Примеры выполнения и описания технологических схем
Министерство образования Российской Федерации
Воронежская государственная технологическая академия
ПРАВИЛА И ПРИМЕРЫ ВЫПОЛНЕНИЯ
ТЕХНОЛОГИЧЕСКИХ СХЕМ
Методические указания к курсовому проектированию
по процессам и аппаратам химических и пищевых производств
Для студентов специальностей 170500 и 170600
Воронеж
1999
Составители: доценты А.В.Логинов, М.И.Слюсарев
УДК: 621.22-82-85.001.63(072)
Правила и примеры выполнения технологических схем: Методические указания к курсовому проектированию по процессам и аппаратам химических и пищевых производств / Воронеж. гос. технол. акад.; Сост. А.В.Логинов, М.И.Слюсарев. Воронеж, 1999. - 28 c.
Содержатся сведения об оформлении технологических схем в соответствии с требованиями ЕСКД. Приводятся условные графические и позиционные обозначения машин и аппаратов, технологических связей между ними, а также элементов, имеющих самостоятельное функциональное назначение. Даются примеры выполнения и описания технологических схем различных производств.
Предназначено для студентов специальности 170500 и 170600 – “Машины и аппараты химических производств” и “Машины и аппараты пищевых производств”.
|
|
Ил. 2. Библиогр.: 5 назв.
Научный редактор - докт. техн. наук, проф. Ю.В.Красовицкий
Рецензент - главный специалист института “ГИПРОПРОМ” И.М.Филатов
Редактор Н.А. Сотникова
Корректор Н.В. Бургонова
ЛР № 020449 от 31.10.97. Подписано в печать 03.06.98. Формат 60х84 1/16.
Бумага для множ. аппаратов. Офсетная печать. Усл.печ.л. 1,6 + 3с. вклейка.
Уч.-изд.л. 1,6. Тираж 100 экз. Заказ . С - .
Воронежская государственная технологическая академия (ВГТА)
Участок оперативной полиграфии ВГТА
Адрес академии и участка оперативной полиграфии:
394017 Воронеж, пр. Революции, 19
© Воронежская
государственная
технологическая
академия, 1999
Введение
В соответствии с учебным планом студентами специальностей 170500 и 170600 по кафедре процессов и аппаратов химических и пищевых производств выполняются курсовая работа и проект.
С целью активизации познавательной деятельности студентов кафедра систематически и целенаправленно применяет в учебном процессе разнообразные методики, методы, приёмы и средства обучения.
Среди них, на наш взгляд, особое место занимает профилизация общепрофессиональных дисциплин, читаемых на кафедре. С этой целью изменяются содержание, структура и объём курсового проектирования.
|
|
Задания по курсовому проектированию составлены с учётом будущей специальности студентов и требуют предварительного ознакомления с тем технологическим процессом конкретного производства, для которого это задание должно выполняться. Результаты такой работы целесообразно представлять в виде технологической схемы и её описания.
Технологическая схема является одним из основных документов проекта любого химического или пищевого производства, поэтому представленный в методических указаниях материал может оказаться полезным для студентов старших курсов и студентов-дипломников при выполнении научно-исследовательских работ и проектов.
Правила выполнения технологических схем
Технологические схемы являются графическим отражением рассматриваемого технологического процесса (системы) и представляют собой условные изображения машин и аппаратов, расположенных в требуемой последовательности, соединённых между собой соответствующими линиями связи (трубопроводами, транспортными средствами и т. п.).
1.1 Виды и типы схем
ГОСТ 2.701-84 устанавливает виды и типы схем изделий всех отраслей промышленности.
|
|
В зависимости от видов элементов[1], входящих в состав изделия, и их связей предусмотрены следующие виды схем и их буквенные обозначения:
электрические – Э;
гидравлические – Г;
пневматические – П;
газовые (кроме пневматических) – Х;
кинематические – К;
вакуумные – В;
оптические – Л;
энергетические – Р;
деления – Е;
комбинированные – С.
Схемы в зависимости от их основного назначения разделяются на следующие типы, обозначаемые цифрами:
структурные – 1;
функциональные – 2;
принципиальные (полные) – 3;
соединений (монтажные) – 4;
подключения – 5;
общие – 6;
расположения – 7;
объединённые – 0.
