Производство осевой заготовки
Впервые в России на ОАО "НТМК" разработана и внедрена технология изготовления осевой заготовки из вакуумированного непрерывно-литого металла. На ГУП "Уралвагонзавод" изготовлена опытная партия осей из непрерывно-литых заготовок, которые прошли лабораторные, стендовые и полигонные испытания во ВНИИЖТ. Испытания показали высокое качество осей нового поколения. По результатам испытаний разработаны и утверждены технические условия - ТУ 3100-109-01124238-2000 "Оси черновые (заготовки профильные) из непрерывно-литого металла". Заключен контракт и поставлена опытная партия осевых заготовок в Швецию.
ПРОКАТНОЕ ПРОИЗВОДСТВО
Цех прокатки широкополочных балок
Цех в составе универсально-балочного стана введен в эксплуатацию в 1977 г. Является крупнейшим в Европе комплексом по выпуску широкополочных балок и колонных профилей.
Специализация цеха - выпуск двутавров с параллельными гранями полок широкого сортамента как по высоте профиля от 150 до 610 мм, так и по ширине полки от 100 до 400 мм, в том числе свайного типа. Двутавры изготавливаются с требованиями как отечественных, так и зарубежных стандартов: американских (ASTM A 6), британских (BS 4), японских (JIS G 3192).
В последнее время осуществляется выпуск шпунта корытного типа Л5-У, а также производство круглого проката диаметром 115-150 мм и квадратной заготовки размером от 100 до 200 мм из трубных, рядовых и конструкционных сталей.
|
|
Исходная заготовка - катаная и непрерывно-литая заготовка прямоугольного сечения и фасонная заготовка для крупных двутавров.
Состав оборудования цеха: три методические печи с шагающим подом для нагрева заготовок; участок стана в составе рабочей линии стана, состоящей из обжимной клети 1300, двух групп клетей в составе универсальной и вспомогательной клетей и чистовой универсальной клети; участок сборки и перевалки клетей; участок пил горячей резки с клеймовочной машиной для маркировки кругов и квадратов в горячем состоянии; участок отделки, состоящий из двух поточных линий в составе двух роликоправильных машин для правки фасонных профилей в двух плоскостях и секций для обработки и приемки продукции; линия до отделки отсортированной продукции с пилой холодной резки.
Производственная мощность - 1600 тыс. тонн в год.
В цехе провели плановый ремонт оборудования, проведена большая работа по улучшению работы нагревательных печей. Заменены рекуператоры на двух печах, что позволило не только улучшить качество нагрева, но и изменить экологическую ситуацию в цехе. Были проведены ремонты рабочих клетей прокатного стана, восстановлены начальные нормативные требования. Специалисты провели замену рабочих роликов рольгангов на участке пил горячей резки и подъемного стола чистовой группы клетей, отремонтировали вертикальные и горизонтальные роликоправильные машины, смонтировали две новые шлепперные тележки, обновили оборудование обжимной клети-1300, провели ревизию магистральных трубопроводов и запорной арматуры. Обновление цеха позволит сделать работу подразделения более стабильной и снизить простои оборудования. Проведенный ремонт положительно скажется на качестве выпускаемой продукции.
|
|
Нагретые в печах с шагающим подом до 1190-1260°С заготовки прокатываются в обжимной клети "1300". Затем прокатка ведется последовательно в двух группах предчистовых и чистовой универсальных клетях. Прокатанные полосы по рольгангу подаются на пилы горячей резки, где производится удаление концевой обрези и порезка на мерные длины. Круглый и квадратный прокат маркируется клеймовочной машиной. Порезанные на пилах полосы рольгангом транспортируются на холодильники.
После охлаждения прокат поступает на участок балкоотделки, где проходит его правка, осмотр и приемка.
После приемки готовый прокат пакетируется и отгружается потребителю.
|
|
Нижнетагильский металлургический комбинат разработал технологию и освоил производство двутавров по международным стандартам ASTM, JIS, DIN, BS и гарантирует их высокое качество, подтвержденное международным сертификатом фирмы "TUV".
Впервые в России, для строительства гидротехнических и иных сооружений, разработана технология и освоено производство шпунта Л-5У, по своим техническим характеристикам не имеющим аналогов в мире. Разработана технология и освоено производство шпунта Л5-УМ с конструкцией замка, обеспечивающей более свободное соединение элементов шпунтовой стенки.
Новые профили: На УБС освоена технология прокатки швеллера № 27, профиля для железнодорожных шпал, а также круглого проката сечением до ø 210 мм.
Рельсобалочный цех
Специализация - выпуск продукции транспортного назначения - рельсы, фасонные профили для вагоностроения, а также для тракторостроения и др. отраслей.
Исходная заготовка - катаная и непрерывно-литая заготовка прямоугольной и квадратной формы.
