По пункту 5. Предварительный выбор конструкции приспособления с учетом направления сил резания.
Подобрать конструкцию приспособления с учетом размещения базирующих установочных элементов, определить предварительную схему зажимного устройства (по справочным данным)
Основные требования к закреплению заготовок в приспособлениях следующие.
1. Закрепление должно обеспечить надежный контакт заготовки с опорами приспособлений и гарантировать неизменность положения заготовки относительно технологической оснастки в процессе обработки или при отключении энергии.
2. Закрепление заготовки необходимо применять только в тех случаях, когда сила обработки или другие силы могут сместить заготовку (например, при протягивании шпоночного паза заготовку не закрепляют).
3. Силы закрепления не должны вызывать больших деформаций и смятия базы.
4. Закрепление и освобождение заготовки должны выполняться с минимальной затратой времени и усилий со стороны рабочего. Наименьшую погрешность закрепления обеспечивают зажимные устройства, создающие постоянную силу закрепления (например, приспособления с пневматическим или гидравлическим приводом).
5. Для уменьшения погрешности закрепления следует использовать базовые поверхности с низкой шероховатостью; применять приспособления с приводом; устанавливать заготовки на опоры с плоской головкой или на точно обработанные опорные пластины.
По пункту 6. Расчет сил закрепления заготовки. При фрезеровании заготовки обрабатывается плоская поверхность в приспособлении с помощью цилиндрической фрезы. На заготовку действуют силы Рz и Рy, стремящиеся повернуть ее относительно точки О (рисунок 3). Повороту противодействуют сила зажима W и сила трения F (трением на опорах пренебрегаем). Условие равновесия заготовки может быть представлено в виде суммы моментов относительно точки О:
|
|
Wа + Fℓ = Рzb + Рyℓ,
где а - плечо силы зажима W, мм; Рz и Рy - окружная и радиальная составляющие силы резания, Н; b - плечо силы Рz, мм; ℓ, - плечо силы Рy, и силы F (длина заготовки), мм.
Рис.3. Схема закрепления заготовок
По пункту 7. Выбор силового механизма и расчет его параметров.
Мощность резания должна быть меньше или равна мощности на шпинделе станка: N ≤ N шп = N м η, где N м - мощность электродвигателя, кВт; η - КПД станка.
Так как сила трения F = ѓ W, где ѓ - коэффициент трения, то после подстановки получим следующее выражение:
k (Рzb + Рyℓ)
W = _____________________,
α+ ѓℓ
где k - коэффициент запаса.
Рис.4. Комбинированное зажимное устройство
Если для фрезерной операции применить приспособление с комбинированным зажимным устройством (винт 3 - клин 2 - рычаг 1), то зажимная сила значительно увеличится (рис.4). Так, при коэффициентах усиления (отношение развиваемой силы к приложенной) равных для винтового устройства.3-120, клина - 2 - 3 и рычажного зажима 1-1,5, и КПД комбинированного устройства η= 0,7 увеличение приложенной силы составит 120·3·I,5· 0,7 = 380раз.
|
|
При точных расчетах сил закрепления учитывают также упругие характеристики зажимного устройства.
По пункту 8. Выполнение эскиза приспособления.
По пункту 9. Описание приспособления.
Погрешность базирования зависит от принятой схемы, базирования. Например, при сверлении отверстия по кондуктору (рис.13.2) при установке заготовки по схеме (рис. (3.2, а) погрешность ∆Е б Н 1 базирования для размера Н 1 равна ≈ 0,12 мм, а по схеме (рис.13.2,6) погрешность ∆Е б Н 2 базирования для размера Н 2 равна ≈ 0,02 мм (при допуске на наружный диаметр заготовки 0,1 мм), т.е. отличается в шесть раз.
Погрешность базирования равна нулю, если технологическая и измерительная базы совпадают (рис.13.2, в), т.е. ∆Е б Н 3 =0.
Рисунок.13.2 Схема к определению погрешности базирования.
Рассмотрим несколько вариантов действия на обрабатываемую деталь сил резания, зажима и их моментов.
Первый вариант (рис. III.1, а). Сила зажима W, приложенная к обрабатываемой детали 1 и сила резания Р одинаково направлены и прижимают деталь к опоре 2 приспособления. При этом требуется минимальная сила зажима Wmin.
|
|
Второй вариант (рис. III.1, б). Сила зажима W и сила резания Р действуют на обрабатываемую деталь 1 в противоположных направлениях; требуемая сила зажима
W=KP.
Третий вариант (рис. III.1, в). Сила зажима W и сила резания Р действуют на обрабатываемую деталь во взаимно перпендикулярном направлении. Силе резания Р противодействуют силы трения между нижней базовой плоскостью детали и опорными штырями приспособления и между верхней плоскостью детали и зажимными элементами.
Четвертый вариант (рис. III.1, г). Сила зажима W прижимает деталь к опорам, при этом одна сила резания P 1 имеет одно направление с силой зажима прижимает деталь к нижним опорам, а вторая сила резания Р2 действует в направлении, перпендикулярном силе зажима. Смещению детали в приспособлении препятствуют силы трения, возникающие на плоскостях контакта детали с установочными и зажимными элементами приспособления.