Наименование схемы определяется её видом и типом. Код схемы должен состоять из буквенной части, определяющей вид схемы, и цифровой части, определяющей тип схемы. Например, схема гидравлическая принципиальная – Г3; схема гидравлическая структурная, принципиальная и соединений – Г0; схема гидропневматическая принципиальная – С3.
Как видно, технологическая схема не включена самостоятельным видом в число тех, которые установлены ГОСТ 2.701-84. Поэтому для обозначения схемы технологической используют букву Т. Если использовать установленную терминологию типов схем применительно к технологической схеме, то она может быть отнесена к принципиальной – 3. Следовательно, код схемы технологической принципиальной – Т3.
|
|
Во многих случаях по виду технологические схемы могут быть отнесены к комбинированным, поскольку содержат элементы и связи других видов схем, например, электрических, гидравлических, пневматических. Тогда код схемы – С3.
1.2 Назначение технологических схем
Технологическая схема является проектным документом, представляющим собой графическое изображение технологического процесса любого химического или пищевого производства. Она служит источником информации о полном составе элементов в установке и связях между ними, о принципах её работы.
Схема используется для общего ознакомления с установкой, в которой осуществляется определённый технологический процесс, для изучения принципов работы установки и основных параметров протекающего в установке процесса.
Объём и содержание схемы вместе с её описанием должны быть достаточными для правильного понимания технологического процесса без дополнительных разъяснений. В то же время схема должна быть составлена в краткой, но ясной и отчётливой форме, чтобы передать всю необходимую информацию с предельной точностью, исключающей возможность неоднозначного толкования передаваемых сведений. Схема не должна содержать второстепенной информации: обозначений и надписей, излишних подробностей в изображении конструкций аппаратов и т. п.
1.3 Изображение элементов и устройств
К элементам и устройствам схемы относят входящие в состав установки для осуществления заданного технологического процесса аппараты, машины, контрольно-измерительные приборы и другое оборудование, а также арматуру. Все элементы и устройства изображаются в виде условных графических обозначений, установленных стандартами ЕСКД:
аппаратов ёмкостного типа – ГОСТ 2.780-96;
насосов и вентиляторов – ГОСТ 2.782-96;
арматуры трубопроводной – ГОСТ 2.785-70;
аппаратов выпарных – ГОСТ 2.788-74;
аппаратов теплообменных – ГОСТ 2.789-74;
аппаратов колонных – ГОСТ 2.790-74;
отстойников и фильтров – ГОСТ 2.791-74;
аппаратов сушильных – ГОСТ 2.792-74;
элементов и устройств машин и аппаратов – ГОСТ 2.793-79;
устройств питающих и дозирующих – ГОСТ 2.794-79;
центрифуг – ГОСТ 2.795-80.
Условные графические обозначения некоторых элементов и устройств из вышеперечисленных стандартов приведены в приложении А.
При отсутствии в стандартах условных графических обозначений элементов и устройств, используемых в технологической схеме, их изображают схематически в виде конструктивного очертания. Хотя аппарат или машину показывают упрощённо, чертёж всё же должен отражать принципиальное устройство и основные его конструктивные особенности. Поэтому с целью более полной передачи информации о конструкции аппарата и его назначении допускается изображать отдельные элементы, находящиеся внутри его, например, змеевики, барботажные тарелки, мешалки и т. п.
Допускается изображать элементы и устройства на схеме без масштаба, но в соотношениях, в которых они выполнены в стандартах.
Условные графические обозначения элементов и устройств на технологических схемах выполняются сплошной линией толщиной S.
1.4 Обозначения элементов и устройств
Элементам и устройствам, показанным на схеме, как правило, присваивают буквенное обозначение, соответствующее начальной букве их наименований:
аппарат – А;
компрессор – К;
вентилятор – В;
насос – Н;
ёмкость – Е;
теплообменник – Т;
вентиль регулирующий – ВР;
вентиль запорный – ВЗ и т. д.