Состав оборудования цеха: методическая печь с шагающими балками для нагрева заготовок (введена в эксплуатацию в 2000 г.); участок стана в составе стана линейного типа, состоящего из обжимной клети 950, двух клетей трио, оборудованных подъемно-качающимися столами, и чистовой клети дуо 850; возвратный поток с ножницами горячей резки; участок пил горячей резки с клеймовочной машиной; участок изотермической выдержки рельсов с 4-мя печами; три роликоправильные машины; участок отделки в составе балкоотделки и трех рельсо-отделочных линий, оборудованных сверлильно-фрезерными агрегатами (первая поточная линия - 2-мя сверлильно-отрезными установками фирмы "Вагнер") и инспекторскими стеллажами для обработки и приемки рельсов; термическое отделение.
|
|
год станет для цеха особенным, поскольку предстоит выполнить большое количество иностранных заказов на продукцию с повышенными требованиями к качеству и профилю, нестандартной длины. В цехе функционируют два вальцетокарных станка фирмы "Геркулес" (Германия), дающие высокую точность обработки прокатных валков. В следующем году цех планирует закупить еще один.
В цехе запущена в работу обновленная печь изотермической выдержки № 2. Она предназначена для удаления остаточного водорода из рельсов, что исключает образование микротрещин в готовой продукции. 54 тонны проката в течение двух часов выдерживаются в печи при температуре 600оС (плюс-минус 20оС). Капитальный ремонт теплотехнического агрегата улучшил качество готовой продукции цеха.
Термическое отделение является участком, расположенным в отдельно стоящем корпусе, со складом подготовки рельсов к термообработке. Предназначено для объемной закалки рельсов и их отделки и приемки.
Состав оборудования термоотделения: участок термической обработки рельсов в составе закалочной печи, закалочной машины и отпускной печи; две роликоправильные машины и два вертикально-правильных пресса; участок неразрушающего контроля в составе установок УЗК и контроля прямолинейности рельсов; пакетоукладчик рельсов.
Производственная мощность, тонн в год:
рельсобалочного цеха - 1500000;
термоотделения - 730000.
Пропускная способность по обработке термоупрочненных рельсов с повышенными требованиями составляет до 420 тыс. тонн в год.
Для нагрева заготовок под прокат рельсов и профилей для вагоностроения и машиностроения промышленности имеется одна методическая печь с шагающими балками, введённая в эксплуатацию в 2000-ом году. Основное прокатное оборудование состоит из стана "950" с двухвалковой реверсивной клетью и стана "850" с двумя клетями "трио", оборудованными подъёмно-качающимися столами, и одной клетью "дуо", расположенными в линию. Раскаты разрезаются на мерные длины пилами горячей резки маятникового типа. Участок изотермической выдержки рельсов, обеспечивающий их противофлокенную обработку, включает в себя пять проходных печей, систему стеллажей и рольгангов для передачи и транспортировки рельсов.
Операции отделки рельсов проводятся на сверлильно-отрезных станках фирмы "Вагнер". Объёмная закалка рельсов длиной 25 м проводится в масле в специальной закалочной машине револьверного типа. Нагрев под закалку и отпуск осуществляется в проходных печах.
Охлаждённые рельсы проходят правку в двух плоскостях в роликоправильных машинах, оценку прямолинейности и подвергаются ультразвуковому контролю.
Рельсы, производимые из непрерывно-литых заготовок, получаемых в конвертерном цехе, имеют высокую чистоту стали по неметаллическим включениям и низкую её газонасыщенность.
На комбинате производятся рельсы для различных условий эксплуатации:
- рельсы низкотемпературной надежности из стали с повышенным содержанием ванадия и азота. Эти рельсы предназначены для эксплуатации в условиях низких температур (до -60°С);
- рельсы повышенной износостойкости, предназначенные для службы в кривых участках пути малого радиуса. Эти рельсы изготовлены из заэвтектоидной стали (с повышенным содержанием углерода) и имеют специальный профиль с закругленной головкой;
- рельсы для скоростных участков пути, отвечающие высоким требованиям по прямолинейности;
- рельсы типов UIC60 и 136RE, отвечающие требованиям международных стандартов, для поставок на зарубежный рынок;
- нетермоупроченные рельсы типов Р50 и Р65 для метрополитенов.
ОАО "НТМК" - единственный в России комбинат, освоивший выпуск профиля Z - 310 для хребтовой балки с повышенными прочностными характеристиками (класс прочности 420), для вагонов нового поколения.
Крупносортный цех
Специализация - производство заготовки для трубных и машиностроительных заводов и выпуск продукции для строительства и др. отраслей.
Исходная заготовка - катаная и непрерывно-литая заготовка прямоугольной и квадратной формы.