Пятый вариант (рис. III.1, д, е). Обрабатываемая деталь зажимается горизонтально действующей силой зажима Р1. Расстояние между силой зажима и силой реакции от бокового упора выбирают таким, чтобы обрабатываемая деталь надежно была прижата к установочным опорам приспособления. На деталь, зажатую в приспособлении, действуют сила зажима W, силы реакции R t и R от установочных и зажимных опор и силы трения F, F 1 и F2 между поверхностями детали, установочными и зажимными элементами приспособления.
|
|
Шестой вариант (рис. III.1, д, е). При обработке детали фрезой на нее действуют силы резания P 1 и Р2. Величину силы зажима с учетом сил резания найдем, приравнивая сумму моментов всех сил относительно точки 0 нулю:
Седьмой вариант (рис. II 1.1, ж). Обрабатываемую деталь выточкой устанавливают на центрирующий жесткий палец приспособления и левой плоскостью прижимают к трем опорным штырям несколькими прихватами. При обработке на деталь действуют сдвигающий момент М и осевая сила Р. Обрабатываемая деталь удерживается от смещения силами трения, возникающими между поверхностями установочных и зажимных элементов приспособления.
Восьмой вариант (рис. III.1, з). Обрабатываемая деталь наружной цилиндрической поверхностью установлена в призме с углом а=90° и зажата силой W. Повороту детали около ее оси противодействуют силы трения, возникающие на поверхностях контакта детали с установочными и зажимными элементами приспособления.
Девятый вариант (рис. II 1.2, а). Рассмотрим действие двух сил резания Рг и Рх на обрабатываемую деталь 1, зажатую в трехкулачковом патроне станка; сила резания Рг создает момент, который стремится повернуть обрабатываемую деталь вокруг ее оси, а сила Рх - переместить обрабатываемую деталь вдоль ее оси.
Рис. II 1.2 Различные варианты взаимодействия сил резаная и сил зажима на деталь, установленную в патроне (а) и на цанговой оправке (б)
Десятый вариант (рис. II 1.2, б). Рассмотрим действие силы резания Рх на обрабатываемую втулку 2, установленную и зажатую на цанговой оправке / (рис. III.2, б). Сила Рг при обработке втулки 2 создает момент резания Мря, которому противодействует момент от силы трения Мгр между" установочной поверхностью цанги и обрабатываемой деталью.
Таблица 2 - Шероховатость поверхности и квалитеты при различных способах обработки резанием
квалитет | 4 | - | ||||||||||
5 | - | - | - | |||||||||
6 | - | - | - | - | - | |||||||
7 | - | - | - | - | - | - | ||||||
8 | - | - | - | - | - | - | - | |||||
9 | - | - | - | - | - | - | - | |||||
10 | - | - | - | - | - | |||||||
11 | - | - | - | - | - | |||||||
12 | - | - | - | - | ||||||||
13 | - | - | - | - | ||||||||
14 | - | - | - | - | ||||||||
15 | - | |||||||||||
16 | - | |||||||||||
17 | - | |||||||||||
Значение параметра шероховатости Rа, мкм | 0,012 | - | ||||||||||
0,025 | - | - | ||||||||||
0,05 | - | - | - | |||||||||
0,1 | - | - | - | |||||||||
0,2 | - | - | - | - | ||||||||
0,4 | - | - | - | - | - | - | - | - | ||||
0,8 | - | - | - | - | - | - | - | - | ||||
1,6 | - | - | - | - | - | - | - | - | ||||
3,2 | - | - | - | - | - | - | ||||||
6,3 | - | - | - | - | - | |||||||
12,5 | - | - | - | - | ||||||||
25 | - | - | - | - | ||||||||
50 | - | - | - | |||||||||
100 | - | - | - | |||||||||
Вид обработки
| точение | Сверление | зенкерование | развертывание | Строгание | Фрезерование | Протягивание | Шлифование | Хонингование | Полирование | Доводка (притирка) |
Примечание: - предельно-допустимые значения
Таблица 3 - Значение параметров шероховатости поверхностей взависимости от способа их обработки