При наличии в схеме нескольких элементов или устройств одного названия используют числовые индексы и цифры, записываемые с правой стороны буквенного обозначения. Для основных аппаратов и машин применяется буквенно-цифровое обозначение, причём высота цифры равна высоте букв, например: А1, А2, В1, В2. Для арматуры и приборов высота числового индекса равна половине высоты букв, например: ВЗ1, ВЗ2, КП1, КП2, М1, М2.
Буквенные обозначения элементов схемы следует проставлять для аппаратов, машин и механизмов непосредственно на их изображении, а при малом масштабе – в непосредственной близости от изображения; для арматуры – рядом с её изображением.
1.5 Линии связи и их обозначения
Линиями связи на технологических схемах называются линии, условно обозначающие трубопроводы и соединяющие между собой все элементы и устройства схемы. Они показываются сплошными линиями толщиной 2S – 3S.
Линии связи должны состоять из горизонтальных и вертикальных отрезков и иметь наименьшее количество изломов и взаимных пересечений. Пересекать изображения аппаратов, машин и других изделий линиями трубопроводов не допускается. Расстояние между смежными параллельными линиями должны быть не менее 5 мм.
На схеме могут быть показаны основные магистральные трубопроводы, расположенные выше или ниже оборудования, изображённого на схеме. Допускается показывать линии магистральных трубопроводов одновременно сверху и снизу схемы. Для их изображения используются только горизонтальные линии.
На каждом трубопроводе у места его отвода от магистрального трубопровода или места подключения или отвода от машины или аппарата необходимо проставлять стрелки, указывающие направление движения среды в трубопроводе. Стрелки указываются также в начале и в конце любого трубопровода, проведённого на схеме, в том числе и магистрального. Стрелки указывают одновременно и вид среды: светлые (незаштрихованные) – газообразные среды, тёмные (заштрихованные) – жидкие среды. Форма стрелки должна представлять собой равносторонний треугольник, а его размеры должны быть соизмеримы с размером условных изображений элементов и устройств на схеме. Максимальный размер сторон стрелки – 5 мм.
В том случае, если технологическая схема отражает лишь часть технологического процесса, то целесообразно в начале и конце основных трубопроводов (исключая магистральные) делать надписи, например, “Исходная смесь”, “На сушку” и т. д.
Количество линий связи на технологической схеме определяется многообразием и различным назначением участвующих в процессе веществ. По одним трубопроводам транспортируют сырьё и полуфабрикаты, непосредственно участвующие в физико-механических или химических превращениях исходного сырья в готовый продукт. Другие служат для перемещения сред, играющих вспомогательную роль в процессе производства продукции, например, для подвода воздуха, тепло - или хладоносителя, для отвода неконденсирующихся газов и т. д.
Для отличия на схеме линий связи (трубопроводов) различного назначения применяют цифровые обозначения, проставляемые в их разрыве. Число проставленных цифровых обозначений на линиях трубопроводов должно быть минимальным, но обеспечивающим понимание чертежа и удобство пользования им. При значительной длине линий связи цифровые обозначения (номера) проставляют через каждые 250-300 мм.
В соответствии с ГОСТ 14202-69 для обозначения транспортируемой среды установлено 10 укрупнённых групп веществ:
1 – вода;
2 – пар;
3 – воздух;
4 – газы горючие;
5 – газы негорючие;
6 – кислоты;
7 – щёлочи;
8 – жидкости горючие;
9 – жидкости негорючие;
0 – прочие вещества.
Каждая группа распределяется на 10 подгрупп, например: 1.1 - вода питьевая; 1.2 - вода техническая и т. д. В случае необходимости, каждая из подгрупп может быть распределена на десять более мелких подразделений, обозначаемых третьим знаком цифрового обозначения (приложение Б).
На трубопроводах на полках выносных линий могут быть указаны (например, если выполнен гидравлический расчёт насосных установок, входящих в технологическую схему) размеры (наружный диаметр и толщина стенки), материал и сведения о внутреннем антикоррозионном покрытии или наружной изоляции. Могут быть указаны также давление в трубопроводе, температура (а иногда и расход) транспортируемого вещества.
Линии связи на схеме, как правило, должны быть указаны полностью. Обрывать их допускается тогда, когда графическое изображение связей удалённых друг от друга элементов затрудняет чтение схемы. Обрывы линий выносят за контуры функционального устройства и заканчивают стрелками с указанием наименования последующего объекта. Около места обрыва допускается наносить обозначение, присвоенное этой линии.