Состав оборудования цеха: три методические четырехзонные печи для нагрева заготовок; участок стана в составе стана линейного типа, состоящего из обжимной клети 850 и стана 650, включающего две клети трио, оборудованные подъемно-качающимися столами, и чистовую клеть дуо 650; участок пил горячей резки (6 штук); участок отделки проката в потоке с двумя линиями в составе роликоправильной машины для правки фасонных профилей, секций для обработки, пакетоукладчиков фланцевых профилей и уголков; линия до отделки отсортированной продукции с пилой холодной резки; линия механизированной зачистки для обработки круглого проката в составе косовалковой роликоправильной машины, сверлильных и четырех горизонтально-фрезерных станков и секций для приемки; линия отделки рельсов узкой колеи с двумя сверлильными станками и секциями для обработки и приемки.
В 2007 году в цехе произвели более 800 тысяч тонн готовой продукции, свыше двух десятков наименований различных профилей сложного типа: швеллеров, двутавров, угловой стали для вагоностроения.
Нагретые в методических печах до 1190-1260 °С заготовки прокатываются в обжимной клети "800". Прокатанные в обжимной клети за 5 - 7 проходов заготовки по рольгангу подаются на стан "650", затем прокатанные полосы по рольгангу подаются на пилы горячей резки, где производится удаление концевой обрези и порезка на мерные длины; на каждую штангу наносится маркировка. Рельсы маркируются клеймовочной машиной, установленной за чистовой клетью. Порезанные на пилах полосы по рольгангу транспортируются на холодильник.
Для замедленного охлаждения трещиночувствительного металла предусмотрено две термоямы. После охлаждения прокат круглого и квадратного сечения выдается на две сортоотделки. Дефекты на круглых и квадратных профилях удаляются на линии механизированной зачистки (ЛМЗ) и вручную, пневматическими молотками на двух стеллажах. Фланцевые профили после охлаждения проходят правку на роликоправильных машинах консольного типа и, после рассортировки на сортоотделках, пакетируются пакетоукладчиками в пакеты массой до 5 тонн. Дефектные полосы с сортоотделок снимаются магнитными кранами в штабеля для последующей доработки. После отделки и приемки готовый прокат отгружается потребителю.
Нижнетагильский металлургический комбинат освоил технологию производства трубной заготовки из шарикоподшипниковой стали ШХ15 и ШХ15СГ. Освоено производство круглого проката диаметром 40 мм.
Колёсобандажный цех
Колесобандажный цех представляет собой комплекс в составе двух отдельных станов: колесопрокатного и бандажного.
На участке полнопрофильной обработки колес осваивают новые карусельные станки Краснодарского завода "Седин". Их выход на проектную мощность существенно улучшит производственные показатели цеха. Обрабатывают на этих станках железнодорожные колеса Ø 957 мм, которые поступают к нам как с новой прессопрокатной линии, так и со старого стана.
Масштабное обновление КБЦ продолжается в течение нескольких последних лет. В цехе уже введены в строй новый прессопрокатный участок, две линии выходного контроля, печь для нагрева заготовок.
На НТМК проведена реконструкция термоучастка. Был заключен контракт с немецкой компанией "Мерц" на сооружение термического участка для колесного производства. Новое оборудование позволит производить термообработку колес высокой твердости с производительностью порядка 100 штук в час. Новое термоотделение станет завершающим этапом реконструкции колесного производства. Благодаря реализации этого проекта, комбинат станет обладать самым совершенным комплексом по выпуску железнодорожных колес, отвечающим всем требованиям мировых стандартов по прочности, твердости и износостойкости продукции, а также природоохранных норм.
В цехе закончилась модернизация линии выходного контроля колес №2. специалистами Томской электронной компании смонтировали транспортерные пути и оборудование двух новых блоков. На линии появилась установка для антикоррозийной покраски и дробенаклепа. Метод поверхностного упрочнения применяется на третьей линии контроля колес, а после ЛВК - 2 все 100% выпускаемых цехом колес упрочняются в соответствии с требованиями Российских железных дорог.
Колесопрокатный стан
Специализация - выпуск цельнокатаных железнодорожных колес и заготовок колес для подвижного состава и кранового машиностроения.
Исходная заготовка - круглая непрерывно-литая заготовка диаметром 430 мм.