Виды обработки | Высота неровностей, мкм | |||||||||||||
320 | 160 | 80 | 40 | 20 | 2,5 | 1,25 | 0,63 | 0,32 | 0,16 | 0,08 | 0,04 | 0,10 | 0,05 | |
Литье | ![]() | ![]() | ![]() | ![]() | ![]() | |||||||||
Ковка | ![]() | ![]() | ![]() | ![]() | ||||||||||
Прокат холодный | ![]() | ![]() | ![]() | |||||||||||
Протягивание чистовое | ![]() | ![]() | ||||||||||||
Протягивание отделочное | ![]() | |||||||||||||
Штамповка горячая | ![]() | ![]() | ![]() | ![]() | ||||||||||
Штамповка холодная | ![]() | ![]() | ![]() | ![]() | ||||||||||
Слесарная опиловка | ![]() | ![]() | ![]() | ![]() | ![]() | |||||||||
Сверление чистовое | ![]() | ![]() | ||||||||||||
Сверление отделочное | ![]() | |||||||||||||
Строгание черновое | ![]() | ![]() | ![]() | |||||||||||
Строгание чистовое | ![]() | |||||||||||||
развертывание | ![]() | ![]() | ||||||||||||
Развертывание чистовое | ![]() | ![]() | ![]() | |||||||||||
Развертывание отделочное | ![]() |
Виды Обработки | Высота неровностей, мкм | |||||||||||||
320 | 160 | 80 | 40 | 20 | 2,5 | 1,25 | 0,63 | 0,32 | 0,16 | 0,08 | 0,04 | 0,10 | 0,05 | |
Точение обдирочное | ![]() | ![]() | ![]() | ![]() | ||||||||||
Точение чистовое | ![]() | ![]() | ![]() | ![]() | ||||||||||
Точение тонкое | ![]() | |||||||||||||
Растачивание обдирочное | ![]() | ![]() | ![]() | |||||||||||
Растачивание чистовое | ![]() | ![]() | ![]() | |||||||||||
Растачивание тонкое | ![]() | ![]() | ||||||||||||
Фрезерование черновое | ![]() | |||||||||||||
Фрезерование чистовое | ![]() | |||||||||||||
Шлифование чистовое | ||||||||||||||
Шлифование тонкое | ![]() | ![]() | ![]() | |||||||||||
Полирование | ![]() | ![]() | ![]() | ![]() | ![]() | ![]() | ||||||||
Хонингование | ![]() | ![]() | ![]() | ![]() | ||||||||||
Обкатка | ![]() | ![]() | ![]() | ![]() | ||||||||||
Виброобкатка | ![]() | ![]() | ![]() | ![]() | ![]() | ![]() | ![]() | |||||||
Доводка | ![]() | ![]() | ![]() | ![]() | ![]() |
Таблица 4 - Отклонения размеров в микрометрах в зависимости от квалитета и номинального размера
Номинальные размеры, мм | КВАЛИТЕТЫ
| |||||||||||
4 | 5 | 6 | 7 | 8 | 9 | 10 | 11 | 12 | ||||
Предельные отклонения, мкм | ||||||||||||
До 1 | 3 | 4 | 6 | 10 | 14 | 25 | 40 | 60 | - | |||
От 1 до 3 | 3 | 4 | 6 | 10 | 14 | 25 | 40 | 60 | 100 | |||
Св.3 до 6 | 4 | 5 | 8 | 12 | 18 | 30 | 48 | 75 | 120 | |||
Св.6 до 10 | 4 | 6 | 9 | 15 | 22 | 36 | 58 | 90 | 150 | |||
Св.10 до 18 | 5 | 8 | 11 | 18 | 27 | 43 | 70 | 110 | 180 | |||
Св.18 до 30 | 6 | 9 | 13 | 21 | 33 | 52 | 84 | 130 | 210 | |||
Св.30 до 50 | 7 | 11 | 16 | 25 | 39 | 62 | 100 | 160 | 250 | |||
Св.50 до 80 | 8 | 13 | 19 | 30 | 46 | 74 | 120 | 190 | 300 | |||
Св.80 до 120 | 10 | 15 | 22 | 35 | 54 | 87 | 140 | 220 | 350 | |||
Св.120 до 180 | 12 | 18 | 25 | 40 | 63 | 100 | 160 | 250 | 400 | |||
Св.180 до 250 | 14 | 20 | 29 | 46 | 72 | 115 | 185 | 290 | 460 | |||
Параметры шероховатости поверхности и соответствующие им классы шероховатости
Класс шероховатости | Параметры шероховатости для документации, разработанной до 1975 г. (ГОСТ 2789-73) | Параметры шероховатости по ГОСТ 2789-73 (соответствует предпочтительному ряду) | |
Rz | Ra | ||
1 | 320 | 50 | |
2 | 160 | 25 | |
3 | 80 | 12,5 | |
4 | 40 | 6,3 | |
5 | 20 | 3,2 | |
6 | 2,5 | 1,6 | |
7 | 1,25 | 0,8 | |
8 | 0,63 | 0,4 | |
9 | 0,32 | 0,2 | |
10 | 0,16 | 0,1 | |
11 | 0,08 | 0,05 | |
12 | 0,04 | 0,025 | |
13 | 0,1 | 0,012 | |
14 | 0,05 | 0,012 |
Дата добавления: 2018-10-26; просмотров: 175; Мы поможем в написании вашей работы! |
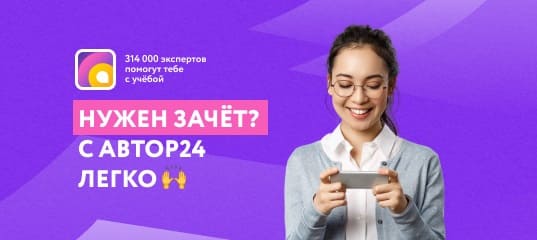
Мы поможем в написании ваших работ!