431410, износ шейки под роликовый подшипник, d=43,980(мм), L= 30(мм);
1.2. Материал – сталь 25ХГМ;
1.3. Твердость – HRCЭ 61…66;
1.4. Масса детали – не более 5 кг;
|
|
1.5. Оборудование - токарно-винторезный станок модели К162;
1.6. Режущий инструмент – проходной прямой резец с пластиной Т15К6;
1.7. Установка детали – в центрах;
1.8. Условия обработки – без охлаждения.
Содержание операции.
2.1. Установить деталь в центрах;
2.2. Проточить шейку под подшипник;
2.3. Снять деталь.
Определение припусков
на обработку.
Ориентировочно значение припусков припуска при наплавке равно 0,6 и более (мм) на сторону, поэтому h=0,9(мм)
Определить припуски на обработку при восстановлении вибродуговой наплавкой
Первичного вала коробки передач (дет.130-1701030-6).
Диаметр изношенной детали Dизн=43,2 (за пределы последнего ремонтного размера)
Перед наплавкой требуется обработка для устранения неравномерности износа. В данном случае механическая обработка.
Припуск на предварительную обработку δ1=0,1-0,2 (на сторону), принимаем δ1=0,1мм.
Расчет режимов обработки.
4.1. Определяем длину обработки
( Л-1, стр.485, табл. 73-74)
где l – длинна шейки;
y – величина врезания и пребега резца.
4.2. Число переходов i принимаем равным 1, i=2
4.3. Определяем теоретическую подачу резца.
Sт=0,5 – 0,7 (мм/об) ( Л-6, стр. 56, табл. 8)
4.4. Определяем фактическую продольную подачу по паспорту станка.
Sф=0,5(мм)
4.5. Определяем скорость резания табличную.
Vтрез=143(м/мин) (Л-6, стр.57, табл.11)
4.6. Корректируем Vтрез с учетом условий обработки детали.
Tскорр.рез.= Vтрез*k1*K2*K3*K4=143*1,44*0,7*1,15*1,0=165,8(м/мин)
(Л-6,стр.57-59, табл.11-16)
4.7. Определяем число оборотов детали.
(Л-1, стр.482)
где υ – расчетная скорость резания, м/мин;
d – Диаметр обрабатываемо поверхности, мм.
4.8. Определяем фактическое число оборотов детали по паспорту станка.
nф=1250об/мин
I. Расчет норм времени.
5.1. Определяем основное время.
(Л-1, стр.485, 5.17)
где L – расчетная длинна обрабатываемой поверхности с учетом врезания и пребега, мм; i – число проходов; n – число оборотов шпинделя обрабатываемой детали в минутах; S – подача, мм/об.
5.2. Определяем вспомогательное время.
TВ=Туст+Тпр=0,38+0,8=38,8(мин) (Л-6,стр.62-63,табл.43-44)
Где Туст – время на установку и снятие детали
Тпр – время, связанное с проходом.
5.3. Определяем дополнительное время.
(Л-1,стр. 498, табл.42)
где То – основное время; ТВ – вспомогательное время; К – доп. Время 8%.
5.4. Определяем штучное время.
ТШТ=ТО+ТВ+ТДОП=0,11+38,8+0,031=39(мин)
В). определяем вибродуговую наплавку.
I. Исходные данные.
1.1. Деталь – первичный вал коробки передач, Зил 431410, износ шейки под подшипник d=43,2(мм), L=30(мм)
1.2. Материал – сталь 25ХНГ
1.3.
1.4. Оборудование – источник питания ТДМ-302 – ремдеталь выпрямитель ВД-201УЗ.
1.5. Положение детали в пространстве – горизонтальное;
1.6. Размер производственной партии – 119 деталей.
II. Содержание операции.
2.1. Установить деталь;
2.2. Наплавить шейку;
2.3. Снять деталь.
III. Определяем толщину определяемого металла с учетом припуска на черновое обтачивание.
IV. Расчет режимов обработки.
1. Толщина наплавляемого слоя – 2,5 мм;
2. Материал – низкоуглеродистая проволока;
3. Диаметр проволоки – 1,6 мм;
4. Сила тока – 70…75 А;
5. Напряжение – 24В
6. Частота вращения детали -10об/мм по паспорту станка;
7. Шаг наплавки – 1,6 мм
принимая во внимание, что скорость подачи электродной проволоки не должен превышать 1,65(м/мин) и используя формулу:
(Л-1, стр. 181, 13,5)
где n – частота вращения детали, мин; s – шаг наплавки, мм/об; D – диаметр детали, мм; h – толщина наплавляемого слоя, мм; d – диаметр электродной проволоки, мм; η – коэффициент наплавки (η=0,85…0,90).
Надежное сплавление обеспечивается при толщине наплавленного слоя, равного 2,5 мм.,
тогда
где VПР – скорость подачи проволоки, м/мин; d – диаметр проволоки, мм;
η – коэффициент наплавки; D – диаметр детали; - толщина наплавки.
Принимаем Sф = 0,5 мм/об по паспорту станка.
8.Раход СО2=8…10 (л/мин).
V. Расчет норм времени.
5.1. Определяем основное время.
(Л-6, стр.142. форм.47)
где L – длинна наплавляемой поверхности, мм; I – число проходов;
n – число оборотов детали в минуту; S – величина продольной подачи суппорта, мм/об.
5.2. Определяем вспомогательное время.
ТВ=Туст+ТПР=0,5+0,9=1,4(мин) (Л-6,стр.140-141.)
Туст – время связанное на снятие и установку детали;
ТПР – время связанное с проходом.
5.3. Определяем дополнительное время.
(Л-6, стр. 141)
5.4. Определение штучного времени.
ТШТ=ТО+ТВ+ТД=6+1,4+0,0111=7,4111мин.
VI. Измерить микрометром.
6.1. Взять микрометр.
6.2. Замерить деталь на месте.
6.3. Отложить микрометр.
Норма времени Т= 0,55мин
Дата добавления: 2018-10-26; просмотров: 71; Мы поможем в написании вашей работы! |
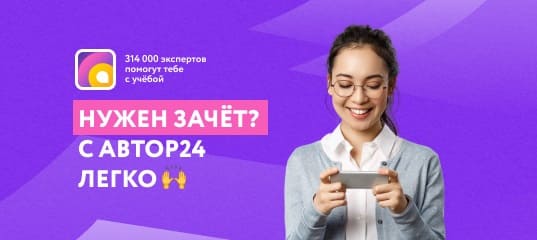
Мы поможем в написании ваших работ!