Состав оборудования: заготовительный участок с шестью пильными установками для порезки на штучные заготовки, обеспечивает заготовками колесопрокатный и бандажный станы; печной участок в составе двух кольцевых печей с вращающимся подом; прессо-прокатный участок в составе пресса усилием 3000 т для обжатия и калибровки заготовки, пресса усилием 500 т для прошивки отверстия, пресса усилием 7000 т для формирования ступицы с отверстием и прилегающей к ней части диска, семивалкового прокатного стана для выкатывания обода с гребнем и прилегающей к ободу части диска, пресса усилием 3000 т для калибровки колеса, выгибки диска и нанесения маркировки; в 2005 году введен новый прессо-прокатный участок производительностью 630000 тысяч колес в год в следующем составе:
· установка для гидрослива окалины
· три пресса с суммарным усилием 19 тыс. тонн
· колесопрокатный стан
· маркировочная машина
· система автоматического замера геометрических параметров и регулировки режимов обработки; С освоением нового прессо-прокатного участка оборудование старого ППУ будет выведено из эксплуатации; участок термической обработки в составе двух кольцевых печей с вращающимся подом для нагрева под закалку, шести закалочных горизонтальных столов, 48 колодцевых отапливаемых печей для отпуска колес садкой по 6 колес в стопе; участок механической обработки колес в составе станков модели 1В502, 1В503, М153, VDM 120-12; в 2005 году введен в эксплуатацию участок полно профильной механической обработки колес с производственной мощностью 180 000 шт. в год в следующем составе:
· две роботизированные линии, включающие 7 станков полно профильной обработки колеса
· станки для балансировки колес и расточки отверстия в ступице; участок приемки колес в составе двух стендов с установками УЗК, стенды вихретокового контроля; в 2004 году введена вторая линия выходного контроля колес производительностью 300 тысяч штук в год в следующем составе:
· оборудование для дробеструйной обработки;
· оборудование для замера твердости;
· установка ультразвукового контроля колес;
· участок покраски колес.
Бандажный стан
Специализация - выпуск бандажей для подвижного состава и заготовок колец различной конфигурации для машиностроения.
Исходная заготовка - круглая непрерывно-литая заготовка диаметром 430 мм.
Состав оборудования: печной участок в составе методической и двух камерных печей для нагрева заготовок; прессопрокатный участок в составе пресса усилием 3200 т для осадки заготовки и прошивки отверстия, чернового стана для предварительной раскатки заготовки, чистового стан для раскатки бандажей и колец до требуемых размеров и формы, пресса усилием 400 т для нанесения маркировки; участок замедленного охлаждения для противофлокенной обработки бандажей и колец из флокеночувствительной стали; участок термической обработки в составе 16 печей шахтного типа для нагрева под закалку и отпуск, специальных закалочных баков; два стенда ультразвукового контроля бандажей.
Производственная мощность, тыс. тонн в год:
колесопрокатного стана - 205.
бандажного стана - 148.
По пропускной способности заготовительного участка цеха в составе 6 пильных установок производственная мощность цеха составляет 235 тыс. тонн в год.
Производство колёс
Исходную непрерывно-литую заготовку диаметром 430 мм из конвертерной стали режут на пилах Вагнера на части. Осмотренные заготовки направляют в рекуперативную кольцевую печь с вращающимся подом для нагрева. Заготовки подают на прессопрокатный участок. После прокатки колёса и заготовки колёс проходят обработку в отапливаемых колодцевых печах, операцию закалки обода с последующим отпуском. Для контроля внутренних дефектов железнодорожных колёс применяют ультразвуковой метод.
На ОАО "НТМК" разработана технология и освоено производство трех типоразмеров железнодорожных колес по международному стандарту UIC-812-3 для поставки в Швецию из стали В82, двух типоразмеров колес из стали R7T для поставки в Болгарию.
Освоено производство колеса диаметром ø 957 мм c S-образным диском, конструкция которого разработана специалистами ОАО "НТМК". Колесо предназначено для вагонов нового поколения.
Колеса с S-образным диском успешно выдержали стендовые усталостные испытания во ВНИИЖТ как при нагрузках, соответствующих сертификационным нормам для рядовых колес, так и при нагрузках, рассчитанных для перспективных условий эксплуатации с осевыми нагрузками 25 и 30 тс для вагонов нового поколения.
На ОАО "НТМК" разработана технология и ведется освоение производства опытной партии цельнокатаных черновых заготовок колес диаметром 36 дюймов для поставки на Североамериканский рынок в соответствии с требованиями стандарта М-107-84/М-208-84.
Производство бандажей
Для получения бандажей используются непрерывно-литые заготовки диаметром 430мм. Заготовки режут на требуемый размер на пилах Вагнера. Осмотренные заготовки направляют в методическую, а затем в камерную печь для нагрева. После прокатки бандажи и кольца подвергаются замедленному охлаждению или изотермической выдержке. На стане имеется оборудование для закалки с отпуском или нормализации бандажей и колец. Все бандажи проходят ультразвуковой контроль.
На бандажном стане разработана технология и освоено производство черновых бандажей из стали марки В6Т для локомотивов для поставки Болгарским железным дорогам, отвечающим требованиям международных стандартов UIC-810-1 и UIC-810-2.
Шаропрокатный цех
Специализация - производство шаров для мельниц горнодобывающей и цементной промышленности.
Исходная заготовка - круглый прокат соответствующего диаметра, изготавливаемый в крупносортном цехе и ЦПШБ.
Цех включает две автономные линии по производству шаров:
диаметром от 40 до 80 мм - стан СПШ - 80;
диаметром от 80 до 125 мм - стан СПШ - 120.