1.6 Требования к выполнению технологических схем
Технологические схемы в зависимости от сущности и масштаба изображаемого процесса могут быть выполнены на листах формата А1, А2 или А3.
Схема вычерчивается слева направо по ходу технологического процесса. В отдельных случаях технологический процесс допускается изображать на схеме в две параллельные линии (цепи) с соблюдением при этом последовательности процесса.
При выборе расстояния между изображениями необходимо руководствоваться тем, что схема должна быть компактной (т.е. изображения элементов на схеме желательно располагать по возможности ближе друг к другу), но в то же время ясной и удобной для чтения. Условные графические обозначения насосов, компрессоров и другого машинного оборудования принято, как правило, выполнять внизу схемы.
Арматура, а также другие приборы, устанавливаемые на оборудовании, должны быть показаны на схеме в соответствии с их действительным расположением и изображены условно в соответствии с действующими стандартами.
На технологических схемах можно помещать различные технические данные. Их записывают либо около графических обозначений элементов, по возможности справа или сверху, либо на свободном поле схемы. Например, около изображений аппаратов указывают номинальные значения параметров процесса (давление, температуру), состав участвующих в процессе масс и др.
Данные об условных графических изображениях, показанных на схеме, записывают в перечень элементов, помещаемый на листе схемы в виде таблицы (рисунок 1) в правом углу над основной надписью. Расстояние между перечнем элементов и основной надписью должно быть не менее 12 мм.
![]() ![]() ![]() | Наименование | Кол. | Примечание |
Рисунок 1
В графах перечня указывают следующие данные:
- в графе “Поз. обозначение” – обозначение элемента или устройства. Элементы и устройства одного типа и размера с одинаковыми технологическими параметрами, имеющие на схеме последовательные порядковые номера, допускается записывать в перечень одной строкой, например, Н1,...,Н3;
- в графе “Наименование” – наименование элемента;
- в графе “Кол.” – количество элементов в схеме;
- в графе “Примечание” при необходимости указывают технические данные элементов. Допускается давать цифровые обозначения элементов схемы, необходимые для обозначения чертежей аппаратов и машин (разряд 1), входящих в схему.
Все элементы записывают в перечень элементов в алфавитном порядке использованных буквенных обозначений сверху вниз.
Условные изображения и обозначения трубопроводов, принятые на схеме, должны быть расшифрованы в таблице условных обозначений (рисунок 2), помещаемой над перечнем элементов.
Рисунок 2
В графах таблицы условных обозначений трубопроводов указывают следующие данные:
- в графе “Условное обозначение” – в разрыве линии, обозначающей трубопровод, цифровое обозначение вещества, протекающего по данному трубопроводу;
- в графе “Наименование среды в трубопроводе” – краткое наименование вещества, протекающего по данному трубопроводу. Наименование должно начинаться с имени существительного, например, “Пар насыщенный”, “Вода горячая” и т. п.
Все вещества в таблицу условных обозначений заносят в порядке использованных цифр, например 1.1, 1.3, 1.8, 2.2, 3.1, 3.8, и т. д.
1.7 Обозначение схем
Обозначение в основной надписи технологических схем, выполняемых, например, в курсовом проекте по дисциплине “Процессы и аппараты пищевых производств” студентами специальности 170600 – “Машины и аппараты пищевых производств”, будет следующим [2]: КП-02068108-ПАПП-170600-17.2-99-00.000 Т3.
В основной надписи записывают, например: “Установка получения диоксида углерода из газов брожения. Схема технологическая”.
2 Описание технологических схем
Технологические схемы сопровождаются описанием, которое включается в пояснительную записку в качестве одного из разделов или подразделов. Оно прилагается к чертежу схемы и проводится по отдельным операциям технологического процесса [3].
Первоначально приводятся сведения о сырье, сообщается о способах поступления, хранения сырья и подачи его на установку. Далее последовательно по ходу технологического процесса даётся описание в краткой форме конструкций всех аппаратов, приводится характеристика протекающих в них процессов и указываются способы их проведения (непрерывные или периодические). При этом перечисляются все основные и побочные продукты, а также отходы, образующиеся на каждой стадии технологического процесса. При характеристике процессов необходимо указывать их основные параметры (давление, температуру и др.).