Состав линии: секционная печь скоростного нагрева заготовок; двухвалковый стан поперечно-винтовой прокатки конструкции ВНИИМЕТМАШ; установка закалки шаров барабанного типа.
Производственная мощность - 180 тыс. тонн в год.
Освоена технология выпуска мелющих шаров повышенной твердости (50-52 HRC).
7. АНАЛИЗ ТЕХНОЛОГИИ ВНЕПЕЧНОЙ ОБРАБОТКИ СТАЛИ НА ОАО "ЕВРАЗ НТМК"
В процессе внепечной обработки стали происходит охлаждение металла, что ограничивает продолжительность обработки. Компенсация тепловых потерь осуществляется различными способами. В этом плане, агрегаты, используемые для вне-печной обработки стали, условно можно разделить на несколько групп: 1)без дополнительного подогрева или подачи тепла в процессе обработки (установки для обработки вакуумом различными методами, для введения в металл реагентов в виде порошка, проволоки, блоков, установки типа накрытого крышкой ковша при продувке металла инертным газом); 2) подвод тепла осуществляется в результате окисления железа и примесей при продувке кислородом (конвертеры типа AOD, VODC, RH-OB, RHO и др. рассмотрены выше); 3) с электрическим подогревом.
Наиболее распространенными в настоящее время способами, позволяющими подогревать металл в процессе обработки, .является ASEA-SKF-процесс возникший в Швеции в 1964 г., и более простой Finkl'-процесс, появившийся несколько позже в США. Первый метод представляет собой способ обработки металла, при котором помимо индукционного перемешивания металл сверху подогревается электрическими дугами (7.1). В таком агрегате металл может выдерживаться под вакуумом длительное время (до 2 ч), что обеспечивает высокую степень рафинирования его от вредных примесей. В некоторых случаях на поверхность перемешиваемого под воздействием индуктора металла вводят также некоторое количество шлакообразующих. Способ сложен и дорогостоящ, однако высокое качество металла компенсирует затраты и данный способ получил достаточно широкое распространение.
Имеются сообщения, в которых дана сравнительная оценка технико-экономических показателей и характеристик качества стали, выплавленной с применением ASEA-SKF (0,0009% О2 и 0,005% S) и методом ЭПШ (0,0014% Ог и 0,004% S). При этом делается вывод в пользу стали, рафинированной на установке ASEA-SKF, из-за более низкой стоимости по сравнению со сталью ЭШП при, по меньшей мере, одинаковых показателях долговечности подшипников. В СССР установки типа ASEA-SKF работают в сталеплавильных цехах некоторых заводов тяжелого и энергетического машиностроения, где отливают крупные слитки для изготовления роторов турбин электростанций и т.п. ответственных изделий. Если в методе ASEA-SKF используется индукционное перемешивание, то в Finkl-процессе перемешивание осуществляется более простым способом - продувкой аргоном, при этом ковш находится в стационарном положении, что упрощает обработку металла при производстве его в больших количествах. Установки типа ASEA-SKF- это уже не просто ковши, а металлургические агрегаты, в которых проводят определенные металлургические операции, процесс становится по существу дуплекс-процессом: печь (или конвертер) - вторичный агрегат.
Постепенно в мировой практике получает распространение процесс, названный процессом ковш- печь (по наименованиям слоев на английском языке в зарубежной литературе процесс получил название LF-процесс. Процесс включает перемешивание продувкой металла аргоном в ковше, Дуговой подогрев и обработку металла синтетическим шлаком в процессе его перемешивания аргоном. Процесс обеспечивает не только получение заданного химического состава и температуры металла, но и снижение количества неметаллических включений в результате удаления серы и кислорода, что привело к значительному улучшению механических свойств. Такой агрегат может устанавливаться в любом сталеплавильном цехе.
Типичная конструкция установки LF (печь - ковш) показана на 7.2. В ковше наводится рафинировочный шлак и в него сверху опускают электроды системы электродугового нагрева таким образом, чтобы обеспечить достаточную эффективную теплопередачу и одновременно защитить огнеупоры ковша от дуги. При этом остаточные оксиды железа в шлаке восстанавливаются графитовыми электродами. В результате получают "улырачистую" сталь с низким содержанием серы.
На 73 показан вариант установки типа ковш- печь, предусматривающий возможность перемеишвания металла аргоном под слоем синтетического шлака, вдувание порошкообразных реагентов и подогрев расплава одновременно. Примером комбинированного процесса с обработкой металла и вакуумом, и продувкой аргоном и синтетическими шлаковыми смесями может служить VAD -процесс [2].
Агрегат состоит (7.4) из камеры, установленной на самодвижущейся тележке, и вакуумного трубопровода в стационарном своде (а не в корпусе камеры). Технология проведения операции следующая: 1) помещение ковша в VAD-камеру и продувка аргоном в течение Змин (без вакуума); 2) отбор пробы металла на химический анализ и перемещение камеры с ковшом на участок скачивания шлака (содержащего FeO и Р2О5); перемещение камеры с ковшом к VAD-устройству, накрьгвание сводом и вакуумирование с подогревом (или без подогрева); подогрев осуществляется при помощи электродов, опускаемых через свод; 3) одновременно с вакуумированием наводится присадкой CaO, CaF2 и алюминия новый шлак и продолжается продувка аргоном; 4) после 20-25 мин такой обработки под вакуумом производится корректировка химического состава и температуры (электроподогревом); 5) после получения требуемых результатов вакуумирование прекращается и камера с ковшом транспортируется на разливочную площадку.
В тех случаях, когда требуется получать < 0,004 % S, в металл дополнительно вдувается порошок СаС2 или силико-кальция. Фурма погружается на глубину 2,5 м, продолжительность вдувания 15 мин, содержание серы до окончания процесса вдувания 0,001%. Фурму для вдувания изготавливают из цельнотянутой трубы с нанизанными на нее катушками из огнеупорного материала, содержащего 60 % А12О3, навинчивающейся пробки (80 % А1гО3) и вставки на месте выхода струи (95 % А12О3). Стойкость фурмы 15 мин (одна продувка). Получаемая сталь может быть предназначена для изготовления крупных емкостей для сжиженного газа, арктических трубопроводов, буровых морских платформ, атомных электростанций, специальных установок химической и нефтехимической промышленности.
Подробное исследование технологии обработки по способу VAD проведено на заводе фирмы "Nippon Kokan" [3]. На заводе имеется 50-т установка VAD; металл на установку поступает с 50-т дуговой печи или из 250-т кислородного конвертера, в последнем случае берется порция 50 т. Легирующие элементы и флюсы присаживаются в ковш под вакуумом, металл продувают аргоном через пористую пробку. Полный цикл обработки стали в установке длится 140 мин, из них первые 80 мин - подогрев металла с 1540 до 1640 °С при давлении 26,6кПа, затем 40мин- снова подогрев и доведение температуры металла до 1600 °С. Для десульфураиии стали использованы шлаки, содержащие при пересчете компонентов на квазитройную систему 50-70 % СаО, 20-35 % А12О3 и 10 % SiO2. По результатам испытаний наибольший коэффициент распределения (S)/[S], превышающий 600, был достигнут в области существования в жидкой фазе и извести и трисиликата кальция. Переход шлака как в области большего количества твердой фазы извести при наличии трисиликата кальция в шлаковом расплаве, так и полностью в область жидкого состояния снижает скорость десульфурации и коэффициент распределения серы. Перед обработкой из ковша скачивали печной шлак, поэтому суммарное содержание оксидов железа и марганца в шлаке для десульфурации не превышало 1 %. Оптимальный состав шлака близок к 60 % СаО, 10% SiO2 и 30% А12О3. ЭТО подтверждено лабораторными экспериментами и расчетом. В качестве основы для расчетов десульфурации металла, раскисленного алюминием, принята реакция: 3(СаО)+ 2[Al]+ 3 [S] = 3(CaS)+ AI2O3.
Помимо установок LF с дуговым подогревом разрабатываются установки с использованием методов индукционного нагрева (и перемешивания). В качестве примера на 7.5 показана схема агрегата, разработанного SCRATA* (ЮАР). Процесс назван LMR* . По сообщениям [4] процесс особенно удобен для получения сравнительно небольших порций легированных (например, 13 % Сг и 4 % Ni) сталей, где требуется гарантированно низкое содержание примесей. Необходимо упомянуть и о попытках использовать в процессе вне-печной обработки и такой традиционный способ нагрева, как юпливные горелки. Так, на заводе "Holmstad" (Швеция) с 1986 г. работает 50-т печь-ковш с двумя топливно-кислородными горелками мощностью по 5 МВт, в которой обрабатываются плавки из 50-т дуговой печи. В процессе обработки металл продувается инертным газом. Горелки установлены в крышке ковша. Типичный период нагрева продолжается 12 мин и за это время температура металла повышается примерно на 15°С со средней скоростью 0,95°С/мин при подводимой мощности 80 кВт/т. Общее количество подводимой энергии 800 кВт-ч, усвоенной- 280 кВт-ч, что соответствует среднему к.п.д. 35 %. К.п.д. изменяется в процессе нагрева с 20 до 45 %. Возможно снижение температуры выпуска стали из дуговой печи и уменьшение при этом расхода энергии в дуговой печи примерно на 50 кВт -ч/т (при расходе энерги в установке печь-ковш 25-30 кВт -ч/т) [5].