В описании должны быть упомянуты все изображённые на схеме аппараты и машины с указанием присвоенных им обозначений и соединяющие эти машины и аппараты трубопроводы с обозначениями.
Примеры выполнения и описания технологических схем
3.1 Технологическая схема абсорбционно-холодильной установки
(чертёж КП-02068108-ПАХТ-170500-4.33-97-00.000 Т3)
Абсорбционно-холодильная установка используется в производстве аммиака для трёх целей: выделения продукционного аммиака из синтез-газа, танковых и продувочных газов цикла синтеза и его охлаждения до минус 33,4 °C (с этой температурой аммиак может подаваться в изотермическое хранилище); межступенчатого охлаждения (на одной из ступеней) компрессора синтез-газа; охлаждения конвертированного газа.
Принципиальная технологическая схема абсорбционно-холодильной установки включает в себя следующие аппараты. В генераторе-ректификаторе ГР аммиак выделяется из раствора за счёт охлаждения конвертированного газа и водяного пара. Генератор-ректификатор представляет собой вертикальный кожухотрубчатый аппарат плёночного типа с теплообменными трубками диаметром 38 мм. Аппарат состоит из трёх основных частей: теплообменной, ректификационной и кубовой. Крепкий водоаммиачный раствор подают в ректификационную часть аппарата в кольцевую перфорированную трубу. Раствор равномерно орошает слой металлических колец Рашига. Через отверстия в колосниковой решётке водоаммиачный раствор попадает в теплообменную часть аппарата, стекая по внутренней поверхности теплообменных труб. В межтрубное пространство теплообменника подают теплоноситель - конвертированный газ с содержанием оксида углерода до 0,5 %, имевший после конвертора оксида углерода второй ступени температуру 240-275 °C и прошедший предварительно охладитель-испаритель, кипятильники регенератора раствора моноэтаноламина и сепаратор. Охлаждённый конвертированный газ направляют для дальнейшего охлаждения в воздушные холодильники, после чего он поступает на абсорбцию диоксида углерода (вышеназванные аппараты без обозначения на схеме не указаны). В трубчатом теплообменнике генератора-ректификатора за счёт теплоты конвертированного газа из водоаммиачного раствора испаряется большая часть аммиака, которая поднимается вверх, проходит слой колец Рашига и поступает на колпачковые тарелки, которые орошаются флегмой. Здесь в верхней части генератора-ректификатора происходит окончательная ректификация аммиака, который в виде паров покидает аппарат через штуцер в крышке и поступает в дефлегматор Д. В дефлегматоре пары аммиака охлаждаются и окончательно очищаются от водяных паров. Из дефлегматора аммиачные пары поступают в конденсатор воздушного охлаждения КВ, где происходит их конденсация при давлении 1,6 МПа. Конденсатор воздушного охлаждения представляет собой аппарат, выполненный в виде горизонтальных секций, расположенных зигзагообразно. Секции аппарата собраны из оребренных труб диаметром 25 мм и толщиной стенки 2 мм.. Секции аппарата обдуваются потоком воздуха, нагнетаемого вентиляторами В, установленными совместно с приводами под секциями. Воздух от вентиляторов проходит через диффузоры, попадает на ребристую поверхность труб и охлаждает протекающий по ним аммиак до минус 34 °C. Жидкий аммиак из конденсатора поступает в ресивер Р1, откуда подаётся в переохладитель ПО, представляющий собой теплообменник типа “труба в трубе”, где в межтрубном пространстве охлаждаются пары аммиака, поступающие из испарителя И. Из трубного пространства переохладителя жидкий аммиак поступает в испаритель И, в котором его давление снижается в дроссельном устройстве до 0,2 МПа (испаритель, а также сборник жидкого аммиака С1 устанавливают в цехе синтеза аммиака). За счёт испарения жидкого аммиака на теплообменной поверхности происходит охлаждение циркуляционного синтез-газа, поступающего в испаритель из конденсационной колонны цеха синтеза аммиака (на схеме не показана), до минус 10 °C и выделение из него продукционного аммиака. Жидкий аммиак из испарителя поступает в сборник жидкого аммиака С1, куда также поступает жидкий аммиак из конденсационной колонны цеха синтеза аммиака. Пары аммиака из испарителя поступают в межтрубное пространство переохладителя и далее – в нижнюю часть абсорбера А. В верхнюю часть абсорбера поступает охлаждённый в теплообменнике Т до 21 оС слабый водоаммиачный раствор, подаваемый насосом Н1. Абсорбер представляет собой аппарат колонного типа с насадкой из беспорядочного засыпанных колец Рашига 50х50х5 мм. Подаваемый в верхнюю часть аппарата слабый водоаммиачный раствор равномерно орошает насадку, стекая в плёночном режиме по кольцам Рашига, и поглощает пары аммиака из смеси, поступающей в нижнюю часть абсорбера и поднимающейся через слой насадки вверх. Из нижней части абсорбера крепкий водоаммиачный раствор собирают в ресивер Р2, откуда он насосом Н2 через трубчатку теплообменника Т и дефлегматора Д поступает на орошение в генератор-ректификатор ГР. Отходящая воздушная смесь с оставшимися в ней парами аммиака из абсорбера, а также воздушные смеси с парами аммиака из сборника жидкого аммиака С1, ресиверов Р1 и Р2, конденсатора воздушного охлаждения КВ, поступают в воздухоохладитель ВО, где вследствие охлаждения пары аммиака и воды конденсируются и водоаммиачный раствор направляется в ресивер Р2, а охлаждённая воздушная смесь с оставшимися парами аммиака направляется в отделитель аммиака О, в котором происходит окончательное отделение паров аммиака от воздуха.
3.2 Установка производства аммиака конверсией углеводородных газов
(чертёж КП-02068108-ПАХТ-170500-3.55-97-00.000 Т3)
Сущность конверсионного метода получения необходимой для синтеза аммиака азотоводородной смеси заключается в разложении при высокой температуре природного газа (чаще метана) на водород и углекислый газ с помощью окислителей – водяного пара и кислорода. Для осуществления процесса первичной конверсии, смесь водорода и предварительно нагретого в подогревателе П метана очищается от серосодержащих соединений в реакторе гидрирования органической серы Р и адсорбере АД, смешивается с водяным паром в соотношении 3:1 и после подогрева в теплообменнике Т1 поступает в трубчатую печь ТП первичной конверсии, в которой при температуре 800-850 °С, создаваемой путём непрерывной подачи в топку печи природного газа и сжатого атмосферного воздуха, метан разлагается в присутствии никелевого катализатора на водород и оксид углерода. Содержание метана после первой ступени конверсии составляет 9-10 %.
После трубчатой печи образовавшаяся азотоводородная смесь с примесью оксида углерода и остаточного метана проходит в шахтный конвертор метана КМ, в котором кислородом воздуха, поступающим в аппарат, осуществляется конверсия остаточного метана при температуре 800-1000 °С. Далее азотоводородная смесь с примесью оксида углерода поступает в котёл-утилизатор КУ1, где за счёт высокой температуры смеси осуществляется нагрев и испарение поступающей в котёл питательной воды с образованием пара высоких параметров.
Охлаждённая в результате прохождения котла-утилизатора газовая смесь направляется на двухступенчатую конверсию оксида углерода: сначала конверсия происходит в конверторе К1 на среднетемпературном железохромовом катализаторе при температуре 430-470 °С, а затем в конвертор К2 с низкотемпературным (около 200-260 °С) цинкохромомедным катализатором. Понижение температуры газовой смеси после первой ступени конверсии оксида углерода производится в котле-утилизаторе КУ2, в котором как и в первом котле-утилизаторе получают пар высоких параметров путём нагрева и испарения высокотемпературной азотоводородной смесью питательной воды, поступающей в котёл.
Удаление образовавшегося в азотоводородной смеси в результате двухступенчатой конверсии оксида углерода углекислого газа осуществляется в насадочном абсорбере А, перед которым установлен холодильник Х1, предназначенный для охлаждения азотоводородной смеси с примесями углекислого газа, поступающей из конвертора оксида углерода К1 в абсорбер А. Охлаждённая этиленгликолем в холодильнике Х1 азотоводородная смесь, проходя насадочный абсорбер, очищается от углекислого газа в результате поглощения последнего водой и в виде смеси чистой газовой фазы и капель воды направляется в сепаратор С1 на разделение на жидкую (отработанная вода) и газообразную (чистая азотоводородная смесь) фазы.