В настоящее время среди металлургов имеются сторонники внепечной металлургии и с использованием установок типа ковш-печь и инжекдионной металлургии. И тот и другой метод имеют свои преимущества и недостатки. Например, для установок печь-ковш металл в печи можно нагревать до оптимальной температуры и в результате этого уменьшить продолжительность плавки в основном агрегате и снизить расход огнеупоров и энергии. При использовании инжекционной металлургии требуется перегрев металла в плавильном агрегате, но можно быстро и эффективно вести процессы десуль-фурации, легирования и раскисления с очень высокой степенью усвоения добавляемых элементов. Как видно из приведенных примеров, активно разрабатываются технологии, представляющие собой сочетание обоих методов. Разрабатываются также системы, предусматривающие использование двух ковшей: в установке печь-ковш и для инжекции порошкообразных реагентов. При этом считают, что такие системы более гибкие и позволяют получать высококачественную сталь с низким расходом электроэнергии и огнеупоров.
Многие чисто технологические приемы работы на агрегатах типа ковш-печь находятся еще в стадии отработки. Так, например, явление вспенивания шлака при внепечной обработке в агрегатах ковш-печь позволяет (так же, как и в электропечи) защитить футеровку ковша и свода от радиационного воздействия дуг и снизить уровень шума в пролете. Поскольку при внепечной обработке окисленность шлака значительно ниже, чем в печи, эффект пенообразования (например, от взаимодействия присадок графита со шлаком) не получает развития и для достижения заметного газовыделения иногда применяют чистые мелкие фракции СаСО3 в смеси с частичками графита (до 10%). Практика использования пенообразующих добавок складывается из учета ограничения попадания печного шлака при выпуске в ковш, наведении в ковше основного шлака добавками СаО (а также по мере необходимости боксита, кремнезема и плавикового шпата), чтобы после короткого периода нагрева в ковше-печи получить шлак, содержащий 55-60 % СаО; 16-24 % SiO2; 8-12 % Al2O3; MgO 8-12%; CaFj до 3 % (FeO + MnO). Суммарный расход шлакообразующих составляет 6-10 кг/т. После этого в ходе рафинирования и нагрева металла в шлак вводят диа-мидную известь с расходом до 1 кг/т. При необходимости улучшения условий пенообразования присадку этой извести повторяют. При таком сиособе обработки отмечено снижение содержания водорода и глубокое раскисление в результате снижения содержания в шлаке оксидов железа и марганца. Установки типа ковш-печь широко применяют также в качестве миксеров для накопления стали при изготовлении особо крупных слитков и отливок. В этих случаях также разрабатывается специальная технология.
Производительность современных установок ковш-печь достаточно высока. Так, в конце 1985 г. одной из компаний ФРГ пущены в Западной Европе в эксплуатацию 50- и 110-т установки ковш-печь. Основные показатели установок (соответственно для 50-т и 110-т): число обрабатываемых плавок в сутки - 14 и 20; продолжительность обработки 37 и 35 мин; расход электроэнергии 35 и 33 кВт • ч/т; расход электродов - 0,35 и 0,23 кг/т; максимальная скорость нагрева - 6 и 4 °С/мин; расход газа для продувки - 0,5 и 0,25 м3/т; расход огнеупоров - 3,3 и 3,9 кг/т; стойкость продувочной фурмы- 10 и 4 плавок.
ЗАКЛЮЧЕНИЕ
В ходе практики мной были детально изучены состав оборудования Конвертерного цеха, технологический процесс сталеплавильного производства, а так же формы и методы управления производством и научной организации труда. Настоящая практика в значительной степени поспособствовала закреплению теоретических знаний, полученных в процессе обучения в институте.
Кроме того, мною был осуществлен сбор материалов для выполнения отчета по практике. Полученные в течении практики сведения, кратко изложены в данном отчете.
БИБЛИОГРАФИЧЕСКИЙ СПИСОК
1. ТИ 102-Д-78-2004. Производство чугуна. Введ. 01.01.2004. Нижний Тагил: ОАО "НТМК", 2005. - 148 с.
2. Вегман Е. Ф., Жеребин Б. Н., Похвиснев А. Н., Юсфин Ю. С., Курунов И. Ф., Пареньков А. Е., Черноусов П. И. Металлургия чугуна: Учебник для вузов. 3-е изд., пепрераб. И доп. / Под редакцией Ю. С. Юсфина. - М.: ИКЦ "Академкнига", 2004. - 774 с.: ил.
3. Вегман Е. Ф. Теория и технология агломерации. - М.: Металлургия, 1974. - 286 с.
4. Пискунов И. Н., Смирнов Ю. М. Пирометаллургия цинка. - Л.: Изд. ЛГУ, 1978. - 101 с.
5. Вегман Е. Ф. Окускованне руд и концентратов. - М.: Металлургия, 1981. - 240 с.
6. Степин Г. М., Мкртчан Л. С., Довлядов И. В., Борщевский И. К. Проблемы цинка в доменном производстве России и пути их решения // Металлург. 2001. №10. С. 39-42.
7. Юсфин Ю. С., Черноусов П. И., Ушакова М. В. Подтверждение факта минералообразования на полигонах техногенных образований // Известия высших учебных заведений. Черная металлургия. 2007. № 3. С. 11-12.