Поступающая с нижней части абсорбера А через дроссель ДР, снижающий давление в сети до атмосферного, насыщенная углекислым газом вода проходит через теплообменник Т2, обогреваемый водяным паром, в десорбер Д для первичной очистки и далее в десорбционную колонну ДК, в которой производятся окончательная очистка воды от углекислого газа. Из десорбционной колонны ДК дегазированная вода насосом Н, через холодильник Х2 предназначенный для её охлаждения до рабочей температуры, подаётся на орошение насадочного абсорбера А.
Для сжатия очищенной азотоводородной смеси, поступающей из сепаратора С1, смешения азотоводородной и циркуляционной смесей, а также циркуляции газовой смеси с невысоким содержанием аммиака в цепи аппаратов синтеза, предусмотрен турбокомпрессор ТК с приводом от паровой конденсационной турбины ПТ. Свежая азотоводородная смесь смешивается с циркуляционной смесью, представляющей собой не прореагировавшие в полочной колонне синтеза ПК газы, и поступает в систему конденсации, состоящую из холодильника Х3, охлаждаемого этиленгликолем, и сепаратора С2, предназначенного для разделения азотоводородной смеси и циркуляционных газов на жидкую (аммиак) и газообразную фазы. Газообразная фаза, включающая пары низкоконцентрированного аммиака и смесь циркуляционных газов и азотоводородной смеси, подогревается в теплообменниках Т3 и Т4 и направляется в полочную колонну синтеза ПК, в которой составляющие газовой фазы при давлении 30 МПа реагируют при непосредственном участии железных катализаторов. Выходящая из колонны с температурой 320-350 °С смесь, содержащая 15-20 % аммиака, проходит последовательно “горячий” теплообменник Т4, отдавая тепло поступающей в полочную колонну ПК газообразной фазе; аппарат воздушного охлаждения Х3, “холодный” теплообменник Т3, работающий с теми же теплоносителями, что и “горячий” теплообменник Т4. Охлаждённая газовая смесь с высоким содержанием аммиака после “холодного” теплообменника Т3 поступает в сепаратор С3 для разделения на жидкий аммиак и циркуляционные (не прореагировавшие) газы, которые затем идут на смешение с чистой азотоводородной смесью в турбокомпрессоре ТК. Аммиак из сепараторов С2 и С3 направляется в хранилище жидкого аммиака.
3.3 Установка производства этанола сернокислотной гидратацией этилена (чертёж КП-02068108-ПАХТ-170500-1.99-97-00.000 Т3)
Этан-этиленовая фракция с содержанием 50-60 % этилена из цеха газоразделения подаётся в нижнюю часть абсорбционной колонны КА. В верхнюю часть колонны подаётся серная кислота с концентрацией 96-98 %. В колонне КА при давлении 2,5 МПа и температуре 67-75 градусов происходит абсорбция этилена серной кислотой с образованием этилсульфата.
Этан выходит из верхней части колонны КА с содержанием этилена 2-4 %. Отходящие из колонны КА газы после дросселирования до 0,7-0,8 МПа в дросселе ДР промываются водой в скруббере С1, нейтрализуются щёлочью в скруббере С2 и после сушки в брызгоуловителе Б направляются на пиролиз в виде возвратной этаноловой фракции. Насос Н1 перекачивает раствор щёлочи из нижней части скруббера С2 на орошение в верхнюю часть. Распределитель Р1 служит для удаления части отработанной щёлочи.
Раствор этилсульфатов из нижней части колонны КА после охлаждения в холодильнике Х1 поступает в гидролизер Г, где смешивается в инжекторе с водой. Гидролиз этилсульфатов осуществляется при давлении 0,2 МПа и температуре 95-100 °С. В результате снижения давления и повышения температуры из раствора выделяются растворённые газы, которые вместе с парами диэтилового эфира выводятся из верхней части гидролизера Г и подаются на промывку в скруббер С1 и нейтрализацию в скруббер С2 вместе с отработанным этаном.