8. Валавин В. С., Юсфин Ю. С., Подгородецкий Г. С. и др. Поведение цинка в агломерационном процессе // Сталь. 1988. № 4. С. 12-17.
9. Глинка Н. А. Общая химия. - М.: Госкомиздат,1956. - 732 с.
10.Исидоров В. А. Экологическая химия: учеб. Пособ. Для вузов. - СПб.: Химиздат, 2001. - 304 с.
11.Хесин Ю. И. Охрана труда в доменном производстве. М.: Металлургия, 1976. - 264 с.
12.1Старк С. Б. Газоочистные аппараты и установки в металлургическом производстве. - М.: Металлургия, 1990. - 400 с.
1. Беспамятнов Г.П., Кротов Ю.А. Предельно допустимые концентрации химических веществ в окружающей среде. Л.: Химия, 1985. 528 с.
. Васильев Г.А., Жидков В.Д., Шакирзянова Л.Г. Основы безопасности труда на предприятиях черной металлургии. М.: Металлургия, 1983. 224 с.
3. Воскобойников В.Г., Кудрин В.А., Якушев А.М. Общая металлургия. 4-е изд., дополн. и перераб. М.: Металлургия, 1985. 480 с.
. Долин П.А. Справочник по технике безопасности. 6-е изд., дополн. и перераб. М.: Энергоатомиздат, 1985. 824 с.
. Доменное производство на рубеже ХХI века // Новости черной металлургии за рубежом. 2000. С. 3-20.
6. Доклад о состоянии окружающей природной среды Свердловской области в 2000 г. // Областная газета. 2001. №10. С. 2-3.
. Алиев Г.М.-А. Техника пылеулавливания и очистки промышленных газов. М.: Металлургия, 1986. 544 с.
8. Государственный доклад "О состоянии окружающей среды и влиянии факторов среды обитания на здоровье населения Свердловской области за 2001 год".
. Меры по повышению длительности кампании доменных печей // Новости черной металлургии за рубежом. 1997. №1. С. 19-32.
10. Даньшин В.В., Черноусов П.И. Справочник доменщика. Челябинск: Металлургия, 1989. 320 с.
11. Опытные доменные плавки на НТМК качканарских неофлюсованных окатышей в смеси с агломератом обычной и повышенной основности (Отчет по теме 08/02). ТОО НПВФ "Феррокс", Меламуд С.Г., Марсуверский Б.А., Екатеринбург, 1993. 46 с.
. НТМК. Заключение по НИР 120-65. Разработка и внедрение технологии доменной плавки с использованием в шихте первичного мартеновского шлака. ЦЛК, Еатеренбург -Нижний Тагил, 1993. 48 с.
. Б.А.Марсуверскии, В.С. Рудин, Г.С. Шибаев, Б.В. Качула, А.Ю. Чернавин Совершенствование технологии выплавки ванадиевого чугуна регулированием процессов восстановления оксидов титана // Сталь. 1995. № 1. С. 7-10 .
. НТМК. Установка приготовления и вдувания пылеугольного топлива в доменные печи №5 и №6. Технико-экономический расчет / АО "Тагилметаллургпроект". Нижний Тагил, 1992. 77 с.
. С.В. Худов, П.И. Самоилов Геологическое строение и комплексная оценка руд Гусевогорского месторождения //Горныи журнал. 1993. № 9-10. С.7-8.
. С.Г. Меламуд, В.Я. Дегодя, В.С. Рудин, Б.А. Марсуверскии Разработка и освоение технологии производства и доменнои плавки неофлюсованных окатышеи // Горныи журнал. 1993. № 9-10. С.33-37.
. НТМК. Рекультивация шлаковых отвалов. Комплексная переработка отходов. Техническое решение Т-52388-ПЗ / ПКИ "Металлургпроект". 1992. 137 с.
. Злобинский Б.М. Охрана труда в металлургии. 2-е изд., дополн. и перераб. М.: Металлургия, 1975. 535 с.
. Васильев Г.А., Вилисов Г.В. Безопасность труда в доменном производстве. М.: Металлургия, 1988. 143 с.
. Юдашкин М.Я. Пылеулавливание и очистка газов в черной металлургии. 2-е изд., дополн. и перераб. М.: Металлургия, 1984. 320 с.
Дата добавления: 2018-09-23; просмотров: 440; Мы поможем в написании вашей работы! |
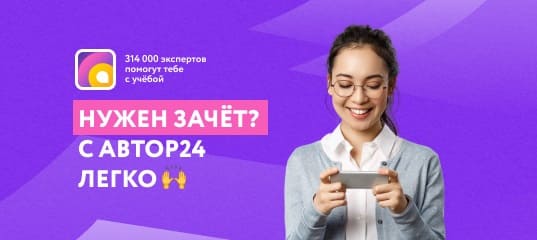
Мы поможем в написании ваших работ!