В гидролизате, отходящем из нижней части гидролизера Г, помимо воды, серной кислоты и этилового спирта, содержится также диэтиловый эфир, непрогидролизовавшиеся этилсульфаты и растворённые газы.
Окончательный гидролиз происходит в отпарной колонне КО, куда вместе с гидролизатом вводят острый пар. В отпарной колонне КО при давлении 0,15 МПа и температуре куба 125 °С и верха 95 °С происходит отгонка из гидролизата спирта, диэтилового эфира и части водяных паров. Отработанная серная кислота с концентрацией около 40 % после отпарной колонны КО направляется на очистку от смолистых соединений.
Отходящая из отпарной колонны КО парогазовая смесь подаётся в нейтрализационно-отпарную колонну КН, куб который обогревается острым паром. Парогазовая смесь нейтрализуется в колонне КН 5 %-ым раствором едкого натра и направляется в конденсатор К. Сконденсированный этиловый спирт обрабатывается в сепараторе СП, где из конденсата выделяются растворённые газы. Газы из сепаратора СП после промывки в скруббере С3, выбрасываются в атмосферу.
После сепаратора СП спирт-сырец направляется в ёмкость Е1, откуда насосом Н2 подаётся в подогреватель П. Нагретый до температуры кипения, равной 94 °С, спирт-сырец поступает в ректификационную насадочную колонну КР, куб которой обогревается глухим паром. Ректификация идёт при атмосферном давлении. Обогащённые этанолом пары конденсируются в дефлегматоре Д. Полученный дистиллят разделяется в разделителе Р2: одна часть, в виде флегмы, идёт на орошение колонны КР, другая часть охлаждается в холодильнике Х3 и попадает в ёмкость дистиллята Е3. Кубовый остаток охлаждается в холодильнике Х2, после чего скапливается в ёмкости Е2.
Ёмкости Е2 и Е3 оснащены насосами Н3 и Н4 для дальнейшего транспортирования жидкостей.
4 Нормативные ссылки
В настоящих методических указаниях использованы следующие стандарты:
ГОСТ 2.701-84 ЕСКД. Схемы. Виды и типы. Общие требования к выполнению;
ГОСТ 2.780-96 ЕСКД. Обозначения условные графические. Кондиционеры рабочей среды, ёмкости гидравлические и пневматические;
ГОСТ 2.782-96 ЕСКД. Обозначения условные графические. Насосы и двигатели гидравлические и пневматические;
ГОСТ 2.785-70 ЕСКД. Обозначения условные графические. Арматура трубопроводная;
ГОСТ 2.788-74 ЕСКД. Обозначения условные графические. Аппараты выпарные;
ГОСТ 2.789-74 ЕСКД. Обозначения условные графические. Аппараты теплообменные;
ГОСТ 2.790-74 ЕСКД. Обозначения условные графические. Аппараты колонные;
ГОСТ 2.791-74 ЕСКД. Обозначения условные графические. Отстойники и фильтры;
ГОСТ 2.792-74 ЕСКД. Обозначения условные графические. Аппараты сушильные;
ГОСТ 2.793-79 ЕСКД. Обозначения условные графические. Элементы и устройства машин и аппаратов химических производств;
ГОСТ 2.794-74 ЕСКД. Обозначения условные графические. Устройства питающие и дозирующие;
ГОСТ 2.795-80 ЕСКД. Обозначения условные графические. Центрифуги;
ГОСТ 14202-69. Трубопроводы промышленных предприятий.
Дата добавления: 2018-10-26; просмотров: 2264; Мы поможем в написании вашей работы! |
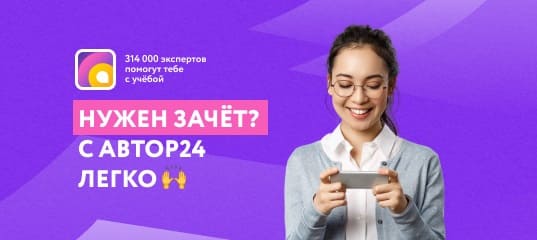
Мы поможем в написании ваших работ!